大层厚316L选区激光熔化工艺优化及性能研究
下载: 1414次
1 引言
选区激光熔化(SLM)是利用高能量激光束将金属粉末逐层熔化直接成型为金属零件的直接金属成型技术。SLM可以成型结构复杂、性能良好的零件,被广泛应用于航天、医学、汽车、模具等领域[1-3]。近年来,SLM已经可以成型高致密零件[4-9],但成型效率较低。
SLM成型效率主要受激光功率、层厚、扫描速度等影响。Niendorf等[10]采用400 W和1000 W激光功率成型了50 μm和150 μm层厚的316L粉末,但效果并不理想。Sun等[11]使用380 W激光功率成型了50 μm层厚的316L粉末,得到的样件致密度为99.9%且成型效率较高。Ma等[12]研究了60~150 μm层厚的1Cr18Ni9Ti合金成型样件的性能;Shi等[13]制备了200 μm层厚的Ti6Al4V样件,均获得了几乎全致密样件。然而,大层厚316L粉末SLM成型的研究鲜有研究,一是因为铺粉层厚越大,越容易产生未熔、翘曲、球化等缺陷;另一个原因则是受SLM设备的限制。
本文采用SLM技术对200 μm层厚316L粉末进行了单熔道及块体实验,通过对样件致密度、缺陷机理、微观组织,拉伸性能等的分析,优化了工艺参数,并获得了高致密、拉伸性能良好的样件。
2 实验设备及方法
2.1 实验设备与材料
采用英国Renishaw公司生产的AM400 SLM设备进行实验,该设备可以通过改变曝光时间及点距的方式对扫描速度进行更改。当成型室内氧气的含量小于0.3%时开始打印,在实验过程中,采用氩气作为保护气体。
由于气雾化制备的316L粉末的氧含量小于水雾化的[14-15],因此,选用Renishaw公司的气雾化316L粉末作为实验材料,其化学成分见
2.2 实验方法
SLM单熔道实验参数见
表 1. 316L粉末的化学成分(质量分数,%)
Table 1. Chemical compositions of 316L powder (mass fraction, %)
|
表 2. SLM单熔道实验参数
Table 2. Parameters for single-scan track SLM experiment
|
拉伸样件几何尺寸如
3 结果与分析
3.1 单熔道实验
SLM是一个由多条扫描线互相搭接形成扫描平面,扫描平面再经过层层堆积获得成型实体的过程[17-18]。单熔道是成型的基础,在块体成型前,先利用单熔道实验对块体实验参数进行筛选。
良好的单熔道各熔池搭接连续,成型单熔道边界清晰光滑,熔池凝固边界明显且呈锐角。当激光功率为400 W,层厚为200 μm时,不同点距及曝光时间下SLM单熔道表面形貌如
1) 当曝光时间为80~100 μs时,单熔道较细且顶部呈山峰状,表面形貌极不稳定。由于曝光时间太短,激光能量输入不足,粉末不能完全熔化,因此无法形成稳固的单熔道。
2) 当曝光时间为120 μs,点距为6~24 μm及曝光时间为140 μs,点距为14~28 μm时,单熔道连续且表面光滑。当点距进一步增大,单熔道表面粗糙不连续。由于点距大,熔池中心距离较远,熔池内液相金属凝固后与前一熔池搭接较少,因此熔道起伏较大甚至出现断点。
3) 当曝光时间增大到160 μs,点距为8~32 μm时,单熔道的状态相对稳定。然而,曝光时间的增加会导致熔池表面张力差增大,熔池扰动;少量的液相金属脱离熔池,在空中凝固后落到单熔道表面而形成飞溅。
4) 当曝光时间进一步增大到180 μs,单熔道边界模糊,熔宽增大,飞溅尺寸及数量都有所增大,局部出现过烧现象。这是因为激光能量输入过大,熔池分裂,金属发生气化形成较大的飞溅。且当前熔池加热时可能熔化前一熔池内凝固的金属,液相金属流动,最终单熔道特征模糊。
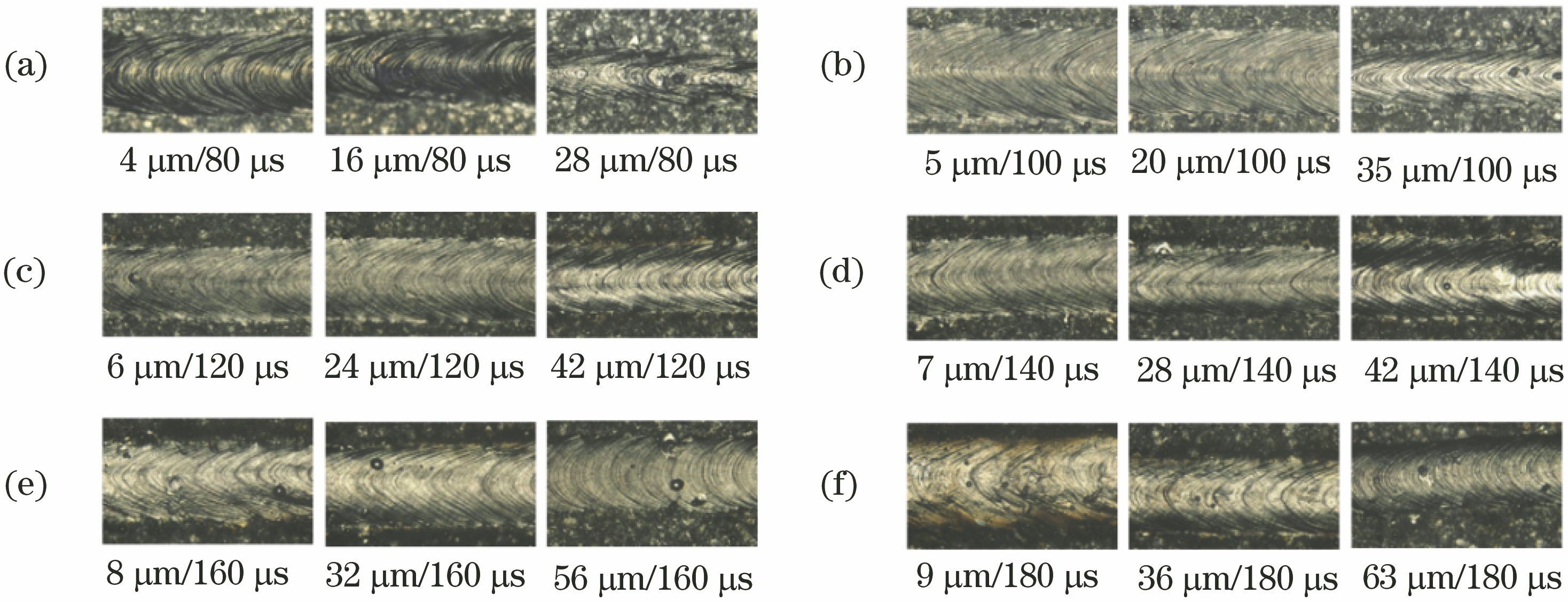
图 3. 不同点距及曝光时间下SLM单熔道表面形貌
Fig. 3. Surface morphologies of single-scan tracks under different point distances and exposure time
3.2 块体致密度分析
通过图像分析软件测得单熔道熔宽为450~550 μm,并根据熔宽及搭接率对线间距进行设置。SLM块体实验参数见
样件致密度分布曲线如
表 3. SLM块体实验参数
Table 3. Parameters for block SLM experiment
|
曝光时间及点距对样件成型的影响如
由
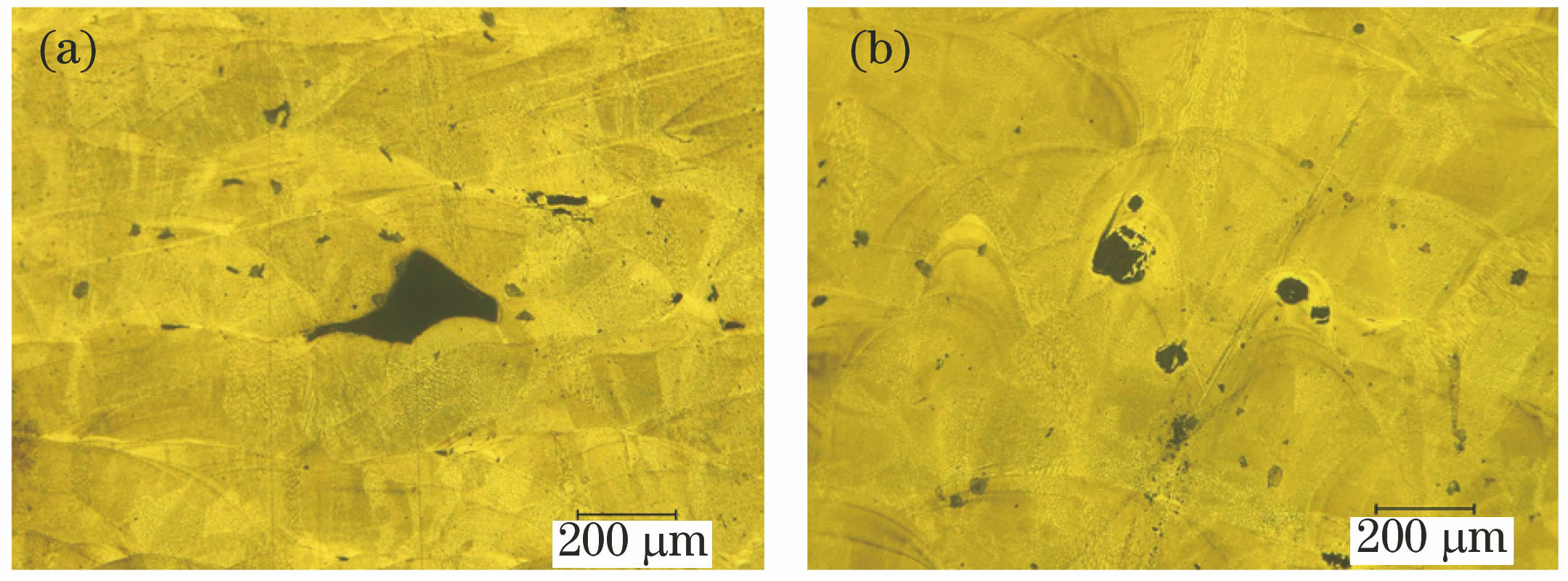
图 5. 曝光时间及点距对样件成型的影响。(a)曝光时间过长;(b)点距过大
Fig. 5. Effects of exposure time and point distance on formation of samples. (a) Long exposure time; (b) large point distance
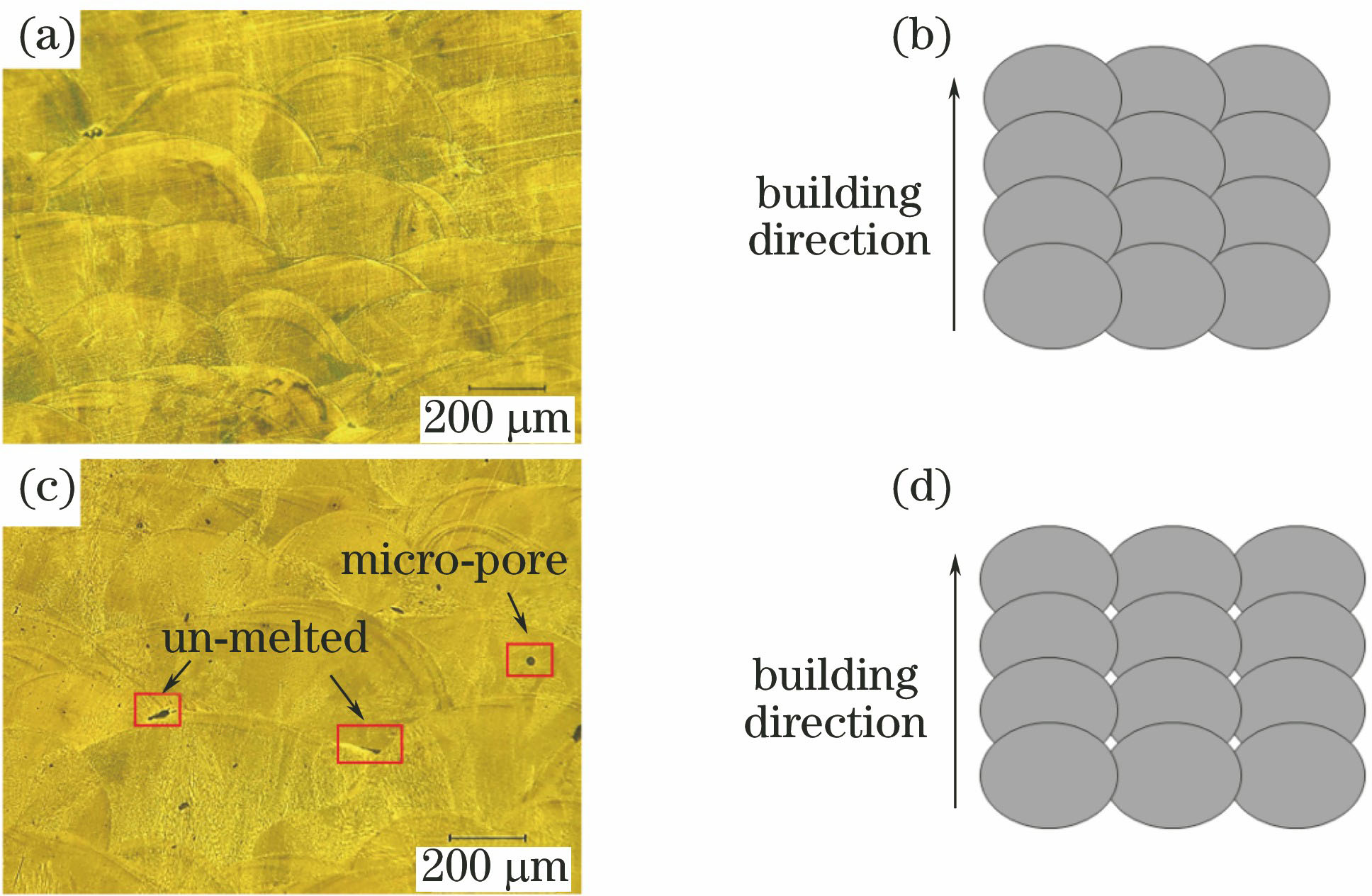
图 6. 不同搭接率下样件的微观形貌。(a)(b)搭接率为40%时表面形貌及释图;(c)(d)搭接率为30%时表面形貌及释图
Fig. 6. Microstructures of samples under different overlap rates. (a)(b) Surface morphology and Interpretation of 40% overlap rate; (c)(d) surface morphology and Interpretation of 30% overlap rate
综上所述,合理的参数设置搭配合理的搭接率可以有效提高样件的致密度,并完全避免未熔合缺陷的形成。
3.3 球化现象
球化现象会使粉末填充、熔化凝固后形成孔隙而减小样件的致密度,严重时会使样件无法成型,因此需要加以避免。减小成型过程中氧含量可以初步抑制球化现象[19]。实验开始前将成型室内的氧含量控制在0.3%以下,并且在底部支撑打印完成后氧气完全被消耗。
不同曝光时间下样件表面球化现象如
从
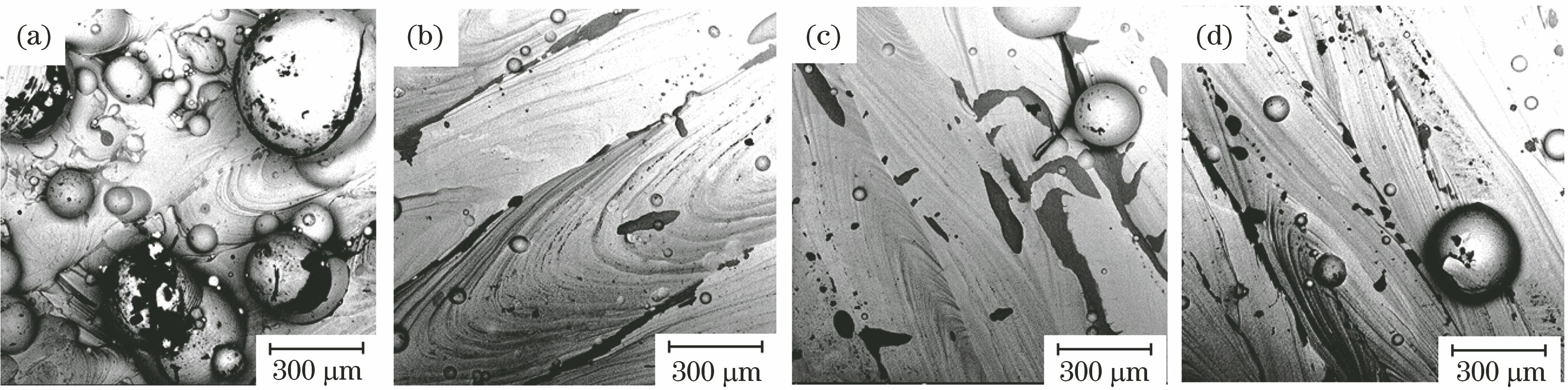
图 7. 不同曝光时间下样件表面球化现象。(a) 100 μs;(b) 120 μs;(c) 140 μs;(d) 160 μs
Fig. 7. Balling phenomena on sample surface under different exposure time. (a) 100 μs; (b) 120 μs; (c) 140 μs; (d) 160 μs
因此,保证足够的激光能量输入可以避免引起大型球化;飞溅形成的球化则可以通过减小曝光时间的方式控制球化尺寸。当层厚为200 μm,曝光时间为120 μs时,飞溅产生的球化尺寸最小,但仍无法完全避免球化现象的发生。
3.4 微观组织及力学性能
140 μs曝光时间下样件的微观形貌如
SLM成型过程中,单个熔池内金属在极短的时间内熔化、凝固,具有极大的过冷度。较大的过冷度会抑制晶粒的生长,形成细小的晶粒。另外,激光光斑内能量呈高斯分布,光斑中心温度最高,使得熔池内存在较大温度梯度。柱状晶的生长与热流方向相反,因此,同一熔池内晶粒的生长方向绝大部分垂直于熔池边界,仅小部分晶粒与熔池边界成一定角度择优生长。
晶粒的生长特性使得SLM大层厚样件晶粒组成及分布规律与小层厚的相同,但是,大层厚所含柱状晶比例明显大于小层厚的。这是由于层厚越大,过冷度越小,晶粒生长形成柱状晶。
选取致密度较大的样件,在相同条件下进行拉伸强度(UTS)、屈服强度(YS)以及延伸率(EL)的测试。由于实验中所选扫描策略为每成型一层,成型方向旋转67°,因此,实验中拉伸性能未出现各向异性。不同曝光时间下样件的拉伸性能如
SLM不同层厚样件的拉伸性能及成型效率见
式中:
由
表 4. SLM不同层厚样件的拉伸性能及成型效率
Table 4. Tensile properties and building rates of samples with different layer-thicknesses by SLM
|
4 结论
采用SLM技术对200 μm层厚气雾化316L粉末进行单熔道以及块体实验,分析了成型件的致密度、缺陷成型机理、微观组织以及拉伸性能,得到以下结论。
1) 单熔道实验可以对块体成型质量进行预估,进而对块体实验工艺窗口进行筛选,结果表明,当曝光时间为120~160 μs时,成型单熔道光滑且连续。
2) 采用阿基米德排水法测量样件致密度。结果表明,当曝光时间为120 μs,点距为12 μm,搭接率为50%;曝光时间为120 μs,点距为24 μm,搭接率为40%;曝光时间为140 μs,点距为14~28 μm;曝光时间为160 μs,点距为16~32 μm,搭接率为40%时,样件致密度较高,可达99.99%。
3) 成型块体缺陷主要包括未熔合缺陷以及球化现象。未熔合缺陷可通过调节曝光时间、点距、搭接率完全避免。输入足够的能量可以避免大型球化产生;适当地降低曝光时间可以有效抑制飞溅产生的球化尺寸,当曝光时间为120 μs时,球化产生的尺寸最小。
4) 微观组织主要为等轴晶及柱状晶,绝大部分垂直于熔池边界生长。晶粒性能使得拉伸强度与延伸率成反比,当曝光时间为140 μs、点距为28 μm、搭接率为40%时,成型效率达12.4 mm3/s,且拉伸性能良好,其屈服强度、拉伸强度和延伸率分别可达530 MPa、635 MPa和31%。
[2] 杨永强, 陈杰, 宋长辉, 等. 金属零件激光选区熔化技术的现状及进展[J]. 激光与光电子学进展, 2018, 55(1): 011401.
[3] 杨永强, 王迪, 吴伟辉. 金属零件选区激光熔化直接成型技术研究进展[J]. 中国激光, 2011, 38(6): 0601007.
[4] 王迪, 杨永强, 吴伟辉. 光纤激光选区熔化316L不锈钢工艺优化[J]. 中国激光, 2009, 36(12): 3233-3239.
[14] Herzog D, Seyda V, Wycisk E, et al. Additive manufacturing of metals[J]. Acta Materialia, 2016, 117: 371-392.
[18] 赵曙明, 沈显峰, 杨家林, 等. 水雾化316L不锈钢选区激光熔化致密度与组织性能研究[J]. 应用激光, 2017, 37(3): 319-326.
[19] 吴伟辉, 杨永强, 王迪. 选区激光熔化成型过程的球化现象[J]. 华南理工大学学报(自然科学版), 2010, 38(5): 110-115.
杨锦, 刘玉德, 石文天, 张飞飞, 祁斌, 韩冬. 大层厚316L选区激光熔化工艺优化及性能研究[J]. 激光与光电子学进展, 2019, 56(1): 011401. Jin Yang, Yude Liu, Wentian Shi, Feifei Zhang, Bin Qi, Dong Han. Process Optimization and Performance Investigation in Selective Laser Melting of Large Layer-Thickness 316L Powder[J]. Laser & Optoelectronics Progress, 2019, 56(1): 011401.