利用FBG传感器监测拉索断丝信号的实验研究
下载: 505次
1 引言
拉索内部的钢绞线是索体系桥梁的主要受力承载构件,其应力分布状态是评价索体系桥梁健康状况的重要指标。索体系桥梁[1-2]中的拉索断裂会导致部分拉索承载力失效,带来重大安全事故和经济损失,如斜拉桥中的斜拉索断裂原因主要是热缩双壁PE护套破坏引起的钢材锈蚀和钢材本身的疲劳。因此,实时监测拉索内部钢绞线是否断丝非常重要。
常用于检测拉索内部断丝的技术主要有外观检查法、磁通量检测法和索力测定法等[3-5]。外观检查法是有经验的技术人员通过观察拉索表面有无缝隙判定拉索有无损伤,这种方法具备投资少、操作简单的优点,但耗时长且无法准确识别损伤。磁通量检测法根据磁化金属(钢绞线或钢丝)中的磁通量变化判定拉索是否断丝。如辛荣亚等[6-8]利用磁通量检测法检测拉索中钢丝纵向是否有断丝信号并确定断丝损伤程度和断丝点位置,取得了较好的结果,但该方法易受电磁干扰,且存在磁极老化等缺点。压力表索力测定法、频率索力测定法等只能测量拉索整体的大致索力,无法准确反映拉索内部钢丝的实际健康状况,存在一定的局限性。
用上述方法监测拉索健康状态时均不满足现代大跨度索类工程结构对索力内部监测的需求。光纤布拉格光栅(FBG)传感器自问世以来,就被国内外学者广泛应用于桥梁工程领域[9-12]。如:加拿大的Beddington Trail大桥使用FBG传感器进行应力测量并长期监测桥梁结构[13];国内的东洲湘江大桥采用FBG传感器进行长期健康状况监测[14]。FBG传感器具有体积小、质量轻、抗电磁干扰能力强以及可远程实时监测等优点,目前将FBG传感器应用于工程领域的相关技术已较为成熟,但利用FBG传感器对桥梁拉索内部断丝信号进行实时监测的研究较少。因此,本文利用FBG传感器监测拉索索力的方法对由19束钢绞线组成的拉索断丝信号进行实验研究。
2 FBG传感器
FBG传感器通过外界参量变化对自身中心波长的调制实现传感。由衍射原理可知,当一束光进入光栅时,只有某种特定波长的光被反射,其余波长的光则会穿过光栅继续向前传输,如
被光栅反射的光波波峰对应的波长
式中:
式中:
将
式中,
式中:
在荷载没有变化的情况下,受力面积的变化会导致拉索的应力产生变化。因此,将FBG应变传感器内嵌预压至钢绞线中心丝制成自感知钢绞线。自感知钢绞线受外荷载作用产生应变,传递给嵌入钢绞线中心丝的FBG传感器,引起
3 拉索断丝实验研究
3.1 实验设计
用机械打散钢绞线取出中心丝,在中心丝上设置深为1 mm、宽为1 mm的凹槽,对中心丝进行张拉,在持荷状态下用环氧树脂将FBG应变传感器粘贴于凹槽内,粘贴长度关于光栅所在位置中心对称,且不小于40 mm。当环氧树脂达到足够强度时,卸载中心丝制备得到智能中心丝,再将智能中心丝与边丝扭绞成自感知钢绞线,如
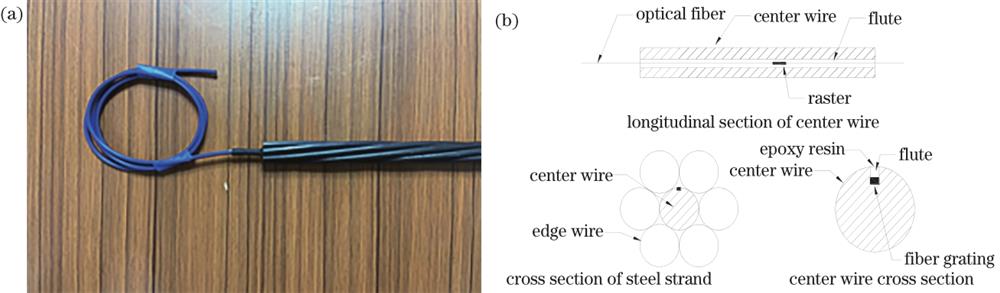
图 2. 自感知钢绞线的结构。(a)实物图;(b)原理图
Fig. 2. Structure of self-sensing steel strand. (a) Physical drawings; (b) schematic diagram
实验采用的钢绞线为1×7标准型,由1根直径为5.2 mm的中心丝和6根直径为5.0 mm的边丝绕中心丝扭绞而成,标准强度fpk=1860 MPa,极限承载力为260.4 kN,公称直径为15.2 mm,公称面积为140 mm2,弹性模量EP=1.95×105 MPa。FBG的中心波长范围为1536~1560 nm,裸光栅长度为1 cm,FBG传感器的带宽为0.3 nm,反射率大于等于85%。解调仪为HCM4CH100HZ-1光谱仪,采样频率为100 Hz,波长精度为2.5 pm,分辨率为1 pm。环氧树脂的弹性模量大于2.5 GPa。
取长为5 m的普通低松弛预应力钢绞线(1×7标准型)57束,共分三组实验,每组由19束钢绞线组成,如
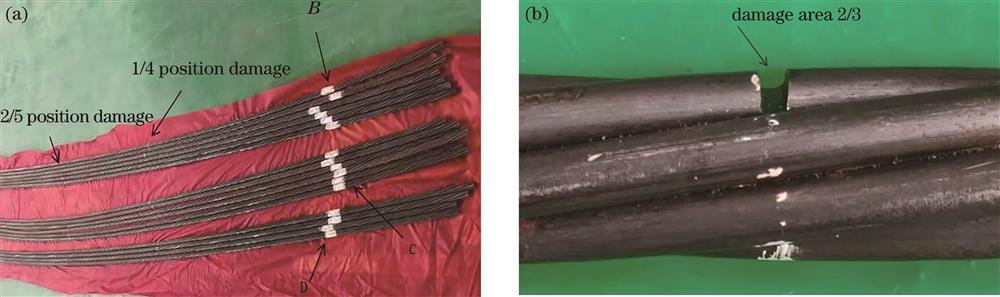
图 3. 普通钢绞线的损伤位置分布。(a)每组钢绞线的损伤位置;(b)B11钢绞线2/3单股的损伤面积
Fig. 3. Damage location distribution of common steel strands. (a) Damage location diagram of each set of steel strand; (b) damage area of single strand of B11 steel strand 2/3
表 1. 每组各试件的边丝损伤情况
Table 1. Edge wire damage of each group of specimens
|
3.2 实验方案及加载方式
采用19束钢绞线组成拉索共进行三组实验,钢绞线在锚具板中的分布如
4 实验数据整理与分析
实验过程中,自动预紧钢绞线后,手动缓慢进行加载,钢绞线索力达到648.135 kN时,钢绞线发生断丝,停止手动加载,确定钢绞线断丝类型,然后继续缓慢手动加载,直至有损伤的钢绞线全部断裂,如
为确认自感知传感器能否识别拉索张拉过程中的断丝信号,探讨了拉索损伤面积和损伤位置与断丝信号强弱的关联性,通过传感器实时采集数据。为方便研究,实验中只讨论了B型、D型两种试件,每组试件均采取200个数据进行绘图。B11、D12、D22试件(第一组)断丝信号的变化曲线如
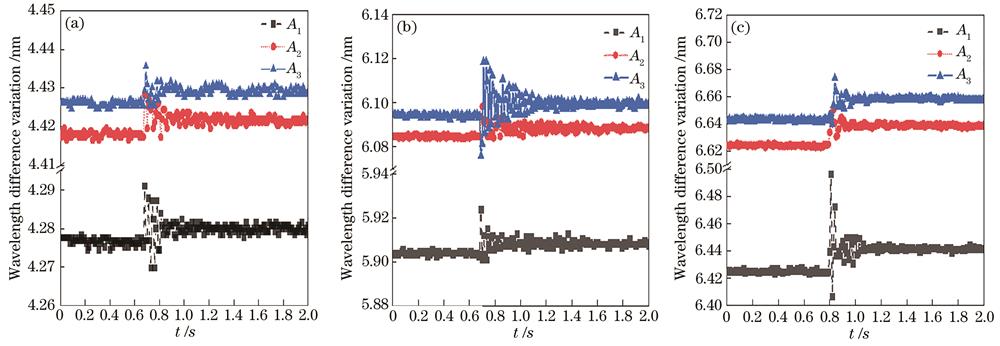
图 7. 第一组试件加载过程中的断丝信号变化。(a)B11;(b)D12;(c)D22
Fig. 7. Changes of broken wire signal of the first group of specimens in loading process. (a) B11; (b) D12; (c) D22
表 2. B11试件断丝时的数据
Table 2. Data of B11 specimen wire breaking
|
表 3. D12试件断丝时数据
Table 3. Data of D12 specimen wire breaking
|
表 4. D22试件断丝时数据
Table 4. Data of D22 specimen wire breaking
|
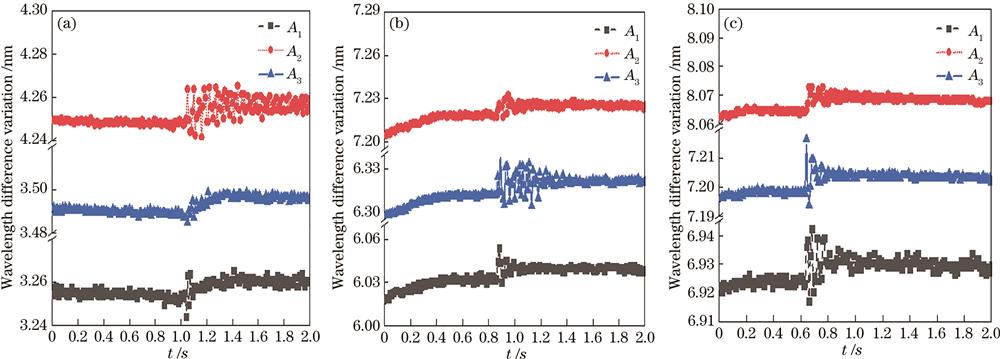
图 8. 第二组试件加载过程的断丝信号变化。(a)B11;(b)D12;(c)D22
Fig. 8. Changes of broken wire signals of the second group of specimens in loading process. (a) B11; (b) D12; (c) D22
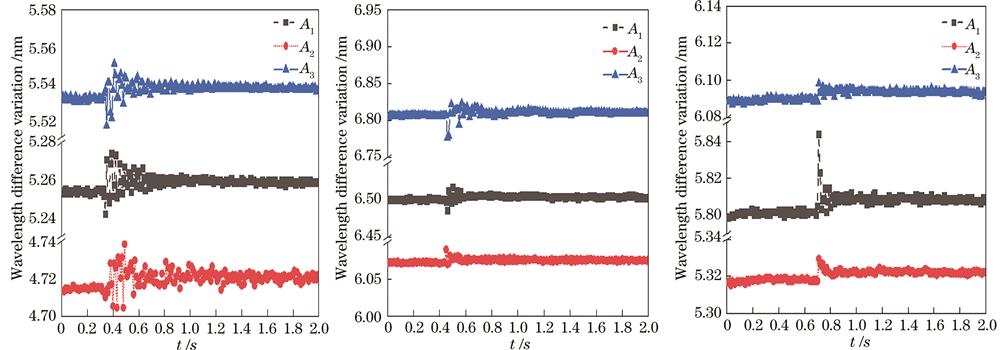
图 9. 第三组试件加载过程的断丝信号变化。(a)B11;(b)D12;(c)D22
Fig. 9. Changes of broken wire signal of the third group of specimens in loading process. (a) B11; (b) D12; (c) D22
从
根据各试件被自感知采集到的断丝数据,抽取第一组断丝试件B11、第二组断丝试件D12、第三组断丝试件D22的数据如
根据每组试件加载过程的断丝信号变化图和断丝数据可知:各自感知钢绞线能全程监测拉索实时受力情况,存活率为100%;各自感知钢绞线都能准确识别到所有钢绞线断丝信号;各自感知钢绞线识别到断丝信号的起始时间相同,结束时间基本一致,且监测到断丝信号时间非常短,仅为0.07~0.23 s;各自感知钢绞线采集的断丝信号强弱与普通钢绞线在锚具板中断裂区域位置有关。自感知钢绞线临近位置断裂的钢绞线采集的信号较强,且各自感知钢绞线采集到的断丝信号强弱与普通钢绞线损伤位置和程度有关:当损伤位置相同时,损伤程度越小,采集的断丝信号越强;当损伤程度相同时,损伤位置距端部越近,采集的信号越强。此外,当各自感知钢绞线采集到的信号波峰差值Δλ≥0.01 nm时,可作为断丝信号的识别值,且各自感知钢绞线识别到的断丝信号与自感知钢绞线中FBG的测点位置无关。
5 结论
针对现有拉索内部结构钢绞线的断丝现象,以FBG传感器为依托,提出一种内嵌FBG钢绞线监测整体拉索内部结构断丝信号的方法,并对19束钢绞线进行三组张拉试验监测。实验结果表明:各自感知钢绞线能准确识别每束钢绞线断丝时刻的断丝信号,且识别到的断丝信号与自感知钢绞线中FBG的测点位置分布无关;各自感知钢绞线采集的断丝信号时间段基本相同,当各自感知钢绞线采集到的信号波峰差值大于等于0.01 nm时可作为拉索断丝预警值。同时,FBG传感器采集到断丝信号的强弱与普通钢绞线损伤位置、损伤程度和断裂区域有关:当损伤位置相同时,损伤程度越小,自感知钢绞线采集的断丝信号越强;当损伤程度相同时,损伤位置距端部越近,自感知钢绞线采集的信号越强;当自感知钢绞线临近位置钢绞线断裂,自感知钢绞线采集的信号较强。
[1] 彭春阳, 李启富, 植磊, 等. 聚脲在悬索桥主缆防腐中的应用[J]. 施工技术, 2021, 50(3): 76-78.
Peng C Y, Li Q F, Zhi L, et al. Application of polyurea in anti-corrosion of main cable of suspension bridge[J]. Construction Technology, 2021, 50(3): 76-78.
[2] 李彦兵. 大跨径斜拉桥断索危害性研究[D]. 重庆: 重庆交通大学, 2013.
LiY B. Research of broken cable hazard for long scale cable-stayed bridge[D]. Chongqing: Chongqing Jiaotong University, 2013.
[3] 梁亚斌, 蔡思佳, 冯谦, 等. 基于无人机航拍的武汉天兴洲长江大桥桥索PE外观检测技术[J]. 大地测量与地球动力学, 2019, 39(11): 1207-1210.
Liang Y B, Cai S J, Feng Q, et al. Cable PE appearance inspection in the Tianxingzhou River Bridge using unmanned aerial vehicle based aerial photo technique[J]. Journal of Geodesy and Geodynamics, 2019, 39(11): 1207-1210.
[4] 贲安然. 在役平行钢丝拉索断丝漏磁检测方法及装置[D]. 武汉: 华中科技大学, 2012.
BenA R. Magnetic flux leakage testing method and tool for broken wires in parallel wire cables in service[D]. Wuhan: Huazhong University of Science and Technology, 2012.
[5] 刘志勇. 斜拉桥斜拉索索力测试方法综述[J]. 铁道建筑, 2007, 47(4): 18-20.
Liu Z Y. Testing method of cable force of cable-stayed bridge[J]. Railway Engineering, 2007, 47(4): 18-20.
[6] 辛荣亚, 张启伟, 李元兵. 桥梁拉索金属面积损失的磁通检测信号特征[J]. 同济大学学报(自然科学版), 2018, 46(10): 1326-1333, 1347.
Xin R Y, Zhang Q W, Li Y B. Characteristic of signal from magnetic flux examination of loss of metallic area in bridge cables[J]. Journal of Tongji University (Natural Science), 2018, 46(10): 1326-1333, 1347.
[7] 辛荣亚, 张启伟. 基于漏磁检测的桥梁拉索断丝识别[J]. 同济大学学报(自然科学版), 2019, 47(4): 458-466.
Xin R Y, Zhang Q W. Broken wire identification in bridge cables based on magnetic flux leakage examination[J]. Journal of Tongji University (Natural Science), 2019, 47(4): 458-466.
[8] 辛荣亚, 张启伟. 基于漏磁检测的桥梁拉索钢丝损伤评估[J]. 桥梁建设, 2019, 49(3): 51-56.
Xin R Y, Zhang Q W. Assessment of steel wire damages in bridge cables based on magnetic flux leakage examination[J]. Bridge Construction, 2019, 49(3): 51-56.
[9] 张俊. 光纤光栅传感器在桥梁振动监测中的应用研究[J]. 交通科技, 2016(6): 12-15.
Zhang J. Fiber Bragg grating sensor applied to bridge vibration monitoring[J]. Transportation Science & Technology, 2016(6): 12-15.
[10] 王天鹏, 周果子. 基于光纤光栅测力环的桥梁拉索索力监测及温度补偿研究[J]. 中外公路, 2017, 37(3): 112-117.
Wang T P, Zhou G Z. Research on cable force monitoring and temperature compensation of bridge based on fiber grating force measuring ring[J]. Journal of China & Foreign Highway, 2017, 37(3): 112-117.
[11] Tochaei E N, Fang Z, Taylor T, et al. Structural monitoring and remaining fatigue life estimation of typical welded crack details in the Manhattan Bridge[J]. Engineering Structures, 2021, 231: 111760.
[12] Sujon M, Dai F. Application of weigh-in-motion technologies for pavement and bridge response monitoring: state-of-the-art review[J]. Automation in Construction, 2021, 130: 103844.
[13] Rizkalla S H, Tadros G. Smart highway bridge in Canada[J]. Concrete International, 1994, 16(6): 42-44.
[14] 庞晰中. 基于光纤光栅的东洲湘江大桥索力实时监测系统[D]. 桂林: 桂林理工大学, 2020.
PangX Z. Real-time monitoring system of cable force of Dongzhou Xiangjiang Bridge based on fiber grating[D]. Guilin: Guilin University of Technology, 2020.
Article Outline
余文成, 骆小勇, 覃荷瑛. 利用FBG传感器监测拉索断丝信号的实验研究[J]. 激光与光电子学进展, 2023, 60(1): 0106003. Wencheng Yu, Xiaoyong Luo, Heying Qin. Experimental Study on Monitoring Cable Broken Wire Signal by FBG Sensor[J]. Laser & Optoelectronics Progress, 2023, 60(1): 0106003.