高铁静态限界测量的二维扫描传感器的设计和标定
下载: 834次
1 引言
铁路机车车辆静态限界是当机车车辆静止时,各部位距轨面的最高尺寸和距轨道线路中心线的垂直面最宽尺寸的轮廓。为保证车辆安全运行,需要对限界上的点的在轨道坐标系下的三维坐标进行精确测量。现有的机车车辆限界测量方法是根据国家GBT 16904标准,采用标准限界规配合人工手动的接触式测量方法[1-3],该方法手工测量,具有检测效率低,检测精度依赖于工人的测量熟练度等缺点。天津大学前期开发了机车限界非接触测量系统[4],该系统通过二维扫描传感器上下和横向运动来检测车辆的静态限界。其二维扫描方式是由伺服电机带动精密丝杠旋转实现的,该方法虽然结构简单,但具有体积大、检测时间长等缺点。基于以上的测量现状,本文设计并开发了一种全新的高铁静态限界测量的二维扫描传感器,该传感器基于回转射线簇原理[5],由高精密转台和相位式激光测距传感器组合而成,可对高铁车厢在列车前行方向进行二维形貌扫描。
2 系统的设计方案与测量原理
2.1 系统设计方案
本传感器应用于新型高铁静态限界测量系统中,测量系统的整体结构如
2.2 传感器的设计方案
二维扫描传感器的具体结构如
如
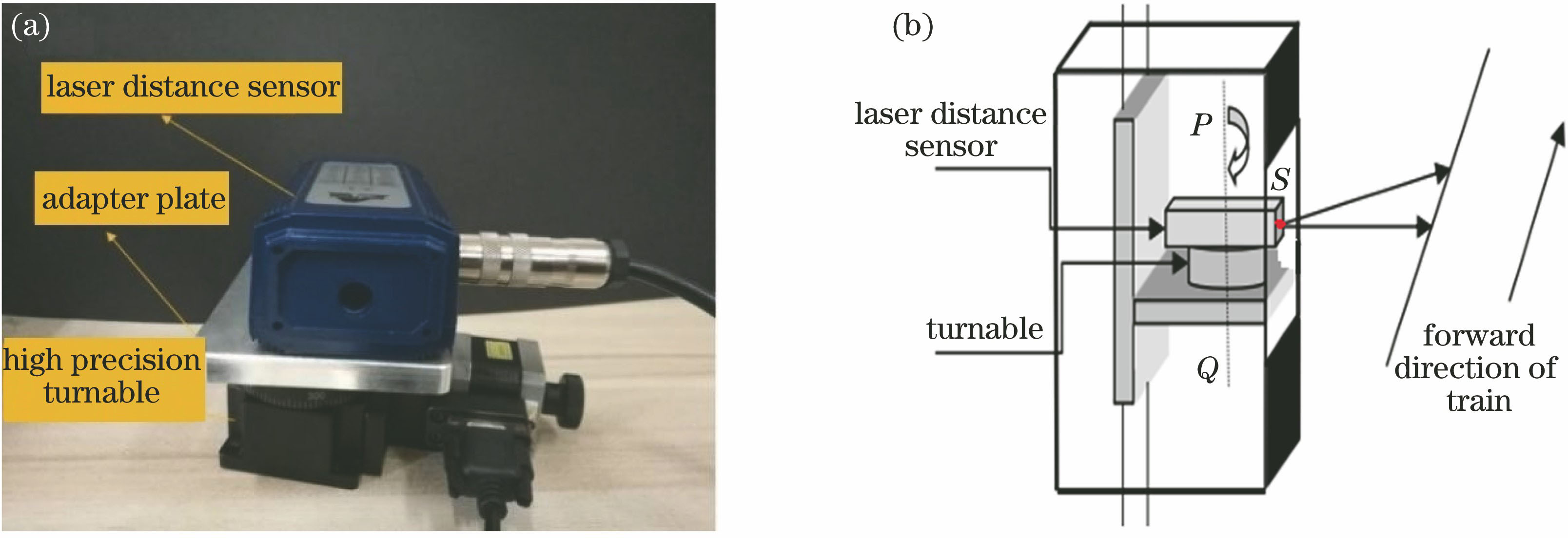
图 2. 传感器设计图。(a)传感器实物图;(b)扫描过程示意图
Fig. 2. Picture of sensor design.(a) Physical picture of sensor; (b) schematic of scanning process
2.3 传感器的测量原理
本传感器采用回转射线簇的测量原理[5],假定空间中存在一条测量射线,该射线具有给出由出射点到被测点之间距离的能力,该射线绕过出射点且在垂直于该射线的回转轴线上旋转[6-7],便可完成平面内被测点相对于旋转中心的极距信息的提取,即回转射线测量模型[8-9]。如
3 标定实验和精度验证实验
3.1 传感器标定过程
采用经过精细打磨的大理石平面对系统进行标定,系统标定示意图如
因此,只需要标定出旋转中心与射线出射点连线的长度d和激光射线与上述直线的夹角θ,即可通过传感器示数和转台旋转角度,由(1)式求解出被测点坐标。
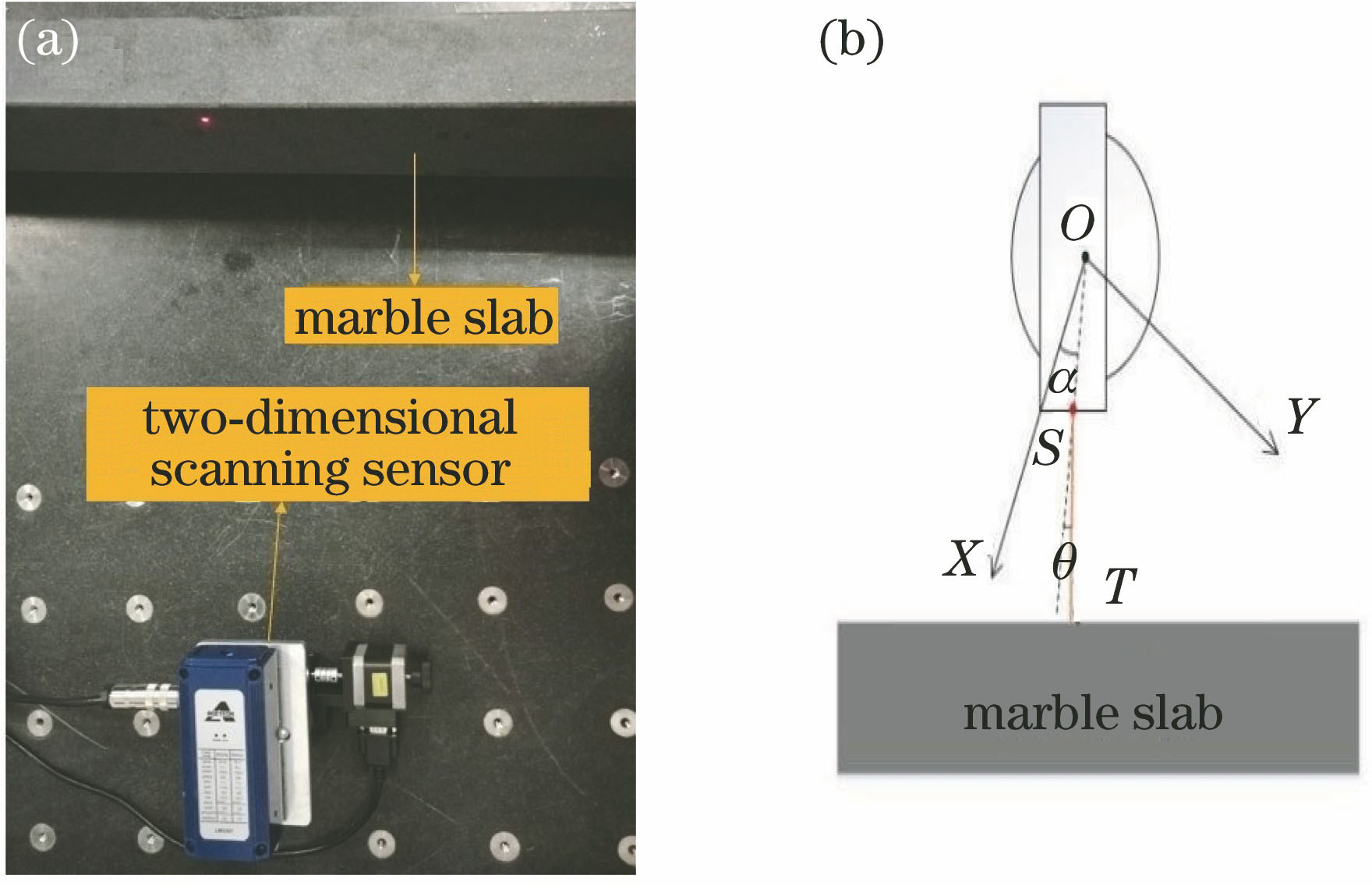
图 3. 系统标定实验图。(a)系统标定实验装置;(b)标定实验示意图
Fig. 3. Picture of system calibration experiment. (a) System calibration experimental device; (b) sketch map of calibration experiment
3.2 标定实验
标定过程如
首先将实验获得的每一组d和θ代入,写出每个点在转台坐标系下的二维坐标值,然后任取其中两点,以这两点的坐标值计算出直线方程,最后将其余各点代入直线,以满足直线方程。根据三角函数的转换特性,可写出一个非线性二次方程组,此方程组没有求根公式,因此求精确解十分困难,可采用迭代法解方程。采取Jacobi迭代法,只需要4个点即可求解出所需的d和θ,并进行多次迭代,理论上误差可达10-6。
标定方法解决了由于安装和机械加工造成的系统误差,但由于激光测距传感器具有随机误差,使得在传感器与被测物均固定的情况下重复测量所得到的数值有偏差。为减小这一误差,可在标定的过程中对同一个点测量50次,并采用五点三次平滑法对数据进行滤波,五点三次平滑法利用多项式最小二乘逼近来对采样点实行平滑滤波,算法简单,效果较好[11]。滤波后再取所有数据的平均值作为该次测量的测量值。滤波后的实验数据如
表 1. 滤波后标定实验的数据
Table 1. Data of calibration experiment after filtering
|
任意选取滤波后的四组数据,代入(1)式,可得到4个带有d、θ两个未知数的点坐标的表达式,即
由于被测物的直线度优于传感器的精度,可认为检测的是一条直线,因此将(X1,Y1),(X2,Y2)联立直线,表达式为
而(X3,Y3),(X4,Y4)应在联立的直线上,因此可以得到一个方程组,即
通过Jacobi迭代法进行多次迭代,可以将d和θ解出,在解算后,已知转台的旋转角度和激光测距传感器的读数,即可求得扫描点的二维坐标。
3.3 标定精度验证实验
根据标定过程对系统进行标定实验,得到激光测距传感器的激光出射点和转台的旋转中心连线长度d为97.136 mm,该直线与激光器出射激光的夹角θ为-0.03°,即激光测距传感器的安装与
表 2. 标定精度验证实验数据
Table 2. Data of calibration accuracy verification
|
经过计算,所有点到直线的距离均小于0.8 mm,可认为系统标定的精度高于0.8 mm。
3.4 测量系统的精度验证实验
在标定过后,对该二维扫描传感器进行精度验证。对设备精度的检验需要比设备精度更高一级的量具,量块也叫块规,由耐磨材料制造,横截面为矩形,并具有一对相互平行测量面的实物量具。两平行平面称为测量面,测量面很平,又很光洁(表面粗糙度Ra≤0.016 μm)[12],因此采用量块对二维扫描传感器进行实验。此外通过更换量块,还可以对不同形状的标准件进行形貌扫描。
实验操作过程如

图 4. 实验装置及测量数据。(a)精度验证实验装置;(b)量块点云图
Fig. 4. Experimental device and measurement data. (a) Device of accuracy verification experiment; (b) point cloud of gauge block
由于量块表面和大理石平面相对于测量系统精度较高,因此将平面上的点拟合成直线,然后计算直线间的间距,并与量块高度的差值进行比较,即可评价测量系统的精度。将量块在相同的扫描起点与终点重复扫描10次,任取其中一点,计算X与Y方向的标准差,可评价测量系统的重复性。选取旋转角度为1°时的数据来计算重复性。具体的实验数据如
表 3. 精度验证实验的数据
Table 3. Data of accuracy verification experiment
|
表 4. 重复性精度验证实验的数据
Table 4. Data of repeatability accuracy verification experiment
|
通过计算可以算出X方向的标准差为0.136 mm,Y方向的标准差为0.148 mm。两个方向的标准差均小于0.15 mm,可以认为系统的重复性良好。拟合直线间距与量块高度差的差的绝对值均在1 mm内,虽然拟合直线时会去除部分极值点,结合测量标准差分析,可认为检测精度在1 mm以内。
4 结论
针对原有的接触式、非接触式测量高铁车厢静态限界的方法所具有的问题,基于回转射线簇原理设计了应用于静态限界测量的新型二维扫描传感器。对该传感器进行了标定和精度验证。实验证明,该传感器精度优于1 mm,且重复性良好、扫描速度快,很好地满足了高铁车厢静态限界的测量需求,即将替换原有的在中铁检验认证中心有限公司机车车辆检验站的二维扫描传感器并投入使用。
[1] 铁道部标准计量研究所. 标准规矩铁路机车车辆检查第2部分: 限界规: GB/T16904.2-2006[S]. 北京: 中国标准出版社, 2007.
Standard metrology institute of ministry of railways. Checking of rolling stock clearance for standard gauge railways Part 2: clearance treadle: GB/T 16904.2-2006[S]. Beijing: China Standard Press, 2007.
[2] 韩梅, 韩伯领, 李红艳, 等. 铁路超限货物限界距离计算方法[J]. 中国铁道科学, 2011, 32(1): 122-126.
Han M, Han B L, Li H Y, et al. Calculation method of the distance between railway out-of-gauge goods and structure gauge[J]. China Railway Science, 2011, 32(1): 122-126.
[3] 郭寅, 刘常杰, 刘刚, 等. 机车车辆静态限界非接触式自动测量系统[J]. 中国铁道科学, 2013, 34(1): 134-138.
Guo Y, Liu C J, Liu G, et al. Non-contact automatic measurement system for the static clearance of rolling stock[J]. China Railway Science, 2013, 34(1): 134-138.
[4] 吴斌, 庄洵, 刘常杰, 等. 铁路机车车辆静态限界测量系统校准方法研究[J]. 传感技术学报, 2013, 26(1): 58-62.
Wu B, Zhuang X, Liu C J, et al. Research on calibration method of static railway vehicle clearance gauge[J]. Journal of Transduction Technology, 2013, 26(1): 58-62.
[5] 吴振刚, 曾周末, 李兴强, 等. 非接触回转射线二面角在机测量方法[J]. 中国激光, 2016, 43(5): 0508001.
[6] 刘新波, 王仲, 林立, 等. 基于单激光束旋转的深孔直线度测量方法[J]. 激光与光电子学进展, 2017, 54(3): 031203.
[7] 刘新波, 王仲, 罗庆跃, 等. 基于单激光束旋转的圆孔直径在机测量方法[J]. 激光与光电子学进展, 2016, 53(4): 041204.
[8] 刘新波, 王仲, 苏野, 等. 基于逼近式定心法测量机床回转轴对导轨的平行度[J]. 中国激光, 2012, 39(11): 1108015.
[9] 王仲, 苏野, 刘新波, 等. 回转激光位移传感器逼近式孔心定位方法[J]. 中国激光, 2012, 39(6): 0608001.
[10] 王祎雯, 付鲁华, 赵炎, 等. 激光传感器光轴垂直度误差标定方法[J]. 中国激光, 2017, 44(4): 0410002.
[11] 武炜, 陈标, 吴剑锋, 等. 基于五点三次平滑算法的入库流量反推研究[J]. 水利水电技术, 2013, 44(12): 100-102.
Wu W, Chen B, Wu J F, et al. Study on reverse deduction of reservoir-inflow based on cubical smoothing algorithm with five-point approximation[J]. Water Resources and Hydropower Engineering, 2013, 44(12): 100-102.
[12] 徐及, 车轩, 原晓慧. 量块的起源及其测量技术的发展[J]. 品牌与标准化, 2010( 4): 63.
XuJ, CheX, Yuan XH. The origin of the gauge block and the development of its measurement technology[J]. Enterprise Standardization, 2010( 4): 63.
Article Outline
卢钢, 刘常杰, 石春珉, 贾鑫林. 高铁静态限界测量的二维扫描传感器的设计和标定[J]. 激光与光电子学进展, 2020, 57(5): 051204. Gang Lu, Changjie Liu, Chunmin Shi, Xinlin Jia. Design and Calibration of Two-Dimensional Scanning Sensor for Static Clearance Measurement of High-Speed Train[J]. Laser & Optoelectronics Progress, 2020, 57(5): 051204.