杂质对氧化锆热障涂层性能的影响
热障涂层(Thermal Barrier Coatings, TBCs)已在发动机燃烧室、高压涡轮叶片等热端部件上得到广泛应用。由于TBCs具有优异的隔热能力, 能够提高部件工作温度, 并减少所需的冷却气量, 从而可有效地提高发动机效率、减少排放、提高推重比[1]。目前应用最多的TBCs系统由金属粘结层和YSZ面层组成, YSZ因其导热系数低、在一定的工作条件下稳定性高、热膨胀系数和韧性适宜, 是迄今为止最成熟的TBCs面层材料。而不断提高热障涂层的高温稳定性和使用寿命是研究的共同目标[2]。
通过改进热障涂层材料体系[1,3-6]、优化涂层结构[1,3,7]、采用新型喷涂技术[7,8]可有效提升热障涂层的性能。其中, 低杂质含量的高纯度热障涂层[2,5,9-10]因具有更好的抗烧结性、更长的耐热冲击寿命而被广泛关注。热障涂层的失效模式研究表明[11,12], TBCs在服役过程中发生烧结, 将显著降低涂层的隔热效果、应变容限及服役寿命[13,14,15]。Vaβen等[16]指出, 在1400 ℃下保温20 h, 高纯度YSZ涂层的烧结收缩率低于含Al2O3或SiO2的YSZ涂层。当Al2O3和SiO2含量在0.02wt%~0.12wt%范围时, YSZ涂层的烧结收缩率与Al2O3和SiO2含量成线性关系。Paul等[17]研究表明, 将高纯度YSZ和含有Al2O3、SiO2杂质的YSZ涂层在1400 ℃下进行热处理, 当杂质含量从0.1wt%~0.2wt%下降到0.01wt%~0.05wt%时, 涂层的烧结速率显著降低。Xie等[18]提出杂质含量的增加会加速相的分解。Helminiak等[19]也认为, 高纯度YSZ涂层的相变速率显著低于杂质含量高的涂层。然而以上研究中的杂质含量无可比性, 仅说明当YSZ涂层中存在SiO2或Al2O3杂质时显著影响涂层的性能, 但对杂质与涂层性能的定量关系尚未给出规律性的说明, 对杂质含量增加或减少时涂层性能的变化未做深入研究。因此, 只有明确杂质含量与涂层性能之间的定量或半定量关系, 并给出杂质含量的控制极限, 才有助于YSZ涂层材料及涂层的成分设计和杂质含量的控制。
本研究设计了系列含低熔点氧化物杂质SiO2、Al2O3、Fe2O3的YSZ热障涂层, 杂质含量范围为小于0.01wt%~1.00wt%。研究了系列涂层的抗热震性、等温时效后的微观结构变化和隔热性能, 并探究了杂质对涂层性能的影响机制。通过研究杂质含量与YSZ涂层性能之间的关系给出控制杂质含量极限的建议。
1 实验方法
1.1 制备喷涂粉末材料
采用喷雾干燥-烧结方法制备YSZ粉末。将高纯度纳米级YSZ粉末(化学成分见表1)与杂质氧化物纳米粉末(纯度>99.9wt%)按设计比例(表2)进行湿法球磨24 h。YSZ粉末的平均粒径为60 nm, 氧化物粉末的平均粒径为30 nm, 团聚YSZ粉末的粒度范围为25~63 μm。
表 1.
YSZ原料的化学成分(wt%)
Table 1. Chemical composition of YSZ raw materials (wt%)
|
表 2.
YSZ喷涂粉末的设计成分(D)及涂层的实测成分(M)(wt%)
Table 2. Design composition (D) of YSZ powders and measured composition (M) of YSZ coatings (wt%)
|
1.2 制备涂层
采用超音速火焰喷涂(High-Velocity Oxygen- Fuel, HVOF)制备Ni23Co25Cr6Al0.6Y粘结层, 设计厚度100 μm, 工艺参数见表3。采用大气等离子喷涂(Air Plasma Spraying, APS)制备面层, 厚度为250~ 300 μm, 工艺参数见表4。由APS制备用于测试热扩散系数和进行高温热处理的单层YSZ涂层, 厚度为1.00~1.25 mm。采用KSL-1700X型电炉进行涂层热处理试验, 以5 ℃/min的速度升温至保温温度, 保温一定时间后随炉冷却。YSZ面层中杂质的实测成分如表2所示, 可以看出, 涂层中杂质含量较设计值有所降低, 这是由于制备粉末过程中产生的误差及喷涂过程中的烧损造成的。涂层中的杂质含量基本处于同一数量级水平, 因此可采用设计成分进行对比。
表 3.
HVOF喷涂工艺参数
Table 3. Parameters of HVOF process
|
表 4.
APS喷涂工艺参数
Table 4. Parameters of APS process
|
1.3 微观结构表征及性能测试
采用日立SU5000型扫描电镜分析形貌, 采用日本电子JEM2100型透射电镜分析结构。根据ASTM E 2109 B测试孔隙率。采用Netzsch LFA 427型激光热导仪测量YSZ涂层的热扩散系数, 测试方法参照ASTM E1461。测量前, 将涂层加热到1400 ℃保温2 h(升温速度5 ℃/min)后随炉冷却。
涂层抗热震性能的测试过程如下: 将涂层试样置入1100 ℃箱式电炉保温10 min后, 取出投入约25 ℃的纯净水中保持60 s, 如此反复循环, 直至涂层剥落面积达到总面积的5%时视为涂层热震失效。
2 结果与讨论
2.1 显微形貌及孔隙率
图1为S1样品(见表2)的喷涂态涂层横截面的典型微观形貌, 可以看出YSZ面层为典型的层状结构, 夹杂部分未熔粉末的微细颗粒。
对不同杂质含量的YSZ涂层在1400 ℃下保温100 h后的孔隙率进行对比, 如图2所示。涂层经热处理后孔隙率均随氧化物杂质含量的增加而降低。当杂质含量低于0.01wt%时, 涂层的孔隙率均在6.5%~7.5%范围内。当Al2O3含量从0.01wt%增加至0.10wt%、SiO2和Fe2O3含量从0.01wt%增加至0.20wt%时, 涂层孔隙率显著降低, 分别降低了0.733%、1.053%和1.500%。当以上杂质含量继续增加至0.65wt%, 即含量增加了0.45wt%~0.55wt%时, 孔隙率降幅减缓, 分别仅降低了0.694%、0.537%和1.15%。杂质含量继续增加至1.00wt%时, 含SiO2涂层的孔隙率下降相对显著, 降低了1.749%。说明在高温条件下, 杂质含量在较低水平范围内变化时, Al2O3含量在小于0.01wt%~0.10wt%范围内、SiO2和Fe2O3含量在小于0.01wt%~0.20wt%范围内时, 涂层孔隙率显著降低。在杂质含量相对较高时, SiO2对涂层孔隙率的影响较为显著。
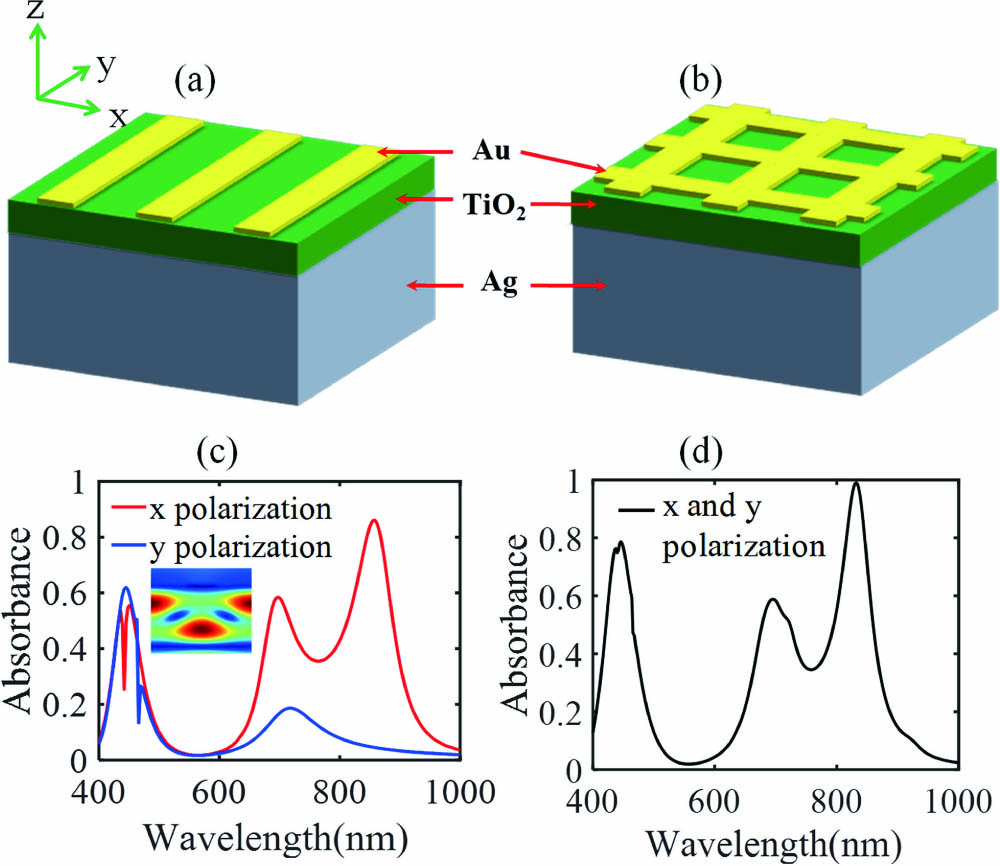
图 2. 1400 ℃热处理100 h后YSZ涂层的孔隙率
Fig. 2. Porosities of YSZ coatings heat-treated at 1400 ℃ for 100 h
为了比较不同氧化物杂质在高温下促进YSZ涂层致密化行为的差异, 对杂质含量均为1wt%的涂层, 在不同温度和不同保温时间下进行热处理, 涂层的孔隙率如图3所示。
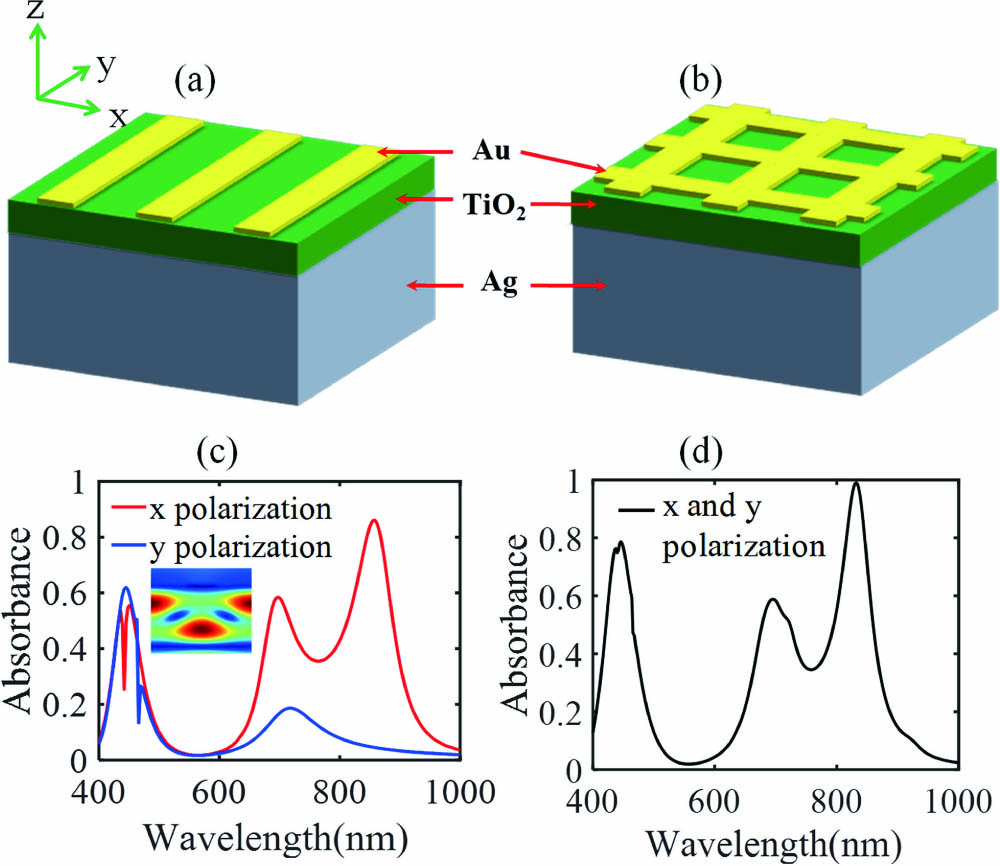
图 3. 不同热处理条件下含1wt%氧化物YSZ涂层的孔隙率
Fig. 3. Porosities of YSZ coatings doped with 1wt% oxides after heat treatment
从图3可以看出, 高纯度涂层的孔隙率随热处理温度的升高和热处理时间的延长发生的变化率最小。含SiO2杂质YSZ涂层的孔隙率随热处理温度的升高和热处理时间的延长显著降低, 表明该涂层具有更明显的烧结性[16]。含Al2O3杂质YSZ涂层的孔隙率与之相似, 但是下降幅度较为平缓。含Fe2O3杂质YSZ涂层的孔隙率在不同温度和保温时间条件下波动明显, 且对热处理时间更为敏感。涂层孔隙率可表征涂层在高温下的烧结状态[18], 以上结果表明, SiO2和Fe2O3对涂层使用温度和使用寿命产生影响。
2.2 热扩散系数
不同杂质含量的YSZ涂层在1200 ℃的热扩散系数如图4所示。热扩散系数是反映涂层隔热性能的重要参量。由图4可知, YSZ涂层的热扩散系数随SiO2、Fe2O3含量的增加而增大。这与高温处理后不同SiO2、Fe2O3含量的YSZ涂层的烧结状态有关。
涂层的热扩散系数通常是涂层固有导热性和微观结构(如涂层孔隙率)的共同效应[20,21]。根据Wang等[22]的研究结果, 涂层中孔隙率对传热的影响最大。涂层中存在的微裂纹和微气孔会大大降低涂层的热扩散系数, 提高涂层隔热性能[21]。而涂层热扩散系数的增大主要是由于1400 ℃下SiO2、Fe2O3促进了涂层的烧结和致密化[23,24]。根据涂层孔隙率的结果, 随着SiO2、Fe2O3含量的增加, 孔隙率降低, 涂层更加致密, 导致涂层热扩散系数增大。随杂质含量的增加, 含SiO2涂层的热扩散系数变化率大, 这与高温处理后含SiO2涂层较大的孔隙率变化率相一致。而含有Al2O3的YSZ涂层热扩散系数随Al2O3含量增加表现出先降低后升高的趋势。当在YSZ中加入Al2O3时, 由于Al3+比Y3+和Zr4+轻, 这导致在YSZ的Y3+或Zr4+位置处由Al3+取代产生质量缺陷, 这个缺陷会造成一个声子散射中心, 增强材料的隔热性能[24]。当Al2O3含量增加到一定程度时, 由于加入到涂层中的杂质促进了烧结, 提高了涂层的致密度[18], 而这种效应对高温下涂层的热性能起着更重要的作用[20], 进而引起涂层热扩散系数的升高。
2.3 热震寿命
含有SiO2、Al2O3、Fe2O3杂质的YSZ涂层平均热震寿命如图5所示。当杂质含量均小于0.01wt%时, 涂层热震寿命均约为130次。随着杂质含量的增加, 热震寿命均呈下降趋势。
当杂质含量从小于0.01wt%增加至0.02wt%时, 涂层热震寿命降幅明显。SiO2、Fe2O3含量增加至0.10wt%以上时涂层热震寿命降幅减缓。同样的现象也发生在Al2O3[25]含量达到0.2wt%以上时, 涂层热震寿命降幅减缓。低熔点杂质会缩短YSZ涂层的热震寿命, 这与Xie等[18]对比高纯度与含杂质的YSZ涂层热循环寿命结果一致。同时, 杂质含量越低时, 杂质含量的变化对YSZ涂层的热震寿命影响越显著。这与本研究中涂层在高温条件下的孔隙率变化情况一致。当Al2O3含量在0.02wt%~0.15wt%之间时, 涂层热震寿命下降缓慢, 热震次数变化出现一个范围较窄的平台, 随后当Al2O3含量继续增加至0.2wt%时, 涂层热震寿命显著降低, 这是由于原料Al2O3粉末有团聚现象, 未能均匀、分散地填充至YSZ体系中, 未起到促进离子扩散的作用。
2.4 透射电镜形貌
采用透射电镜观察了S10、A10涂层在热处理前后的微观组织变化, 如图6和图7所示, 分别为S10、A10涂层喷涂态及经过1400 ℃/10 h热处理后涂层的透射电镜照片及衍射斑点。
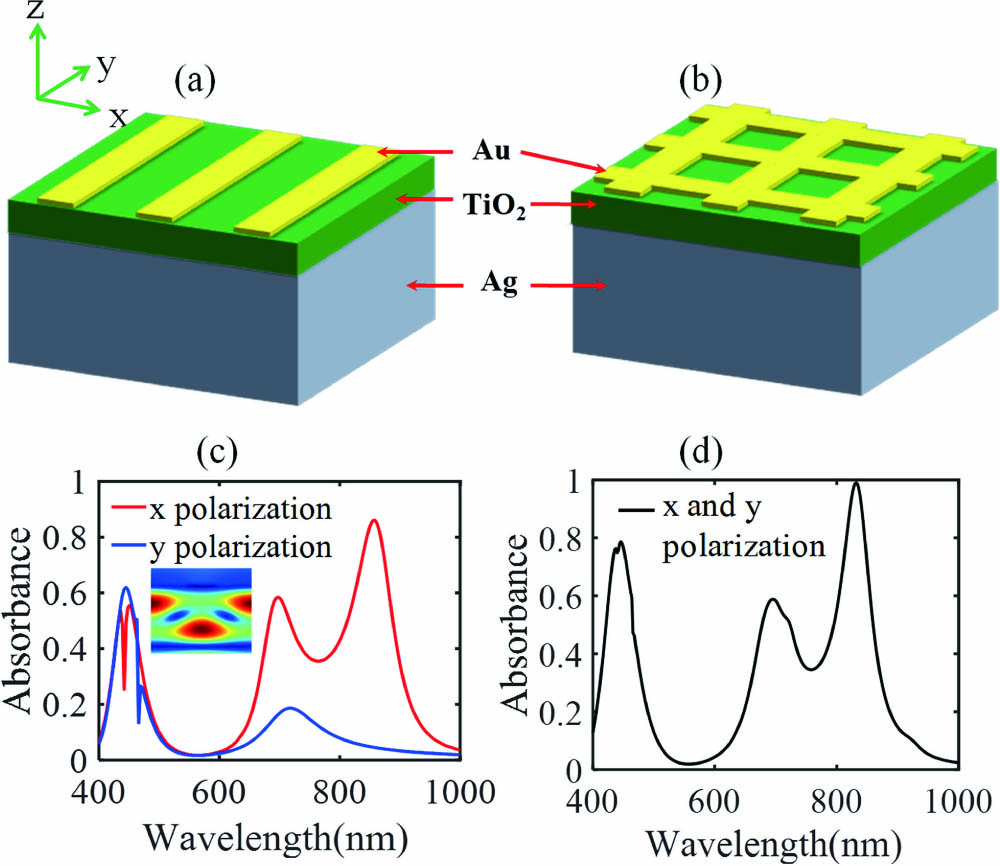
图 6. 含1wt% SiO2YSZ涂层的(a)喷涂态及(b)经1400 ℃热处理10 h后的TEM照片及衍射斑点
Fig. 6. TEM microstructures and diffraction spots of YSZ coatings doped with 1wt% SiO2
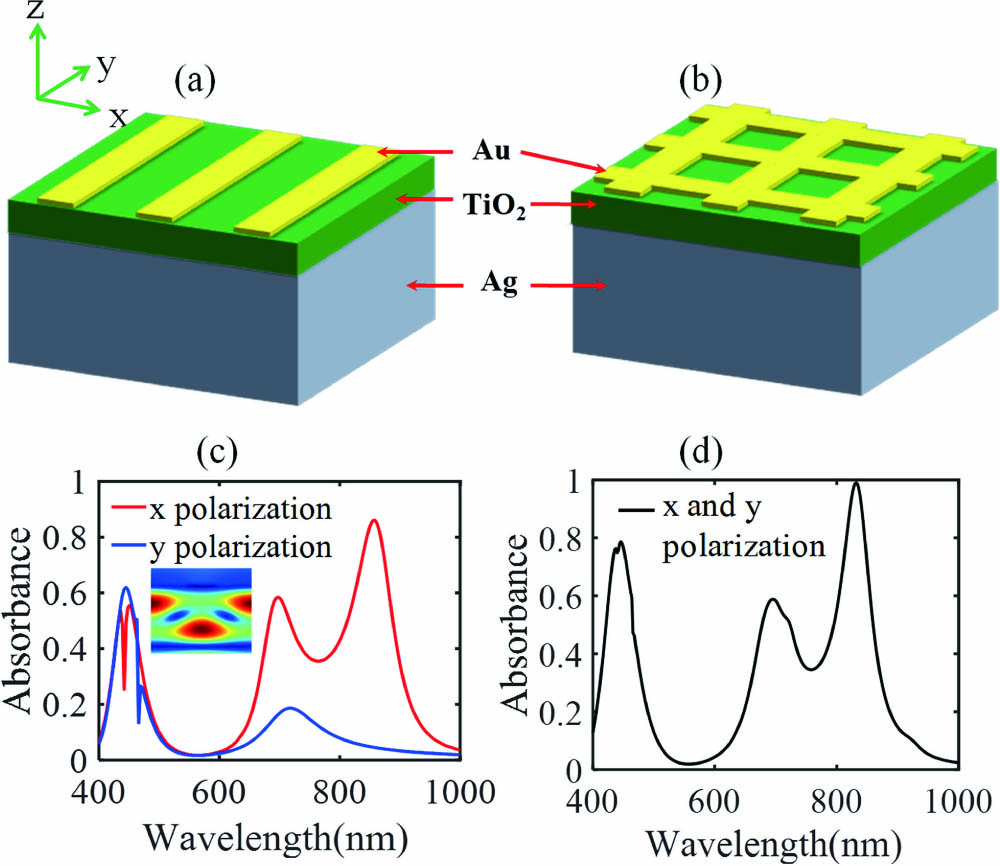
图 7. 含1wt% Al2O3的YSZ涂层的(a)喷涂态及(b)经1400 ℃热处理10 h后的TEM照片及衍射斑点
Fig. 7. TEM microstructure and diffraction spots of YSZ coatings doped with 1wt% Al2O3
如图6所示, S10涂层喷涂态的晶粒大小约为200~300 nm, 热处理后晶粒明显长大, 约为600~ 800 nm。图6(b)中间狭长白亮区域为非晶态SiO2, 在晶界处富集并在高温形成玻璃相, 使晶界变得圆滑[26]。涂层经过热处理后, 由立方相部分转变为单斜相, 通过计算发现, 立方相晶格参数由喷涂态时的0.5115 nm缩小至热处理后的0.5057 nm, 说明部分SiO2进入ZrO2晶格中, 由于Si的原子半径较小, 使晶格发生畸变。而这种含有Si、Y、Zr的共晶化合物熔点较低, 这也是加速涂层在高温下烧结的原因[27]。
如图7所示, A10涂层喷涂态的晶粒大小约为200 nm, 这与含SiO2的涂层类似, 而热处理后晶粒明显长大, 约为600 nm~1 μm。文献表明[28,29], YSZ体系中晶粒长大过程受阳离子扩散过程的影响, 部分Al3+离子替代Zr4+离子, 为了维持电荷平衡, 阳离子空位浓度及间隙浓度增加, 而间隙浓度为氧化锆中扩散速率的控制环节, 进而促进晶粒长大, 并改善了固相烧结[30]。
3 结论
本研究设计制备了分别含有(小于1.00wt%)SiO2、Al2O3、Fe2O3低熔点氧化物的YSZ热障涂层, 并对涂层的微观形貌、抗热震性能和陶瓷层的导热性能进行了分析, 就低熔点氧化物对YSZ热障涂层性能的影响得出以下结论:
1) 对YSZ陶瓷面层经过不同条件热处理后的截面孔隙率的分析发现, 随着低熔点氧化物杂质含量的增加, 高温下涂层孔隙率下降明显, SiO2对涂层服役温度和时间均敏感, Fe2O3对涂层服役时间更敏感, SiO2和Fe2O3易对涂层的使用温度和服役寿命产生不利影响。
2) 低熔点氧化物影响涂层的烧结程度, 从而影响涂层的导热性。
3) 随着低熔点氧化物含量的增加, 涂层的热震寿命缩短。综合考虑氧化物杂质对涂层微观形貌及热震性能的影响, 在YSZ热障涂层中, 控制SiO2、Fe2O3、Al2O3的含量在0.10wt%以下, 尤其是控制在0.01wt%以下时, 涂层抗热震性及隔热性能更优异。
[2] CURRY N, MARKOCSAN N, LI X H, et al. Next generation thermal barrier coatings for the gas turbine industry[J]. Journal of Thermal Spray Technology, 2011, 20(1/2): 108-115.
[3] STӦVER D, PRACHT G, LEHMANN H, et al. New material concepts for the next generation of plasma-sprayed thermal barrier coatings[J]. Journal of Thermal Spray Technology, 2004, 13(1): 76-83.
[4] XUE Z L, GUO H B, GONG S K, et al. Novel ceramic materials for thermal barrier coatings[J]. Journal of Aeronautical Materials, 2018, 38(2): 10-20.
[5] CURRY N, JANIKOWSKI W, PALA Z, et al. Impact of impurity content on the sintering resistance and phase stability of dysprosia- and yttria-stabilized zirconia thermal barrier coatings[J]. Journal of Thermal Spray Technology, 2014, 23(1/2): 160-169.
[6] LYU G, CHOI B G, LU Z, et al. Effect of thermal cycling frequency on the durability of Yb-Gd-Y-based thermal barrier coatings[J]. Surface & Coatings Technology, 2019, 364: 187-195.
[7] GORAL M, KOTOWSKI S, NOWOTNIK A, et al. PS-PVD deposition of thermal barrier coatings[J]. Surface & Coatings Technology, 2013, 237: 51-55.
[8] ŁATKA L. Thermal barrier coatings manufactured by suspension plasma spraying- a review[J]. Advances in Materials Science, 2018, 18(3): 95-117.
[9] JONNALAGADDA K P, ERIKSSON R, LI X H, et al. Thermal barrier coatings: life model development and validation[J]. Surface & Coatings Technology, 2019, 362: 293-301.
[10] PARK H M, JUN S H, LYU G, et al. Thermal durability of thermal barrier coatings in furnace cyclic thermal fatigue test: effects of purity and monoclinic phase in feedstock powder[J]. Journal of the Korean Ceramic Society, 2018, 55(6): 608-617.
[11] KARLSSON A M. Modeling failures of thermal barrier coatings[J]. Key Engineering Materials, 2007, 333: 155-166.
[12] HUA J J, ZHANG L P, LIU Z W, et al. Progress of research on the failure mechanism of thermal barrier coatings[J]. Journal of Inorganic Materials, 2012, 27(7): 681-686.
[13] MATSUI K. Sintering kinetics at constant rates of heating: mechanism of silica-enhanced sintering of fine zirconia powder[J]. Journal of the American Ceramic Society, 2008, 91(8): 2534-2539.
[14] TSIPAS S A, GOLOSNOY I O, DAMANI R, et al. The effect of a high thermal gradient on sintering and stiffening in the top coat of a thermal barrier coating system[J]. Journal of Thermal Spray Technology, 2004, 13(3): 370-376.
[15] CHOI S R, ZHU D M, MILLER R A. Effect of sintering on mechanical properties of plasma-sprayed zirconia-based thermal barrier coatings[J]. Journal of the American Ceramic Society, 2005, 88(10): 2859-2867.
[16] VAβEN R, CZECH N, MALLÉNER W, et al. Influence of impurity content and porosity of plasma-sprayed yttria-stabilized zirconia layers on the sintering behaviour[J]. Surface and Coatings Technology, 2001, 141: 135-140.
[17] PAUL S, CIPITRIA A, GOLOSNOY I O, et al. Effects of impurity content on the sintering characteristics of plasma-sprayed zirconia[J]. Journal of Thermal Spray Technology, 2007, 16(5/6): 798-803.
[19] HELMINIAK M A, YANAR N M, PETTIT F S, et al. The behavior of high-purity, low-density air plasma sprayed thermal barrier coatings[J]. Surface & Coatings Technology, 2009, 204: 793-796.
[20] MARKOCSAN N, NYLÉN P, WIGREN J, et al. Low thermal conductivity coatings for gas turbine applications[J]. Journal of Thermal Spray Technology, 2007, 16(4): 498-505.
[21] ZHU D M, MILLER R A. Development of advanced low conductivity thermal barrier coatings[J]. International Journal of Applied Ceramic Technology, 2004, 1(1): 86-94.
[22] WANG L, WANG Y, SUN X G, et al. Influence of pores on the thermal insulation behavior of thermal barrier coatings prepared by atmospheric plasma spray[J]. Materials and Design, 2011, 32: 36-47.
[23] ZHU D M, MILLER R A. Thermal conductivity and elastic modulus evolution of thermal barrier coatings under high heat flux conditions[J]. Journal of Thermal Spray Technology, 2000, 9(2): 175-180.
[24] ZHU D M, MILLER R A, NAGARAJ B A, et al. Thermal conductivity of EB-PVD thermal barrier coatings evaluated by a steady- state laser heat flux technique[J]. Surface and Coatings Technology, 2001, 138: 1-8.
[25] LI Y J, YU Y G, JI X J, et al. Effects of Al2O3 content on properties of YSZ thermal barrier coatings[J]. Thermal Spray Technology, 2018, 10(1): 61-67.
[26] GREMILLARD L, EPICIER T, CHEVALIER J, et al. Microstructural stucy of silica-doped zirconia ceramics[J]. Acta Materialia, 2000, 48: 4647-4652.
[27] HODGSON S N B, CAWLEY J, CLUBLEY M. The role of SiO2 impurities in the microstructure and properties of Y-TZP[J]. Journal of Materials Processing Technology, 1999, 86: 139-145.
[28] MATSUI K, YOSHIDA H, IKUHARA Y. Phase-transformation and grain-growth kinetics in yttria-stabilized tetragonal zirconia polycrystal doped with a small amount of alumina[J]. Journal of the European Ceramic Society, 2010, 30: 1679-1690.
[29] SAKKA Y, ISHII T, SUZUKI T S, et al. Fabrication of high-strain rate superplastic yttria-doped zirconia polycrystals by adding manganese and aluminum oxides[J]. Journal of the European Ceramic Society, 2004, 24: 449-453.
Article Outline
冀晓鹃, 于月光, 卢晓亮. 杂质对氧化锆热障涂层性能的影响[J]. 无机材料学报, 2020, 35(6): 669. Xiaojuan JI, Yueguang YU, Xiaoliang LU.