标记非对称变形导致的对准误差修正方法及其在套刻测量中的应用
下载: 1535次
1 引言
集成电路是信息产业的核心,光刻机是极大规模集成电路制造的关键装备。目前193 nm浸没式投影光刻机与多重图形技术结合已经实现10 nm乃至7 nm节点集成电路的量产[1-4]。套刻精度是光刻机的三大性能指标之一,集成电路工艺节点的持续缩小对套刻精度(即两层曝光图形间的相对位置精度)提出了越来越高的要求,对于10 nm工艺节点,套刻精度要求在3 nm以下[5-7]。两层曝光图形之间的纳米精度套刻要求以亚纳米精度测量硅片位置[4],在光刻机中硅片位置的测量是通过硅片对准系统实现的,其测量精度是保障套刻精度的关键。由于硅片对准中用到的对准标记制作在硅片上,对准位置测量精度容易受到光刻工艺的影响,因此提高硅片对准的工艺适应性显得尤为重要。当前,高端光刻机中的主流硅片对准技术是自参考干涉仪智能对准传感器混合(SMASH)对准技术实现的,采用的硅片对准标记是相位衍射光栅[8-10]。硅片对准标记经过化学机械抛光等工艺后会产生非对称变形,这种非对称变形会引入硅片位置测量误差。
目前,降低对准标记非对称变形导致的位置测量误差的主要方法是工艺验证方法,对已完成的包含两层图形的硅片,该方法采用扫描电子显微镜(SEM)精确测量实际的套刻误差,根据测量结果,在相同的工艺中修正对准测量位置误差,以提高套刻精度[9,11-12]。然而,即使在相同的批次或相同的光刻工艺中,甚至在硅片不同的曝光场之间,对准标记非对称变形程度也会不一致,从而使得工艺验证方法存在一定误差,因此工艺验证方法存在一定的工艺适应性问题。另外,工艺验证方法也存在耗时且价格昂贵等问题[5,11]。
在SMASH对准技术中,一般采用多种波长和偏振态的照明光束。采用不同波长和偏振态的照明光束照明对准标记非对称变形时,对准位置的测量结果存在差异。利用这种差异,本文提出了一种新的修正对准标记非对称变形导致的对准位置测量误差的方法,与工艺验证方法相比,所提方法具有较高的工艺适应性,并可在对准过程中进行实时修正。由于对准标记和套刻测量标记在集成电路制造的前道工艺中经过了相同的工艺流程,因此两者的非对称变形存在一定的关联。本文进一步利用不同波长和偏振态照明情况下的对准位置差异来修正套刻测量标记非对称变形导致的套刻测量误差,从而提高套刻测量的工艺适应性。
2 标记非对称变形对对准精度的影响
SMASH对准技术原理如
当对准标记结构对称时,对准信号强度
式中:
对准标记位置可表示为
当对准标记发生非对称变形时,对准信号强度
对准标记位置可表示为
由(2)、(4)式可以得到由对准标记非对称变形引入的对准误差为
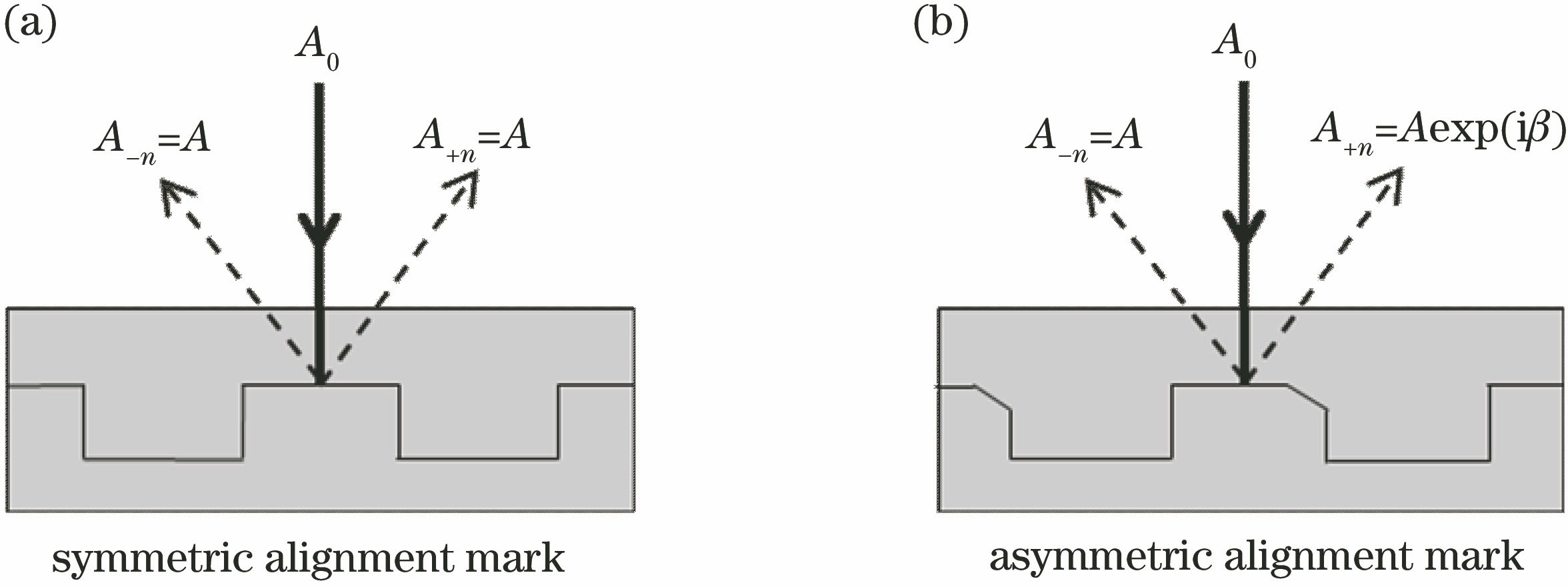
图 2. 不同对准标记的光束衍射示意图。 (a)对称对准标记;(b)非对称对准标记
Fig. 2. Beam diffraction diagrams of different alignment marks. (a) Symmetric alignment mark; (b) asymmetric alignment mark
3 对准测量误差仿真及修正方法
由上述分析可知,对准标记的非对称变形会引入衍射光束的相位变化,从而带来对准位置测量误差。本节通过仿真软件COMSOL模拟在不同波长和偏振态照明情况下,对准标记衍射光束的相位,得到对准测量误差与对准标记非对称变形的形状、变形量的关系,并根据仿真数据修正对准标记非对称变形引入的对准测量误差。
仿真模型如
仿真用到的材料(Si和SiO2)的折射率如
表 1. 不同波长下对准标记材料的折射率
Table 1. Refractive indexes with alignment mark materials under different wavelengths
|
对准标记产生的非对称变形形状随光刻工艺的不同而变化[11,14-15],为了简化仿真模型,一般采用圆角和楔角两种形状的非对称变形形状[16-17],其结构分别如

图 4. 不同形状的非对称对准标记。 (a)圆角形状;(b)楔角形状
Fig. 4. Asymmetric alignment marks with different shapes. (a) Round shape; (b) wedge shape
通常用对准标记的±1、±3、±5和±7级衍射光束测量对准标记的位置,对于周期为16 μm的光栅对准标记,这4组衍射光束形成的对准信号与由对准标记非对称变形引入的对准误差相近[14],下面以对准标记±3级衍射光束形成的对准信号为例进行对准测量误差分析。在不同的波长和偏振态照明时,圆角和楔角形状的非对称变形对准标记引入的对准测量误差的仿真结果分别如
到了18 nm;而对于楔角非对称变形,在
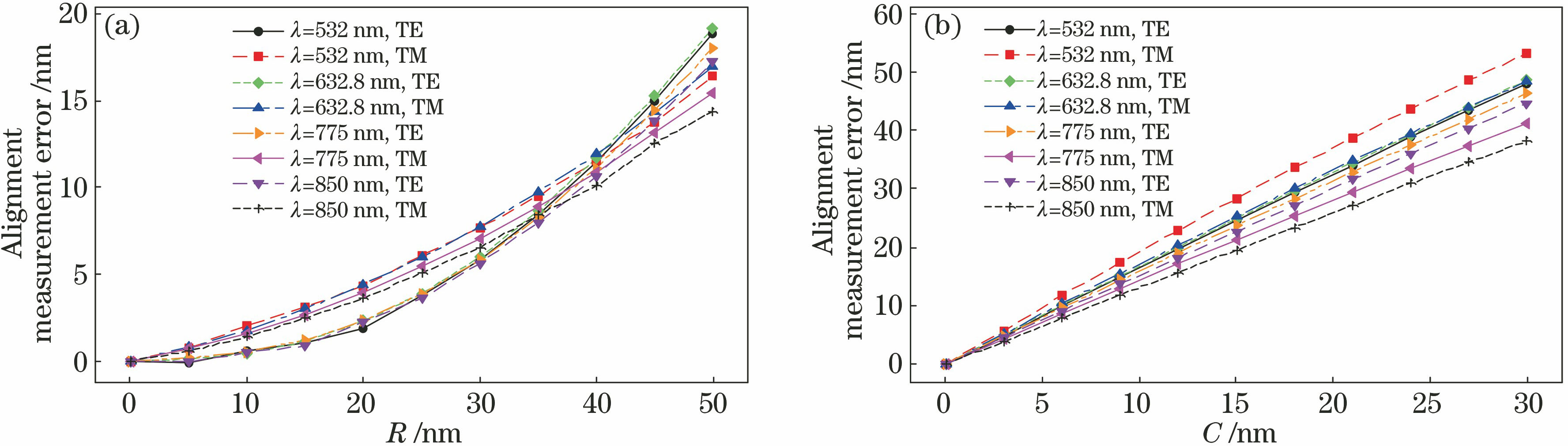
图 5. 不同波长和偏振态照明情况下,对准测量误差与不同非对称对准标记变形量间的关系。 (a)圆角形状;(b)楔角形状
Fig. 5. Alignment measurement errors as functions of deformations of different asymmetric alignment marks under illuminations with different wavelengths and polarizations. (a) Round shape; (b) wedge shape
为获得较高的对准测量误差来修正灵敏度,可以选取对准测量误差差异较大的两个测量通道进行对准测量误差的修正。为便于分析,将632.8 nm照明波长、TE偏振态时圆角非对称变形引入的对准测量误差表示为
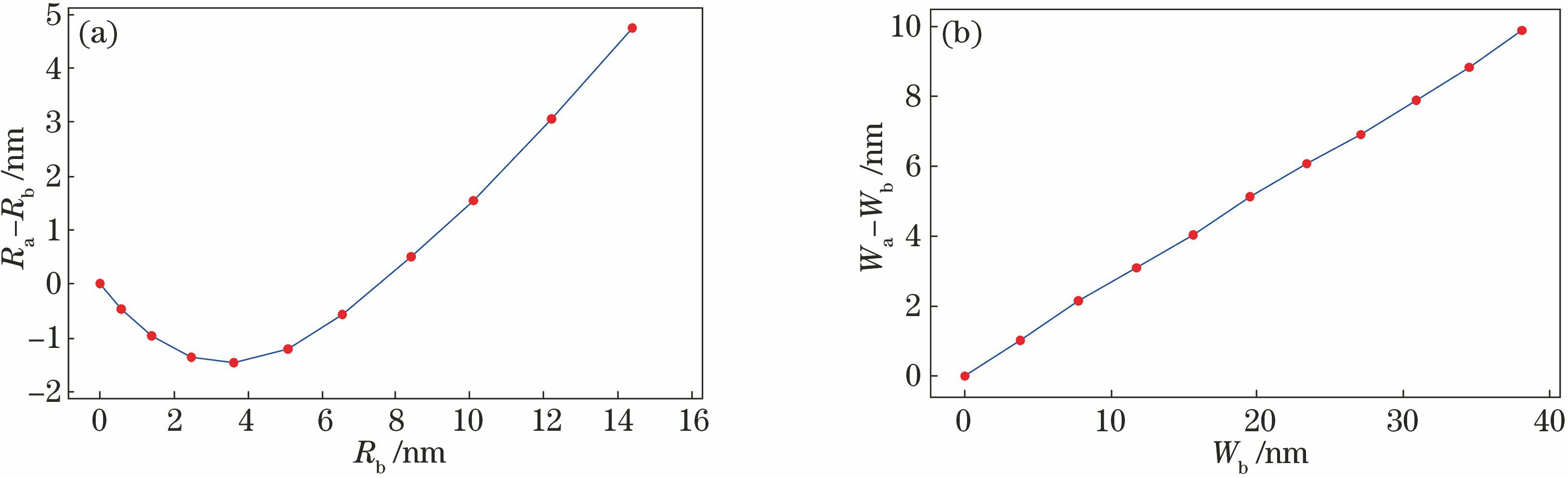
图 6. 仿真结果。 (a) Ra-Rb与Rb的关系;(b) Wa-Wb与Wb的关系
Fig. 6. Simulation results. (a) Ra-Rb as a function of Rb; (b) Wa-Wb as a function of Wb
根据
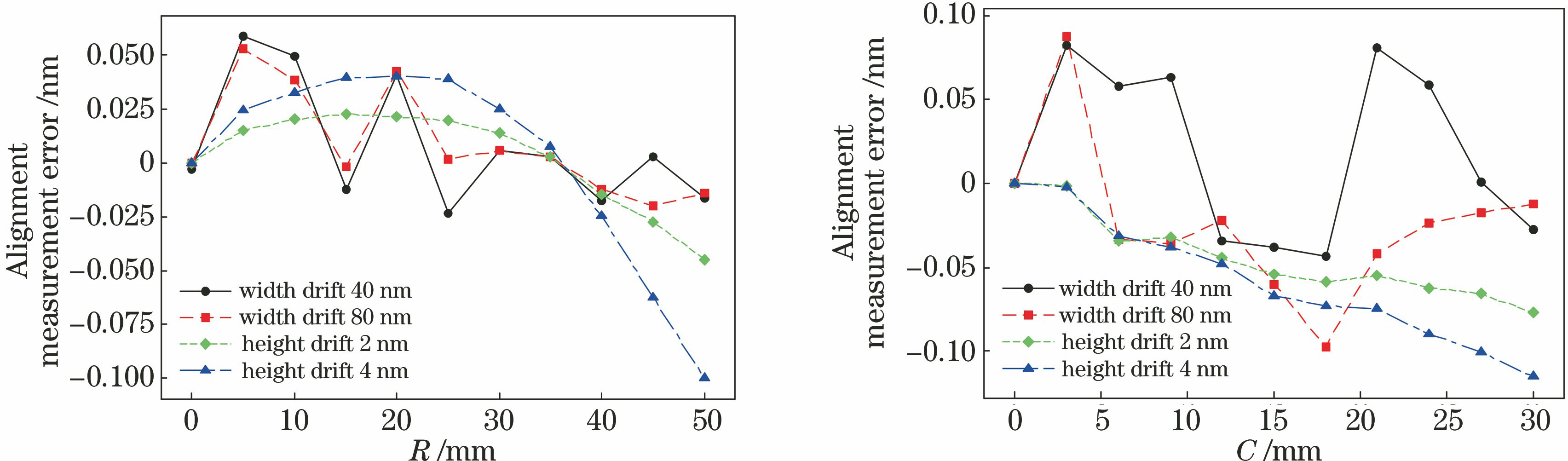
图 7. 不同形状非对称对准标记下修正后的对准测量误差。 (a)圆角形状;(b)楔角形状
Fig. 7. Alignment measurement errors caused by asymmetric alignment marks with different shapes after calibration. (a) Round shape; (b) wedge shape
从
以周期为16 μm的相位衍射光栅作为对准标记,以±3级衍射光束形成的对准信号为例对提出的修正方法进行验证,但该方法也适用于其他的光栅周期和衍射级次,而且对于将细分型等其他形式的相位衍射光栅作为对准标记的情况也依然适用。假定对准标记的非对称变形为圆角和楔角两种形状,并且变形只发生在对准标记光栅的栅线一侧。在实际的光刻工艺中,标记形状变化比较复杂,对于这种复杂形状的标记,本方法同样适用。可以采用SEM等手段获得实际标记的具体参数,然后将获得的标记参数代入该方法的仿真模型中进行计算。同时,为了提高对准测量误差的修正精度,可以同时利用多个照明波长和偏振态、多个衍射级次形成的对准测量信号进行修正。
4 在套刻测量中的应用
套刻测量的目的是用来判断两层不同工艺层中集成电路图形的相对位置偏差,即测量实际光刻工艺的套刻精度。套刻测量是用来监控光刻工艺的实际套刻精度,并进行工艺改善,以提高套刻精度的重要方法。基于衍射的套刻测量(DBO)技术是主流的套刻测量技术[18-19],

图 8. 基于DBO技术测量套刻精度的原理图。(a) eoverlay<0;(b) eoverlay=0;(c) eoverlay>0
Fig. 8. Principle diagrams of overlay precision measurement based on DBO technique. (a) eoverlay<0; (b) eoverlay=0; (c) eoverlay>0
式中:
与对准标记经过光刻工艺后会产生非对称变形相似,作为套刻标记的相位衍射光栅经过相同的光刻工艺后也会产生非对称变形。当套刻标记中的光栅产生非对称变形时,即使套刻误差为0,套刻标记的正负级次衍射光束的能量也不再相等,并因此带来套刻测量误差。如
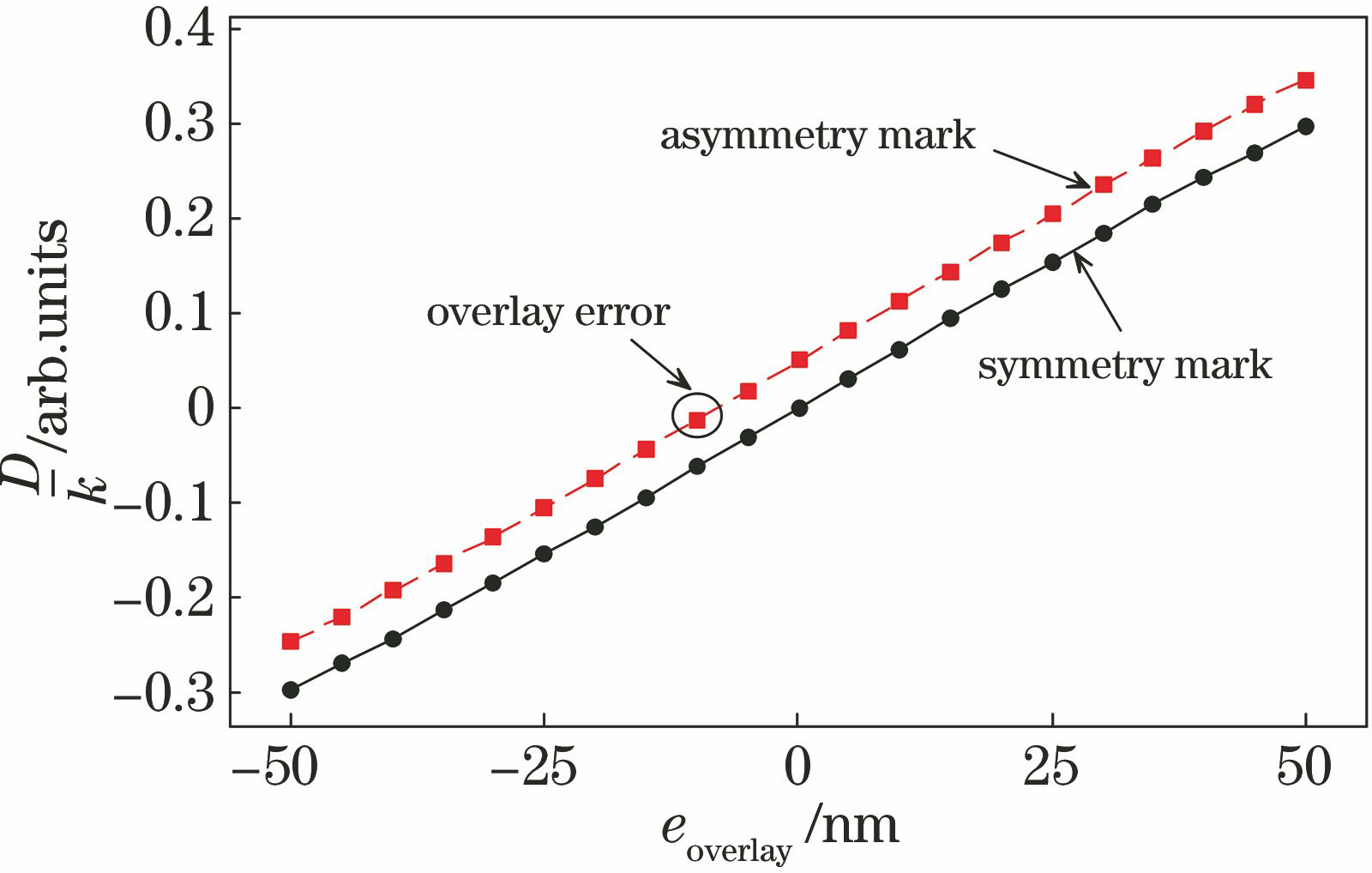
图 9. 套刻标记非对称变形导致的套刻测量误差
Fig. 9. Overlay measurement error caused by asymmetric deformation of overlay mark
以
仿真用到的材料折射率如
表 2. 不同波长下套刻标记材料的折射率
Table 2. Refractive indexes of overlay mark materials under different wavelengths
|
套刻标记非对称变形导致的套刻测量误差的仿真结果如
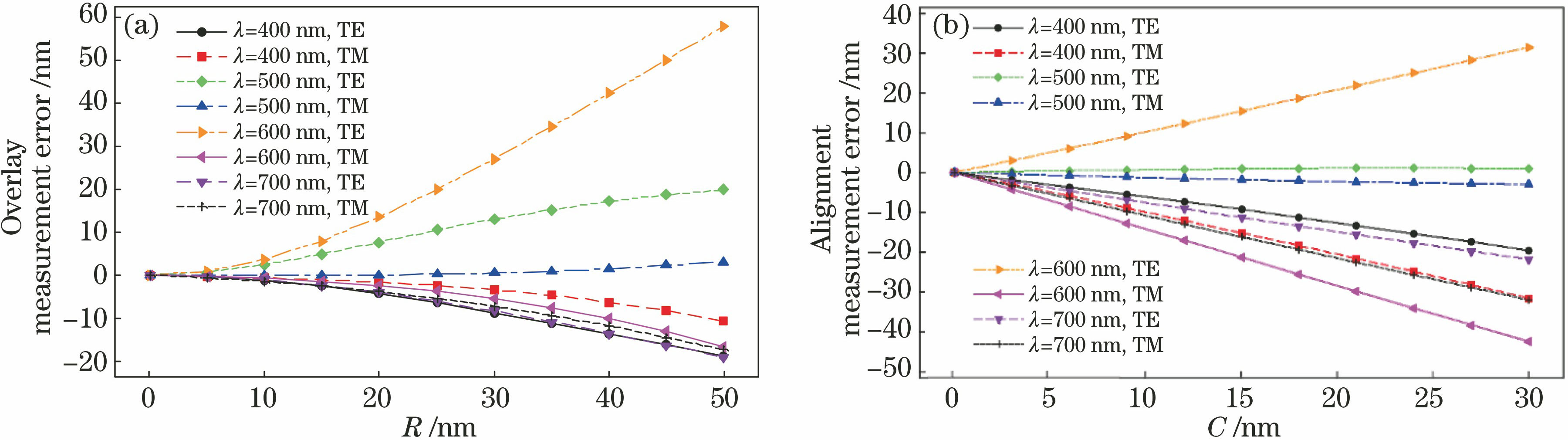
图 11. 不同波长和偏振态照明情况下,套刻测量误差与不同非对称套刻标记变形量间的关系。(a)圆角形状;(b)楔角形状
Fig. 11. Overlay measurement error as a function of deformation of different asymmetric overlay marks under illuminations with different wavelengths and polarizations. (a) Round shape; (b) wedge shape
由套刻标记非对称变形引入的套刻测量误差同样可以利用对准标记非对称变形对应的多通道对准测量信息差异进行校正。假定对准标记和套刻标记在同一曝光场,并经过相同的光刻工艺,非对称变形量相同,可以选择
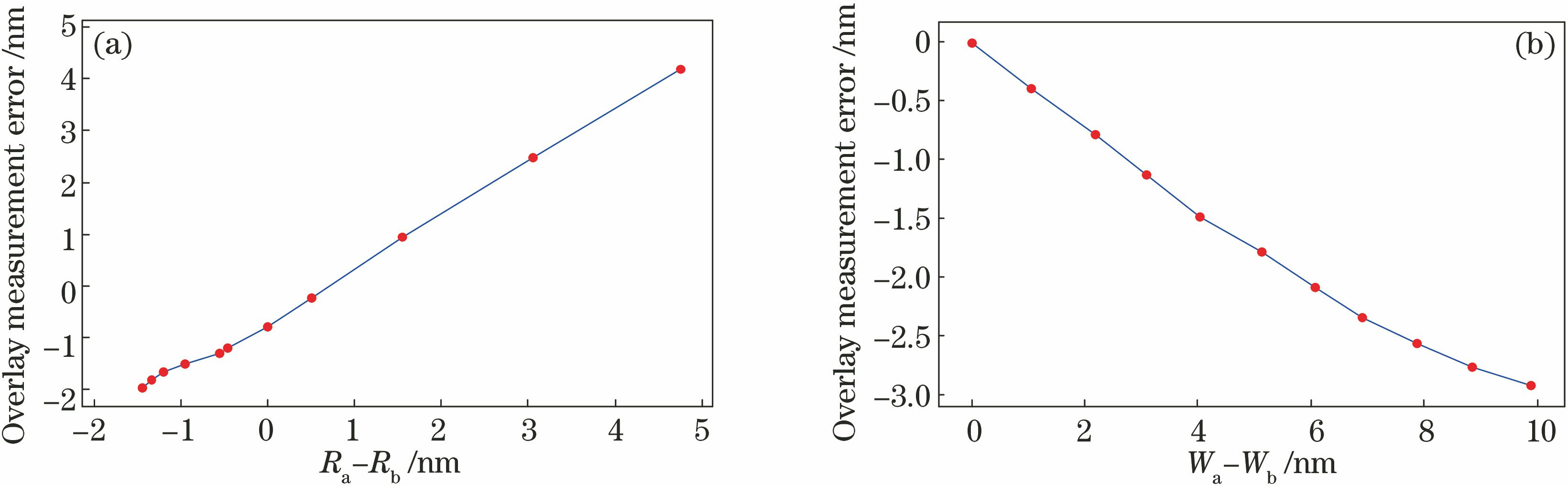
图 12. 不同非对称变形引入的套刻测量误差与对准测量误差间的关系。 (a)圆角形状;(b)楔角形状
Fig. 12. Overlay measurement error as a function of alignment measurement error caused by different asymmetric deformations. (a) Round shape; (b) wedge shape
在对准标记槽深分别变化2 nm和4 nm、槽宽分别变化40 nm和80 nm的情况下,由标记非对称变形引入的套刻测量误差修正后的仿真结果如
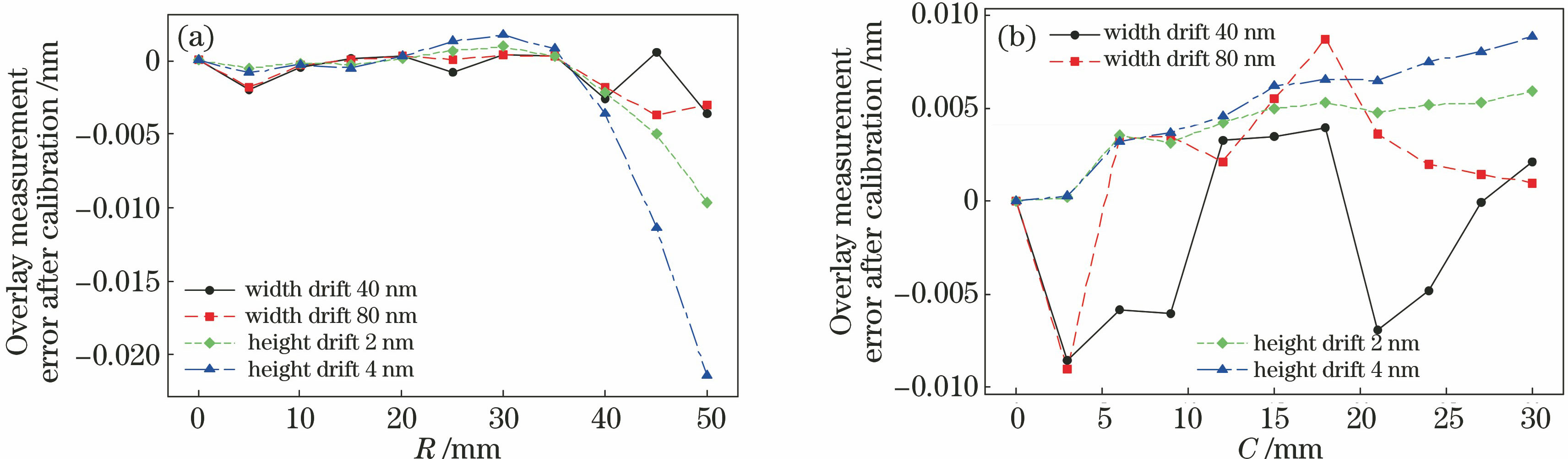
图 13. 不同形状非对称套刻标记下修正后的套刻测量误差仿真结果。(a)圆角形状;(b)楔角形状
Fig. 13. Simulation results of overlay measurement errors caused by asymmetric overlay marks with different shapes after calibration. (a) Round shape; (b) wedge shape
从
同样,考虑到对准光栅标记和套刻光栅标记的光栅周期不同,相同的光刻工艺引入的非对称变形量会有所差异,此套刻误差修正方法也可以根据实际测量得到的对准标记和套刻标记之间对应的非对称变形量关系,对套刻测量误差进行修正。
5 结论
本文提出了一种针对对准标记非对称变形引起的对准测量误差进行修正的方法,其原理是利用非对称变形对准标记的对准位置与照明波长、偏振态的相关性,修正由对准标记非对称变形带来的对准测量误差。仿真结果表明,在槽深受光刻工艺影响分别变化4 nm和80 nm的情况下,当对准标记产生圆角和楔角形状非对称变形时,利用所提方法修正后的由对准标记非对称变形引入的对准测量误差小于0.13 nm,说明了所提方法具有较好的工艺适应性。
研究了该方法在套刻标记非对称变形导致的套刻测量误差修正中的应用,仿真结果表明,在考虑对准标记槽深和槽宽受光刻工艺影响分别变化4 nm和80 nm的情况下,当对准标记和套刻标记发生圆角和楔角形状非对称变形时,利用所提方法修正后的由套刻标记非对称变形引入的套刻测量误差小于0.022 nm,可以忽略不计。
[1] 诸波尔, 王向朝, 李思坤, 等. 超高NA光刻投影物镜高阶波像差检测方法[J]. 光学学报, 2017, 37(4): 0412003.
[8] Boef AJ, HoogerlandM, Gajdeezko B. Alignmentsystem and method:US7564534[P/OL]. 2009-07-21[2019-01-05]. https:∥patents.google.com/patent/US7564534B2/en?oq=us7564534.
[10] 杜聚有, 戴凤钊, 步扬, 等. 基于自相干叠栅条纹的光刻机对准技术[J]. 中国激光, 2017, 44(12): 1204006.
[13] Refractive index[OL]. [2019-01-05].http:∥refractiveindex.info/.
Article Outline
杜聚有, 戴凤钊, 王向朝. 标记非对称变形导致的对准误差修正方法及其在套刻测量中的应用[J]. 中国激光, 2019, 46(7): 0704004. Juyou Du, Fengzhao Dai, Xiangzhao Wang. Calibration Method for Alignment Error Caused by Asymmetric Deformation of Mark and Its Application in Overlay Measurement[J]. Chinese Journal of Lasers, 2019, 46(7): 0704004.