玻璃表面嵌入式亚微米金属线的制备
下载: 1147次
1 引言
线宽在亚微米至几十纳米尺度的金属结构具有特殊的物理和化学性能,在微纳光子学、先进催化等[1-5]科学与工程领域具有重要应用。目前,金属微纳结构的制备有很多通用方法,如平面光刻、电子束和激光束直写、增材打印等[6-10]。其中,利用激光作为直写型工具制备金属微纳结构的技术具有空间构型灵活可控等突出优势[11-17]。Tanaka等[11]利用双光子诱导直接还原金属离子技术首次在银离子水溶液中制备出微米级线宽的三维立体导电金属结构。Cao等[12]通过在银离子水溶液中添加表面活性剂N-癸酰基肌氨酸钠盐来控制多光子诱导还原出的银纳米颗粒的尺寸,制备出最小线宽分别约为120 nm和180 nm的二维和三维金属银结构。Maruo等[13]在内含银离子的聚乙烯吡咯烷酮聚合物薄膜中通过激光直写制备出线宽可控(0.2~1.7 μm)且连续的二维和三维金属微结构。Xu等[14]通过在以柠檬酸钠为还原剂的化学镀银液中进行飞秒激光直写,实现了非平面基底上银纳米线的图案化沉积。Son等[15]通过飞秒激光直接烧结溶液沉积金属纳米颗粒的方法,实现了高分辨率金属纳米尺度图案的数字化制备。但需要指出的是,利用激光在液相、聚合物中直写制备的金属微纳薄膜通常直接附着在待沉积基底的表面。对于一些电介质基底,如玻璃、晶体等材料,上述沉积的金属和基底的本征结合力较弱,从而在很大程度上影响了器件长期工作的稳定性和可靠性。而通过在基底表面制备沟槽并结合后续的选择性金属沉积方法制备出嵌入式金属微纳结构是一种提高金属-电介质基底结合力的途径[18-21]。本研究组[18-20]曾利用飞秒激光在多种玻璃、铌酸锂等绝缘体表面烧蚀出了内含催化颗粒的凹槽,然后采用选择性化学镀制备出了具有强附着力的嵌入式二维和三维金属微结构。Berg等[21]将飞秒激光烧蚀微槽方法与激光诱导前向转移的金属印刷技术相结合,在玻璃基底上制备出了强附着力的嵌入式金属铜微结构。此外,通过激光直写烧蚀光敏玻璃形成改性粗糙表面,然后再进行后续化学镀铜也可以形成具有强附着力的金属铜微结构[22]。但是上述方法制备出的金属线的最小线宽一般在几微米,目前还没有看到嵌入式亚微米金属线制备的相关报道。
针对上述问题,本文基于飞秒激光烧蚀的阈值效应,提出了一种将连续流化学金属镀以及后续的热处理和机械抛光结合起来在玻璃表面制备嵌入式亚微米金属线的方法。首先,将飞秒激光的单脉冲能量控制在烧蚀阈值附近,在玻璃表面制备出烧蚀线宽小于激光波长的表面凹槽;然后通过连续流化学镀在激光处理后的玻璃表面上沉积出全覆盖的金属薄膜。与传统的搅拌式化学镀工艺相比,连续流化学镀可提高溶液在待沉积基底表面的溶质交换速率,进而提高液相中沉积金属的表面质量和均匀度[23-24]。连续流化学镀之后的热处理可进一步增强金属沉积层的致密度及其与玻璃的结合力。最后的机械抛光处理可有效去除激光烧蚀凹槽区域以外的金属,只保留凹槽内的金属结构,从而实现亚微米级的选择性表面金属化。本文利用此方法制备出了线宽可控(0.6~2.4 μm)、电导率高的金属银导线(电阻率约为1.83 μΩ·cm,约为体积银电阻率的1.2倍)。
2 实验过程
实验中使用的玻璃样品为六面抛光的石英玻璃(Corning 7980),其尺寸为10 mm×5 mm×2 mm。所用激光器(Pharos,20 W)的中心波长为1030 nm,脉冲宽度为290 fs,重复频率为50 kHz。通过旋转光路中的衰减片来动态控制激光的脉冲能量(0.1~1 μJ连续可调),并在激光进入物镜前利用功率计进行检测。激光直写加工速度为0.2 mm/s。所用聚焦物镜(MPLFLN50X)的数值孔径为0.80,此物镜对所使用激光的透过率约为25%。
如
制备的金属线的形貌表征通过光学显微镜(BX53)和扫描电子显微镜(Gemini450)来实现;制备的金属线的电学性能通过四探针测试装置(RCS-80-1)来测试。
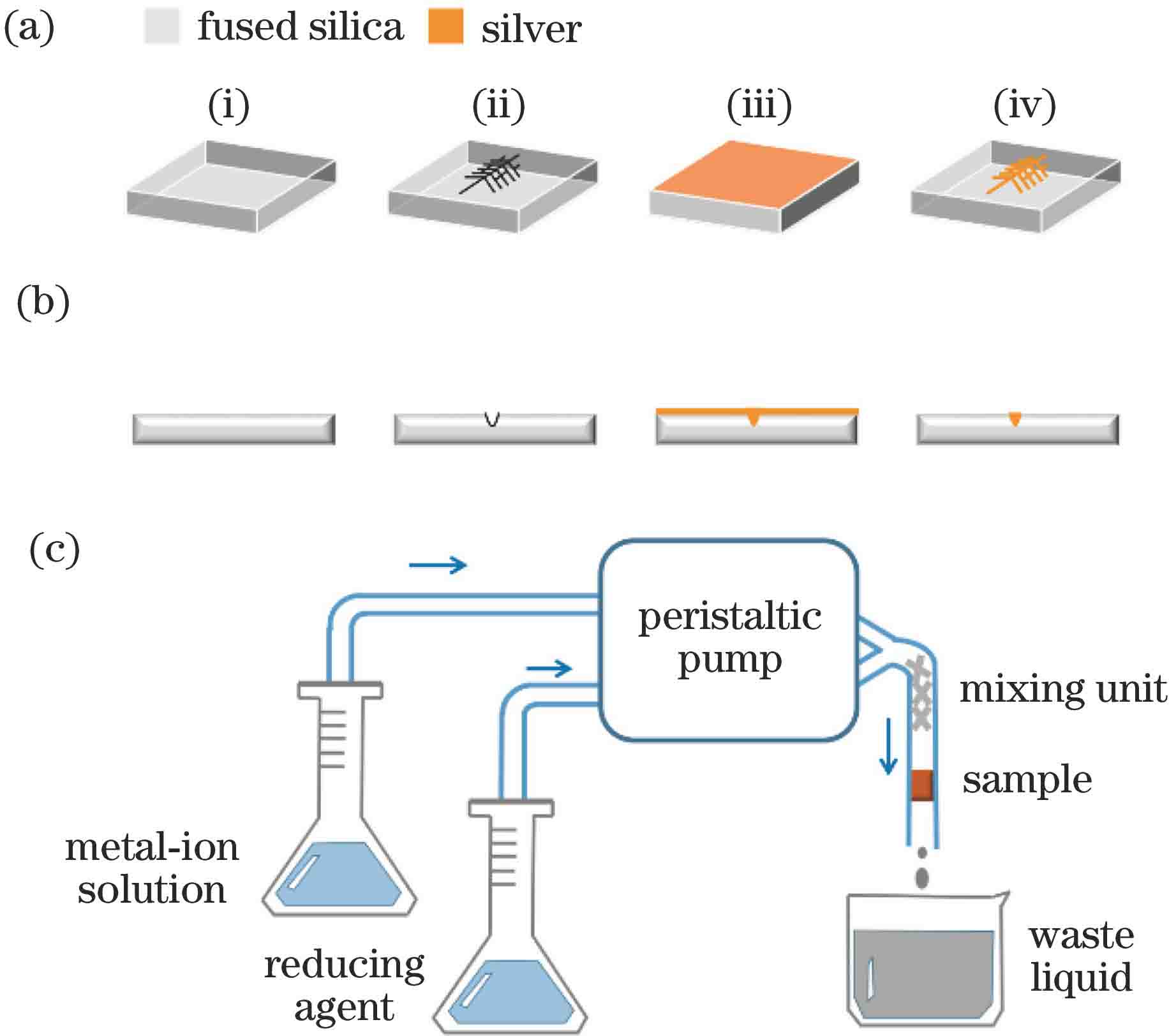
图 1. 在石英玻璃表面制备嵌入式亚微米金属线。(a)制备流程的三维示意图;(b)制备流程的截面示意图; (c)连续流化学镀实验装置示意图
Fig. 1. Fabrication of embedded submicron metal lines on fused silica surfaces. (a) Three-dimensional schematic of fabrication procedure; (b) cross-sectional schematic of fabrication procedure; (c) a schematic of experimental setup for continuous-flow electroless plating
3 结果与讨论
首先研究其他条件相同的情形下激光单脉冲能量对直写烧蚀的凹槽线宽以及后续机械抛光后金属线宽的影响。
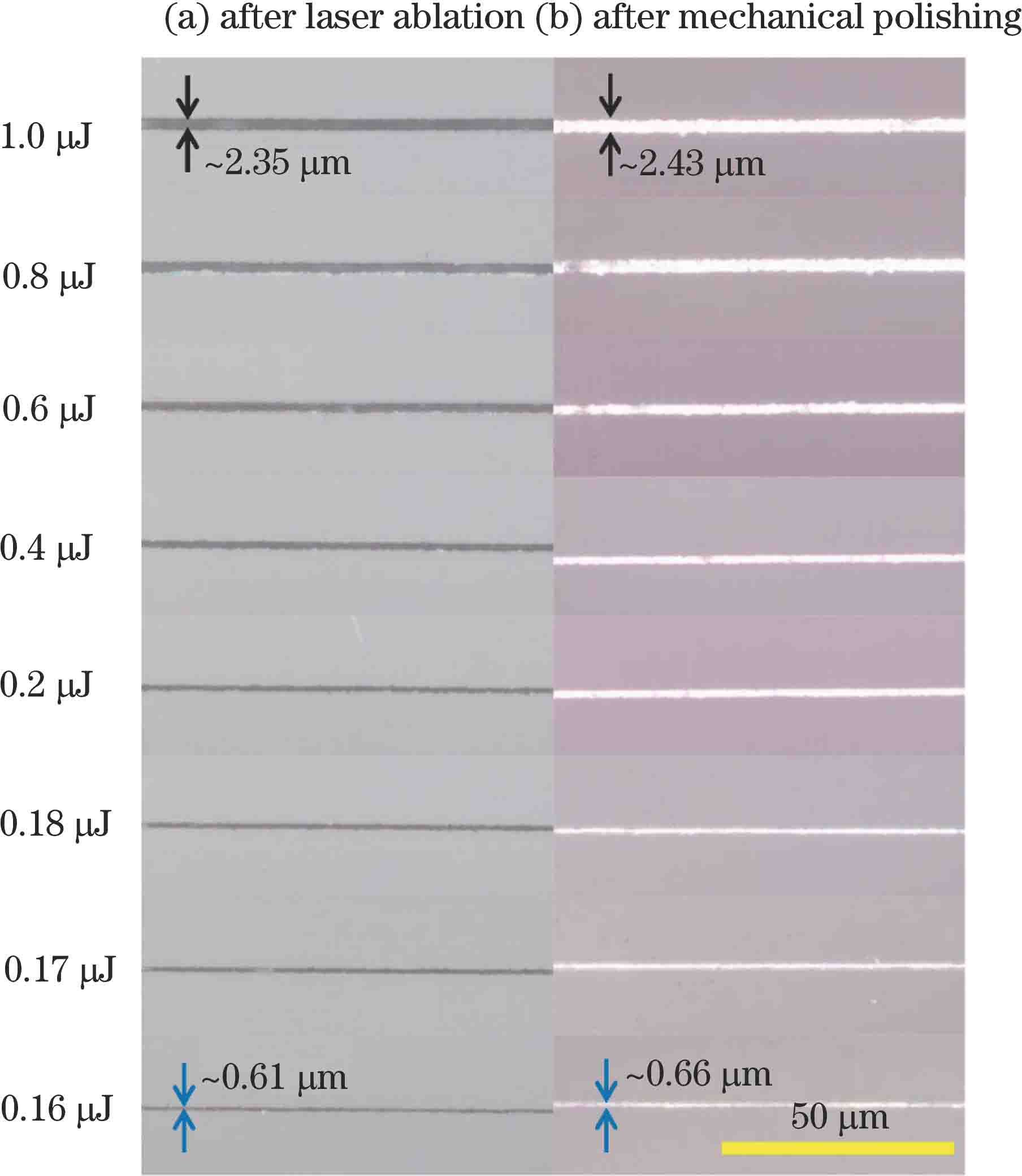
图 2. 不同脉冲能量激光烧蚀凹槽及机械抛光后金属线的光学显微图
Fig. 2. Optical micrographs of grooves ablated by laser with different pulse energies and metal lines after mechanical polishing
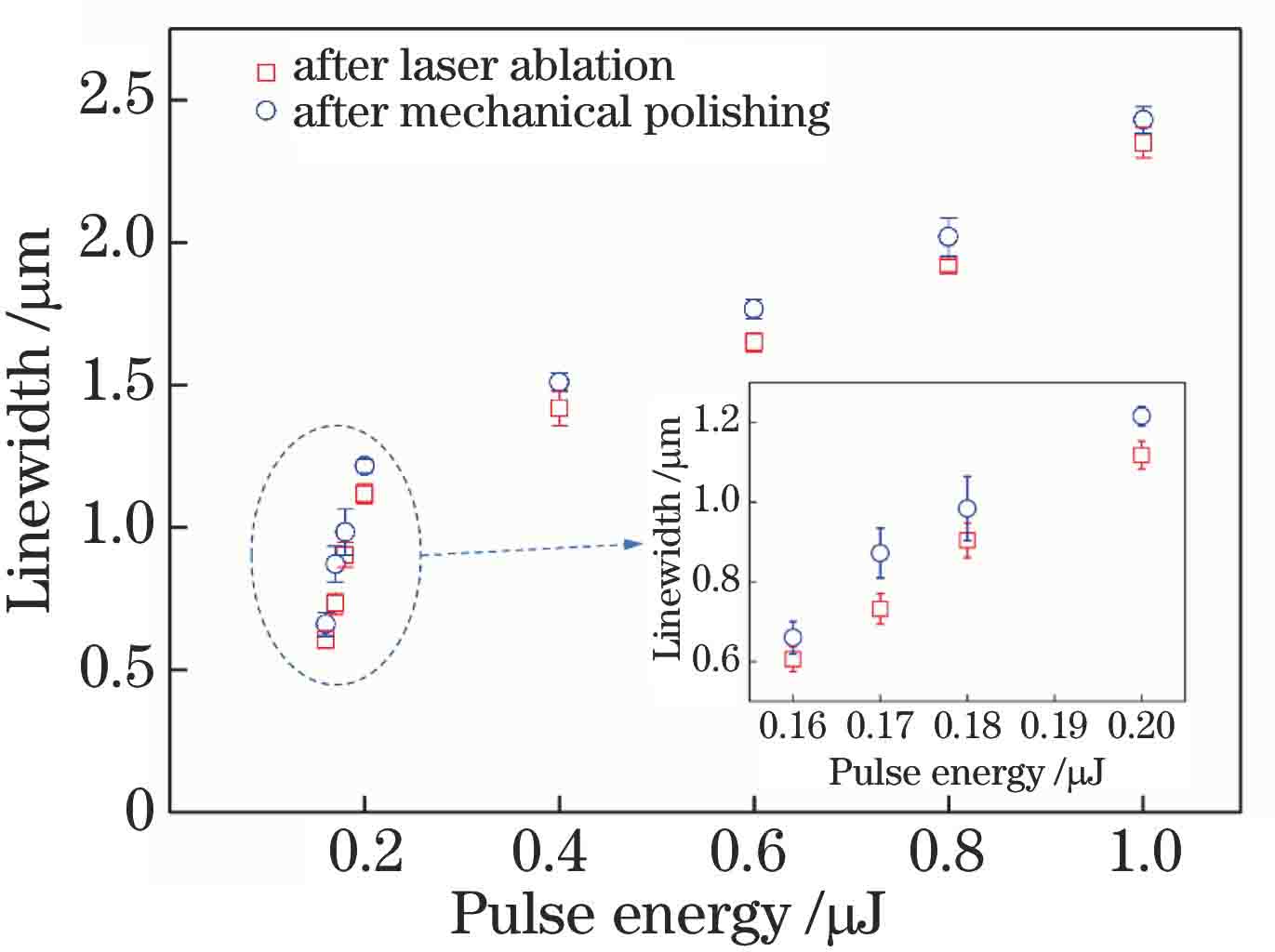
图 3. 脉冲能量与烧蚀凹槽线宽、机械抛光后金属线宽的关系
Fig. 3. Pulse energies versus linewidths of laser-ablated grooves and metal lines after mechanical polishing
为了稳定地实现嵌入式亚微米金属线的可控制备,除控制激光烧蚀的脉冲能量外,还需要考虑玻璃表面选择性金属化的实现方式。本文利用了连续流化学镀并结合热处理及后续机械抛光的方式来实现亚微米级别的选择性金属化。需要说明的是,在机械抛光之前的热处理对于后续高电导率和强附着力的亚微米金属结构的制备具有重要作用。四探针法测试结果表明,在同样条件下进行连续流化学镀银热处理(600 ℃,2 h)前后的金属结构的电阻率分别为8.58 μΩ·cm和1.83 μΩ·cm,后者约为体积银电阻率(1.59 μΩ·cm)的1.2倍。热处理的引入可将制备出的金属结构的电阻率降低为未热处理的1/4.7,其原因主要在于热处理促进了金属颗粒和颗粒间的熔融结合和互连,提高了沉积金属银膜的致密度,这可从
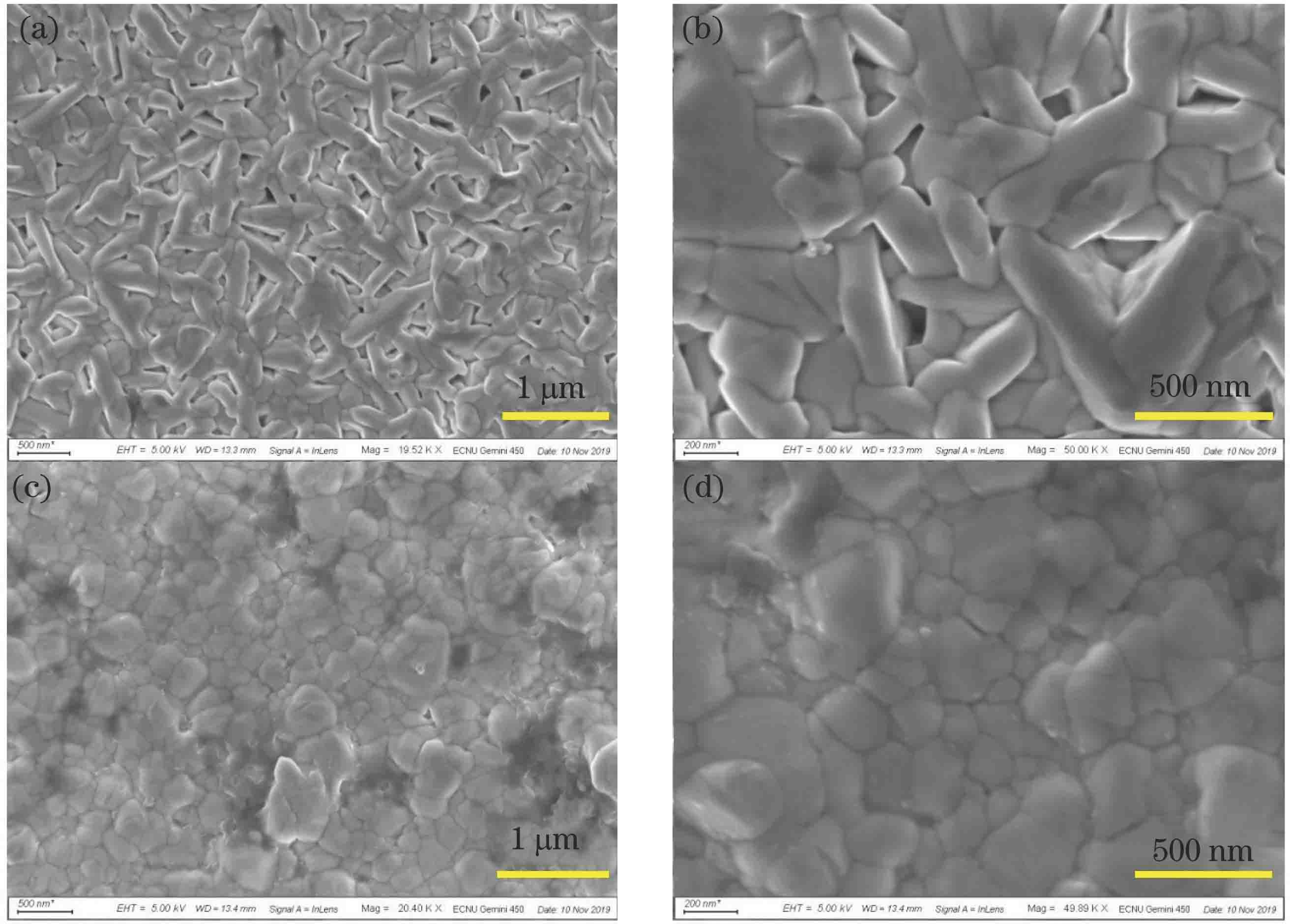
图 4. 连续流化学镀沉积金属银微结构在热处理前后的SEM图。(a)(b)热处理前;(c)(d)热处理后
Fig. 4. SEM images of silver microstructures deposited by continuous-flow electroless plating before and after thermal treatment. (a)(b) Before thermal treatment; (c)(d) after thermal treatment
为演示此法制备嵌入式亚微米金属结构的任意构型能力,本文在石英玻璃表面制备了一系列不同形状的金属线图案。如
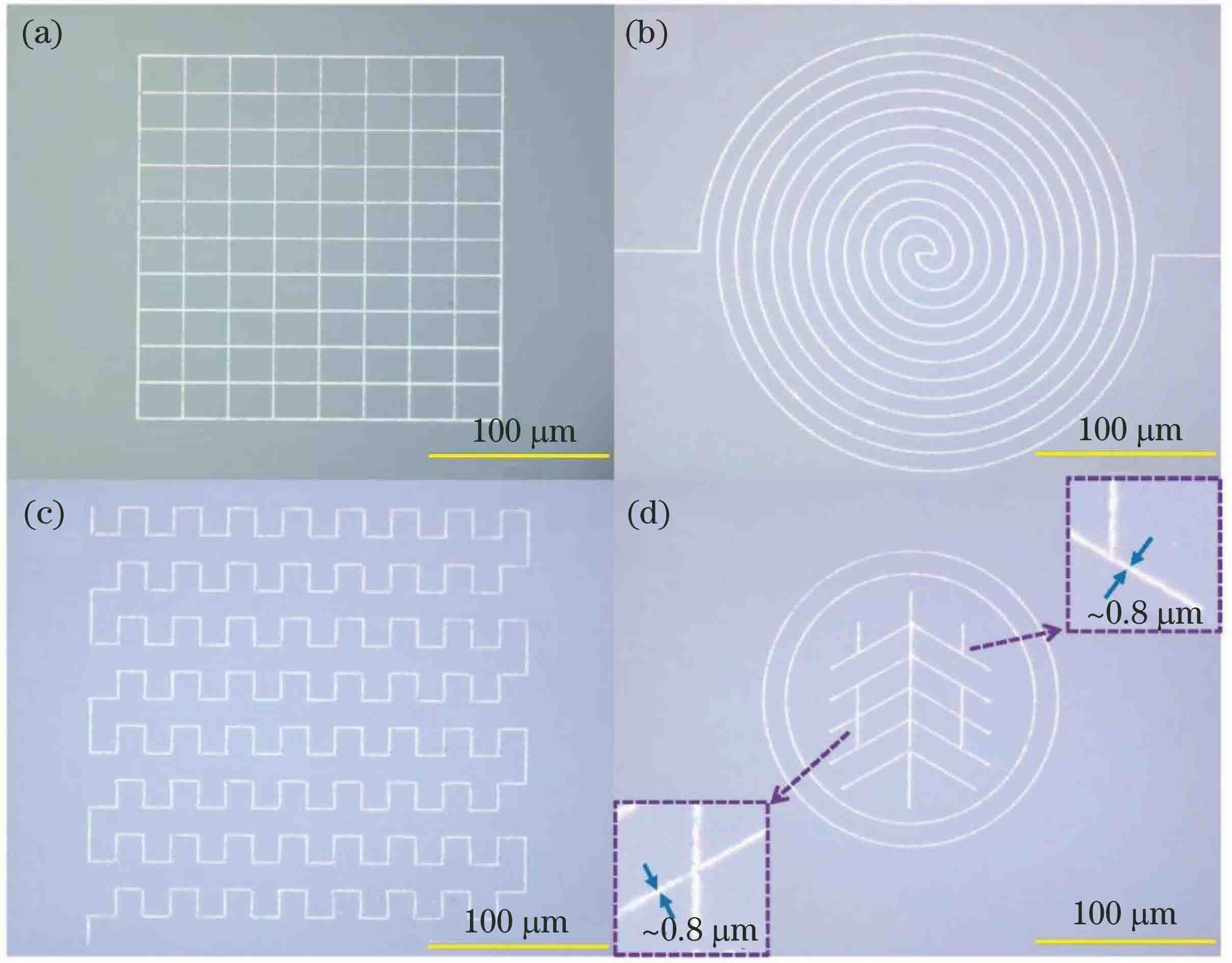
图 5. 不同形状的嵌入式亚微米金属线(线宽约为0.8 μm)。(a)网格状;(b)螺旋状;(c)方波状;(d)汉字图案
Fig. 5. Embedded submicron metal lines with various shapes (linewidths of metal lines are about 0.8 μm). (a) Grid; (b) spiral; (c) square-wave; (d) Chinese character patterns
4 结论
本文提出了一种将飞秒激光烧蚀与连续流化学镀及后续热处理和机械抛光结合起来实现玻璃表面嵌入式亚微米金属线的制备方法。利用此方法可制备出空间构型和线宽可控、电导率高、附着力强的嵌入式亚微米金属线结构。值得说明的是,通过进一步优化连续流化学镀反应体系以及将其与激光烧蚀、机械抛光结合起来,有望在同一块基底上同时集成多种类型的金属。嵌入式亚微米金属结构的可控制备,对于发展新型微纳结构表面电学互连与控制,以及提高微纳连接的稳定性具有重要意义。
[1] El-Sayed M A. Some interesting properties of metals confined in time and nanometer space of different shapes[J]. Accounts of Chemical Research, 2001, 34(4): 257-264.
[2] Barnes W L, Dereux A, Ebbesen T W. Surface plasmon subwavelength optics[J]. Nature, 2003, 424(6950): 824-830.
[3] Henzie J, Lee M H, Odom T W. Multiscale patterning of plasmonic metamaterials[J]. Nature Nanotechnology, 2007, 2(9): 549-554.
[4] Hossain M M, Gu M. Fabrication methods of 3D periodic metallic nano/microstructures for photonics applications[J]. Laser & Photonics Reviews, 2014, 8(2): 233-249.
[6] Geissler M, Xia Y. Patterning:principles and some new developments[J]. Advanced Materials, 2004, 16(15): 1249-1269.
[7] Stellacci F, Bauer C A, Meyer-Friedrichsen T, et al. Laser and electron-beam induced growth of nanoparticles for 2D and 3D metal patterning[J]. Advanced Materials, 2002, 14(3): 194-198.
[8] Shukla S, Furlani E P, Vidal X, et al. Two-photon lithography of sub-wavelength metallic structures in a polymer matrix[J]. Advanced Materials, 2010, 22(33): 3695-3699.
[9] Hirt L, Reiser A, Spolenak R, et al. Additive manufacturing of metal structures at the micrometer scale[J]. Advanced Materials, 2017, 29(17): 1604211.
[10] Moran C E, Radloff C, Halas N J. Benchtop fabrication of submicrometer metal line and island arrays using passivative microcontact printing and electroless plating[J]. Advanced Materials, 2003, 15(10): 804-807.
[11] Tanaka T, Ishikawa A, Kawata S. Two-photon-induced reduction of metal ions for fabricating three-dimensional electrically conductive metallic microstructure[J]. Applied Physics Letters, 2006, 88(8): 081107.
[12] Cao Y Y, Takeyasu N, Tanaka T, et al. 3D metallic nanostructure fabrication by surfactant-assisted multiphoton-induced reduction[J]. Small, 2009, 5(10): 1144-1148.
[13] Maruo S, Saeki T. Femtosecond laser direct writing of metallic microstructures by photoreduction of silver nitrate in a polymer matrix[J]. Optics Express, 2008, 16(2): 1174-1179.
[14] Xu B B, Xia H, Niu L G, et al. Flexible nanowiring of metal on nonplanar substrates by femtosecond-laser-induced electroless plating[J]. Small, 2010, 6(16): 1762-1766.
[16] 陈忠贇, 方淦, 曹良成, 等. 飞秒激光光镊直写银微纳结构[J]. 中国激光, 2018, 45(4): 0402006.
[17] 廖嘉宁, 王欣达, 周兴汶, 等. 飞秒激光直写铜微电极研究[J]. 中国激光, 2019, 46(10): 1002013.
[18] Xu J, Liao Y, Zeng H D, et al. Selective metallization on insulator surfaces with femtosecond laser pulses[J]. Optics Express, 2007, 15(20): 12743-12748.
[19] Liao Y, Xu J, Sun H Y, et al. Fabrication of microelectrodes deeply embedded in LiNbO3 using a femtosecond laser[J]. Applied Surface Science, 2008, 254(21): 7018-7021.
[20] Song J X, Liao Y, Liu C, et al. Fabrication of gold microelectrodes on a glass substrate by femtosecond-laser-assisted electroless plating[J]. Journal of Laser Micro/Nanoengineering, 2012, 7(3): 334-338.
[21] Berg Y, Winter S, Kotler Z. Embedded metal microstructures in glass substrates by a combined laser trenching and printing process[J]. Journal of Laser Micro/Nanoengineering, 2018, 13(2): 131-134.
[22] Hanada Y, Sugioka K, Midorikawa K. Selective metallization of photostructurable glass by femtosecond laser direct writing for biochip application[J]. Applied Physics A, 2008, 90(4): 603-607.
[23] Goluch E D, Shaikh K A, Ryu K, et al. Microfluidic method for in-situ deposition and precision patterning of thin-film metals on curved surfaces[J]. Applied Physics Letters, 2004, 85(16): 3629-3631.
[24] Xu J, Li X L, Zhong Y, et al. Glass-channel molding assisted 3D printing of metallic microstructures enabled by femtosecond laser internal processing and microfluidic electroless plating[J]. Advanced Materials Technologies, 2018, 3(12): 1800372.
[25] Lenzner M, Krüger J, Sartania S, et al. Femtosecond optical breakdown in dielectrics[J]. Physical Review Letters, 1998, 80(18): 4076-4079.
[26] Joglekar A P, Liu H, Meyhofer E, et al. Optics at critical intensity: applications to nanomorphing[J]. Proceedings of the National Academy of Sciences of the United States of America, 2004, 101(16): 5856-5861.
[27] Sugioka K, Cheng Y. Ultrafast lasers: reliable tools for advanced materials processing[J]. Light: Science & Applications, 2014, 3(4): e149.
余浩锋, 徐剑, 张傲东, 程亚. 玻璃表面嵌入式亚微米金属线的制备[J]. 中国激光, 2020, 47(5): 0502009. Haofeng Yu, Jian Xu, Aodong Zhang, Ya Cheng. Fabrication of Embedded Submicron Metal Lines on Glass Surfaces[J]. Chinese Journal of Lasers, 2020, 47(5): 0502009.