射流抛光中抛光液黏度对材料去除函数的影响
下载: 950次
1 引言
随着空间光学、高功率激光及**等应用领域的不断发展,现代光学系统对高精度非球面和自由曲面等复杂型面光学元件的需求逐步增大[1],传统抛光技术难以满足这类光学元件的加工要求。研究人员对新型的非球面抛光技术进行了大量研究[2],其中,较有代表性的技术之一是射流抛光技术[3]。射流抛光是将射流加工与计算机控制确定性抛光(COSS)技术有机结合,利用混有磨粒的抛光液输送至喷嘴加速,形成柔性射流束,将其作用于工件表面产生材料去除,进一步通过控制射流压力、方向及驻留时间等定量修正待加工工件的面形。相比于其他非球面抛光技术,射流抛光具有边缘效应弱、亚表面损伤低、无热效应及对工件表面形状适应性强等优点,在复杂型面光学元件抛光中有着独特的优势。
研究射流抛光材料去除机理,获得稳定可控材料去除函数是建立抛光工艺控制模型、获得高精度面形的必要条件[4]。为此,国内外研究学者围绕射流抛光材料去除机理在理论与实验等方面开展了大量研究。Fähnle等[5]指出射流抛光的入射压力较低,磨粒与工件的碰撞是产生材料去除的关键因素,抛光液基液对材料去除近无贡献。方慧等[6]通过纯水射流与磨粒射流对比实验证明了上述观点,并进一步研究了入射角度、入射压力、入射距离和驻留时间等射流工艺参数对材料去除率的影响。李兆泽等[7]从脆塑转变临界切削深度理论出发,认为射流抛光材料去除为塑性剪切去除,并分析了磨料种类、粒径和浓度等参数对材料去除率的影响。施春燕等[8]基于计算流体动力学理论,研究了入射距离与抛光材料去除的影响。香港理工大学的Cao等[9]将塑性去除理论与流体数值仿真相结合,获得了磨粒、工件材料参数与材料去除率之间的函数关系。
现有射流抛光材料去除机理研究主要围绕射流工艺参数、工件与磨粒参数,针对抛光液黏度的研究相对较少。射流抛光中抛光液的基液通常由水、添加剂和分散剂组成,实际加工中使用添加剂和分散剂的种类和含量不同均会引起抛光液的黏度变化[10],改变材料去除函数,会影响射流抛光效果。本文研究抛光液黏度变化对光学元件射流抛光材料去除函数的影响,首先阐述连续相、离散相数学模型以及磨粒冲蚀磨损模型,在此基础上建立多相射流有限元计算模型,计算不同黏度下的流场分布、磨粒运动轨迹以及射流去除函数,再搭建射流抛光实验平台,结合工艺实验验证仿真分析结果,探究黏度对材料去除函数的影响机制。
2 磨料水射流数学模型
射流抛光的基本原理如
2.1 连续相模型
在射流抛光过程中,可假设抛光液及空气为不可压缩流体,且其温度与密度保持恒定。根据不可压缩形式Navier-Stokes方程,可得到连续相控制方程[12]:
式中,
2.2 离散相模型
射流束可分为自由射流区、冲击区和壁面射流区,其中,冲击区是发生材料去除的主要区域。在射流的冲击区内,射流由沿喷嘴轴向流动急速改变为平行于工件表面流动,存在较大的压力梯度与速度梯度。根据多相流动力学,磨粒在射流束的携带下的运动方程可表达为[13]
式中,
式中,
2.3 磨损模型
磨料射流产生的材料去除函数可以看作是一定时间和一定区域内射流束携带的每个磨粒产生材料去除量之和。假定喷嘴出口速度为
式中:
式中:
3 仿真建模与计算
3.1 仿真模型及参数设置
以喷嘴轴线与工件表面法向重合的垂直入射方式为研究对象,基于2节所述数学模型在Fluent软件中建立如
表 1. 抛光液参数
Table 1. Polishing slurry parameters
|
3.2 计算结果与分析
在固定入射速度为30 m/s的情况下,按
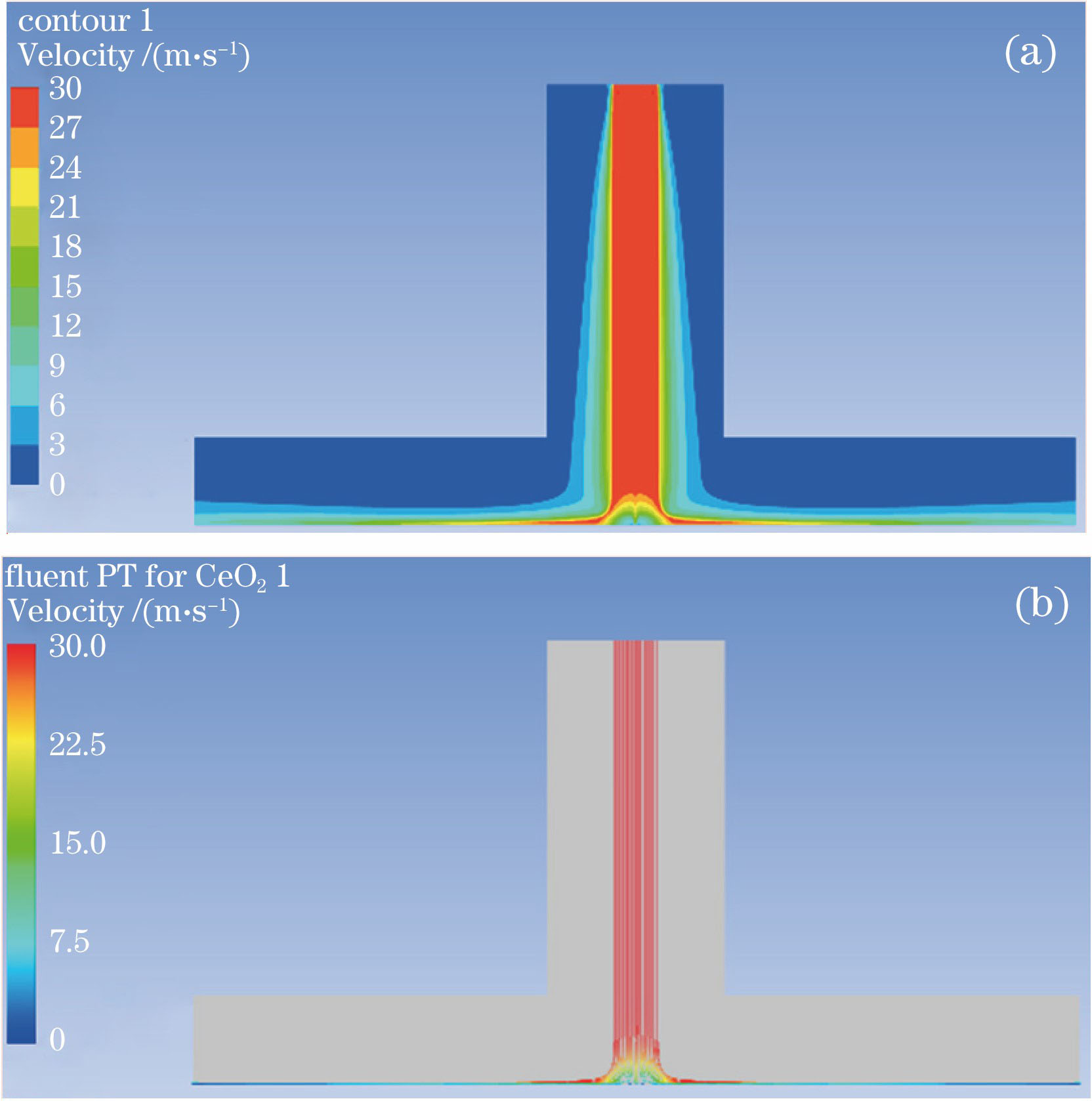
图 3. 抛光液黏度为1.01 mPa·s,入射速度为30 m/s时的计算结果。(a)流体速度分布;(b)磨粒运动轨迹
Fig. 3. Calculation results under 1.01 mPa·s polishing slurry viscosity and 30 m/s incident velocity conditions. (a) Velocity of liquid; (b) pathlines of abrasive particles
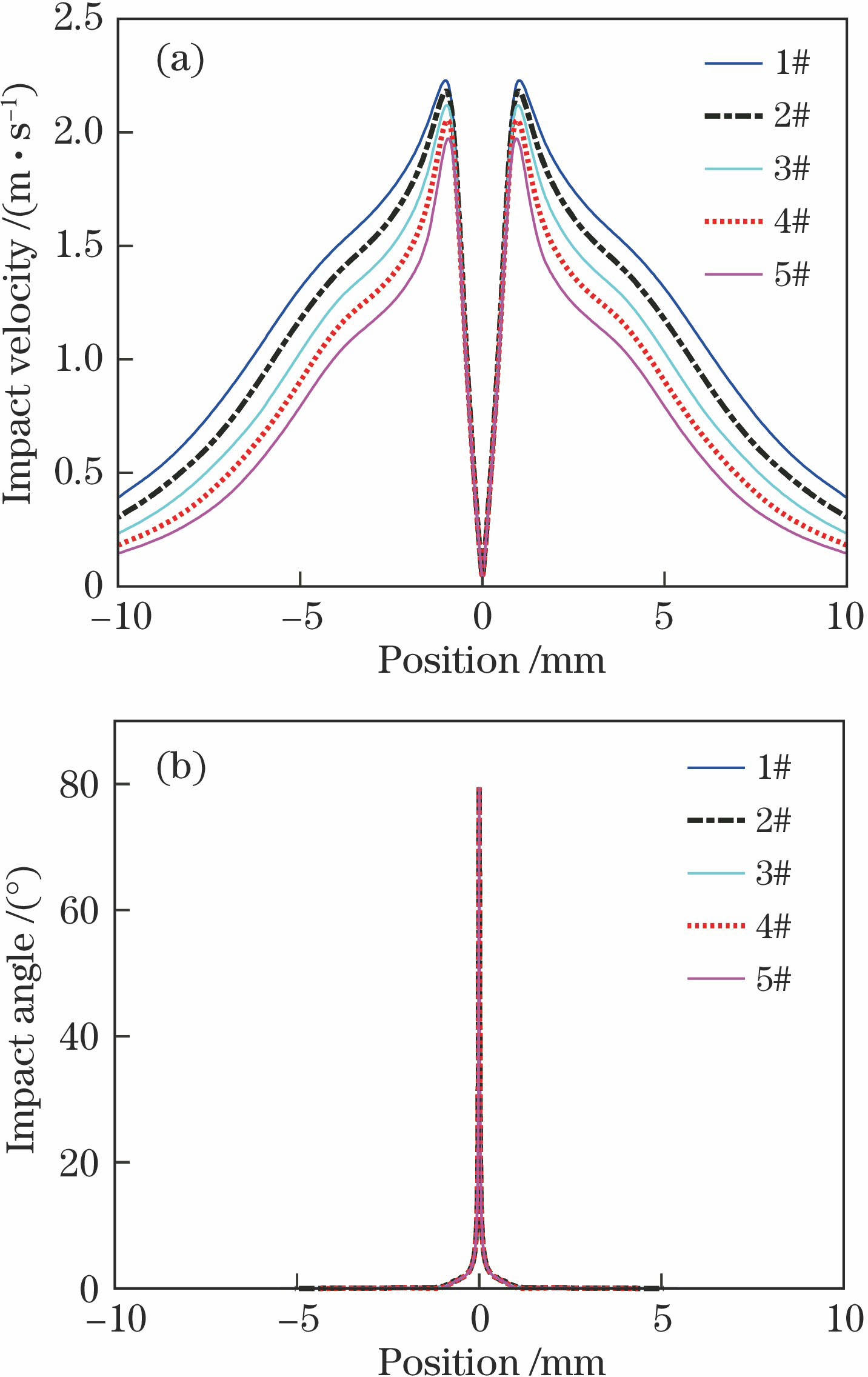
图 4. 不同黏度离散相模型计算结果对比。(a)磨粒碰撞速度分布;(b)磨粒碰撞角度分布
Fig. 4. Comparison of calculation results of DPM under different viscosity conditions. (a) Velocity distribution of abrasive particles; (b) angle distribution of abrasive particles
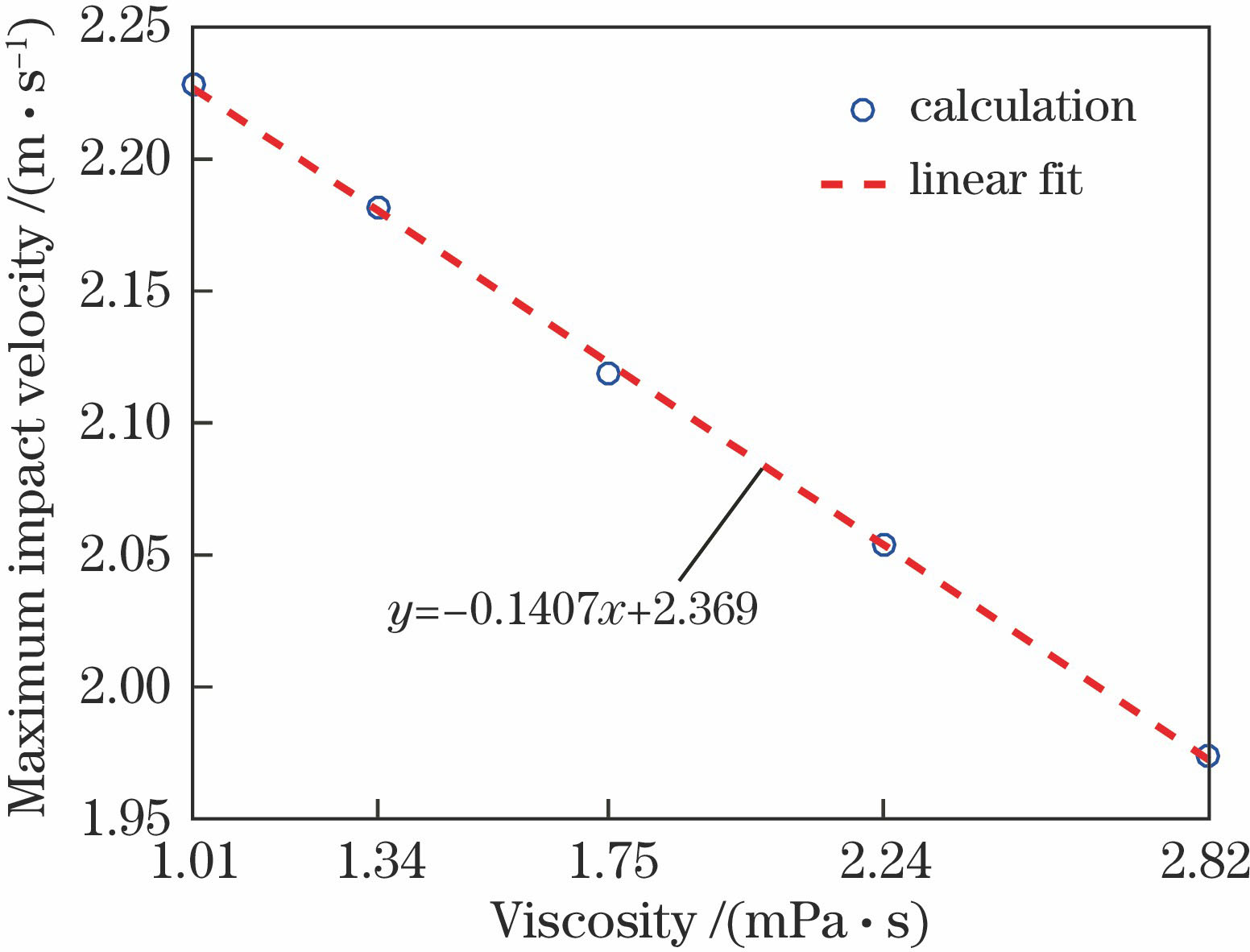
图 5. 抛光液黏度对磨粒最大碰撞速度的影响
Fig. 5. Influence of the polishing slurry viscosity on the maximum impact velocity of abrasive particles
分析DPM模型计算结果,定义磨粒速度方向与工件表面的夹角为磨粒碰撞角度,以驻点为中心,定义驻点坐标为0,工件表面路径获得的不同黏度下磨粒与工件的碰撞速度、碰撞角度分布如
基于上述磨粒碰撞速度和碰撞角度计算结果,可根据(5)~(9)式进一步分析黏度对材料去除函数的影响。根据已有文献[15-16],塑性去除模型中的
4 射流抛光实验研究
4.1 实验方案
在前文分析黏度对材料去除率的影响趋势基础上,在如
按照
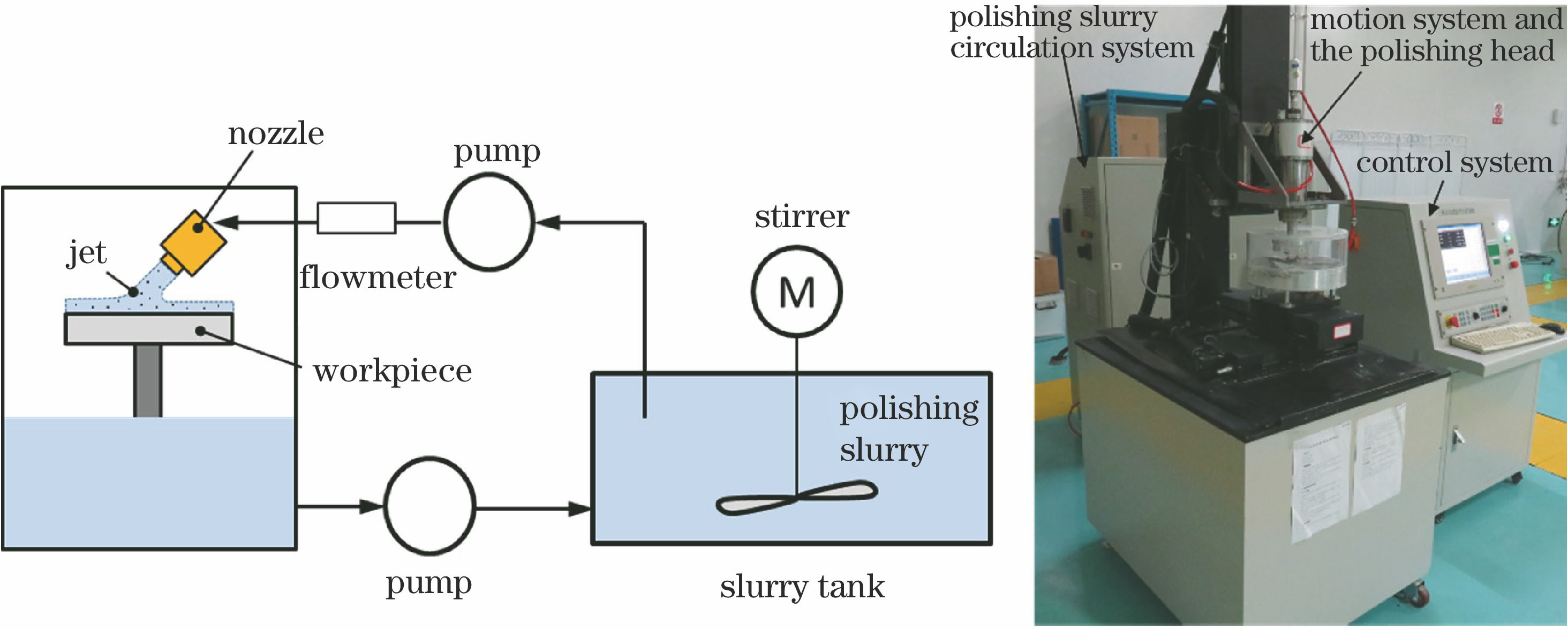
图 6. 射流抛光系统结构示意图(左)与实物图(右)
Fig. 6. Schematic (left) and labeled photo (right) of fluid jet polishing system
4.2 分析与讨论
利用白光干涉仪测量各抛光斑面形,其中使用1#抛光液获得的抛光斑如
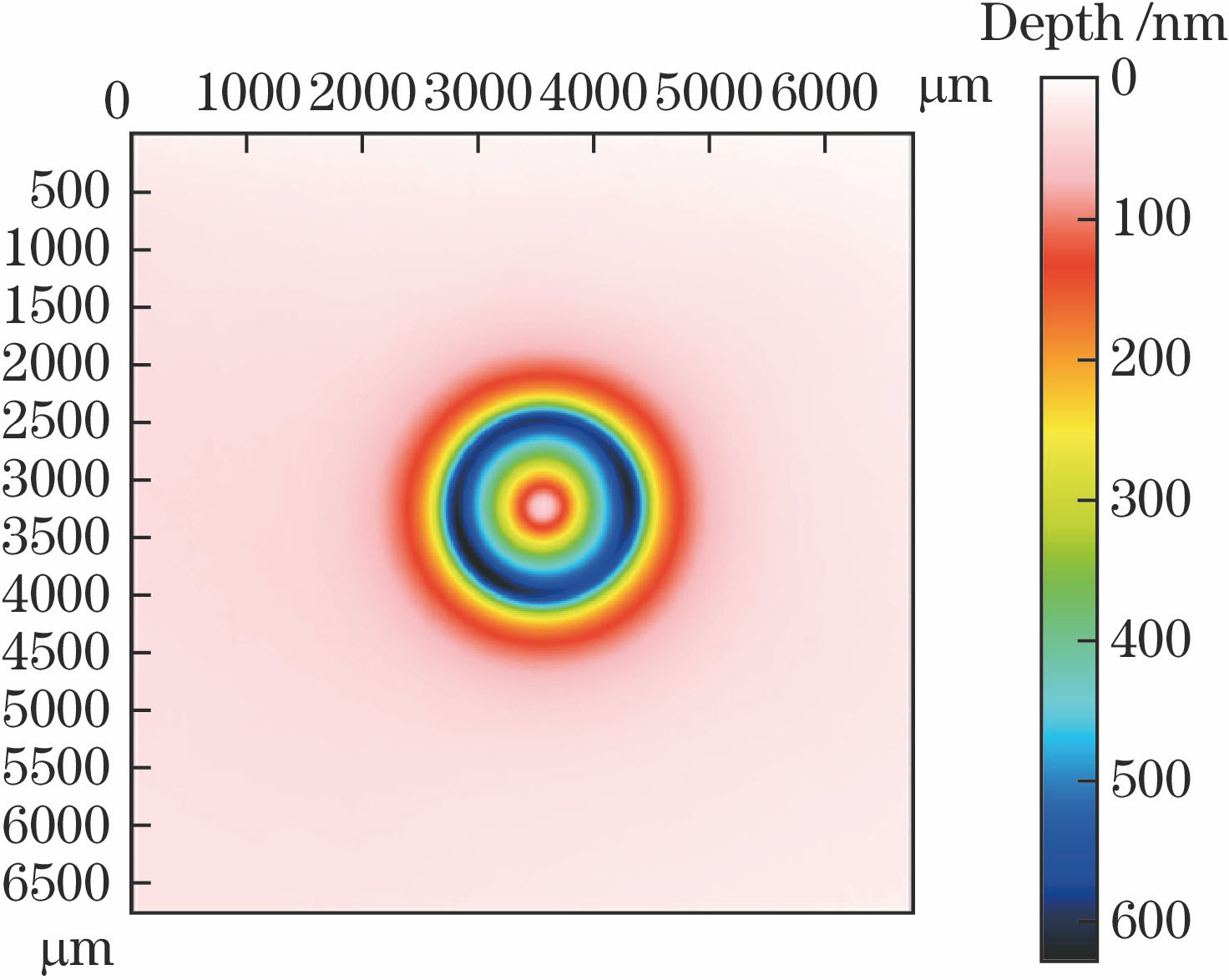
图 7. 入射速度为30 m/s,1#抛光液条件下的抛光斑
Fig. 7. Polishing spot under 1# polishing slurry with 30 m/s incident velocity
在不同的抛光液黏度下,材料去除函数均呈“W”型分布,理论计算与实验获得的材料去除函数分布总体吻合情况较好,证明了上述磨损模型的正确性。同时也注意到在使用4#和5#高黏度抛光液情况下,理论计算结果与实验结果存在一定偏差,实验中去除函数中心的材料去除量不为0,这可能是由高黏度情况下去除深度较小,材料去除函数受工件初始面形及加工误差等方面的影响增大所致。
表 2. 磨损模型参数表
Table 2. Parameters of the erosion model
|
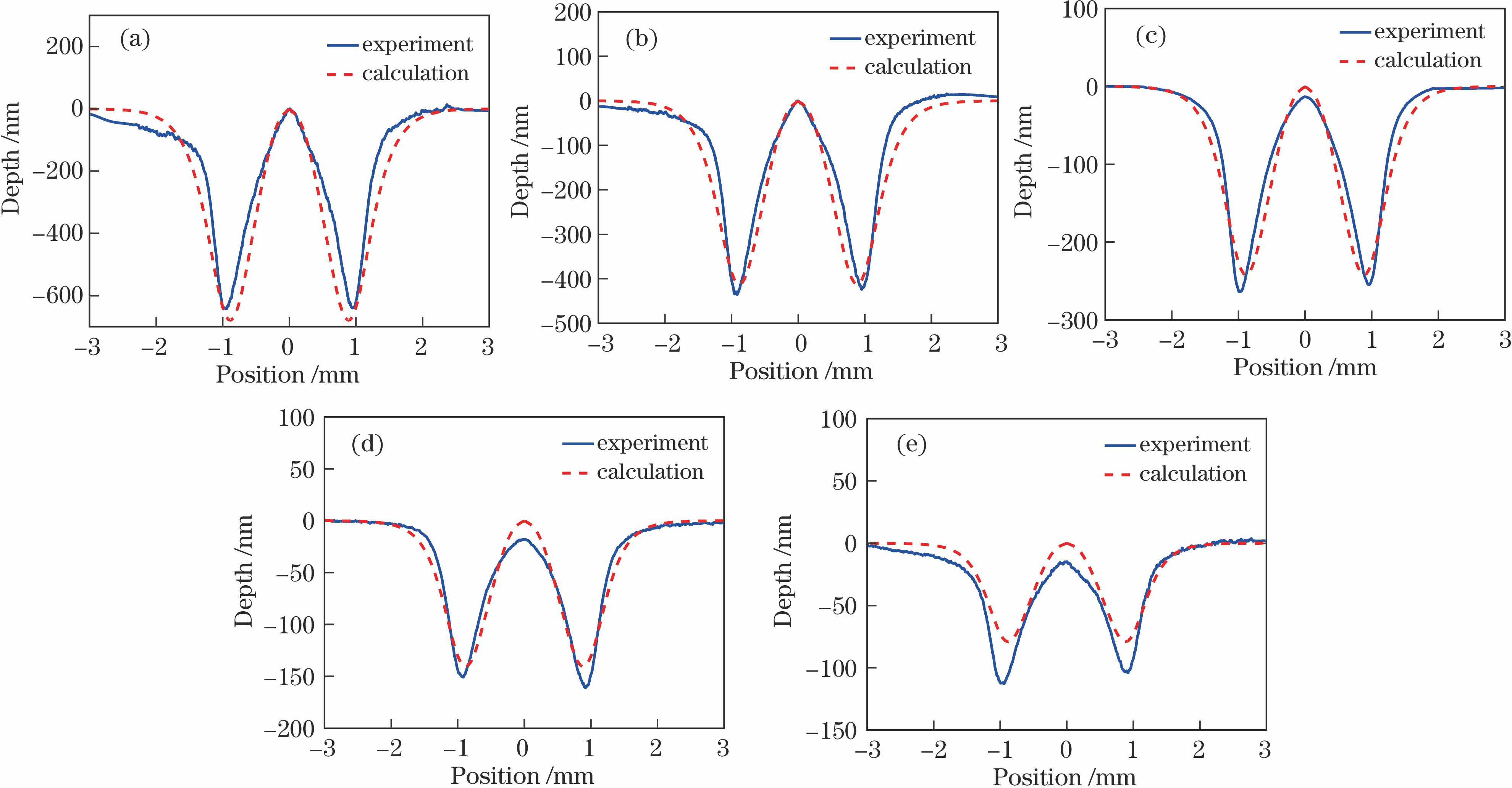
图 8. 不同黏度抛光液下材料去除函数实验与计算结果对比。(a) 1# 抛光液;(b) 2#抛光液;(c) 3#抛光液;(d) 4#抛光液;(e) 5#抛光液
Fig. 8. Comparison between the material removal functions obtained by experiments and calculation under different polishing slurry viscosity conditions. (a) 1# polishing slurry; (b) 2# polishing slurry; (c) 3# polishing slurry; (d) 4# polishing slurry; (e) 5# polishing slurry
进一步分析计算与实验结果,实际参与材料去除的磨粒比例系数与黏度之间的关系如
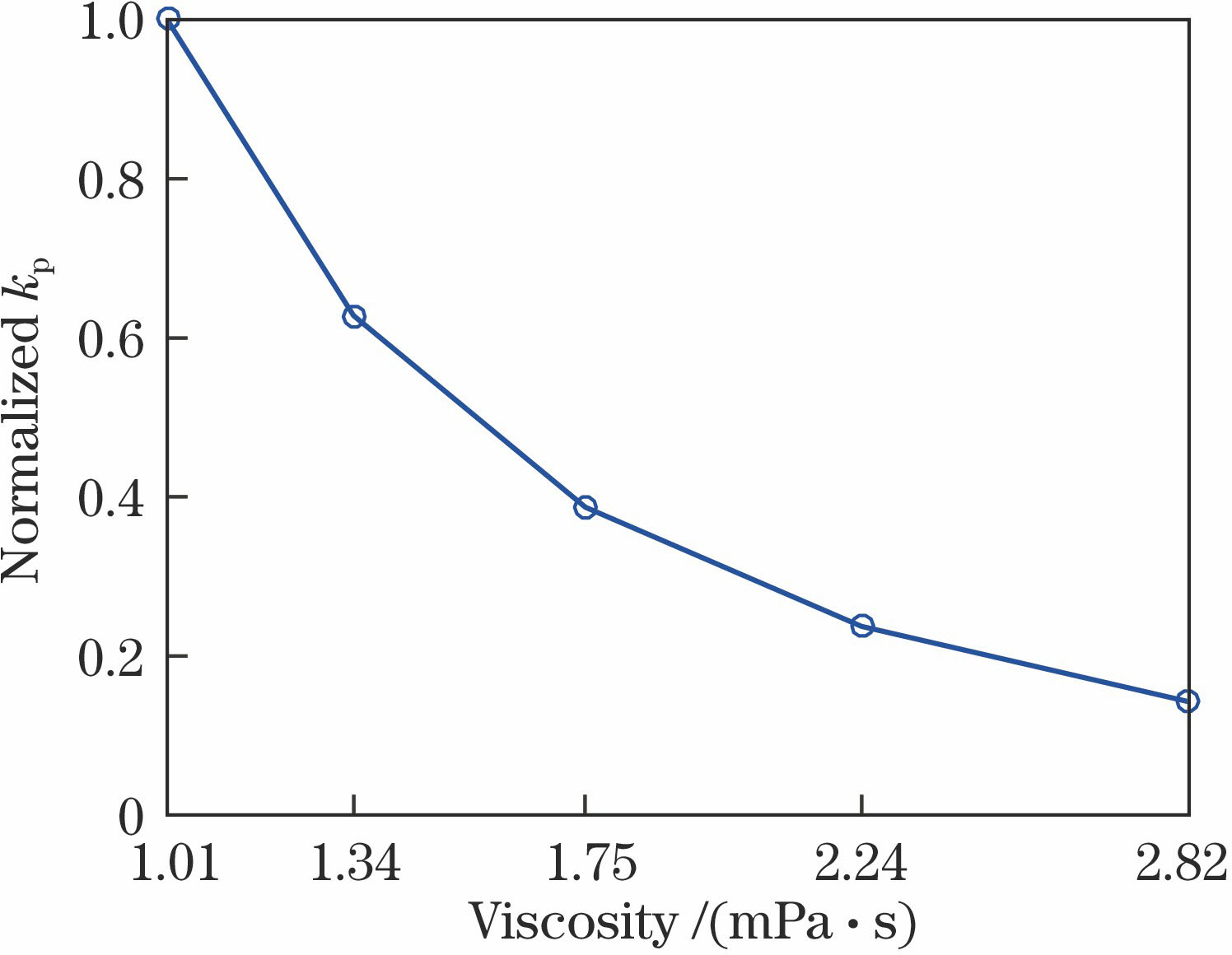
图 9. 实际参与材料去除的磨粒比例系数随黏度变化规律
Fig. 9. Variation law of wear-particle proportion coefficient with viscosity change in material removal
在获得抛光液黏度对材料去除函数影响规律的基础上,进一步研究上述材料去除函数变化对射流抛光表面粗糙度的影响。以尺寸为20 mm×20 mm×10 mm、初始粗糙度
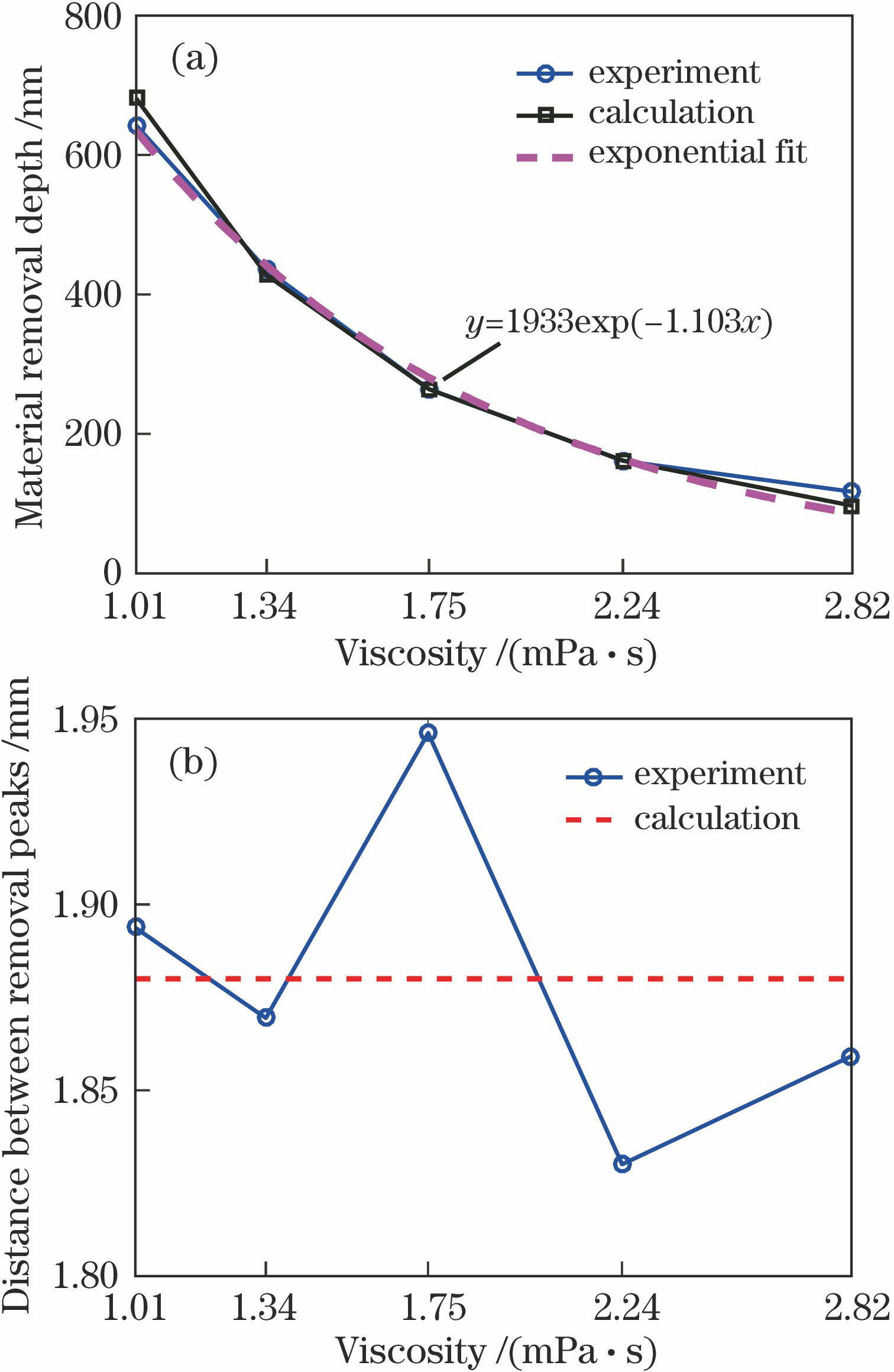
图 10. 去除函数特征量随黏度变化规律。(a)最大去除深度;(b)去除函数峰值间距
Fig. 10. Variation law of characteristic quantity of removal function for different viscosities. (a) Maximum material removal depth; (b) distance between removal peaks
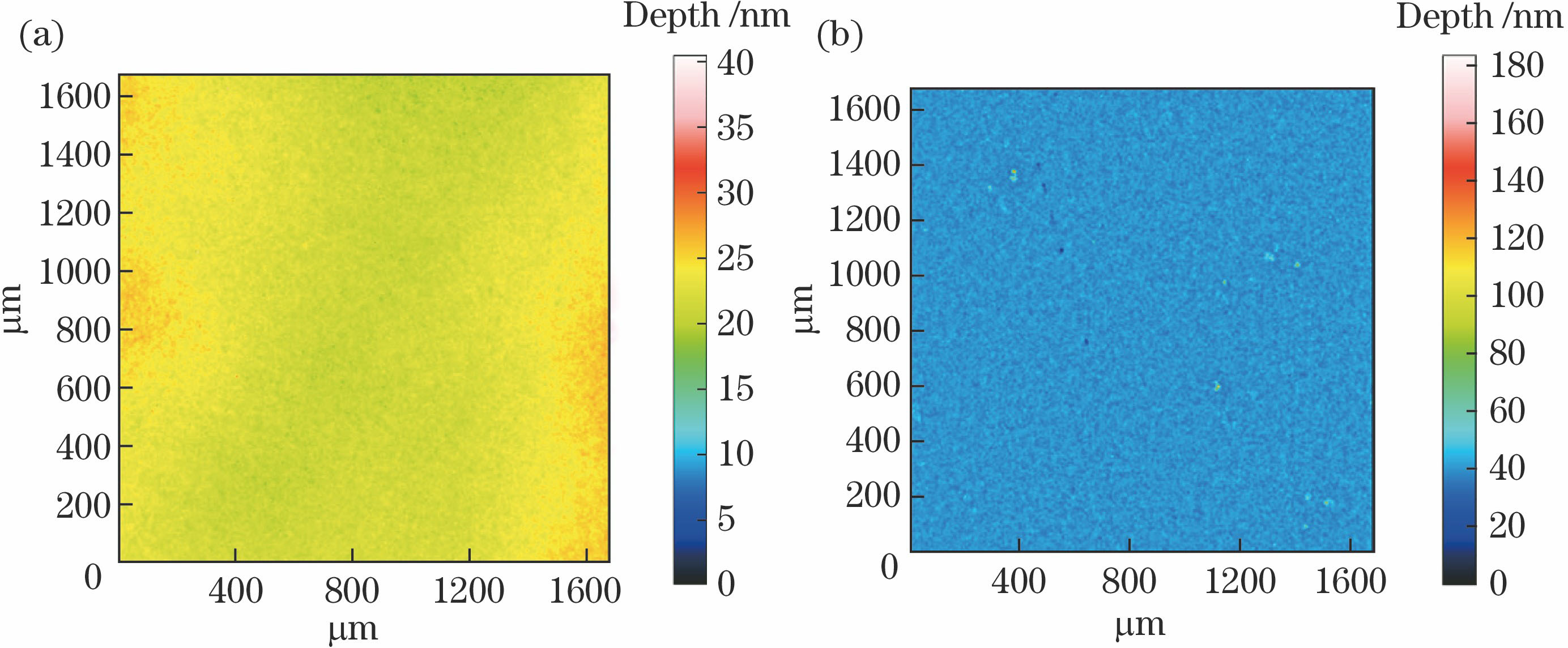
图 11. 使用不同黏度抛光液均匀抛光后的工件表面粗糙度对比。(a) 1#抛光液,Ra=7.778 nm;(b) 5#抛光液,Ra=1.445 nm
Fig. 11. Comparison of surface roughness of workpieces after uniform polishing using different polishing slurry viscosities. (a) 1# polishing slurry, Ra=7.778 nm; (b) 5# polishing slurry, Ra=1.445 nm
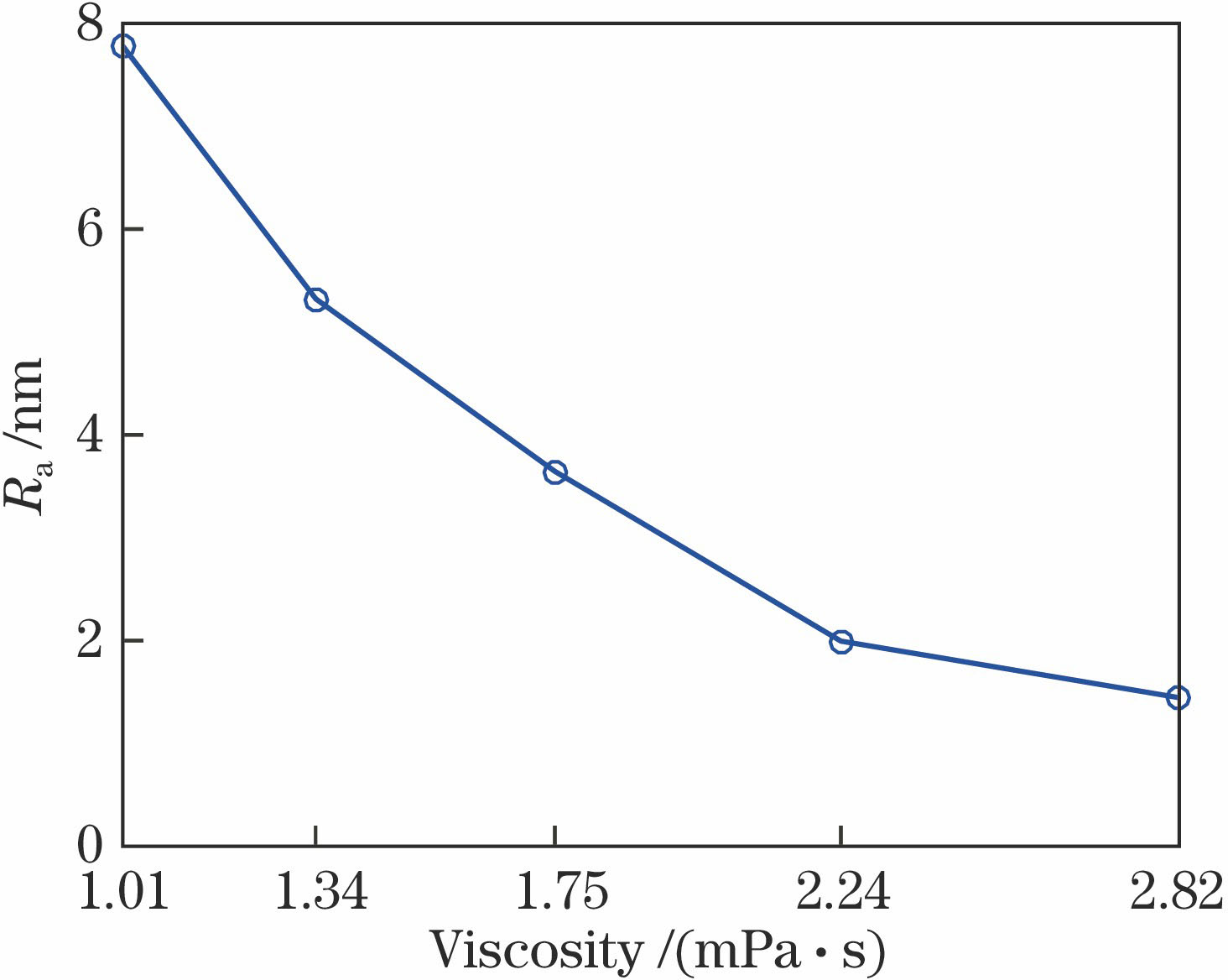
图 12. 抛光液黏度对工件表面粗糙度的影响
Fig. 12. Influence of slurry viscosity on the surface roughness of workpieces
5 结论
在建立射流抛光数学模型的基础上,结合仿真计算与实验研究了抛光液黏度对射流抛光材料塑性去除的影响。研究发现:增大抛光液黏度导致射流冲击区速度梯度增大,降低了磨粒撞击速度,最大碰撞速度随黏度近似呈线性减小趋势,碰撞角度则基本保持不变;同时,磨粒与工件表面之间的润滑作用增强,磨粒冲蚀磨损过程中参与去除的磨粒比例降低。在这两方面因素共同作用下,随着抛光液黏度的增大,光学元件射流抛光材料去除函数呈现出总体形状保持不变、去除深度近似呈指数型降低及去除范围保持不变的变化特征。进一步的均匀抛光工艺实验结果表明,黏度增大引起的材料去除函数变化有利于降低射流抛光表面粗糙度,提高工件表面质量。为此,在实际抛光过程中,可合理调制抛光液比例成分、调控抛光液黏度;粗抛阶段可选择低黏度抛光液,以提高面形收敛效率;精抛阶段可根据表面粗糙度与黏度之间的指数型关系,结合粗抛结果适当提高抛光液黏度,从而提升抛光精度至满足实际工艺需求。
[1] 庞志海, 樊学武, 马臻, 等. 自由曲面校正光学系统像差的研究[J]. 光学学报, 2016, 36(5): 0522001.
[2] 袁巨龙, 吴喆, 吕冰海, 等. 非球面超精密抛光技术研究现状[J]. 机械工程学报, 2012, 48(23): 167-177.
[3] 吕亮, 马平, 朱衡, 等. 水射流抛光去除函数对面形误差修正的影响[J]. 中国激光, 2016, 43(4): 0416003.
[4] 施春燕, 袁家虎, 伍凡, 等. 射流抛光误差分析与材料去除稳定性研究[J]. 光学学报, 2011, 31(1): 0112012.
[6] 方慧, 郭培基, 余景池. 液体喷射抛光技术材料去除机理的有限元分析[J]. 光学精密工程, 2006, 14(2): 218-223.
[7] 李兆泽. 磨料水射流抛光技术研究[D]. 长沙: 国防科技大学, 2011: 29- 32.
Li ZZ. Study on Abrasive Jet Polishing Technology[D]. Changsha: National University of Defense Technology, 2011: 29- 32.
[8] 施春燕, 袁家虎, 伍凡, 等. 冲击角度对射流抛光中材料去除面形的影响分析[J]. 光学学报, 2010, 30(2): 513-517.
[11] 方慧, 郭培基, 余景池. 液体喷射抛光材料去除机理的研究[J]. 光学技术, 2004, 30(2): 248-250.
[13] 郭烈锦. 两相与多相流动力学[M]. 西安: 西安交通大学出版社, 2002: 340- 360.
Guo LJ. Two phase and multiphase fluid dynamics[M]. Xi'an: Xi'an Jiaotong University Press, 2002: 340- 360.
[15] Oka Y I, Yoshida T. Practical estimation of erosion damage caused by solid particle impact: part 2: mechanical properties of materials directly associated with erosion damage[J]. Wear, 2005, 259(1): 102-109.
Article Outline
孙鹏飞, 张连新, 李建, 王中昱, 周涛. 射流抛光中抛光液黏度对材料去除函数的影响[J]. 光学学报, 2018, 38(12): 1222003. Pengfei Sun, Lianxin Zhang, Jian Li, Zhongyu Wang, Tao Zhou. Influence of Polishing Slurry Viscosity on the Material Removal Function for Fluid Jet Polishing[J]. Acta Optica Sinica, 2018, 38(12): 1222003.