多层薄膜沉积的应力仿真分析
下载: 2643次
1 引言
薄膜在半导体工业中的应用非常广泛。薄膜在沉积过程中会产生薄膜应力,进而引起很多问题,如会改变薄膜的电阻率[1],改变波导中光的模式[2],应力过大还会引起芯片开裂等。因此,分析薄膜沉积过程中的应力,对分析器件的可靠性,研究应力对器件功能的影响,优化薄膜沉积工艺,以及控制薄膜应力具有重要的意义。多层薄膜沉积过程中,各层膜之间会相互影响,应力分析较复杂。多层薄膜的应力包括本征应力和热应力,王锡明等[3-4]对多层膜的热应力进行了建模与计算,但这些模型经过了很多简化,且计算复杂。有限元分析被学者们广泛应用于薄膜的应力研究中[5-7],但主要是用于分析单层膜的热应力,不包括本征应力,对多层膜应力进行有限元分析的研究鲜有报道。本文基于工程实际应用,采用有限元方法建立了一种多层薄膜应力分析的模型,分析了多层薄膜在每个沉积阶段中的应力,包括本征应力和热应力。
2 薄膜应力
薄膜应力按照产生的根源分为热应力和本征应力。热应力由薄膜与基底材料的热膨胀系数差异和沉积前后温度差异决定,热应力公式为
式中
本征应力的产生机理比较复杂[8],其中一个典型的观点认为,本征应力是由晶格失配引起的。晶格失配产生
式中
3 多层薄膜应力数值模拟
3.1 热应力模拟
采用有限元法分析薄膜的热应力,应力方程为
式中
借助成熟的商业有限元分析软件,可以很方便地获得热应力。
3.2 本征应力模拟
对于某个给定的沉积条件,本征应力是可重复的,即在给定的沉积条件下,(2)式中
式中
(4)式和(2)式具有相同的表达形式,因此可以采用(3)式对(4)式进行数值模拟。引入本征应力系数后,可借助热应力的有限元分析程序分析本征应力。
本征应力系数采用试验和模拟相结合的方法获得,在特定沉积条件下,在纯基底上沉积一层膜,冷却至室温(293 K),测出基底的曲率变化[10-11],该曲率变化为温度从沉积温度降至293 K引起的热变形和本征应力引起的变形的叠加,如
本征应力与晶格结构相关,而晶格结构与基底晶态[12]、沉积速率[13]、沉积工艺[14]等因素相关,因此,本征应力系数的使用条件应与测试条件一致。
3.3 材料生长应力模型
应力在多层膜生长过程中是不断变化的,各层膜的应力是相互影响的。用有限元分析方法模拟生长过程中的应力时,涉及到材料加减问题。采用生死单元技术可以模拟材料的加减,先建立包含所有材料的有限元模型,然后“杀死”部分单元,在后续的分析中,逐步激活所需要的死单元。但是,多层膜的沉积过程是一个大变形过程,采用生死单元技术模拟时,被“杀死”的单元会因活单元的变形而严重扭曲,因此该生死单元技术不适用于多层膜沉积过程的模拟。
初始应力分析技术可以解决此问题。在上一层膜应力分析完成后,保存应力分析结果,更新模型,保持模型节点编号不变,然后在更新的模型上再增加下一层膜的模型,将上一层膜的应力分析结果作为包含下一层膜模型的应力分析的初始应力条件。
3.4 多层膜应力分析流程
包含本征应力和热应力的多层膜应力分析流程如
4 工程实例
试验所用芯片截面如
采用有限元分析软件,用多层膜应力分析流程进行应力分析。基于芯片的结构特点,采用广义平面应变模型进行建模。沉积的掺锗二氧化硅薄膜经过大面积刻蚀后,掺锗二氧化硅薄膜产生的应力得到释放,故可以不单独分析这层膜,把波导芯层和BPSG一起建模。二氧化硅膜和BPSG膜都经历过高温退火,故不用考虑膜的本征应力。
分析中用到的材料参数见
钛金属膜需要考虑本征应力,通过试验测定单层膜晶圆曲率变化,并结合有限元分析方法,可得到本征应力系数,分析中使用的本征应力系数为1.4×10-3 K-1,假设温度降低0.1 K。
表 1. 硅的材料参数
Table 1. Material parameters of Si
|
表 2. SiO2的材料参数
Table 2. Material parameters of SiO2
|
表 3. 钛、氮化硅和BPSG的材料参数
Table 3. Material parameters of titanium, SiNx, and BPSG
|
分析过程如下:
1) 双面氧化的硅基板在1293 K温度下退火,初始处于零应力状态, “杀死”BPSG单元,冷却至723 K;
2) BPSG膜在723 K温度下退火,设BPSG在退火后处于零应力状态,激活BPSG单元,冷却至室温293 K;
3) 增加钛膜,设置钛的热膨胀系数为本征应力系数,初始化应力,然后温度降低0.1 K;
4) 更新钛的热膨胀系数为钛的实际热膨胀系数,初始化应力,升温至593 K;
5) 增加氮化硅层,初始化应力,冷却至室温293 K。
分析得到多层薄膜在各沉积阶段应力分布如
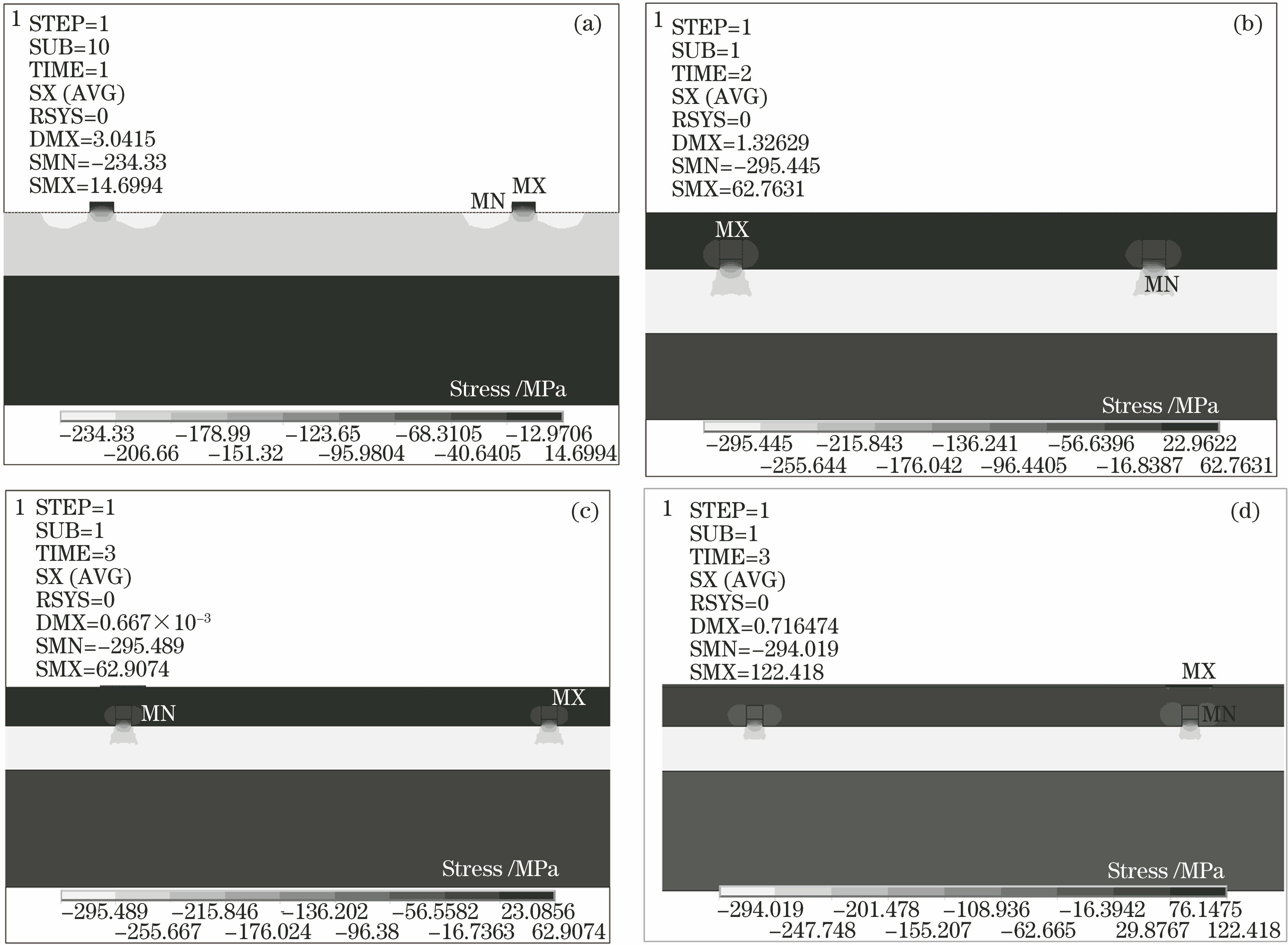
图 5. 多层薄膜在各沉积阶段的应力分布。(a)氧化生成SiO2膜;(b)沉积BPSG膜;(c)沉积钛膜;(d)沉积氮化硅膜
Fig. 5. Stress distribution of multilayer films at each deposition stage. (a) Oxidized SiO2 films; (b) BPSG deposition film; (c) titanium deposition film; (d) SiNx deposition film
5 结论
提出了一种薄膜本征应力的模拟方法,对多层薄膜沉积过程中的热应力和本征应力进行了数值仿真分析。通过引入与材料热膨胀系数相当的本征应力系数,借助现有的热应力有限元分析程序,模拟了薄膜的本征应力,采用模型重构-应力初始化的方法模拟了材料增长,建立了一种多层薄膜应力分析模型。利用该方法对一种多层薄膜芯片进行了应力分析,结果表明,该方法可以连续得到多层薄膜在各个沉积阶段的本征应力和热应力。
[1] 唐武, 邓龙江, 许可为, 等. 金属薄膜电阻率与表面粗糙度、残余应力的关系[J]. 稀有金属材料与工程, 2008, 37(4): 617-620.
Tang W, Deng L J, Xu K W, et al. Relationship between resistivity of metallic film and its surface roughness, residual stress[J]. Rare Metal Materials and Engineering, 2008, 37(4): 617-620.
[3] 王锡明, 王军军, 周嘉. 多层薄膜微结构热应力计算[J]. 微细加工技术, 2007, 2(2): 20-23.
Wang X M, Wang J J, Zhou J. Calculation of thermal stress in microstructure fabricated by multilayer thin films[J]. Microfabrication Technology, 2007, 2(2): 20-23.
[4] 陈焘, 罗崇泰, 王多书. 多层薄膜热应力研究[J]. 真空科学与技术学报, 2006, 26(z1): 6-8.
Chen T, Luo C T, Wang D S. Theoretical study of multilayer thermal stresses[J]. Chinese Journal of Vacuum Science and Technology, 2006, 26(z1): 6-8.
[5] 董位, 左然, 赖晓慧, 等. 蓝宝石基GaN薄膜的热应力模拟分析[J]. 激光与光电子学进展, 2013, 50(7): 073101.
[6] 张耀平, 张云洞, 凌宁, 等. 薄膜残余应力有限元分析研究[J]. 激光与光电子学进展, 2005, 42(10): 23-26.
[7] 王小增. Al2O3衬底上GaN薄膜热应力和变形极差分析[J]. 激光与光电子学进展, 2015, 52(4): 041602.
[8] 陈焘, 罗崇泰. 薄膜应力的研究进展[J]. 真空与低温, 2006, 12(2): 68-73.
Chen T, Luo C T. The research progress of thin film stress[J]. Vacuum and Cryogenics, 2006, 12(2): 68-73.
[10] 范瑞瑛, 范正修. 薄膜应力分析及一些测量结果[J]. 光学仪器, 2001, 23(5/6): 84-91.
Fan R Y, Fan Z X. Stress analysis of thin films and some testing results[J]. Optical Instruments, 2001, 23(5/6): 84-91.
[12] 郭佳露, 刘晓凤, 赵元安, 等. 基底晶态对HfO2薄膜晶向结构和力学特性的影响[J]. 中国激光, 2016, 43(6): 0603001.
[13] 赵娇玲, 贺洪波, 王虎, 等. 沉积速率对直流脉冲溅射钼薄膜微结构与光学性能的影响[J]. 光学学报, 2016, 36(9): 0931001.
[14] 肖和平, 孙如剑, 马祥柱, 等. PECVD法制备SiO2薄膜致密性的特性[J]. 激光与光电子学进展, 2016, 53(12): 123101.
李长安, 杨明冬, 全本庆, 关卫林. 多层薄膜沉积的应力仿真分析[J]. 激光与光电子学进展, 2018, 55(4): 043101. Chang'an Li, Mingdong Yang, Benqing Quan, Weilin Guan. Stress Simulation Analysis of Multilayer Film Deposition[J]. Laser & Optoelectronics Progress, 2018, 55(4): 043101.