5083铝合金真空激光焊缝成形的影响因素
下载: 1040次
1 引言
5083铝合金不仅具有优异的比强度和低温力学性能,还拥有良好的耐腐蚀性和可加工性,被广泛应用于船舶、汽车、轨道交通、航空航天等领域[1-5],其焊接应用是研究热点之一。传统焊接方法在中厚板铝合金的焊接中存在诸多不足,如焊材填充量大、热影响区较宽、焊接效率低等。高功率激光焊接作为一种新型焊接方法,为该领域提供了一种全新的解决手段,相关的研究和应用逐渐增多[6-10]。然而,高功率激光焊接铝合金也存在一些难题,一方面,铝合金具有高导热性和高反射率的特点,对激光能量的利用率低,熔深不够大[8];另一方面,铝合金在激光焊接中极易产生两类气孔,一类是氧化膜吸附的水分带来的氢气孔,另一类是匙孔塌陷形成的气孔[11-12]。
近年来,国内外学者提出了包括表面清理、复合焊、优化工艺参数及真空焊在内的多种解决方法[13-18]。Haboudou等[13]对铝合金的钇铝石榴石(YAG)激光焊接进行了研究,认为焊接表面的预处理可以有效减小焊后气孔率。王治宇[14]研究了YAG激光与熔化极稀有气体保护(MIG)电弧复合焊接对焊缝形貌的影响,发现激光电弧的交互作用可在一定范围内增大熔深,但随着电弧功率的增大先增后减。Sánchez-Amaya等[15]研究发现,激光焊接速度减慢时,铝合金的焊缝尺寸有一定增大。Katayama等[16]分别用高功率CO2激光器和YAG激光器在真空下焊接A5083铝合金,结果显示二者熔深都有所增大,并且负压下气孔数量明显减少,在压力为0.4 kPa时气孔基本消失。Cai等[17]采用5 kW光纤激光器对10 mm厚的A5083铝合金在不同环境压力下焊接的熔深特点及小孔行为进行了研究对比,结果表明,常压下熔深为4.9 mm;当压力为10 Pa时,熔深可达8.7 mm。目前,学者们对中厚板铝合金的真空激光焊接焊缝成形及缺陷影响因素已有一定研究,但基于正交法分析不同因素的影响程度和影响机理的研究鲜有报道。
为了综合对比不同条件对焊缝熔深及气孔缺陷的影响程度及影响机理,本文基于正交试验,研究了激光功率、焊接速度、环境压力等关键因素对厚度为30 mm的铝合金激光焊缝成形及其焊接质量的影响规律,分析了其对焊缝中气孔缺陷的影响程度及影响机理,为5083铝合金中厚板激光焊缝成形的控制和气孔缺陷的抑制提供了参考。
2 试验材料与方法
2.1 试验材料与装置
试验所用材料为30 mm厚的5083铝合金,焊前使用NaOH和浓HNO3溶液对铝板试样进行清洗,除去表面氧化膜及油污,并进行烘干处理。试验在一个真空激光焊接试验平台中进行,如
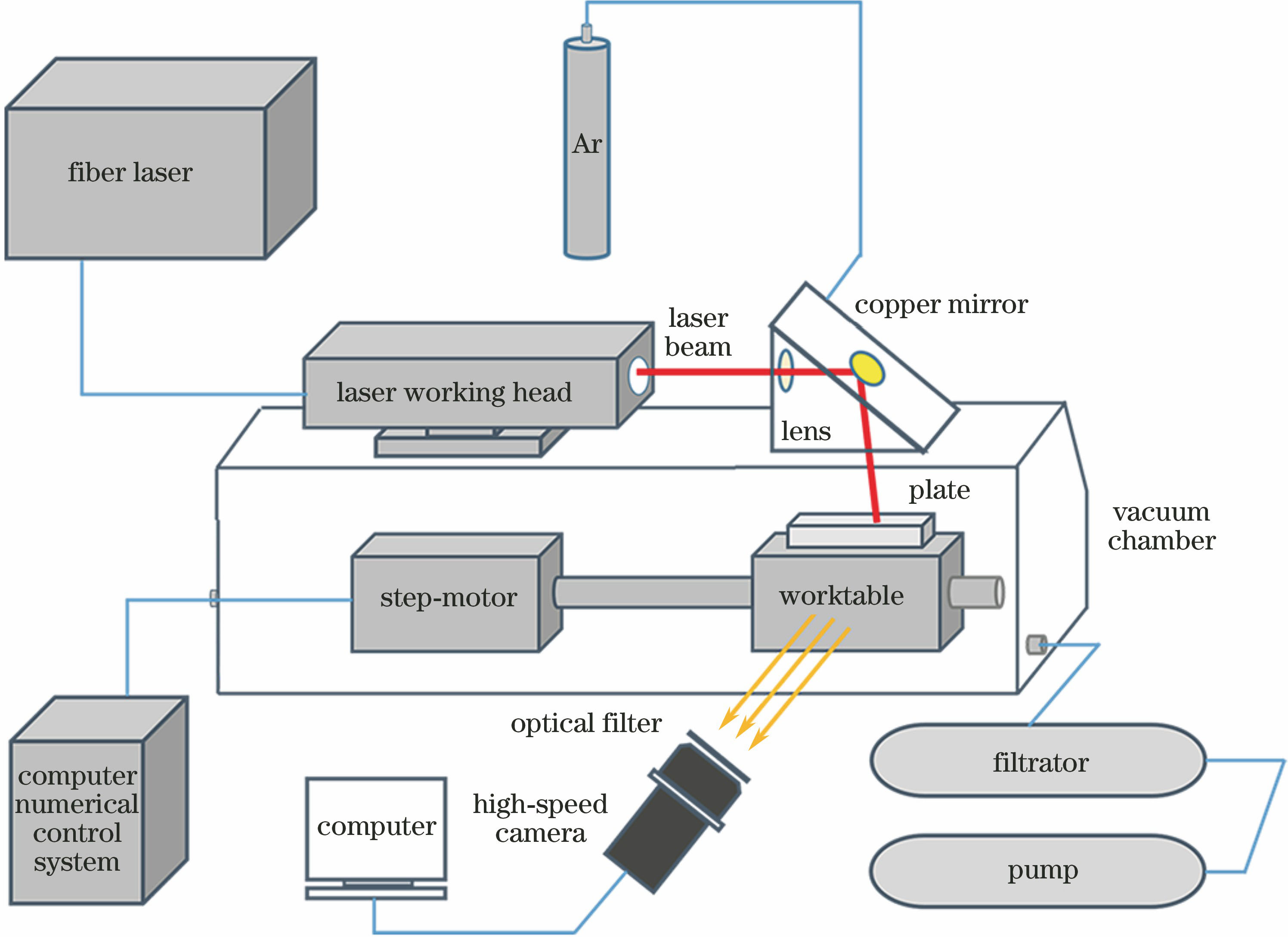
图 1. 真空激光焊接试验平台的示意图
Fig. 1. Schematic of experimental platform for laser welding in vacuum
2.2 试验与表征方法
为探究不同因素对焊缝成形及气孔的影响程度,设计三因素四水平正交试验表,如
表 1. 正交试验表
Table 1. Orthogonal tests
|
采用如下参数对正交试验结果进行评估:
1) 某因素下某水平的指标均值
2) 极差
3) 各因素
正交试验结果评价指标包括气孔率、熔深、深宽比。气孔率
式中
为了进一步探究环境压力对激光焊接的影响,通过高速摄影采集焊接过程中的金属蒸气羽烟图像并对其进行图像处理,引入平均灰度
式中
面积像素比的计算公式为
式中
3 试验结果与分析
3.1 不同环境压力下的金属蒸气羽烟特征
在不同条件下进行焊接,采集焊接过程中的金属蒸气羽烟图像,其中环境压力对焊接过程的影响最为明显,不同环境压力下金属蒸气羽烟的高速摄影典型结果如
激光的折射、散射和吸收与金属蒸气羽烟的高度、密度、温度及吸收系数等有关。图像的亮度可以在一定程度上体现金属蒸气羽烟的密度;图像面积的大小反映出高温区的大小,在一定程度上反映了吸收激光能量的多少。对采集到的金属蒸气羽烟图像进行处理,用平均灰度来表征其平均辐射光强,用图像面积来表征其二维尺度。

图 2. 不同压强下金属蒸气羽烟的高速摄影图像。(a) 101 kPa;(b) 80 kPa;(c) 50 kPa;(d) 20 kPa;(e) 5 kPa
Fig. 2. Images of plasma plume captured by high speed camera under different pressures. (a) 101 kPa; (b) 80 kPa; (c) 50 kPa; (d) 20 kPa; (e) 5 kPa
对图像进一步处理并计算平均灰度和面积像素比,结果如
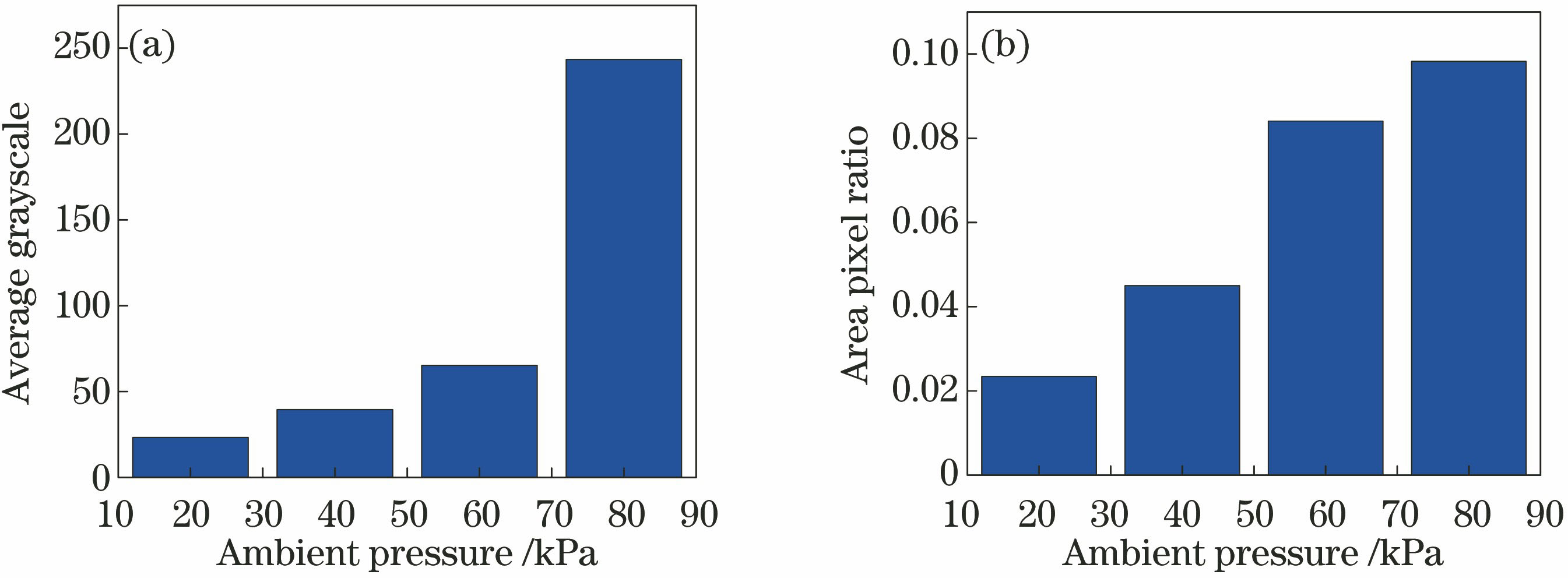
图 3. 不同压强下的羽烟平均灰度及羽烟面积像素比。(a)平均灰度;(b)面积像素比
Fig. 3. Average grayscales and area pixel ratios of plasma plume under different pressures. (a) Average grayscale; (b) area pixel ratio
3.2 正交试验结果
针对正交试验所得的焊缝,利用表征方法对气孔率、熔深、熔宽、深宽比等进行统计,结果如
表 2. 正交试验结果
Table 2. Results of orthogonal tests
|
对
对气孔率而言,均值越小越好。计算结果表明,三个因素中环境压力的
对
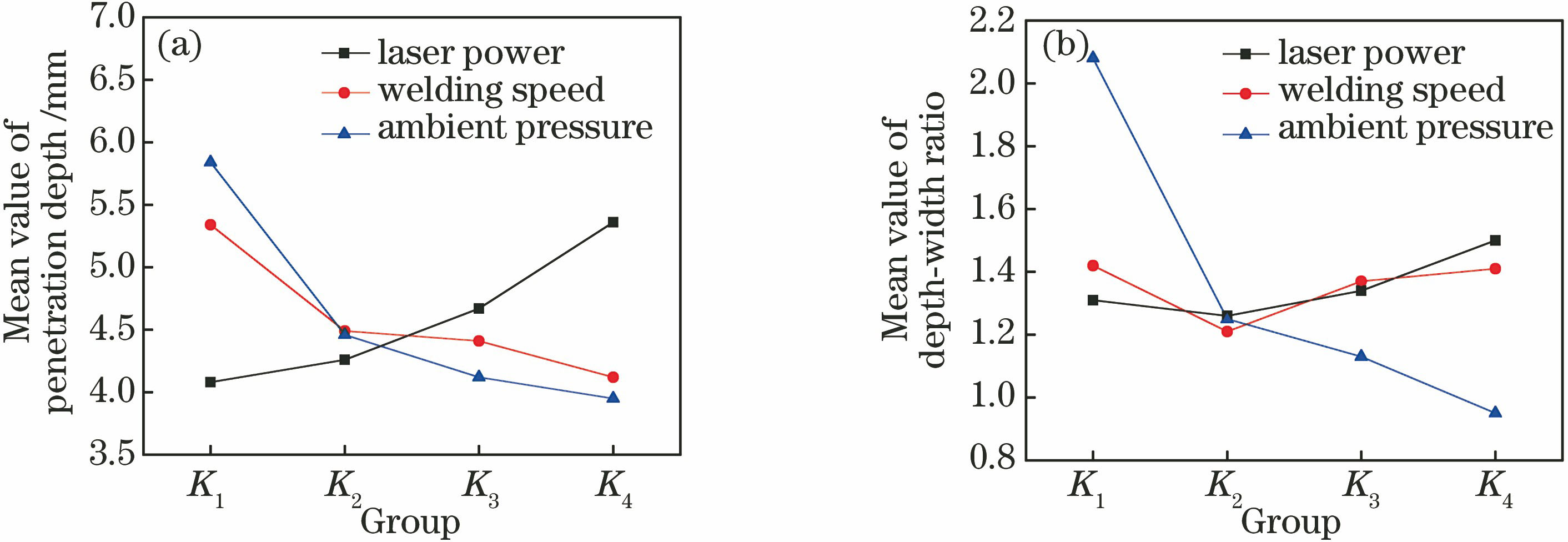
图 5. 各因素对熔深与深宽比的影响。(a)熔深;(b)深宽比
Fig. 5. Effects of each factor on penetration depth and depth-width ratio. (a) Penetration depth; (b) depth-width ratio
势。当激光功率从6.0 kW增大至7.5 kW时,深宽比先略微减小后增大;当焊接速度从1.0 m/min增大至1.6 m/min时,深宽比的变化曲线与功率改变时的相似,先减小后增大,总体变化趋势不明显,而环境压力对焊缝深宽比有显著影响。计算结果表明,三个因素中环境压力因素的
3.3 焊缝成形特点及其影响因素分析
3.3.1 环境压力对焊缝成形的影响
正交试验结果表明,环境压力对焊缝熔深、气孔等均有较大影响。保持焊接功率为7.5 kW、焊接速度为1.0 m/min不变,设定环境压力分别为101,15,10,5 kPa,进行激光焊接试验。焊后观察焊缝表面成形及横截面形貌,结果如
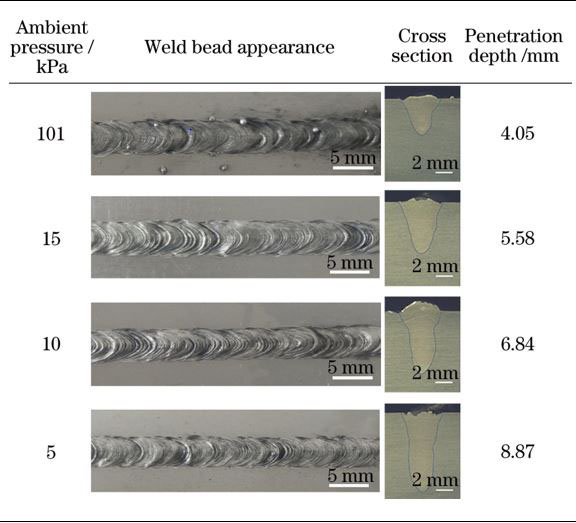
图 6. 不同激光功率下的焊缝横截面。(a) 6 kW;(b) 8 kW
Fig. 6. Cross-sections of welds under different laser powers. (a) 6 kW; (b) 8 kW
从焊缝表面可以看出,随着压强的降低,焊缝表面的飞溅逐渐减少,最后基本消失,焊缝表面更为均匀;焊缝横截面的形貌由大气环境下的倒三角形变为针形,并且这一变化发生于15 kPa以下的压强条件;当压强降至5 kPa时,熔深约为常压下的2倍。
压强降低使熔深增大的原因主要有以下几方面。1) 随着环境压力的降低,金属的熔沸点降低,相同激光能量下小孔内部的金属更容易气化,能量利用率提高,熔深增大[19]。2) 由
3.3.2 激光功率对焊缝成形的影响
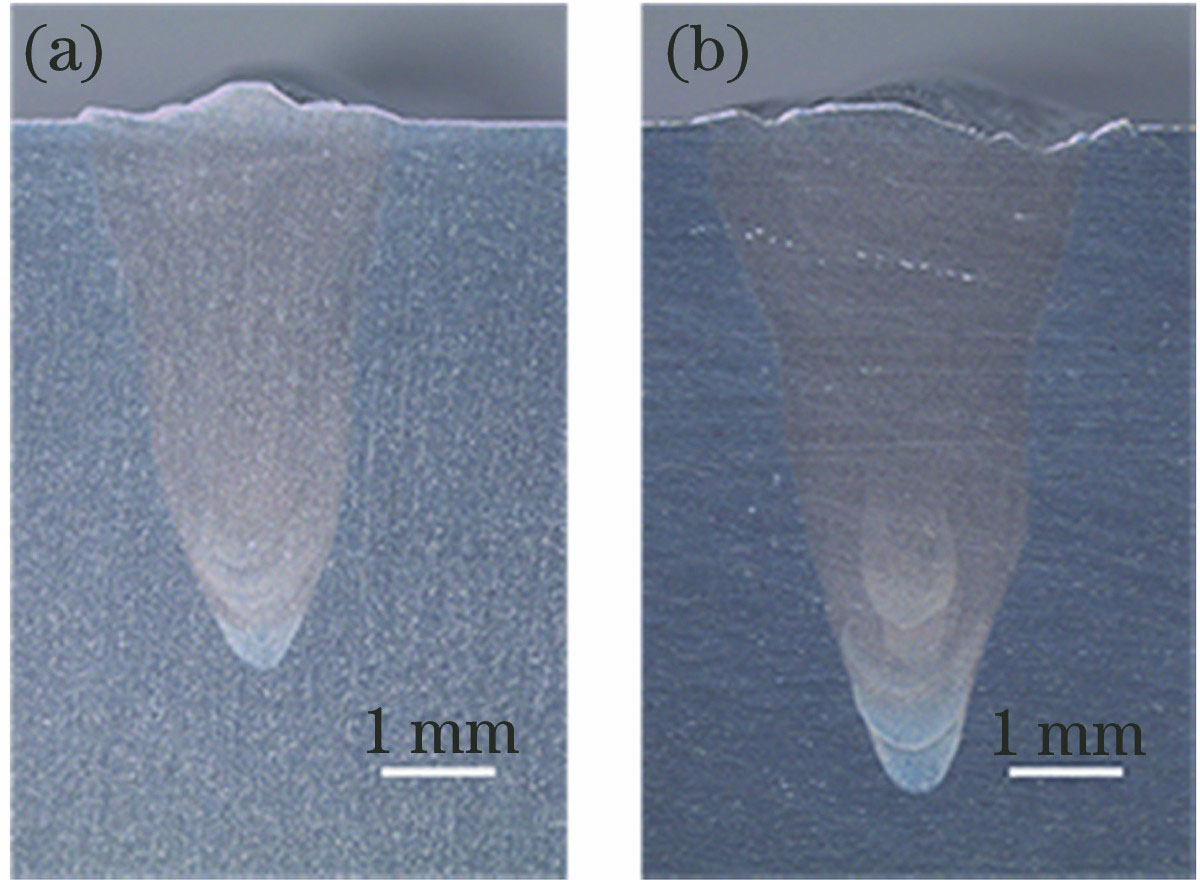
图 7. 不同焊速下的焊缝横截面。(a) 1.0 m·min-1;(b) 1.4 m·min-1
Fig. 7. Cross-sections of welds under different welding speeds. (a) 1.0 m·min-1; (b) 1.4 m·min-1
3.3.3 焊接速度对焊缝成形的影响
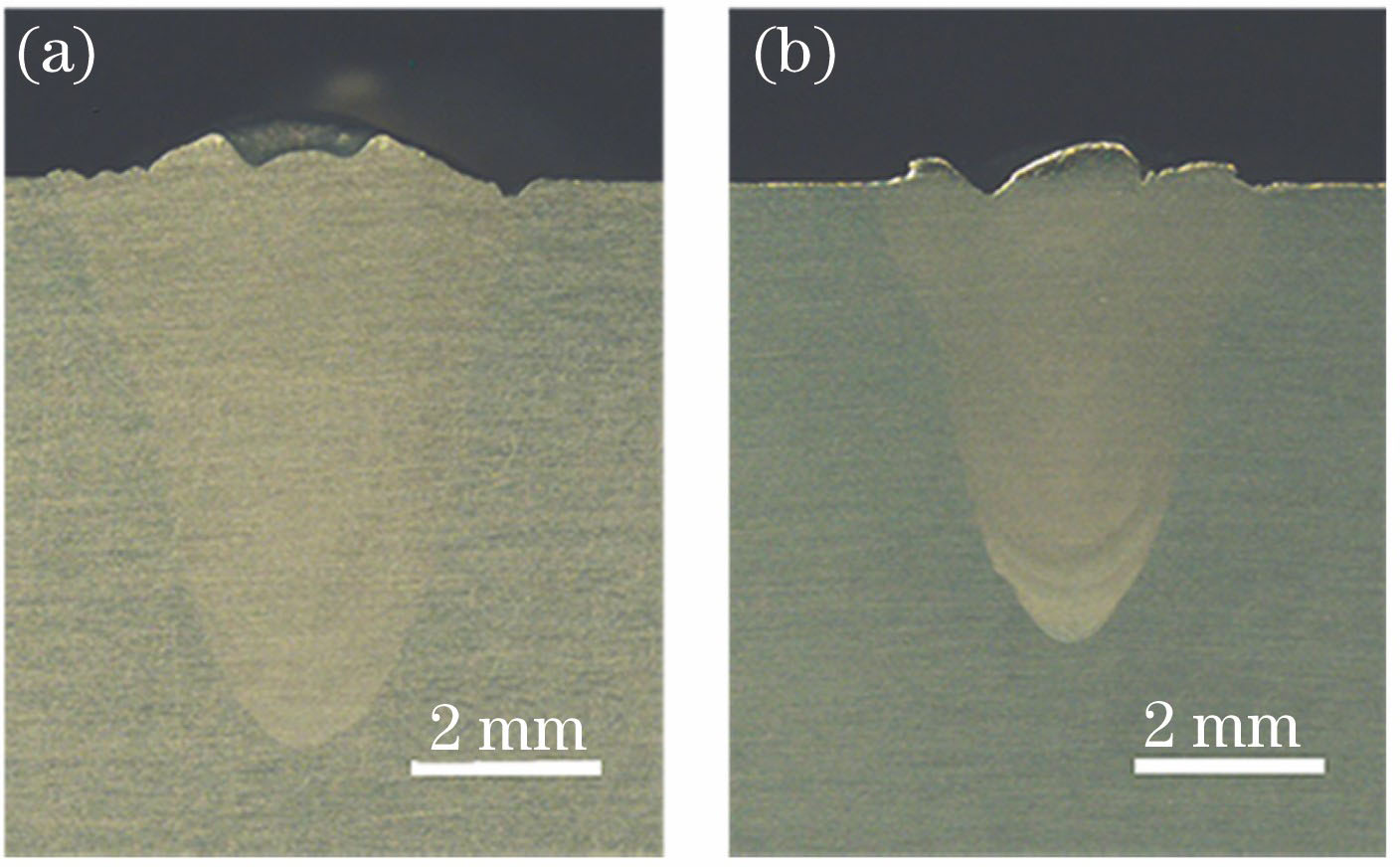
图 8. 不同压强下的气孔分布。(a) 101 kPa;(b) 15 kPa;(c) 5 kPa
Fig. 8. Pore distributions under different pressures. (a) 101 kPa; (b) 15 kPa; (c) 5 kPa
3.4 气孔形成特点及其影响因素分析
3.4.1 环境压力对气孔形成的影响
在铝合金的激光焊接中常常会出现气孔,这类焊接缺陷会减小焊接接头的有效载荷横截面面积,也会造成应力集中,降低焊接接头的力学性能。在保持其他焊接工艺参数不变的条件下,观察不同环境压力下激光焊接试样的焊缝中心纵截面上的气孔缺陷,并通过图像处理软件对焊缝气孔分布和气孔率等进行分析,结果如
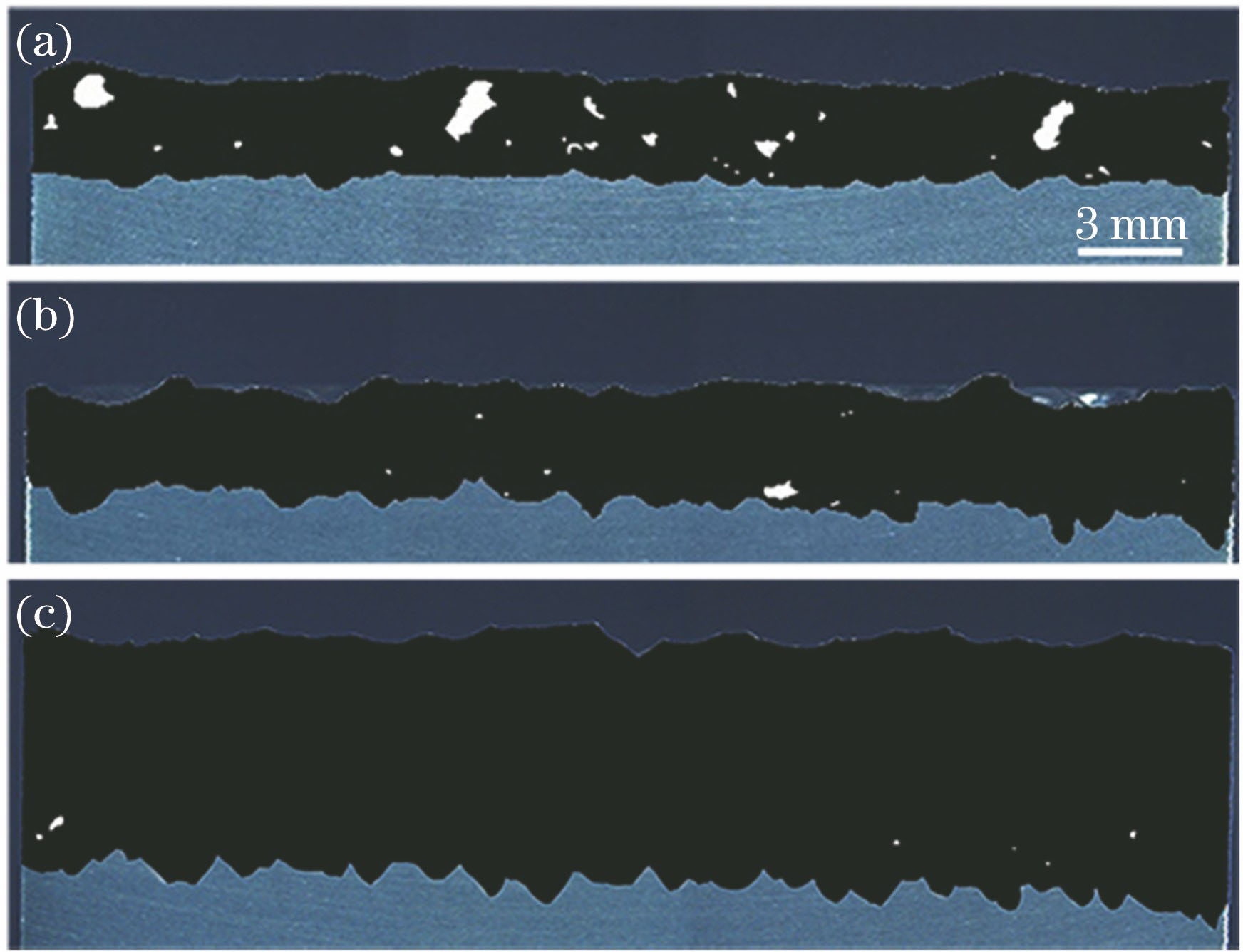
图 9. 中、下部气孔的微观特征。(a)气孔形貌;(b)气孔壁褶皱;(c)气孔内堆积物
Fig. 9. Microscopic features of pores in middle-bottom parts. (a) Pore morphology; (b) fold of pore wall; (c) deposits in pore
统计焊缝中心纵截面上的气孔率可知,在101,15,5 kPa压强下的气孔率分别为3.740%,0.304%,0.057%;压强为5 kPa时气孔几乎消失,仅在焊缝底部存有少量尺寸较小的气孔。从气孔形貌来看,气孔基本呈现不规则形状,且成一定角度,该角度与激光的入射倾斜角度近似,呈现出明显的工艺性气孔特点。从气孔的分布来看,在常压下,焊缝的上、中、下各部分均有气孔;当环境压力降至15 kPa时,在焊缝的中、下部分有气孔;当环境压力降至5 kPa时,仅在焊缝底部有少量气孔。即随着环境压力的降低,焊缝近表面的气孔先消失,而后中、下部的气孔减少。
选取焊缝中、下部较小的气孔,通过扫描电子显微镜(SEM)观察其形貌,结果如
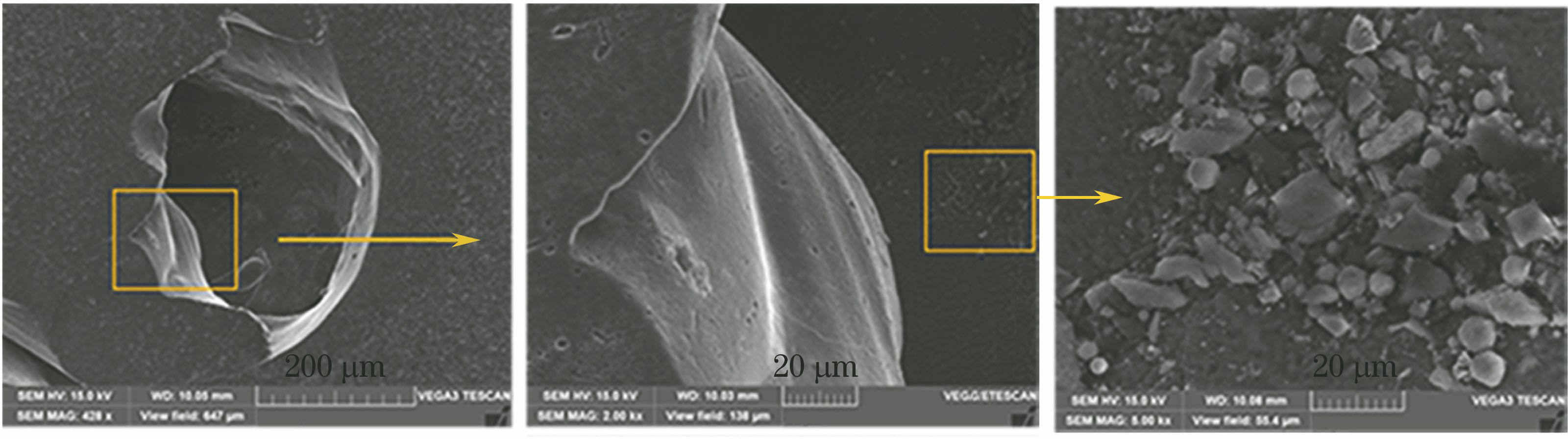
图 10. 熔池流动示意图。(a)常压;(b)真空
Fig. 10. Schematic of pool flow patterns. (a) Normal pressure; (b) vaccum
2.35%。推测主要物质为Al和Mg及其氧化物,是小孔塌陷时来不及溢出的金属蒸气被封闭于气泡中沉积所致[21]。
焊缝中气孔的形成主要取决于焊接过程中气泡的产生和溢出两个阶段。在铝合金深熔焊接过程中,除了材料本身因素造成的冶金型气孔(试验在Ar环境下进行,可忽略),还存在小孔坍塌形成的工艺性气孔。常压下,由于金属蒸气羽烟的影响,激光能量难以均匀作用于整个小孔,小孔上部产生能量聚集,大量液态金属聚集于熔池上部,对小孔的稳定性极为不利,同时激光与金属蒸气羽烟的相互作用会使小孔中激光能量的传递产生周期性的波动[22],造成熔池及小孔的剧烈波动,导致小孔塌陷形成气泡。当环境压力降低时,小孔上方的金属蒸气羽烟受到抑制,小孔中激光能量密度较高且更加均匀,焊接熔池变窄,小孔更细长并趋于稳定,小孔不易发生坍塌,气泡数量和尺寸大大减小。
随着环境压力的降低,熔池中金属的流动方式发生改变[20],气泡的溢出方式亦发生变化,如
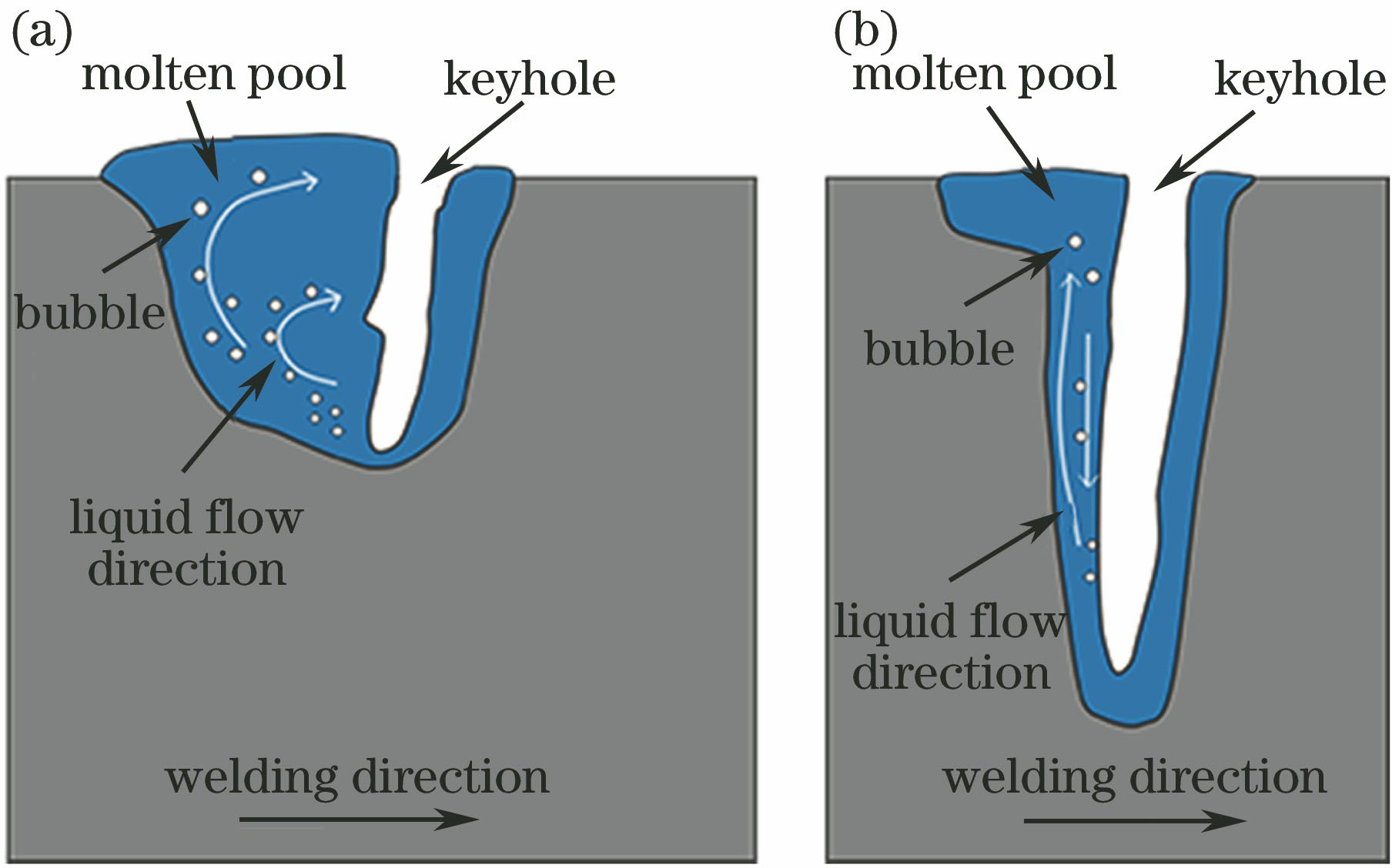
图 11. 不同激光功率下的气孔分布。(a) 6 kW;(b) 8 kW
Fig. 11. Pore distributions under different laser powers. (a) 6 kW; (b) 8 kW
3.4.2 激光功率对气孔形成的影响
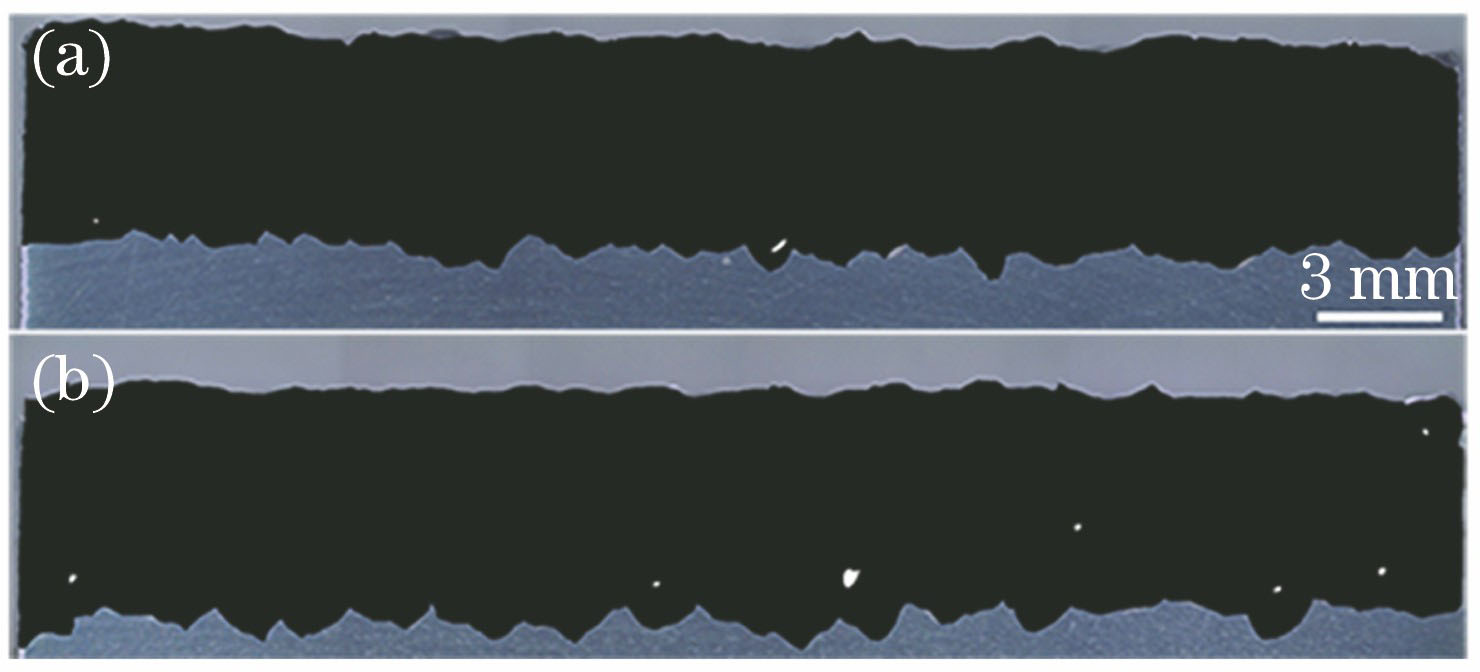
图 12. 不同焊速下的气孔分布。(a) 1.4 m·min-1;(b) 1.0 m·min-1
Fig. 12. Pore distributions under different welding speeds. (a) 1.4 m·min-1; (b) 1.0 m·min-1
3.4.3 焊接速度对气孔形成的影响
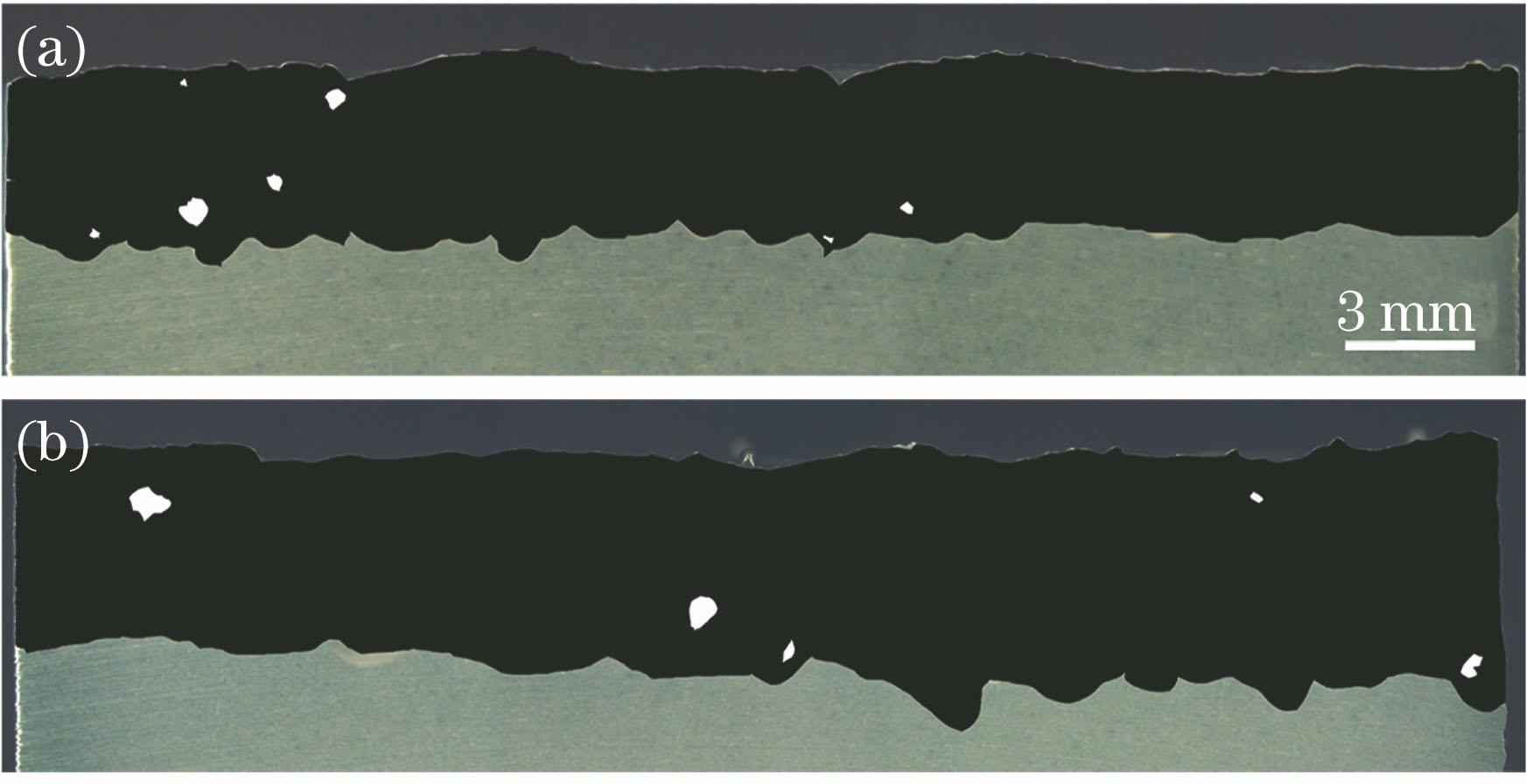
图 13. 不同压强下的焊缝表面成形及横截面形貌
Fig. 13. Weld surface formations and cross-sectional morphologies under different pressures
4 结论
激光功率、焊接速度、环境压力是影响铝合金激光深熔焊接的焊缝质量的重要因素,通过正交试验研究了一定参数范围内三个因素对焊缝熔深、深宽比、气孔率的影响程度与机制,得到如下结论。
1) 激光功率、焊接速度、环境压力均对焊缝成形具有一定影响,正交试验极差
2) 金属蒸气羽烟的光强和图像灰度值在一定程度上表征了其对激光的吸收能力,随着环境压力的降低,羽烟的光强、图像面积及灰度均减小,表明羽烟强度减小。当环境压力由常压降至20 kPa时,平均灰度仅为常压下的10%,面积像素比减小至1/4。
3) 环境压力对焊缝成形有较大影响,随着压强的降低,飞溅消失,焊缝表面更为均匀,焊缝熔深明显增大,焊缝的横截面形貌由常压下的倒三角形变为针形。当压强降至5 kPa时,熔深达到常压下的2倍。激光功率、焊接速度对焊缝熔深也有一定影响,但对焊缝深宽比及横截面形状的影响较小。
4) 环境压力对焊缝气孔有较大影响,随着压强的减小,焊缝近表面的气孔先消失,而后中、下部气孔减少。当环境压强降至5 kPa时,焊缝中的气孔几乎消失。激光功率、焊接速度对气孔也有一定的影响,但影响效果不如环境压力的明显。
[2] 许良红, 田志凌, 彭云, 等. 高强铝合金的激光焊接头组织及力学性能[J]. 中国激光, 2008, 35(3): 456-461.
[3] Iqbal S. Gualini M M S, Rehman A U. Dual beam method for laser welding of galvanized steel: Experimentation and prospects[J]. Optics & Laser Technology, 2010, 42(1): 93-98.
[5] 梅丽芳, 陈根余, 金湘中, 等. 车用铝合金光纤激光搭接焊的研究[J]. 中国激光, 2010, 37(8): 2091-2097.
[6] 王狮凌, 房丰洲. 大功率激光器及其发展[J]. 激光与光电子学进展, 2017, 54(9): 090005.
[7] Gapontsev V P, Fomin V, Ount A, et al. 100-kW ytterbium fiber laser[J]. Proceedings of SPIE, 1999, 3613: 49-54.
[8] 崔丽, 张彦超, 贺定勇, 等. 高功率光纤激光焊接的研究进展[J]. 激光技术, 2012, 36(2): 154-159.
[9] 黄坚, 李铸国, 唐新华. 中厚板的高功率激光焊接[J]. 航空制造技术, 2010( 2): 26- 29.
HuangJ, Li ZG, Tang XH. High-power laser welding of plate[J]. Aeronautical Manufacturing Technology, 2010( 2): 26- 29.
[10] 吴世凯, 肖荣诗, 陈铠. 大厚度不锈钢板的激光焊接[J]. 中国激光, 2009, 36(9): 2422-2425.
[11] 李小婷, 朱宝华. 铝合金激光焊接[J]. 电焊机, 2015, 45(2): 122-126.
Li X T, Zhu B H. Laser welding of aluminum alloy[J]. Electric Welding Machine, 2015, 45(2): 122-126.
[14] 王治宇. 激光—MIG电弧复合焊接基础研究及应用[D]. 武汉: 华中科技大学, 2006.
Wang ZY. Fundamental research on laser-MIG hybrid welding and its application[D]. Wuhan: Huazhong University of Science and Technology, 2006.
[18] 罗燕, 唐新华, 芦凤桂, 等. 局部负压激光焊缝成形特点及其影响因素[J]. 中国激光, 2014, 41(6): 0603008.
[20] 罗燕. 负压激光焊接过程蒸气羽烟及熔池行为研究[D]. 上海: 上海交通大学, 2015.
LuoY. Research on plasma plume and molten pool behavior in fiber laser welding under subatmospheric pressure[D]. Shanghai: Shanghai Jiao Tong University, 2015.
[21] 王军. 铝合金光纤激光及其复合焊接的等离子体行为与工艺研究[D]. 武汉: 华中科技大学, 2012.
WangJ. Study on the technology and plasma behaviour during the fiber laser and laser hybrid welding of aluminum alloy[D]. Wuhan: Huazhong University of Science and Technolog, 2012.
[22] 邱文聪, 杨立军, 刘桐, 等. 激光深熔焊等离子体波动特征光电信号分析[J]. 中国激光, 2018, 45(4): 0402001.
Article Outline
王天鸽, 唐新华, 韩潇潇, 芦凤桂, 崔海超. 5083铝合金真空激光焊缝成形的影响因素[J]. 中国激光, 2018, 45(11): 1102001. Wang Tiange, Tang Xinhua, Han Xiaoxiao, Lu Fenggui, Cui Haichao. Factors Influencing Weld Formation for Laser Welding of 5083 Aluminum Alloy in Vacuum[J]. Chinese Journal of Lasers, 2018, 45(11): 1102001.