光学元件的疵病检测及现状
下载: 653次
1 引 言
在各种各样的光学仪器中,几乎都要使用平面光学零件,而平面光学零件所用的光学材料主要是光学玻璃。在光学玻璃的加工过程中,通常需要通过粗磨、精磨和抛光三大基本工序,才能将毛坯加工成透明的光学表面[1]。其中,抛光是获得光学表面最主要的工序,针对不同光学零件将会有不同的抛光方法。
化学机械平面化[2](CMP)是一种独特的超精密加工技术,它是利用化学力和机械力使光学玻璃等表面光滑平整而进行的抛光,可以获得良好的局部或全局平面性。CMP工艺由于具有全局平面化、缺陷少、台阶覆盖好、适用于各种材料等优点而应用广泛。
本质上,不同抛光工艺所产生的缺陷是及其近似的,主要的不同是抛光过程中所使用的抛光氧化物类型、表面缺陷的类型和表面缺陷严重程度的不同。在CMP过程中产生的疵病及其原因大致分为以下几类[3-4]:
(1)由于研磨垫、研磨剂和光学元件片表面之间存在复杂的相互作用,导致光学元件表面产生不同类型的划痕,比如微划痕、长而深的划痕以及颤振等。划痕又称擦痕,是光学零件表面上的任何一种狭长的痕迹或磨损,它对光非常敏感。这些是最常见的疵病。
(2)碱性溶液的侵蚀作用和水(潮气)导致的腐蚀、麻点等。
(3)局部的高抛光率和研磨垫的灵活可变性导致的凹陷、侵蚀和沟槽的现象。
(4)局部过大的机械应力和抛光作用产生的剪切力所导致的玻璃变形、涂污、断裂等机械损伤。
(5)CMP后清洗过程很差时研磨垫材料和研磨垫碎片所产生磨料颗粒污染、抛光残留物的嵌入污染和污渍现象。
CMP过程中所使用的磨料颗粒在纳米范围内,所产生的疵病也在微纳米级别,但这些表面疵病将会产生不同程度的成品率损失,影响产品的可靠性、视场清晰度、元件寿命等。由于现代光学元件或集成电路中需要抛光的材料越来越多,因此对抛光过程中所产生的表面疵病的来源、表面疵病的检测标准及检测方法进行更深入的研究是十分必要的。本文以平面光学元件为研究对象,介绍其在CMP工艺中疵病的检测标准及检测方法。
1 疵病检测国家标准及应用
任何一种产品都存在检验标准,而标准是判断该类产品是否合格的主要判据。目前,对光学元件外观的检验标准主要包括国际标准ISO 10110-7、国家标准GB/T 1185—2006、德国工业标准DIN3140-7以及美国军用规范MIL-PRF-13830B[5-7],其中美国军用规范的使用比较广泛。长期以来,描述光学表面质量的实际标准方法一直是使用一对数字,即采用“数字1-数字2”来表示划痕和凹坑规范。划痕和凹坑规范是一个高度主观的适用于表面的可见性标准。起初划痕和凹坑的标准适用于**产品,后来延伸到民用产品。
目前所用的划痕和凹坑规范是于1954年首次作为**标准发布的,它是指在特定的暗场照明条件下,对测试表面缺陷进行视觉比较并确定缺陷可见性或“等级”的比较标准。这种处理表面缺陷的方法最初是由McLeod和Sherwood在1945年提出的[8]。该标准由两个用短线分隔的数字组成,比如60-40或20-10,其中:第一个数字有时被称为划痕的最大宽度(单位为 μm),但实际上是为了与一组标有划痕号的标准划痕进行视觉比较;第二个数字是凹坑允许的最大直径(单位为 mm/%)。因此,60-40规格表示划痕的视觉外观允许与60#标准划痕相匹配,凹痕直径允许高达0.4 mm。
划痕和凹坑规范还对所有划痕的总长度和划痕的总数量进行了限制。在光学元件表面上,划痕的长度与允许的最大划痕数的总和不得超过光学元件直径的四分之一,较小的划痕也有限制。设lj为第j个划痕的长度,根据标准要求这些参数应该满足
式中:n为光学元件实际划痕数;D为光学元件的直径,单位为mm;smax为标准规范中允许的最大划痕数。只有在实际的划痕数达到允许的最大值时,式(1)标准才适用。如果实际的划痕数低于允许的最大划痕数,则对划痕长度的限制放宽到
允许的最大尺寸凹坑数量为
式中 Int表示对数值取整。所有凹坑直径之和为
式中:dj为第j个凹坑的直径;dmax为标准规范允许的最大直径(单位为 mm)。例如,对于60-40规范,则对应的dmax为0.4 mm。MIL-PRF-13830B需要更多的细节和资格,而上面给出的规范对我们目前的应用已经足够了。
长期以来,人们一直试图使用表面疵病中的划痕和凹坑规范来控制精密光学系统表面的缺陷,而这又是一个高度主观的可见性标准。在现有的疵病中,划痕的长度、宽度或者凹坑的直径大小均未涉及疵病深层结构,仅能对二维平面的疵病进行标准化。由此可见,目前针对光学元件的疵病检测还没有统一的客观标准。
2 光学元件疵病检测方法
表面缺陷对光学元件的表面质量有很大影响,在CMP工艺中产生的表面疵病种类繁多,形式不一。而针对表面缺陷的检测技术大体可分为接触式和非接触式两大类,在两大类下又可细分成很多种,具体分类如
接触式检测法以扫描探针式表面轮廓仪和原子力显微镜[9](atomic force microscope,AFM)为代表。经轮廓仪探针对光学元件表面所有点扫描后,我们可得到光学元件表面的凸起与凹坑的位置、大小,划痕长度、宽度、深度等信息,由此检测出光学元件表面的微损伤。虽然AFM的检测精度可以达到纳米级,但是接触式检测法与元件表面的工作距离过短,容易造成二次损伤,并且点扫描的检测方式效率低下,检测成本过高,不适合大尺寸元件的检测。
非接触式检测方法又可以分为电子显微法、声学法、热学法和光学法[10],其中光学法又分为干涉法、衍射法和散射法。电子显微法是利用扫描电子显微镜[11](scanning electron microscope,SEM)聚焦的电子束扫描出被测光学元件表面的各种物理信号,并对这些信号进行调制成像,从而得到被测光学元件表面的形貌、成分等。电子显微法虽然能够得到表面各种凹凸不平的细微结构,但是该方法只能针对电导表面进行检测,对于非导体材料表面则需要镀金属膜,而镀膜又会进一步损坏元件表面。声学法一般使用超声检测技术[12-14],该方法是根据超声波经被测元件后特性的变化来判断被测元件的缺陷和异常。在光学元件表面存在疵病时,超声波在元件表面会产生不同的反射、折射和透射现象,通过对反馈信号的处理可以从中提取出被测表面的疵病特征。声学法需采用电传感器激励和接收超声信号,所以对被检测材料会产生影响,也容易受到外部的干扰,因此对于敏感的高精度基片已不再适用,且对表面形状的复杂性也有一定限制。热学法[15]是通过激光在光学元件表面产生的光热效应对光学元件表面的疵病进行热成像来实现缺陷检测,理论上具有对固体材料不同深度进行非破坏性检测的独特本领,然而深度信息还是不能在疵病检测标准中体现,并且这种方法对元件材料有限制,还需要严格的实验条件。
光学法[16]是非接触式检测法中最大的一类,其中的干涉法[17]是利用因微损伤产生的光程差实现对微损伤的检测,如干涉显微镜[18]、激光干涉轮廓仪[19]、白光干涉仪[20]等。干涉法的优点在于可以检测出微损伤的深度信息,但干涉条纹会在微损伤处发生断裂,解调方法复杂,横向分辨率有限,待检元件口径不宜过大。衍射法[21]是指光束正入射到表面微损伤处,在透射平面形成衍射图样,该法以衍射图样法为代表。衍射图样法光源一般采用激光或相干性较好的平行光,该法可以同时检出微损伤的种类和尺寸,但这种方法建立的微损伤形状、尺寸与衍射图样的关系不够精确,只适用于形状规则的微损伤(如圆形麻点、直线形划痕),不具通用性。
损伤属于元件表面折射率突变,当光入射到微损伤处,微损伤会对入射光的相位产生随机调制,从而产生散射,因此大多数损伤检测方法都是基于散射机理。散射检测法按照是否利用散射光对微损伤成像可以分为成像法和非成像法两类。散射法中的目视法[22]是一种最原始的非成像检测法,目前该方法仍然在国内光学元件疵病检测上广泛使用,如
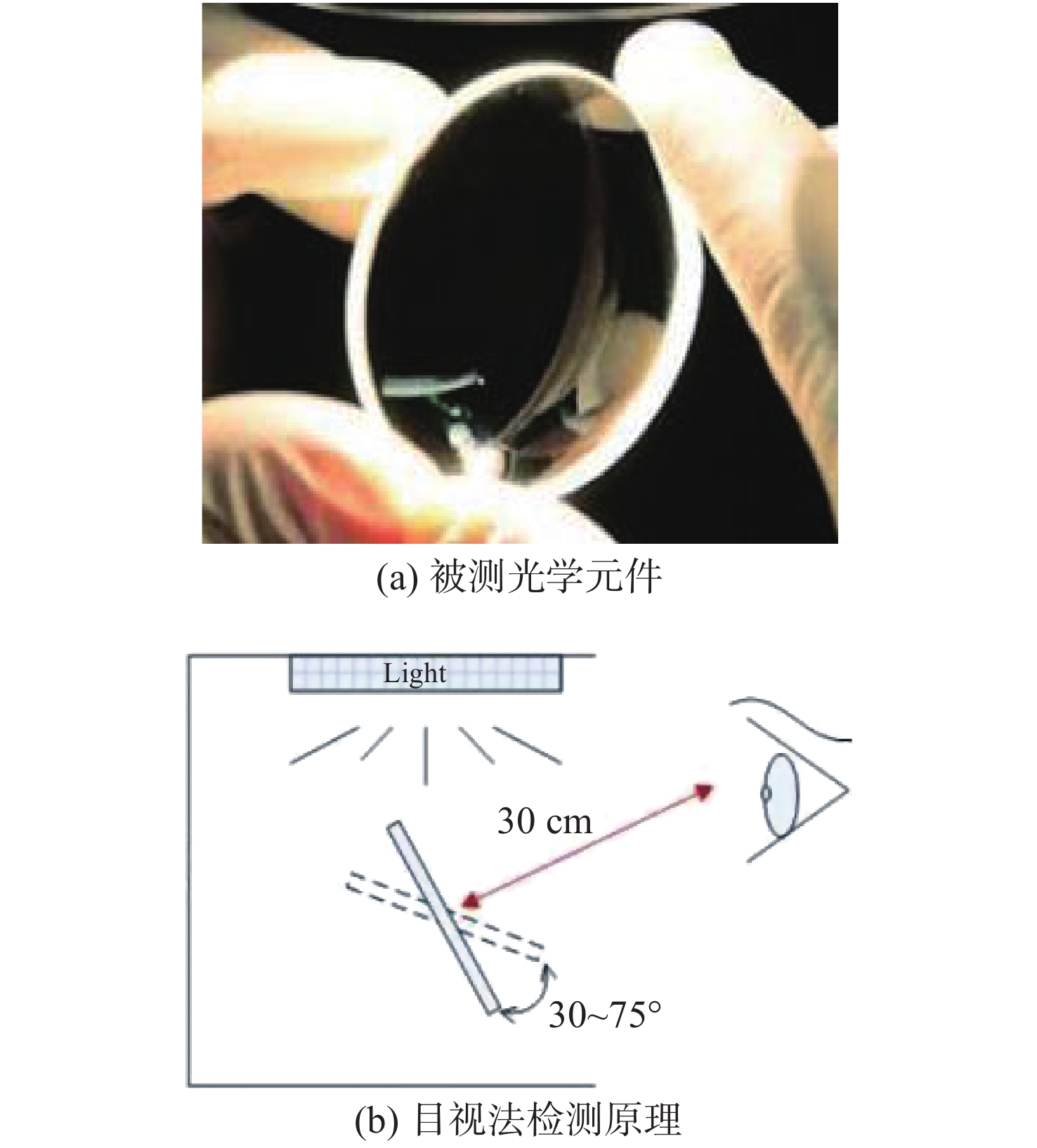
图 2. 目视法检测光学元件疵病原理
Fig. 2. Principle of optical element defect detection by visual method
散射暗场成像法[23]如
激光共焦显微检测法[24]原理如
自适应滤波成像法[25]基本原理,如
全内反射显微法[26]是一种无损的亚表面缺陷检测技术,在光学元件缺陷检测技术中该方法根据光的全内反射原理对光学元件内部缺陷进行暗场成像。全内反射显微法原理如
但是,现有的全内反射显微检测技术只能定性或半定量地表征表面缺陷,想要定量地描述各种表面缺陷还需要进一步探索。
光切断法[27]原理如
光学元件表面疵病的非成像散射测量方法有两种,一是以矢量散射理论为基础的角分辨散射测量法[28],二是以标量散射理论为基础的总积分散射测量法[29]。角分辨散射(angle resolved scattering,ARS)测量法是利用散射光的光强及其分布来测量表面粗糙度参数。该方法所采用的仪器结构复杂,成本较高。总积分散射(total integrated scattering,TIS)测量法是指入射光照射到光学元件表面后,采用积分球收集光学元件表面散射的漫反射光以及镜向反射光的总体反射光。该方法虽然成本较低,但无法获得光学表面形貌的全部特征及散射光的空间分布。并且在测量透明材料表面时,需要镀金属膜、采用匹配液等方法来降低后向散射和体散射的影响。另外,该方法对测试环境要求较高,需要在较暗、洁净度较高的环境下进行,如若存在表面脏污,则会导致测量结果产生较大误差。
在现有的疵病检测手段中,接触法一般能够得到光学元件表面的三维形貌信息,但是这在检测标准中无法呈现量化信息,而非接触法基本上得到的是二维表面缺陷的长度、面积等信息,可利用现有的检测标准准确描述疵病情况,但特征信息量较少。检测人员为了观察到极为微小的表面微损伤[30 -31],往往会增加显微镜放大倍率或提高照明光源的亮度或使用暗场照明条件,但大多只是原理性方案,目前还没有一种表面质量的检测技术可以做到对所有类型损伤实现满足行业所需精度的检测,另外由于检测视场受限,难以定量等技术障碍而无法建立高效、自动化的检测分析设备。
3 发展趋势及关键技术分析
通过对光学元件表面疵病检测标准和检测方法归纳,可以看出光学元件表面疵病标准和检测方法的发展趋势如下:
(1)疵病检测的标准是一个高度主观的可见性标准。针对不同的表面疵病,不同的国家有不同的标准,目前常用的美国军用规范仅能展示疵病信息的长度、宽度、面积等,在深度方面无法给出标准。可见,在光学元件疵病检测方面急需统一规划标准,以对疵病进行客观描述。
(2)损伤属于元件表面折射率突变,当光入射到微损伤处,微损伤会对入射光的相位产生随机调制,从而产生散射。因此,大多数损伤检测方法都是基于散射机理对微损伤检测。
(3)散射法中的成像法比其他散射法更直接、简明易懂,但无论是直接散射还是暗场散射,都需要针对不同的疵病进行不同的算法研究,需建立数据库,过程复杂。
4 结 论
本文针对表面疵病自动化检测亟待解决的关键技术,对光学元件表面疵病产生的原因、种类以及检测标准进行了介绍。重点分析了光学元件表面疵病的检测方法,指出了目前有关光学元件表面疵病检测所存在的问题。分析表明,目前还没有一种标准可以做到对所有类型疵病实现满足行业所需精度的检测,并且由于受检测仪器视场的限制以及光学元件缺陷难以定量等技术难题而无法建立高效、自动化的检测分析设备。
[1] 蔡立, 耿素杰, 付秀华. 光学零件加工技术[M]. 北京: 兵器工业出版社, 2006: 96 99.
[2] 李思, 张雨. 化学机械抛光技术发展及其应用[J]. 电子工业专用设备, 2019(5): 1-6, 20.
[3] 金寿平, 童宏伟, 张玉慧. 化学机械抛光的钛宝石晶体低损伤加工[J]. 红外与激光工程, 2019, 48(12): 1215002.
[5] 国际标准化组织. ISO 101107: 1996 Optics optical instruments. Preparation of drawings f optical elements systemsPart 7: surface imperfection tolerances[S]. 北京: 中国标准出版社, 2006.
[6] 中华人民共和国国家质量监督检验检疫总局, 中国国家标准化管理委员会. GBT 1185—2006 光学零件表面疵病[S]. 北京: 中国标准出版社, 2007.
[7] MILPRF13830B Perfmance specificationoptical components f fire control instruments: general specification governing the manufacture, assembly, inspection[S]. USA, 1997.
[8] 王丽荣. 美国军用规范MIL-PRF-13830B表面疵病要求详解[J]. 硅谷, 2012(4): 181-182, 193.
[10] 岳鹏飞, 晏永飞, 王楠. 非接触式带钢表面缺陷检测纹理方向特征分析[J]. 辽宁石油化工大学学报, 2018, 38(4): 82-86.
[11] 王秀, 张冲. 基于扫描电镜的页岩有机孔隙空间定量表征[J]. CT理论与应用研究, 2019(5): 519-527.
[12] 杨丹丹, 王健, 孙科伟. 用高分辨X射线衍射面扫描评估4H-SiC晶片结晶质量[J]. 半导体技术, 2019, 44(6): 477-482.
[13] 张广兴. 管道横向裂纹超声波检测及应用[J]. 焊接技术, 2019, 48(5): 105-108.
[14] 姬冠妮, 王亚亚, 史二娜. 激光超声检测技术的材料表面微小损伤检测[J]. 激光杂志, 2019, 40(9): 65-68.
[15] PARK H M, JOO K N. Endoscopic precise 3D surface profiler based on continuously scanning structured illumination microscopy[J]. Current Optics and Photonics, 2018, 2(2): 172-178.
[16] 李晓舟, 于化东, 于占江. 微小尺寸零件表面缺陷光学检测方法[J]. 兵工学报, 2011, 32(7): 872-877.
[17] 钟诗民, 孙方圆, 陈维杰. 马赫曾德双成像的镜面材料内部缺陷检测系统[J]. 光子学报, 2019, 48(8): 19-26.
[20] 于浩, 张志利. 衍射光学可变图像表面缺陷检测系统设计[J]. 激光杂志, 2019, 40(10): 90-94.
[22] 向弋川, 林有希, 任志英. 光学元件表面缺陷检测方法研究现状[J]. 光学仪器, 2018, 40(1): 78-87.
[24] 周建忠, 李华婷, 孙奇. 基于清洗表面形貌的AH32钢激光除锈机制[J]. 光学 精密工程, 2019, 27(8): 1754-1764.
[25] CORMACK R, JOHNSON K M, ZHANG L. Optical inspection of manufactured glass using adaptive Fourier filtering[J]. Optical Engineering, 1988, 27(5): 358.
[26] 崔辉, 刘世杰, 赵元安. 全内反射显微技术探测亚表面缺陷新方法研究[J]. 光学学报, 2014, 34(6): 0612004.
[27] 张朝生. 应用激光切割改善TRIP钢板凸缘延伸性能[J]. 上海金属, 2002, 24(6): 44.
[28] 王璐璐, 高爱华, 刘卫国. 基于LabVIEW的角分辨空间激光散射测量系统[J]. 光学与光电技术, 2018, 16(3): 40-45.
[29] 黄聪, 张科鹏, 王翔. 基于总散射测量的表面质量检测新方法[J]. 光学学报, 2019, 39(7): 0712005.
[30] LANGER G, LANGER A, BUCHEGGER B, et al. Frequency domain optical resolution photoacoustic fluescence microscopy using a modulated laser diode[C]Proceedings of SPIE 10064, Photons plus ultrasound: imaging sensing 2017. San Francisco, Califnia, United States: SPIE, 2017: 1006426.
[31] 唐如欲, 刘德安, 朱健强. 基于局部信噪比的微小损伤自适应检测技术研究[J]. 中国激光, 2018, 45(7): 0704001.
Article Outline
陆敏, 王治乐, 高萍萍, 郭继锴. 光学元件的疵病检测及现状[J]. 光学仪器, 2020, 42(3): 88. Min LU, Zhile WANG, Pingping GAO, Jikai GUO. Defect detection and current situation of optical components[J]. Optical Instruments, 2020, 42(3): 88.