Thermal process of silica glass microchannels fabricated by femtosecond laser ablation
Download: 908次
With the progress of science and technology and the improvement of the quality of life, people pay more attention to the pursuit of health. A microfluidic chip is an important device of health detection through the concept of lab-on-a-chip, which is revolutionizing fields such as biology and chemistry[1,2]. The microfluidic channel is the basic structure of the chip. Fused silica glass provides the necessary guarantee of high sensitivity and high reliability of microfluidic chips, but what is more important is that it has high transmittance in the visible and ultraviolet bands, which is convenient for optical detection. Therefore, fused silica glass is the most ideal choice of building many chip lab systems[3].
Although mature semiconductor technology can combine lithography and etching technology and machine various microchannels with various sizes and complex morphology based on glass and silicon materials[4–
People pay more attention to the production of microchannels with a high depth to diameter ratio, where techniques, such as the time domain shaping of a double pulse and control of the polarization state[10,11], are applied. However, the roughness of the microchannel has great influence on the fluid wettability, and the study of the control of surface roughness is not enough. Yahng
This Letter explores the improvement of high-temperature thermal post-treatment on the morphology of microchannels. The effects of laser power, temperature, and the incubation time on the morphology of microchannels processed by femtosecond laser ablation were investigated, respectively. Also, through the confocal laser scanning microscope (LCM) and scanning electron microscope (SEM) images, we discussed the underlying mechanism about the effect of temperature on the ablation results.
Figure
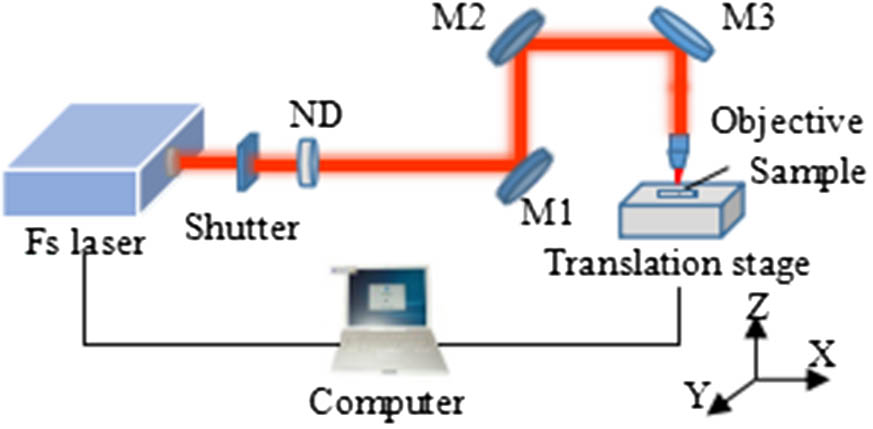
Fig. 1. Schematic diagram of the experimental setup. M, mirror; ND, neutral density attenuator.
Laser pulse power is one of the key factors affecting the morphology of the microchannel. The power used in our experiments is adjusted by an attenuator and ranges from 5 to 15 mW with the gradient of 2 mW. Figure
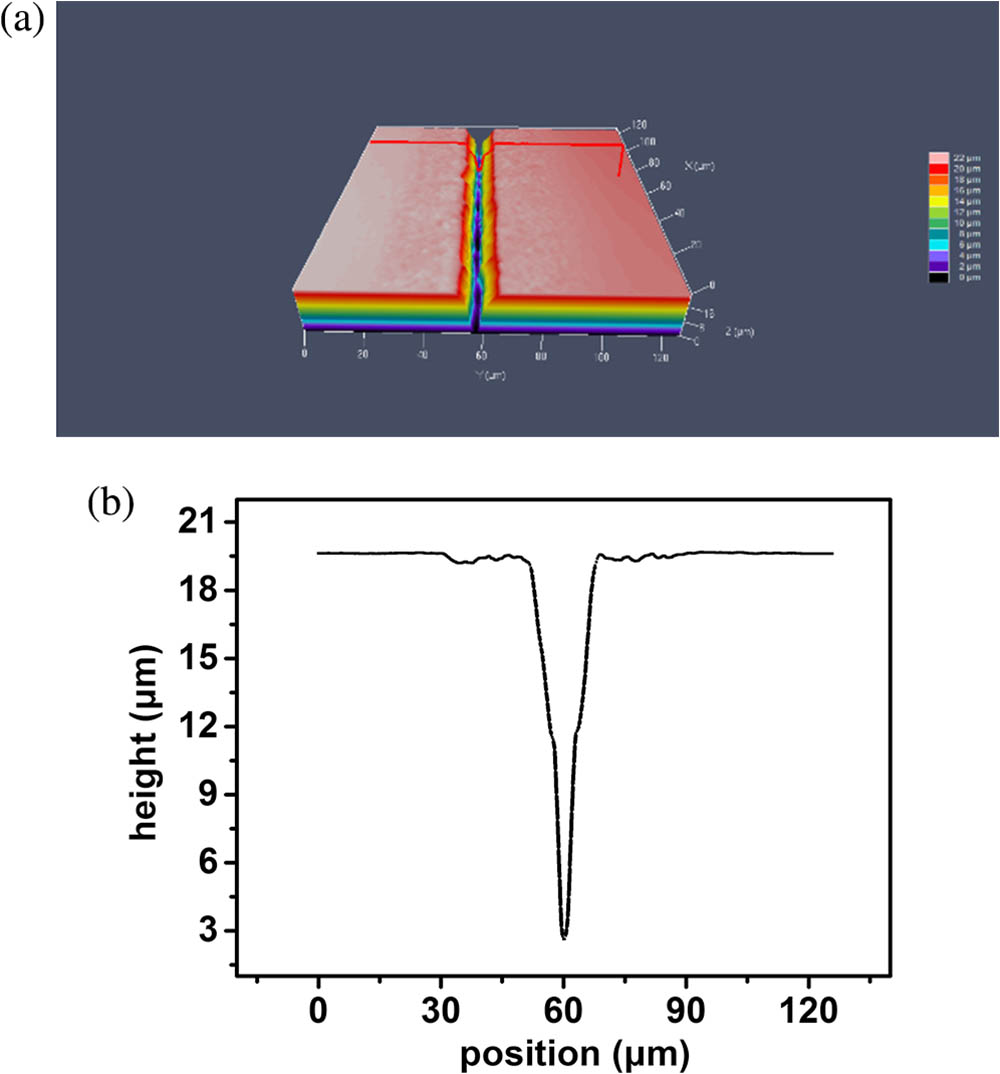
Fig. 2. (a) Morphology of the microchannel measured by the LCM; (b) cross-section profile.
It can be seen from the Fig.
We design a microchannel where the width is 15 μm, and the depth is 20 μm. When the laser power is 15 mW, it can meet the requirement. Therefore, in the following experiment, the samples are processed by 15 mW laser power. However, the channel roughness is very large, above 1.6 μm. In order to improve its morphology, we have adopted the method of heat treatment. We heat the sample from room temperature to 800°C with the temperature gradient of 200°C. When the heating furnace reaches the set temperature, it will be kept for 1 h and then cooled in the air naturally. Figure
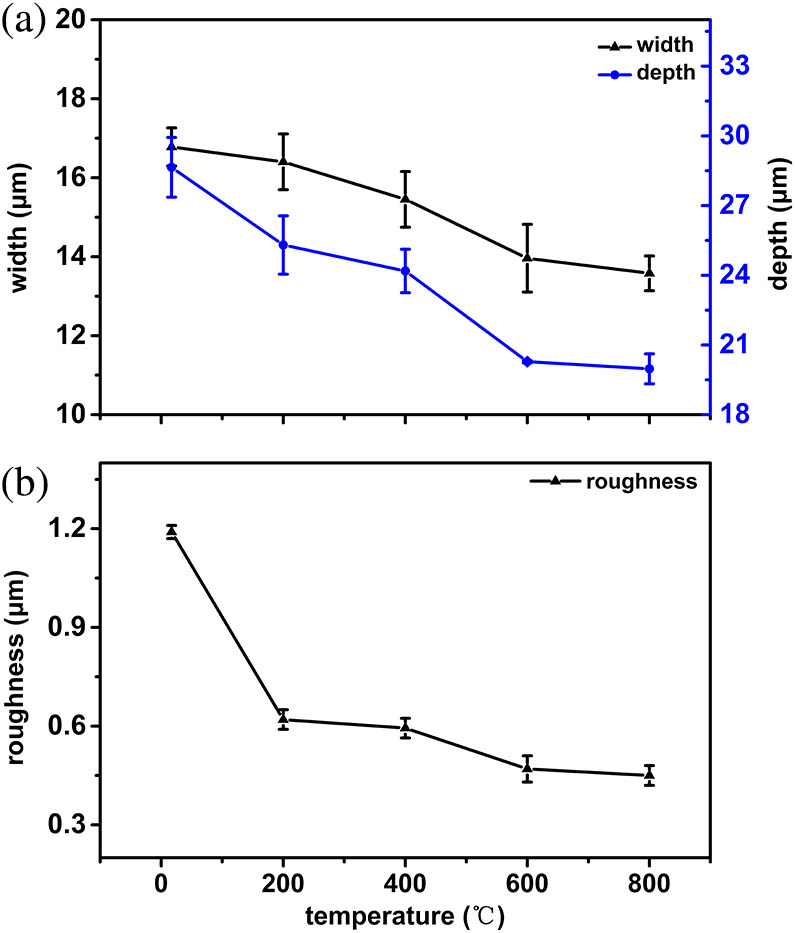
Fig. 4. Trend of width, depth, and roughness of microchannels varies with the temperature.
With the increasing post-treatment temperature, the width, depth, and roughness of the microchannel are decreased, and the change rate of all of the parameters increases. Before laser processing, there are numerous
The surface of the channel fabricated by femtosecond laser ablation consists of 3 or 4 rings. When the temperature raises, the Si–O–Si bond angle of the fused silica glass decreases, resulting in reduction of tetrahedron volume, which makes the structure denser. However, in this experiment, the width and the depth of the surface channel reduced at the same time. The post-treatment temperature is much lower than that of femtosecond laser ablation. Therefore, the Si–O–Si bond angle of the low bond angle structure of the ablation channel will not decrease with the increase of temperature, but increase instead, resulting in the volume of the surface material increasing with temperature, and the depth and the width of microchannel decreasing. The higher the temperature, the greater the influence on the Si–O–Si bond angle, leading to the change rate increase with the temperature.
When fused silica glass is heated, the surface melts at the beginning. The drop of viscosity results in viscous flow, which can partially repair the micro-defects. The specific surface area of the microchannel is large, and the proportion of the surface atoms is larger than the unprocessed area, since after the laser irradiation, the structure of three rings in the microchannel increased, whose most adjacent atoms are less than those in the internal six rings structure. The binding force is weaker, and the thermal motion of the atom is less constrained, therefore, the unflattened surface in the microchannel can be melted at a lower temperature[19]. The effect of thermodynamics plays an important role in reducing the roughness. According to the thermodynamic size effect, the size of the microstructure in the channel surface decreases with the increase of temperature. This results in the roughness decrease with the increase of temperature. To further study the effect of temperature on roughness, a scanning electron microscope measurement is carried out, as is shown in Fig.
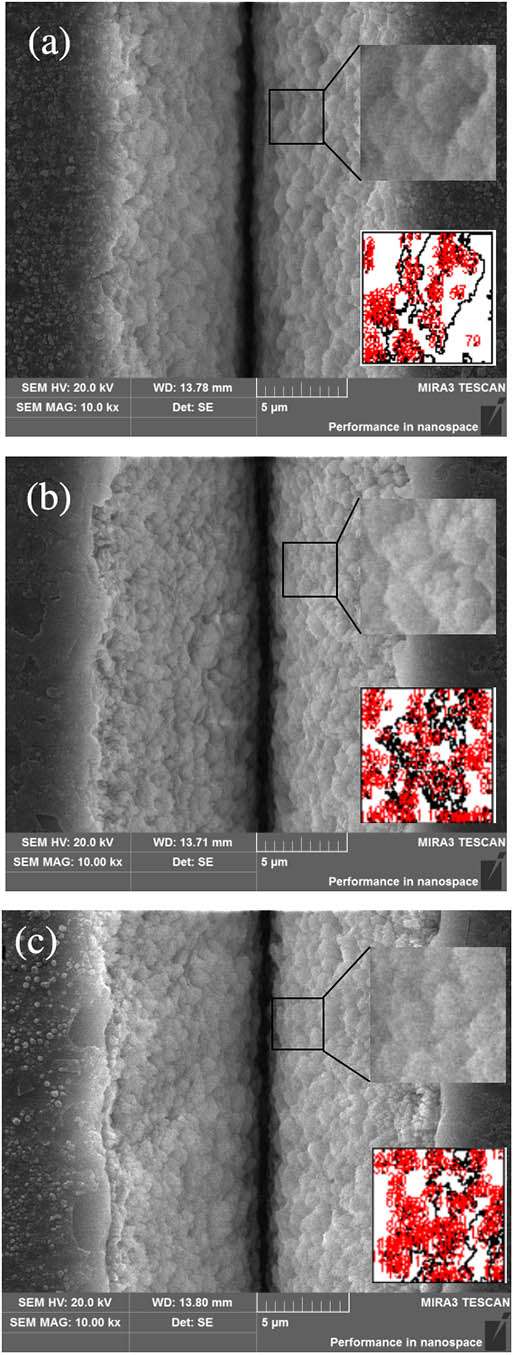
Fig. 5. SEM images of 15 mW heating at different temperatures and at an incubation time for 1 h. (a) Room temperature; (b) 400°C; (c) 800°C; the upper right corner is the selected area, and the lower right corner is the counting result.
Then, we further explored the influence of the incubation time on the microchannel morphology. According to Fig.
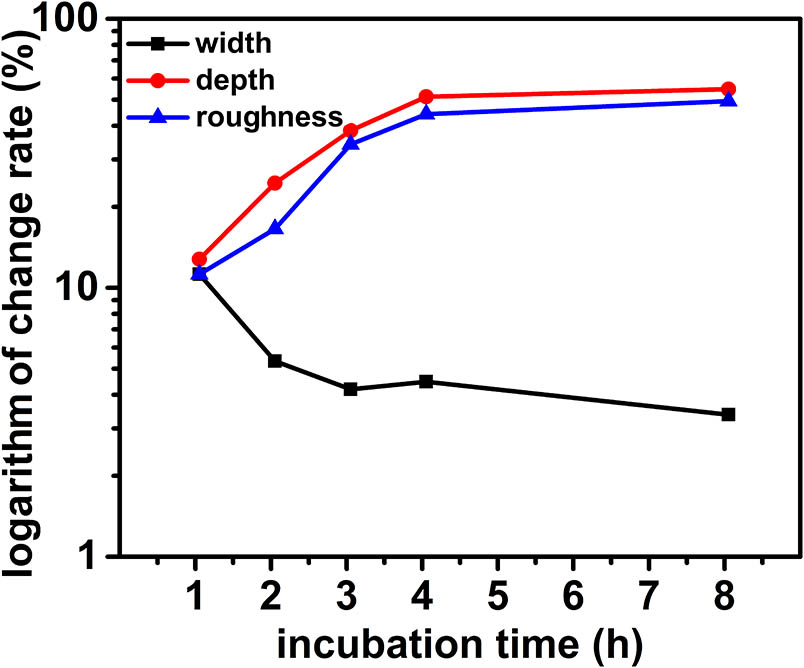
Fig. 6. Relationship between the change rate of the morphology and the incubation time when the work piece is heated to 800°C.
It can be seen that with the increase of the incubation time, the change rate of width decreases at the beginning, and then it tends to be stable. While the change rates of depth and roughness increase, they tend to be stable. It is obvious that with the prolongation of the constant temperature, the volume of the microchannel decreases and tends to be stable, and the roughness is reduced and tends to be stable. The thermal expansion coefficient of fused silica glass is very small, and it needs enough time to transmit the temperature of the resistance box to that of the glass itself. Therefore, with the prolongation of the constant temperature, there is uniform heating of the glass, and it can be understood as equivalent to the increase of temperature. Due to the size effect of thermodynamics, a micro-melting zone exists in the microchannel structure, which results in particles becoming smaller and denser, and therefore, the roughness decreases with the incubation time. The surface tension increases with the rise of temperature. As a result, the depth of the microchannel gets shallower as time goes on, but there is no surface tension in the width direction of the microchannel, and thereby, the variation in the width direction is not obvious. The result of the comprehensive effect is that the volume of the microchannel gets smaller and smaller until it reaches a stable state.
To sum up, in order to improve the roughness of the microchannel processed by a femtosecond laser, we have carried out some experiments on high-temperature annealing. The effects of different power, temperature, and thermostat time on the microchannel morphology were investigated. The experimental results show that the depth, width, and roughness of the microchannel will decrease with the increase of temperature. This is due to the fact that the Si–O–Si bond angle of the femtosecond laser ablation microchannel increases with processing temperature, resulting in an increase in the volume of the surface material as the temperature increases and a decrease in the size of the microchannel. The width and depth of the microchannel decrease. Due to the size effect of thermodynamics, the structure of the microchannel is not stable, and it can melt at a relatively low temperature. There the micro-melting zone may exist, which leads to the decrease of roughness. Because of the existence of surface tension, with the extension of constant temperature, the depth of the microchannel will be shallower until it reaches a stable state. At the same time, the volume of the microchannel is the smallest. In order to obtain a much lower surface roughness, the thermal process temperature should be higher, and for the processing temperature of 800°C, 4 h of incubation time is an optimized parameter.
[1]
[2]
[3]
[5]
[6]
[7]
[8]
[9]
[12]
[13]
[15]
[16]
[17]
[18]
[19]
Xiaoyan Sun, Dongmei Cui, Youwang Hu, Dongkai Chu, Guowei Chen, Jinlong Yu, Jianhang Zhou, Ji’an Duan. Thermal process of silica glass microchannels fabricated by femtosecond laser ablation[J]. Chinese Optics Letters, 2018, 16(10): 101402.