基于机器视觉的聚氯乙烯管材表面缺陷检测
下载: 1253次
1 引言
聚氯乙烯(PVC)管材具有质量小、耐酸碱腐蚀和阻燃耐老化等优点,凭借良好的性能与价格优势,在管材市场占据着举足轻重的地位[1]。因此,PVC管材表面质量检测有很大的市场需求。在PVC管材的制造过程中,由于原材料、生产设备以及生产环境等问题,管材表面很容易出现褶皱、杂质、污染、划痕、凹坑和气泡等缺陷。目前在生产车间中主要依靠工人对管材表面进行观察并发现缺陷[2],这种肉眼观察法具有很多弊端[3-4],如人工成本高、存在较大的主观性,以及容易发生漏检和误检、工人检测速度慢等,无法保证检测效率。
目前,基于机器视觉的表面缺陷检测算法主要分为3类:模型法、频谱法与统计法。模型法通过分形体[5]、随机场模型[6]和反散射模型[7]等描述表面缺陷特征;频谱法通过傅里叶特征[8]、小波特征[9]和Gabor特征[10]等描述物体表面缺陷特征;统计法通过直方图统计特征[11]、自相关法[12]和形态学法[13]等描述物体表面缺陷特征。
已有学者对PVC管材表面缺陷检测进行了研究,但相关文献较少。马艳[14]将边缘检测技术应用到PVC管材检测中,对比分析了多种边缘检测算子的检测效果;龙晓薇等[15-16]将图像分割和形态学处理引入PVC管材表面缺陷检测,并对检测到的缺陷初步分类;Dehghan等[17]设计了全方位成像方案,以获取最佳空间分辨率管材图像;Prabuwono等[18]设计了流水线上PVC塑料瓶缺陷在线视觉检测系统,对流水线上转数为106 r/min的塑料瓶图像采集精度达94.264%,为在线视觉检测提供了理论基础。这些学者均通过相应的检测系统,取得了较好的实验效果。然而,能够胜任实际工厂生产环境PVC管材表面检测平台的却鲜有报道。
在实际生产中,高温环境下生产的PVC管材通常用水冷却,管材表面残留的水珠会影响管材检测效果;PVC管材型号较多,单一检测方法很难应用到所有型号的管材检测中;此外,检测算法还需要适应PVC管材生产线速度,保证工厂生产效益等。
针对以上问题,本文提出了一种基于机器视觉的PVC管材表面检测算法,以相应的硬件作支持,真正地将PVC管材表面检测应用到实际工厂环境中,检测准确性与检测速度均满足工厂生产检测要求。
2 PVC管材表面检测平台
基于机器视觉的PVC管材表面检测平台内部结构如
本检测平台采用研华科技610L工业控制计算机、朗歌斯触摸屏显示器、海康威视200万工业CCD灰度相机、海康威视12 mm工业镜头和锐视科技定制环形防水光源,光源中心留有圆孔令PVC管材穿过。此外,还配备塑胶环形滤水圈,PVC管材通过时便可滤除绝大部分残留在表面的水珠。工业生产中,常见PVC管材表面缺陷包括皱褶、杂质、污染、划痕、凹坑和气泡等,
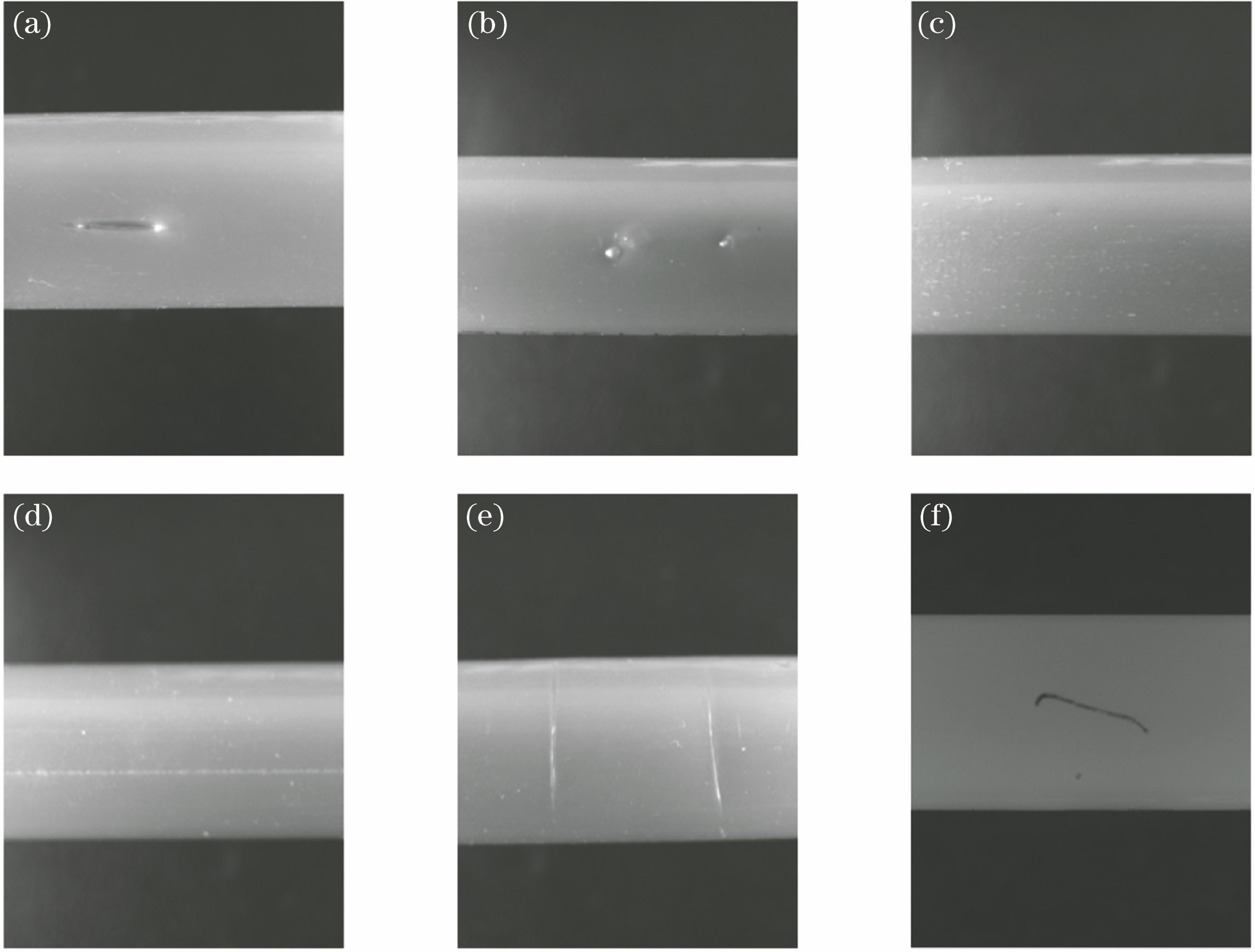
图 2. PVC管材表面缺陷图。(a)凹坑;(b)气泡;(c)杂质;(d)褶皱;(e)划痕;(f)污染
Fig. 2. Surface defects on PVC pipes. (a) Pits; (b) bubbles; (c) impurities; (d) wrinkles; (e) scratches; (f) pollution
3 PVC管材表面缺陷检测算法
3.1 查表法快速Gamma变换
受光源亮度或管材运动过程产生抖动等因素的影响,相机抓取到的图像会出现对比度较低、缺陷显示效果不明显等情形,直接影响最终检测结果。因此,需要对图像进行Gamma变换,以保证检测结果的准确性。
传统Gamma变换[19]需要对图像中所有像素点进行计算,相同参数下像素值相同的点经Gamma变换后值相同,造成重复计算。为降低检测算法的冗余度,提高运行速度,采用查表法进行快速Gamma变换。按照
Gamma变换处理效果如
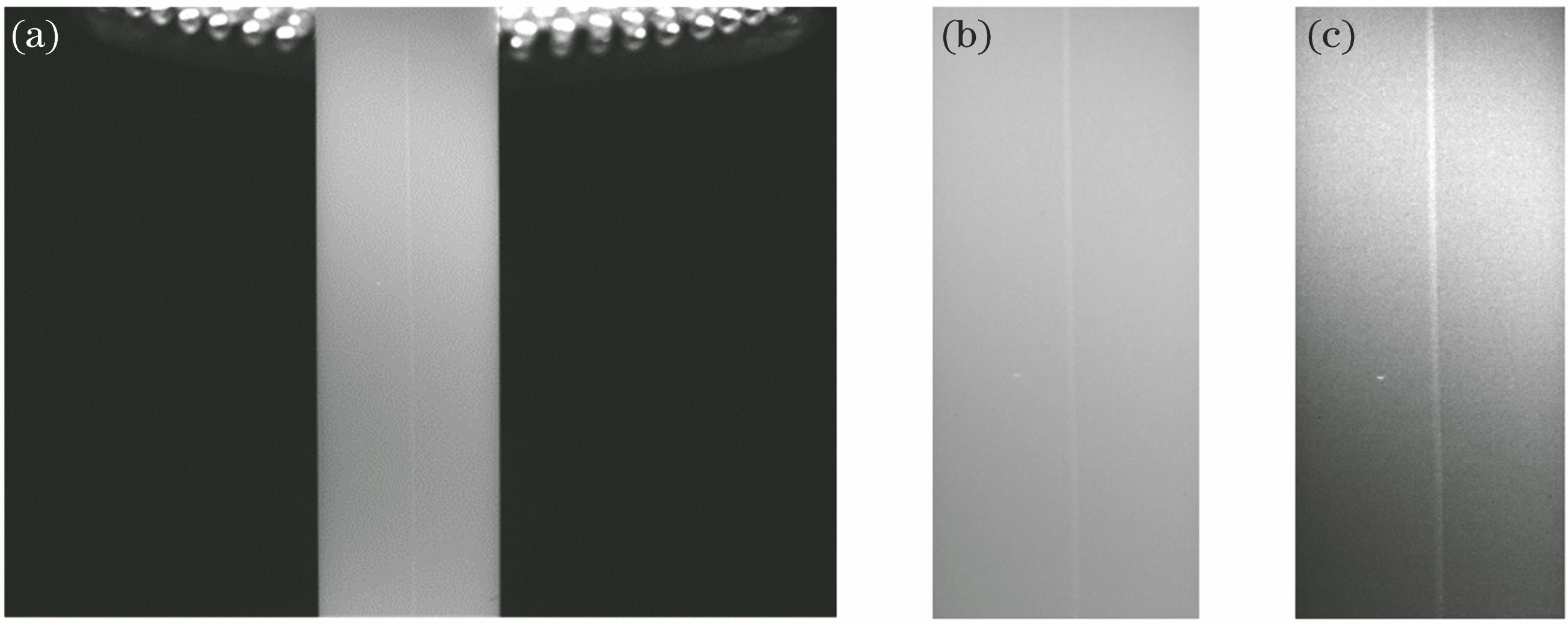
图 4. Gamma变换以及对比图。(a)原图;(b)褶皱区域;(c) Gamma变换效果图
Fig. 4. Gamma transformation and contrast diagrams. (a) Original image; (b) area of wrinkle; (c) image after Gamma transformation
3.2 水平投影与垂直投影
水平投影是将图像中每一行中所有像素点的像素值累加求和,同理,垂直投影则将每列所有像素点的像素值累加求和。然后统计在一个坐标系中[20]。第
式中:
通过大量计算和实验发现,相比传统投影法,投影值一阶微分的5差值[以垂直投影为例:
3.3 快速区域生长法寻找连通域
连通域标记可以对图像中的目标进行提取,并分析其几何特征。前期实验与工厂实际检测发现,可以通过寻找管材表面灰度图像中连通域的方法标记PVC管材表面缺陷。
采用区域生长法寻找连通域时,需遍历种子点及聚合后的每个生长点的邻域,由于邻近点的邻域重合,造成大量重复计算,使整个检测系统的运行速度难以得到提升。对此,文献[ 21]对区域生长法做了加速改进,在一定程度上避免了重复计算,节省了算法运行时间。但该算法需要对生长段前后两行进行生长,仍存在一定的重复计算。
在管材图像中,点状缺陷是部分像素点聚集在一起形成的连通区域。点状缺陷以及图像中由几个像素点聚集成的较小噪声点都有可能被检测到,造成误检。因此,在实际检测中,适当减少对图像的搜索次数,既可避免误检又可提高速度。本文进一步加速改进区域生长法,改进算法步骤为:
1) 缺陷区域的像素值与周围正常区域有较大差异,因此在选择生长点时,首先设定最大和最小2个像素阈值对缺陷进行限定,该幅图像中像素值在两阈值范围内的点,均判为不合格点,并将像素值置为0,以此作为生长点选择依据。
2) 按从左到右、从上到下的顺序对图像进行遍历处理,若首行首列像素值为零,则判为种子点,否则不作处理;对该行所有点依次进行判断,在从左到右的寻找过程中,若像素值由非零变为零,则记该点为种子生长点,将该行之后的所有像素值为零的点归入一个生长段,直到再次出现非零点,将其记为生长段终止点;若每行末尾点像素值为0,则同样判为生长终止点。
3) 生长段寻找完成后,由当前行对下一行进行区域生长,由种子生长点开始,经过生长段到生长终止点为止,判断下一行同列的点
4) 生长完成后的所有被合并的点形成一个区域,即为缺陷部位。
在检测过程中,上述步骤中所有生长点、生长段以及终止点的坐标均需保存在相对应的矢量变量里,方便后续计算。
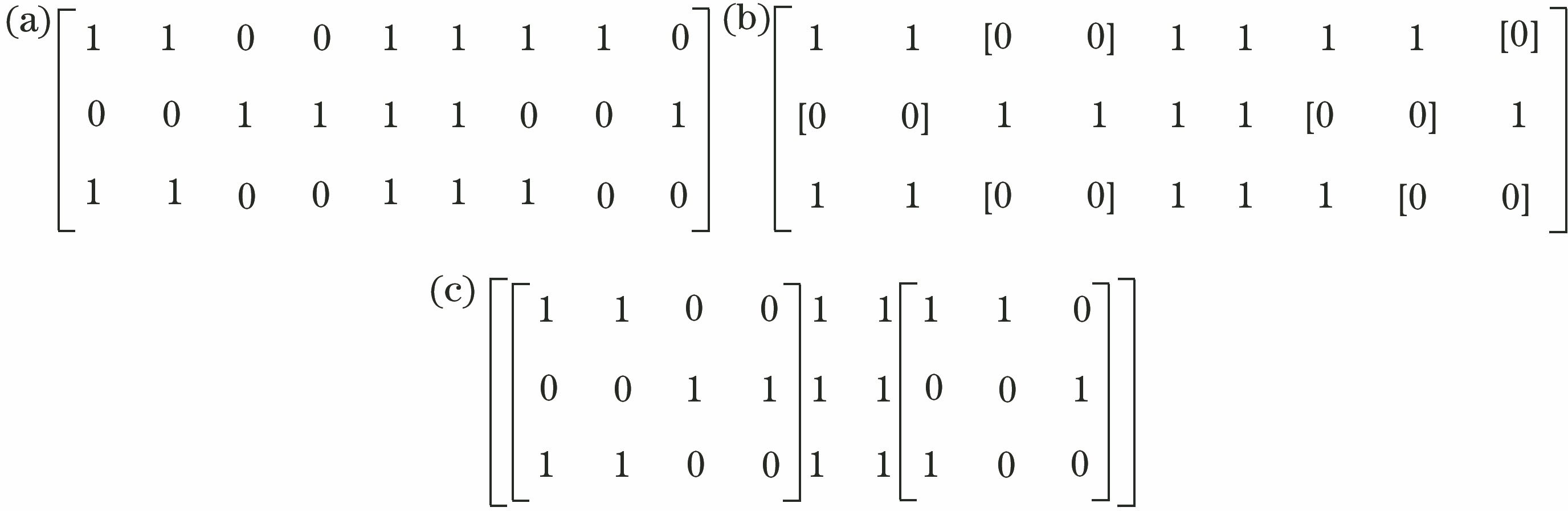
图 7. 快速区域生长示意图。(a)原图矩阵中的生长点;(b)每行生长结果;(c)最终生长结果
Fig. 7. Schematic of fast region growing. (a) Growing point in original matrix; (b) growing results per line; (c) final growing result
3.4 管材图像分块精准检测
采用上述处理方式仍未检测出PVC管材表面缺陷时,需对图像进行更深入的分块处理,该处理步骤对较小的缺陷具有很好的敏感性,可以进一步提高检测精度。通过大量实验以及现场检测结果发现,当原图像为800 pixel×1200 pixel,分块后每个子块大小为15 pixel×15 pixel时检测效果最好。
分块处理后分别求得每个子块的像素均值
之后再对每个子块单独检测。先求得每点的像素值与均值
最终判断该子块是否存在缺陷时,将二者数值进行对比
对该子块中一点
PVC管材表面的点状缺陷如
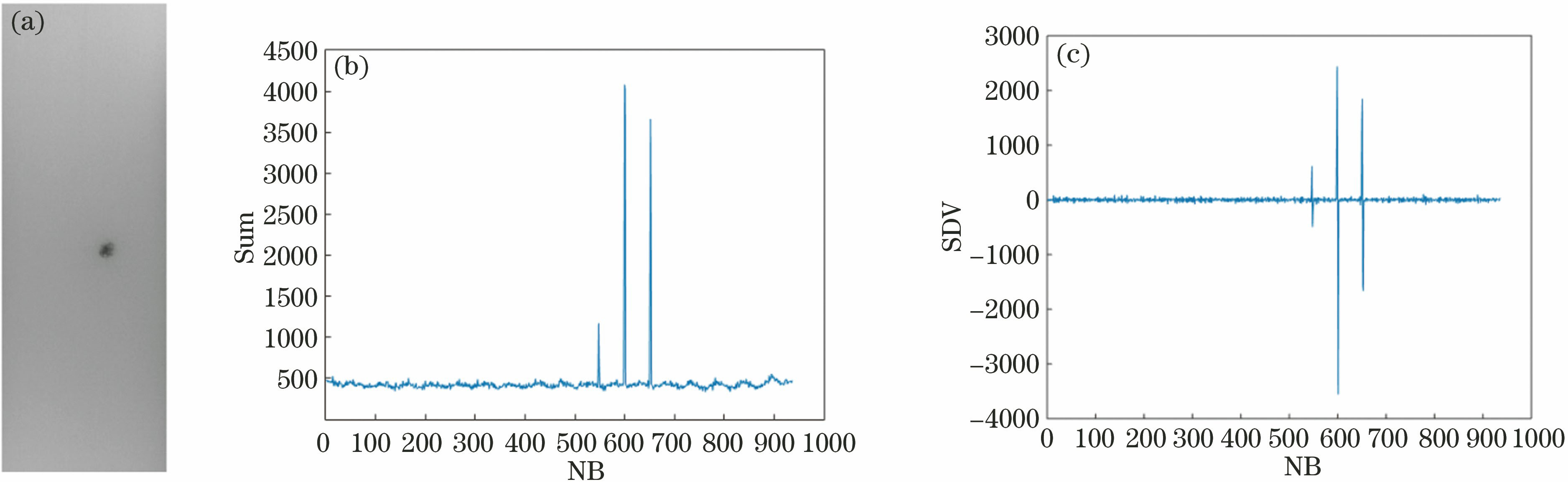
图 8. 分块效果图。(a)点状缺陷;(b)分块投影;(c)分块一阶微分
Fig. 8. Effect of block processing. (a) Point defect; (b) block projection; (c) block first-order differential
4 实验部分
为验证本文算法在实际检测环境中的可行性,与相应的硬件设备结合,在Visual Studio 2010(VS2010)环境下开发了PVC管材表面缺陷检测平台。
该平台检测算法流程如
1) 若无PVC管材输入,对该帧图像不作任何处理,继续读取下一帧图像,判断是否有管材边缘存在,为等待检测状态。
2) 若有PVC管材输入,对拍摄到的图像进行预处理,通过遍历条纹检测法,遍历图像寻找设定范围像素值,判断管材表面条纹数量,通过条纹识别结果对该帧图像进行
实验验证以及对日丰、日泰和华信等PVC管材的现场检测结果表明,该算法能检测直径为16~32 mm的管材,可检测颜色包括白色、红色、绿色、蓝色、橙色、紫色、黄色、金色、粉红、灰色,以及各颜色的亚光与亮光情形,实时检测速度超过60 m/min,缺陷最小检测面积为0.05 mm2,检测准确率可达97.6%,误检率为0.27%,且管材运行中单边抖动小于5 mm不产生误报警,管材在运行速度为45 m/min时漏检率为0,满足实际生产检测需求。
该算法除检测结果准确性好、精度高外,还对Gamma变换以及区域生长法作了加速改进。因此,设计了一系列实验对加速效果进行量化对比分析,所有实验均运行在64位Windows 7系统、Intel Core i5 2.5 GHz CPU、4 GB RAM的PC环境中,运行软件同样为VS2010。

图 10. PVC管材表面缺陷在线检测平台检测结果。(a)凹坑;(b)杂质;(c)气泡;(d)褶皱;(e)划痕;(f)污染
Fig. 10. Detection results of surface defect online detection platform of PVC pipes. (a) Pits; (b) impurities; (c) bubbles; (d) wrinkles; (e) scratches; (f) pollution
表 1. Gamma变换法的用时对比
Table 1. Comparison of time cost for Gamma transformation
|
表 2. 区域生长法的用时对比
Table 2. Comparison of time cost for region growing
|
5 结论
针对实际工业生产中对PVC管材表面质量检测需求,设计了一种基于机器视觉的PVC管材表面缺陷快速检测算法,通过与必要的硬件设备结合成检测平台,实现了对实际工厂生产线上PVC管材表面缺陷的快速检测。该检测算法将投影法、区域生长法、分块法应用到表面缺陷检测中,经实验证实,该算法分别能够精确检测PVC管材的条状缺陷、点状块状缺陷与细小缺陷。工厂实地检测证实,能够检测16~32 mm直径管材,可检测颜色包括白色、红色、绿色、蓝色、橙色、紫色、黄色、金色、粉红、灰色,以及各颜色的亚光与亮光情形,缺陷最小可检测面积为0.05 mm2,检测速度最高可达60 m/min,综合检测准确率为97.6%。同时,设备能满足管材运行中单边抖动不大于5 mm时不产生误报警现象,能保证管材在运行速度45 m/min时漏检率为0。各指标均达到了实际生产中的检测要求。
[1] 李成吾, 左继成. 国内外PVC管技术现状及发展方向[J]. 当代化工, 2015, 44(4): 711-714.
[2] 卢荣胜, 吴昂, 张腾达, 视觉, 等. 检测技术及其在缺陷检测中的应用综述[J]. 光学学报, 2018, 38(8): 0815002.
[3] 苑玮琦, 李绍丽, 李德健. 基于纹理主、旁瓣特征的雪糕棒裂缝缺陷检测[J]. 仪器仪表学报, 2017, 38(11): 2779-2787.
[4] 李克斌, 余厚云, 周申江. 基于形态学特征的机械零件表面划痕检测[J]. 光学学报, 2018, 38(8): 0815127.
[9] Hu G H, Wang Q H. Fabric defect detection via un-decimated wavelet decomposition and Gumbel distribution model[J]. Journal of Engineered Fibers and Fabrics, 2018, 13(1): 15-32.
[10] 王庆香, 李迪, 张舞杰, 等. 软性电路板金面缺陷的无监督检测[J]. 光学精密工程, 2010, 18(4): 981-987.
[11] 王泽润, 方益明, 冯海林, 等. 木材节子缺陷检测与定位方法[J]. 激光与光电子学进展, 2018, 55(5): 051501.
[13] 陈广锋, 管观洋, 魏鑫. 基于机器视觉的冲压件表面缺陷在线检测研究[J]. 激光与光电子学进展, 2018, 55(1): 011501.
[14] 马艳. 边缘检测技术在PVC型材产品检测中的应用研究[D]. 杭州: 浙江工业大学, 2004: 19- 27.
MaY. The application research of PVC product inspection by edge detection[D]. Hangzhou: Zhejiang University of Technology, 2004: 19- 27.
[15] 龙晓薇. 基于图像视觉的PVC表面缺陷检测方法及应用[D]. 长沙: 中南大学, 2007: 9- 19.
Long XW. PVC surface defect detection method based on image vision and application[D]. Changsha: Central South University, 2007: 9- 19.
[16] 龙晓薇, 阳春华, 龙永红. PVC建材表面缺陷检测系统研究与设计[J]. 计算技术与自动化, 2010, 29(2): 46-50.
[18] Prabuwono AS, SulaimanR, Hamdan AR, et al. Development of intelligent visual inspection system (IVIS) for bottling machine[C]∥TENCON 2006 - 2006 IEEE Region 10 Conference, November 14-17,2006, Hong Kong, China. New York: IEEE, 2006: 343887.
[19] 张铮, 王艳萍, 薛桂香. 数字图像处理与机器视觉: Visual C++与Matlab实现[M]. 2版. 北京: 人民邮电出版社, 2014: 70- 72.
ZhangZ, Wang YP, Xue GX. Digital image processing and machine vision: implementation of Visual C++ and Matlab[M]. 2nd ed. Beijing: Posts and Telecommunications Press, 2014: 70- 72.
[20] 蒋笑笑, 张振军, 王耀南, 等. 基于灰度投影梯度扩散的PET满瓶快速检测[J]. 电子测量与仪器学报, 2016, 30(8): 1152-1159.
[21] 高红波, 王卫星. 一种二值图像连通区域标记的新算法[J]. 计算机应用, 2007, 27(11): 2776-2777, 2785.
Article Outline
李书华, 周亚同, 王丹, 何静飞, 张忠伟. 基于机器视觉的聚氯乙烯管材表面缺陷检测[J]. 激光与光电子学进展, 2019, 56(13): 131006. Shuhua Li, Yatong Zhou, Dan Wang, Jingfei He, Zhongwei Zhang. Surface Defect Detection of Polyvinyl Chloride Pipes Based on Machine Vision[J]. Laser & Optoelectronics Progress, 2019, 56(13): 131006.