激光重熔A356铝合金表面的力学性能
下载: 1204次
1 引言
相对于传统的铁基合金,铝合金具有非常优异的性能,如较小的密度、相对较好的耐腐蚀性及导热性。A356铝合金常被用于铸造铝合金轮毂、发动机缸体等。由于铝合金的硬度较低,其耐磨性不能满足许多应用场合的要求[1],因此对铝合金表面进行强化处理是必不可少的。目前,已有很多激光表面强化技术,如表面激光重熔[2]、激光表面合金化[3]、激光喷丸强化[4]以及激光熔覆[5]等。
近些年来,许多研究人员采用不同的工艺在铝合金表面制备了一层硬质材料保护层。如:雷临苹等[6]采用脉冲Nd∶YAG激光器在6061铝合金表面制备了NiAl合金涂层和NiAl/Al2O3-TiO2复合涂层,这两种涂层中均形成了硬质相,提高了合金的耐磨性及显微硬度;Biswas等[7]将Cu-Fe熔覆于铝合金表面制备了熔覆层,其硬度可达600 HV0.025。然而这种硬质涂层普遍存在涂层与基板结合能力较弱的缺陷。虽然在激光熔覆过程中硬质涂层与基板之间形成了冶金结合,但是由于涂层与基体材料性能的差别较大,它们的冶金结合能力并不是很强,在实际工况中使用时会产生涂层剥落的现象。最近,Pakieła等[8]通过对AlMg5Si2Mn铝合金进行激光重熔处理,使铝合金获得了更好的力学性能。
表面强化技术必然会使试件表面出现分层现象,因此,评估激光重熔强化层的力学性能是相当复杂的。Sharma等[9]指出,弯曲强度是衡量表面力学性能最重要的指标之一,同时也是最为有效的一种指标。通过弯曲试验可以准确检测出引起表面强化层中第一裂纹出现的载荷或应力,同时还可以检测表面强化层是否与基体发生分离,因此,弯曲试验可以为表面强化层力学性能的表征提供有效数据。Kadolkar等[10]指出,使表面强化层中出现第一裂纹的载荷为临界载荷,它决定了表面强化层的内聚强度。随后的负载可能通过分层或深入基板的裂缝的扩展导致表面强化层破裂,表面强化层的破裂类型取决于表面强化层与基体界面的力学性能。
目前,在A356铸态铝合金表面强化的研究中,利用弯曲强度评估激光重熔强化层与基体结合能力的研究相对较少,因此,本文利用三点弯曲试验评估了A356铸态铝合金激光重熔后的表面力学性能,为A356铸造铝合金的表面激光重熔处理提供相关理论支持,以促进弯曲性能在评估激光重熔表面力学性能上的应用。
2 基本原理
2.1 试验材料
选择用于该研究的基材是由中信戴卡股份有限公司提供的A356铸造轮毂铝合金,其化学成分如
表 1. A356铝合金的化学成分
Table 1. Chemical composition of A356 aluminum alloy
|
2.2 试样的制备
从10 mm厚的铸造板上线切割出尺寸为50 mm×25 mm×10 mm的试样。首先使用超声波清洗机在水中清洗试样10 min,然后用砂纸将试样切割表面打磨平整,将试样浸泡于质量分数为3%的HCl溶液中,清洗其表面的氧化膜;接着,使用丙酮溶液清除试样表面的油酯,最后用墨水对试样表面进行黑化处理。
2.3 激光重熔处理
此次试验使用的激光器为CO2激光器。以3种不同的激光束功率(1000,1500,2000 W)在试样上进行激光重熔处理,制备表面强化层。激光在样品表面上具有均匀的光点尺寸(直径为3.0 mm)和恒定的移动速率(10 mm/s)。激光的能量密度通常被用于综合描述激光加工参数对熔覆层质量的影响[11]。能量密度E[12]的计算公式为
式中:P为激光束功率(W);v为激光束的行进速度(mm/s);ξ为光斑尺寸(mm)。因此,当激光束功率为1000,1500,2000时,能量密度分别为33.3,50.0,66.7 J/mm2。
2.4 试验测试
使用X射线衍射(XRD)技术研究重熔层中的相变,扫描速率为5 (°)/s,扫描范围2θ为10°~90°。
采用Regulus 8100扫描电子显微镜(SEM)表征重熔层的微观结构。横截面样品的制备:先用不同粒度的砂纸连续打磨,然后用金刚石研磨膏抛光,得到镜面抛光表面;然后用Keller试剂刻蚀抛光的样品。
使用Q10A+型显微硬度计在样品截面处测试显微硬度,加载载荷为1.96 N,保载时间为15 s。测试点位置如
在Inspekt
对4个试样进行弯曲试验,4个试样分别为在1000,1500,2000 W功率下制备的重熔层试样以及A356母材试样。试样的尺寸均为50 mm×15 mm×5 mm,所有样品均在相同的条件下进行三点弯曲测试,加载速度为1 mm/min,支撑长度为21 mm。数据的记录从试件受力开始至试件受力为其最大值(Fmax)的80%时结束。三点弯曲试验示意图如
3 分析与讨论
3.1 组织分析
3.1.1 微观组织形貌
如
式中:Tm为交点温度;σ为单位面积的自由能;Lm为熔化潜热;rk为临界晶核半径;ΔT为过冷度。根据(2)式可知临界晶核半径与过冷度成反比关系。由于激光重熔加工过程对金属表面产生了急热急冷作用,大大提高了金属凝固时的过冷度,从而减小了临界晶核半径,因此单位体积内的晶胚成核率大大提高,晶粒明显细化[13]。
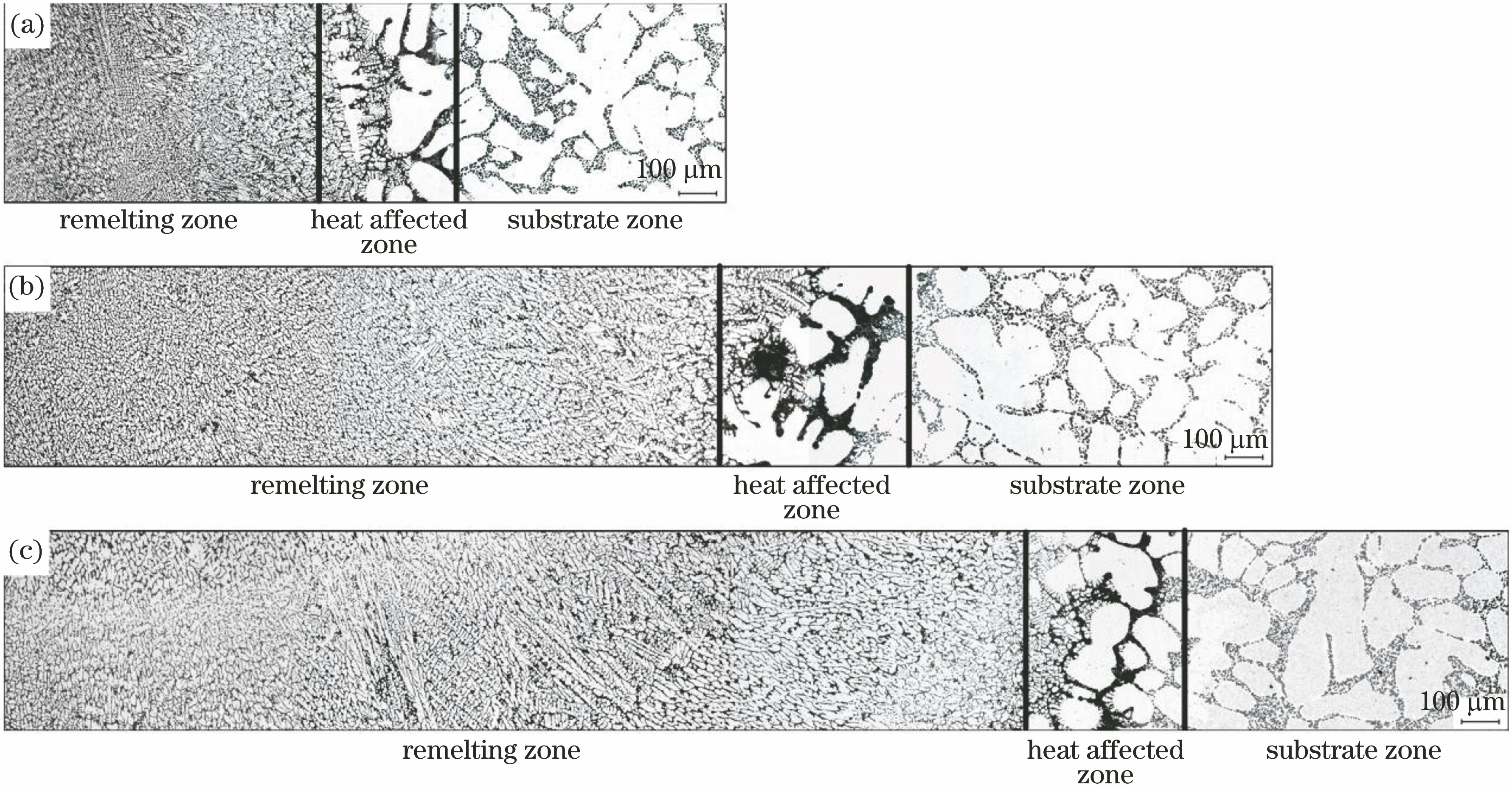
图 3. A356铝合金经过不同功率激光重熔处理后的显微组织全貌。(a) 1000 W;(b) 1500 W;(c) 2000 W
Fig. 3. Microstructures of A356 aluminum alloy after laser remelting treatment at different power. (a) 1000 W; (b) 1500 W; (c) 2000 W
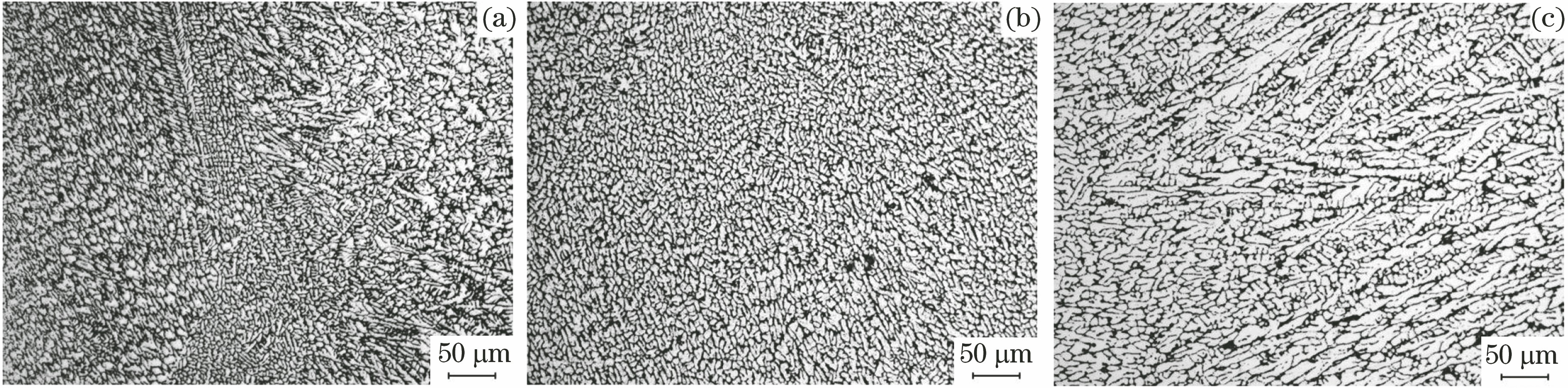
图 4. 不同激光功率下得到的重熔层的显微组织。(a) 1000 W;(b) 1500 W;(c) 2000 W
Fig. 4. Microstructures of remelting layer obtained at different laser power. (a) 1000 W; (b) 1500 W; (c) 2000 W
3.1.2 相分析
金相试验结果以及XRD、EDS数据显示,激光功率参数的变化只会引起晶粒尺寸的变化,不会导致物相发生变化。因此,在相分析过程中,特以2000 W激光功率下制备的试样作为例子进行分析。结合EDS测试结果及XRD测试结果可以发现,基材A356铝合金主要由α-Al相与Al-Si共晶相组成,其中Al-Si共晶相为第二相。
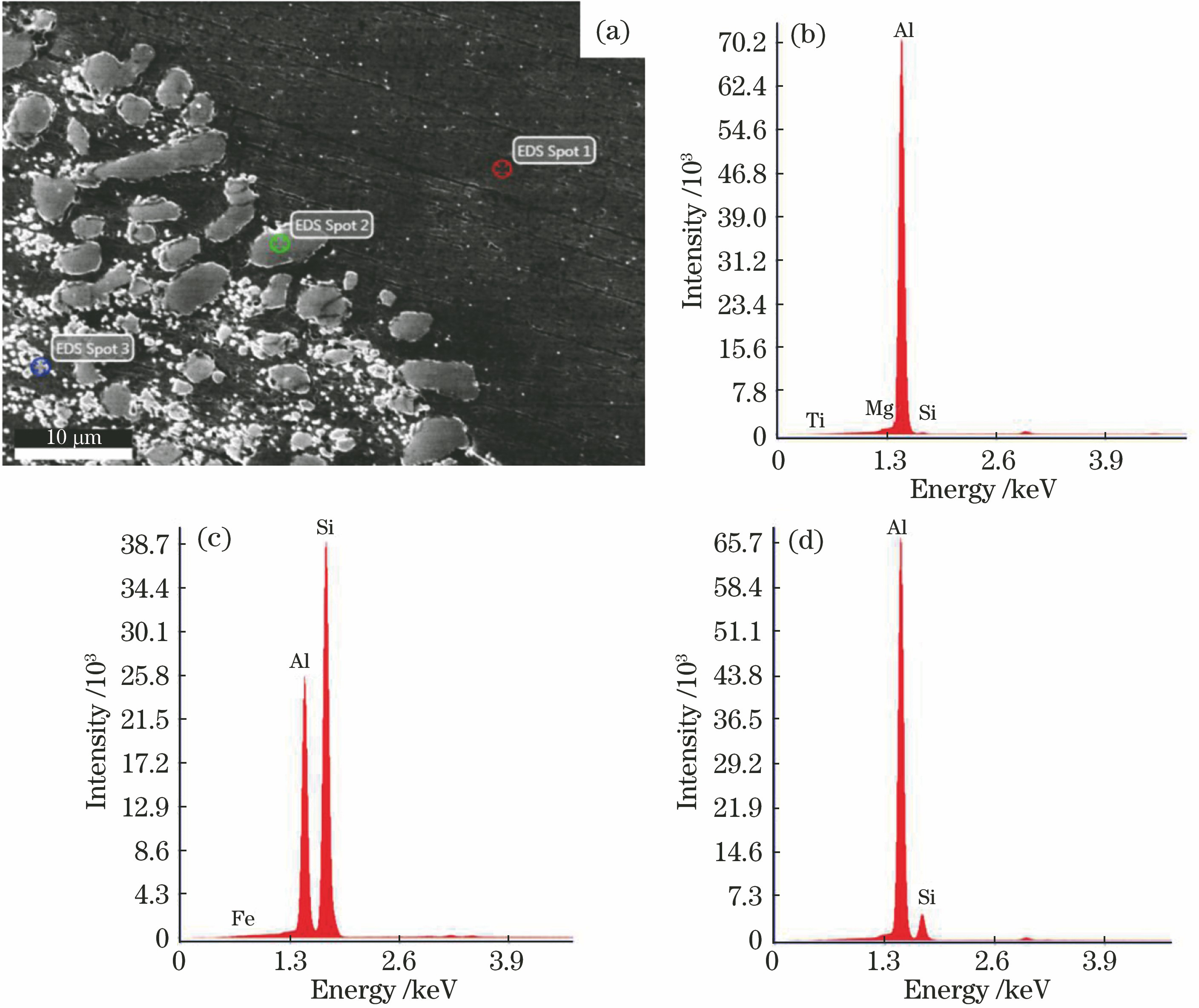
图 5. 基板区的EDS能谱图。(a) EDS测试点分布图;(b) Spot 1点的EDS能谱图;(c) Spot 2点的EDS能谱图;(d) Spot 3点的EDS能谱图
Fig. 5. EDS spectra of substrate area. (a) EDS test points distribution map; (b) EDS spectrum of Spot 1point; (c) EDS spectrum of Spot 2 point; (d) EDS spectrum of Spot 3 point
表 2. 基板区的EDS测试结果
Table 2. ESD results of substrate area
|

图 6. 2000 W激光功率下得到的重熔层的XRD图谱
Fig. 6. XRD patterns of remelting layer obtained at laser power of 2000 W
3.1.3 细晶强化及弥散强化
激光重熔后,铝合金表面组织的晶粒得到了细化,从而优化了铝合金的表面性能。利用截线法测得重熔层各区域组织的尺寸如
表 3. 不同激光功率下得到的重熔层中各相的尺寸
Table 3. Size of each phase in remelting layer obtained at different laser power
|
激光重熔后,铝合金表面的组织分布得较为均匀,达到了弥散强化的目的。如

图 7. 2000 W激光功率下得到的重熔层各区域的SEM图。(a)重熔区,×1000;(b)热影响区,×1000;(c)基板区,×1000;(d)重熔区,×3000;(e)热影响区,×3000;(f)基板区,×3000
Fig. 7. SEM images of each region in remelting layer obtained at laser power of 2000 W. (a) Remelting zone, ×1000; (b) heat affected zone, ×1000; (c) substrate zone, ×1000; (d) remelting zone, ×3000; (e) heat affected zone,×3000; (f) substrate zone, ×3000
3.1.4 显微硬度
在金相照片中可以看到A356铝合金中两种相的尺寸相差较大。在基板区的显微硬度测试过程中发现,Al-Si共晶相聚集处的硬度高于α-Al相聚集处的,对Al-Si共晶相聚集处的硬度进行测量后得到其显微硬度值为65 HV0.2,对α-Al相聚集处进行测量后得到其显微硬度值为35 HV0.2。但是由于Al-Si共晶相在基板区不均匀分布,因此,基板区的硬度较低。
由
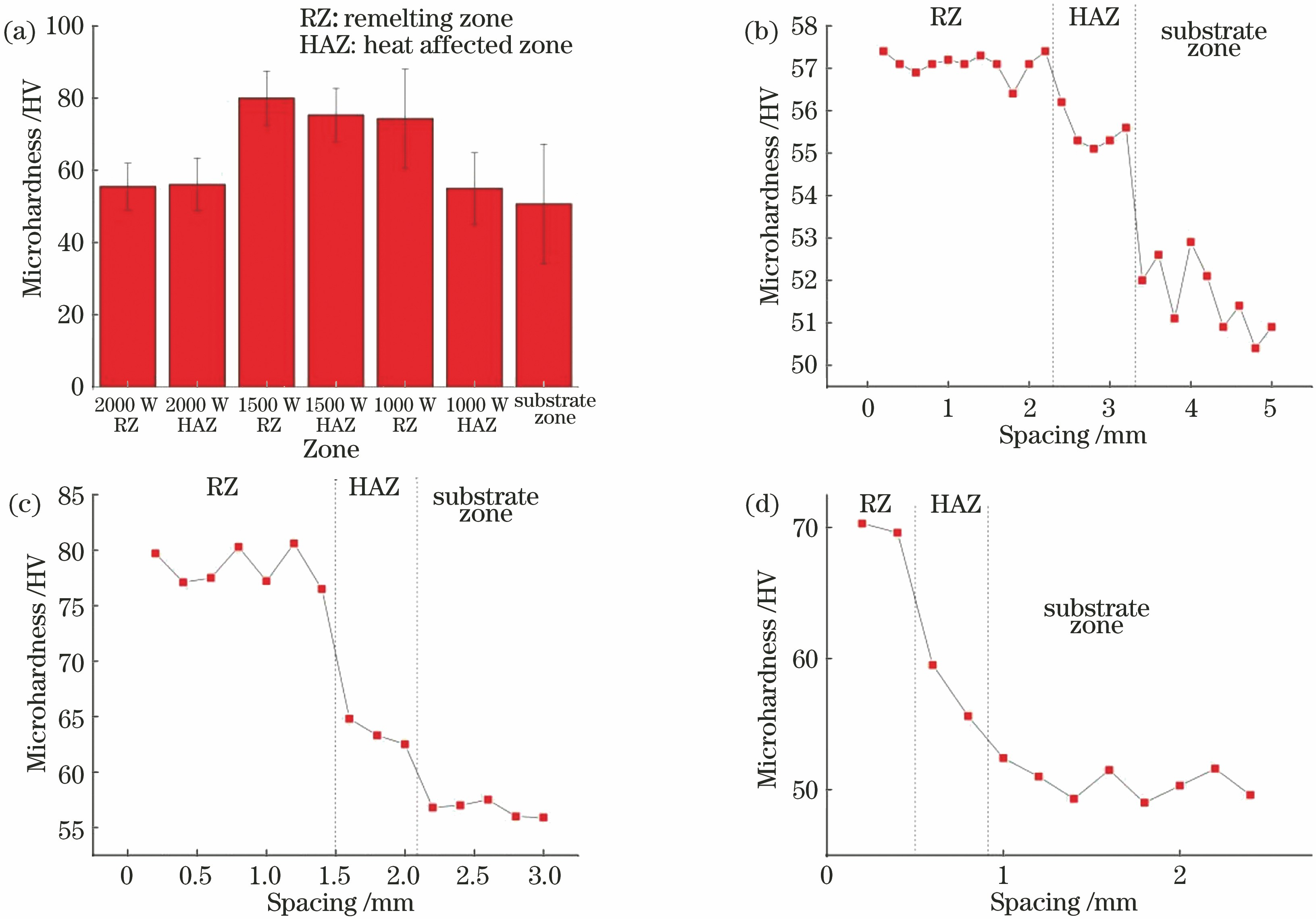
图 8. 显微硬度图。(a)显微硬度柱状图;(b) 2000 W激光功率下得到的重熔层的显微硬度图;(c) 1500 W激光功率下得到的重熔层的显微硬度图;(d) 1000 W激光功率下得到的重熔层的显微硬度图
Fig. 8. Microhardness diagrams. (a) Microhardness histogram; (b) microhardness of remelting layer obtained at laser power of 2000 W; (c) microhardness of remelting layer obtained at laser power of 1500 W; (d) microhardness of remelting layer obtained at laser power of 1000 W
3.1.5 三点弯曲试验
可以通过三点弯曲试验来确定表面强化层拉伸区域第一裂纹的外观以及表面强化层与基板的分层情况。Kadolkar等[10]曾指出,表面强化层的性能可以以强化层的内聚强度来表示,在弯曲测试期间进行的载荷-位移测量有助于确定与裂纹萌生相应的载荷。引发强化层破裂所需的载荷提供了强化层强度的量度。采用基于基本梁理论和材料强度并结合混合规律的简化方法来计算重熔层的内聚强度,内聚强度与临界载荷成正比关系。如
由
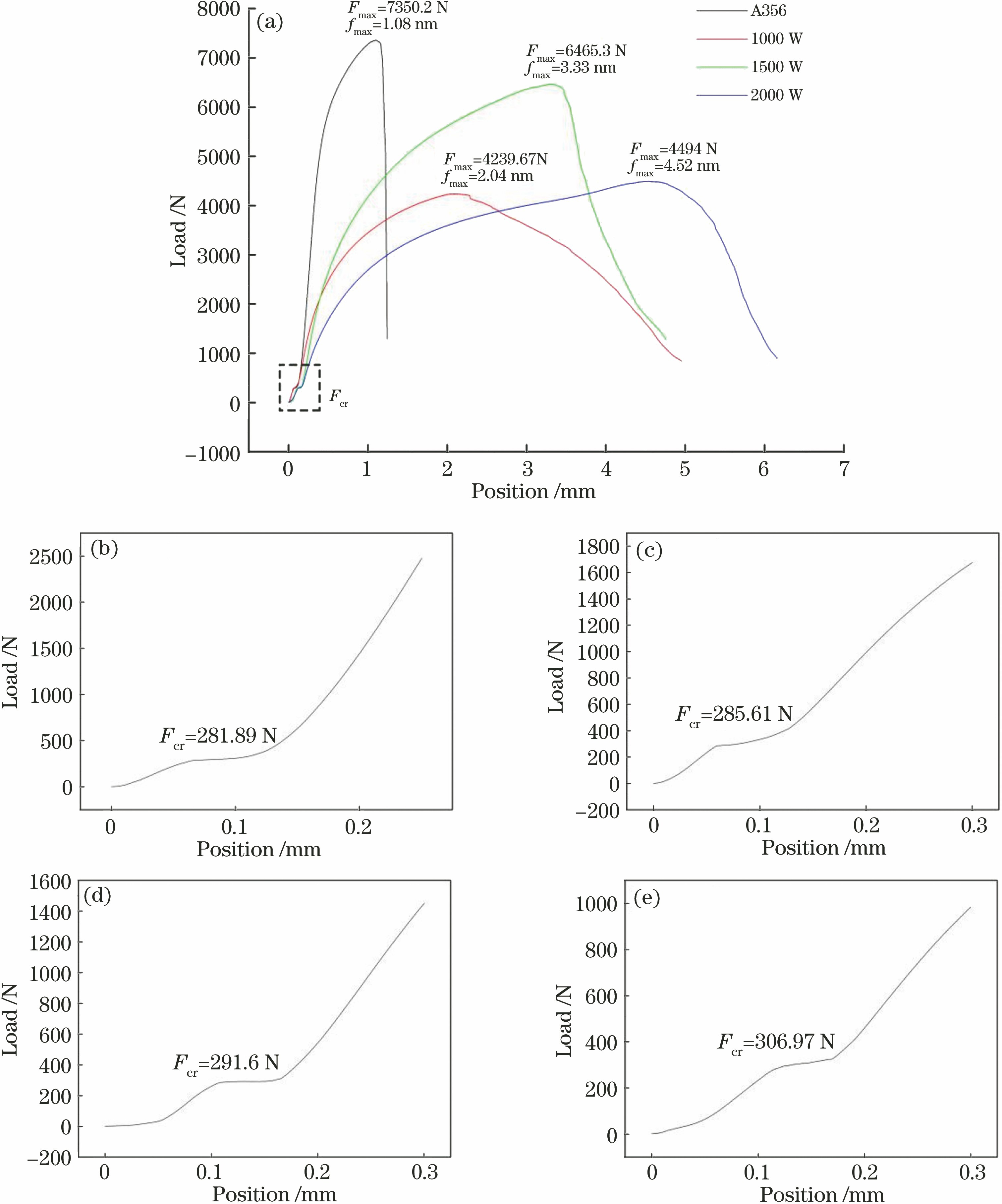
图 9. 弯曲试验结果。(a)基体试样及不同激光功率下得到的熔覆试样的弯曲试验结果;(b) A356基体的Fcr局部图;(c) 1000 W激光功率下获得的熔覆试样的Fcr局部图;(c) 1500 W 激光功率下获得的熔覆试样的Fcr局部图; (d) 2000 W 激光功率下获得的熔覆试样的Fcr局部图
Fig. 9. Bending test results. (a) Bending test results of substrate sample and remelting samples obtained at different laser power; (b) partial view of Fcr for A356 base metal; (c) partial view of Fcr for remelting sample obtained at laser power of 1000 W; (c) partial view of Fcr for remelting sample obtained at laser power of 1500 W; (d) partial view of Fcr for remelting sample obtained at laser power of 2000 W
晶粒尺寸是影响材料塑性的主要因素之一。由上文讨论可知,对于激光重熔后的铝合金,其表面强化层的晶粒尺寸相比基体明显细化;同时,随着激光功率增大,表面强化层的细晶区厚度增大。晶粒细化对塑性的影响主要是由于:1)在受力过程中,晶粒细小使得晶内的位错与位错增殖率增大;2)裂纹穿过晶界进入相邻晶粒并改变方向的频率增大,消耗的能量增加;3)晶粒细小,塑性变形时所需的晶粒转动小[18]。因此,2000 W激光功率下获得的重熔试样的塑性提升的幅度最大。
如

图 10. 不同试样中弯曲裂纹的金相图。(a) A356铝合金基体;(b) 1000 W激光功率下获得的重熔试样;(c) 1500 W激光功率下获得的重熔试样;(d) 2000 W激光功率下获得的重熔试样
Fig. 10. Metallographic images of bending cracks in different samples. (a) A356 aluminum alloy base material; (b) remelting sample obtained at laser power of 1000 W; (c) remelting sample obtained at laser power of 1500 W; (d) remelting sample obtained at laser power of 2000 W
由
由
4 结论
对于经过激光重熔处理的A356铝合金,其表面强化层中的晶粒相较基体晶粒明显细化,第二相分布得更均匀。与基体相比,在1000,1500,2000 W激光功率下获得的重熔试样的表面硬度均有所提高,1500 W下获得的重熔试样的硬度提升得最为明显。
在弯曲测试后发现:与基体相比,激光重熔层的表面塑性大幅提升;在1000,1500,2000 W激光功率下获得的重熔试样在最大弯曲应力下的挠度分别为2.04,3.33,4.52 mm。
由于表面强化层较薄,在1000 W激光功率下获得的重熔试样的表面强化层与基体发生了分层现场,而在1500 W及2000 W激光功率下获得的重熔试样未出现类似的情况。随着激光功率增大,表面强化层增厚,表面强化层与基体的结合力增强。
[1] Dubourg L, Ursescu D, Hlawka F, et al. Laser cladding of MMC coatings on aluminium substrate: influence of composition and microstructure on mechanical properties[J]. Wear, 2005, 258(11/12): 1745-1754.
[2] Chen S X, Richter B, Morrow J D, et al. Pulsed laser remelting of A384 aluminum, part I: measuring homogeneity and wear resistance[J]. Journal of Manufacturing Processes, 2018, 32: 606-614.
[3] Chi Y M, Gu G C, Yu H J, et al. Laser surface alloying on aluminum and its alloys: a review[J]. Optics and Lasers in Engineering, 2018, 100: 23-37.
[4] 孙云辉, 周建忠, 盛杰, 等. 深冷激光喷丸强化2024-T351铝合金拉伸性能及断口分析[J]. 中国激光, 2017, 44(8): 0802003.
[5] 张光耀, 王成磊, 高原, 等. 稀土La2O3对6063Al激光熔覆Ni基熔覆层微观结构的影响[J]. 中国激光, 2014, 41(11): 1103001.
[6] 雷临苹, 叶宏, 宋坤, 等. Al2O3-TiO2对铝合金表面激光熔覆NiAl涂层组织性能的影响[J]. 表面技术, 2018, 47(10): 145-150.
Lei L P, Ye H, Song K, et al. Effect of Al2O3-TiO2 on microstructure and properties of NiAl coating by laser cladding on aluminum alloy[J]. Surface Technology, 2018, 47(10): 145-150.
[7] BiswasK, GalunR, Mordike BL, et al., 2004, 334/335: 517- 523.
[8] Pakieła W, Tanski T, Pawlyta M, et al. The structure and mechanical properties of AlMg5Si2Mn alloy after surface alloying by the use of fiber laser[J]. Applied Physics A, 2018, 124(3): 263.
[10] Kadolkar P, Dahotre N B. Effect of processing parameters on the cohesive strength of laser surface engineered ceramic coatings on aluminum alloys[J]. Materials Science and Engineering: A, 2003, 342(1/2): 183-191.
[11] Zhou S F, Huang Y J, Zeng X Y. A study of Ni-based WC composite coatings by laser induction hybrid rapid cladding with elliptical spot[J]. Applied Surface Science, 2008, 254(10): 3110-3119.
[12] Emamian A, Corbin S F, Khajepour A. The effect of powder composition on the morphology of in situ TiC composite coating deposited by Laser-Assisted Powder Deposition (LAPD)[J]. Applied Surface Science, 2012, 261: 201-208.
[13] 刘智恩. 材料科学基础[M]. 3版. 西安: 西北工业大学出版社, 2013.
Liu ZE. Material science[M]. 3rd ed. Xi'an: Northwestern Polytechnical University Press, 2013.
[14] Kadolkar P, Dahotre N B. Variation of structure with input energy during laser surface engineering of ceramic coatings on aluminum alloys[J]. Applied Surface Science, 2002, 199: 222-233.
[15] 刘颖卓, 党波, 刘峰. 冷却速率对A356铝合金显微组织和微观硬度的影响[J]. 西安工业大学学报, 2013, 33(2): 128-133.
Liu Y Z, Dang B, Liu F. Effects of cooling rate on microstructure and microhardness of A356 alloy[J]. Journal of Xi'an Technological University, 2013, 33(2): 128-133.
[16] 高士学, 孙跃军, 高艳静. 稀土La对A356铝合金组织及硬度的影响[J]. 热加工工艺, 2016, 45(5): 81-83.
Gao S X, Sun Y J, Gao Y J. Effects of La on microstructure and hardness of A356 aluminium alloy[J]. Hot Working Technology, 2016, 45(5): 81-83.
[17] 何兵, 覃铭, 李德贵, 等. 固溶时间对含钪A356铝合金组织与力学性能的影响[J]. 金属热处理, 2018, 43(3): 185-189.
He B, Qin M, Li D G, et al. Effects of solution time on microstructure and mechanical properties of A356 aluminium alloy containing Sc[J]. Heat Treatment of Metals, 2018, 43(3): 185-189.
[18] Apps P J, Berta M, Prangnell P B. The effect of dispersoids on the grain refinement mechanisms during deformation of aluminium alloys to ultra-high strains[J]. Acta Materialia, 2005, 53(2): 499-511.
[19] Fadavi Boostani A, Tahamtan S. Fracture behavior of thixoformed A356 alloy produced by SIMA process[J]. Journal of Alloys and Compounds, 2009, 481(1/2): 220-227.
[20] 易有福, 龙思远, 徐绍勇, 等. 低压铸造A356铝合金轮毂的微观组织和力学性能[J]. 特种铸造及有色合金, 2008, 28(5): 373-375.
Yi Y F, Long S Y, Xu S Y, et al. Microstructure and mechanical properties of low-pressure casting A356 aluminum alloy wheel hub[J]. Special Casting & Nonferrous Alloys, 2008, 28(5): 373-375.
[21] Katipelli L R, Agarwal A, Dahotre N B. Interfacial strength of laser surface engineered TiC coating on 6061 Al using four-point bend test[J]. Materials Science and Engineering: A, 2000, 289(1/2): 34-40.
[22] 孙训方, 方孝淑, 陆耀洪. 材料力学[M]. 3版. 北京: 高等教育出版社, 2012.
Sun XF, Fang XS, Lu YH. Mechanics of materials[M]. 3rd ed. Beijing: Higher Education Press, 2012.
王建刚, 高士友, 陈旭升, 张梦雨. 激光重熔A356铝合金表面的力学性能[J]. 中国激光, 2020, 47(4): 0402002. Wang Jiangang, Gao Shiyou, Chen Xusheng, Zhang Mengyu. Mechanical Properties of A356 Aluminum Alloy after Laser Surface Remelting[J]. Chinese Journal of Lasers, 2020, 47(4): 0402002.