基于自动阈值的窄间隙端接焊缝识别技术
下载: 999次
1 引言
激光焊接广泛应用于航空航天制造、汽车制造、民用等多个领域[1-2]。结合机器人的自动化激光焊接已经成为焊接自动化的研究热点。与传统的焊接方法相比,激光焊接的高能量密度需要更严格的装配质量[3]。就激光焊接本身特性而言,激光聚焦光斑直径大约为0.3 mm。为了避免焊缝中心线产生不对称的热源,激光聚焦中心与焊缝中心之间的偏移量应小于0.1 mm,否则容易导致焊接质量下降,甚至失败。在工业生产制造过程中,端接接头多用于2 mm厚的高强合金箱体密封件的连接,其连接间隙往往小于0.5 mm。因此,激光焊接端接接头对焊缝位置和焊缝宽度的提取精度提出了更高要求。
焊接自动化过程中的视觉传感可以分为主动传感和被动传感[4]。Xu等[5]采用被动视觉传感器,利用弧光或辅助光源捕捉图像,通过改进的边缘检测算法,获得0.3 mm以内的焊缝位置精度。Chen等[6]提出了一个视觉传感器系统,该系统由CCD摄像机和一个白色LED光源组成,主要用于检测宽度小于0.2 mm的窄缝。但是,焊接过程中焊接飞溅、等离子体等带来的噪声对被动视觉传感的影响很大,往往不易得到高质量的图像[7]。
另外,高向东等[8]设计了一种利用磁光传感器检测出对接焊缝的方法,精度能达到0.1 mm以下,但这种方法仅适用于磁性材料。Shao等[9]设计了一种新型的视觉传感器,实现了0.1 mm以下窄间隙焊缝的识别,这种新的视觉传感器目前还停留在实验室阶段,尚未在工业领域大量应用。最近,Wang等[10]开发了一套采用多个光学放大器探测窄间隙焊缝的焊缝测量系统,其焊缝宽度和焊缝位置的测量精度分别为6 mm和8 mm,但是镜头的视野范围仅有1.3 mm2,使其应用范围受限。以上所介绍的视觉传感方法虽然能精确地识别焊缝间隙,但是由于其设备的复杂性或较差的实时性难以满足自动化焊接过程的工业化需求。
要实现自动化焊接生产,不仅需要系统能精确地识别焊缝间隙,而且还应能实时根据扫描结果做出相应调整,因此对图像采集、处理和特征提取的速度要求较高。Qu等[11]采用基于symlet小波函数的小波分析算法提取焊后表面窄间隙缺陷,对于0.2 mm左右的间隙识别误差较小。Chen等[6]采用了轮廓提取、霍夫变换和最小二乘拟合等一系列算法,提取焊缝位置。上述图像处理算法比较复杂,且在实际应用时缺乏足够的稳定性,难以稳定快速地应用于常用的工业图像处理软件中。通过分析扫描式视觉传感器采集图像的识别难点,本文从图像滤波和特征点提取算法入手,在传统方法的基础上引入阈值,突出焊缝窄间隙处的图像特征,并结合相邻多次扫描对识别结果进行时域分析,从理论上减小焊缝窄间隙特征的提取误差。
2 实验设计
2.1 扫描式激光视觉传感器
现阶段工业上广泛应用于焊接自动化的主动式视觉传感器主要有两大类:结构光式和扫描式。结构光式传感器由于成像特征较好,被广泛应用于焊缝跟踪领域[12]。相关研究表明,结构光往往无法准确识别较窄的焊缝间隙,尤其是那些小于0.1 mm的缝隙,特别容易忽略[6,8],其原因在于结构光式视觉传感器测量的视场深度较浅,造成表面与底部光强不一致,从而很容易导致小缝隙的漏检。此外,结构光对于高反射性材料容易发生二次反射,增大后续图像处理的难度。扫描式视觉传感器的水平方向分辨率独立于垂直方向的分辨率,视场宽度大,且点扫描激光功率高,可获得良好的图像质量。由于点光源比线光源更容易达到较高的亮度,因此,扫描式激光传感器具有更高的信噪比和更强的抗弧光干扰能力[13]。
本文采用辅助光源为点状激光的激光扫描视觉传感器。系统工作时,内部的点状激光横向扫描焊接接头,经线阵CCD转换得到一组512 pixel点阵列。计算机接收数据并实时显示焊缝截面轮廓,再经图像滤波处理和特征点位置提取后得到当前图像焊缝中心线,与原先焊缝中心线相比较得到的偏差量作为反馈输出信号,系统响应并实时调整焊枪姿态。实验所用接头试样为端接接头,系统扫描过程如
2.2 任务分析
传统的光学三角测量的焊缝测量原理如
然而,由
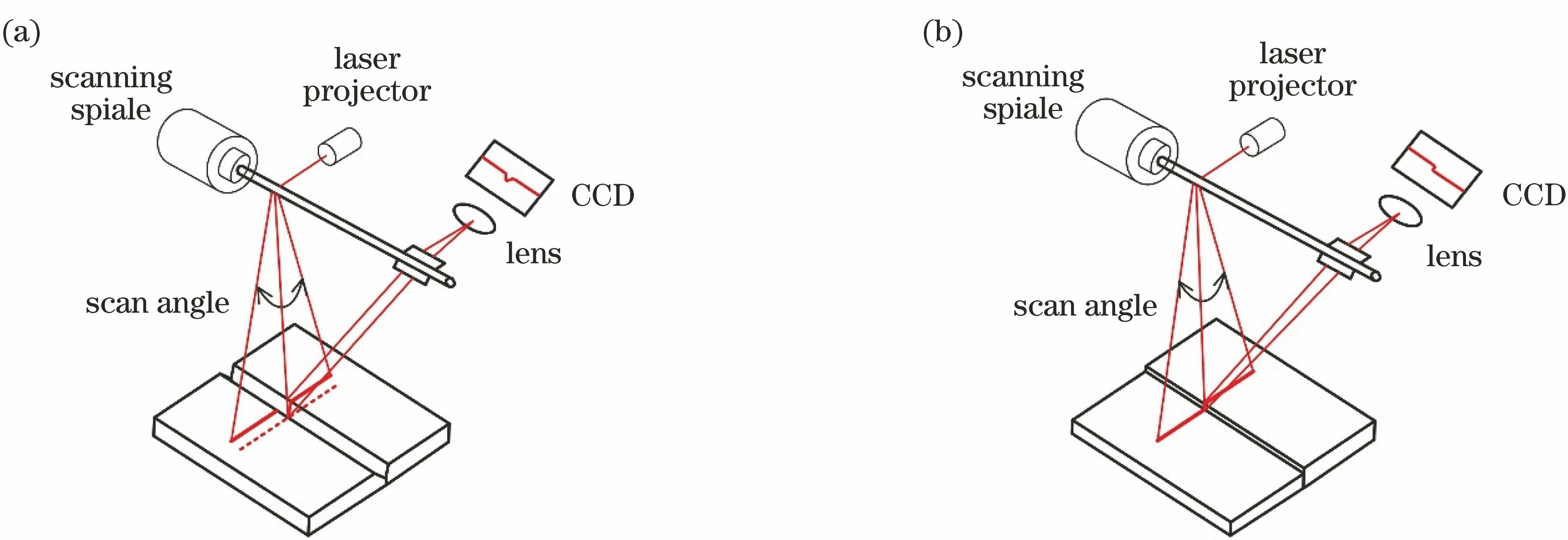
图 2. 扫描光的光学三角法测量焊缝。 (a) V型坡口角接接头;(b)含错边的对接接头
Fig. 2. Seam measurement by optical triangulation with scanning light. (a) V-shaped groove butt joint; (b) butt joint with misalignment
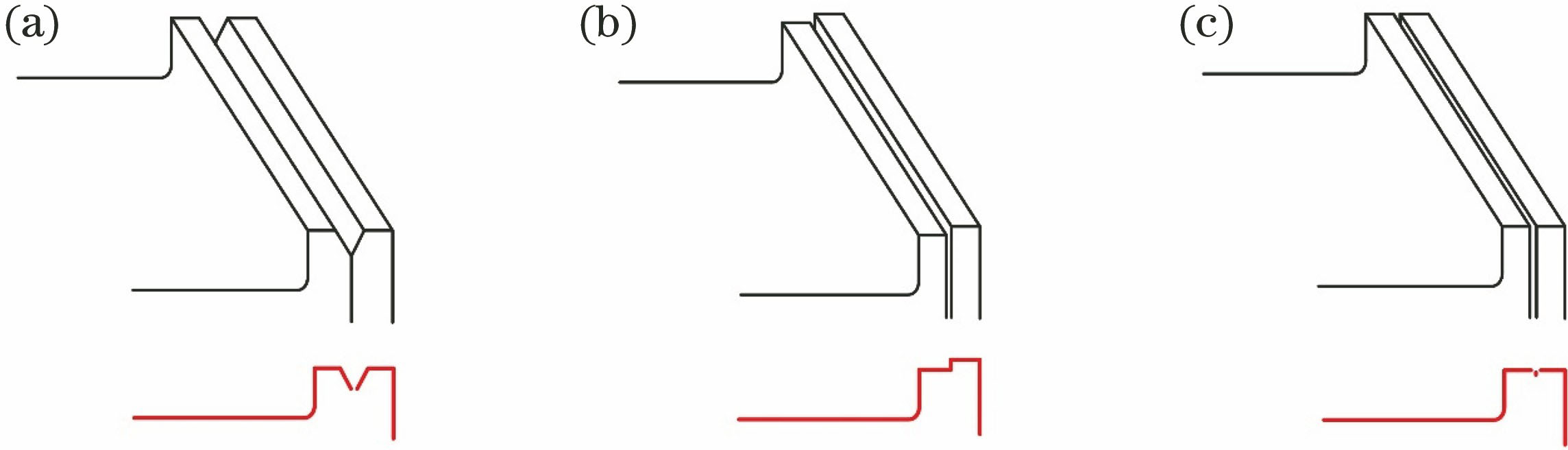
图 3. 不同焊缝下扫描光变形量的比较。(a) V型坡口;(b)含有错边;(c)缝隙宽度小于0.5 mm且没有错边偏差
Fig. 3. Comparison of deformation amount under different weld joints. (a) V-shaped groove; (b) with misalignment; (c) small gap less than 0.5 mm and without misalignment
端接接头是指两焊件重叠或两焊接表面之间夹角不大于30°构成的端部接头。在工业生产制造过程端接接头多用于2 mm厚的高强合金箱体密封件的连接,其连接间隙往往小于0.5 mm,其扫描图像与
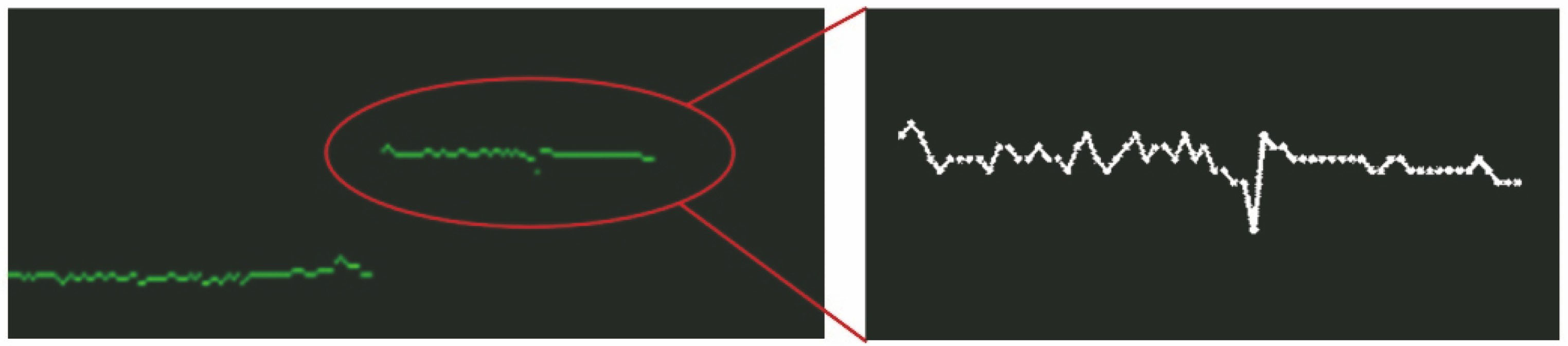
图 4. 原始焊缝扫描图像及局部放大图
Fig. 4. Original weld seam image captured by vision sensor and its local large map
3 图像处理
根据激光扫描得到的焊缝图像,准确识别焊缝宽度和焊缝位置是图像处理的目的。这主要包括图像滤波去噪处理和焊缝特征点提取。其中,图像滤波去噪处理是在尽可能保留图像细节的情况下对图像进行去除噪声和平滑处理,以减小焊接过程中飞溅、等离子体等带来的噪声干扰;在此基础上,利用相应的算法提取焊缝间隙两端特征点从而得到焊缝宽度和焊缝位置。
3.1 图像滤波去噪处理
传统的中值滤波法的整体滤波效果很好,数据波动范围较小,但是没有很好地保护图像细节,将某些重要的真实像素点也进行了中值替换,破坏了真实数据特征,增大了识别难度,尤其对窄间隙焊缝特征点的提取非常不利。
提出了一种基于自动阈值的自适应中值滤波法:通过设定阈值的方式,建立动态变化的图像细节保护区间,以有效减小真实像素点的丢失,保护条纹细节。合适的阈值能够准确区分真实像素和噪声[14],而标准差
一组测量数据的标准差定义为
式中
将平均值和标准差作为区分真实像素和噪声的阈值,正负信号的分离阈值分别为
式中
1) 选择合适的固定区间,包含2
2) 根据实际情况选择
3) 判断该点是否为噪声点。如果
4) 重复步骤3),直至
通过

图 5. 不同中值滤波法处理效果比较。(a)~(c)传统中值滤波法处理效果;(d)~(f)为改进中值滤波法处理效果
Fig. 5. Comparison of results using different median filterings. (a)-(c) Results of traditional median filtering; (d)-(f) results of improved median filtering
3.2 图像窄间隙特征点提取
3.2.1 斜率分析法
目前研究大多采用分析斜率的方法提取焊缝特征点。如
斜率分析法算法简单、计算量小,但在用于提取窄间隙特征点时由于间隙处往往特征点过于集中,计算所得截距变化较小,算法定位误差较大。
3.2.2 “细节放大”思想提取焊缝特征点
由于窄间隙处特征点过于集中,且特征不明显(
式中
式中
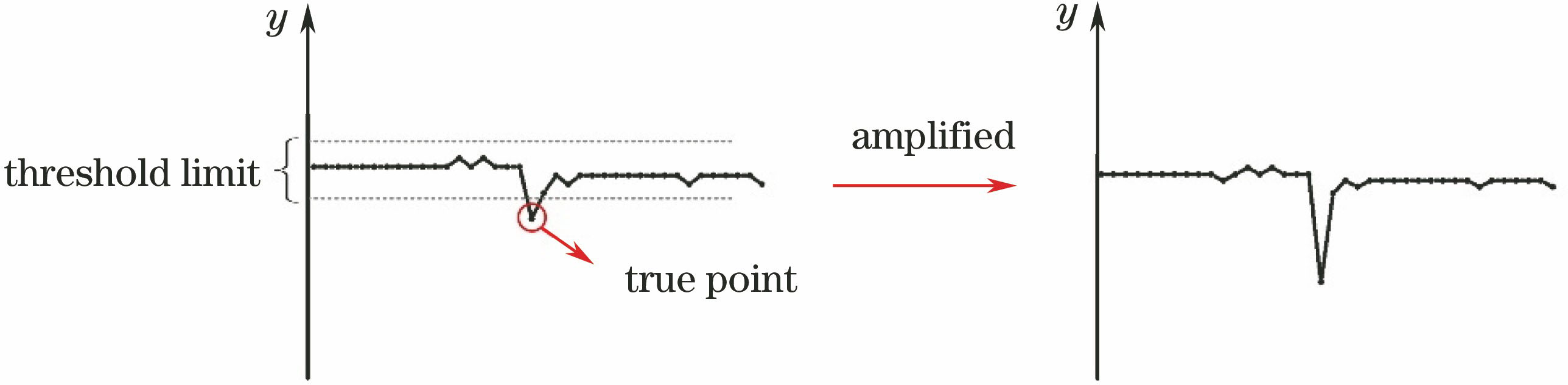
图 7. 基于阈值的“细节放大”方法原理图
Fig. 7. Principle diagram of magnifying details method based on threshold
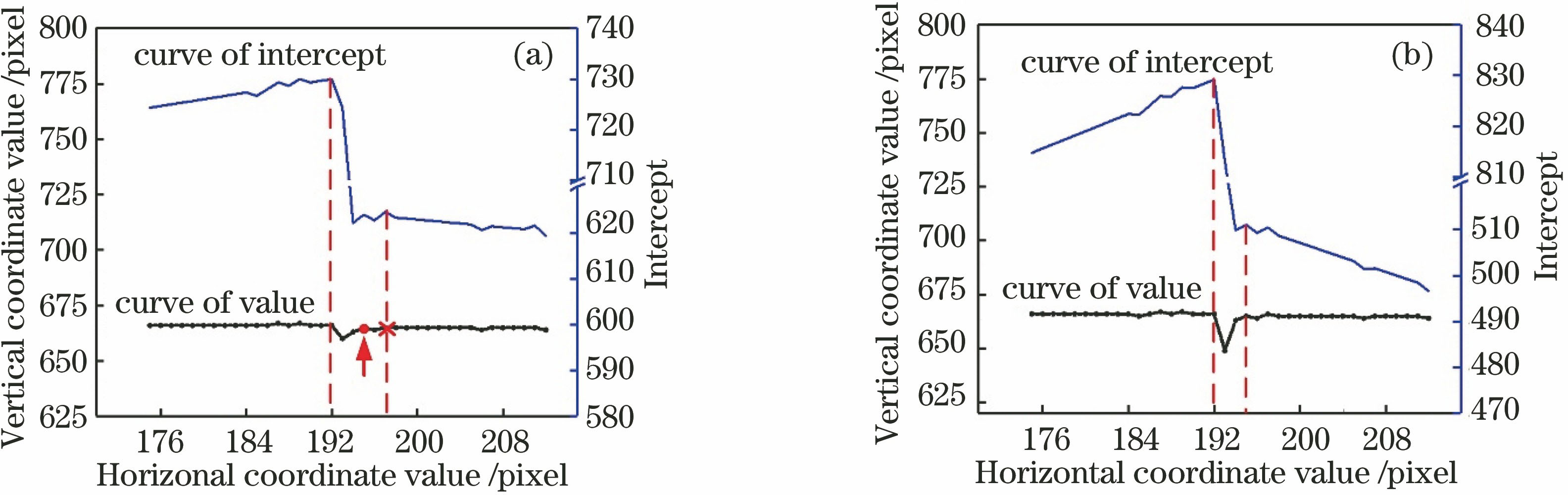
图 8. (a)未经过“细节放大”算法和(b)经过“细节放大”算法计算截距变化曲线
Fig. 8. Curves of intercept (a) without magnifying details and (b) with magnifying details
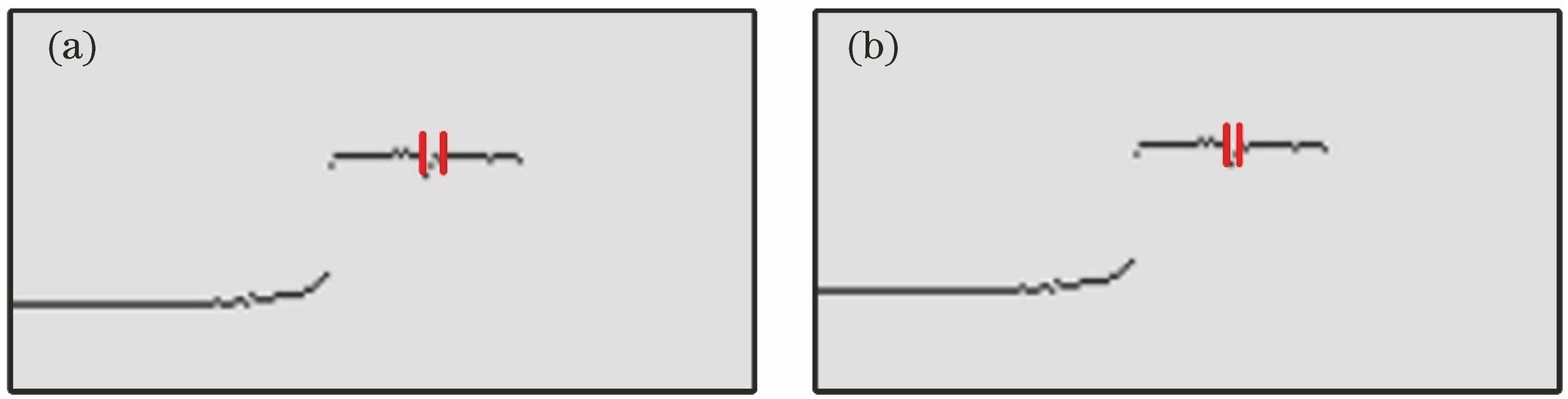
图 9. (a)未经过“细节放大”算法和(b)经过“细节放大”算法窄间隙特征点提取结果
Fig. 9. Extracted results of narrow-gap feature points (a) without magnifying details and (b) with magnifying details
3.2.3 特征点时域分析与误差抑制
为进一步抑制噪声、提高特征点精度,对短时间内多次扫描得到的特征点进行时域平均,即焊前在该点附近邻域内综合若干次扫描图像,对提取得到的多个焊缝特征点进行时域分析,经过数据平均得到该位置的精确定位,得
式中
4 实验
将扫描式视觉传感器安装在激光焊接的焊枪运动前方。
表 1. 焊接过程参数
Table 1. Configuration of weldment
|
为了验证算法精度及其抗干扰能力,进行了两组共8次实验,实验材料分别为一对2 mm厚和一对3 mm厚的钢板,每次实验结果为5次扫描的平均值。如
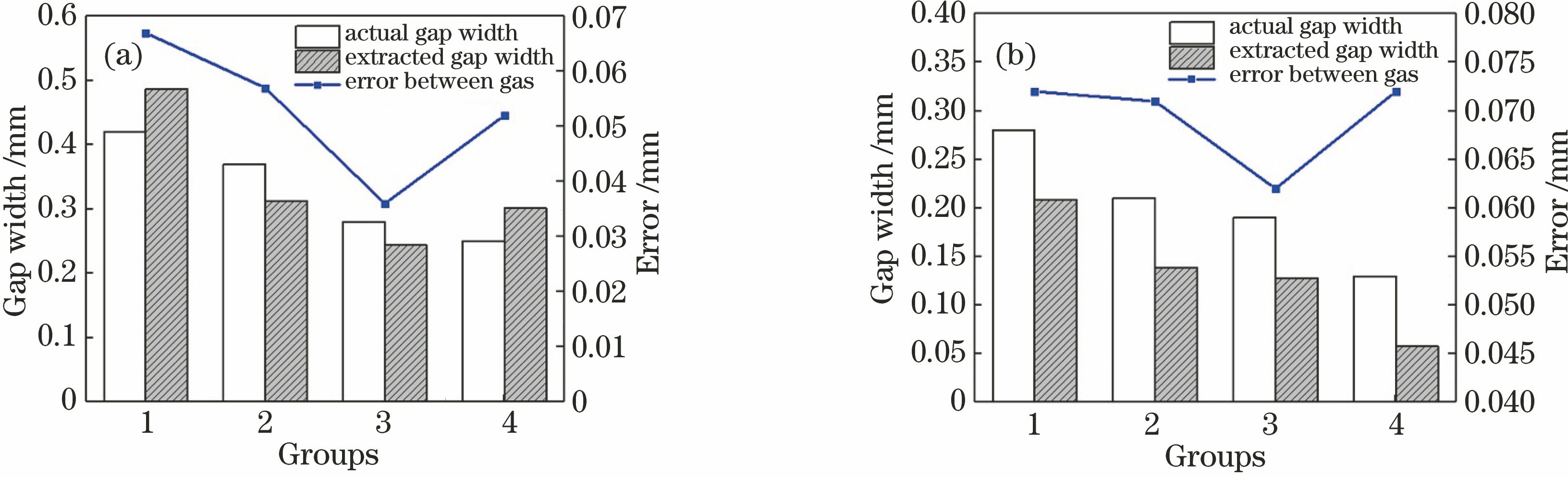
图 11. 不同板厚条件下的实验结果及误差曲线。 (a)板厚为2 mm;(b)板厚为3 mm
Fig. 11. Experimental results and error curves under different thickness conditions. (a) Thickness is 2 mm; (b) thickness is 3 mm
5 结果与讨论
本研究采用的扫描式传感器精度有限,限制了该算法测量精度的提高,在实际应用时提高传感器分辨率,采用此图像处理算法可以进一步减小视觉测量误差。
另外,利用本文方法进行自动化激光焊接跟踪实验,得到的焊缝微观形貌如
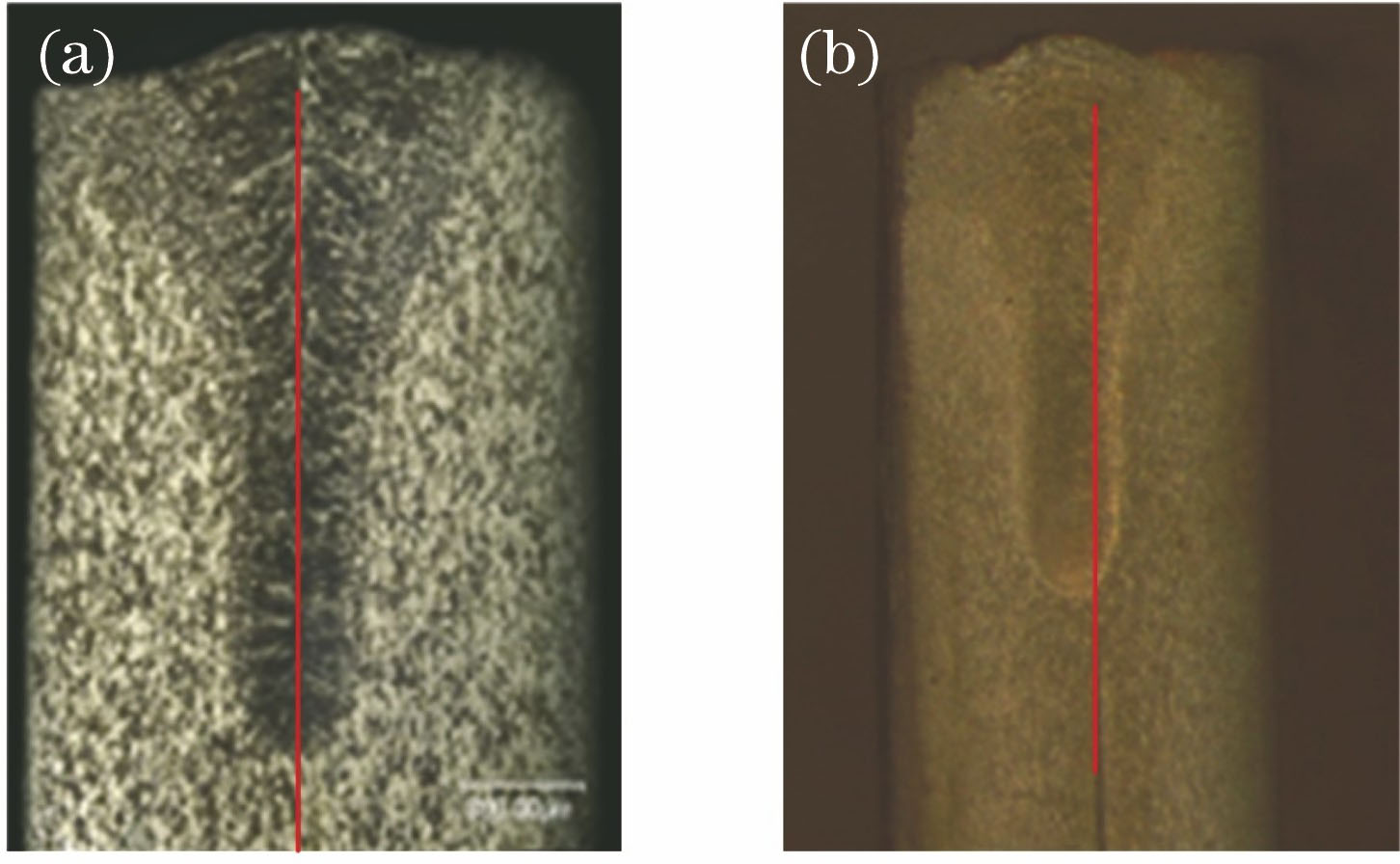
图 12. 端接焊缝微观形貌。(a)焊缝对称分布;(b)焊缝偏离中心
Fig. 12. Microtopography of weld seam. (a) Symmetric distribution; (b) off center
6 结论
基于传统的中值滤波法,提出了一种基于自动阈值的改进中值滤波法,只对那些超出设定阈值范围的像素点进行中值替换。通过与传统中值滤波法的滤波效果进行对比,发现该方法在一定程度上保护了那些真实像素点,焊缝窄间隙特征点得以保留,为准确提取特征点提供了必要条件。
通过分析现有的斜率分析法在提取窄间隙特征点过程中的不足,提出了一种“细节放大”的特征点提取方法,通过设定阈值将焊缝窄间隙特征点与周围点的差异放大,增大了截距曲线的变化幅度,减小了窄间隙特征点误判的可能性,大大降低了特征点提取的难度。然后利用时域分析,通过计算同一焊缝窄间隙位置相邻5次扫描所得特征点的平均值,进一步将误差减小到原来的1/
实验后将焊缝宽度的算法计算结果与实际测量结果进行比较,得到其最大偏差为0.072 mm,小于0.08 mm,满足激光焊接薄板的要求。焊缝窄间隙宽度在0.1~0.5 mm之间可以准确测量。由于焊缝中心位置取自焊缝宽度中心点,因此焊缝中心的定位精度与焊缝窄间隙宽度测量精度相同。
利用本方法进行了自动化激光焊接跟踪实验,结果表明,焊缝基本对称分布在板的两侧,强度高,满足自动化激光焊接的要求。
[1] 陈彦宾. 现代激光焊接技术[M]. 北京: 科学出版社, 2005: 1- 4.
陈彦宾. 现代激光焊接技术[M]. 北京: 科学出版社, 2005: 1- 4.
Chen YB. Modern laser welding technology[M]. Beijing: Science Press, 2005: 1- 4.
Chen YB. Modern laser welding technology[M]. Beijing: Science Press, 2005: 1- 4.
[2] 游德勇, 高向东. 激光焊接技术的研究现状与展望[J]. 焊接技术, 2008, 37(4): 5-9.
游德勇, 高向东. 激光焊接技术的研究现状与展望[J]. 焊接技术, 2008, 37(4): 5-9.
You D Y, Gao X D. Studies and prospect of laser welding technology[J]. Welding Technology, 2008, 37(4): 5-9.
[3] 许二娟, 高向东, 萧振林, 等. 激光焊接过程焊缝跟踪传感方法[J]. 电焊机, 2016, 46(1): 28-35.
许二娟, 高向东, 萧振林, 等. 激光焊接过程焊缝跟踪传感方法[J]. 电焊机, 2016, 46(1): 28-35.
Xu E J, Gao X D, Xiao Z L, et al. Sensing methods of seam tracking in laser welding process[J]. Electric Welding Machine, 2016, 46(1): 28-35.
[4] 齐秀滨. 激光焊接过程视觉传感技术的发展现状[J]. 焊接学报, 2008(29): 108-112.
齐秀滨. 激光焊接过程视觉传感技术的发展现状[J]. 焊接学报, 2008(29): 108-112.
Qi X B. State-of-arts of visual sensing technology to monitor laser welding process[J]. Transactions of the China Welding Instruction, 2008(29): 108-112, 118.
[7] 陈彦宾, 李俐群, 陈凤东, 等. 图像处理在自动焊接中的应用和展望[J]. 材料科学与工艺, 2003, 11(1): 106-112.
陈彦宾, 李俐群, 陈凤东, 等. 图像处理在自动焊接中的应用和展望[J]. 材料科学与工艺, 2003, 11(1): 106-112.
Chen Y B, Li L Q, Chen F D, et al. Application and prospect of image processing in welding[J]. Materials Science & Technology, 2003, 11(1): 106-112.
[11] Qu Z G. Chong A Y B, Chacon J L F, et al. Study on the laser-based weld surface flaw identification system employing wavelet analysis methodology[J]. Research in Nondestructive Evaluation, 2016, 27(3): 137-154.
Qu Z G. Chong A Y B, Chacon J L F, et al. Study on the laser-based weld surface flaw identification system employing wavelet analysis methodology[J]. Research in Nondestructive Evaluation, 2016, 27(3): 137-154.
[13] 赵菁, 林三宝. 用于焊接自动化过程的激光视觉传感器[J]. 电焊机, 2010, 40(11): 1-5.
赵菁, 林三宝. 用于焊接自动化过程的激光视觉传感器[J]. 电焊机, 2010, 40(11): 1-5.
Zhao J, Lin S B. Introduction to laser sensors for automated welding[J]. Electric Welding Machine, 2010, 40(11): 1-5.
[14] 王欢, 王修晖. 基于阈值判断的自适应中值滤波算法[J]. 中国计量学院学报, 2011, 22(4): 382-385.
王欢, 王修晖. 基于阈值判断的自适应中值滤波算法[J]. 中国计量学院学报, 2011, 22(4): 382-385.
Wang H, Wang X H. An improved adaptive median filter based on noises detection[J]. Journal of China University of Metrology, 2011, 22(4): 382-385.
[15] PapoulisA, Pillai SU. Probability,random variables, and stochastic processes[M]. 3 rd ed. New York: McGraw-Hill, Inc. , 1991.
PapoulisA, Pillai SU. Probability,random variables, and stochastic processes[M]. 3 rd ed. New York: McGraw-Hill, Inc. , 1991.
雷正龙, 沈健雄, 黎炳蔚, 周恒, 陈彦宾. 基于自动阈值的窄间隙端接焊缝识别技术[J]. 光学学报, 2018, 38(8): 0815011. Zhenglong Lei, Jianxiong Shen, Bingwei Li, Heng Zhou, Yanbing Chen. Recognition of Narrow-Gap Edge Welding Seam Based on Autonomous Threshold Value[J]. Acta Optica Sinica, 2018, 38(8): 0815011.