基于MATLAB与非球面轮廓仪的Q-Type非球面检测技术
下载: 1424次
1 引言
近年来,非球面光学元件在现代光学系统中得到了越来越广泛的应用,但传统幂级数非球面的数学表达方式存在着固有缺陷,对于一个确定形状的曲面,当利用10项以上多项式进行高精度拟合时,与之相关的Gram矩阵容易呈现病态,导致面形表征失败。为了解决这个问题, 2007年美国QED公司的Forbes [1]提出了一种新的非球面数学表征形式,即用一个非标准正交基底取代传统且过于简单的附加多项式,并称之为Q-type函数多项式[2]。其在光学设计过程中具有明显优势,如基底在定义域内正交,在曲面优化设计时各项系数之间互不影响,能够通过控制各项系数进而控制面形偏离量,设计与加工评价同时进行,以提高系统的设计效率等[3]。目前Q-type非球面的研究大多为光学系统设计,主要应用在全景光学系统[4]、内窥镜物镜光学系统[5]、照相机光学系统[6-7]等。
虽然Q-type非球面具有优良的光学性质,但是对于Q-type非球面加工过程中的检测问题,还没有一个简单高效的解决方法,这也是影响非球面超精密加工的关键因素之一。对非球面的检测主要分为接触式与非接触式两种[8]。接触式一般采用轮廓仪法,非接触式主要分为补偿法和计算全息法(CGH)[9-10]。Q-type非球面,由于是旋转对称的非球面,利用轮廓仪检测是一种快捷有效的方法。若使用计算全息法检测,不仅全息片计算量大,对其复位精度要求严格,而且不同参数的非球面需要对应制作不同的全息片,通用性较差[11-12]。本文提出了一种MATLAB软件与非球面轮廓仪相结合的方法,通过MATLAB软件将Q-type多项式拟合为非球面轮廓仪的理论参考方程,即标准偶次非球面方程,拟合得到非球面系数后将其输入到非球面轮廓仪中得到检测数据,再对检测数据和拟合误差进行数据处理后得出检测结果。该方法可以简捷有效地解决加工过程中Q-type非球面的检测问题,以便后续的加工。
2 Q-type非球面
2.1 Q-type函数多项式的数学描述
Q-type函数多项式包括Q-con和Q-bfs两种形式,Q-con型函数多项式表征非球面的基本形式是在二次曲面的基础上附加新型多项式。Forbes等[1-2]通过选择一系列正交基底构造新型多项式,其表达式为
Q-bfs型函数多项式则定义了一个非球面,其特征量是从最佳拟合球面到非球面的方均根斜率偏离量,其表达式为
式中:
2.2 Q-type非球面表面的拟合
本文中待检测的是Q-bfs型非球面,具体参数如下:
非球面轮廓仪的理论参考方程为标准偶次非球面方程[15],表示为
式中:
在MATLAB软件中使用非线性最小二乘法进行数据拟合[16-17],拟合误差在±50 nm以内,检测完成后的数据处理阶段会将拟合误差加入其中,因此拟合误差不会对检测结果产生影响。拟合后的标准偶次非球面顶点曲率半径
如
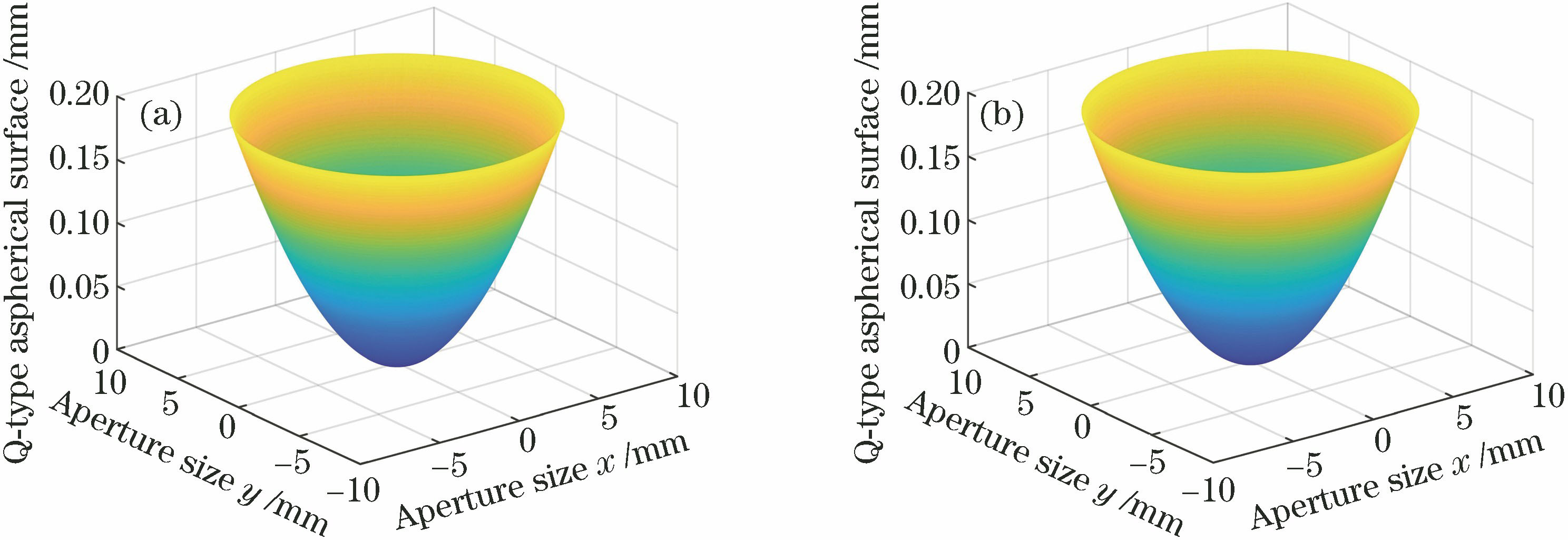
图 1. 非球面理论面形。(a) Q-type非球面;(b)拟合标准偶次非球面
Fig. 1. Theoretical aspherical surface. (a) Q-type asphere; (b) fitting standard even asphere
3 Q-type非球面的检测
在检测之前需完成Q-type非球面和拟合标准偶次非球面的加工。本次加工使用型号为Nanoform 700 Ultra的单点金刚石超精密车床,选取两把刀尖半径为1 mm、前角为0°的金刚石刀具,分别用作粗加工、半精加工与精加工,最终达到面形误差峰谷(PV)值<0.1 μm,表面粗糙度方均根(RMS)值<0.02 μm的超精密加工要求。在加工过程中,将各非球面面形参数输入到加工软件Diffsys中,得到两个非球面的最佳拟合球面半径,即用来进行粗加工的球面半径。由MATLAB软件可计算得到非球面偏离最佳拟合球面的面形偏离量,即精加工需去除量。如
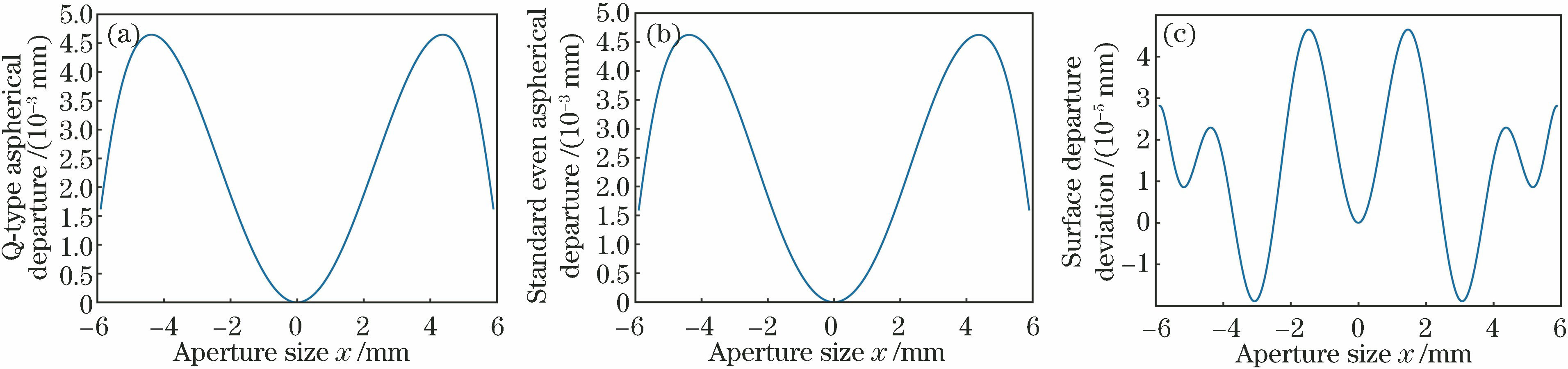
图 3. 面形偏离量曲线。(a) Q-type非球面;(b)拟合标准偶次非球面;(c)两非球面偏离量差值
Fig. 3. Surface departure curves. (a) Q-type asphere; (b) fitting standard even asphere; (c) difference of deviation between two aspheric surfaces
编写好加工程序后,采用多轴联动的加工方式,对两个非球面设置相同的加工参数。各个阶段的主要加工参数[18],即主轴转速、进给率、切削深度见
待精加工完成后将工件从车床取下,如
本次检测使用的非球面轮廓仪型号为Taylor-Hobson PGI-1240,选择的钻石探针针尖半径为0.02 mm,
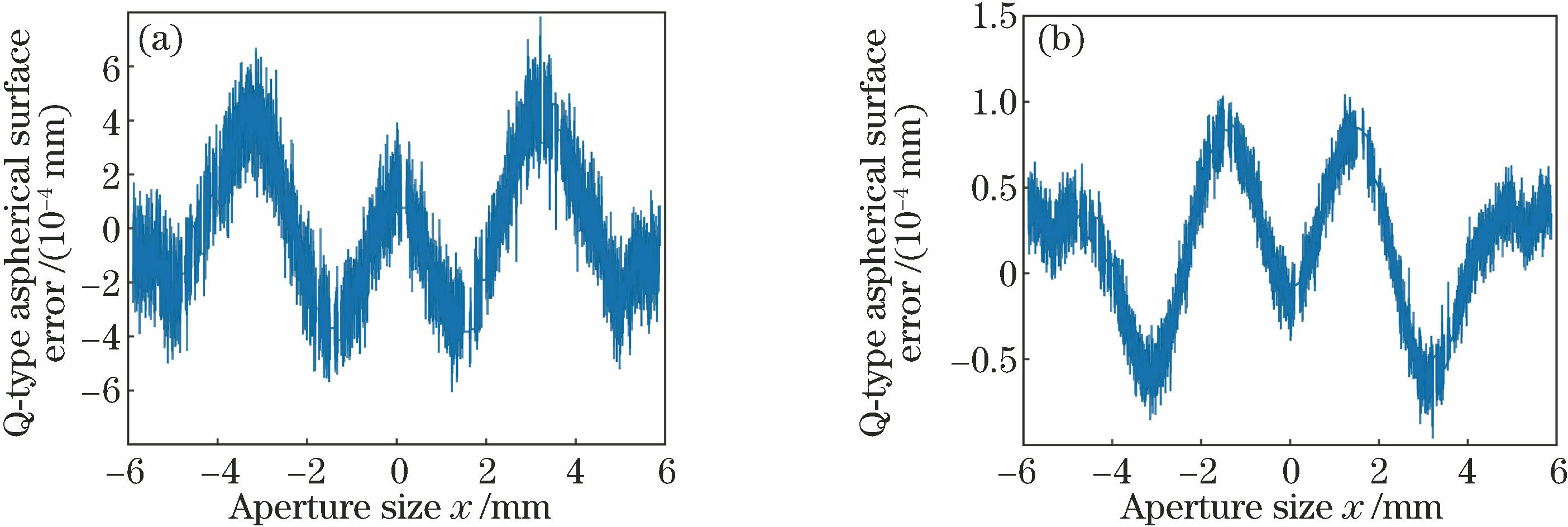
图 6. Q-type非球面检测结果。(a)数据处理前;(b)数据处理后
Fig. 6. Detection results of Q-type asphere. (a) Before data processing; (b) after data processing
表 1. 主要加工工艺参数
Table 1. Main processing parameters
|
4 结论
利用Nanoform 700 Ultra单点金刚石超精密车床加工了材料为单晶铜,全口径为11.8 mm的Q-type非球面和标准偶次非球面,并在首次加工完成后使用非球面轮廓仪检测Q-type非球面,以确定是否满足第一阶段加工精度要求。对待测Q-type非球面多项式进行最小二乘拟合,将其拟合为非球面轮廓仪的理论参考方程,并得到拟合误差曲线。检测过程中利用非球面轮廓仪采集大量坐标点得出工件表面相对于理论参考值的面形误差。将拟合误差加入到面形误差值中得到的即为最终加工面形误差。检测结果表明,Q-type非球面的面形误差PV值为0.1963 μm,表面粗糙度RMS值为0.03412 μm,满足第一阶段加工精度要求,可开始下一阶段加工。
[4] 周向东, 白剑. Q-type非球面小畸变全景环带光学系统设计[J]. 光学学报, 2015, 35(7): 0722003.
[5] 李闯, 薛常喜, 杨红芳, 等. 基于Q-type非球面的电子内窥镜物镜光学系统设计[J]. 光学学报, 2017, 37(6): 0622001.
[8] 师途, 杨甬英, 张磊, 等. 非球面光学元件的面形检测技术[J]. 中国光学, 2014, 7(1): 26-46.
[9] 席建普, 李彬, 任东旭, 等. 大口径非球面元件磨削轮廓测量技术研究进展[J]. 激光与光电子学进展, 2018, 55(3): 030008.
[10] 何丽, 武中华, 康燕, 等. 大非球面度快焦比中大口径高次非球面检测[J]. 激光与光电子学进展, 2016, 53(12): 122201.
[11] 高松涛, 隋永新, 杨怀江. 用计算全息图对非球面的高精度检测与误差评估[J]. 光学学报, 2013, 33(6): 0612003.
[12] 邵山川, 陶小平, 王孝坤. 基于条纹反射的超精密车削反射镜的在位面形检测[J]. 激光与光电子学进展, 2018, 55(7): 071203.
[15] 潘君骅. 光学非球面的设计、加工与检验[M]. 苏州: 苏州大学出版社, 2004: 62- 68.
Pan JH. The design, manufacture and test of the aspherical optical surfaces[M]. Suzhou: Soochow University Press, 2004: 62- 68.
[16] 尤越, 王乔方, 字正华. 一种基于Matlab的非球面光学元件面形参数测试技术[J]. 红外技术, 2014, 36(4): 331-335.
[17] Solaguren-Beascoa Fernández M. MATLAB implementation for evaluation of measurements by the generalized method of least squares[J]. Measurement, 2018, 114: 218-225.
贾孟, 薛常喜, 李闯, 兰喜瑞, 王蕾, 王伦, 吴百融. 基于MATLAB与非球面轮廓仪的Q-Type非球面检测技术[J]. 激光与光电子学进展, 2019, 56(15): 151201. Meng Jia, Changxi Xue, Chuang Li, Xirui Lan, Lei Wang, Lun Wang, Bairong Wu. Q-Type Asphere Testing Technology Based on MATLAB and Aspheric Profilometer[J]. Laser & Optoelectronics Progress, 2019, 56(15): 151201.