激光视觉传感系统的电弧增材制造侧表面成形分析
下载: 984次
1 引言
电弧增材技术具有低成本、高效率、高致密性等优点,在汽车、船舶、航空航天、**等领域得到了广泛应用[1]。电弧增材技术是一种以电弧为热源,焊丝为原材料,将焊丝快速熔化成高温液态金属,并以熔滴过渡的方式层状堆积成形的技术[2-4]。针对堆积过程中的热积累、散热条件差、熔池过热等问题,研究者在电弧增材过程中引入主动冷却技术来减少堆积层的热积累,提高堆积层的成形质量和效率[5]。为研究不同焊接参数对多层单道薄壁件表面粗糙度的影响,设计研究方案,量化电弧增材制造的表面粗糙度[6],对多层多道焊缝的成形过程进行数学建模,通过控制堆积层的成形尺寸获得最佳成形效果下的焊接参数[7]。
利用视觉传感技术可检测焊接状态及焊缝成形质量[8],而激光视觉传感技术是通过激光条纹的变形来获取焊缝形态信息的[9],可有效保证接头质量[10],实现焊接自动化。在电弧增材技术的发展过程中,研究者利用激光视觉传感技术,提出一种基于遗传算法的平面焊缝特征提取方法,该方法能够迭代地剔除噪声,快速获取激光条纹的准确位置和焊缝特征点坐标[11]。针对坡口及焊缝表面提出一种基于激光视觉传感的三维轮廓测量方法,该方法可实现坡口及焊缝表面三维轮廓的实时测量,准确率较高[12]。采用基于激光视觉传感的三维重建技术对焊缝熔高和角变形等信息进行提取和质量评估,可实现对焊缝形状特征的定量(深度图和等高线图)和定性评价[13]。
研究者大多利用图像处理技术提取焊缝堆积层的表面特征,或者使用激光视觉传感系统对焊缝进行三维重建,较少对提取后的三维点云进行相关数据处理。本文使用激光视觉传感系统对电弧增材制造堆积层的侧表面进行三维重建,重点研究堆积层侧表面三维形状的特征提取和表面粗糙度的量化方法。相较于焊缝轮廓的二维分析方法,三维点云处理方法能够更加直观、具体地对焊缝表面进行描述,为电弧增材制造表面成形检测和量化分析提供新方法。
2 电弧增材实验及成形测量
2.1 电弧增材实验
实验中采用熔化极气体保护焊接,装置如
表 1. 平板堆焊实验参数
Table 1. Experimental parameters of flat welding
|
2.2 堆积层侧表面成形测量
堆积层侧表面成形检测装置如
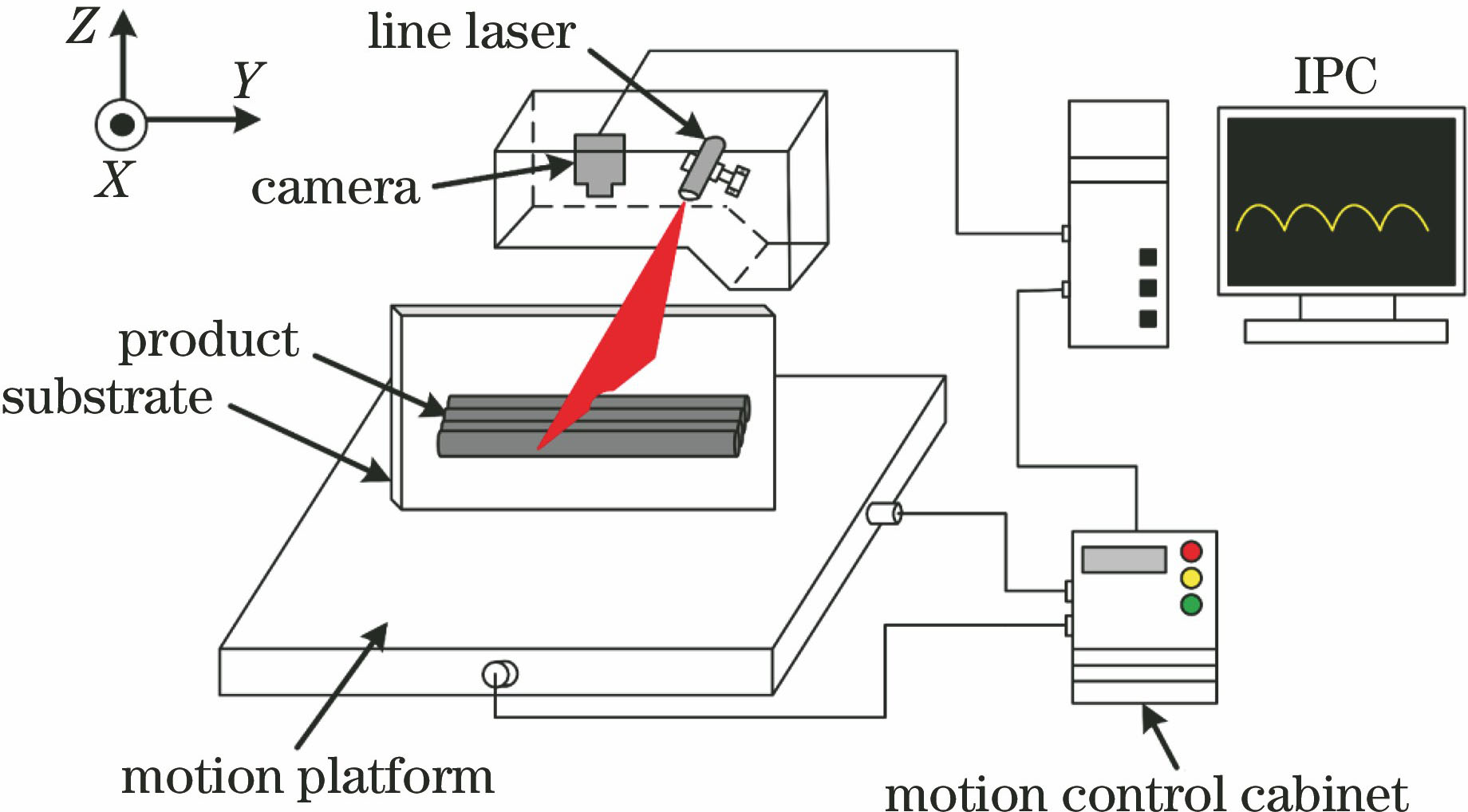
图 2. 堆积层侧表面成形检测装置示意图
Fig. 2. Diagram of surface forming measurement device on the side of deposition layer
2.3 测量系统标定实验
为实现堆积层侧表面的三维重建,必须对激光视觉传感器进行标定,建立图像坐标与世界坐标的转换关系,即图像像素偏差与实际空间位置偏差之间的关系。激光视觉传感器扫描过程中相机始终垂直于待测轮廓表面,在保证标定精度符合三维测量精度要求的前提下可以采用锯齿靶标线性标定法[14]。如
将锯齿靶标固定于运动平台上,
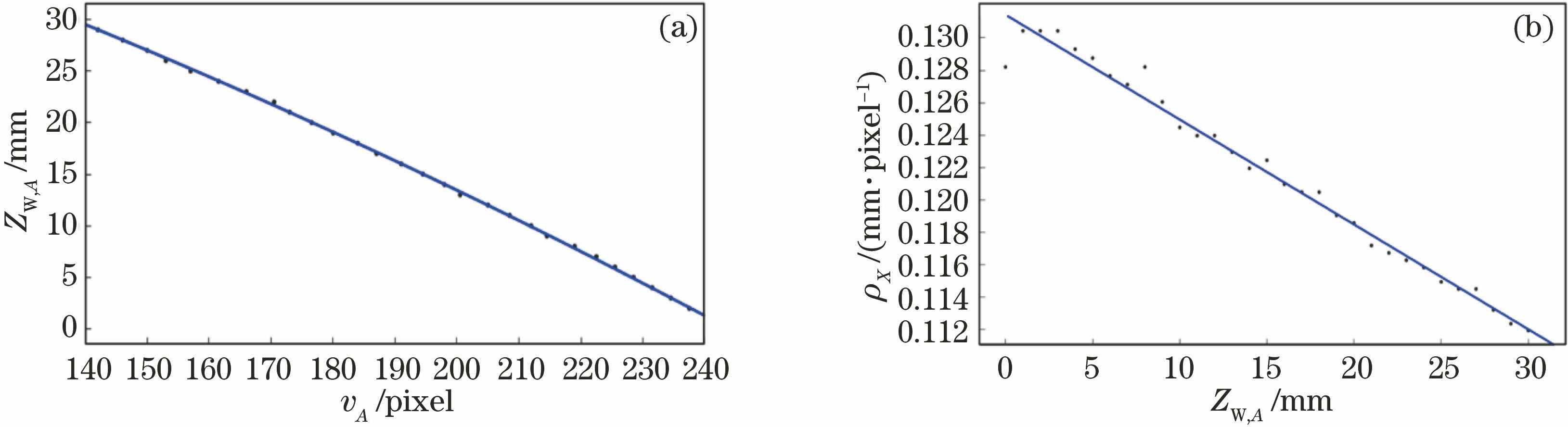
图 5. 多项式拟合曲线。(a) Z W,A 与vA 二次拟合曲线;(b) ρX 与Z W,A 线性拟合曲线
Fig. 5. Polynomial fitting curves. (a) Quadratic fitting curve of Z W,A and vA (b) linear fitting curve of ρZ and Z W,A
由于相机出现畸变,
为获得激光视觉传感系统的测量精度,对扫描后的标准锯齿靶标进行三维重建,结果如
表 2. 锯齿靶标重复性测量结果
Table 2. Repeated temperature measurement of sawtooth target
|
3 图像及三维数据处理
3.1 激光条纹图像像素坐标提取
激光条纹图像像素提取流程如
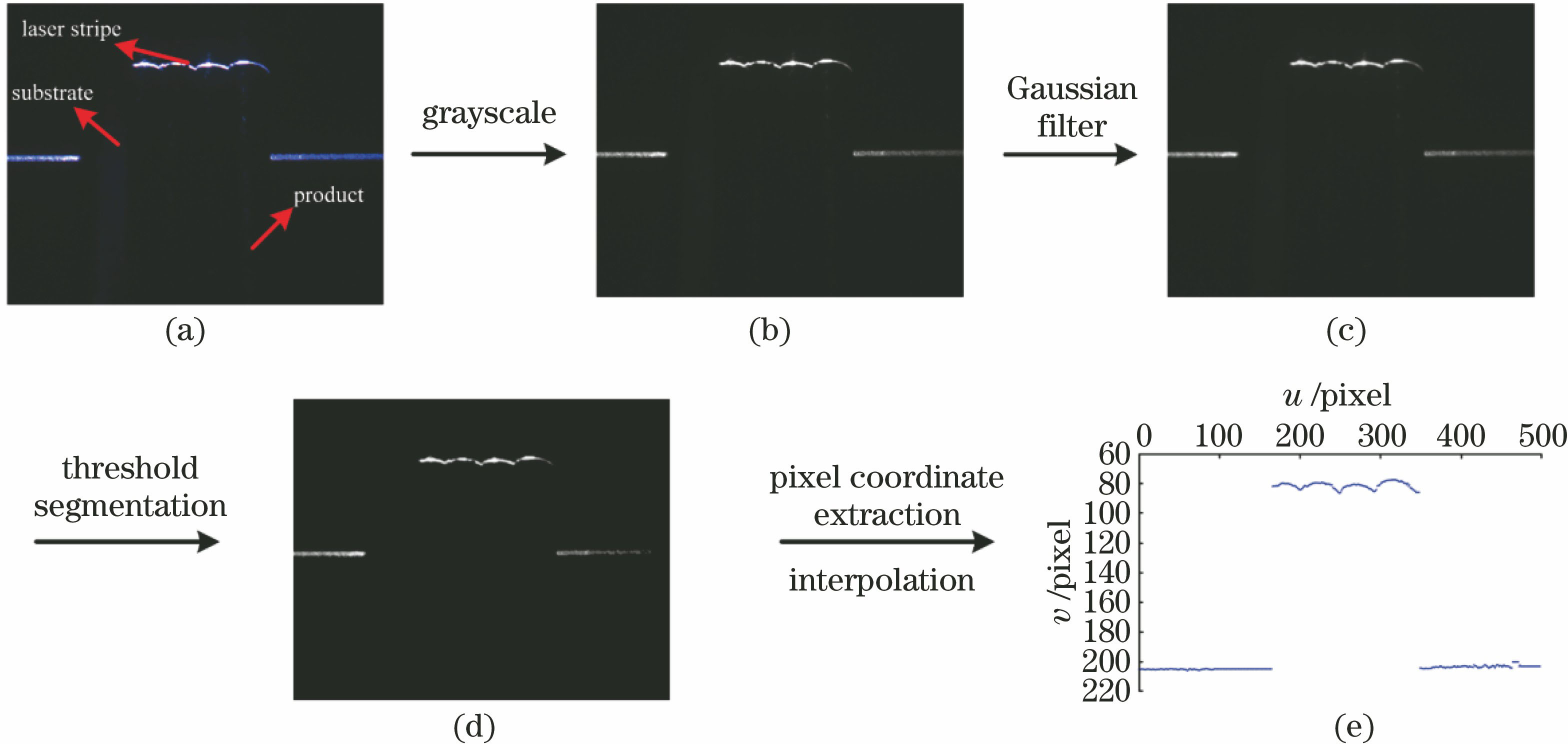
图 7. 像素坐标提取流程图。(a)原始图像;(b)灰度图;(c)高斯滤波;(d)阈值分割;(e)像素坐标提取
Fig. 7. Flow chart of pixel coordinate extraction. (a) Original image; (b) grayscale image; (c) Gaussian filter; (d) threshold segmentation; (e) pixel coordinate extraction
1) 对预处理后的图像进行逐列扫描,寻找每一列中灰度值最大的像素点坐标,并将其设为(
2) 利用灰度重心公式求得激光条纹中心线第
3) 逐列扫描时,使用最近邻插值修复条纹断点,最终的提取结果如
3.2 堆积层侧表面三维信息处理
以
RANSAC(Random Sample Consensus)点云分割算法可以有效分割出三维点云中的平面[16],其基本思想是针对具体问题设计出一个判断准则(此处为平面模型),通过选取合适的距离阈值迭代剔除与平面模型参数不一致的点云。使用C++开发语言并结合PCL算法库,从原始的堆积层三维点云中分割底部平面。设置距离阈值为5 mm,最大迭代次数为10000次,剔除无效的点云信息。迭代完成后提取出的点云平面如
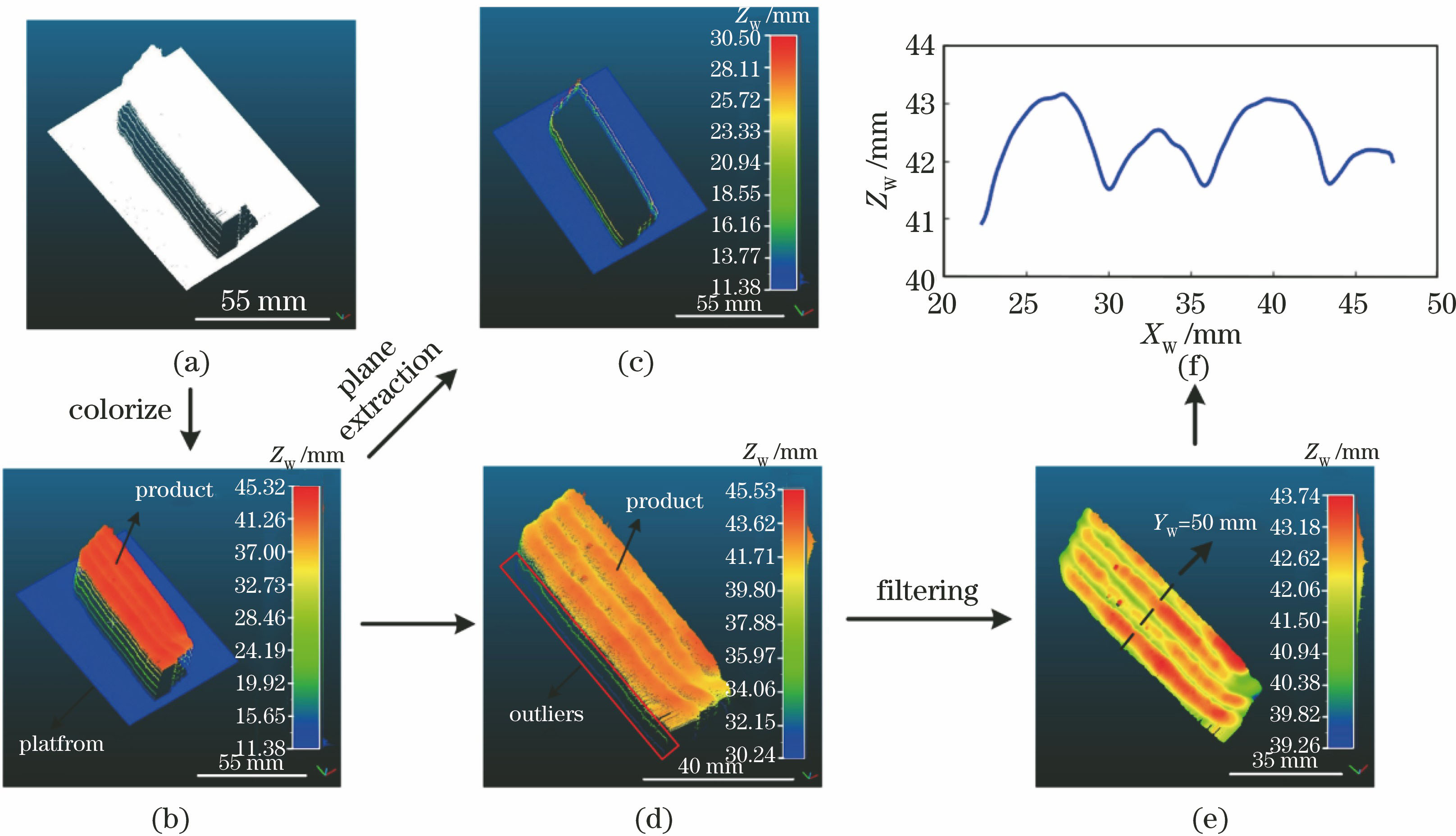
图 8. Z as=6 mm时焊缝侧表面三维数据处理流程图。(a)原始点云;(b)深度渲染;(c)点云分割平面;(d)未去噪堆积层侧表面;(e) KNN滤波;(f) Y w=50 mm处的横截面轮廓
Fig. 8. Flow chart of 3D data processing of weld side surface when Z as= 6 mm. (a) Original point data; (b) deep rendering; (c) point cloud segmentation plane; (d) side surface of deposition layer with noise; (e) KNN filtering; (f) cross-sectional profile when Y w=50 mm
不同
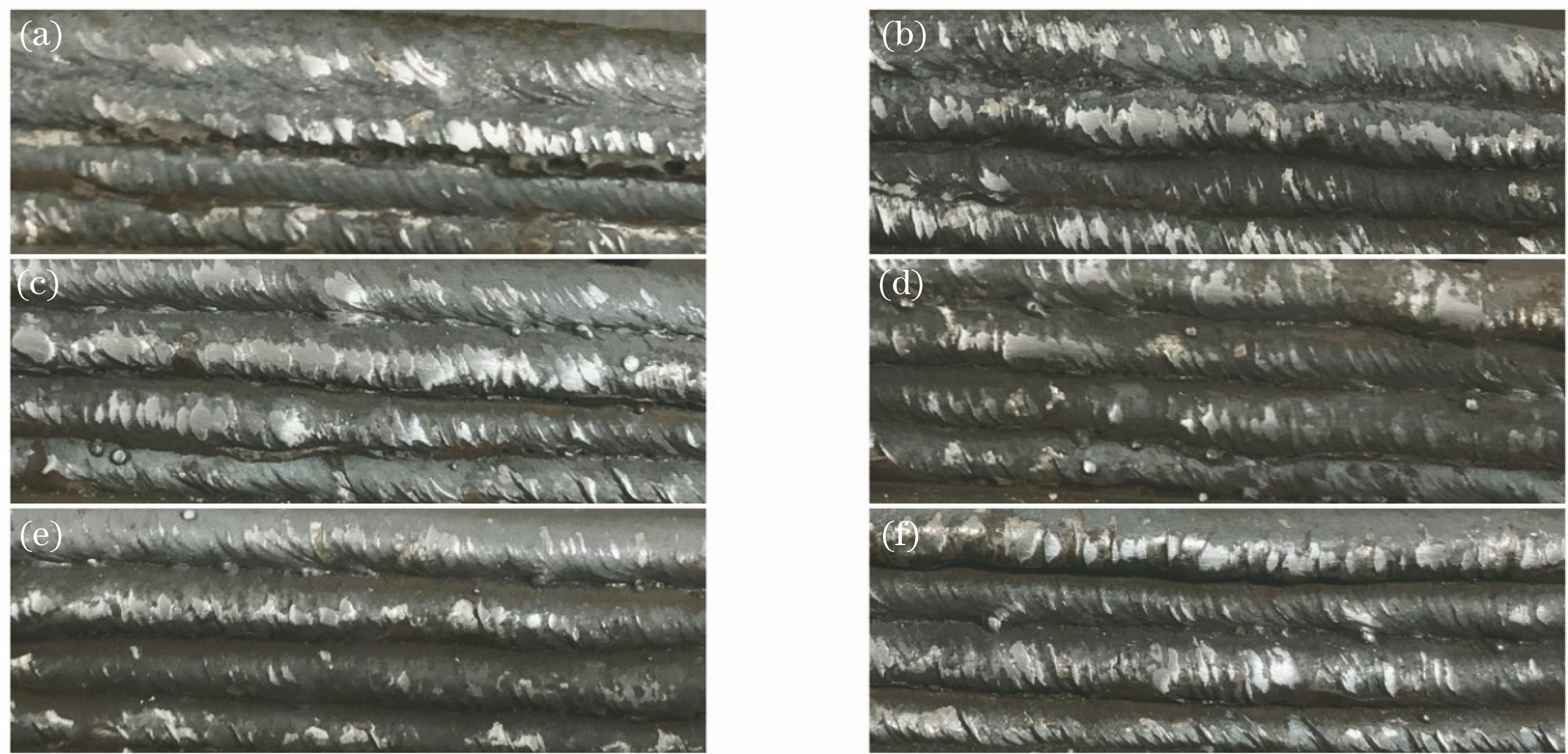
图 9. 不同焊接参数下堆积层侧表面实物图。 (a) Z as=3 mm;(b) Z as=4 mm;(c) Z as=5 mm;(d) Z as=6 mm;(e) Z as=7 mm;(f) Z as=8 mm
Fig. 9. Side surface physical maps of the deposition layers under different welding parameters. (a) Z as=3 mm; (b) Z as =4 mm; (c) Z as=5 mm; (d) Z as=6 mm; (e) Z as=7 mm; (f) Z as=8 mm
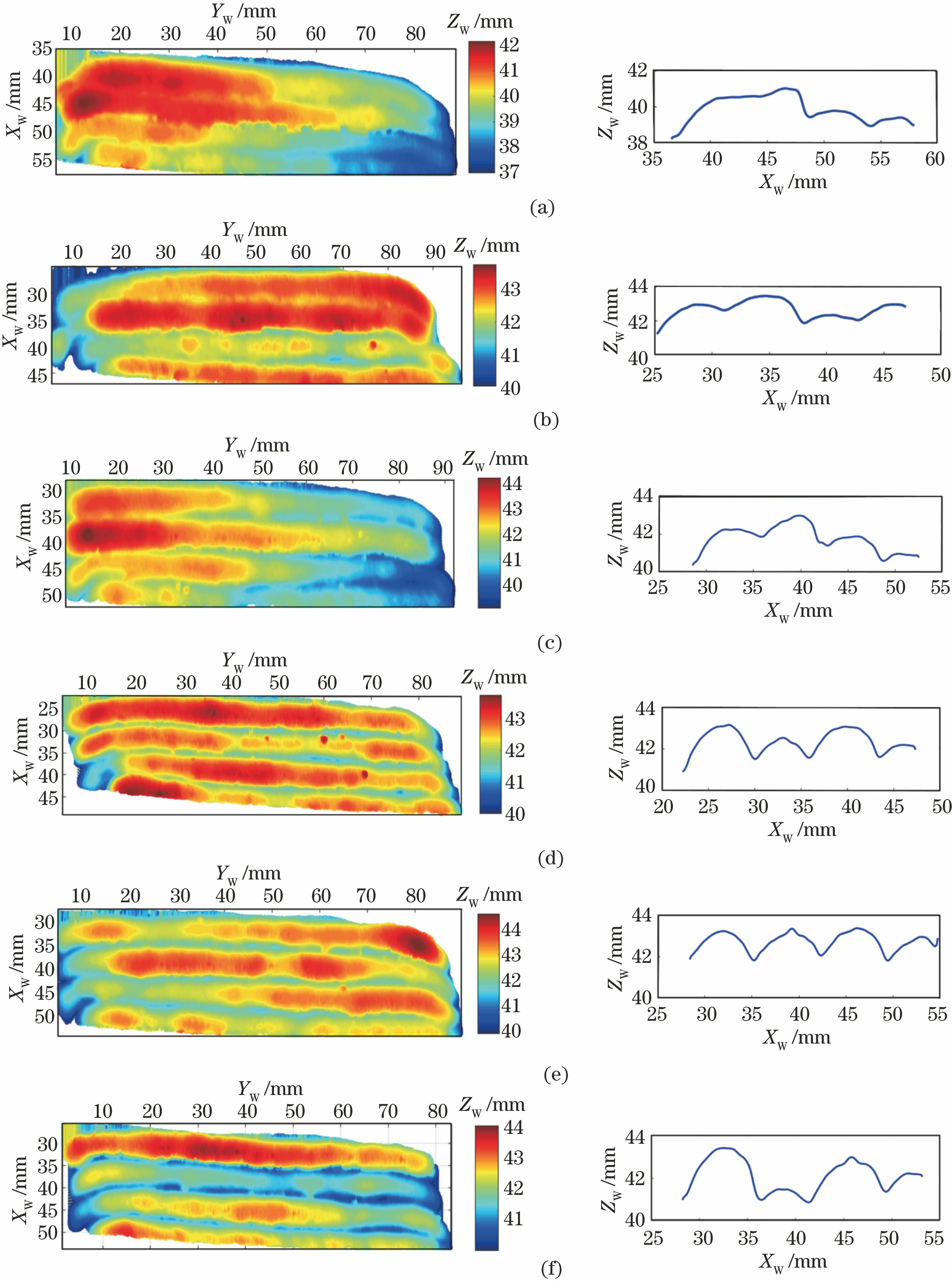
图 10. 不同焊接参数下堆积层侧表面深度图。(a) Z as=3 mm;(b) Z as=4 mm;(c) Z as=5 mm;(d) Z as=6 mm;(e) Z as=7 mm;(f) Z as=8 mm
Fig. 10. Side surface depth maps of deposition layers under different welding parameters. (a) Z as=3 mm;(b) Z as=4 mm; (c) Z as=5 mm; (d) Z as=6 mm; (e) Z as=7 mm; (f) Z as=8 mm
当
3.3 堆积层侧表面粗糙度测量
堆积层侧表面的粗糙度可在一定程度上反映堆积层的表面成形质量,为堆积层质量评价提供了量化标准[6]。粗糙度测量原理如
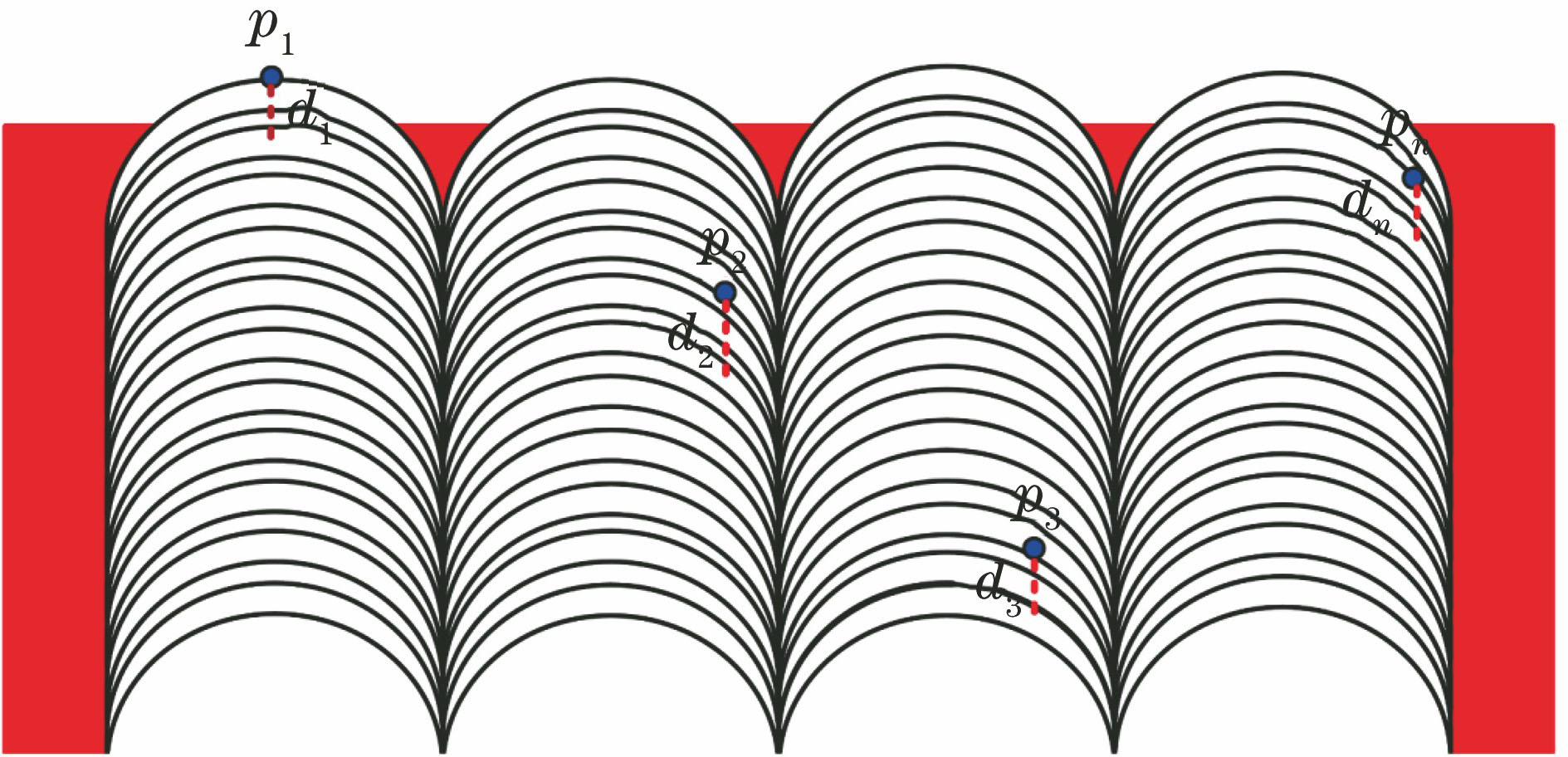
图 11. 堆积层侧表面粗糙度测量原理图
Fig. 11. Measurement schematic of side surface roughness of deposition layer
由于起弧和收弧时,电弧电流稳定性不是受
表 3. 不同焊接条件下堆积层侧表面粗糙度
Table 3. Surface roughness of the deposition layer under different welding conditions
|
4 结论
通过激光视觉传感系统对电弧增材侧表面进行三维重建,使用锯齿靶标的线性标定方法将三维重建误差控制在0.2 mm以内,采用基于统计概率思维的三维点云处理算法提取并分析堆积层侧表面的三维特征,通过堆积层侧表面的三维点云视图以及表面粗糙度定性和定量分析电弧增材侧表面的三维成形情况。改变焊丝末端与板材间距会引起电弧增材侧表面的三维成形及粗糙度变化,距离过大或者过小都会引起层间分布不均匀,表面粗糙度增加。
[1] 周祥曼, 田启华, 杜义贤, 等. 电弧增材成形单道两层熔积过程中的晶粒生长模拟[J]. 机械工程学报, 2018, 54(22): 86-94.
[2] 冯毅, 张鹏贤, 贾金龙. 近两年丝材+电弧增材制造研究进展[J]. 热加工工艺, 2018, 47(21): 23-26.
[3] 熊俊, 薛永刚, 陈辉, 等. 电弧增材制造成形控制技术的研究现状与展望[J]. 电焊机, 2015, 45(9): 45-50.
[4] 杨海欧, 王健, 周颖惠, 等. 电弧增材制造技术及其在TC4钛合金中的应用研究进展[J]. 材料导报, 2018, 32(11): 1884-1890.
[8] 高向东, 龙观富, 汪润林, 等. 大功率盘形激光焊飞溅特征分析[J]. 物理学报, 2012, 61(9): 098103.
[10] 黄怡洁, 高向东, 林少铎. 激光焊接参数对有机玻璃与不锈钢接头力学性能的影响[J]. 中国激光, 2017, 44(12): 1202006.
[11] 张斌, 常森, 王桔, 等. 基于遗传算法的激光视觉焊缝特征点提取[J]. 中国激光, 2019, 46(1): 0102001.
[12] 张鹏贤, 张国强, 韦志成, 等. 坡口及焊缝表面三维轮廓的激光视觉测量[J]. 焊接学报, 2017, 38(12): 85-89.
[14] 王文超, 高向东, 丁晓东, 等. 无坡口对接焊缝特征角点检测方法[J]. 焊接学报, 2018, 39(9): 61-64.
[15] CloudCompare. 3D point cloud and mesh processing software open source project[Z/OL]. [2019-05-01].http:∥www.danielgm.net/.
[16] 黄凯, 程效军, 贾东峰, 等. 一种密集管道点云数据自动分割算法[J]. 中国激光, 2018, 45(11): 1104004.
Article Outline
马波, 高向东, 黄怡洁, 张艳喜, 游德勇, 张南峰. 激光视觉传感系统的电弧增材制造侧表面成形分析[J]. 中国激光, 2019, 46(11): 1102005. Bo Ma, Xiangdong Gao, Yijie Huang, Yanxi Zhang, Deyong You, Nanfeng Zhang. Side-Surface-Form Analysis of Arc Additive Manufacturing Based on Laser Vision Sensing System[J]. Chinese Journal of Lasers, 2019, 46(11): 1102005.