Micro-fabrication and hermeticity measurement of alkali-atom vapor cells based on anodic bonding
Download: 1321次
The interaction between light and atoms is an important component in many aspects of quantum optics research, including the Planck constant, Fano resonances[1,2], Bose–Einstein condensates[3], cold Rydberg atoms[4], and quantum sensing[5]. In modern society, an increasing amount of precision-metering information is needed for different variables, such as frequency, magnetic field, and gravity acceleration, which can be acquired from the interaction between light and atoms. The problems in traditional atomic sensors, especially with large volume, can be solved using micro-electromechanical systems (MEMS) technology[6,7]. MEMS technology has not only led to the development of the micro-manufacturing industry, but also meets the requirements of modern atomic sensors, such as small size, low consumption, light weight, and intelligent integration. Vapor cells, which are typical micro-reaction cavities providing a well-controlled and stable inner atmosphere for the interaction of atoms, are a key component for atomic sensors, including atomic gyroscopes, atomic magnetometers[8], and chip-scale atomic clocks[9,10].
The hermeticity of vapor cells and miniaturization of atomic clocks are two major problems that must be solved. Owing to the small size of a vapor cell, if a slight leak occurs, the alkali metal filled in the reactive cavity is easily oxidized, rendering the micro-sensor ineffective. Leak also causes a change in the composition of the buffer gas filled in the vapor cell, which deteriorates the long-term frequency stability of the atomic clock[11]. According to existing literature, several methods are used for wafer-level packing: anodic bonding[12,13], silicon fusion bonding[14,15], organic bond bonding[16], glass frit bonding[17], and solder bonding[18]. Anodic bonding has the merits of cost effectiveness and convenient reaction during the vapor cell fabrication process.
We present the micro-fabrication of an MEMS wafer-level hermit vapor cell based on vacuum anodic-bonding technology, in which the voltage is increased in steps of 200 V. Further, the bonding surface was experimentally investigated using a scanning electron microscope (SEM). The leak rate was measured using a helium leak detector. Analyses of D2 absorption spectroscopy, leak rate, and bonding strength verified the quality of the vapor cells.
A microloop-gap resonator[19,20], the traditional optical microwave cavity, limits the requirement of a small volume in the vapor cell. Now, the coherent population trapping (CPT) principle is implemented in chip-scale atomic devices to achieve this goal. With the development of the MEMS technology, batch-fabrication of chip-scale atomic devices comes true. An MEMS wafer-level dual-cavity vapor cell with a glass–silicon–glass three-layer physical architecture is introduced, as shown in Fig.
Reactions in a single-cavity vapor cell have limitations. The residue is not conducive to light passing through it, which will negatively affect the detection of the spectral line. However, such disturbances can be avoided in a dual-cavity vapor cell. What is more, a dual-cavity vapor cell provides different spaces for storing the alkali-metal dispenser (reactive cavity) and reacting for light and atoms (optical cavity). In the optical cavity, one pump beam generates a coherent, and another probe beam detects the optical signal. The two cavities are connected by micro-channels, which not only helps the alkali-metal atoms to diffuse from the reaction cavity to the optical cavity but also isolates substances from the reactive cavity to some extent.
Anodic bonding is an encapsulation method commonly used for simple glass–silicon steps. The principle underlying the anodic bonding between silicon and glass is shown schematically in Fig.
In this experiment, we used a 4-in.-diameter, 1.5-mm-thick P-type <100> double-sided polished silicon wafer and two pieces of 4 in. 500-μm-thick BF33 glass plates that can be bonded to each other. The thermal-expansion coefficients of these materials are close to each other. For a high bonding strength, both the glass plates and silicon wafer must have high surface roughness and flatness, and they are thoroughly cleaned before use.
Fabrication of a vapor cell relies on the following technologies: silicon micromachining, rubidium dispenser manipulation, and packaging. The main four steps are fabricating silicon holes with deep reactive ion etching (DRIE) technology, placing the rubidium dispenser for producing natural abundance rubidium, sealing with the anodic-bonding technology, and alkali-metal reaction.
First, a double-sided polished silicon wafer is etched using photolithography with a mask and the DRIE technology, as shown in Fig.
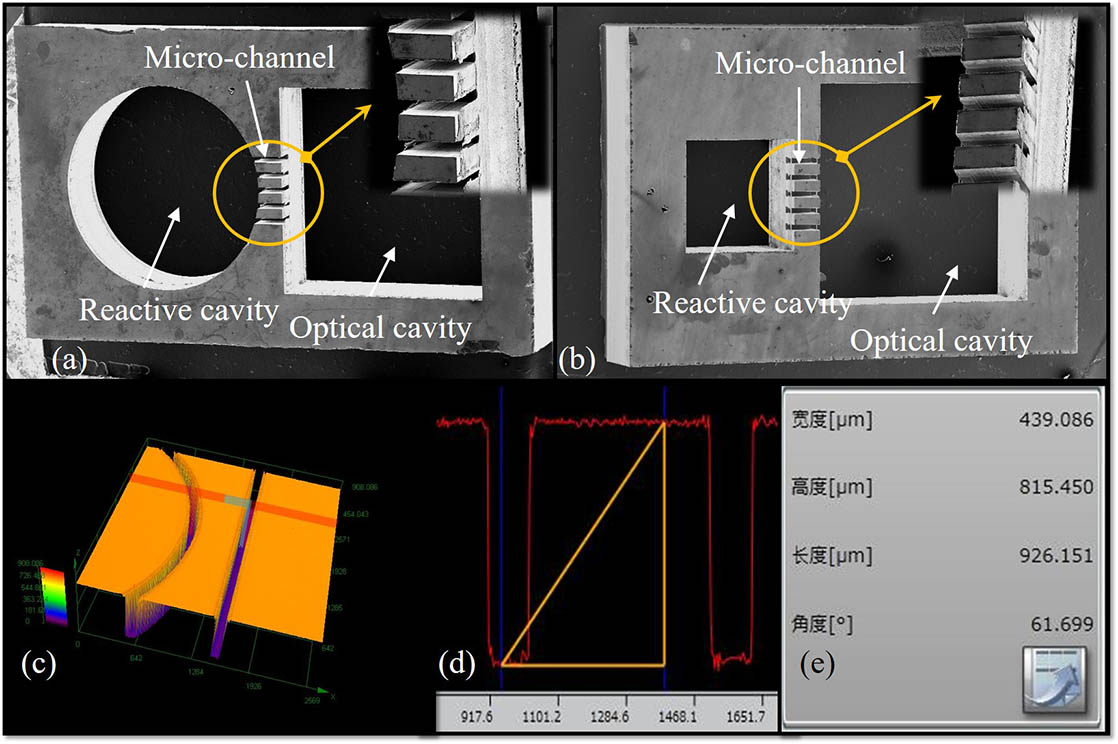
Fig. 4. (a) and (b) SEM images of a vapor cell with different shapes. (c) Schematic of the simulated etching effect. (d) and (e) Etching depth during the etching process.
Second, the anodic-bonding process was performed using the EVG510 wafer bonding system (EV Group). The etched silicon wafer, after cleaning with acid and deionized water, and a BF33 glass plate of the same size are placed on a bonder chuck and clamped by three separation flags under a high-vacuum environment of
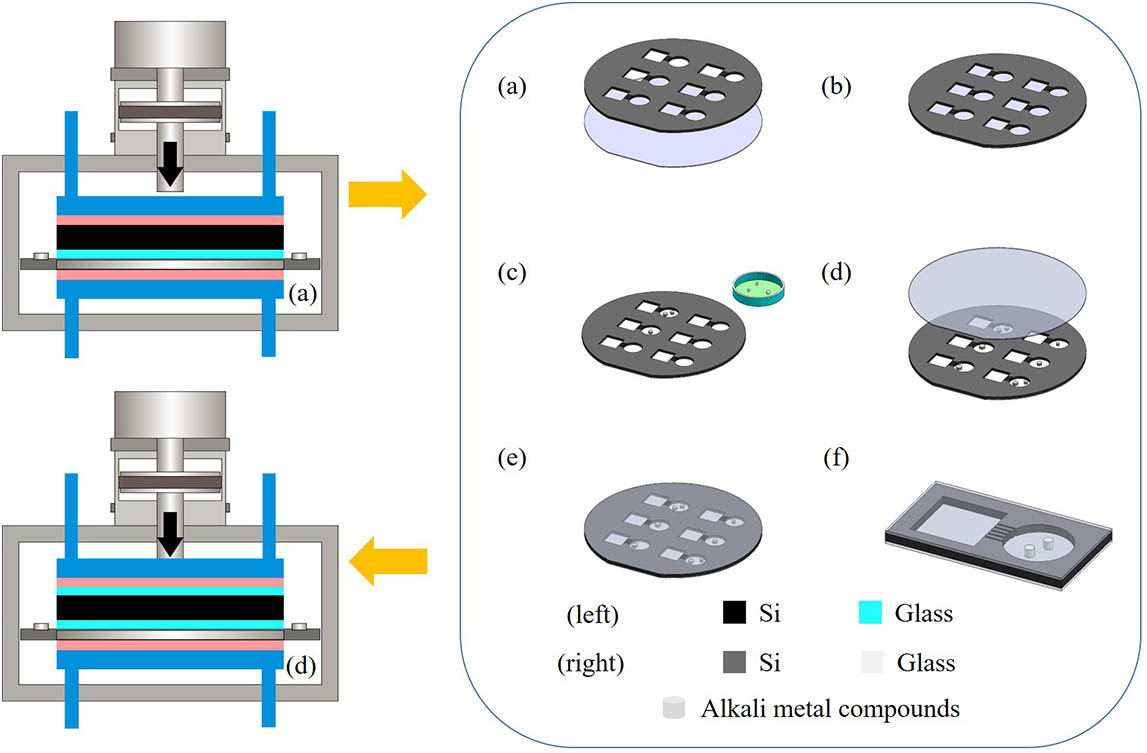
Fig. 5. Schematic of the anodic-bonding process. (a) and (b) First anodic bonding. (c) Filled alkali-metal compounds. (d) and (e) Second anodic bonding. (f) Completed vapor cell.
The images of the etched silicon wafer and the bonded silicon wafer are shown in Fig.
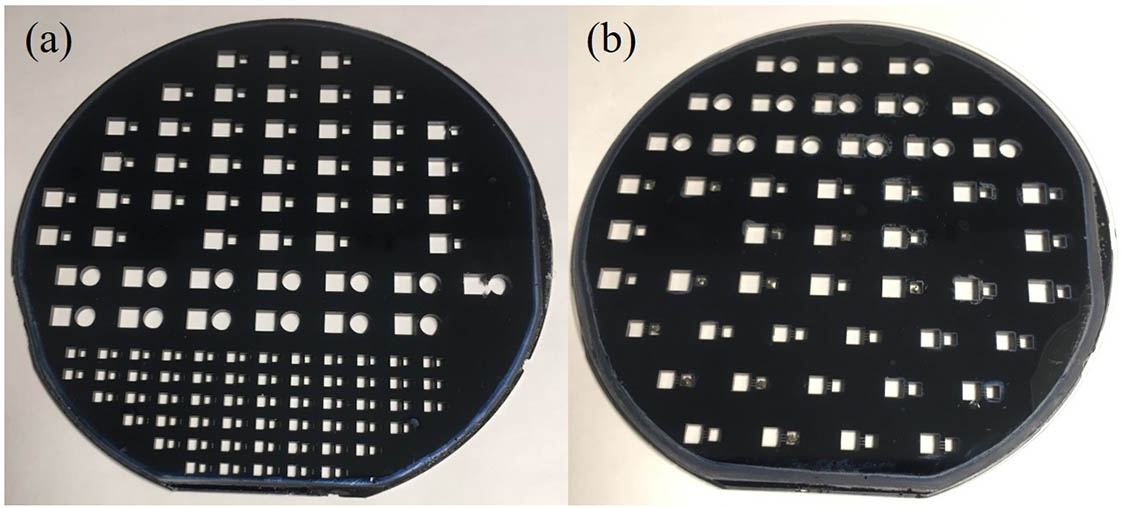
Fig. 7. (a) Image of the etched silicon wafer. (b) Image of the fabricated bonded silicon wafer.
Several double-cavity vapor cells have different lengths of optical cavities. Figure
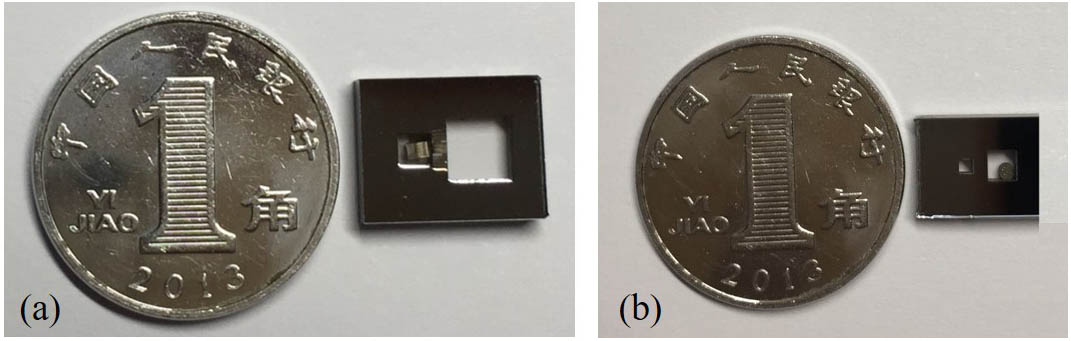
Fig. 8. Vapor cells of different optical cavity lengths compared with a dime: (a) 4 mm long and (b) 1 mm long.
We carried out the absorption spectroscopy experiment to verify the properties of the vapor cell. The light source is a vertical cavity surface emitting laser (VCSEL) tuned on the Rb D2 line at 780 nm. The linewidth is less than 300 kHz, and the diameter is 1 mm. The incident power is 320 μW. The laser was modulated with a 1 V, 10 Hz triangle wave. Then, the laser passed through an optical isolator, which can prevent optical feedback; then, a lens and a
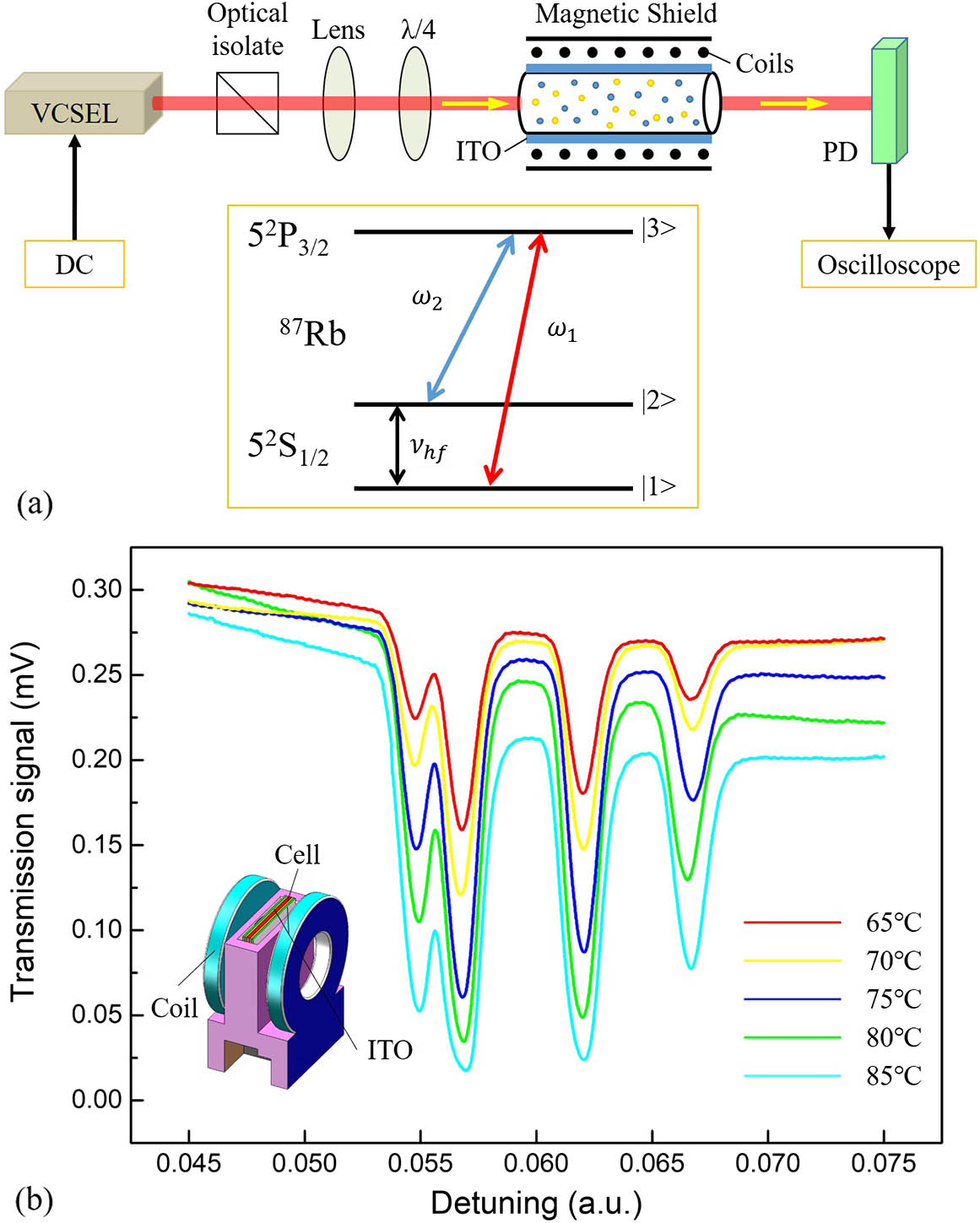
Fig. 9. (a) Test platform for D2 absorption spectroscopy. (b) D2 absorption spectra at different temperatures.
The relationship between the pressure
The hermeticity of the vapor cell affects the stability and aging of atomic sensors. According to the MIL-STD-883E, Method 1014.9 (1995), electronic device packaging always needs to measure the hermeticity. The process of helium fine inspection is as follows. (a) Adding helium pressure: place the vapor cell in a tank filled with helium gas. The tank is vacuumed in advance until it reaches a vacuum environment at 5 bar, and helium of purity of 99% is filled into the tank. After maintaining this state for approximately 4 h, the tank is slowly depressurized, and the vapor cells are extracted from the tank. (b) Purification: when the vapor cell is extracted from the tank, the surface-adsorbed helium is blown off with dry nitrogen. (c) Leak rate detection: put the vapor cell into the test container and connect the container to the helium leak detector. The container is vacuumed in advance, and the leak detector is checked for leak detection. By measuring the content of helium escaping from the package structure, the leak rate can be obtained. Figure

Fig. 10. Helium leak rate measurement of vapor cells with different optical cavity lengths.
Furthermore, the silicon–glass adhesive layer was inspected by SEM to detect larger cracks. Figure
The vapor cell plays an important role as a core component of atomic sensors. We have presented micro-fabrication of an MEMS wafer-level hermit vapor cell based on DRIE and vacuum anodic-bonding technology. Cavities and micro-channels were fabricated with DRIE technology, providing a smooth interior wall. The anodic-bonding process was performed with a maximum voltage of 1000 V and maximum current of 20 mA for vapor cell bonding, and the bonding had a critical influence on vapor cell hermeticity. In order to measure the bonding effect, the silicon–glass bonding surface was experimentally investigated by SEM, which illustrated that there were no visual cracks and defects in the bonding surface. The leak rate was measured using an ALCATEL ASM 142 helium leak detector. The result shows that the vapor cells with different optical cavity lengths comply with the MIL-STD-883E standard (
[1]
[2]
[3]
[4]
[5]
[6]
[7]
[8]
[9]
[10]
[11]
[13]
[14]
[15]
[16]
[17]
[18]
[20]
[21]
[22]
[23]
[24]
[25]
[26]
[27]
[28]
[29]
[30]
[31]
[32]
Lu Zhang, Wendong Zhang, Shougang Zhang, Shubin Yan. Micro-fabrication and hermeticity measurement of alkali-atom vapor cells based on anodic bonding[J]. Chinese Optics Letters, 2019, 17(10): 100201.