Etching-assisted femtosecond laser modification of hard materials
Download: 1452次
1 Introduction
With advantages of excellent optical transmittance, high electrical insulation, high hardness, thermal and chemical stability, hard materials (high hardness materials, e.g., silica, sapphire, diamond, silicon, etc.) exhibit various applications in opto-electronic devices, consumer electronics, mechanical micromachining and optical devices, etc., especially in harsh conditions, such as in space and deep sea. Meantime, the properties of high stability and high hardness also make these hard materials difficult to realize high precision micro/nanofabrication. Traditional technologies, including mechanical machining and photolithography, have been widely used to process hard materials1, 2. The low precision and the wear of abrasive tools of mechanical machining in processing of hard materials limit its further application in precision manufacturing, especially for optical devices. Although, photolithography combined with reactive ion etching exhibits high precision with nanometer resolution when processing hard materials, it suffers from the difficulty to fabricate complex three-dimensional (3D) micro/nanostructures and can only machine planar substrates. Therefore, it is still a great challenge for precise 3D processing of hard materials to satisfy the demands of practical applications.
In recent decades, femtosecond laser direct writing (FsLDW) has demonstrated to be a high precision processing method that can be used for 3D micro/nanofabrication of almost any materials. With these advantages, the technology has exhibited great potential applications in micro-optics, microelectronics, micro-mechanics, microfluidics, micro-optoelectronics, sensing, bionics and biomanufacturing3-14. Femtosecond laser direct writing technology can be divided into two categories: additive manufacturing and subtractive manufacturing. The former method has been widely used for fabrication of complex 3D polymer structures with high resolution15. Although metal and ceramic structures have been realized by the laser additive manufacturing method16, 17, the mechanical and opto-electric properties of the additive manufactured materials cannot be compared with the original bulk materials. For processing of hard materials, the latter method (femtosecond laser ablation) is adopted via laser-induced materials removal. The basic principle of femtosecond laser ablation is to use the tightly focused femtosecond laser as the processing " knife" , which has the characteristics of non-contact, no wear and deformation. The scanning of laser focus is controlled by pre-set computer-aided design (CAD) graphic data to directly realize digital processing. Normally, high laser power higher than laser-induced damage threshold is used to realize materials removal, which results in the low precision and high surface roughness. On the other hand, high power laser ablation also limits the improvement of processing efficiency. Therefore, the low efficiency, low precision and high surface roughness are the main stumbling blocks for femtosecond laser processing of hard materials. Although many attempts have been taken for processing hard materials with other kinds of lasers via some special technologies, such as pocket scanning18, laser-induced plasma-assisted ablation19, nanosecond laser-induced backside wet etching20 and particle-assisted ablation21, the fabrication precision is too low for optical applications. What's more, the low efficiency is the mutual problem for point-by-point laser scanning ablation methods.
Etching-assisted femtosecond laser machining has demonstrated to be a potential technology to solve the above problems when processing of hard materials. The fundamental of etching-assisted femtosecond laser machining is introducing materials modification by laser to change the etching rate. By scanning of laser focus to form 3D modified regions to act as the removing area or the etching mask in the subsequent etching process according to the etch rate. Then, 3D micro/nanostructures can be formed on the surface or inside hard materials. Micro/nanostructures with high precision and smoothness can be realized by near threshold laser modification, due to the smooth boundary of laser modified region and the polishing effect of etching. Besides, low power laser modification helps increase processing efficiency. In this review, the etching related femtosecond laser modification of hard materials will be introduced in detail. The advantages and difference of wet-etching and dry-etching assisted femtosecond laser modification technologies will be firstly summarized and discussed. And the recent developments and applications of etching-assisted femtosecond laser modification of hard materials will be reviewed. Finally, the challenges and prospects of the etching-assisted femtosecond laser modification will be discussed.
2 Femtosecond laser modification
The key for the etching-assisted femtosecond laser modification is the capability to selectively modify the target materials by laser irradiation, which can induce difference of etching rate between laser modified region and original region. According to the values of photon energy and band gap, single photon absorption or nonlinear absorption would be generated by the interaction between laser pulses and target hard materials, such as semiconductors and dielectric glasses22, 23. For the case of a dielectric glass, phenomena including multiphoton ionization, avalanche ionization, tunneling ionization and subsequent induced micro-explosion would be generated when the laser energy density is sufficiently high22, 24-26. Except surface processing, laser beam can also be focused into the transparent materials with high resolution due to the strong nonlinear absorption in the confined region27. Therefore, three-dimensional modified regions could be formed inside transparent materials by scanning of the femtosecond laser focus.
During laser processing of hard materials, various laser induced materials properties would be changed. The properties of laser modified regions are heavily depended on the laser fluence28. When laser fluence is higher than the damage threshold but lower than or near self-focusing threshold, only non-damage energy depositions with smooth bond energy change are formed inside materials. With laser power further increasing, the materials would be damaged to form phase change. In addition, the components also could be changed by photochemical reaction in suitable gas environment or laser doping. Here, we introduce the non-damage energy deposition, phase change and component change, which could influence the subsequent etching rate.
2.3 Non-damage energy deposition
With low energy femtosecond laser modification, chemical structure of the target materials would be changed without significant damage. Many research groups have tried to explain the principle of chemical change after laser modification in silica28, 29. Chan et al.30 experimentally observed the increasing of the number of 3- and 4-membered Si-O rings in the silica network induced by femtosecond laser, which results in the decreasing of overall bond angle and increasing of density. Ponader et al.31 observed the continuous variation of Raman spectrum peaks at 1060 and 1200 cm-1 of femtosecond laser modified fused silica compared with the original region. They discovered that the increasing of density contributed to the increasing of the Si-O bond length and meantime the decreasing of the mean Si-O-Si bond angle in femtosecond laser modified fused silica. These explanations are mainly based on the rearrangement of the silica network due to the fast temperature change by ultrafast laser modification. Another explanation is the formation of defects, including oxygen-deficient and oxygen-excess, which are caused by the relaxation of self-trapped excitons during femtosecond laser modification32, 33. For example, Zoubir et al.32 studied the photoinduced defects in silica by absorption spectroscopy, indicating that oxygen-deficient centers and oxygen-excess centers are formed according to the presence of peaks at 248 nm and 650 nm. Although the exactly fundamental chemical structure change induced by femtosecond laser is not fully understood, the phenomenon of laser induced non damage energy deposition with bond energy excitation is undisputed.
It has been demonstrated that most of these chemical changes would lead to the refractive index change in silica and has been expanded to various transparent materials34-38. Based on the laser induced refractive change, various optical devices are fabricated by femtosecond laser modification, including optical storage devices, waveguides, photonic crystals and micro-optical elements39-44. For example, Wei et al.44 realized the fabrication of three-dimensional photonic crystals in lithium niobate (LiNbO3) crystal by femtosecond laser modification, as the schematic diagram shown in
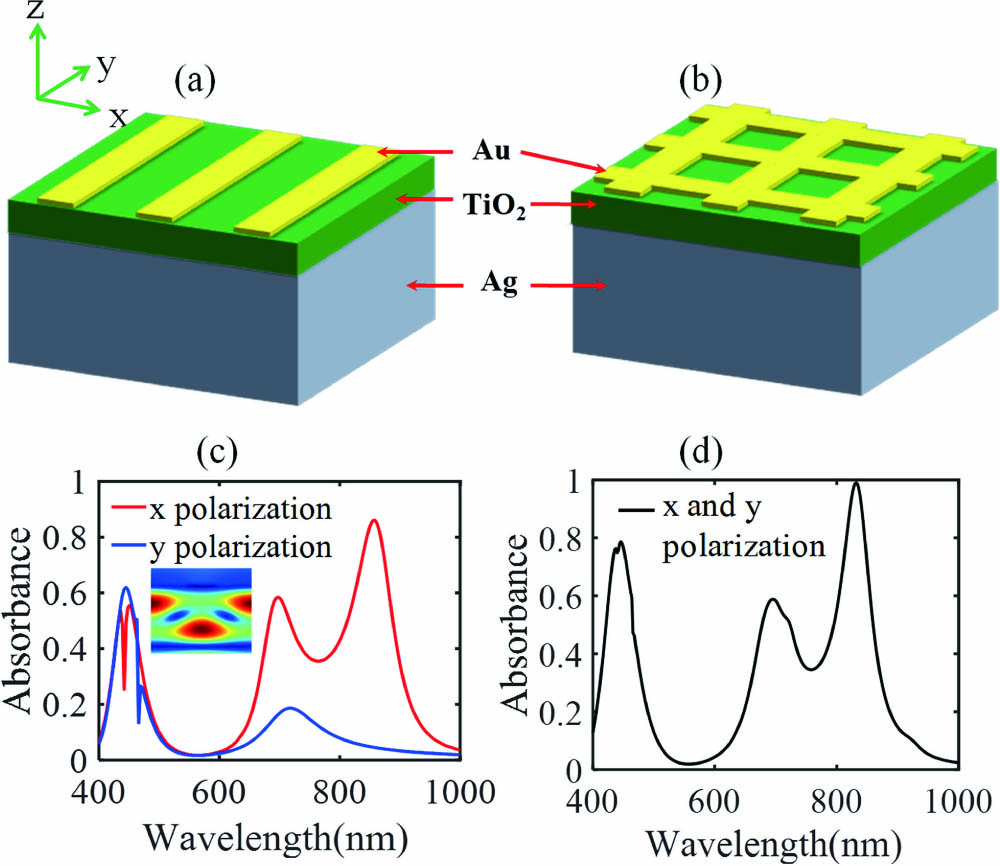
Fig. 1. Laser induced refractive index change for fabrication of photonic crystals in LiNbO3.
(a ) Schematic diagram. (b ) The relationship of the amplitude of second-harmonic and the phase-matching mechanism. (c ) and (d ) Second-harmonic confocal microscopy image of the 3D photonic crystal and which in X -Y plane. (e ) Intensity distribution along the black line in (d). Figure reproduced from ref.44, Springer Nature.
2.4 Laser induced phase change
Femtosecond laser has ultrashort pulse width and ultrahigh peak power. Therefore, the laser beam can instantaneously induce generation of high-temperature and high-pressure condition that is restricted in a local region when it is focused inside the materials with a low power45-47. Laser induced phase change would occur under these extreme conditions, which can be divided into four types, including crystalline phase melting and quenching to amorphous phase, direct solid-state amorphization, recrystallization and order-to-order phase transition45, 48-50. Laser induced phase change has been experimentally demonstrated in various materials, such as silicon, vanadium oxide, titanium dioxide, sapphire and so on51-54. For example, Vailionis et al.54 observed a new Al phase that is fabricated by femtosecond laser focused inside sapphire, which is formed due to the separation of Al ion and O ion under the high-temperature and high-pressure conditions (
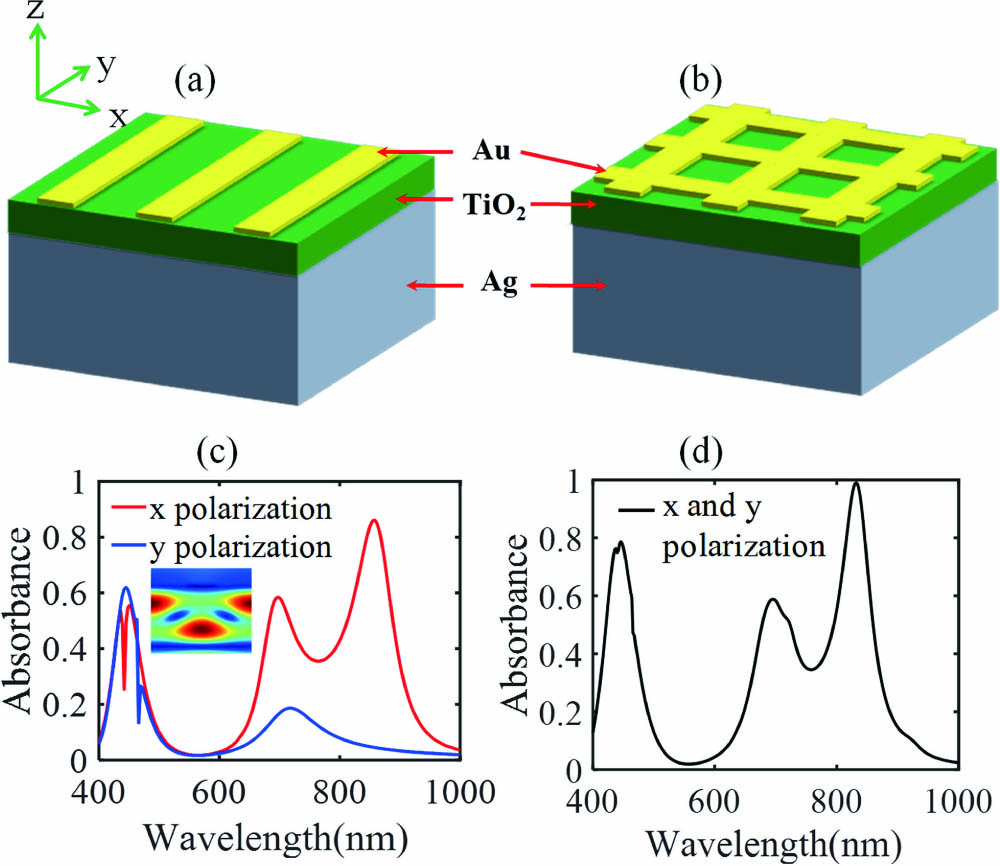
Fig. 2. Laser induced phase change.
(a ) Schematic diagram of the fabrication of phase change in sapphire by femtosecond laser. (b ) MicroX-ray diffraction measurement for evidence on the formation of bcc-Al. (c ) Schematic of phase transformations in laser modified sapphire. (d ) Laser induced phase change in GST films for fabrication of field emission transistor. (e ) TEM image and (f ) electron diffraction patterns of laser induced crystalline-to-amorphous transition in sapphire. Figure reproduced from (a-c) ref.54, Springer Nature; (d) ref.56, AIP Publishing; (e, f) ref.57, WILEY-VCH Verlag GmbH & Co. KGaA, Weinheim.
Many researchers have introduced the phase change phenomenon to micro/nanofabrication combined femtosecond laser and subsequent etching. Lin et al.56 proposed a phase-change nanolithography technique to rapidly fabricate of large area three-dimensional nanostructures. They introduced a phase change alloy (Ge1Sb2Te4 (GST)) film on the samples, which has two phase states of amorphous and crystalline phases. The phase states in local position of GST film can be changed from amorphous to crystalline phase by femtosecond laser irradiation, as shown in
2.5 Component change
The components of material also influence the use of etching solvent or gas and therefore influence the corresponding etching rate, which further affect the profile of fabricated structures. It has been widely demonstrated that the components of materials can be changed by femtosecond laser induced redox reactions and femtosecond laser doping process58-63, as shown in
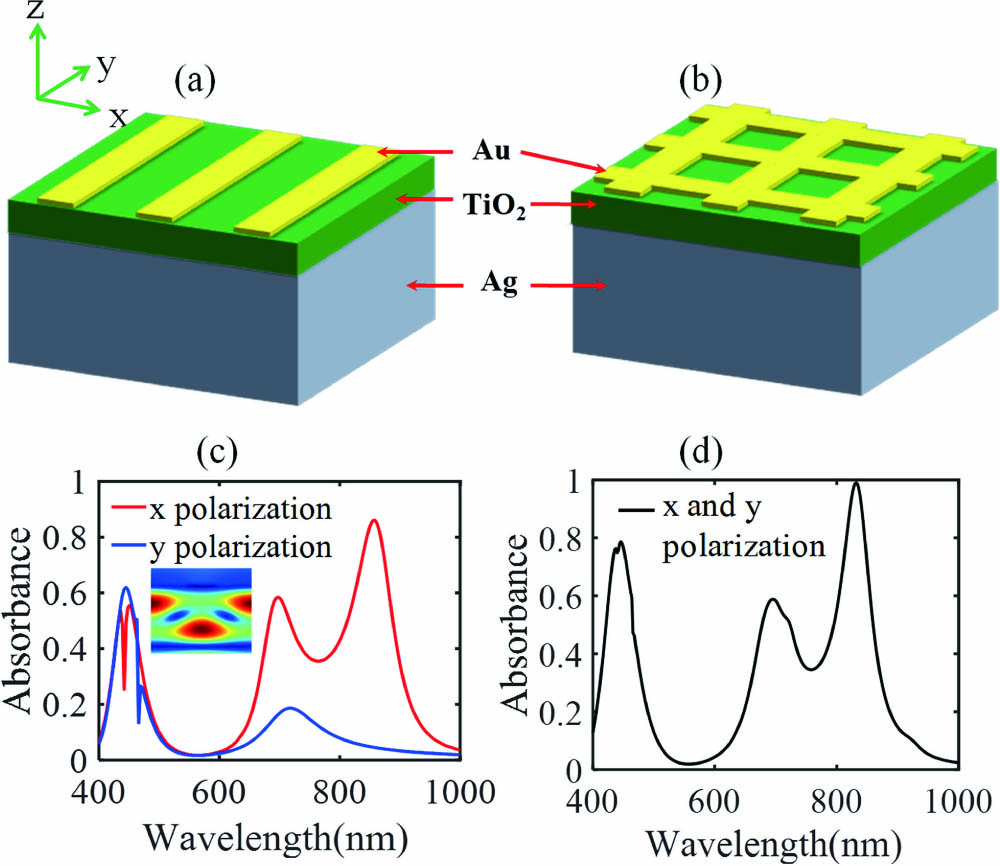
Fig. 3. Laser induced materials components change.
(a ) Schematic of formations of Ag nanoparticles inside silver containing zinc phosphate glasses by femtosecond laser. (b ) Laser induced helicoidally-distributed emitting silver clusters arrays. (c ) Demonstration of femtosecond laser doping of silver into titanium surface. Figure reproduced from (a, b) ref.61, WILEY-VCH Verlag GmbH & Co. KGaA, Weinheim; (c) ref.59, WILEY-VCH Verlag GmbH & Co. KGaA, Weinheim.
Femtosecond laser doping has been widely used in silicon surface modification for applications in photoelectric detectors and solar cells, which needs the presence of a precursor gas or film65-67. The precursor can be excited to dopant atoms with photolysis or pyrolysis of the gas or solid film by femtosecond laser irradiation. Then the dopant atoms can be doped into the sub-surface of silicon networks which are melted by laser in the meantime. During the re-solidification, the dopant atoms diffused into the deep surface of the silicon wafer. According to this principle, femtosecond laser doping can be expanded to processing of more extensive materials with component change. For example, silver atoms can be doped inside titanium surface, as shown in
3 Wet-etching-assisted femtosecond laser modification
The wet-etching-assisted femtosecond laser modification includes two main steps: femtosecond laser modification and subsequent chemical wet etching. First, tight focused femtosecond laser beam was used to induce materials modification inside transparent materials. Then, selecting a suitable etching solution (acidic solution or aqueous alkali) to corrode the modified zone and to achieve the fabrication of three-dimensional hollow structures68, 69. The technology was firstly proposed by Marcinkevičius et al. in 200170. They demonstrated the fabrication 3D microchannels in silica. Since then, many efforts have been focused on optimizing process and extending applications. Nowadays, the technology has been developed to a subtractive computer controlled 3D printing technology and realized commercialization71. For improving the precision and surface quality of fabricated structures, femtosecond laser-induced backside wet etching (LIBWE) technology has been proposed and shows potential applications in micro/nanofabrication72. This technology has been widely used to fabricate three-dimensional microchannels in photosensitive glass and silica. The selectivity of the etching solution to laser modified region and unmodified region, which is depended on the laser fabrication parameters and the etching parameters73, is important to fabricate high-aspect-ratio microchannels. For example, by using temporally shaped femtosecond laser, the energy deposition efficiency can be improved by adjusting the pulse delay to yield a stronger material modification, which helps to increase the etching selectivity74. In addition, by using different etching solutions64, 75, more complex structures can by realized.
The mostly used photosensitive glass is Foturan glass, which consists of lithium aluminosilicate glass with doping by a small amount of silver ions and cerium ions. With femtosecond laser irradiation, large number of free electrons would be directly generated without the photosensitizer, resulting in the reduction of silver ions to silver atoms76. During the thermal annealing process, Ag atoms are aggregated to form nanoclusters, which could induce the generation of crystalline lithium silicate in Foturan glass. The crystalline lithium silicate can be dissolved by HF solution, leading to the removal of laser modified regions. By using this method, complex 3D microstructures can be fabricated inside the photosensitive glass77-79. Hu et al.80 exhibited the fabrication of all-glass 3D optofluidic microlens integrated in closed microchannels by wet-etching-assisted femtosecond laser modification, as shown in
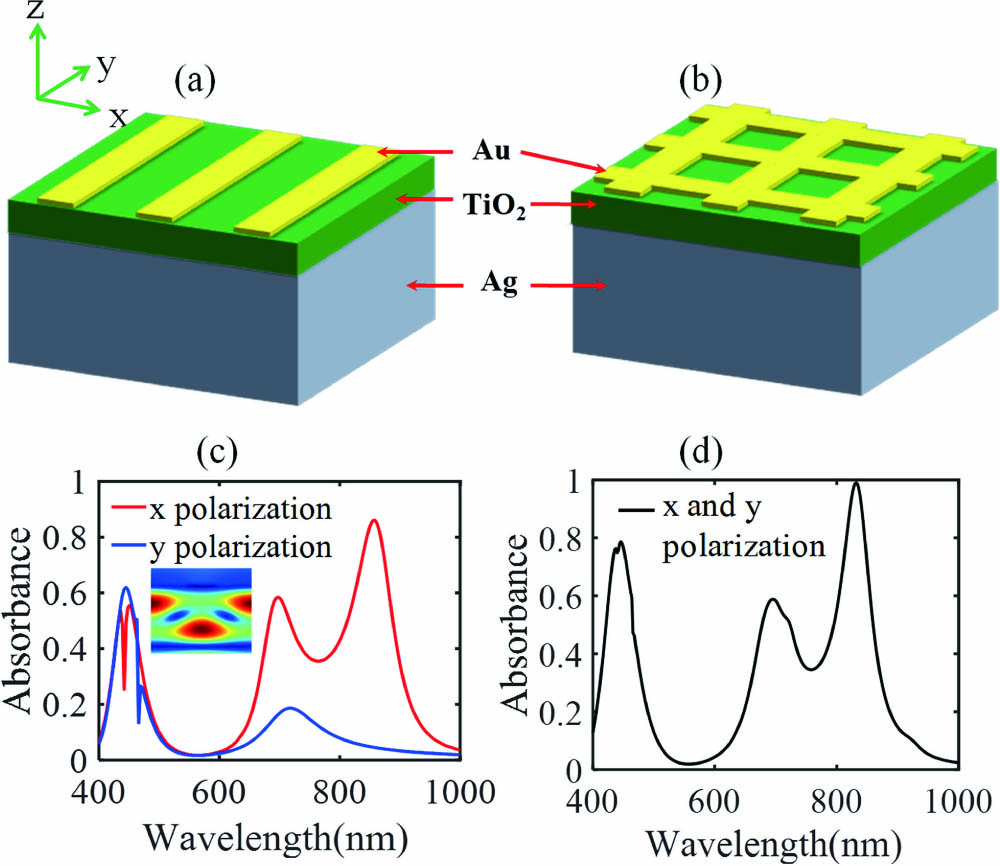
Fig. 4. 3D optofluidic microlens integrated in microchannels.
(a ) Schematic of fabrication process. Optical images of microlens in microchannels (b ) after laser modification and (c ) after complete formation. (d-f ) Focusing properties of microlens in microchannels in air, ethanol and sucrose solution, respectively. Figure reproduced from (a-f) ref.80, WILEY-VCH Verlag GmbH & Co. KGaA, Weinheim.
Except for photosensitive glass, some other transparent materials can also be used to fabricate 3D micro/nanostructures by wet-etching-assisted femtosecond laser modification, such as silica glass, sapphire, yttrium aluminium garnet (YAG) and so on82-86. Different with photosensitive glass, the mechanism of selective etching of laser modified region in these non-photosensitive glasses can be attributed to the mass density changes and stress corrosion effect87, 88. For silica, the fabricated microchannels always have the significant taper along the channel direction due to the higher concentration of solution and larger reaction time at channel entry compared with channel center. However, in sapphire and YAG, the HF solution etching selectivity between laser modified region and the original region shows a higher value than that in silica. Ródenas et al.89 demonstrated the fabrication of large area 3D dense nanopore lattices in YAG and sapphire crystal by multiphoton 3D laser writing combined with chemical wet etching, as shown in
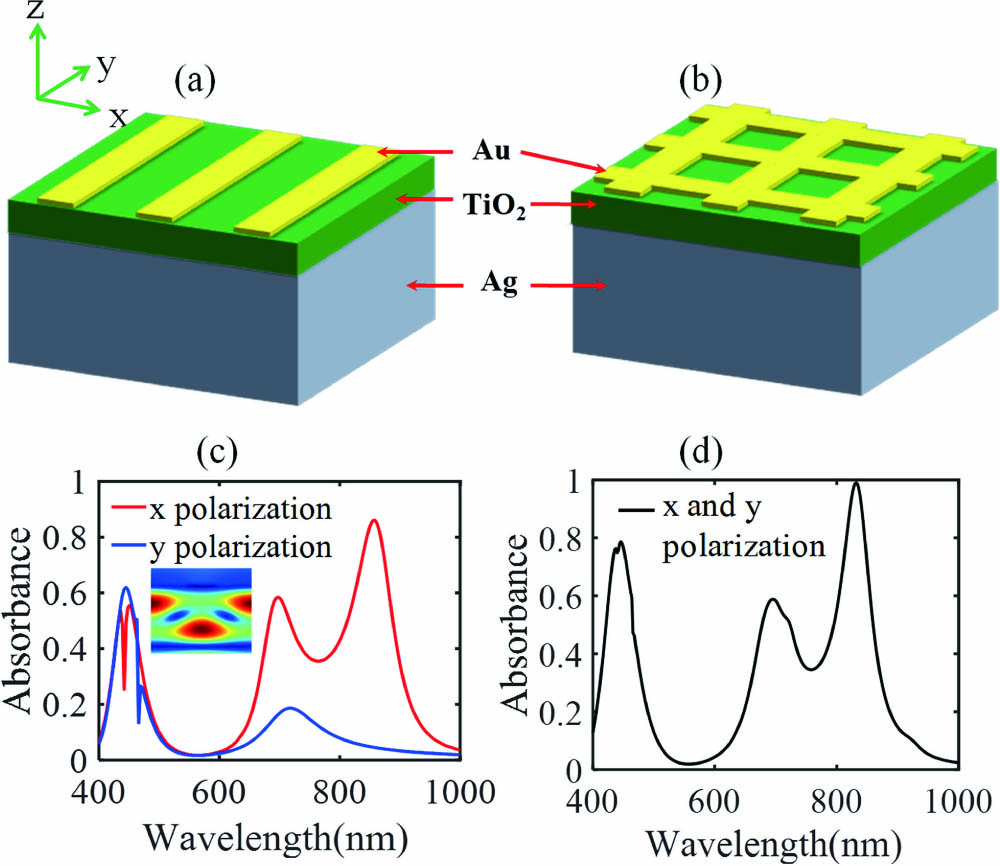
Fig. 5. Subwavelength gratings and optical waveguide fabricated in YAG crystals by wet etching assisted femtosecond laser modification.
(a ) Optical images of the gratings with centimeter-long and 700 nm-pitch. (b ) Diffraction efficiency of the gratings with a wavelength of 1070 nm. The insert image is the SEM of the fabricated gratings. (c ) The cross-section SEM image of the optical waveguide in YAG crystal. (d ) Simulated and (e ) experimental light intensity mode profiles of the optical waveguide with a wavelength of 1550 nm. Figure reproduced from (a-e) ref.89, Springer Nature.
Furthermore, Tokel et al.90 firstly introduced this method to fabricate complex 3D microstructures deep inside silicon, which is not transparent for laser beams with visible wavelength. Current semiconductor manufacturing technologies can't be used to fabricate micro/nanostructures directly inside silicon chips for applications in photonic devices and other functional microdevices. However, similar to other transparent materials, laser modified silicon shows higher etching rate compared with unmodified region by a mixed solution including Cu(NO3)2, HF, HNO3 and CH3COOH. Therefore, by using a pulsed fiber laser with 1.55 μm wavelength, which is transparent for silicon wafer, desired 3D microstructures were realized deep inside silicon, such as high-aspect-ratio micropillars, microchannels, through-Si vias and 3D cantilever-like structures90, as shown in
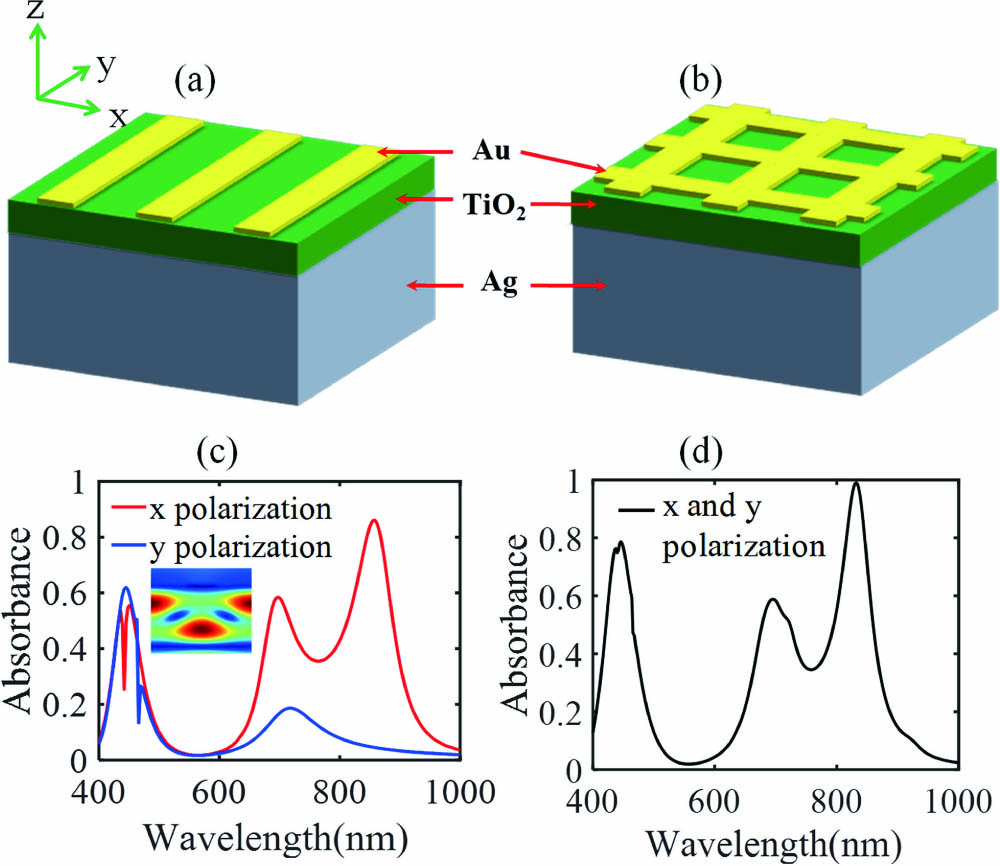
Fig. 6. 3D arbitrary micro-architectures fabricated in silicon wafer The SEM image of (a ) high-aspect-ratio micropillars array and (b ) sidewall of embedded microchannels inside silicon. Inset in (a) is the amplified view of the micropillars array. Inset in (b) is 3D profiles of the microchannels that was measured by laser scanning microscopy. (c ) The SEM image of 3D cantilever-like structures. (d ) SEM image of silicon plates. (e ) An artificially coloured SEM image of a complex silicon micro-cityscape. Figure reproduced from (a-e) ref.90, Springer Nature.
Another important application is using the fabricated microchannels or microstructures as the mold for rep- licating polymer or metal microstructures92-96. Chen et al. demonstrated the fabrication of polymer planar convex microlens arrays and compound eyes by replication of silica concave microlens arrays, which were fabricated by wet-etching-assisted femtosecond laser modification94, 95, as the diagram shown in
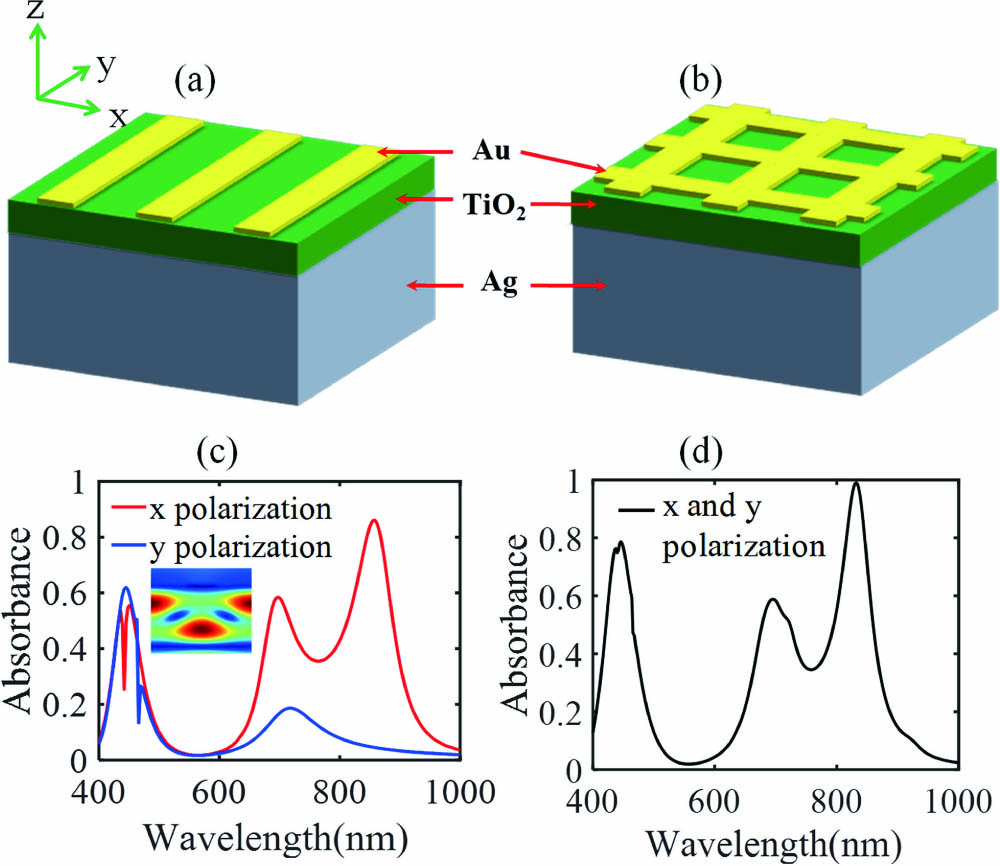
Fig. 7. Fabrication of 3D polymer compound eyes.
(a ) Diagram of fabrication of polymer compound eyes by replication of microlens arrays mask fabricated by femtosecond laser modification with subsequent wet etching. (b-d) SEM images of the polymer compound eye. Figure reproduced from (a-d) ref.95, WILEY-VCH Verlag GmbH & Co. KGaA, Weinheim.
Wet-etching-assisted femtosecond laser modification has been widely used to fabricate artificial 3D microstructures inside some hard materials. However, the method is difficult to process materials with corrosion resistance, such as diamond. Wet etching of crystal materials is always crystal-orientation-based etching, which would result in the distortion of designed structures. For realizing isotropic chemical wet etching, a mixed solution with complex and accurate dosage ratio of components is essential, which would increase the technological requirements.
4 Dry-etching-assisted femtosecond laser modification
Dry etching is currently the most mature and widely used etching process in the industry. Broadly speaking, all etching techniques that do not involve chemical solution etching are referred to as dry etching. In the micro/nano manufacturing of the semiconductor industry, photolithography is usually the first step in the designing of micro/nanostructures.Then, the pattern is transferred on the substrate material to achieve a certain function device. The photoresist is only used as a mask structure and will be removed after the pattern is transferred. The dry etching technology has become the main etching technology in the semiconductor process due to its controllability, high precision, and batch etching. Ion beam etching (IBE), plasma etching (PE) and inductiviely coupled plasma (ICP) etching are the widely used etching process in industry, which are essentially used plasma to etch materials. IBE is a pure physical bombardment process and can be used for removal almost any materials. PE is mainly a chemical etching processing due to a weak electric field at the anode surface where the sample is placed on. ICP etching has the advantage to control the ratio of physical bombardment etching and chemical etching by adjustment of the etching power. Therefore, the ratio of lateral and vertical etching rates can be precisely controlled, which is helpful for fabricating complex 3D micro/nanostructures.
Taking advantages of well controllability, high precision, wide range of processable materials and compatibility with semiconductor manufacturing of dry etching, Liu et al.97 firstly proposed the dry-etching-assisted femtosecond laser modification technology to process hard materials, which also includes two steps: femtosecond laser modification for pattern definition and subsequent ICP etching for structures developing, as the schematic diagram shown in
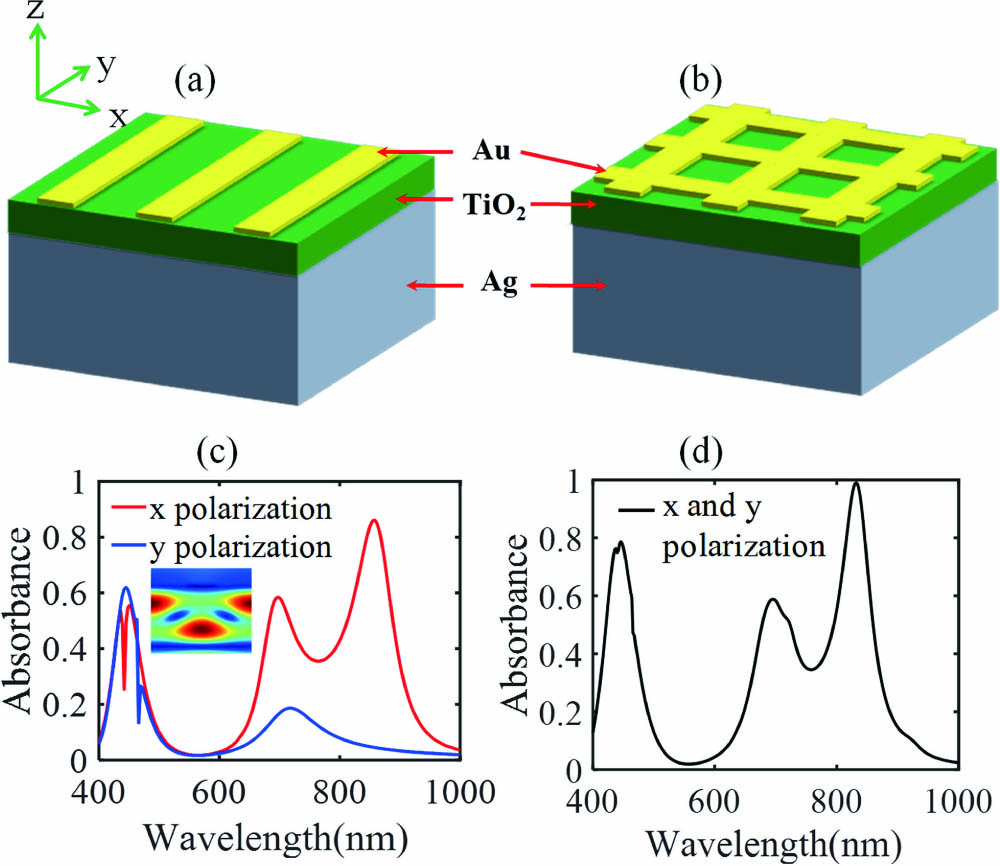
Fig. 8. Fabrication of silicon concave microlens arrays by dry-etching-assisted femtosecond laser modification.
(a ) Diagram of fabrication of silicon microlens arrays. (b ) Diagram of the evolution of the microlens formation. (c ) SEM of the closely packed silicon concave microlens arrays. (d ) SEM of microlens integrated on the micro-cantilever. Figure reproduced from (a-d) ref.97, WILEY-VCH Verlag GmbH & Co. KGaA, Weinheim.
Except for silicon, by using the high power plasma etching, other hard materials even ultrahard materials can be processed for 3D fabrication. For example, sapphire can be etched by a gas mixture which is consisted of chlorine (Cl2) and boron trichloride (BCl3) using an ICP system98. Sapphire has been widely used as the substrates and optical windows of optoelectronic devices, due to its outstanding features of high hardness, thermal and chemical stability and high transparency at wavelength ranging from ultraviolet to near infrared. Realizing high precision micro/nano processing of sapphire is necessary for applications in integrated micro/nano-optics. Due to the dependence of etching rate with crystal orientation, wet-etching-assisted femtosecond laser modification is not suitable for flexible fabrication of high quality smooth curved micro optical elements99. Liu et al.100 demonstrated the controllable fabrication of sapphire concave microlens by dry-etching-assisted femtosecond laser modification. By using femtosecond laser 3D fabrication system that consisted of a theta lens and a galvanometer-based scanner, cm-sized microlens arrays could be rapidly fabricated on the surface of a curved sapphire substrate, forming a concave sapphire compound eye. The fabrication efficiency was increased approximately two-orders-degree compared with that fabricated by laser ablation. Based on the large difference of thermal expansion coeffcients between sapphire and K9 glass, sapphire concave compound eye can act as the mold for high temperature casting replication of K9 glass compound eyes (
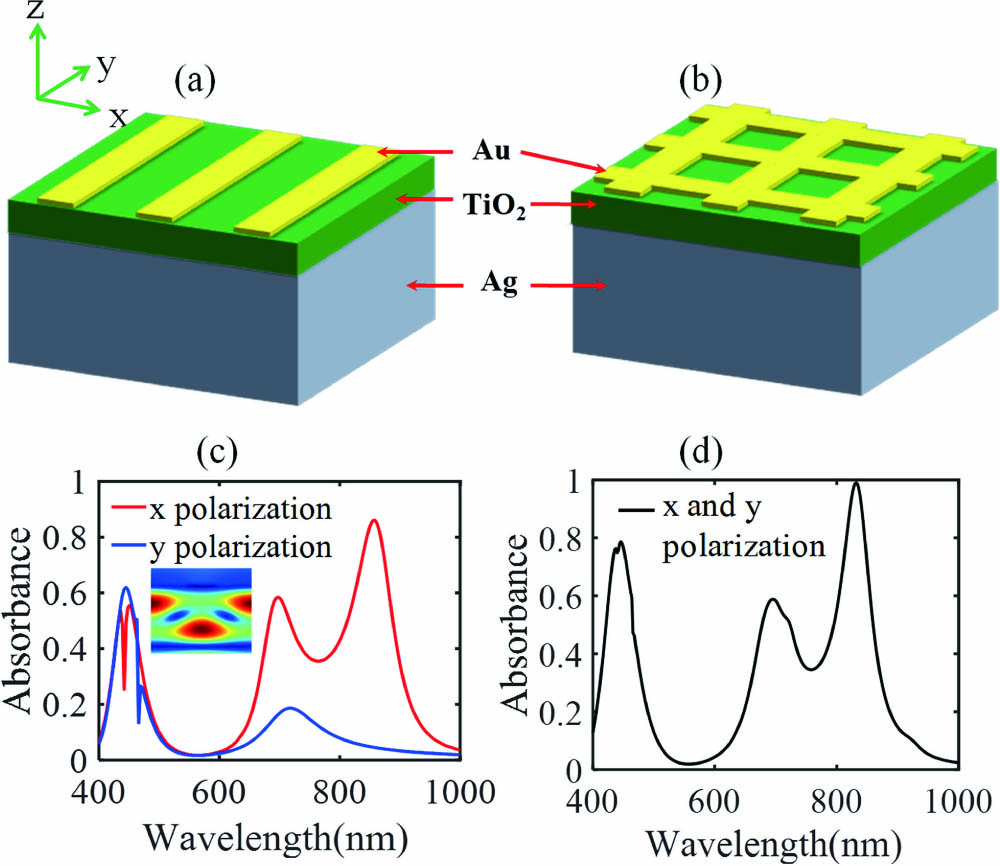
Fig. 9. K9 glass compound eyes.
(a ) Diagram of the fabrication of sapphire compound eyes and the thermal replication of K9 glass compound eyes. (b ) Optical image and (c, d ) SEM of the centimeter-sized K9 glass compound eye. Insert in (d) is the amplified SEM image. (e-g ) Optical images of focal spots with incident angle of 0°, 30° and 45°, respectively. Figure reproduced from (a-g) ref.100, WILEY-VCH Verlag GmbH & Co. KGaA, Weinheim.
As mentioned above, the components of materials can be changed during femtosecond laser modification via redox reactions or femtosecond laser doping. It was demonstrated that the silicon atoms in laser modified regions could be insufficiently oxidized when processing in air. As the ratio of etching rate between silicon and silica is about 10:1 when etched by fluorine-based gas102, 103, the laser modified pattern can be used as the mask for 3D microstructures transferring63. More interestingly, the ability of etching resistant of laser modified region is greatly related to the concentration of oxygen atoms which can be adjusted by laser parameters104. Therefore, gray-scale 2D patterns with a concentration of oxygen atoms change with in-site position by femtosecond laser modification. Then, 3D microstructures can be fabricated on silicon wafer after suitable dry etching conditions. Based on this principle, Liu et al.104 verified the feasibility of the dry-etching-assisted femtosecond laser gray-scale modification technology by successful fabrication of complex 3D microstructures on silicon wafer. For example, the 2D Fresnel zone plate pattern (
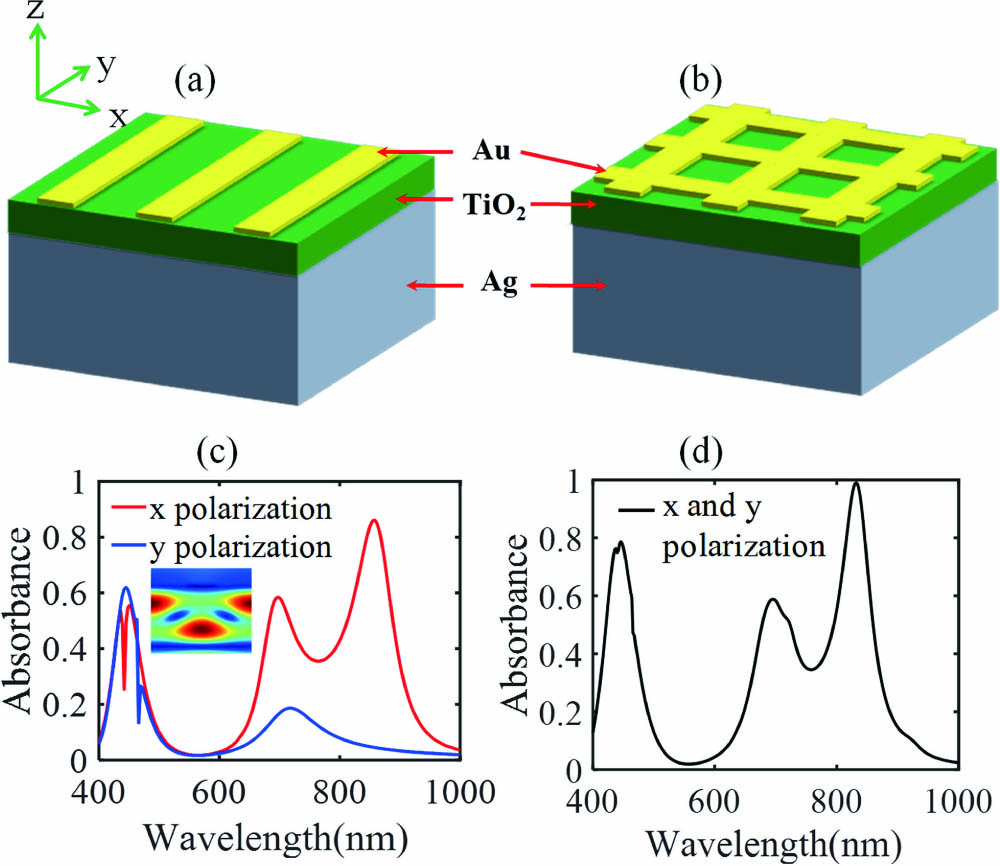
Fig. 10. Dry-etching assisted femtosecond laser gray-scale modification.
(a ) Diagram of the fabrication process. (b ) SEM of 2D Fresnel zone plate pattern fabricated by femtosecond laser modification. (c ) SEM of 3D well-defined Fresnel zone plate fabricated by transferring of 2D pattern with subsequent dry etching. Figure reproduced from (a-c) ref.104, AIP Publishing.
In integrated circuit industry, photolithography and dry etching are often used together to fabricate micro/nanostructures on the substrate. However, traditional photolithography can only fabricate two-dimensional (2D) micro/nanostructures on planar substrate. Recently, femtosecond laser two-photon polymerization has been widely used to fabricate arbitrary complex 3D micro/nanostructures on non-planar substrate105, 106. Therefore, 3D micro/nanostructures can be fabricated on non-planar hard materials by transferring polymer patterns using dry etching107. Various sapphire ultra-smooth micro-optical-components have been demonstrated by this dry etching assisted femtosecond laser lithography technology107. The surface roughness of these micro-optical-components is approximately 1.5 nm due to the nanometric resolution of ICP etching and femtosecond laser two-photon polymerization.
5 Conclusions and outlooks
We have summarized recent development in high precision and high efficiency micro/nanofabrication of hard materials by etching-assisted femtosecond laser modification from the fundamental and their applications. Due to the strong nonlinear laser-matter interactions, phenomena of non-damage energy deposition, phase change and components change would be generated by femtosecond laser modification. Based on the etching selectivity of the laser modified regions and the original regions, arbitrary complex 3D micro/nanostructures can be fabricated inside hard materials. The advantages and disadvantages of wet-etching-assisted and dry-etching-assisted femtosecond laser modification are discussed and their applications are introduced. These efforts promote the development of the technology for high precision machining in industry.
So far, although a lot of achievements have been obtained in micro/nanofabrication of hard materials by etching-assisted femtosecond laser modification, several problems are still existed in fabrication efficiency, precision and structural diversity. First, as a point-by-point direct writing technology, the fabrication efficiency is very low which limits the practical applications. It is necessary to explore new strategies to improve the fabrication efficiency of femtosecond laser modification. For example, parallel processing technology, such as laser interference and spatial light modulator is being developed for multi-beam processing and for 3D focal field scanning108-111. Second, due to the strong nonlinear laser-matter interaction, the surface roughness of the fabricated structures is difficult to satisfy the requirements of optical devices. More efforts should be made to increase the precision and surface smoothness by investigating the mechanism of laser modification, spatiotemporal focusing and post-processing80, 112-114. Third, wet-etching-assisted femtosecond laser modification has the advantage to fabricate 3D microchannels inside hard materials, while dry-etching-assisted femtosecond laser modification exhibits superiority in surface processing. The reported structures are still relatively simple. The combination of wet etching, dry etching and femtosecond laser modification need to be further investigated for realizing the integration of microdevices.
In short, the etching-assisted femtosecond laser modification technology plays an increasingly important role in fabrication of arbitrary 3D micro/nanostructures in hard materials, which has been applied in many fundamental researches. With the further exploration of the mechanism of laser-matter interaction and improvement of processing technology, it will be helpful to realize the integration of diversified micro/nano-devices and promote the industrialization of this technology.
6 Acknowledgements
This work was supported by the National Key Research and Development Program of China and National Natural Science Foundation of China (NSFC) under Grants 2017YFB1104300, 61590930, 61825502, 61805098 and 61960206003.
7 Competing interests
The authors declare no competing financial interests.
[18]
[19]
Article Outline
Xue-Qing Liu, Ben-Feng Bai, Qi-Dai Chen, Hong-Bo Sun. Etching-assisted femtosecond laser modification of hard materials[J]. Opto-Electronic Advances, 2019, 2(9): 09190021.