小模数齿轮齿面双道激光熔覆工艺
下载: 824次
1 引言
小模数齿轮因功率范围广、传动效率高、传动比正确而在精密器械中应用广泛,小模数齿轮的模数较小,因此轮齿的宽度较窄,齿高较低;此外,齿轮材料一般为45钢,齿轮工作面的硬度较小,而由于齿轮在工作中是高副接触,高应力接触会导致齿面产生磨损、点蚀等损伤,而齿面磨损会影响齿轮的传动平稳性,严重时会导致齿轮失效。对失效齿轮进行修复再制造是降低企业成本和提高产品使用寿命的有效途径。对小模数齿轮齿面采用激光修复的重要技术指标包括机械加工余量不大于0.28 mm,熔深在0.3~0.6 mm之间,涂层表面均匀连续且具有金属光泽,涂层硬度达到50 HRC[1]。目前,对于小齿轮齿面的激光熔覆而言,主要存在的技术难题如下:1)小模数齿轮的齿顶部位很薄,在单道激光制备镍基合金熔覆涂层过程中非常容易对齿顶部位造成烧蚀,严重时将会导致齿轮表面发生形变,对齿轮后期的齿形修复造成很大影响;2)激光光源为高斯热源,光束能量分布不均且光源中间能量较高,容易造成齿面中部基材熔深较大,从而导致涂层的稀释率较高,进而影响涂层的组织和性能。
本文以在1模数的直齿齿轮齿面上制备出的性能优良的镍基合金熔覆涂层作为研究对象,针对单道激光熔覆过程中易出现的熔覆缺陷,提出了双道激光熔覆的实验方法,并对其进行优化研究。双道激光加工的本质是对原本不均匀的高斯光束的能量进行优化处理,将原本一个大的高斯热源的能量等价到两个小高斯热源上,因此双道加工中每一道激光束的峰值能量都要低于原有的单光束峰值能量,进而缓解单道激光所造成的齿面烧蚀和热变形。通过对比优化前的单道齿面加工和优化后双道齿面加工的基材的熔深、涂层稀释率、涂层的显微组织形貌以及熔覆层横截面的显微硬度,验证光束能量分布状态对镍基合金熔覆涂层加工效果的影响,进而确定小模数齿轮齿面双道激光依次加工齿顶和齿底部位的镍基合金涂层加工工艺方法。
2 实验设备与方法
2.1 实验设备
本实验选用的加工设备为三轴联动数控激光加工操作系统,激光器为德国的IPG 准连续光纤激光器,型号为YLS-250,最大输出功率
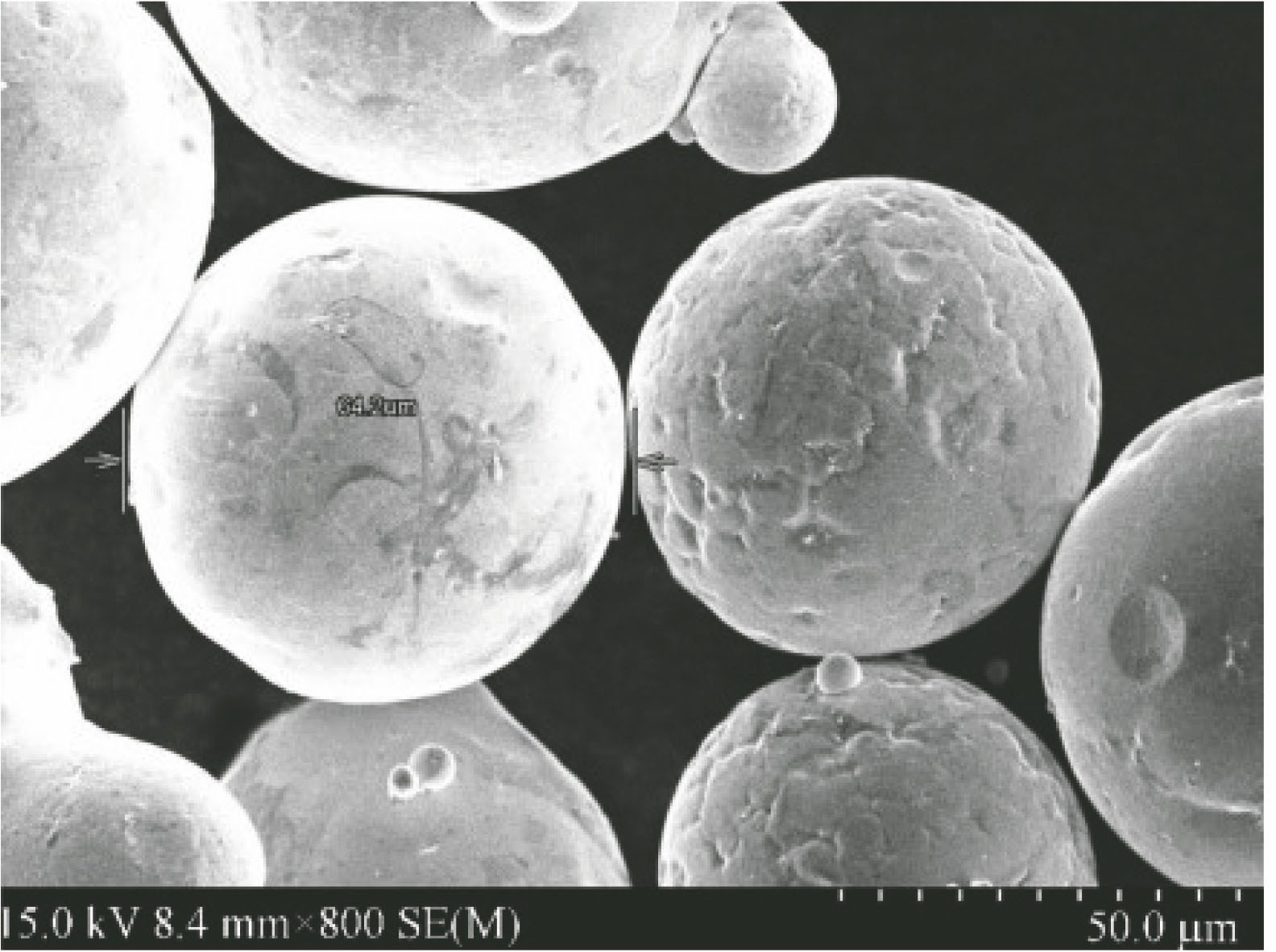
图 2. Ni60自熔性合金粉末的扫描电子显微镜图
Fig. 2. Scanning electron microscope graph of Ni60 self-fluxing alloy powder
2.2 实验方法
采用冷预置涂层的方式预制备熔覆涂层,所选取的黏结剂为聚乙烯醇水溶液,将试样放到真空干燥箱中加热干燥,在120 ℃下烘干6 h,以彻底去除预置涂层中的水分。采用预置粉末的工艺具有方便、简单、操作性强、成本低、无污染、无噪声等优点,预置涂层厚度为1 mm。
激光熔覆是一个较复杂的工艺过程,影响熔覆层质量的主要因素是材料参数和工艺参数。工艺参数主要有激光功率
式中:
由于实验过程中采用的光斑近似圆形,所以有
式中:
通过控制功率密度这一单一变量的方法在较低功率下得到理想的镍基合金熔覆涂层,实验过程中在保持激光功率(250 W)和光斑直径(1 mm)不变的前提下,改变激光器的扫描速度,以此来调节每次单道实验过程中的激光功率密度,按照这个思路建立如
表 1. 单道激光熔覆齿轮齿面的加工参数
Table 1. Processing parameters of single-pass laser cladding coatings on gear-tooth surface
|
2.3 齿面单道激光功率密度的确定
为了更加直观地观察激光功率密度对熔覆层宏观形貌以及涂层稀释率的影响,在光学显微镜下测出每组样品的截面尺寸,并计算出对应的涂层稀释率,如
表 2. 不同功率密度下齿面镍基合金涂层的截面 尺寸及稀释率
Table 2. Cross-sectional dimensions and dilution rates of nickel-based alloy coatings on tooth surface at different power densities
|
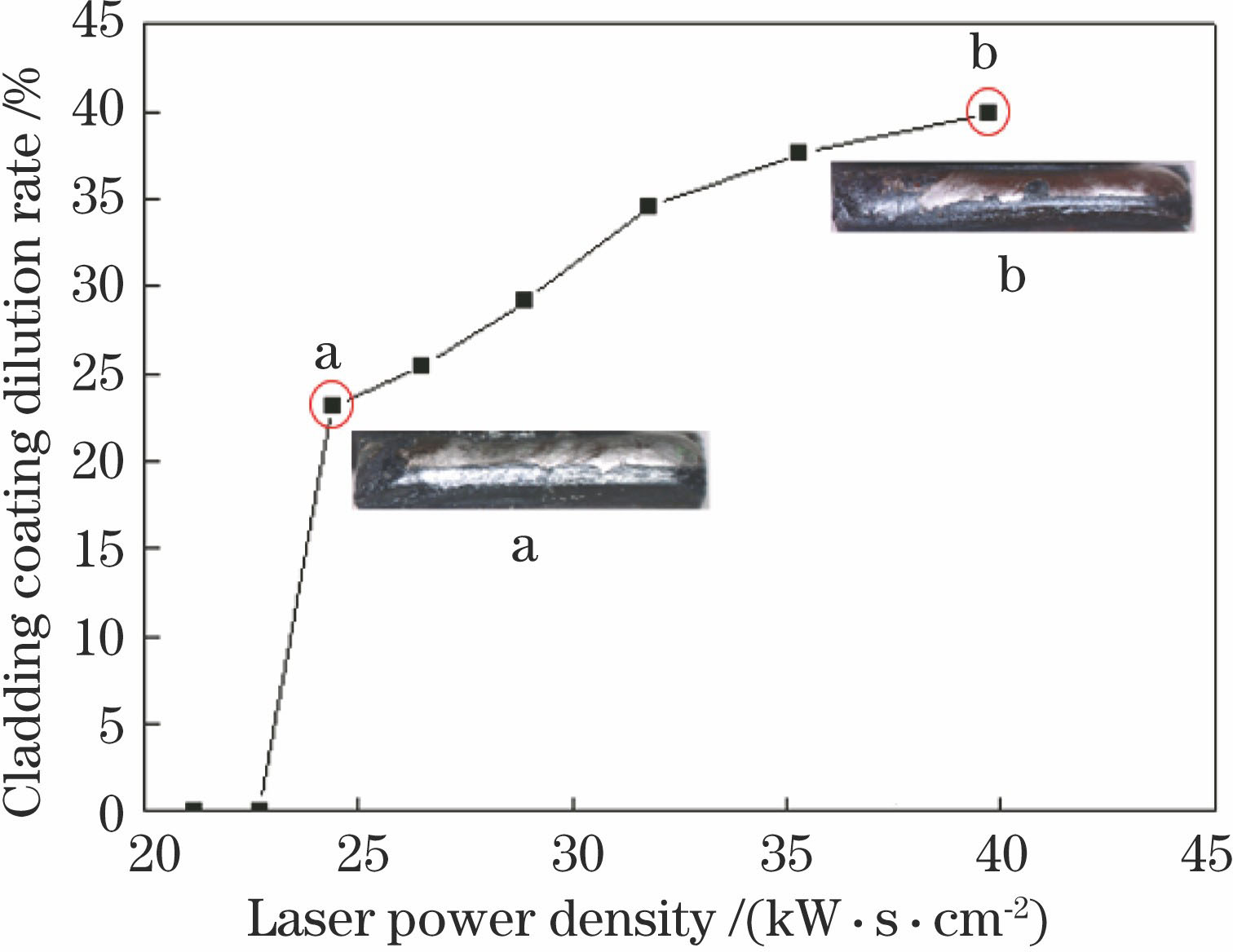
图 3. 不同激光功率密度下齿面单道激光熔覆涂层的稀释率
Fig. 3. Dilution rates of single-pass laser cladding coatings on gear-tooth surface at different laser power densities
结合熔覆层的宏观形貌可以看出,当激光功率密度达到39.7 kW·s·cm-2时,基材出现了明显的过度烧蚀,此时的涂层稀释率为40%,说明了齿面镍基合金熔覆涂层的稀释率应该控制在一个合理的范围内。在保证镍基合金与基材形成良好冶金结合的前提下,同时考虑对基材的损伤尽可能的小,初步确定较为适宜的齿面加工激光功率密度范围为24.4~35.3 kW·s·cm-2。
为了研究不同能量密度下制得的熔覆层组织与基材的结合程度,利用扫描电子显微镜观察4组不同功率密度下制得的熔覆层与基材融合区域的冶金结合带附近的组织是否存在熔覆缺陷,并使用能谱仪(EDS)分析组织内部的元素分布情况,进一步研究功率密度对涂层内部元素含量变化的影响。不同功率密度下制备的熔覆层的扫描电镜轮廓图如
从

图 4. 不同功率密度下制备的熔覆层底部的显微形貌。(a) 24.4 kW·s·cm-2;(b) 26.5 kW·s·cm-2;(c) 31.8 kW·s·cm-2;(d) 35.8 kW·s·cm-2
Fig. 4. Microstructures of bottom of cladding layers at different power densities. (a) 24.4 kW·s·cm-2;(b) 26.5 kW·s·cm-2; (c) 31.8 kW·s·cm-2; (d) 35.8 kW·s·cm-2
3 齿面双道激光熔覆涂层的制备及分析
3.1 齿面单道激光熔覆涂层的优化思路
上文得到了小模数齿轮表面制备镍基合金涂层较为适宜的激光功率密度为31.8 kW·s·cm-2,熔覆层的晶粒组织主要为Ni、Fe的化合物参与形成的奥氏体组织,而晶间组织为以Cr、C和B元素参与形成的粒状渗碳体组织。但还是可以明显地看到,由于所使用的高斯激光光源能量分布不均,能量过于集中导致齿轮齿面熔深过大,一方面导致对基材的热影响较大,如

图 5. 激光功率密度为31.8 kW·s·cm-2时制备的单道激光熔覆涂层。(a)熔覆层的橫截面形貌;(b)熔覆层的显微组织;(c)熔覆层的宏观形貌
Fig. 5. Single-pass laser cladding coatings obtained with laser power density of 31.8 kW·s·cm-2.(a) Cross-sectional morphology of coating; (b) microstructure of coating; (c) macroscopic morphologies of coatings
针对上述问题,可以设想在保证激光总输入能量不变的条件下,将原有单束激光的能量按一定的能量配比方案分配到两个小光斑上,依次加工齿轮的齿顶部位和齿底部位。
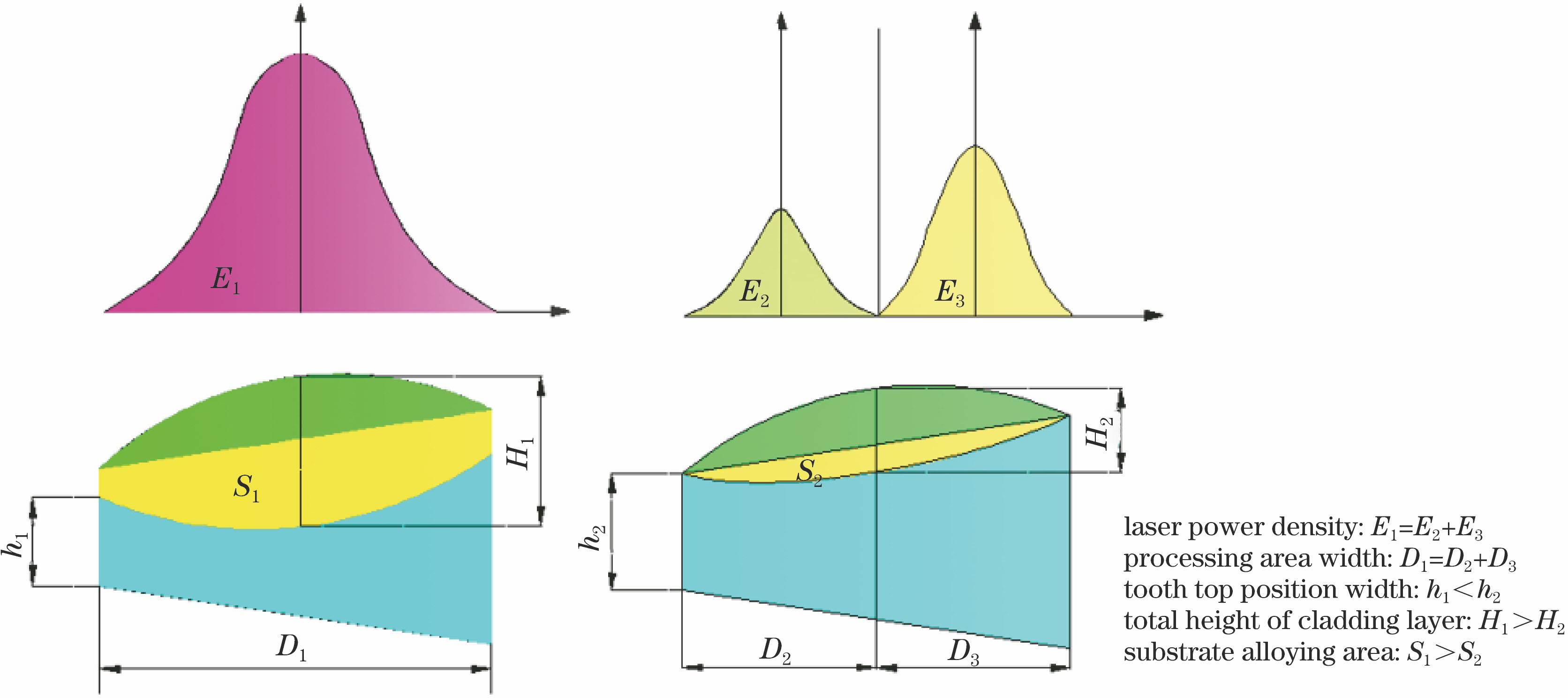
图 6. 双道光束加工示意图及其预期目标改善效果
Fig. 6. Schematic of double-pass laser processing and its expected effect of target improvement
3.2 双道1 mm光斑下熔覆涂层的制备及分析
由于1模数的直齿齿轮齿面的宽度为2.15 mm,这里首先尝试使用两个直径为1 mm的光斑(以下简称“1 mm 光斑”)依次加工齿轮的齿顶部分和齿底部分,通过改善激光器输出的高斯光引起的能量分布不均的现象,提升小模数齿轮齿面熔覆镍基合金涂层的加工效果,如
在齿面单道激光熔覆实验中确定了齿面镍基合金熔覆涂层最适宜的能量密度为31.8 kW·s·cm-2,为了进一步降低单光束加工过程中齿顶部位的烧蚀情况以及基材的熔深,并保证齿底部位的涂层与基体实现较好的结合,设计出两束激光的能量配比方案以及根据功率密度表达式反求出的每道激光的扫描速度,如
表 3. 1 mm光斑下双道激光熔覆的功率密度配比以及每道激光的扫描速度
Table 3. Power-density ratio of double-pass laser cladding with two 1-mm spots and scanning speed of each laser
|
表 4. 1 mm光斑下双道激光熔覆实验参数表
Table 4. Experimental parameters of double-pass laser cladding with two 1-mm spots
|
双道1 mm光斑在不同功率密度配比下的镍基合金熔覆涂层的表面形貌都较好,熔覆层表面均匀连续,没有明显的气孔、夹渣以及裂纹等缺陷;从截面形貌可以看出:不同功率密度配比下的合金涂层与基材的截面形貌存在一定的差异性。为了方便统计出不同加工参数下涂层截面形貌的区别,将涂层截面形貌的参数进行对比,如
表 5. 双道1 mm光斑加工下熔覆层的截面形貌参数
Table 5. Cross-sectional morphology parameters of cladding layers under laser processing by using two 1-mm spots
|
根据
1) 随着第一道光束的功率密度增大,激光对齿轮齿顶部位的烧蚀情况加重,虽然基材表面合金化区域的面积增大,但也会对后期齿轮齿形的修复精度造成一定影响。
2) 熔覆层总高度和稀释率的大小说明了在熔覆过程中有多少基材进入到了合金化区域,稀释率的大小不仅会影响合金涂层与基材的结合效果,还会对熔覆层原有的性能产生影响。在上文已经得出镍基合金熔覆涂层的涂层稀释率应大于25.2%,这4组样本均满足要求。
3) 合金化区域底边边线的宽度说明了基材表面有效合金强化区域面积的大小,该值越大,说明齿面合金化区域越大,对加工质量的提升越明显。
综上所述,双道激光加工工艺可明显改善单道齿面镍基合金熔覆涂层的表面质量以及基材的烧蚀、热影响等现象,当选择双道1 mm光斑进行齿面镍基合金加工时,齿顶部位和齿底部位双道激光的功率密度比选择4∶6时较为适宜。
3.3 双道1.5 mm光斑下熔覆涂层的制备及分析
除了两个小光斑刚好覆盖待加工齿面的面积外,还可以考虑两个中等大小的光斑在一定搭接率下覆盖待加工齿面的面积,如
与双道1 mm激光光斑加工过程类似,在保证总能量密度为31.8 kW·s·cm-2不变的情况下,为了进一步降低单光束加工过程中齿顶部位的烧蚀情况以及基材的熔深,并保证齿底部的涂层与基材有较好的结合,设计出两束激光的能量配比方案,并根据功率密度表达式反求出每道激光的扫描速度,如
双道1.5 mm光斑加工出的镍基合金熔覆涂层的截面形貌在不同功率密度配比下有一定的变化趋势,通过观察发现熔覆层截面形貌主要呈现两种状态,如
在显微镜下观察熔覆层显微组织时可以发现:当双道光束的功率密度相差较大时,齿顶部位的组织与齿底部位的组织明显不同,由于激光功率密度较低,齿顶部位组织内部的温度梯度较小,涂层组织由针状、棒条状、块状相互交错分布,涂层组织的再结晶现象不明显,而且熔覆层与基材之间的亮白色冶金结合带较窄,使得两者之间的结合效果较差,没有起到对整个轮齿表面强化的目的;当逐渐增大齿顶部位的第一束激光,并减小齿底部位第二束激光输入时,齿顶部位输入的能量大于其传递散失的热量,使得齿顶部位的基材逐渐受热熔化进入熔池中,与镍基合金发生冶金结合,所以熔覆层截面过渡圆弧的弧长明显变长,基材表面的熔深明显变大,齿轮表面有效合金化区域的面积明显变大,有效提升了齿面激光熔覆的工艺效果,如
表 6. 1.5 mm光斑下双道激光熔覆实验参数表
Table 6. Experimental parameters of double-pass laser cladding with 1.5-mm spots
|
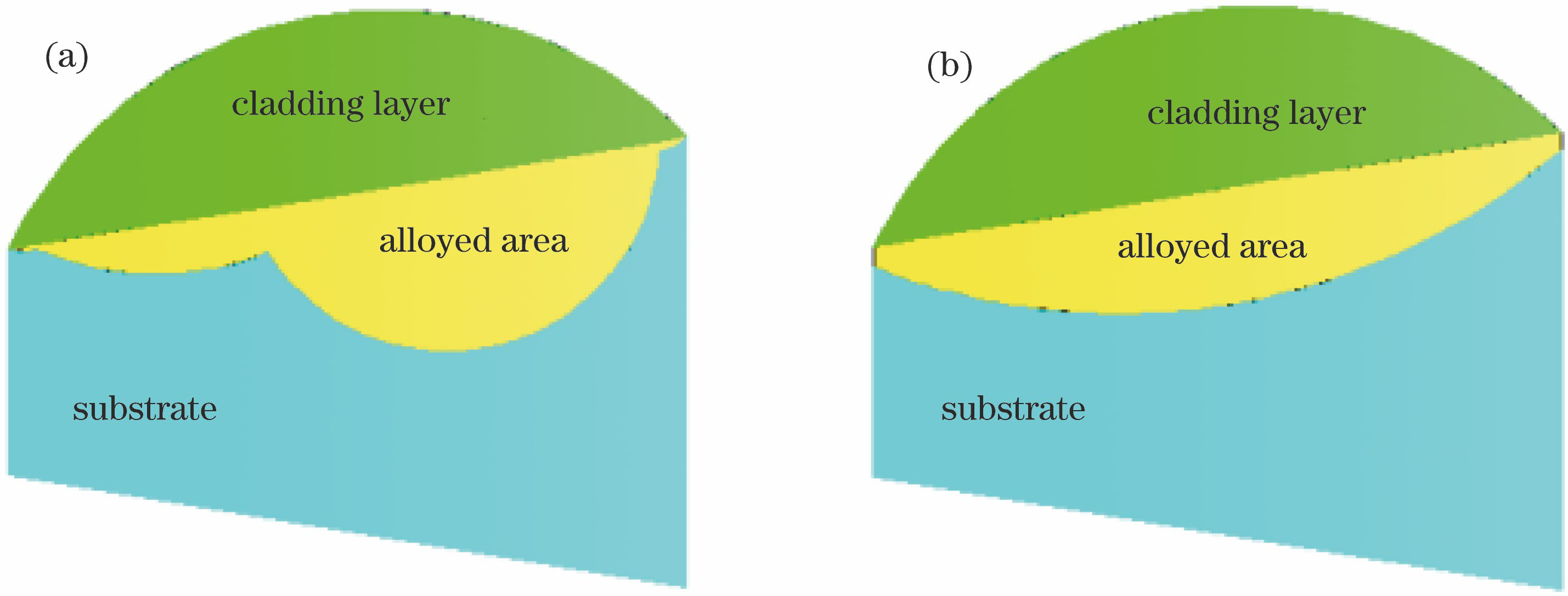
图 9. 不同加工工艺下的熔覆层截面形貌。(a)双道光斑功率密度相差较大;(b)双道光斑功率密度相差较小
Fig. 9. Cross-sectional morphologies of cladding layers under different processing techniques. (a) Large difference between power densities of double-pass laser spots; (b) small difference between power densities of double-pass laser spots
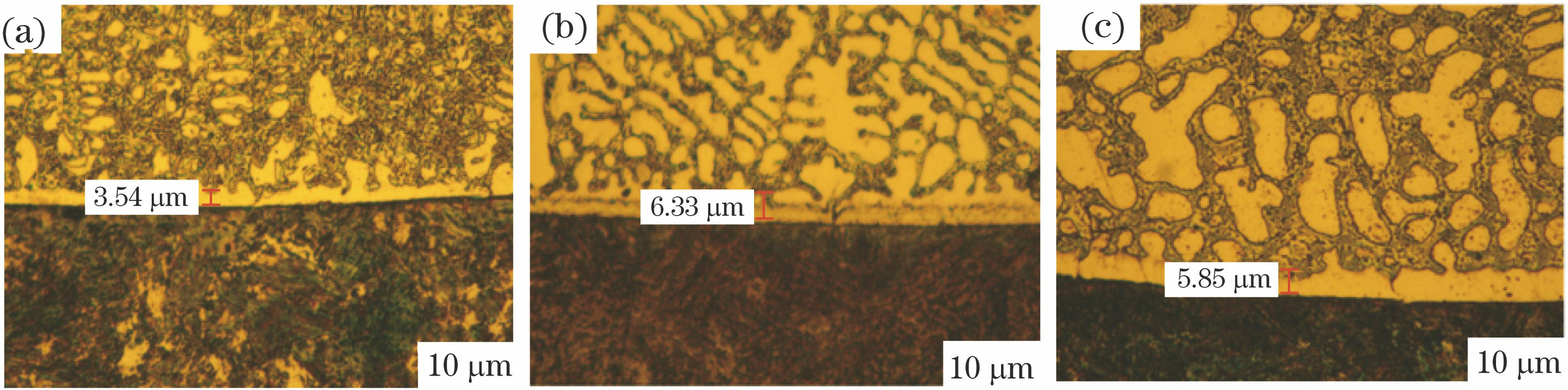
图 10. 不同工艺参数下得到的合金涂层的截面组织。(a)齿顶输入的激光功率密度大于12.72 kW·s·cm-2;(b)齿底输入的激光功率密度大于19.08 kW·s·cm-2;(c)齿顶和齿底输入的激光功率密度为15.9 kW·s·cm-2
Fig. 10. Cross-sectional microstructures of alloy coatings under different process parameters. (a) Input laser power density at tooth top of gear is greater than 12.72 kW·s·cm-2; (b) input laser power density at tooth bottom of gear is greater than 19.08 kW·s·cm-2; (c) input laser power densities at tooth top and bottom of gear are both 15.9 kW·s·cm-2
此外双道光斑功率密度差异应该满足既不对齿顶产生过度烧蚀和对基材的热影响较小,又能保证在齿底部位形成牢固的冶金结合,控制合金涂层稀释率在合理的范围内。为了确定最适宜的激光能量分配密度以及光斑搭接率,这里将剩下的6组熔覆层截面形貌的参数列于
综合考虑以上因素,选择双道1.5 mm光斑进行齿面镍基合金加工时,齿顶部位和齿底部位双道激光的功率密度比为4∶6,且搭接率为40%时,熔覆层的表面质量较好,比单道加工对基材的烧蚀和热影响都要低一些,宏观上看也没有出现气孔、夹渣以及裂纹等宏观缺陷。
表 7. 双道1.5 mm光斑加工下的熔覆层截面形貌参数
Table 7. Cross-sectional morphology parameters of cladding layers under laser processing by using two 1.5-mm spots
|
4 单道与双道激光工艺下熔覆层质量的对比分析
4.1 齿顶烧蚀程度和涂层稀释率的对比分析
由
在高倍显微镜下观察单道熔覆层和不同加工工艺下的双道熔覆层的截面组织可以发现组织的形态分布具有明显的差异性,如
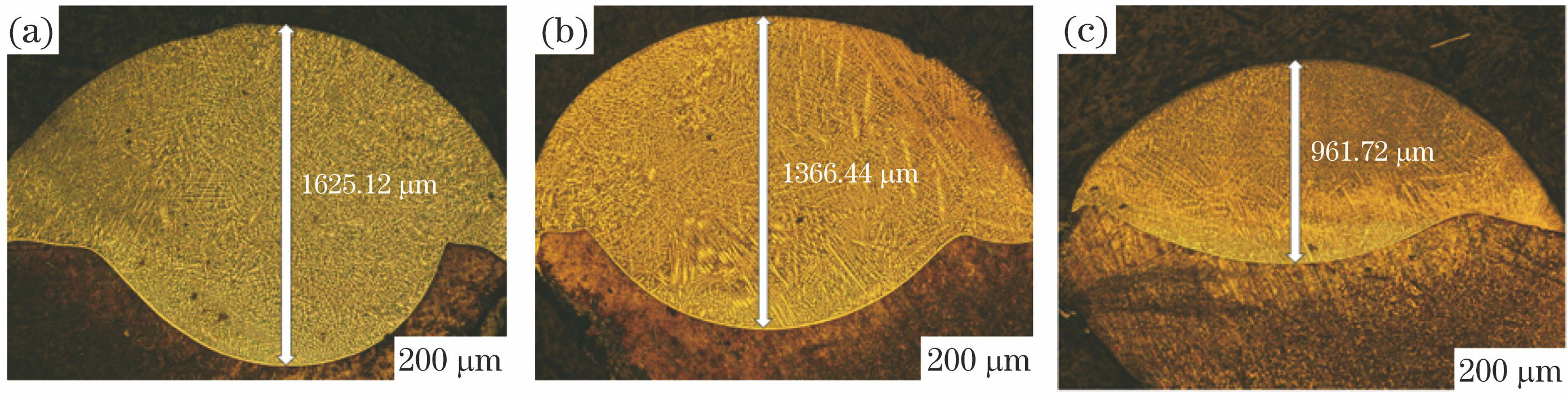
图 11. 不同加工工艺下熔覆层截面的熔深的对比。(a)单道激光工艺参数:P =250 W,u =0.5 mm/s,D =2 mm;(b)双道1.5 mm激光工艺参数:P =250 W,u 1=1.67 mm/s,u 2=1.12 mm/s,D =1.5 mm,η =40%;(c)双道1 mm激光工艺参数:P =250 W,u 1=2.5 mm/s,u 2=1.67 mm/s,D =1 mm
Fig. 11. Comparison of penetration depths of cladding layers under different processing techniques. (a) Single-pass laser process parameters: P =250 W, u =0.5 mm/s, D =2 mm; (b) double-pass 1.5-mm laser process parameters: P =250 W, u 1=1.67 mm/s, u 2=1.12 mm/s, D =1.5 mm, η =40%; (c) double-pass 1 mm-laser process parameters: P =250 W,
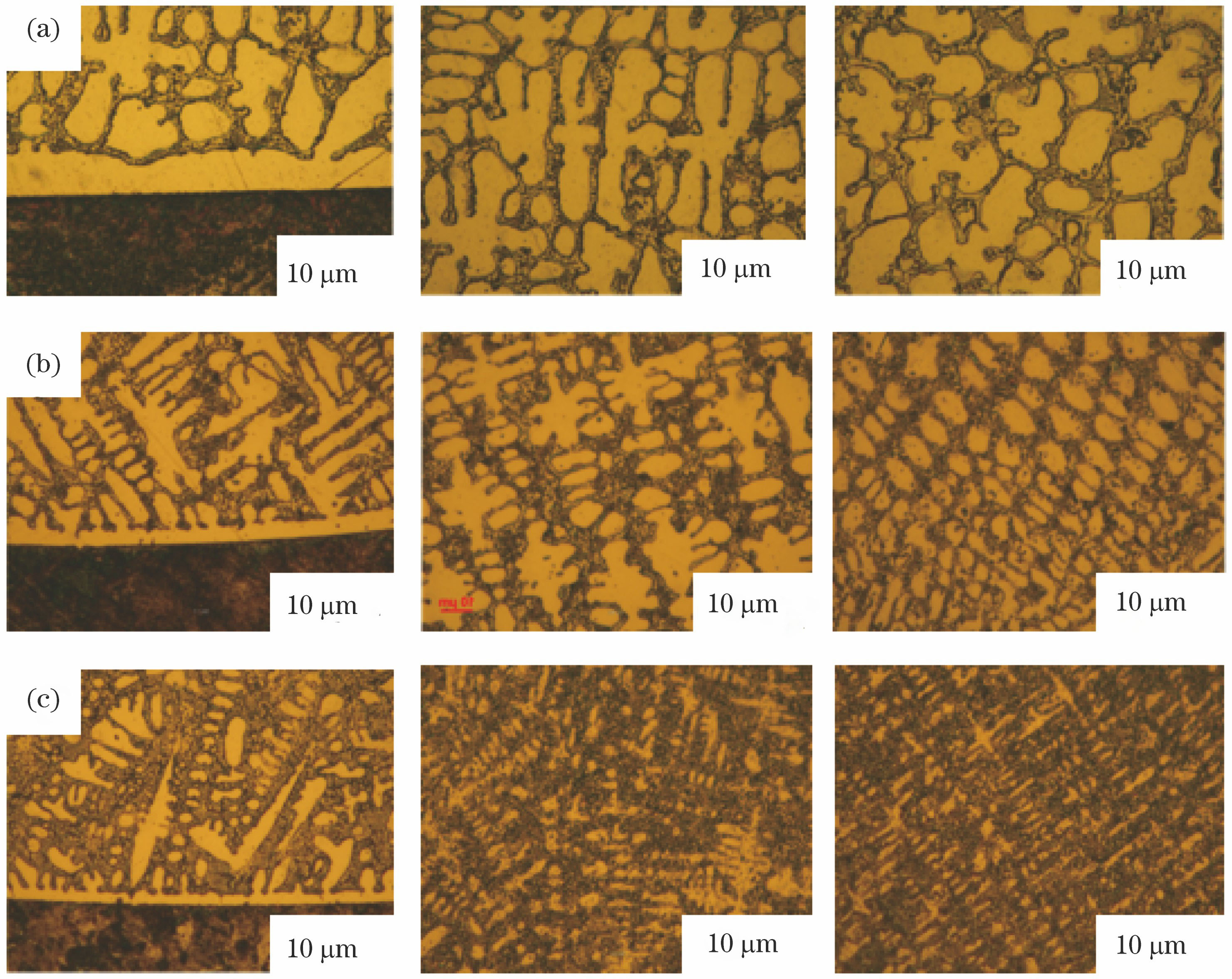
图 12. 不同加工工艺下制备的镍基合金熔覆涂层的截面形貌。(a)单道激光加工;(b)双道激光搭接加工;(c)双道激光独立加工
Fig. 12. Cross-sectional morphologies of nickel-based alloy cladding coatings under different processing techniques.(a) Single-pass laser processing; (b) double-pass laser lap processing; (c) double-pass laser independent processing
根据Hoadley提出的以激光束为热源的热输入模型[5](
式中:
熔覆层合金的结晶形态受熔池内液相成分和形状控制因子的影响[6]。形状控制因子是结晶方向上的温度梯度
将不同加工工艺下得到的XRD图谱进行对比分析。
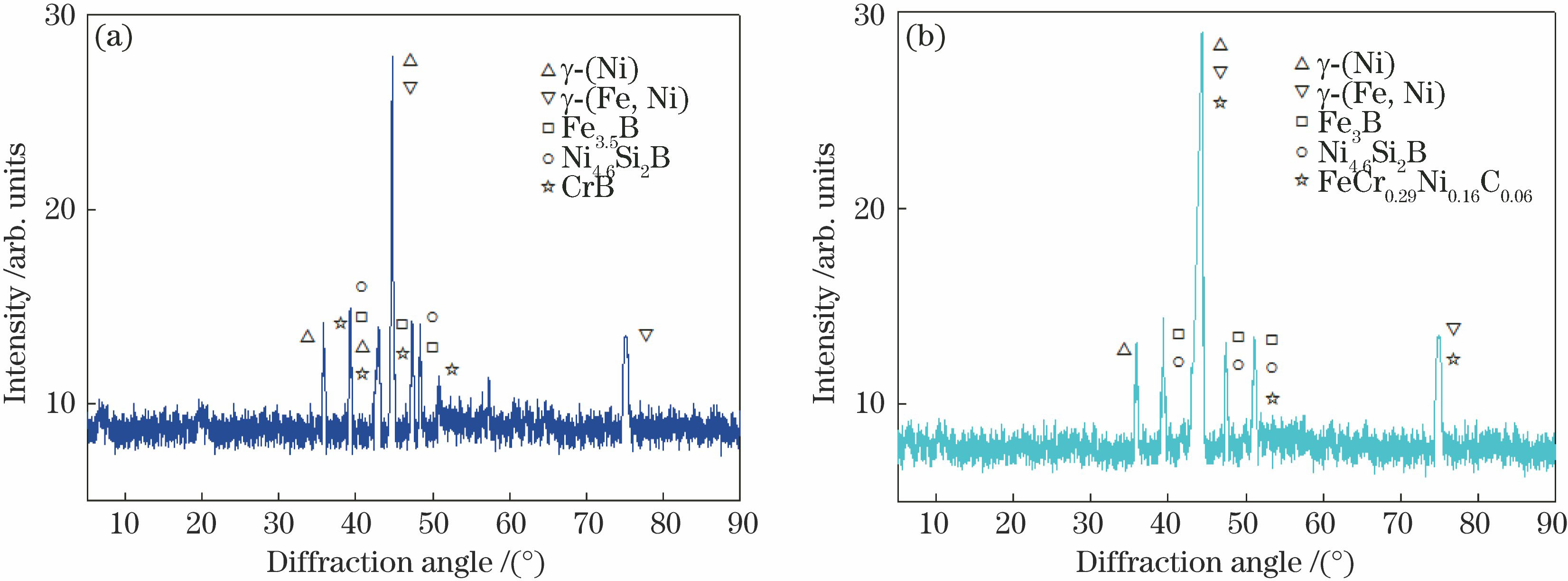
图 15. 不同加工工艺下制备的镍基合金熔覆涂层的XRD图谱。(a)双道1 mm光斑;(b)双道1.5 mm光斑
Fig. 15. XRD spectra of nickel-based alloy cladding coatings under different processing techniques. (a) Double-pass 1-mm laser spots; (b) double-pass 1.5-mm laser spots
4.2 熔覆层的显微硬度对比
从
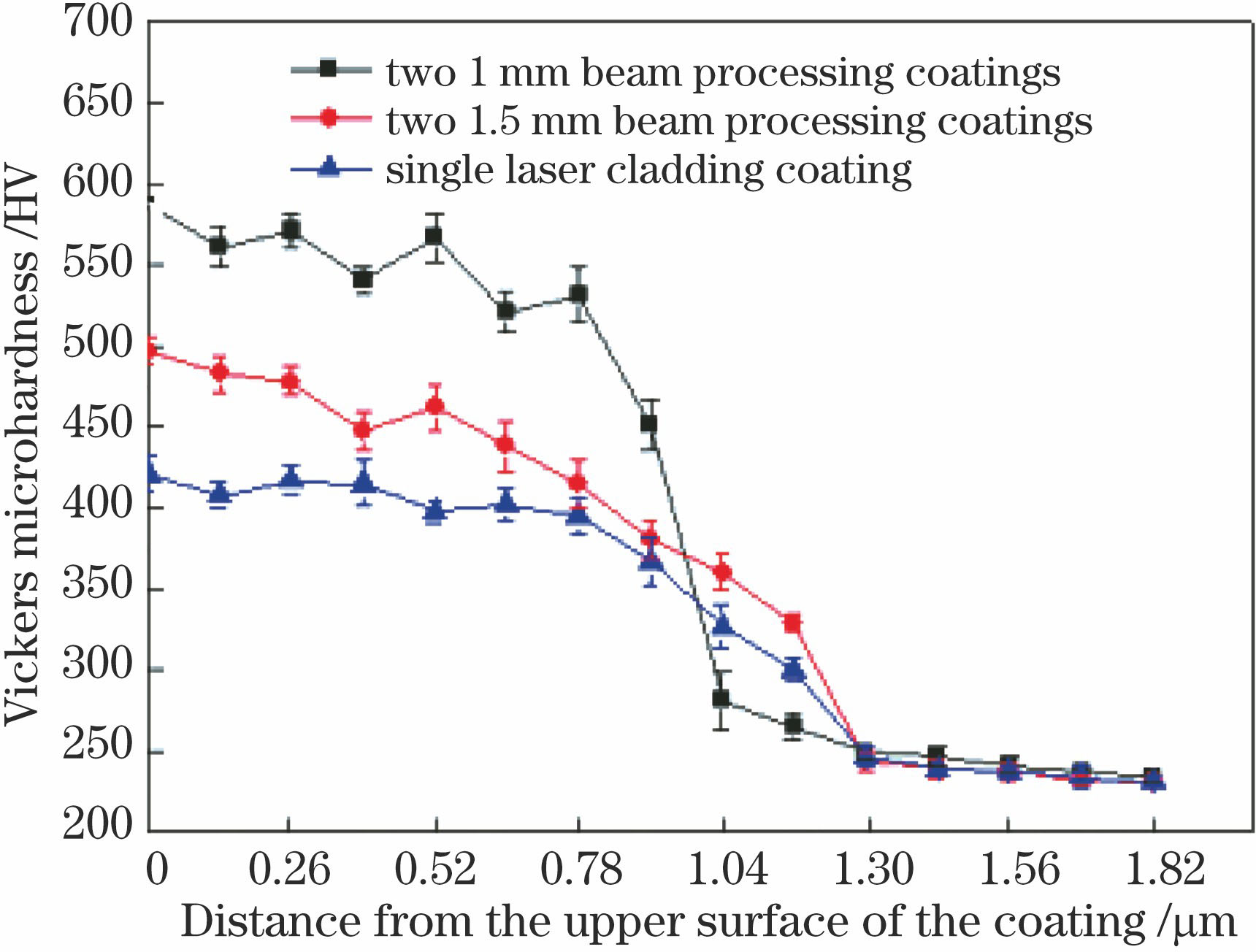
图 16. 不同加工工艺下制备的熔覆层截面的显微硬度变化曲线
Fig. 16. Variation curves of cladding coatings' cross-sectional microhardness under different processing techniques
5 结论
围绕小模数齿轮表面制备镍基合金涂层的微观组织和工艺参数进行了实验研究。采用双光束激光熔覆手段改善单光束熔覆过程中易出现的熔覆缺陷问题,通过双道激光熔覆工艺改善原有高斯光源的能量分布状态,使熔覆层内部的温度梯度明显降低,加快涂层的凝固速度,该过程对熔覆层组织的细化作用明显。此外,双道激光熔覆工艺下制备的熔覆层中晶状奥氏体析出较少,粒状渗碳体组织较多,平均显微硬度明显高于单道激光熔覆制备的熔覆层。实验得到了在1模数齿轮齿面加工1 mm厚镍基合金涂层的工艺参数为:
[1] 马贤智.[\s]{1}实用机械加工手册[M].[\s]{1}沈阳:[\s]{1}辽宁科学技术出版社,[\s]{1}2002.[\s]{1}
Ma[\s]{1}XZ.[\s]{1}Practical[\s]{1}mechanical[\s]{1}working[\s]{1}manual[M].[\s]{1}Shenyang:[\s]{1}Liaoning[\s]{1}Science[\s]{1}and[\s]{1}Technology[\s]{1}Publishing[\s]{1}House,[\s]{1}2002.[\s]{1}
[2] 何力佳, 赵晓杰, 王函, 等. 45号钢基体光纤激光熔覆镍基合金的组织与性能[J]. 特种铸造及有色合金, 2015, 35(9): 909-912.
[3] 鲍志军.[\s]{1}小模数齿轮激光熔覆修复工艺试验研究[D].[\s]{1}上海:[\s]{1}上海海事大学,[\s]{1}2007.[\s]{1}
Bao[\s]{1}ZJ.[\s]{1}Experimental[\s]{1}study[\s]{1}on[\s]{1}repair[\s]{1}process[\s]{1}of[\s]{1}small[\s]{1}module[\s]{1}gear[\s]{1}laser[\s]{1}cladding[D].[\s]{1}Shanghai:[\s]{1}Shanghai[\s]{1}Maritime[\s]{1}University,[\s]{1}2007.[\s]{1}
[4] 刘洪喜, 曾维华, 张晓伟, 等. 不锈钢表面多道激光熔覆Ni基涂层的组织与性能[J]. 光学精密工程, 2011, 19(7): 1515-1523.
[7] 路阳, 巩禄, 杨效田, 等. 表层绝热对定向凝固Ni60合金涂层凝固行为的影响[J]. 中国表面工程, 2018, 31(4): 130-139.
[9] 刘亚楠, 孙荣禄, 牛伟, 等. Ti811表面激光熔覆复合涂层的微观组织及摩擦磨损性能[J]. 中国激光, 2019, 46(1): 0102010.
[10] 赵淑珍, 金剑波, 谢敏, 等. 扫描速率对激光熔覆Cu80Fe20偏晶涂层组织与耐磨性能的影响[J]. 中国激光, 2019, 46(3): 0302005.
Article Outline
刘干成, 黄博. 小模数齿轮齿面双道激光熔覆工艺[J]. 中国激光, 2019, 46(10): 1002009. Gancheng Liu, Bo Huang. Double-Pass Laser Cladding Process for Small-Modulus Gear-Tooth Surface[J]. Chinese Journal of Lasers, 2019, 46(10): 1002009.