自由曲面的慢刀伺服车削轨迹优化
下载: 8613次
1 引言
自由曲面光学元件与传统的球面、非球面相比具有很多优点,主要在头盔显示器[1]、望远镜[2]、空间探测[3]等光学系统中得到了广泛的应用,但由于自由曲面光学元件面形复杂,加工难度大,限制了其应用[4-7]。自由曲面光学元件常采用快刀伺服和慢刀伺服车削技术进行加工。快刀伺服车削技术具有加工精度高、效率高等特点,已经应用在微透镜阵列等自由曲面光学元件车削加工中,但由于伺服装置的行程一般小于1 mm,因此加工范围受到限制[8-10]。慢刀伺服车削技术是加工自由曲面光学元件常用的一种方法,但由于自由曲面面形复杂,需要确定合适的车削轨迹,才能有效提高自由曲面光学元件的面形精度[11-12]。关朝亮等[13]利用慢刀伺服车削技术对自由曲面面形加工的车削轨迹进行了研究,提出采用稳定X轴的刀具半径补偿方案;同样对于车削轨迹规划研究,于慧娟[14]提出等角度与等弧长组合法,采用两种方法生成的轨迹点沿着Z方向步距增量相等的点,作为组合法衔接点,研究中未对衔接点处的误差进行分析,也未考虑衔接后的车削轨迹是否满足正常加工要求,目前对这种组合车削轨迹的规划方法研究较少。本文主要针对等弧长法和等角度法组合衔接点进行研究,分析了等弧长法和等角度法生成刀具轨迹的线性化误差趋势,详细说明组合法衔接点的选取方法,使用MATLAB对其进行仿真分析,表明使用提出的衔接点生成的组合车削轨迹可以提高自由曲面的面形精度。
2 慢刀伺服车削及刀具轨迹生成
刀具轨迹生成是自由曲面单点金刚石车削加工中的关键环节,精确的刀具轨迹是保证单点金刚石车削超精密加工完成的基础[15-16]。机床的结构一般采用T型布局,如
慢刀伺服加工技术与快刀伺服加工技术相类似,但也有不同之处。快刀伺服车削技术中,刀架的控制与X轴、C轴的控制是分离的,快刀伺服系统安装在Z轴上,获取主轴C轴和X轴的位置信息并将其传输到快刀伺服系统中,Z轴根据获得的位置信息作出相应的运动。慢刀伺服车削技术中,采用X、Z、C三轴联动的方式进行加工,仅使用Z轴带动刀具作往复运动,并不采用任何附加伺服装置,因此慢刀伺服车削相对于快刀伺服车削更适用于加工大口径、矢高变化大的自由曲面。
慢刀伺服车削加工自由曲面光学元件常用确定车削点的方法有等角度法和等弧长法。等角度法是指任意相邻两切削点之间构成的圆弧所对应的圆心角是相等的,等角度法生成的车削点分布如
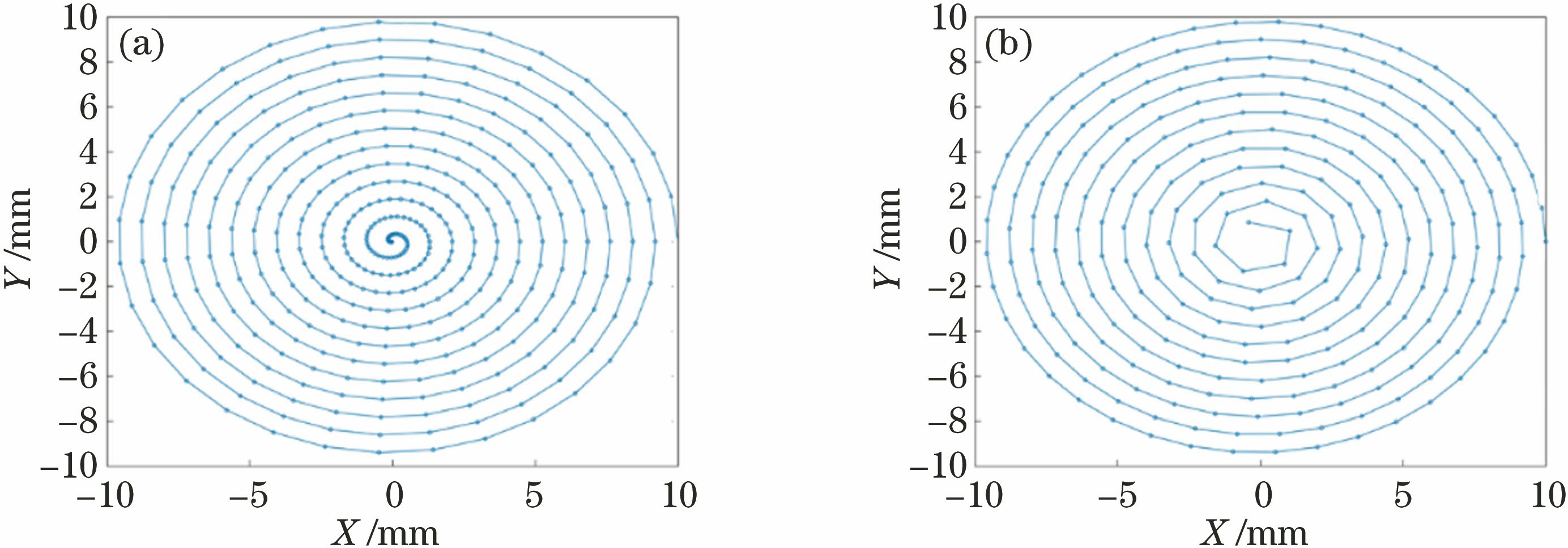
图 2. 刀具车削轨迹。(a)等角度法;(b)等弧长法
Fig. 2. Tool turning path. (a) Constant-angle method; (b) constant-arc method
曲面生成过程中,刀具在X-Y平面的车削轨迹为阿基米德螺旋线。
式中:R为工件半径;Rt为车削点到工件中心的距离;θt为车削点相对于X轴的夹角;v为刀具径向进给速度;t为车削时间。
代入切削点坐标(X,Y)可得到
3 车削轨迹规划
3.1 车削轨迹线性化误差
曲面生成已不再只是刀具路径的生成,同时也是不同车削方式优化面形精度的必要工具。传统的慢刀伺服车削过程中,自由曲面常在加工后进行评定判断,使加工表面存在不满足加工精度要求的风险,因此提出的车削线性化误差可以用来评价加工后的自由曲面是否满足要求,从而提高曲面面形精度。
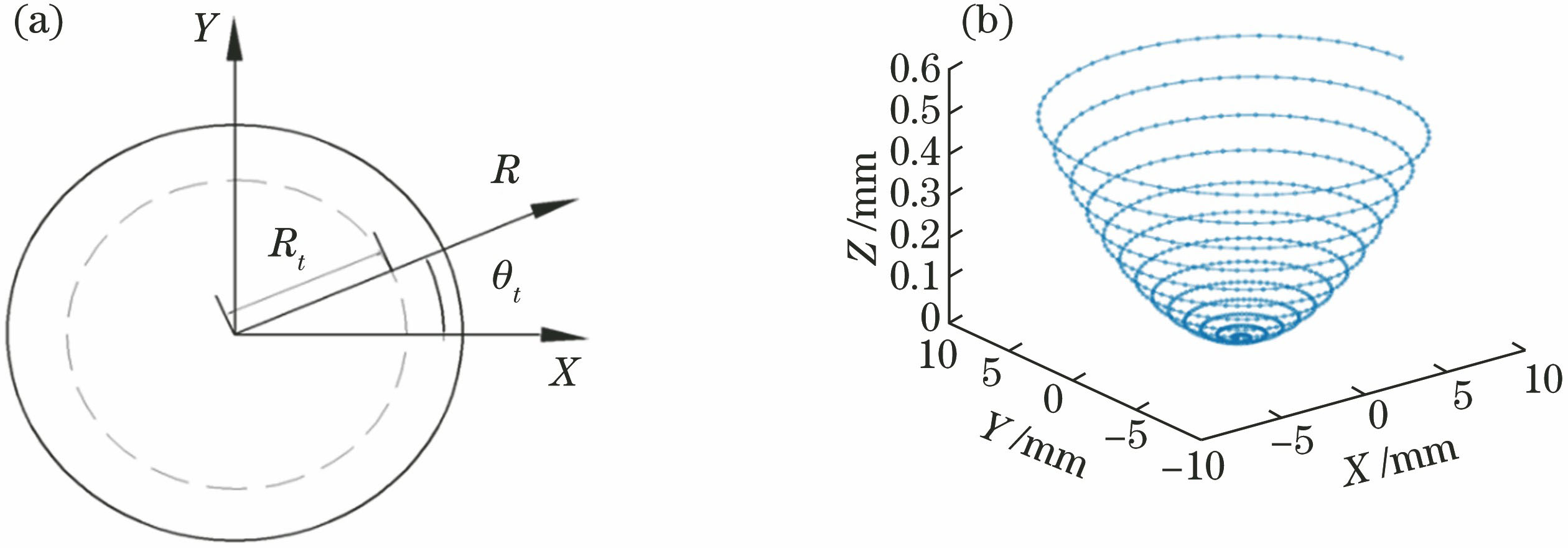
图 3. 自由曲面车削点分布。(a)车削点坐标系;(b)车削轨迹分布
Fig. 3. Cutting points distribution of freeform surface. (a) Coordinate system of cutting points; (b) cutting path distribution
理想情况下的车削轨迹是一条连续光滑的曲线,但实际情况是所有切削点连接成的一段段折线组成的车削轨迹,每相邻两个切削点近似逼近所对应的曲线,因而在实际车削轨迹与理想车削轨迹之间的偏差称为切削线性化误差,如
如
对整个螺旋车削轨迹上所有的车削点进行计算,就可以求出整个曲面的周向轮廓误差值。
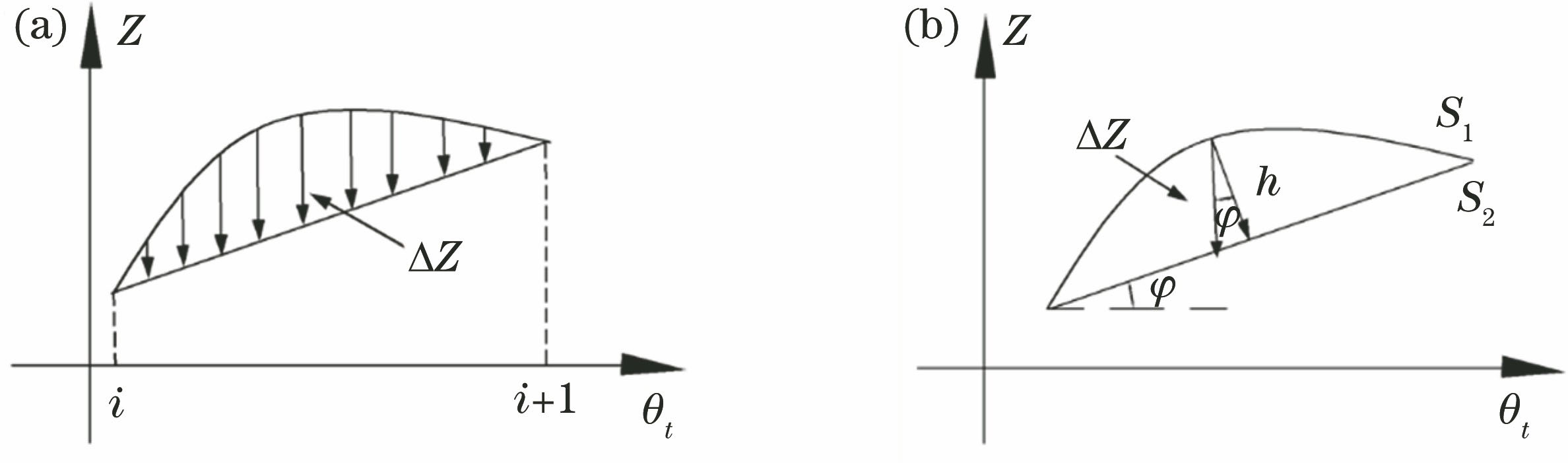
图 5. 线性化误差原理图。(a)实际车削轨迹与理想车削轨迹差值;(b)线性化误差值
Fig. 5. Schematic of linearization error. (a) Difference between the actual cutting path and the ideal cutting path;(b) linearization error value
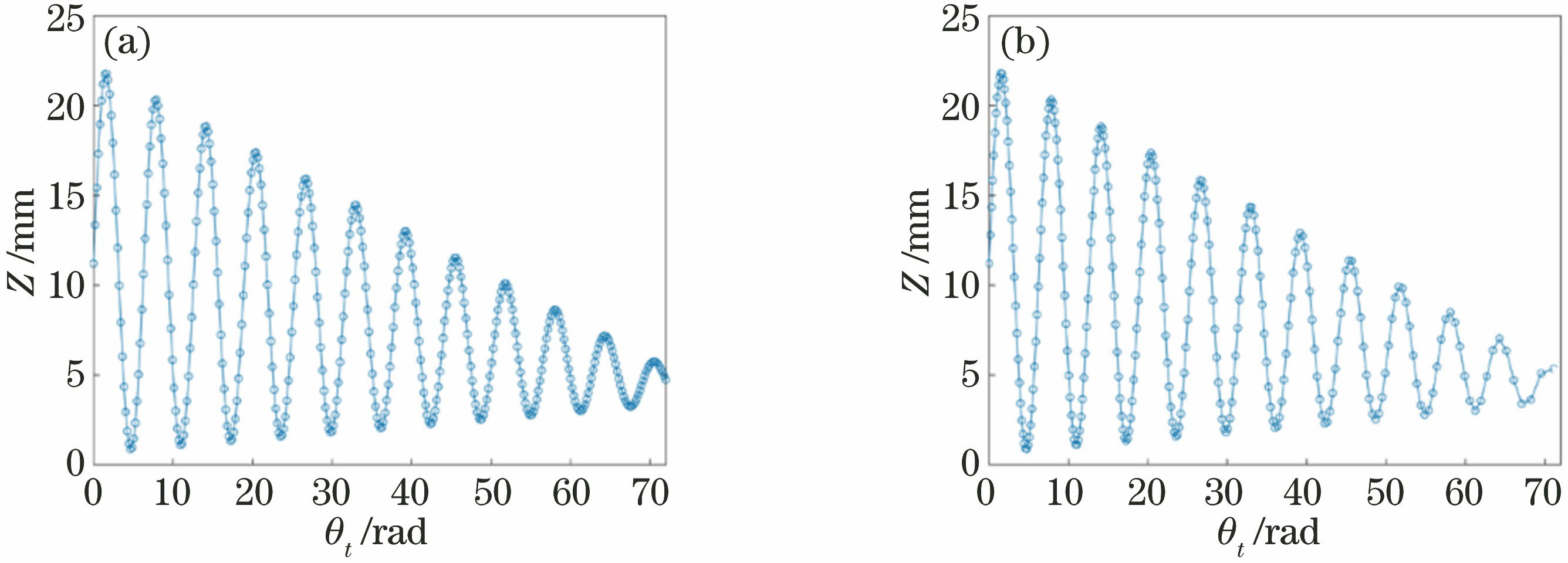
图 6. 车削轨迹展开曲线。(a)等角度法;(b)等弧长法
Fig. 6. Expansion curve of cutting path. (a) Constant-angle method; (b) constant-arc method
根据等角度法和等弧长法螺旋线上点的分布,可知等角度法生成的车削轨迹,在工件外围的加工点分布稀疏,越靠近工件中心,加工点分布越密集。因此,相邻两点之间构成的圆弧所对应的弧长在逐渐减小。等弧长法生成的车削点在工件外围均匀分布,越靠近工件中心,加工点越稀疏,相邻两点之间构成的圆弧所对应的角度逐渐增大。如
根据线性化误差计算原理可知,线性化误差的大小主要取决于车削方向上理想车削轨迹与实际车削轨迹之间的距离,两个相邻车削点的距离越小,线性化误差越小。
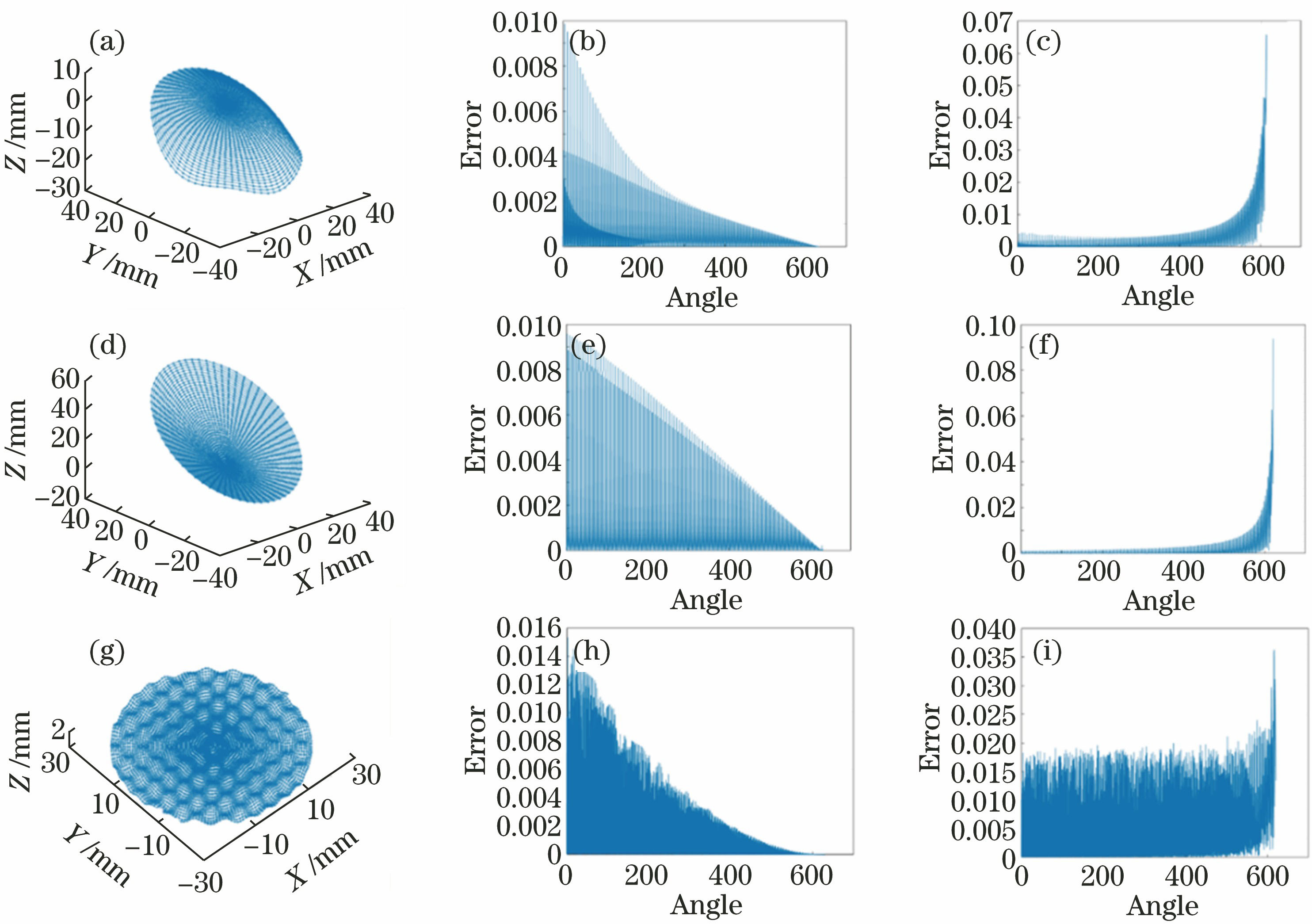
图 7. 自由曲面面形和线性化误差曲线。(a)(d)(g) XY多项式、Zernike多项式、正弦网格的面形;(b)(c) XY多项式等角度法和等弧长法线性化误差曲线;(e)(f) Zernike多项式等角度法和等弧长法线性化误差曲线;(h)(i)正弦网格等角度法和等弧长法线性化误差曲线
Fig. 7. Freeform surfaces and linearization error curves. (a)(d)(g) Surfaces of XY polynomial, Zernike polynomial, and sinusoidal grid; (b)(c) XY polynomial linearization error curves of constant-arc and constant-angle methods; (e)(f) Zernike polynomial linearization error curves of constant-arc and constant-angle methods; (h)(i) sinusoidal grid linearization error curves of constant-arc and constant-angle methods
根据上述两种方法生成车削轨迹存在的缺点,选择小角度、短弧长进行加工,以减小车削轨迹线性化误差,但等角度法的角度选择过小,工件中心部分车削点密集,在实际加工中会造成加工跳点,而采用短弧长加工,保证工件中心部分面形精度,但工件表面车削点增加,降低整体工作效率。为提高自由曲面的面形精度,提出一种车削轨迹规划的方法来避免两种方法的缺点。
3.2 车削轨迹优化
根据等角度法和等弧长法线性化误差分布的特点,采用先等弧长法、后等角度法相结合的车削方法作为新的车削轨迹,这样可以避免两种方法因车削点分布不均匀造成的局部误差偏大的缺点。但生成的车削轨迹是连续的螺旋线,所以确定轨迹衔接点的位置是新的车削轨迹优化法的关键。目前,提出的车削轨迹组合优化法衔接点的选取存在一定的局限性。
由于等角度法和等弧长法生成车削点的位置分布不同,衔接点的选取需要保持原始的等距螺旋轨迹不变,同时又能满足正常加工。因此采用选择满足上述两种车削轨迹在相同角度内误差的差值最小且衔接后整体的线性化误差最小的点作为衔接点。该方法是在原始等角度和等弧长产生的等距螺旋线的基础上,分别计算两者的线性化误差值,根据上述获得的规律,将等距螺旋线以车削角度展开为二维曲线并进行多项式拟合,确定拟合曲线的交叉位置,即组合法的衔接点。取此位置之前对应的等弧长法螺旋线和此位置之后对应的等角度法螺旋线进行组合,生成新的车削轨迹。
利用MATLAB进行计算,用等角度法生成车削点的线性化误差值依次减去等弧长法生成车削点的线性化误差值,选择相同角度内误差差值最小值对应的车削轨迹的车削点作为两种方法误差的转换点。设待加工自由曲面Z=f(X,Y),误差差值最小点Ez
式中:Edeg(θt)为等角度法线性化误差点;Earc(θt)为等弧长法线性化误差点;Ez(θt)为等角度法与等弧长法线性化误差的差值。
由于自由曲面的面形变化不规则,因此相同角度内的线性化误差差值最小点会有多个重复值,无法找到满足条件的唯一衔接点。如
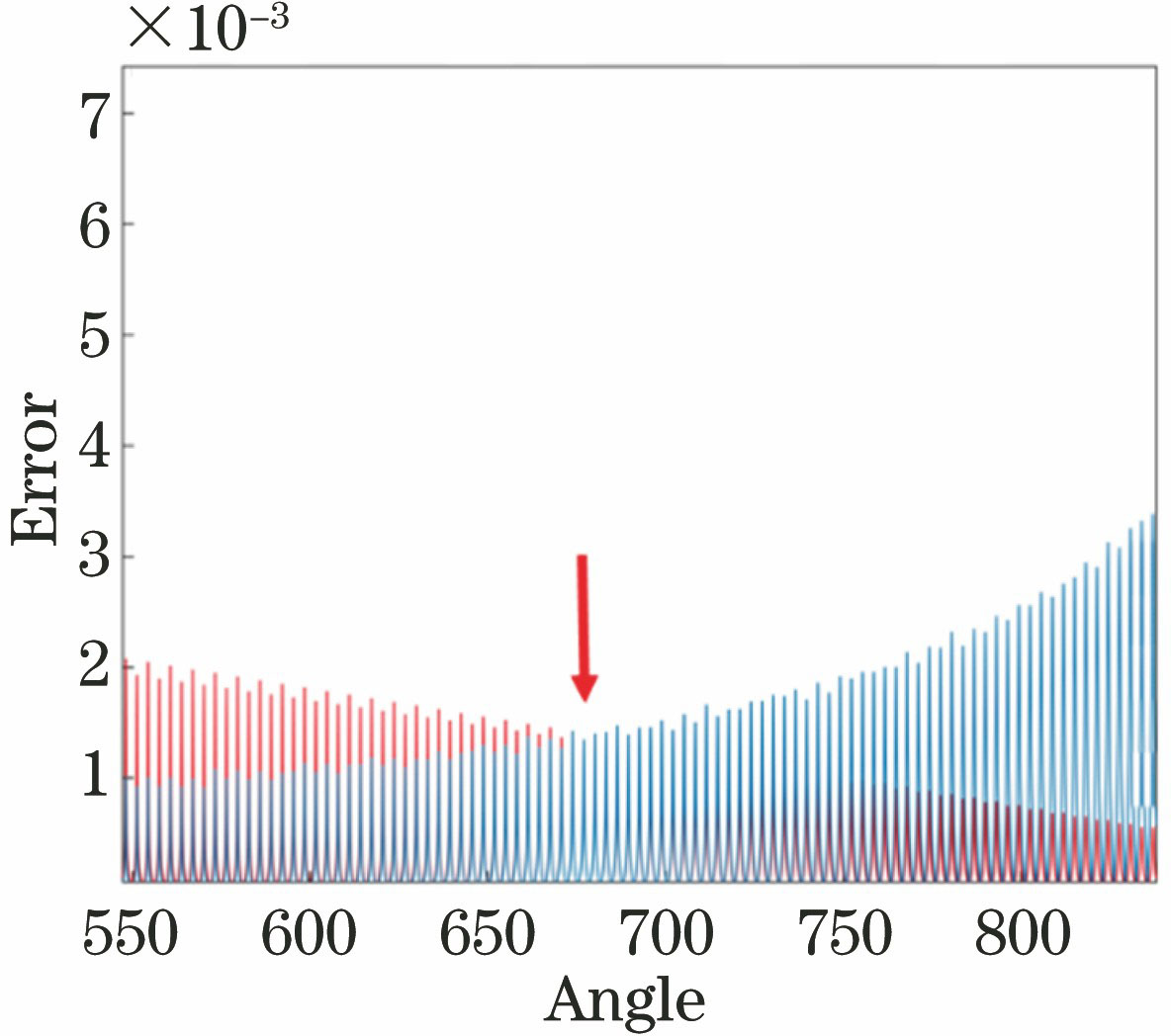
图 8. 等弧长法和等角度法线性化误差曲线
Fig. 8. Linearization error curves of constant-arc and constant-angle methods
根据3.1节计算等弧长法和等角度法的线性化误差值,利用MATLAB软件进行多项式拟合,拟合后的等弧长法线性化误差曲线和等角度法线性化误差曲线分别为一条光滑曲线,且分别与原始的线性化误差曲线变化趋势一致,所以将两条曲线的交点作为新的车削轨迹的衔接点,即在相同角度内误差的差值最小且衔接后整体的线性化误差最小的点作为衔接点。如
4 仿真实例
为了验证所提出的车削轨迹规划方法,以正弦网格曲面为例,采用以下参数在MATLAB中进行仿真:待加工工件半径R=30 mm,主轴转速N=100 r/min,X轴向进给速度v=6 mm/min,等角度法采用的角度为2°,等弧长法采用的弧长为0.3 mm。
车削轨迹优化效果如
表 1. 不同车削轨迹对应正弦网格曲面的最大线性化误差
Table 1. Maximum linearization errors of sinusoidalgrid surface for different tool paths
|
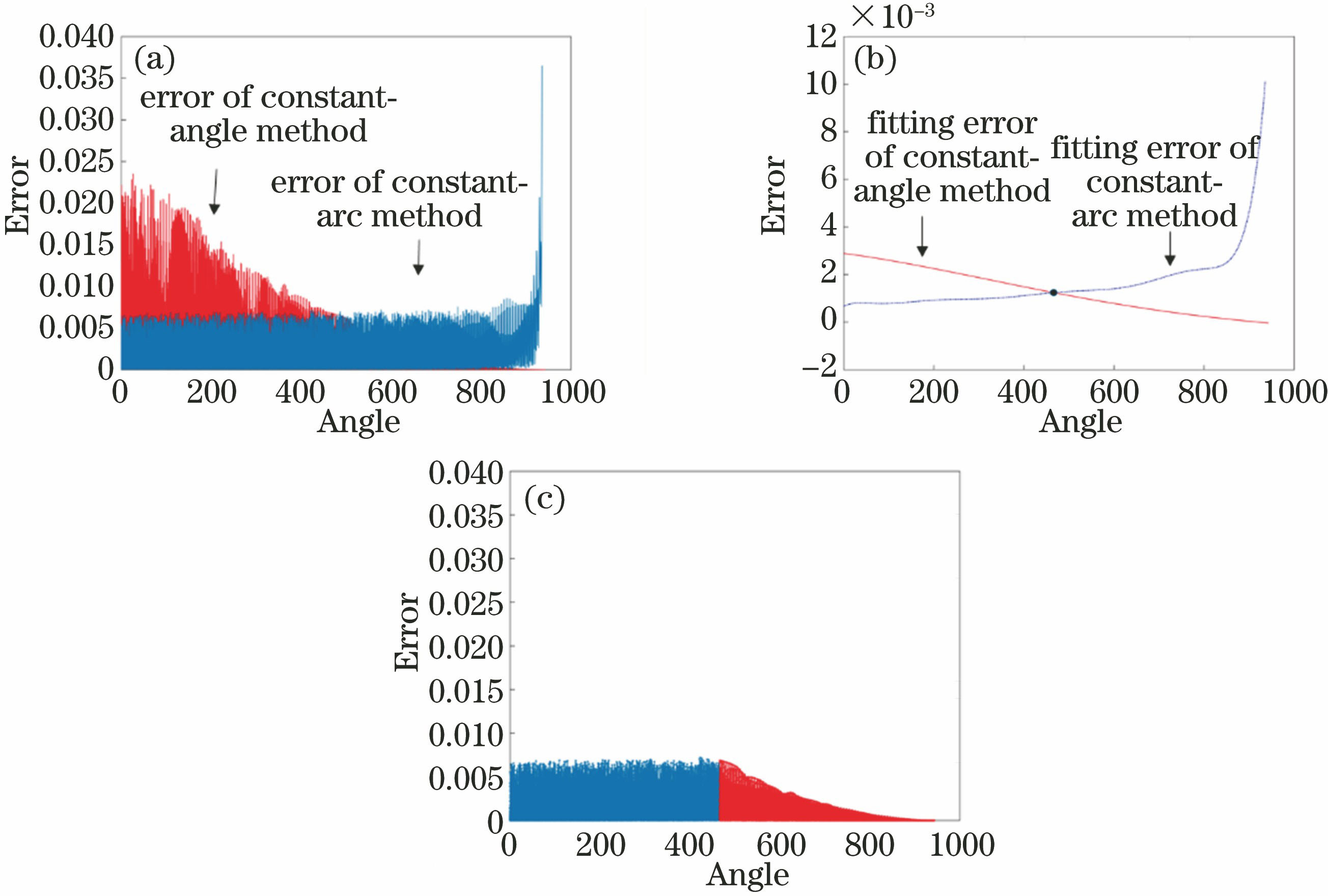
图 10. 线性化误差曲线。(a)等弧长法和等角度法;(b)拟合后误差曲线;(c)组合后误差曲线
Fig. 10. Linearization error curves. (a) Constant-arc and constant-angle methods; (b) fitting error curves; (c) error curves of the combination method
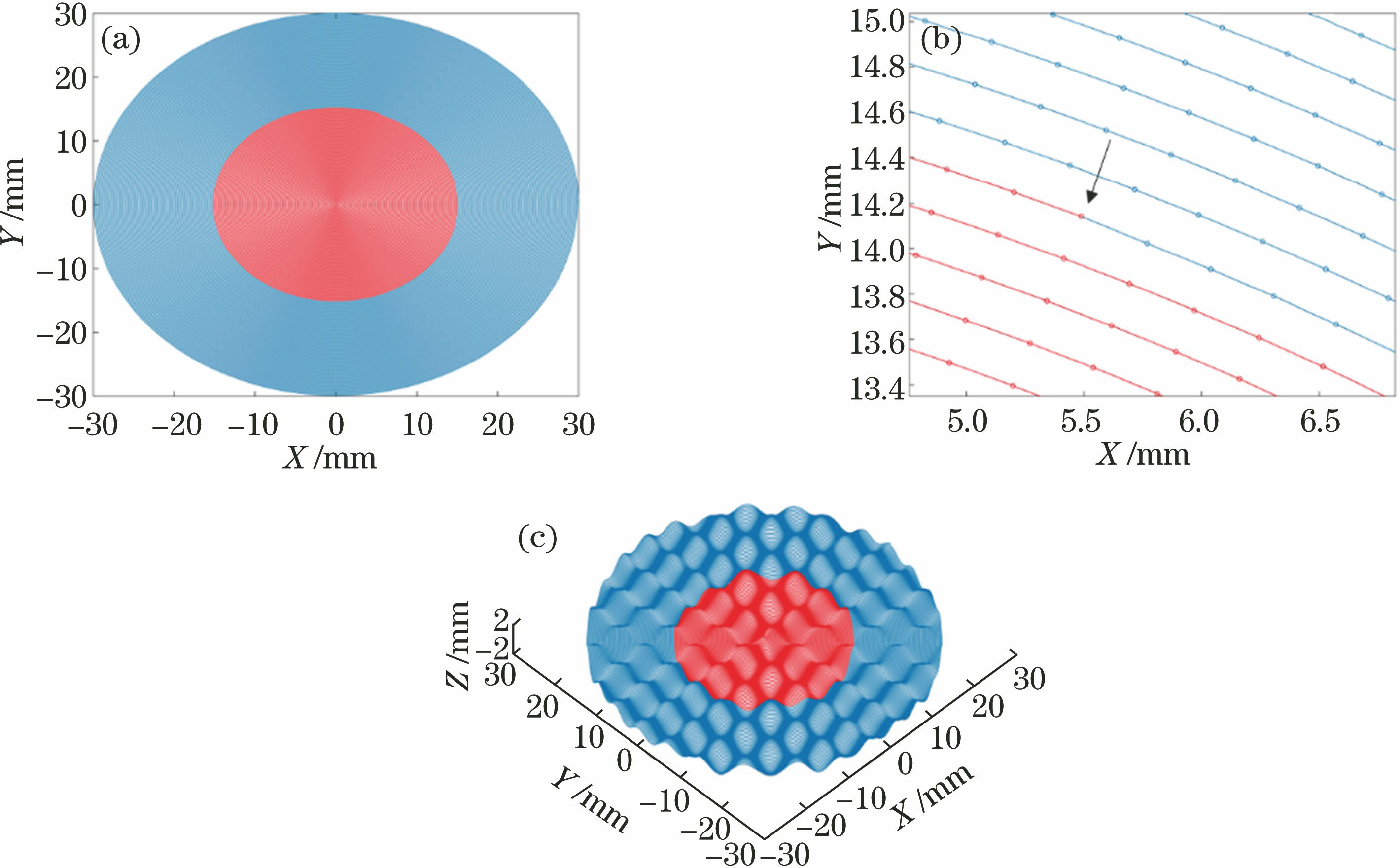
图 11. 车削轨迹优化效果图。(a) X-Y平面车削轨迹优化;(b)车削轨迹局部放大图;(c)正弦网格曲面车削轨迹优化
Fig. 11. Optimization effect of tool path generation. (a) Tool path optimization of X-Y plane; (b) partial enlargement of the tool path; (c) tool path optimization of sinusoidal grid surface
5 结论
在介绍慢刀伺服切削原理及车削轨迹生成过程的基础上,根据等角度法和等弧长法车削点的分布特点可知,等角度法中随着车削角度的增加,整个待加工曲面的线性化误差逐渐减小,而等弧长法中待加工曲面的线性化误差变化趋势正好相反。因此提出了一种先等弧长法、后等角度法组合的车削轨迹优化方法。该方法针对衔接点的选取,通过多项式拟合等弧长法和等角度法线性化误差曲线,选取拟合曲线的交点作为两种方法的衔接点。仿真结果表明,组合后的车削轨迹线性化误差的最大值比两种方法的线性化误差最大值降低30%。与传统的方法相比,提出的组合优化车削轨迹能够提高待加工自由曲面的面形精度,对大口径、矢高大的自由曲面加工具有重要意义。
[1] 叶井飞, 徐凯迪, 杨明珠, 等. 基于自由曲面的离轴两反头戴显示光学系统设计[J]. 光学学报, 2018, 38(7): 0722003.
[2] 关姝, 王超, 佟首峰, 等. 空间激光通信离轴两镜反射望远镜自由曲面光学天线设计[J]. 红外与激光工程, 2017, 46(12): 1222003.
[3] 倪栋伟, 李旭阳, 杨明洋, 等. 基于自由曲面的大视场天基探测光学系统[J]. 光学学报, 2018, 38(11): 1122003.
[5] Fang F Z, Zhang X D, Hu X T. Cylindrical coordinate machining of optical freeform surfaces[J]. Optics Express, 2008, 16(10): 7323-7329.
[6] Kenneth G, Bruegge T, Hoffman J, et al. Design tools for freeform optics[J]. Proceedings of SPIE, 2005, 5874: 58740A.
[7] 徐恺, 贾志刚, 房丰洲. 人眼实际观察状态下的自由曲面眼镜片的透射波前像差测量[J]. 光学学报, 2018, 38(2): 0212001.
[8] Zhu L L, Li Z X, Fang F Z, et al. Review on fast tool servo machining of optical freeform surfaces[J]. The International Journal of Advanced Manufacturing Technology, 2018, 95: 2071-2092.
[9] Yu D P, Wong Y S, Hong G S. Optimal selection of machining parameters for fast tool servo diamond turning[J]. The International Journal of Advanced Manufacturing Technology, 2011, 57: 85-99.
[10] Kim H S, Kim E J, Song B S. Diamond turning of large off-axis aspheric mirrors using a fast tool servo with on-machine measurement[J]. Journal of Materials Processing Technology, 2004, 146(3): 349-355.
[11] Wu Q H, Sun Y Z, Chen W Q, et al. Theoretical and experimental investigation of spindle axial drift and its effect on surface topography in ultra-precision diamond turning[J]. International Journal of Machine Tools and Manufacture, 2017, 116: 107-113.
[12] 李荣彬, 张志辉, 杜雪, 等. 自由曲面光学的超精密加工技术及其应用[J]. 红外与激光工程, 2010, 39(1): 110-115.
Li R B, Zhang Z H, Du X, et al. Ultra-precision machining technology of freeform optics and its applications[J]. Infrared and Laser Engineering, 2010, 39(1): 110-115.
[13] 关朝亮, 戴一帆, 尹自强. 自由曲面光学元件的慢刀伺服车削加工技术[J]. 激光与光电子学进展, 2010, 47(2): 022202.
[14] 于慧娟. 光学自由曲面单点金刚石超精密车削理论与技术研究[D]. 长春: 吉林大学, 2015: 19- 30.
Yu HJ. Theoretical and technological research on optical freeform surface of single point diamond ultra-precision turning[D]. Changchun: Jilin University, 2015: 19- 30.
[15] 关朝亮, 铁贵鹏, 尹自强. 光学阵列器件的慢刀伺服车削加工技术[J]. 国防科技大学学报, 2009, 31(4): 31-35, 47.
Guan C L, Tie G P, Yin Z Q. Fabrication of array lens optical component by using of slow tool servo diamond turning[J]. Journal of National University of Defense Technology, 2009, 31(4): 31-35, 47.
[16] Yin ZQ, Dai YF, Li SY, et al. and Manufacture, 2011, 51(5): 404-410. n
Article Outline
张琦, 薛常喜. 自由曲面的慢刀伺服车削轨迹优化[J]. 激光与光电子学进展, 2020, 57(5): 052203. Qi Zhang, Changxi Xue. Optimization of Tool Path Generation for Freeform Surface by Slow Tool Servo Diamond Turning[J]. Laser & Optoelectronics Progress, 2020, 57(5): 052203.