基于热力耦合的激光熔覆数值模拟与实验研究
下载: 1608次
1 引言
在建设资源节约型和环境友好型社会,发展循环经济的大背景下,开发再制造技术将产生巨大的经济效益和社会效益[1-2]。作为再制造修复的一种常见加工技术,激光熔覆利用高能激光束辐照熔覆粉末颗粒与基体材料,使粉末颗粒完全熔化、基体材料表面微熔、冷凝后二者形成冶金结合整体,从而有效改善基体材料的耐磨、耐腐蚀及耐疲劳等性能,具有热影响区小、冶金结合良好、熔覆层组织致密等优点[3]。在激光熔覆过程中,材料的升温速度和熔池的冷凝速度极快,所产生的温度场和应力场与熔覆层裂纹敏感性存在着密切联系,高能激光束作为能量来源,其工艺参数对温度场和应力场具有重要影响[4-8]。
国内外学者针对激光熔覆过程数值模拟和激光工艺参数影响规律进行了相关研究,取得了一定的研究成果。Mirzade等[9]通过研究同轴送粉激光熔覆的数值模型,发现影响熔池动力学和温度的主要参数为激光功率、扫描速度和送粉速率。李豪等[10]通过建立基于椭圆热源的三维瞬态激光熔覆有限元模型,研究了温度场和流场的特征,发现温度场具有后拖现象,流体速度矢量在熔池中部主要分布于纵向截面内。刘昊等[11]针对送粉式激光熔覆,建立了计算瞬态温度场及熔覆层几何形貌的三维数值模型,通过不同送粉速率的熔覆实验,验证了模型的有效性。综合已有文献可看出,通过有限元方法能够实现对激光熔覆过程的有效模拟,特别是在熔覆过程中瞬态温度场的特征方面,有了较多的研究成果,但针对不同激光工艺参数下激光熔覆温度场和应力场分布规律及对薄板类熔覆件变形影响的研究相对较少。
为探索激光工艺参数影响规律,提高熔覆质量,本文在研究激光熔覆基本原理的基础上,基于有限元分析的生死单元技术,利用ANSYS参数化设计语言(APDL)建立了单道激光熔覆的热传导模型,在温度场的基础上,通过单元转换,把热分析模型转换为结构分析模型,得到激光熔覆的应力场,通过对6组不同的激光工艺参数进行数值模拟和熔覆实验,探索了激光功率和扫描速度对温度场和应力场分布规律的影响,为减小薄板类熔覆件的变形提供理论依据。
2 激光熔覆基本原理
激光熔覆作为一种利用高能激光束熔化合金粉末及基体表层并使二者形成良好冶金结合的先进表面加工技术,是一个强非线性多物理场耦合的过程,具有熔池小、热量高、变化快的特点,很难得到温度、应力和组织等场量的解析结果,采用有限元软件建立模型对激光熔覆过程进行数值模拟,是研究激光熔覆机理和优选工艺参数的有效途径[12-15]。
3 数值模拟与结果分析
3.1 有限元模型的建立
利用ANSYS有限元软件对单道激光熔覆的温度场和应力场进行数值模拟,基本思路为:1) 在激光熔覆过程的某个时刻,激光辐照集中在基体表面一个较小区域,形成熔池;2) 熔池的高温经过热传导作用传递给基体材料,改变基体的温度分布,形成不均匀的温度场,从而产生一定的温度梯度,并且随着激光辐照区域的移动而发生动态改变;3) 在温度梯度的作用下,材料发生膨胀或收缩,且熔覆层和基体作为两种不同的材料而具有不同的线膨胀系数,从而导致模型原始位置的每个节点发生不同方向和大小的位移,即材料发生不同方向和程度的膨胀或收缩,于是形成了不同程度的热应变;4) 考虑到熔覆层和基体材料的弹性模量、屈服强度、切变模量和泊松比等力学参数一般不同,从而会产生一定的热应力,最终表现为位移云图上的结构形变和应力云图上的残余应力。
考虑激光熔覆实际过程中各种影响因素相互作用和多物理场耦合的复杂性,需要在一定程度上对有限元模型进行合理简化:1) 忽略激光传播过程中反射、折射等物理现象的影响,激光吸收率不随温度变化;2) 假设粉末和基体材料吸收的有效能量全部用于升温,温度场只受激光功率与热物性参数影响;3) 忽略熔池中液体的流动和表面张力,将流体视为屈服应力极低的固体[16];4) 假设环境状态稳定且材料各向同性[17];5)忽略粉末和基体材料在熔化过程中因元素扩散导致的物理化学性质改变的影响[14]。
针对三维温度场数值模拟计算,ANSYS有多种热分析单元,其中三维8节点6面体单元比较适合在空间和时间上因激光能量辐照导致的温度剧烈变化情况,具有较高的精度。模型选择SOLID70单元类型,具有8个节点,每个节点包含1个自由度温度,可以输出节点温度、温度变化分量等,适用于瞬态和稳态的热分析,可实现匀速热流的传递,并且能够转换为SOLID45结构单元进行残余应力分析。
模型的基体材料为316L不锈钢,熔覆粉末选用钴基合金。使用ANSYS进行数值模拟时,需给定材料的热学和力学参数,主要包括:材料密度、比热容、考虑熔池对流的热传导系数、考虑辐射和对流的总换热系数、弹性模量、屈服强度、切变模量、线膨胀系数和泊松比等[18]。其中,除了泊松比不随温度变化之外,其余参数均随温度的改变有不同取值,对于部分超出材料手册温度范围的高温数据,可参考已有数据通过插值外推法获取,见参考文献[ 18]。
模型中基体的尺寸为200 mm×30 mm×4 mm(长×宽×高)。在模型的长度方向上进行单道激光熔覆,根据前期实验积累的数据资料,设置熔覆层横截面的形状如
在网格划分时,为保证计算精度,同时兼顾计算效率,对熔覆层及其相邻部位的网格进行了细化,而距离熔覆区域较远的部位则选用了较粗的网格进行划分[20]。有限元模型局部网格划分结果以及模型的笛卡尔坐标系如
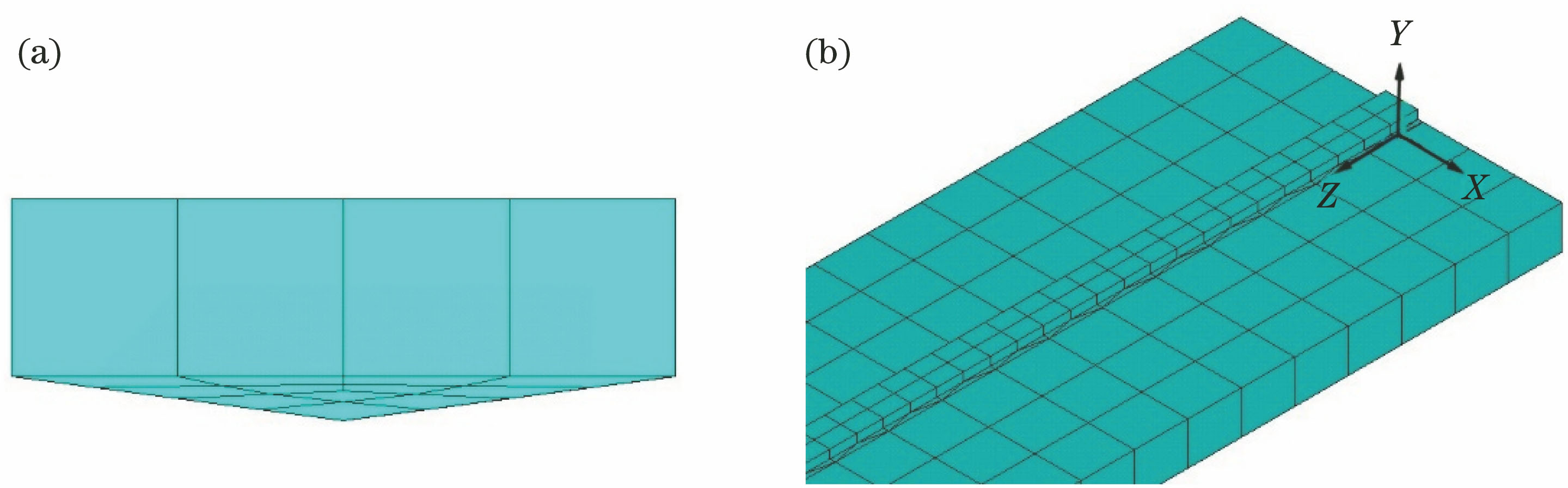
图 1. 熔覆层横截面和网格划分。(a)熔覆层横截面;(b)网格划分
Fig. 1. Cross section of cladding layer and meshing. (a) Cross section of cladding layer; (b) meshing
采用生死单元技术[21],在开始加载热源进行计算之前,将所有熔覆层单元均设定为“死”单元,然后根据时间参数和载荷步的向前推进,通过
对于热源模型,通过运用透射式光束积分镜并且辅助适当刻面,能够将激光器输出的基模高斯光束转换为宽带激光光束,其光斑形状为狭长的长方形,功率密度分布均匀,可显著提高加工效率[22]。近年来,随着大功率半导体激光器的发展,矩形光斑也越来越多地应用于激光制造过程中,而且由于模型采用了同轴送粉的方式,金属粉末在到达基体上时已处于熔融状态,所以选择以体积生热的方式来模拟激光能量的输入,生热率计算公式为
式中
有限元模型的初始条件和边界条件主要体现在温度和力两个方面[23]。对于温度场,考虑初始温度和换热系数。在模型进行激光熔覆之前,通过进行一次稳态分析,可将模型所有单元的初始温度设为室温(25 ℃)。换热方式主要有对流换热和辐射换热,其中在熔池附近区域会有均103 ℃的高温,此时模型主要以辐射的方式与周围环境进行热交换,因此换热系数会随着温度的改变而变化。考虑对流换热和辐射效应对温度场的影响,以更好地反映真实环境中的传热现象,将辐射效应转换成随温度变化的对流换热系数,得到一个综合考虑辐射和对流的总换热系数,总换热系数随温度的变化有不同的取值[24](
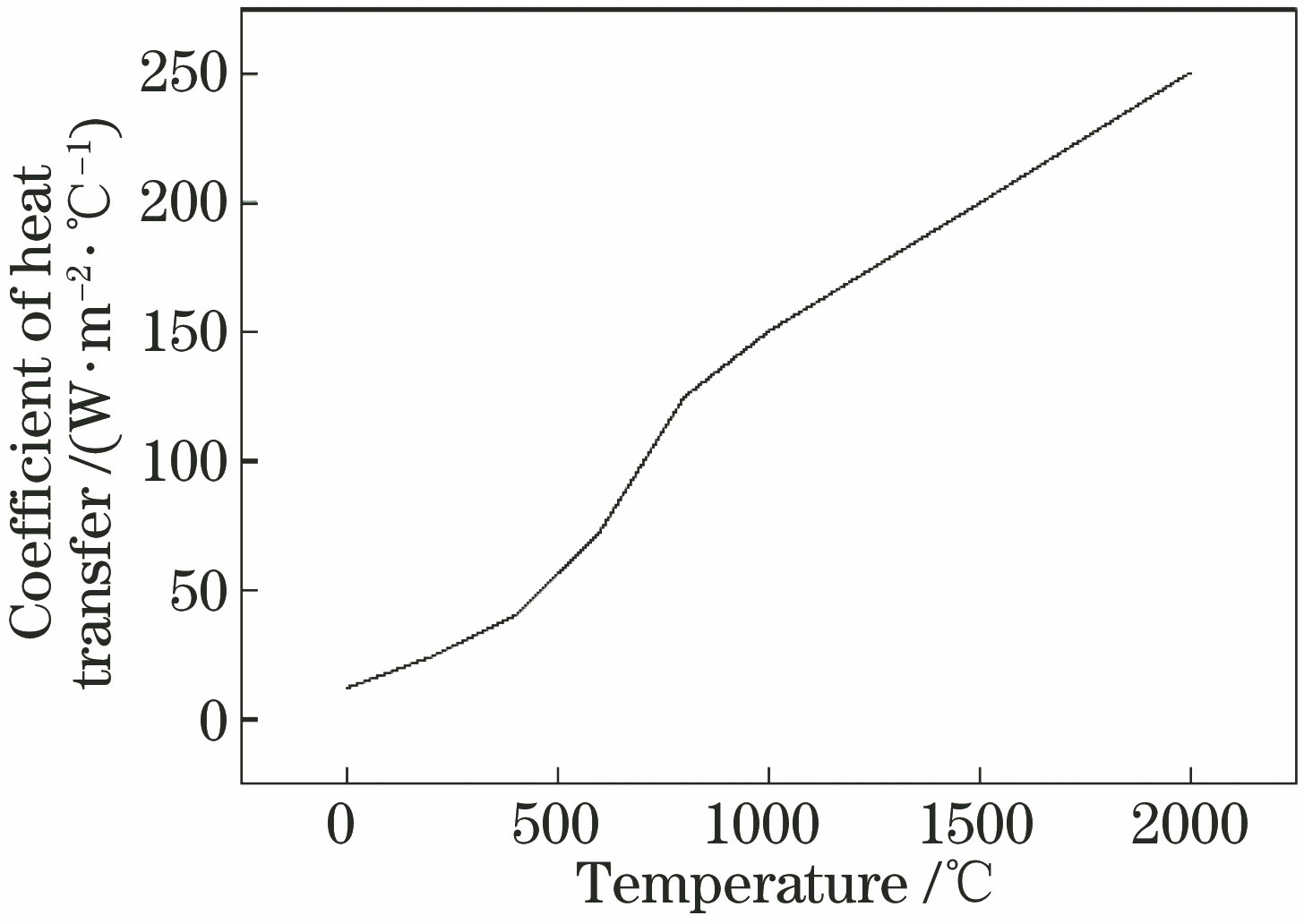
图 2. 总换热系数随温度的变化曲线
Fig. 2. Comprehensive coefficient of heat transfer varing with temperature
采用热-结构间接耦合非线性有限元分析方法对温度场与应力场进行数值模拟,即先建立单道激光熔覆的热传导模型,得到模型的温度场,然后在此基础上,通过单元转换,把热分析模型转换为结构分析模型,得到激光熔覆的应力场。在应力场计算中,通过激活牛顿-拉普森方法线性搜索选项,以得到较好的收敛解。
3.2 模型可行性分析
以激光功率2800 W,扫描速度10 mm/s,光斑直径3 mm为例,对网格划分进行无关性分析。通过数值模拟得到几组不同网格划分情况下初始时刻温度场的最高温度,见
表 1. 不同网格划分下模型温度场的最高温度
Table 1. The maximum temperature of model temperature field under different meshes
|
由
根据几何特性,将熔覆层横截面划分为[26]熔覆区(CZ)、基体熔化区(MZ)、热影响区(HAZ)和基体(SZ),如
同样以激光功率2800 W、扫描速度10 mm/s、光斑直径3 mm为例,通过数值模拟得到温度场,与相同工艺参数下激光熔覆实验试件金相组织形貌进行对比,如
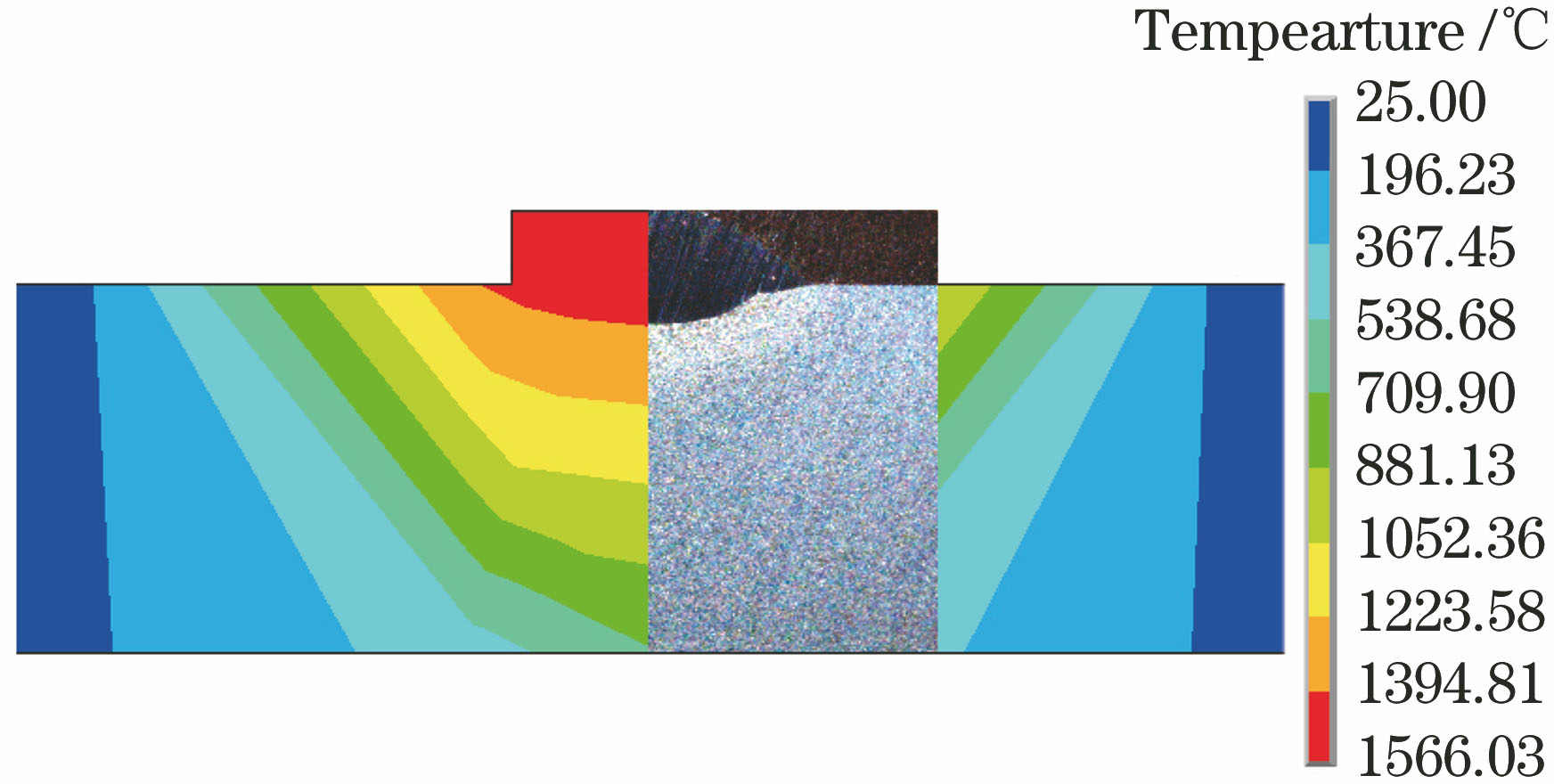
图 4. 温度场与试件金相组织形貌对比
Fig. 4. Comparison between temperature field and metallographic structure of test piece
对于试件金相组织,在体式显微镜下测得
3.3 温度场分析
数值模拟得到激光熔覆温度场,如
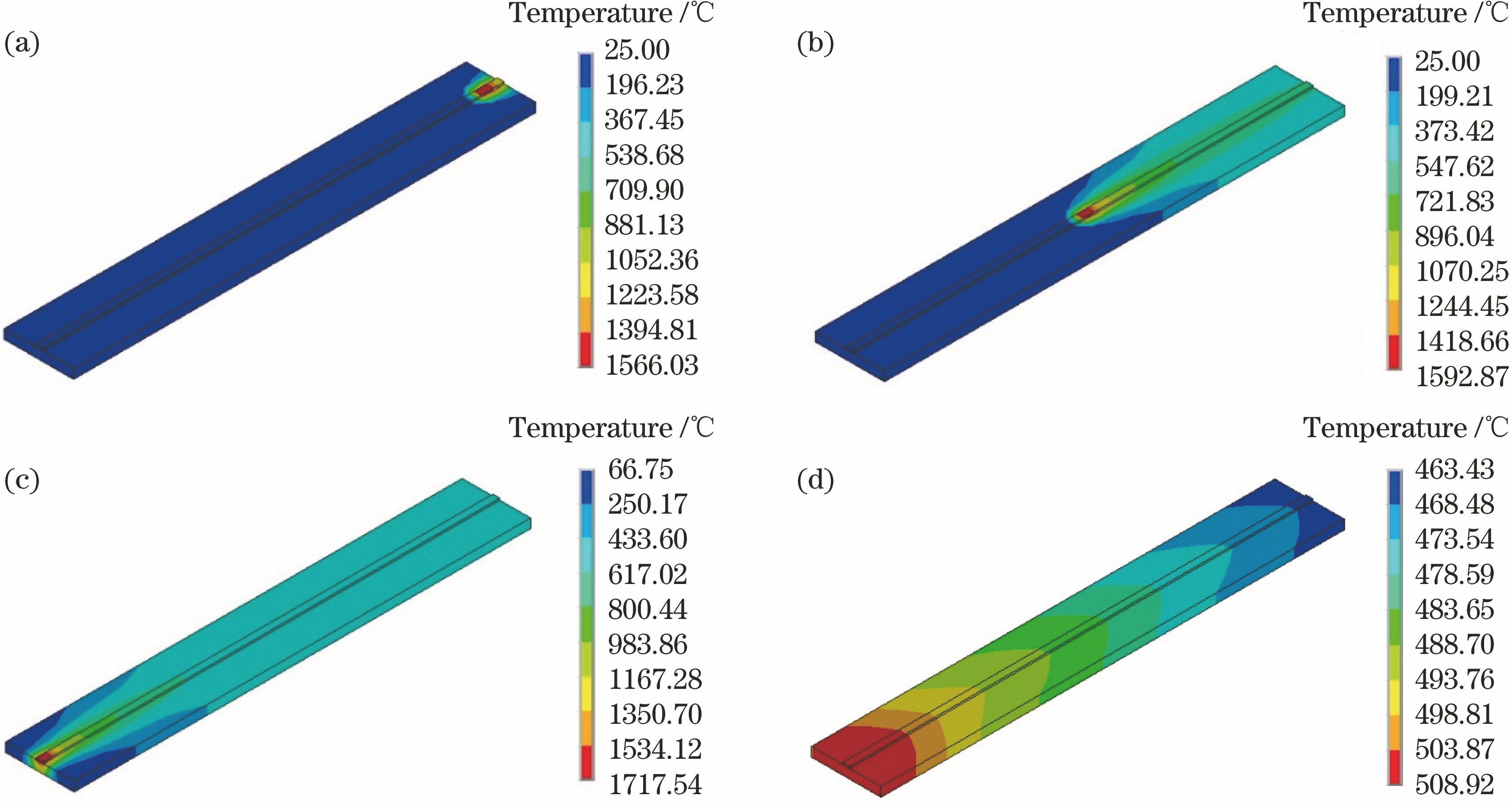
图 5. 激光熔覆温度场。(a)初始;(b)中间;(c)终点;(d)冷却20 s
Fig. 5. Temperature fields of laser cladding. (a) Initial; (b) middle; (c) final; (d) cooling after 20 s
在熔覆层表面中间位置沿
由
3.4 应力场分析
在移动式激光辐照作用下,熔覆件形成动态的温度梯度,不同温度区域具有不同的膨胀程度,形成残余应力[23]。根据基于第四强度理论的Von Mises准则,当材料应力大于其屈服强度时,会发生塑性变形以释放部分应力,导致翘曲变形,降低结构刚性和尺寸稳定性[27]。温度场分析之后,进行单元转换,在模型左端施加约束作为固定端,读入热分析结果作为应力场的分析载荷,求解得到Von Mises应力云图和位移云图,如
由
在模型上设置3条路径:路径1选取熔覆层与基体结合面的中间位置,沿着
由

图 7. Von Mises应力云图和位移云图。(a) Von Mises应力;(b)位移
Fig. 7. Von Mises stress nephogram and displacement nephogram. (a) Von Mises stress; (b) displacement
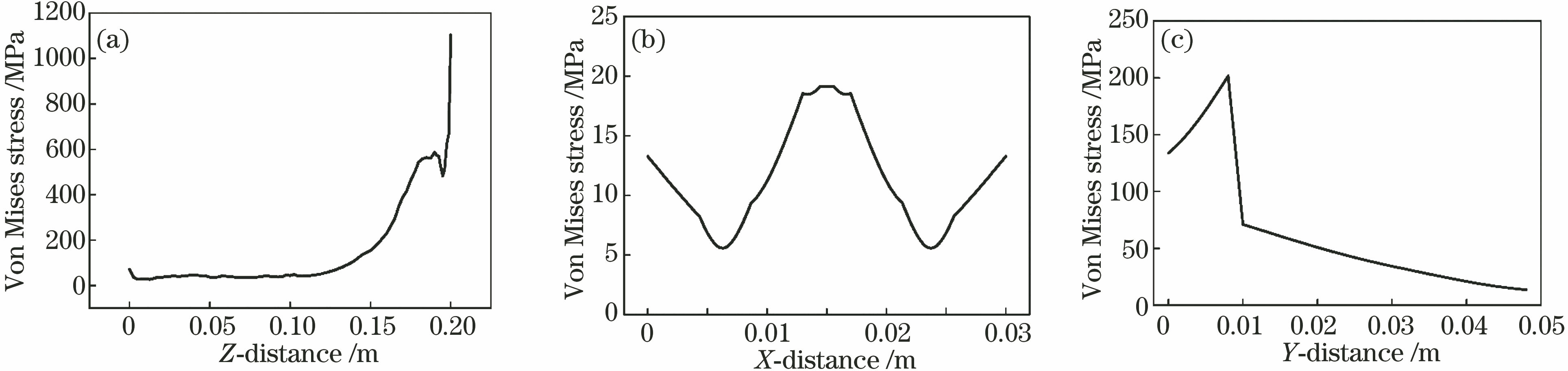
图 8. 不同路径的应力分布曲线。(a)熔覆层与基体结合面中部沿Z轴方向;(b)基底中部沿X轴方向;(c)自由端中部沿Y轴方向
Fig. 8. Stress distribution curves along different paths. (a) Along the Z axis in the middle of the bonding surface of the cladding layer and the matrix; (b) along the X axis in the middle of the matrix undersurface; (c) along the Y axis in the middle of the free end
4 激光工艺参数影响规律分析
在一定范围内选取不同的激光功率和扫描速度,得到6组激光工艺参数组合,记为A、B、C、D、E和F,如
表 2. 激光工艺参数分组和计算结果
Table 2. Grouping and calculation results of laser process parameters
|
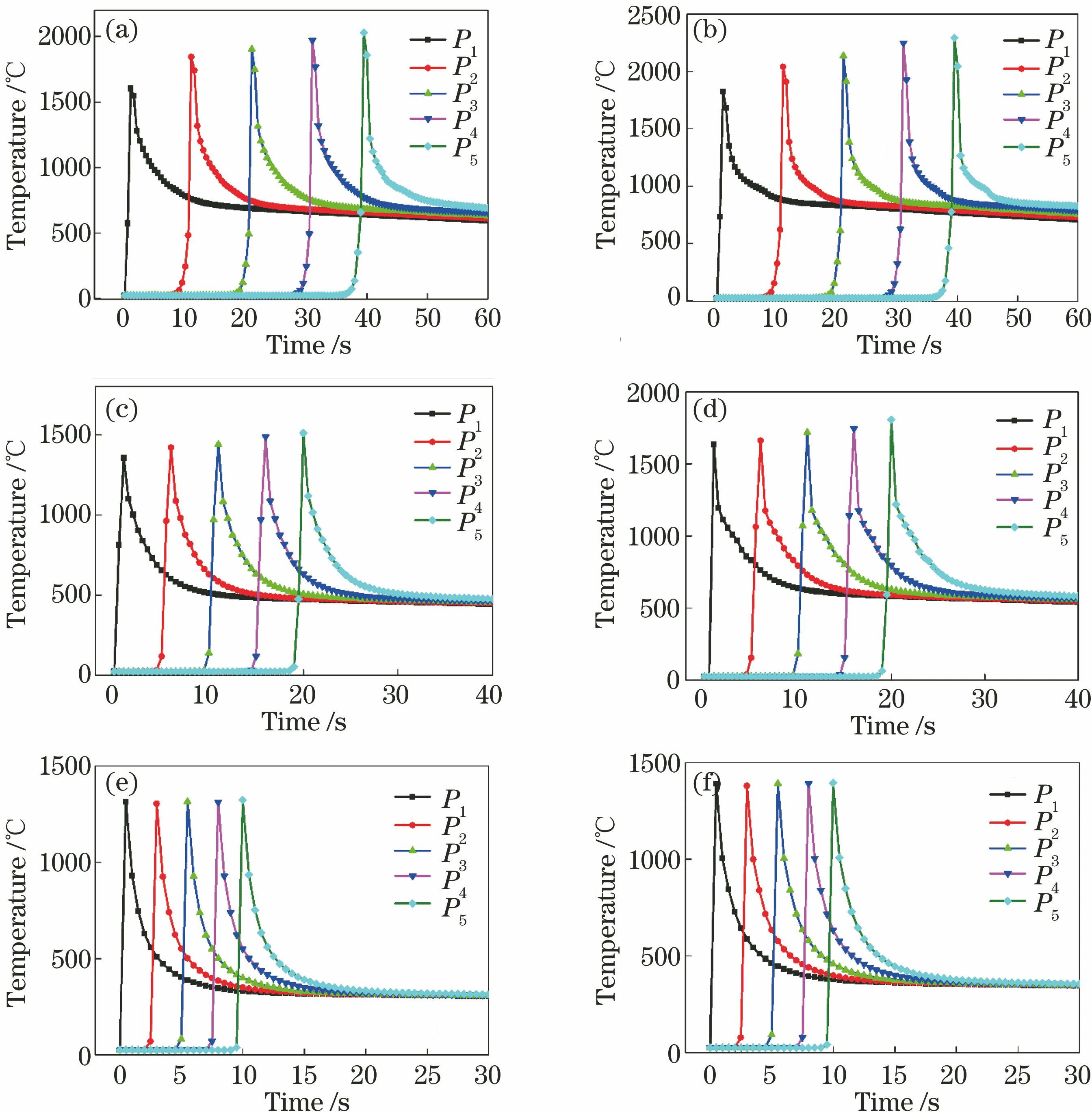
图 9. 不同激光工艺参数组合下的温度-时间曲线。(a) A组;(b) B组;(c) C组;(d) D组;(e) E组;(f) F组
Fig. 9. Temperature-time curves for different laser processing parameters. (a) Group A; (b) group B; (c) group C; (d) group D; (e) group E; (f) group F
数值模拟求解温度场和应力场,采集节点
由
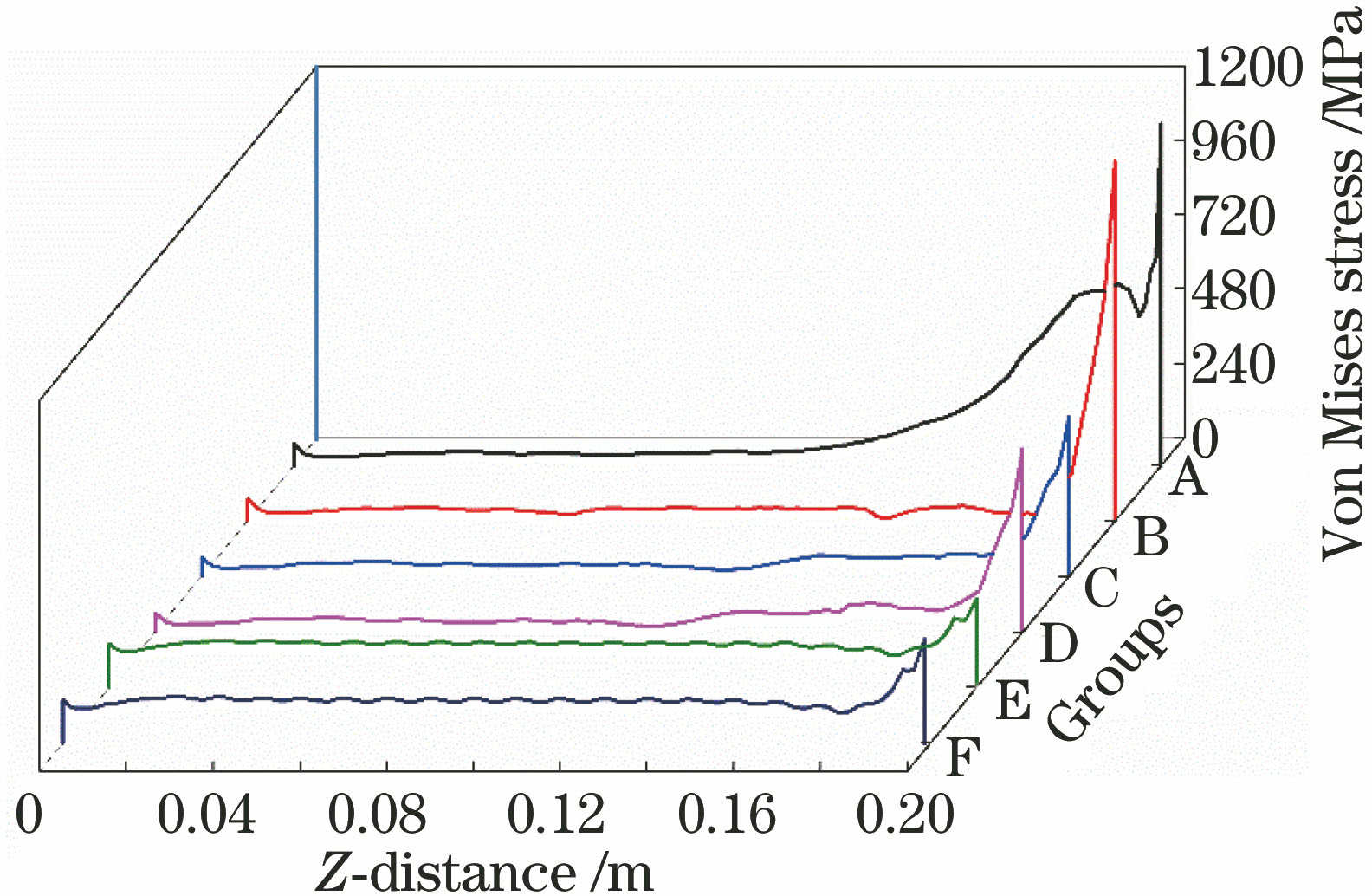
图 10. 不同激光工艺参数下沿路径1的应力分布曲线
Fig. 10. Stress distribution curves of different laser processing parameters along path 1
由于模型容易在长度方向上发生翘曲变形,因此选取路径1研究不同激光工艺参数下的应力分布曲线,如
5 激光熔覆实验
选用200 mm×30 mm×4 mm(长×宽×厚)的316L钢板作为基材。实验前,先用砂纸打磨待熔覆表面,并用丙酮清洗干净。选用钴基合金作为熔覆粉末。实验采用德国通快公司TruDisk 12003型激光器,6组激光工艺参数中的激光功率和扫描速度依据
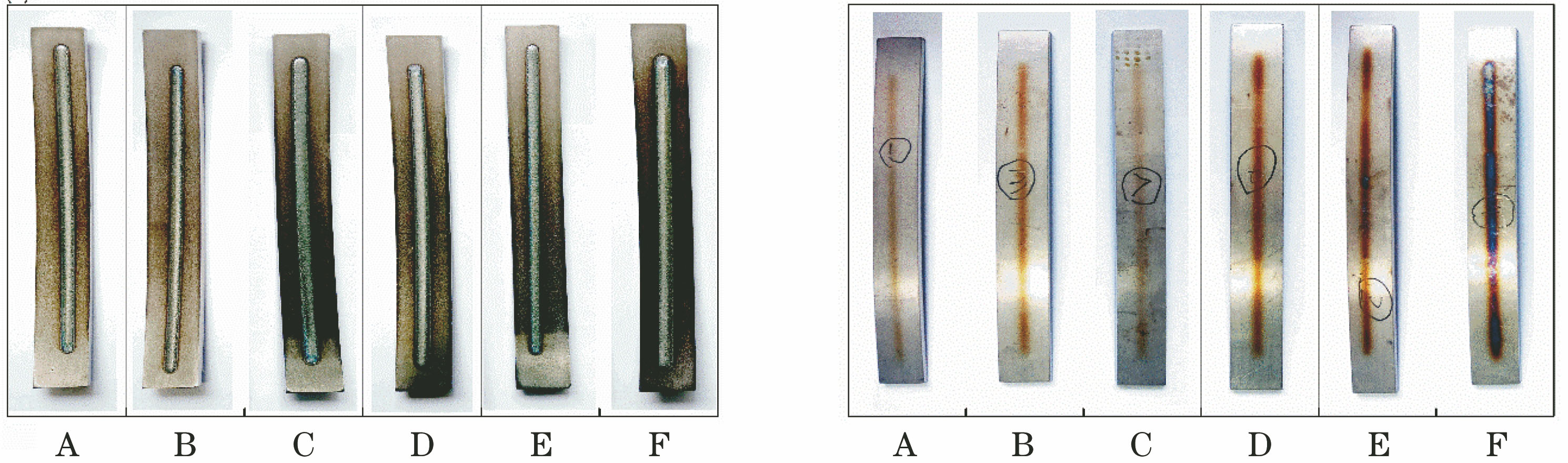
图 11. 熔覆试件形貌。(a)正面;(b)背面
Fig. 11. Morphology of laser cladding specimens. (a) Front; (b) back
对试件翘曲变形程度进行测量,如
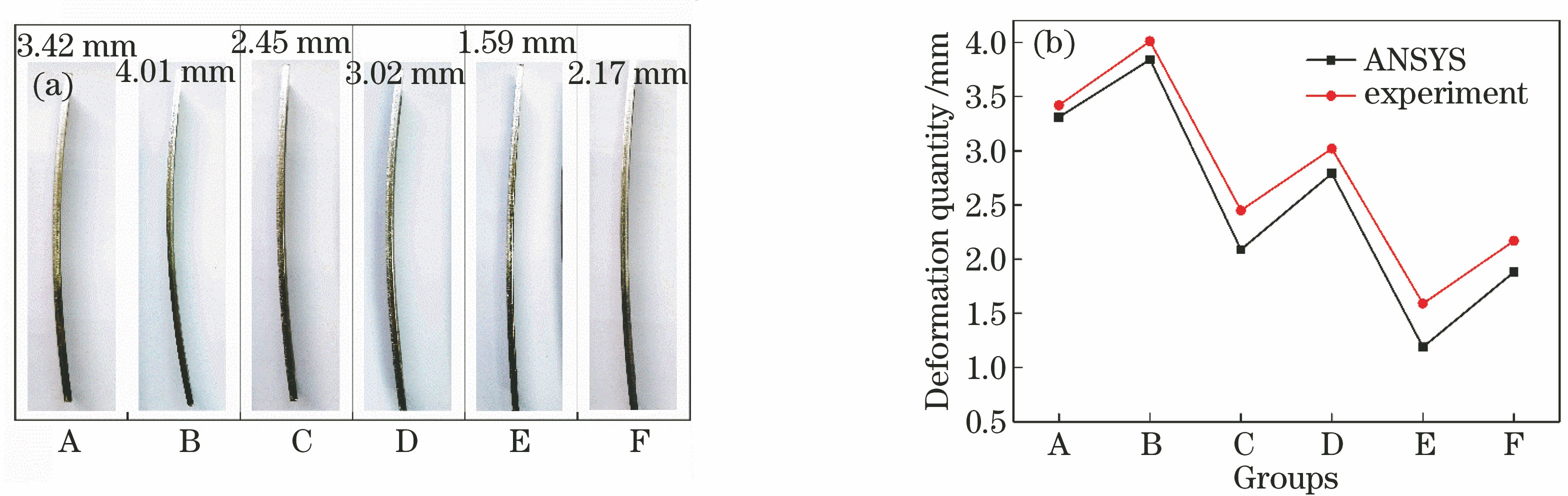
图 12. 熔覆试件的变形。(a)试件照片;(b)变形量对比
Fig. 12. Deformation of cladding specimens. (a) Photos; (b) deformation comparison
由
由
激光熔覆的数值模拟和实验结果表明,激光工艺参数对温度分布和应力分布都有影响,进而影响试件的熔覆质量和变形情况;对于一些薄壁类零部件,可通过调节激光功率和扫描速度来提高熔覆质量、减小工件变形,以达到激光熔覆修复的目的。
6 结论
建立了单道激光熔覆的有限元模型,利用ANSYS生死单元技术对激光熔覆的温度场和应力场进行了数值模拟。对于温度场,在熔覆层表面沿激光扫描方向每隔50 mm取一个节点,得到的节点温度-时间曲线具有逐渐增大的峰值;升温过程近似直线,降温曲线近似双曲线的一支。应力沿不同路径存在不同的分布规律,在熔覆层和基体结合处易形成应力集中和突变;在一定参数范围内,相比于激光功率,扫描速度对应力分布的影响较大。对于应力引起的变形,在变形量的分布规律上,实验测量值和模拟结果比较吻合,但数据大小存在一定的偏差;后续可通过改进数值模拟条件、提高实验测量准确性等途径寻求解决方法。
[1] 徐滨士, 李恩重, 郑汉东, 等. 我国再制造产业及其发展战略[J]. 中国工程科学, 2017, 19(3): 61-65.
[3] 封慧, 李剑峰, 孙杰. 曲轴轴颈损伤表面的激光熔覆再制造修复[J]. 中国激光, 2014, 41(8): 0803003.
[10] 李豪, 王彦芳, 石志强, 等. 基于椭圆热源模型的激光熔覆温度场与流场数值模拟[J]. 应用激光, 2017, 37(2): 218-222.
[11] 刘昊, 虞钢, 何秀丽, 等. 送粉式激光熔覆中瞬态温度场与几何形貌的三维数值模拟[J]. 中国激光, 2013, 40(12): 1203007.
[12] 宋建丽, 李永堂, 邓琦林, 等. 激光熔覆成形技术的研究进展[J]. 机械工程学报, 2010, 46(14): 29-39.
[13] 华亮, 田威, 廖文和, 等. 基于非线性连续疲劳损伤的激光熔覆构件疲劳寿命评估[J]. 中国激光, 2015, 42(9): 0903006.
[14] 李美艳, 蔡春波, 韩彬, 等. 预热对激光熔覆陶瓷涂层温度场和应力场影响[J]. 材料热处理学报, 2015, 36(12): 197-203.
[16] 方金祥, 董世运, 徐滨士, 等. 考虑固态相变的激光熔覆成形应力场有限元分析[J]. 中国激光, 2015, 42(5): 0503009.
[17] 戴德平, 蒋小华, 蔡建鹏, 等. 激光熔覆Inconel718镍基合金温度场与应力场模拟[J]. 中国激光, 2015, 42(9): 0903005.
[18] 中国航空材料手册编辑委员会. 中国航空材料手册[M]. 2版. 北京: 中国标准出版社, 2002: 510- 526.
China Aeronautical Materials Handbook Editorial Committee. China aeronautical materials handbook[M]. 2nd ed. Beijing: China Standard Press, 2002: 510- 526.
[19] 曹云龙. 316L不锈钢表面激光熔覆Co/稀土涂层组织与性能的研究[D]. 吉林: 吉林大学, 2015: 37- 47.
Cao YL. Research of microstructure and properties of laser cladding Co/RE on 316L stainless steel[D]. Jilin: Jilin University, 2015: 37- 47.
[20] 宫新勇, 高士友, 咸士玉, 等. 基于温度特征的单道激光熔覆翘曲变形[J]. 激光与光电子学进展, 2017( 10): 101410.
Gong XY, Gao SY, Xian SY, et al. Warp deformation in single-track laser cladding based on temperature characteristics[J]. Laser & Optoelectronics Progress, 2017( 10): 101410.
[21] 李美艳, 韩彬, 蔡春波, 等. 36(5): 25-28[J]. . 激光熔覆镍基合金温度场和应力场数值模拟. 焊接学报, 2015, 32: 114.
Li M Y, Han B, Cai C B, et al. 36(5): 25-28[J]. stress fields of laser cladded Ni-based coating. Transactions of the China Welding Institution, 2015, 32: 114.
[22] 刘衍聪, 范常峰, 尹晓丽, 等. 铸铁表面双光束激光熔覆温度场与应力场分析[J]. 应用激光, 2014, 34(4): 288-293.
[23] 王凯, 赵剑峰, 潘浒, 等. 工件形状对镍基高温合金激光再制造应力场分布的影响[J]. 激光与光电子学进展, 2013, 50(4): 041402.
[24] 吴晶. 辐射对流耦合换热过程性能优化准则分析[J]. 工程热物理学报, 2013, 34(10): 1922-1925.
[25] 李松, 蔡翔, 朱路飞, 等. 基于单流道和结构网格的湿式潜水泵数值模拟[J]. 华东理工大学学报(自然科学版), 2016, 42(4): 580-586.
[26] 潘浒, 赵剑峰, 刘云雷, 等. 激光熔覆修复镍基高温合金稀释率的可控性研究[J]. 中国激光, 2013, 40(4): 0403007.
Article Outline
任仲贺, 武美萍, 唐又红, 韩基泰, 龚玉玲. 基于热力耦合的激光熔覆数值模拟与实验研究[J]. 激光与光电子学进展, 2019, 56(5): 051404. Zhonghe Ren, Meiping Wu, Youhong Tang, Jitai Han, Yuling Gong. Numerical Simulation and Experimental Research of Laser Cladding Based on Thermo-Mechanical Coupling[J]. Laser & Optoelectronics Progress, 2019, 56(5): 051404.