扫描方向对变厚度熔覆成形件组织与力学性能的影响
下载: 947次
1 引言
激光熔覆沉积技术是成形金属薄壁件的一种主要方法[1],采用该技术能够制造具有复杂结构的薄壁件[2]。根据熔覆层厚度的变化,薄壁件成形方式主要分为两种[3]:等厚度熔覆层沉积(等厚度沉积)和变厚度熔覆层沉积(变厚度沉积)。现阶段,对等厚度沉积成形薄壁件性能的研究已取得显著进展。薄壁件的组织与力学性能受多种因素的影响,如:激光功率[4]、搭接率[5]、沉积方向[6]等工艺参数。Dinda等[7]指出,扫描方向会改变晶粒的生长方向。由于激光熔覆沉积的工艺特点,其成形件的拉伸性能具有显著的各向异性,表现为垂直于沉积方向的力学性能优于沉积方向的力学性能[8]。为解决该问题,相关学者进行大量研究后发现,通过优化扫描方式来控制热循环,可以改变成形件的微观组织,提高成形件的力学性能[9],主要体现为改变成形件的强度分布[10]。此外,热处理和热等静压等工艺方式也能细化晶粒,减小组织和性能的各向异性[11-12]。
在成形具有复杂几何特征的斜坡薄壁结构时,采用等厚度切片分层的增材成形方式会引起台阶效应,降低尺寸精度,而采用变厚度熔覆层成形则能有效解决该问题[13],但目前对变厚度熔覆层沉积性能的研究还比较少,尤其是关于扫描方向对力学性能的影响。鉴于此,本文重点研究了扫描方向对变厚度熔覆成形件组织与力学性能的影响,采用从低到高和从高到低的扫描方向,以变厚度沉积的方式成形相同倾斜角度的斜坡薄壁件,并与等厚度沉积方式成形的薄壁件进行对比,探究不同扫描方向下薄壁件抗拉强度的各向异性,以及不同位置处微观组织和硬度的变化规律,为变厚度成形薄壁件的工艺规划提供依据。
2 试验
2.1 试验条件
斜坡薄壁件在SVW80C-3D增/减材复合加工中心沉积成形,沉积原理如
表 1. 316L不锈钢的化学成分
Table 1. Chemical compositions of 316L stainless steel
|
表 2. 基板的化学成分
Table 2. Chemical compositions of substrate
|
2.2 扫描轨迹规划与参数选择
如

图 2. 沉积方式。(a)从高到低等厚度沉积;(b)从高到低变厚度沉积;(c)从低到高变厚度沉积
Fig. 2. Deposition methods. (a) Uniform thickness deposition (from high to low); (b) variable thickness deposition (from high to low); (c) variable thickness deposition (from low to high)
影响熔覆层几何尺寸的工艺参数主要包括送粉速率、激光功率及扫描速度。送粉速率和激光功率对熔覆层尺寸的控制具有迟滞性,难以对其进行准确、动态控制[3],因此选用动态扫描速度成形变厚度熔覆层。
本试验中的主要成形参数源于前期基础试验,参数值如
表 3. 激光熔覆沉积成形过程中的工艺参数
Table 3. Process parameters of laser cladding deposition
|
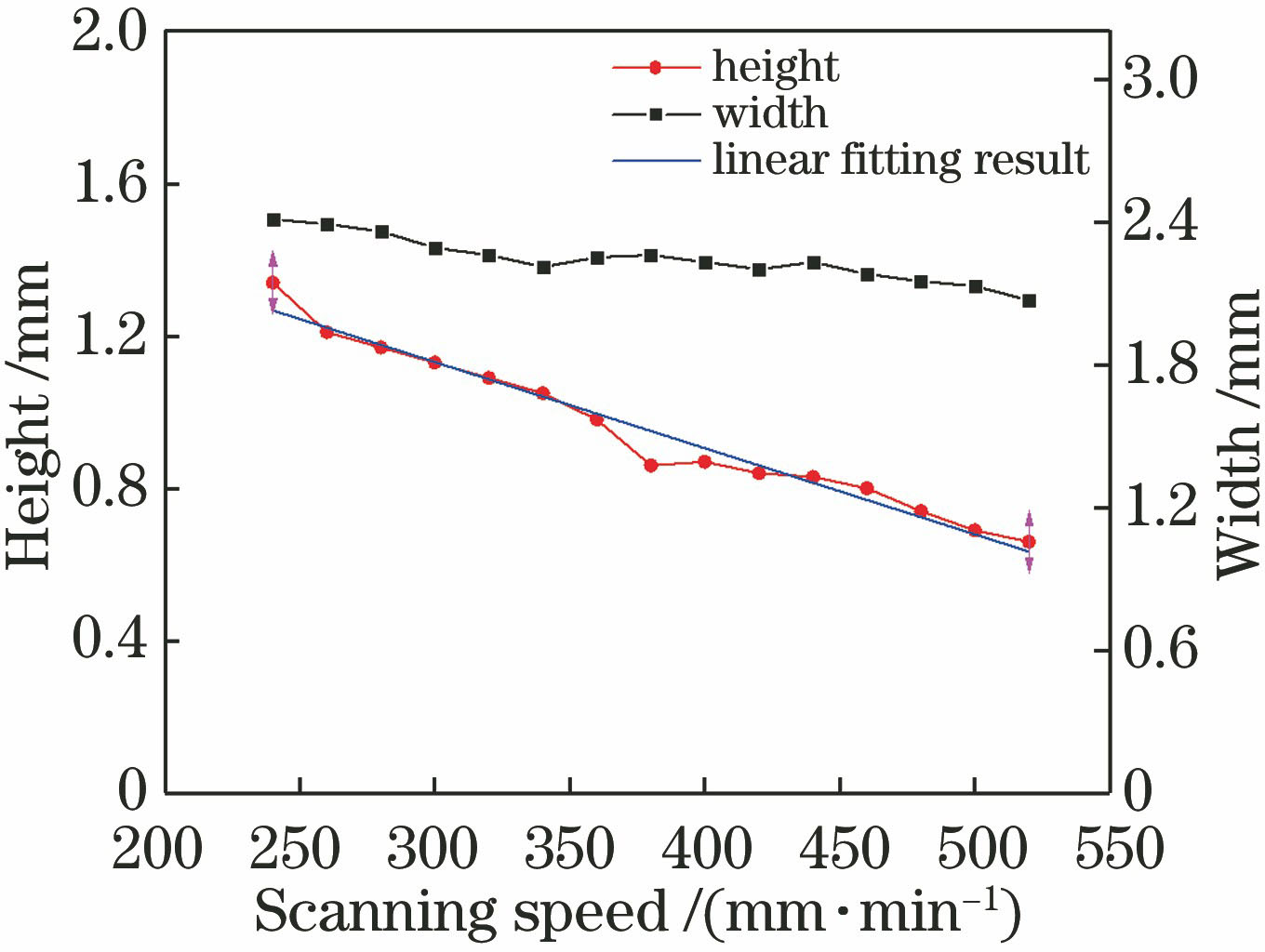
图 3. 扫描速度对熔覆层宽度与高度的影响
Fig. 3. Effect of scanning speed on height and width of cladding layer
2.3 试验过程
采用标准金相方法制备样品,用王水溶液(硝酸和盐酸溶液按体积比为1∶3配制而成)对试样表面进行化学腐蚀,然后通过OLS4100 3D 激光共聚焦显微镜观察斜坡薄壁件纵截面、横截面上晶粒的生长方向及分布。根据国标GB/T 228.1—2010设计的拉伸件尺寸和选取位置如
3 试验结果与分析
3.1 微观组织分析
薄壁件横截面上的晶粒分布如
在激光沉积成形过程中,熔覆层的显微组织与温度梯度、凝固速率
薄壁件同一高度处纵截面的微观组织如
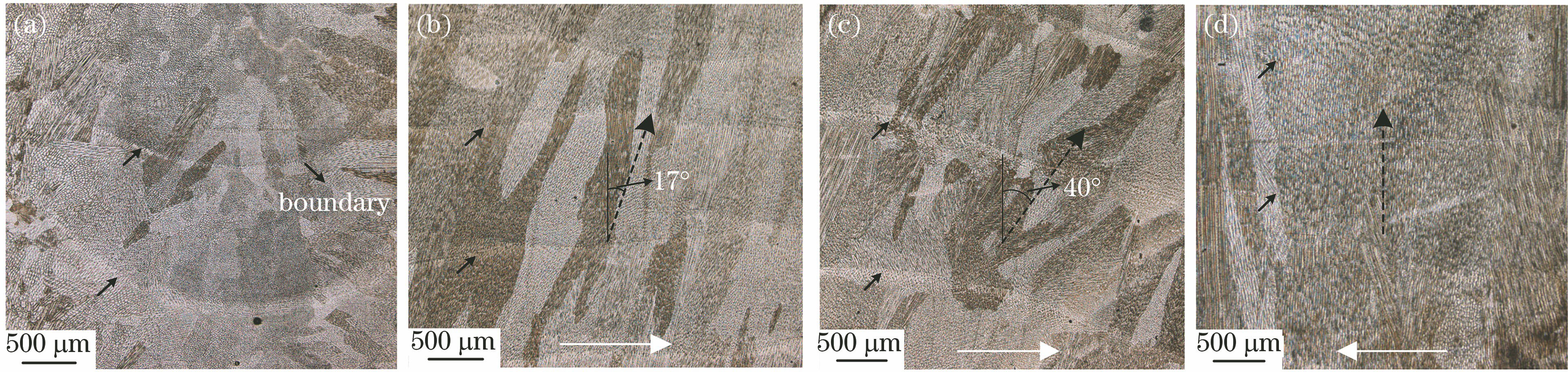
图 6. 微观组织。(a)横截面;(b)从高到低等厚度沉积纵截面;(c)从高到低变厚度沉积纵截面;(d)从低到高变厚度沉积纵截面
Fig. 6. Microstructures. (a) Cross section; (b) longitudinal section by uniform thickness deposition (from high to low); (c) longitudinal section by variable thickness deposition (from high to low); (c) longitudinal section by variable thickness deposition (from low to high)
3.2 拉伸性能
为避免边缘气孔、裂纹等缺陷的影响,拉伸件过渡区的位置应尽量偏离边缘处。由
由
表 4. 不同沉积方式下不同位置处拉伸件的抗拉强度与伸长率
Table 4. Tensile strength and elongation of tensile part at different positions under different deposition strategies
|
从
从低到高变厚度沉积成形薄壁件中选择抗拉强度最大的试件,对其断口进行分析,断口形貌如
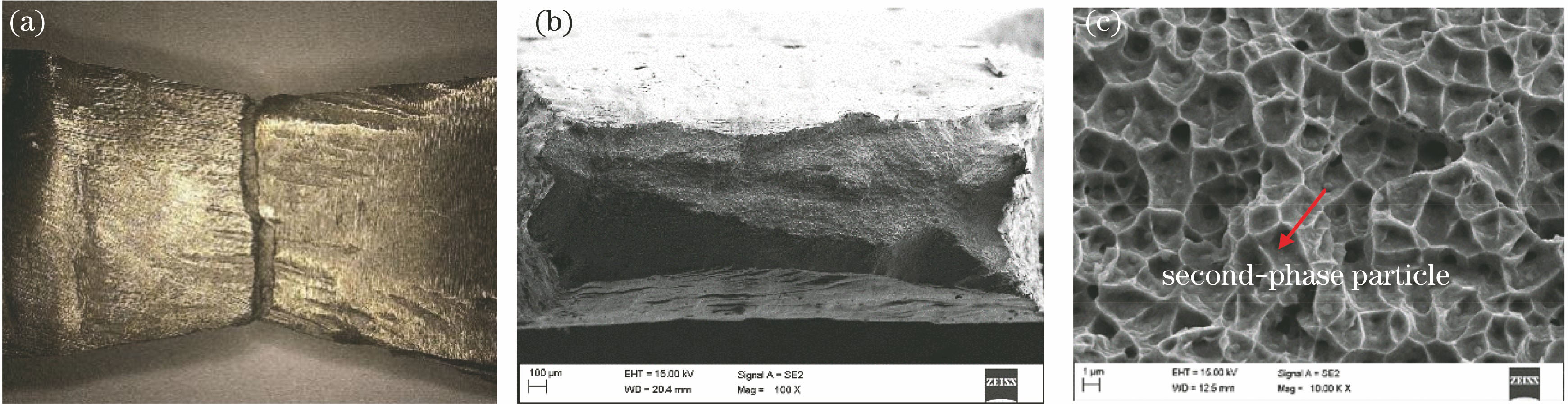
图 7. 扫描电镜下的断口形貌。(a)拉伸试样的宏观断口形貌;(b)低倍扫描电镜下的断口截面;(c)高倍扫描电镜下的断口截面
Fig. 7. Fracture morphologies obtained by scanning electron microscope. (a) Macro fracture morphology of tensile sample; (b) fracture morphology obtained by scanning electron microscope with low magnification; (c) fracture morphology obtained by scanning electron microscope with high magnification
3.3 硬度
在水平方向上,与等厚度沉积成形方式相反,变厚度沉积成形件硬度最高点均在高端测量点附近,如
从
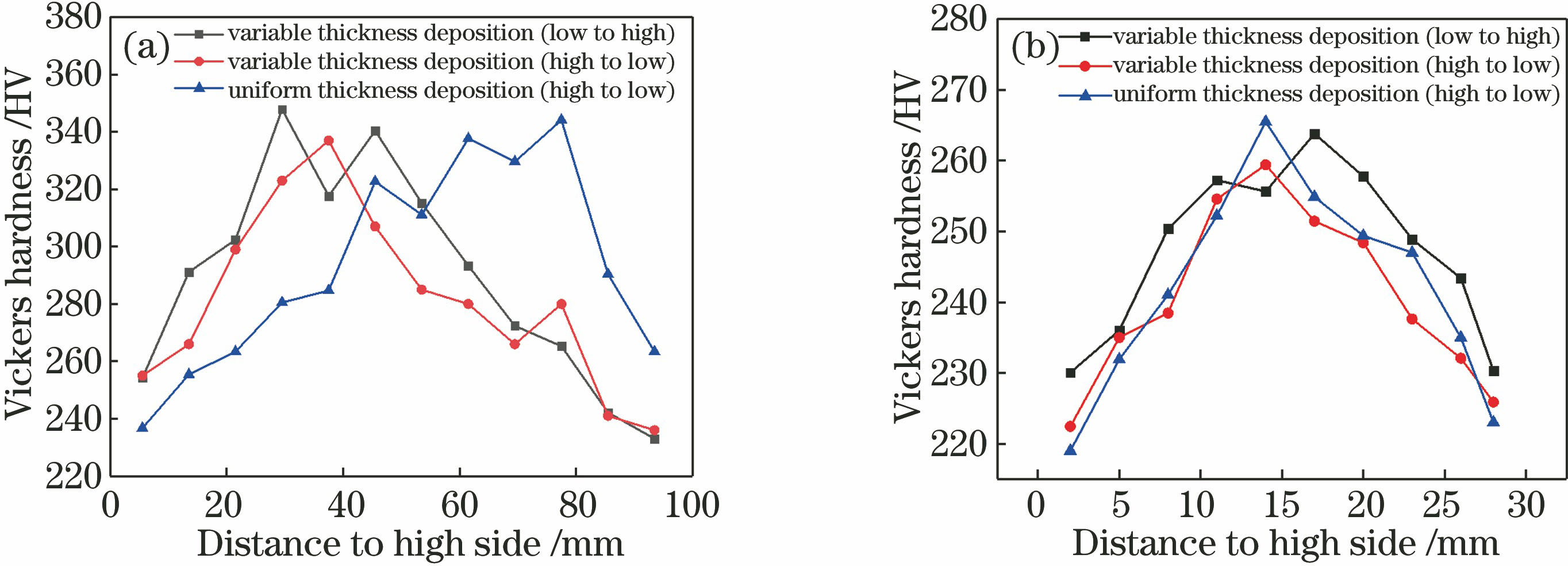
图 8. 硬度曲线。(a)水平方向;(b)沉积方向
Fig. 8. Plots of hardness. (a) Horizontal direction; (b) deposition direction
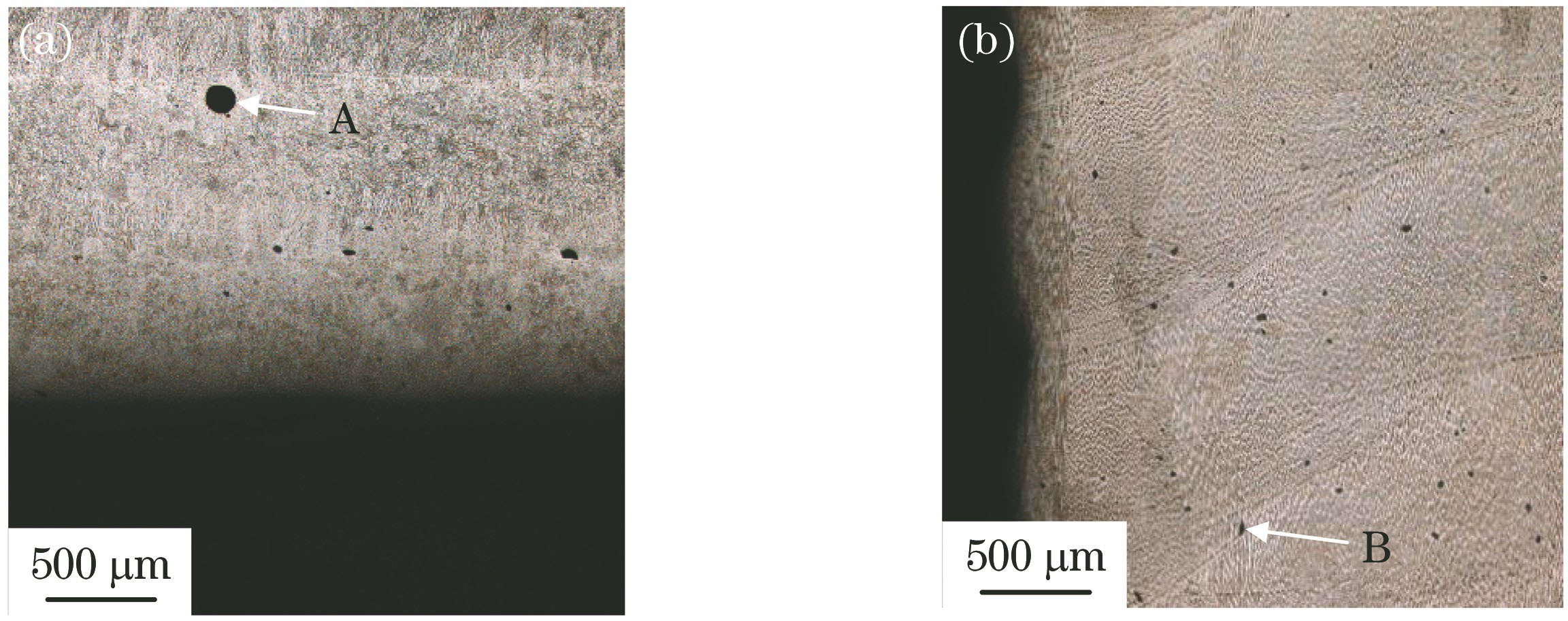
图 9. 斜坡薄壁件不同位置处的孔洞分布。(a)底部;(b)边缘
Fig. 9. Pore distributions at different positions of ramp's thin-walled part. (a) Bottom; (b) edge
在沉积方向上,等厚度和变厚度沉积成形薄壁件硬度的变化趋势一致,如
4 结论
变扫描方向沉积变厚度成形的斜坡薄壁件的微观组织、硬度和拉伸性与等厚度沉积的明显不同。
薄壁件晶粒由定向生长的细长柱状晶和等轴晶组成。在斜坡薄壁件的横截面上,晶粒的生长方向垂直于层与层的边界,指向熔池中心。纵截面上晶粒的生长方向与熔覆头的扫描路径有关,采用从高到低变厚度沉积成形的薄壁件的晶粒生长方向更加倾斜。
晶粒生长方向和扫描轨迹共同决定了试样的抗拉强度,采用从低到高变厚度沉积方式可以避免晶粒生长方向与扫描轨迹垂直,强度优于其他两种方式成形的试样的强度。激光熔覆沉积成形316L合金拉伸试样出现韧性断裂,断口呈韧窝状,且韧窝内存在第二相粒子。
在水平方向上,三种沉积方式成形的试样的硬度都不均匀,在240~360 HV范围内变化,但变厚度沉积成形薄壁件高端测量点的硬度优于低端测量点,扫描方向对其硬度的影响较弱。由于其高度连续可变,变厚度成形具有广阔的工程化应用前景,本文的研究内容对变厚度沉积的应用具有一定的参考意义。
[1] 邓志强, 石世宏, 周斌, 等. 不等高弯曲弧形薄壁结构激光熔覆成形[J]. 中国激光, 2017, 44(9): 0902005.
[2] 王续跃, 王彦飞, 江豪, 等. 圆形倾斜薄壁件的激光熔覆成形[J]. 中国激光, 2014, 41(1): 0103006.
[4] 肖鱼, 路媛媛, 郭溪溪, 等. 激光增材制造薄壁结构件工艺及性能的研究[J]. 激光与光电子学进展, 2018, 55(8): 081405.
[8] MertensA, ReginsterS, ContrepoisQ, et al. Microstructures and mechanical properties of stainless steel AISI 316L processed by selective laser melting[J]. Materials Science Forum, 2014, 783/784/785/786: 898- 903.
[9] 陈德宁, 刘婷婷, 廖文和, 等. 扫描策略对金属粉末选区激光熔化温度场的影响[J]. 中国激光, 2016, 43(4): 0403003.
[11] 丁利, 李怀学, 王玉岱, 等. 热处理对激光选区熔化成形316不锈钢组织与拉伸性能的影响[J]. 中国激光, 2015, 42(4): 0406003.
[15] Lai YB, BoY, Wang DY. Theoretical calculation and experimental verification of Z increment in laser metal direct manufacturing[C]∥International Symposium on Mechanical Engineering and Material Science (ISMEMS 2017), May 25-26 2017, Xi'an, China.France: Atlantis Press, 2017.
[19] AbdalkariemHassan. 增材制造中激光扫描路径对倾斜薄壁件力学性能的影响研究[D]. 大连: 大连理工大学, 2016: 29- 34.
HassanA. Effect of slicing trajectories on mechanical properties of sloped thin-walled part produced by laser additive manufacturing[D]. Dalian: Dalian University of Technology, 2016: 29- 34.
周显新, 辛博, 巩亚东, 张伟健, 张海权. 扫描方向对变厚度熔覆成形件组织与力学性能的影响[J]. 中国激光, 2019, 46(8): 0802003. Xianxin Zhou, Bo Xin, Yadong Gong, Weijian Zhang, Haiquan Zhang. Effect of Scanning Direction on Microstructure and Mechanical Properties of Part Formed via Variable Thickness Layer Cladding Deposition[J]. Chinese Journal of Lasers, 2019, 46(8): 0802003.