基于高斯脉冲激光空间分辨测量光学元件表面激光损伤阈值研究
下载: 943次
1 引言
随着激光器输出能量的不断提高,其对光学元件的抗激光损伤能力的要求也会随之提高。对于光学元件,精准的激光损伤阈值可以客观地表示光学元件的抗激光损伤能力[1-7]。激光损伤阈值不仅为光学元件提供了安全的使用范围,并且在提高其抗损伤性研究中也起到至关重要的作用[8-17]。对于光学元件的长脉冲激光损伤,其损伤机制为热过程。大多数激光损伤都是由光学元件中存在的缺陷引起的,这些缺陷诱导的缺陷损伤对应的激光损伤阈值要远远小于待测样品自身性质引起的本征损伤能量密度。例如在Sc2O3薄膜的激光损伤阈值测试中,由薄膜缺陷引发的缺陷损伤对应的激光损伤阈值要比Sc2O3自身性质引发本征损伤对应的激光损伤阈值小10倍[18]。而在国际标准1-on-1激光损伤阈值测试中,是将高斯光斑内空间能量分布为高斯分布的高斯光斑面积,等效地看作为都以高斯峰值能量平均分布的有效面积,并且将高斯峰值能量除以有效面积获得的峰值能量密度作为所测样品的激光损伤密度[19-22]。而在实际应用中,一方面光学元件中存在着种类繁多且分布不均匀的缺陷,这些缺陷都有着各自对应的激光损伤阈值;另一方面高斯脉冲激光能量在空间上是不均匀分布的,因此将未出现在激光峰值能量密度处的激光损伤点进行细化分析,是研究光学元件抗激光损伤能力的重要环节。
针对此类问题,国内外也已经有相应的研究。2011年Hu等[23]提出了基于激光辐照图像处理法实现单脉冲测量激光损伤阈值。其方法是运用二进制光栅对激光光束进行分束,通过计算机对激光辐照后的图像进行处理,获得每个激光分束所对应的激光能量密度,结合单脉冲激光辐照后样品的损伤情况,推导出其所测元件的激光损伤阈值。2016年Liu等[24]提出对样品激光辐照后的图像进行分析,统计并讨论辐照后损伤区域和未损伤区域的面积关系,利用图像灰暗度分析的方法得到每个光斑分区的激光能量密度,从而实现单脉冲获得所测元件的激光损伤阈值。以上两种测试方法都采用计算机对激光辐照后图像的灰暗度分析处理来得到激光能量密度,其中存在着一定的误差;运用单脉冲激光辐照的损伤情况来描述测试样品整体的抗激光损伤能量,同样存在着一定的异议。
针对上述问题,本文基于激光能量密度高斯分布理论,提出一种基于高斯脉冲激光空间分辨测量光学元件激光损伤阈值的测试方法。同时利用此方法和1-on-1方法分别针对三种不同样品进行激光损伤阈值测试,分析并讨论两种方法的测试结果,证明本文提出的激光损伤阈值测试方法解决了1-on-1测试中激光损伤点未出现在激光峰值能量密度处、却以峰值能量密度作为激光损伤密度的问题。讨论了该测试方法中的变量因素对测试结果的影响,并根据测试方法建立缺陷分析模型,分析并讨论缺陷信息,证明基于高斯脉冲激光空间分辨测试方法的优势以及使用价值。
2 基于高斯激光空间分辨测量激光损伤阈值的原理及方法
2.1 测量原理
在1-on-1激光损伤阈值测试中,将高斯光斑中心峰值能量
式中
若激光辐照后出现损伤,则将激光峰值能量密度
但是在实际测试过程中,由于高斯光斑的能量分布为高斯分布,并且会有损伤点并未出现在峰值能量密度处的情况,此时就需要针对这些损伤点所对应的激光损伤密度进行准确分析,提出的基于高斯脉冲激光空间分辨测量激光损伤阈值法正是针对此类问题进行研究。
由于高斯脉冲激光光斑内的空间能量密度分布为高斯分布,因此在高斯光斑内的损伤点坐标能量密度可以表示为[26]:
式中
可以根据入射峰值能量密度设定一个激光能量密度差,对高斯光斑进行等能量密度差的光斑分区,通过(3)式可以反推得到每个激光能量密度分区的面积
最后通过讨论每个激光能量密度分区的损伤密度与能量密度的关系,设定一个零损伤密度的激光能量密度作为所测样品的激光损伤阈值。
2.2 测量方法
所设计的基于高斯脉冲激光空间分辨测量激光损伤阈值的测试装置与1-on-1激光损伤阈值测试装置相同,如
为了证明所提出的激光损伤阈值测试方法具有可重复性,分别选取三种45°、532 nm的反射膜进行实验,测试样品的材料与镀膜工艺如
表 1. 测试样品
Table 1. Testing samples
|
所提出的基于高斯脉冲激光空间分辨测量激光损伤阈值方法的核心是对高斯激光光斑内的损伤点分布情况与高斯激光空间能量分布情况的讨论,因此需要先将光束质量分析仪中的光斑位置与CCD中的样品表面光斑位置对应起来。
研究利用由半波片和偏振片组成的衰减系统,将Nd∶YAG激光器发出的高斯激光能量衰减到极低,经过透镜聚焦到金属膜表面,并用CCD相机记录靶面上激光光斑的轮廓。由分光劈板分出的一束激光由光束质量分析仪对其光斑面积以及能量空间分布进行实时记录。通过对比CCD的光斑轮廓图像与光束质量分析仪中的能量分布图,以及对比两幅图中的光斑位置、轮廓以及特殊点,利用放大、位移等方式,将两幅图对应起来,如
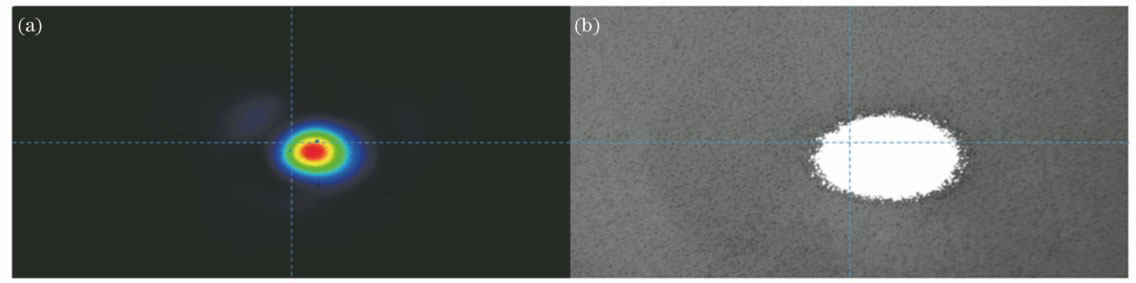
图 2. (a)光束质量分析仪光斑位置与(b) CCD中光斑位置关系图
Fig. 2. Relationship between (a) spot position in beam quality analyzer and (b) spot position in CCD
由于实验时激光入射角度为45°,需通过投影建立高斯光斑内横、纵两个方向上的高斯半径关系。根据光束质量分析仪实时测量得到的高斯光斑有效面积为0.26 mm2,可以得到光斑高斯半径
随后根据估测激光损伤阈值,选取一个接近估测损伤阈值的激光能量密度,对测试样品进行100次激光辐照,记录并统计出每一次激光辐照后的损伤点坐标情况,根据像素定位每个损伤点的坐标位置,其辐照前后对比图如
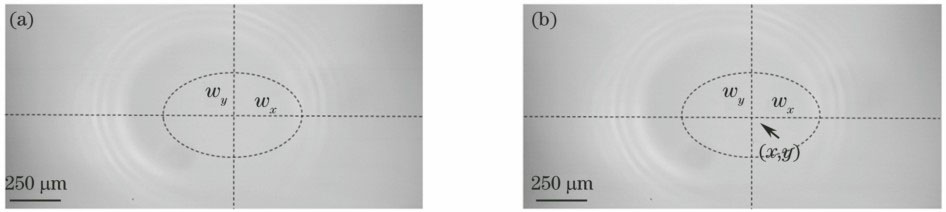
图 3. (a)高斯光斑位于CCD中的位置;(b)激光辐照后损伤点的坐标
Fig. 3. (a) Position of the Gaussian spot in CCD; (b) coordinates of the damage point after laser irradiation
根据统计100次高斯脉冲激光辐照后离散的损伤点坐标情况,发现越接近高斯光斑中心的峰值能量密度处,损伤点越密集。由于高斯脉冲激光光斑内空间能量分布为高斯分布,因此根据上文所述理论模型,可以根据损伤点坐标计算出每一个损伤点所对应的激光能量密度。
随后对高斯脉冲激光光斑按照等能量密度差进行高斯光斑能量密度分区。以Al2O3/SiO2样品为例,激光有效面积为0.26 mm2,激光辐照峰值能量密度为10 J/cm2,以1 J/cm2为能量密度差对高斯光斑进行能量密度分区,即以等能量密度差将高斯光斑分成10个能量密度分区。根据100次激光辐照后激光损伤点分布情况,可以统计得出每个光斑能量密度分区所对应的损伤点个数,如
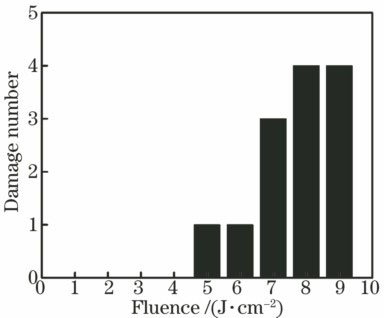
图 4. Al2O3/SiO2样品以10 J/cm2的激光能量密度辐照 100次后损伤点分布情况
Fig. 4. Distribution of damage points of Al2O3/SiO2sample irradiated at a laser energy density of 10 J/cm2 for 100 times
最后根据每个光斑能量分区所对应的激光能量密度,以及上文所述的测量原理计算可得每个能量密度分区的损伤密度。此时需要注意的是测试样品是经过100次激光辐照后得到的损伤点个数,因此辐照面积
运用所提出的高斯脉冲激光空间分辨测试方法测量样品的激光损伤阈值后,再利用1-on-1激光损伤阈值测试方法对同一样品进行测试。为了便于对比后讨论,将1-on-1激光损伤阈值测试方法中的激光能量台阶设置为10个,每个能量台阶激光辐照10次,以确保两种测试方法的激光辐照总次数均为100次。
3 结果与讨论
3.1 实验结果与分析
所测样品的1-on-1激光损伤阈值测试结果以及高斯脉冲激光空间分辨法测量激光损伤阈值中激光能量密度的选取和实验结果如
表 2. 实验结果
Table 2. Experimental resultsJ·cm-2
|
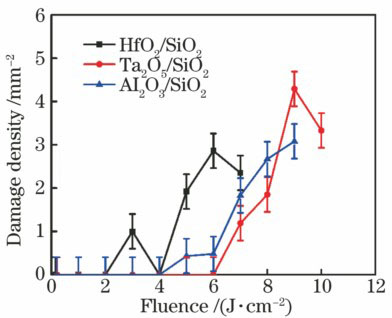
图 5. 高斯空间分辨法测量激光损伤阈值实验结果
Fig. 5. Experimental results of laser damage thresholds measured by Gaussian spatial resolution method
由实验结果可看出,所提出的基于高斯脉冲激光空间分辨测量得到的激光损伤阈值要比1-on-1激光损伤阈值测试法得到的激光损伤阈值低。原因在于1-on-1激光损伤阈值测试方法是将能量分布为高斯分布的高斯光斑以峰值能量为基准等效为有效光斑,并将峰值能量与有效光斑的比值作为峰值能量密度,并当作测试样品的损伤能量密度。而实际上,高斯光斑空间能量分布以及激光损伤点的分布都不是均匀分布的,正是在1-on-1的基础上,针对损伤点未出现在激光峰值能量密度处的情况,对损伤点的激光能量密度进行细分研究,因此实验所得损伤阈值比1-on-1测试方法得到的结果要小。
3.2 高斯激光入射能量密度的取值对实验结果的影响
在基于高斯脉冲激光空间分辨法测量光学元件表面激光损伤阈值的研究中,高斯脉冲激光能量密度的选取是影响实验结果的重要因素。因此,以Al2O3/SiO2样品为例,分别选取激光能量密度为8,10,15,20,25 J/cm2进行激光辐照测试,从而完成对比实验。实验结果如
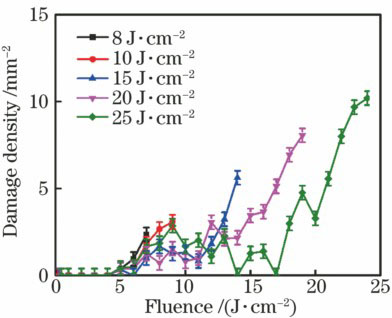
图 6. 激光辐照能量密度的选取对实验结果的影响
Fig. 6. Effect of laser irradiation energy density selection on experimental results
由对比实验可知,随着能量密度的提高,最大损伤能量密度始终为4 J/cm2,并不会随之变化。原因在于样品中存在的缺陷种类都有着其对应的激光损伤阈值。并且,当激光辐照能量密度高于其缺陷损伤阈值时,便会诱发其缺陷损伤。因此对于缺陷损伤阈值最低的缺陷种类,其损伤都会出现在一个固定的激光能量密度浮动范围内,并不会随着激光辐照能量密度的变化而变化。
3.3 基于空间分辨法对于缺陷特性的分析
纳秒激光辐照产生的破坏与样品的缺陷种类以及缺陷密度紧密相关,由于各类缺陷都各自具有尺寸以及吸收能力等不同特性,因此对于样品中存在的缺陷种类进行区分与讨论,是研究光学元件抗激光损伤能力的重要组成部分。研究根据法国菲涅耳实验室的Krol等[27-28]提出的假设缺陷阈值服从高斯分布的统计模型,结合1-on-1与基于高斯激光空间分辨法这两种激光损伤阈值测试方法,得到了所测样品中缺陷密度以及缺陷阈值的分布情况,并讨论了这两种测量方法所得到的缺陷信息。
此模型假设每个缺陷都有其对应的阈值
式中
在提出的基于高斯脉冲激光空间分辨法测量激光损伤阈值应用中,仅有若干离散的损伤密度,因此对能量密度分区的单位面积损伤点进行积分计算,结果即为每个能量密度分区的损伤密度。可采用拟合的方法来确定缺陷信息:缺陷密度
实验拟合结果如
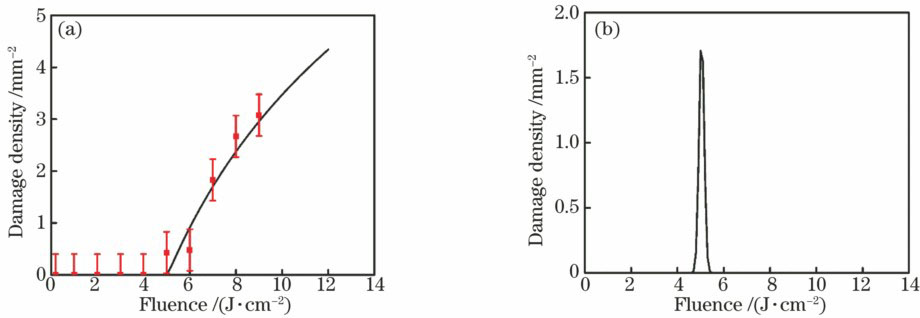
图 7. (a)基于高斯激光空间分辨测量并拟合的损伤密度曲线;(b)基于高斯分布的统计模型拟合的缺陷信息
Fig. 7. (a) Damage density curve based on Gaussian laser spatially resolved measurement; (b) defect information of statistical model fitting based on Gaussian distribution
在1-on-1激光损伤阈值测试应用中,仅有若干离散的损伤概率值,因此运用此缺陷分析模型与泊松分布模型相结合,同样可以判断得到缺陷信息。
若
式中
同样以Al2O3/SiO2样品为例,1-on-1测试与缺陷分析结果如
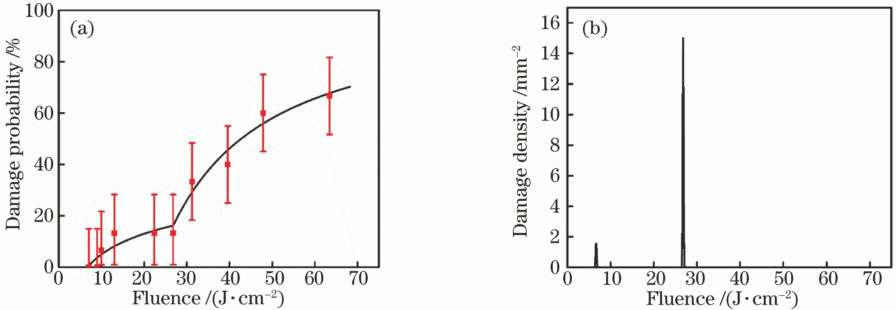
图 8. (a)基于1-on-1激光损伤阈值测试并拟合的损伤概率曲线;(b)基于高斯分布的统计模型拟合的缺陷信息
Fig. 8. (a) Damage probability curve based on 1-on-1 laser damage threshold test; (b) defect information of statistical model fitting based on Gaussian distribution
由于基于高斯脉冲激光空间分辨法选择的入射激光能量密度为10 J/cm2,没有达到1-on-1激光损伤阈值测量方法中分析得到的第二种缺陷的平均阈值,因此基于高斯脉冲激光空间分辨法分析只得到一种缺陷。但是对于同一种缺陷而言,1-on-1与高斯脉冲激光空间分辨法得到了不同的缺陷信息,如
由
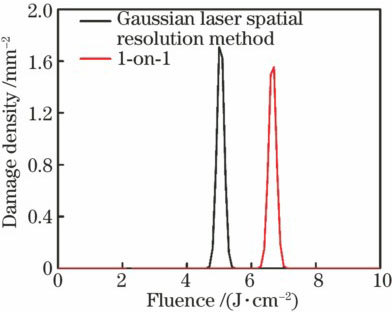
图 9. 两种激光损伤阈值测试方法对同一种缺陷的分析结果
Fig. 9. Analysis results of the same defect by two laser damage threshold test methods
4 结论
提出了一种基于高斯脉冲激光空间分辨测量光学元件表面激光损伤阈值的测试方法,通过对高斯激光光斑进行等能量密度差的能量密度分区,以及对每个能量密度分区的损伤密度进行统计,从而得到待测样品的激光损伤阈值。所提出的测试方法可以运用到反射膜或者增透膜等,相比于国际标准1-on-1激光损伤阈值测试方法,所提方法完成了对高斯光斑内能量密度分布以及损伤点分布的细化分析。基于高斯脉冲激光空间分辨测量的光学元件表面激光损伤阈值可以得到更加精确的低损伤阈值缺陷的缺陷信息,同时也有利于更好地研究限制缺陷的方法。
[2] Sheehan LM, SchwartzS, Battersby CL, et al. Automated damage test facilities for materials development and production optic quality assurance at Lawrence Livermore National Laboratory[C]. SPIE, 1998, 3578: 302- 313.
[3] 徐俊海, 赵元安, 邵建达, 等. 不同工艺条件下 TiO2 单层膜的吸收和损伤阈值测试[J]. 中国激光, 2012, 39(4): 0407001.
[4] 郑如玺, 易葵, 范正修, 等. 充氧口位置对电子束蒸发沉积 HfO2 薄膜性质的影响[J]. 中国激光, 2016, 43(10): 1003001.
[5] 杨明红, 赵元安, 苏涵韩, 等. 基底亚表面裂纹对减反射膜激光损伤阈值的影响[J]. 中国激光, 2012, 39(8): 0807001.
[7] 苗心向, 袁晓东, 吕海兵, 等. 激光装置污染物诱导光学元件表面损伤实验研究[J]. 中国激光, 2015, 42(6): 0602001.
[8] 李大伟, 赵元安, 贺洪波, 等. 光学元件激光损伤阈值的指数拟合法以及测试误差分析[J]. 中国激光, 2008, 35(2): 273-275.
[11] 时双, 孙明营, 郝艳飞, 等. 表面处理工艺对铝合金抗激光损伤能力的影响[J]. 中国激光, 2016, 43(12): 1202001.
[13] 苑利钢, 陈国, 侯天禹, 等. 2 μm 激光对磷锗锌晶体的损伤阈值测量及影响因素分析[J]. 中国激光, 2015, 42(8): 0802001.
[14] MillerP, SuratwalaT, BudeJ, et al. Laser damage precursors in fused silica[C]. SPIE, 2009, 7504: 75040X.
[15] 王洪祥, 沈璐, 李成福, 等. 光学元件激光诱导损伤分析及实验研究[J]. 中国激光, 2017, 44(3): 0302006.
[17] 刘晓凤, 李大伟, 李笑, 等. 电子束蒸发制备 HfO2/SiO2高反膜的1064 nm激光预处理效应[J]. 中国激光, 2009, 36(6): 1545-1549.
[18] RudolphW, Emmert LA, SunZ, et al. Laser damage in thin films—what we know and what we don't[C]. SPIE, 2013, 8885: 888516.
[22] "ISO 11254-2, Laser and laser-related equipment. determination of laser-induced damage threshold of optical surface-part 1: S-on-1 test, " ISO ISO11254-2:2001( 2001).
[25] "ISO21254-1:2011: Test methods for laser induced damage threshold—part 1: Definitions and general principles," ISO ISO 21254-1:2011(2011).
Article Outline
单翀, 赵元安, 张喜和, 胡国行, 王岳亮, 彭小聪, 李成. 基于高斯脉冲激光空间分辨测量光学元件表面激光损伤阈值研究[J]. 中国激光, 2018, 45(1): 0104002. Shan Chong, Zhao Yuan′an, Zhang Xihe, Hu Guohang, Wang Yueliang, Peng Xiaocong, Li Cheng. Study on Laser Damage Threshold of Optical Element Surface Based on Gaussian Pulsed Laser Spatial Resolution[J]. Chinese Journal of Lasers, 2018, 45(1): 0104002.