激光熔覆304不锈钢稀释效应的数值模拟与实验
下载: 1166次
1 引言
增材制造技术是近几十年来快速发展起来的一种先进制造技术,其主要优势为快速和自由制造,可在零件表面快速形成一种金属复合涂层[1-2]。该技术为大型复杂金属构件的低成本快速制造提供了新的途径[3-4]。激光熔覆是增材制造的一种方式,根据送粉方式可分为预置送粉和同步送粉。预置送粉激光熔覆由于粉末对基体的热屏障作用,所以在较宽范围的工艺参数下都有较小的稀释率[5]。激光熔覆过程中的物理化学现象十分复杂,熔池中的温度分布很难通过实验的方法直接测出,利用有限元模型分析该过程是一种有效的研究方式[6]。目前有很多关于激光熔覆过程数值模拟的报道。Hao等[7]通过逆向建模方法构建了自适应熔覆层和移动热源模型,得到随工艺参数变化的熔覆层温度分布。郑丽娟等[8]对45钢表面激光多道熔覆过程进行了数值仿真,发现熔覆过程中基体上各点的温度虽然随时间有所变化,但是各点以固定的温度随着热源同步向前移动,形成准稳态温度场。宫新勇等[9]在ANSYS软件上求解了单层单道激光熔覆温度场,并根据其温度场特征分析了熔覆基板沿激光扫描方向上的翘曲变形问题。华亮等[10]对16MnR钢表面激光熔覆Ni-Cr-B-Si合金粉末过程进行了仿真分析,得到不同激光熔覆参数下的温度场及残余应力分布,据此确定了最优的激光熔覆工艺参数,并对其进行了验证。
激光熔覆技术可以提高材料的表面强度、硬度和耐磨性,该技术因涂层与基体结合强度高、工件变形小等优势而倍受关注[11-12]。激光熔覆过程中,为保证熔覆材料与基体实现良好的冶金结合,必须有一定量的基体熔化,熔化的基体将对熔覆层产生稀释,稀释率的大小直接影响熔覆层的性能。因此,有效控制稀释率是获得优良熔覆层的关键[13-14]。为了研究扫描速度对激光熔覆304不锈钢稀释效应的影响,本文通过ANSYS有限元分析软件对激光熔覆304不锈钢过程进行数值模拟,并进行了相同条件下的激光熔覆实验,分别对数值模拟和实验的结果进行了分析。
2 激光熔覆的数值模型和仿真
激光熔覆是一个十分复杂的材料快速熔化和快速凝固的变化过程。激光熔覆熔池的温度场反映了熔池冶金动力学特性,但是由于熔池的温度较高,温度梯度较大,无法对其直接测量,只能通过数值模拟得到其温度场。另外,通过数值模拟还可以优化工艺参数,与采用实验的方法相比,数值模拟可以节约实验成本,缩短研究周期。为了确定有限元模型,对激光熔覆过程做如下描述:如
2.1 假设
影响激光熔覆过程的因素有很多,目前尚缺少准确描述该过程实际情况的模型,为了方便计算并尽可能准确地表达该过程,对激光熔覆过程做如下假设:1) 温度场只受输入的热量和材料的热物理参数的影响,只考虑材料与空气的热对流和热辐射,忽略相变潜热等因素的影响; 2) 材料连续,且其热物理性能为各向同性;3) 忽略熔池的流动作用;4) 忽略由气化作用造成的材料损失;5) 工件的初始温度为20 ℃。
2.2 控制方程
激光熔覆过程中温度场对熔覆层材料的组织和宏观形貌以及稀释率有着重要的影响。激光作用于熔覆粉末表面时,粉末中的传热机制十分复杂,包括内部介质及颗粒本身的热传导、颗粒表面的辐射传热以及颗粒接触区域的对流传热,其中颗粒接触区域的对流传热非常微弱,可以忽略。因此,本模型中只考虑辐射传热和热传导。在移动热源的作用下,基体材料和熔覆材料的温度升高,材料的热物理参数都会随温度的变化而发生变化。可见,激光熔覆过程是一个典型的非线性瞬态传热过程,其控制方程为[15]
式中:
2.3 边界条件
根据热平衡方程的含义,激光熔覆过程中,材料应满足的热平衡为:材料自身所吸收的热量、辐射散失的热量和材料与外界对流的热量之和应等于材料从激光光束中吸收的热量,其表达式为[16]
式中:-
在输入边界条件时,假设如下:1) 周围的空气与基体之间的对流换热系数为25 W·m-2·℃-1;2) 周围环境的温度为20 ℃;3) 基体和熔覆粉末的初始温度分布均匀,为室温20 ℃;4) 激光束作用到熔覆粉末表面时,一部分光能被吸收,另一部分被反射,忽略熔覆粉末对激光的折射,综合考虑,将激光光能的吸收系数取为0.7。
2.4 热源模型
热源与能量分布有着直接的关系,且能量分布会直接影响温度场模拟的精度,因此,选择高能量密度的移动热源是实现激光熔覆的基本条件。在对激光熔覆数值模拟的研究中,提出了一系列热源计算模型[17]。最常用的热源模型包括:呈高斯函数分布的热源模型、半球状热源模型与椭球型热源模型等。在进行激光熔覆时,激光光束能量分布不均匀,呈正态分布,光束中心能量密度大,距离中心越远的位置能量密度越小,激光热源的热流密度可用高斯函数近似描述。因此,本文采用经典的热源模型——移动高斯热源,其热流密度为[18]
式中:
2.5 有限元模型
实验基体的尺寸为40 mm×20 mm×10 mm,304不锈钢熔覆层的尺寸为40 mm×20 mm×2 mm。通过ANSYS有限云分析软件模拟出激光熔覆过程中的温度场,采用ANSYS参数化设计语言(APDL)实现移动高斯热源的加载。为了尽可能提高计算精度和缩短计算时间,熔覆层采用较密的网格划分,划分成0.4 mm×0.4 mm×0.4 mm,基体材料选用较疏的网格划分,将距离熔覆层较远的基体划分成2 mm×2 mm×2 mm,热影响区(HAZ)采用自由网格划分。在熔覆层和远离熔覆层的基体区域选用SOLID70实体单元,热影响区选择SOLID90作为过渡单元。考虑到熔覆层的上表面既需要施加移动高斯热源载荷,又需要施加对流换热边界条件,所以在熔覆层的上表面创建表面效应单元,其单元类型为Surf152。将移动高斯热源载荷施加到表面效应单元上,将对流换热边界条件施加到实体表面单元上。
3 实验材料与方法
选用27SiMn钢作为基体材料,其尺寸为40 mm×20 mm×10 mm。熔覆材料选用粒度为100~300目的304不锈钢粉末(长沙天久金属材料有限公司),
对所得到的单道熔覆层材料进行线切割加工,得到垂直于激光扫描方向的横截面金相试样,并对所得到的金相试样进行镶嵌、打磨、抛光、腐蚀和干燥,之后,采用光学显微镜(MA200,尼康公司,日本)观察其横截面形貌,并测量横截面的尺寸;利用能谱分析测试仪(VEGAⅡAMU型,TESCAN公司,捷克)分析熔覆层的元素组成;使用显微硬度计(HMAS-D1000SZ,上海研润光机科技有限公司,上海)在熔覆层的横截面上进行打点测试。
4 结果和讨论
4.1 数值模拟和实验结果的稀释率分析
为了仿真预置送粉的激光熔覆过程,将移动高斯热源模型施加到熔覆粉末的上表面,有限元模型考虑了熔覆层和基体表面的热辐射以及各个表面与周围空气之间的对流换热。数值模拟的结果表明,移动熔池和熔池周围的温度分布达到了一个准稳态。熔池的轮廓为静态,且一直维持到激光扫描结束。
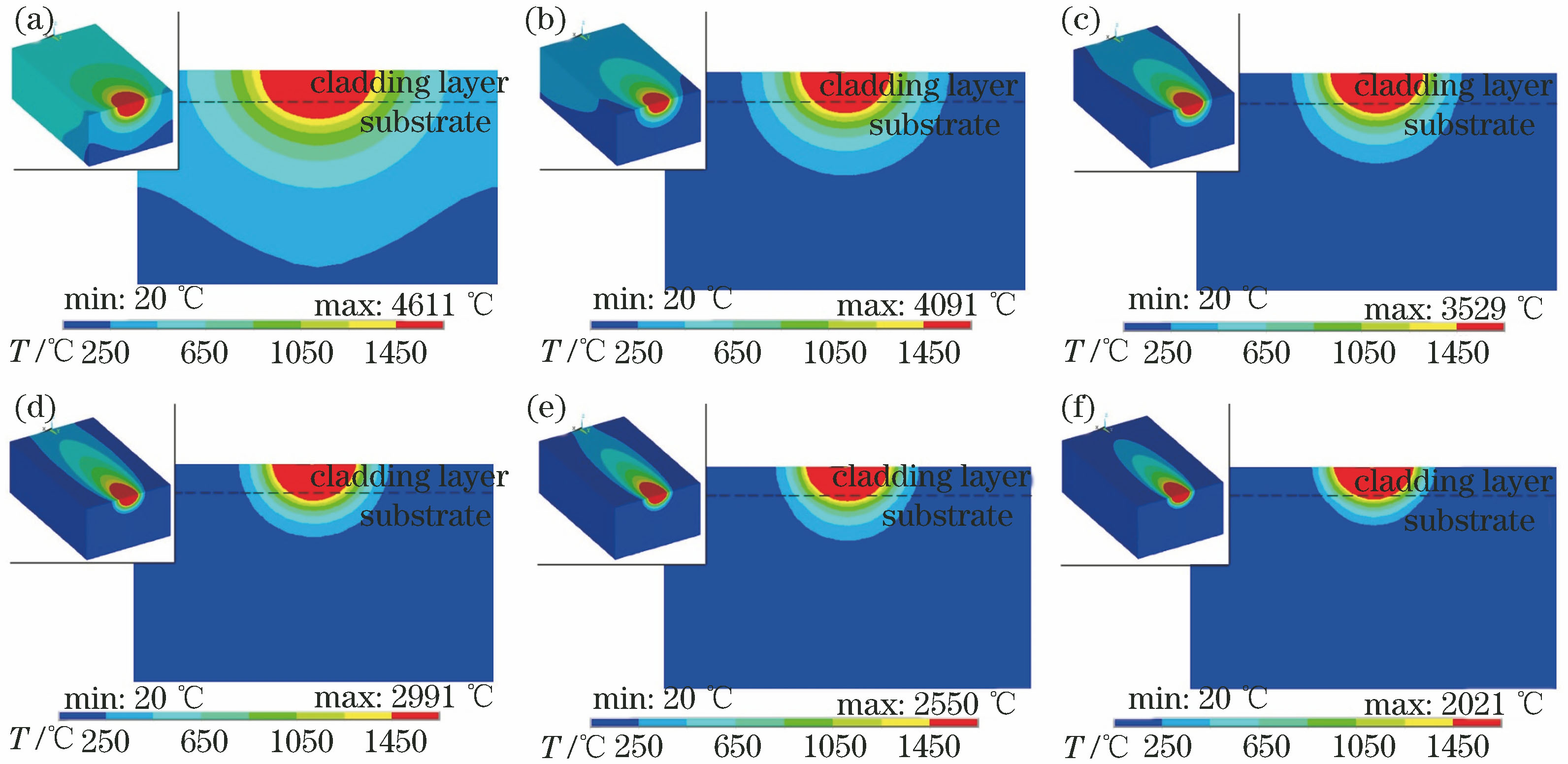
图 3. 不同扫描速度下单道熔覆层的温度场分布。(a) v=2 mm/s;(b) v=4 mm/s;(c) v=7 mm/s;(d) v=10 mm/s;(e) v=13 mm/s;(f) v=16 mm/s
Fig. 3. Temperature field distributions of single cladding layer under different scanning speeds. (a) v=2 mm/s; (b) v=4 mm/s; (c) v=7 mm/s; (d) v=10 mm/s; (e) v=13 mm/s; (f) v=16 mm/s
采用与数值模拟相同的激光束条件和工艺参数进行激光熔覆实验。
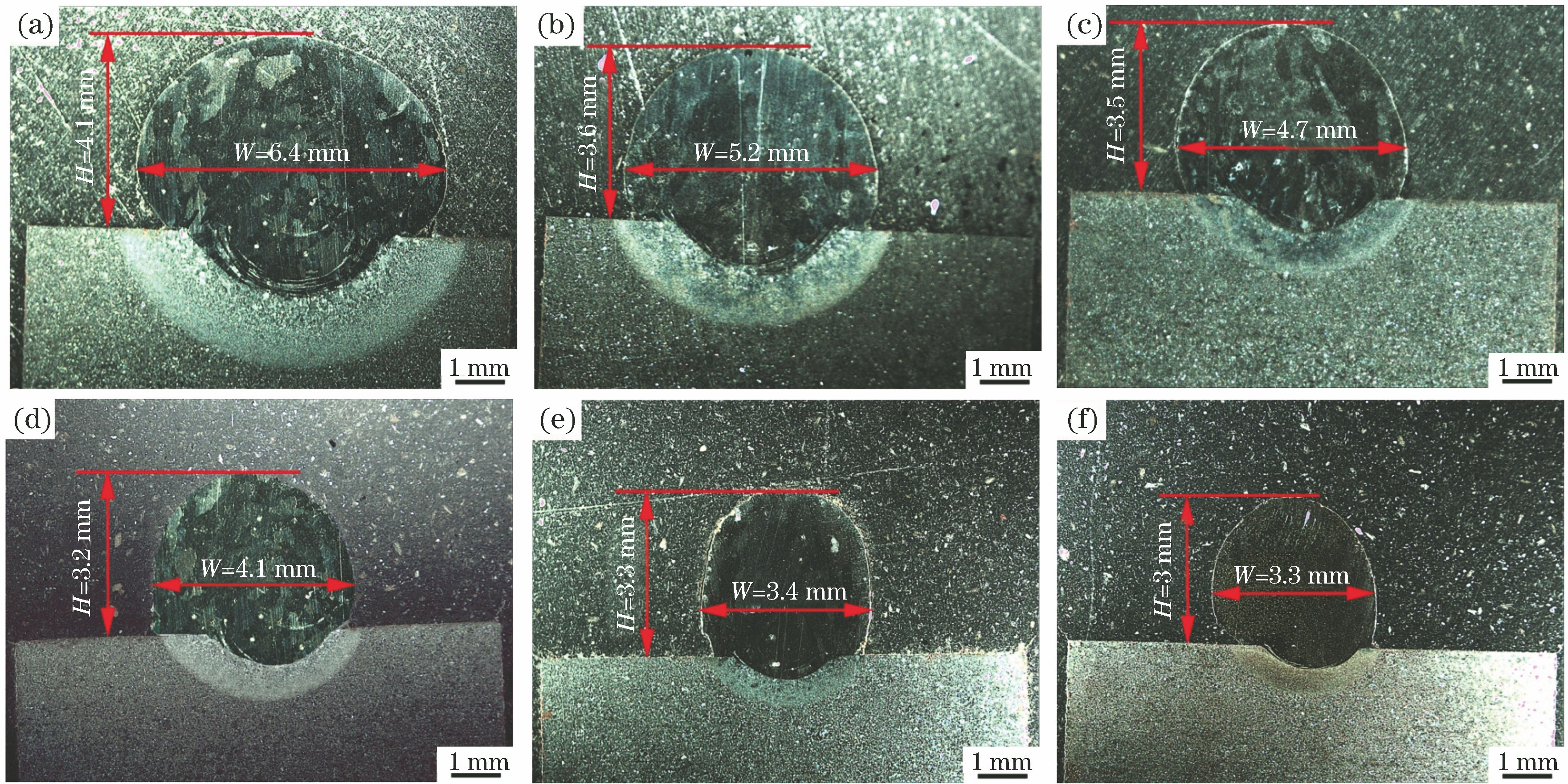
图 4. 不同扫描速度下单道304不锈钢熔覆层的横截面形貌图。(a) v=2 mm/s;(b) v=4 mm/s;(c) v=7 mm/s;(d) v=10 mm/s;(e) v=13 mm/s;(f) v=16 mm/s
Fig. 4. Cross sections of single 304 stainless steel cladding layer under different scanning speeds. (a) v=2 mm/s; (b) v=4 mm/s; (c) v=7 mm/s; (d) v=10 mm/s; (e) v=13 mm/s; (f) v=16 mm/s
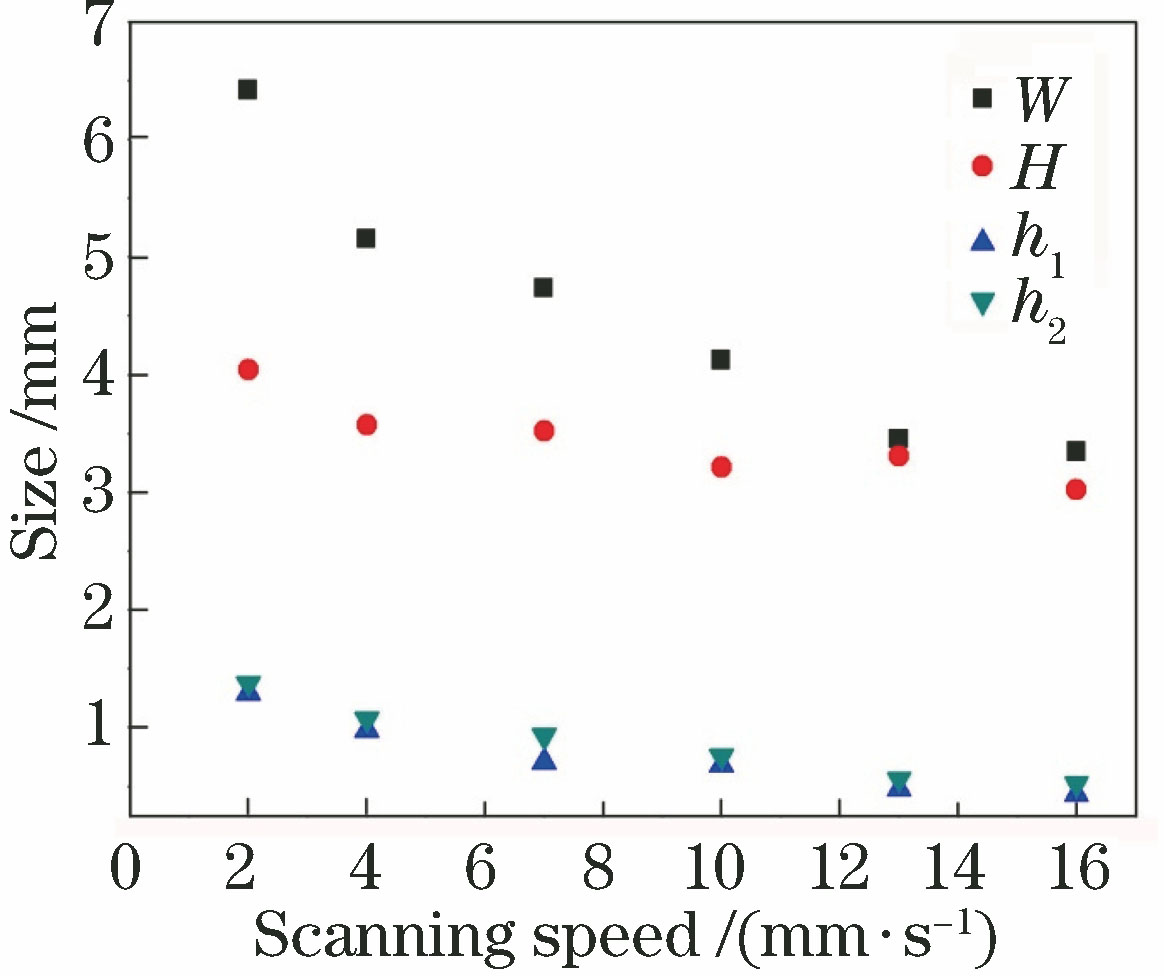
图 6. 单道304不锈钢熔覆层的横截面尺寸与扫描速度间的关系曲线
Fig. 6. Cross section sizes of single 304 stainless steel cladding layer under different scanning speeds
从
式中:
如
将
验得到的基本吻合,随着激光扫描速度的增大,均呈下降的趋势,其原因在于,不同的扫描速度意味着不同的能量输入,在给定的铺粉厚度、激光功率等工艺参数下,当扫描速度增大时,基体的熔化量减小,从而导致稀释率下降。
4.2 稀释效应对元素分布的影响
为了研究熔覆层中元素组成的稀释效应,对熔覆层中的不同区域进行了能谱分析。
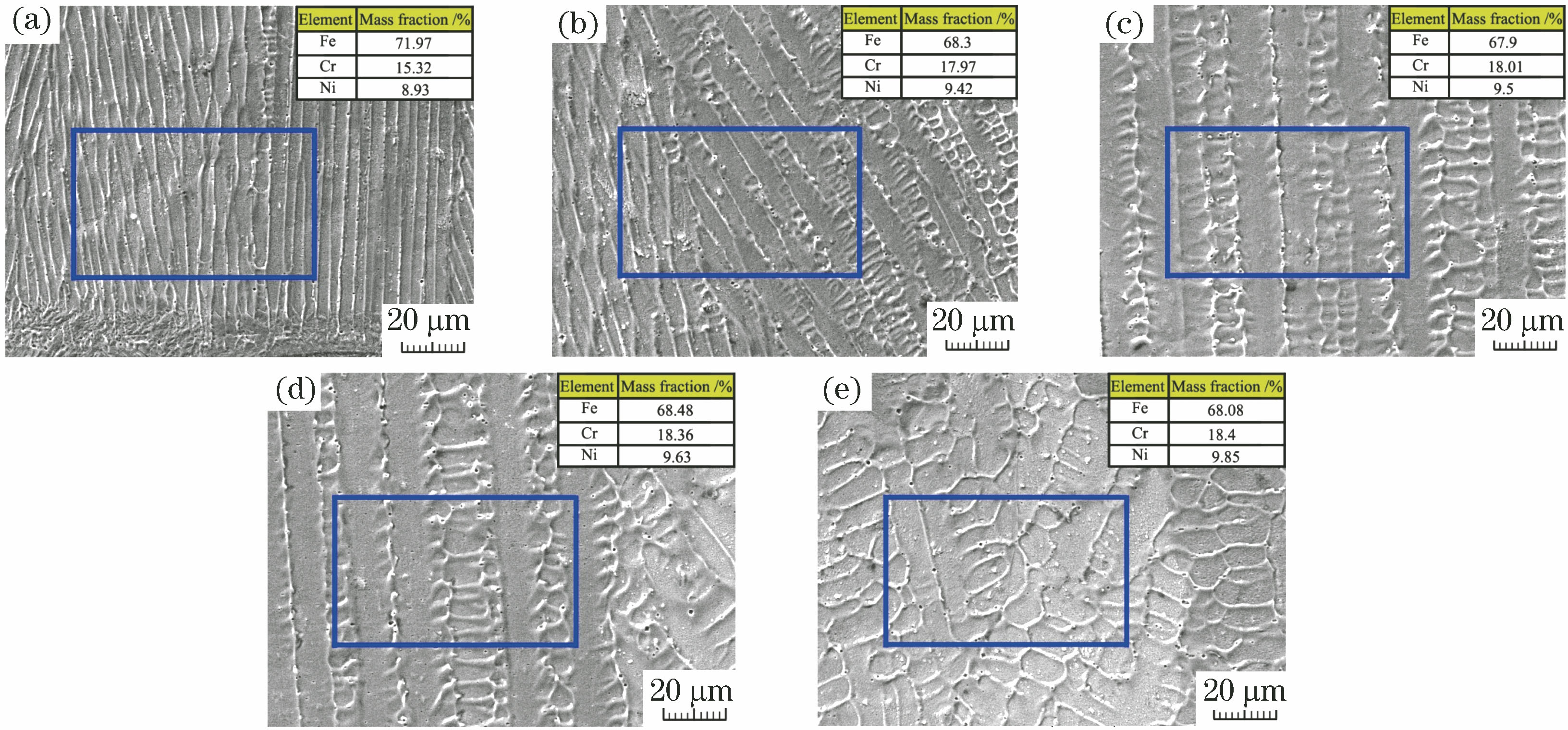
图 9. 扫描速度为10 mm/s时熔覆层的能谱分析结果。(a)采样区A;(b)采样区B;(c)采样区C;(d)采样区D;(e)采样区E
Fig. 9. Energy spectrum analysis for cladded sample prepared at scanning speed of 10 mm/s. (a) Sampling area A; (b) sampling area B; (c) sampling area C; (d) sampling area D; (e) sampling area E
实验所用304不锈钢熔覆粉末中的Fe/Cr的比值约为3.5,在此将该比值作为表征熔覆层中元素稀释效应的参考值。
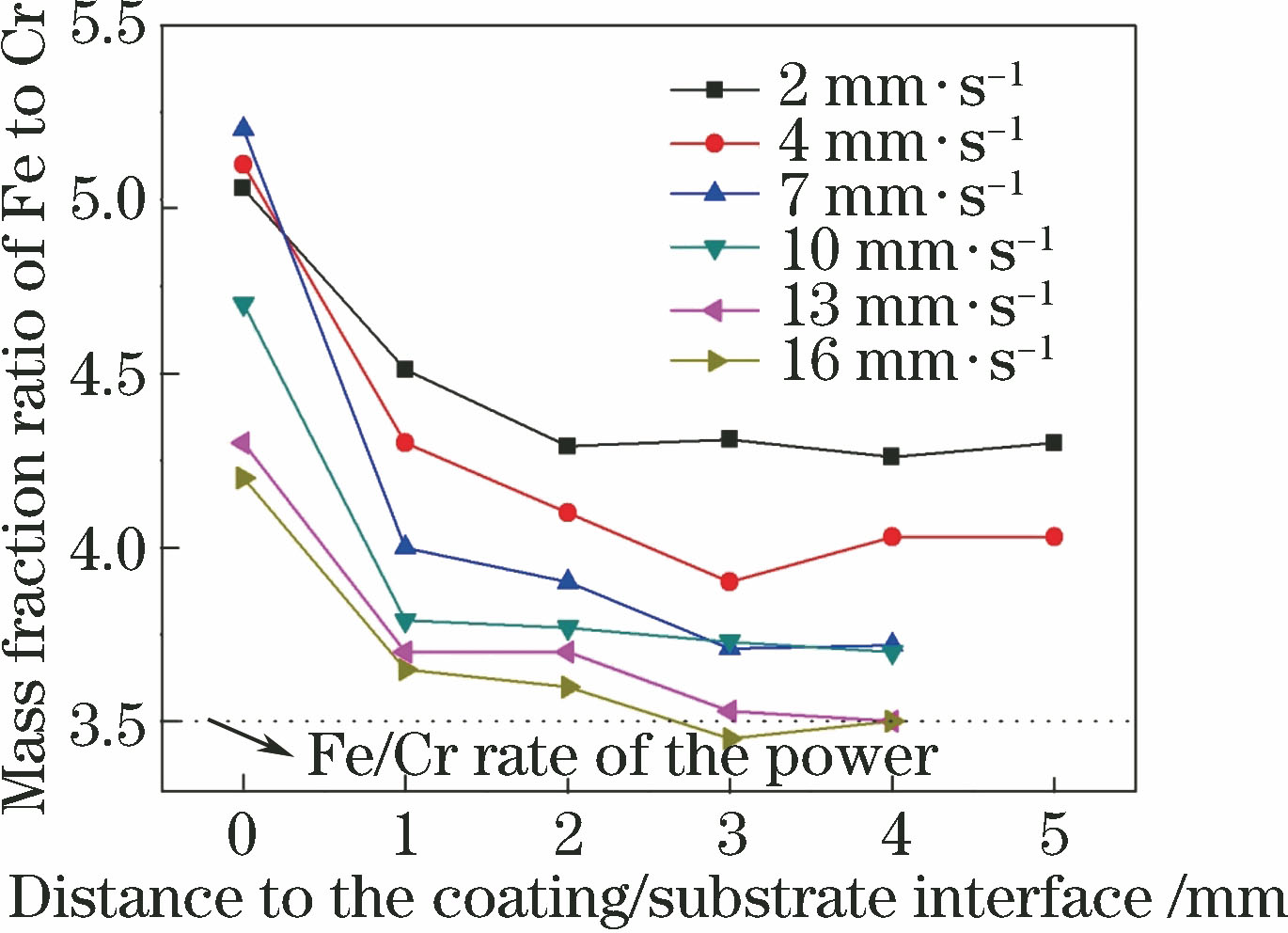
图 10. 熔覆层中不同采样区Fe与Cr的质量分数比值
Fig. 10. Mass fraction ratios of Fe to Cr at different sampling areas in cladding layers
4.3 显微硬度分布曲线
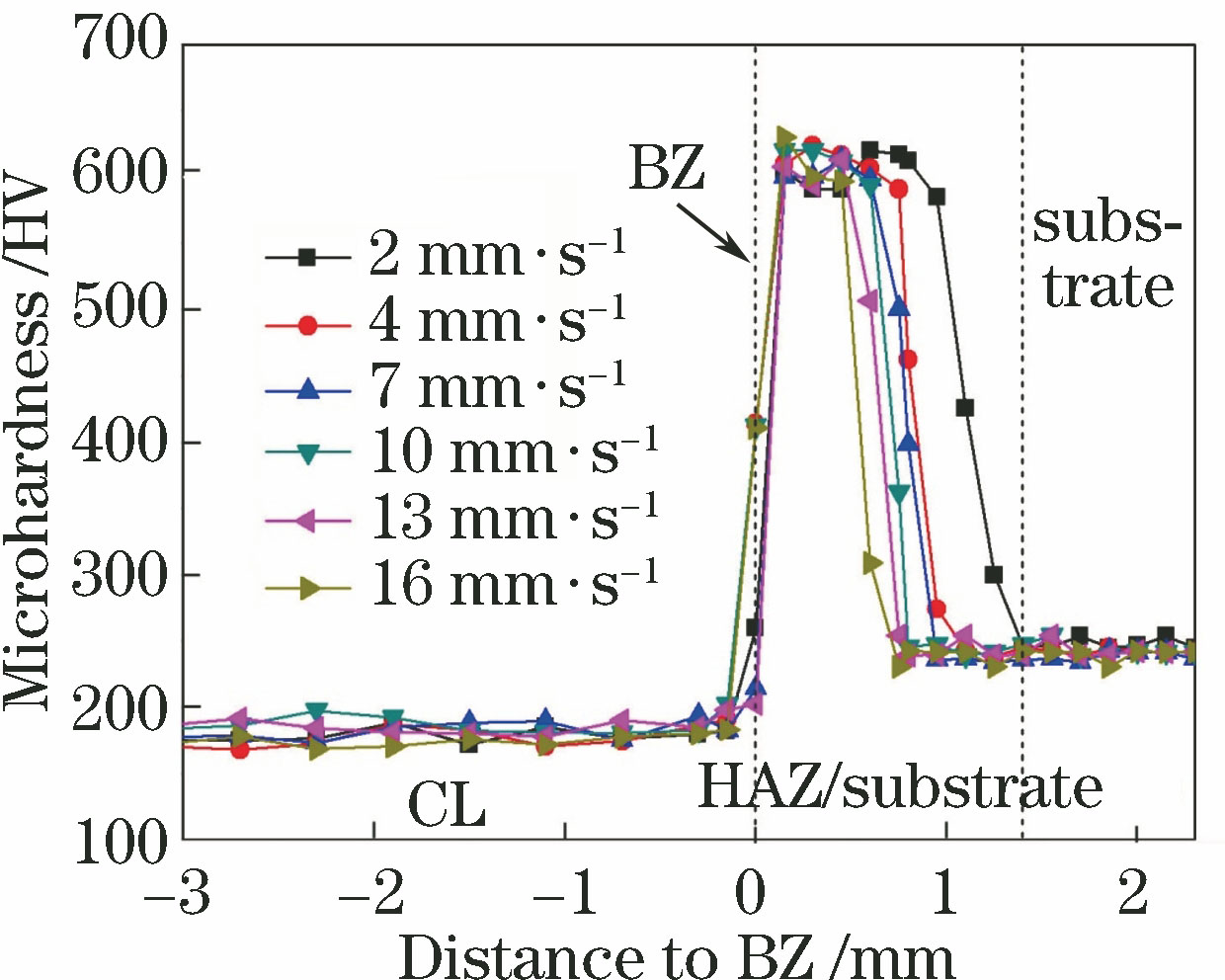
图 12. 不同扫描速度下熔覆层的显微硬度曲线
Fig. 12. Microhardness curves of cladding layers obtained under different scanning speeds
5 结论
利用ANSYS有限元分析软件对单道激光熔覆304不锈钢过程进行了数值模拟,并进行了相同条件下的激光熔覆实验,研究了扫描速度对激光熔覆过程中的稀释效应的影响。
数值模拟的结果表明,移动高斯热源所形成的温度场的表面形状呈彗星状,越靠近光斑中心的区域,温度梯度越大,且随着激光扫描速度的增大,基体的熔化量逐渐减小。实验结果表明,熔覆层的横截面呈椭圆状,且横截面的面积和热影响区的深度均随着扫描速度的增大逐渐减小。数值模拟和实验所得到的稀释率基本一致,均随着扫描速度的增大,呈现出逐渐减小的趋势。
对熔覆层的元素分析结果表明,熔覆层中靠近熔覆层/基体结合面的区域的Fe/Cr比值较高,在熔覆层中,随着到熔覆层/基体结合面距离的逐渐增大,Fe/Cr比值逐渐减小,然后趋于稳定。当扫描速度为2,4,7,10 mm/s时,整个熔覆层的元素组成均偏离了熔覆粉末;当扫描速度为13 mm/s和16 mm/s时,熔覆层中靠近熔覆层表面区域的元素组成与熔覆粉末基本一致。不同扫描速度下的熔覆层的显微硬度曲线均呈现出“低-高-低”的变化趋势,熔覆层的显微硬度最低,热影响区的最高,基体的显微硬度介于二者之间,且随着扫描速度的增大,“高”硬度区域的宽度逐渐减小,即热影响区的深度逐渐减小。
[1] 卢秉恒, 李涤尘. 3D打印)技术发展[J]. 机械制造与自动化, 2013, 42(4): 1-4.
Lu B H, Li D C. Development of the additive manufacturing (3D printing) technology[J]. Machine Building & Automation, 2013, 42(4): 1-4.
[2] 方琴琴, 傅戈雁, 王聪, 等. 带连接筋双层薄壁件激光直接成形工艺[J]. 中国激光, 2017, 44(2): 0202005.
[3] 何博文, 冉先喆, 田象军, 等. 激光增材制造TC11钛合金的耐蚀性研究[J]. 中国激光, 2016, 43(4): 0403004.
[4] 王志会, 王华明, 刘栋. 激光增材制造AF1410超高强度钢组织与力学性能研究[J]. 中国激光, 2016, 43(4): 0403001.
[6] 韩会, 祁文军, 党元晓, 等. 路径设置对304不锈钢激光熔覆温度场及应力应变场的影响[J]. 热加工工艺, 2017( 12): 148- 152.
HanH, Qi WJ, Dang YX, et al. Effect of path set on laser cladding temperature field and stress and strain field of 304 stainless steel[J]. Hot Working Technology, 2017( 12): 148- 152.
[8] 郑丽娟, 李燕, 何大川, 等. 激光多道熔覆温度场及熔覆层组织分析[J]. 红外与激光工程, 2013, 42(S1): 52-57.
[9] 宫新勇, 高士友, 咸士玉, 等. 基于温度特征的单道激光熔覆翘曲变形[J]. 激光与光电子学进展, 2017, 54(10): 101410.
[10] 华亮, 田威, 廖文和, 等. 激光熔覆热影响区及残余应力分布特性研究[J]. 激光与光电子学进展, 2014, 51(9): 091401.
[11] 周野飞, 高士友, 王京京. 激光熔覆高碳铁基合金组织性能研究[J]. 中国激光, 2013, 40(12): 1203001.
[12] 鲍雨梅, 高海明, 张冬明, 等. 基于温度场模拟的激光熔覆生物陶瓷涂层工艺参数选择[J]. 激光与光电子学进展, 2014, 51(11): 111601.
[17] 李豪, 王彦芳, 石志强, 等. 基于椭圆热源模型的激光熔覆温度场与流场数值模拟[J]. 应用激光, 2017, 37(2): 218-222.
Article Outline
郭卫, 李凯凯, 柴蓉霞, 张丽苹. 激光熔覆304不锈钢稀释效应的数值模拟与实验[J]. 激光与光电子学进展, 2019, 56(5): 051402. Wei Guo, Kaikai Li, Rongxia Chai, Liping Zhang. Numerical Simulation and Experiment of Dilution Effect in Laser Cladding 304 Stainless Steel[J]. Laser & Optoelectronics Progress, 2019, 56(5): 051402.