激光熔覆碳纳米管增强高熵合金涂层及耐腐蚀性能
The research of laser cladding CoCrFeNi high-entropy coating reinforced by carbon nanotubes (CNTs) is still limited. The corrosion resistance of a new CoCrFeNi-CNTs composite coating is highly necessary. However, solving the agglomeration problem of CNTs on raw powder surface is quite challenging and key in the laser cladding process of CoCrFeNi-CNTs composite coating. The microstructure and neutral salt spray corrosion resistance are highly important characteristics for studying laser cladding CoCrFeNi-CNTs composite coating.
CoCrFeNi and multi-walled CNTs raw powders are mixed by mechanical mixing method without milling ball. The optimized mixing parameters are CNT mass fraction of 1.0%, rotation speed of 240 r/min, mixing time of 10 h, drying time of 4 h, and argon gas protection. The CoCrFeNi-CNTs composite coating is fabricated on a 304 stainless steel substrate using a system platform consisting of a 6-axis industrial robot, a fiber laser, a powder feeder, and an alternating strategy with 90° rotation for each layer. The optimized laser cladding parameters are laser power of 870 W, laser scanning velocity of 12.5 mm/s, overlap rate of 50%, powder feeding rate of 8.7 g/min, layer thickness of 0.5 mm, and argon gas flow rate of 20 L/min. The macrostructural characteristics of the CoCrFeNi-CNTs composite coating is observed using an optical microscope (OM). The precipitated phases are detected using an X-ray diffraction (XRD). The microstructural features of the CoCrFeNi-CNTs composite powder and CoCrFeNi-CNTs composite coating are analyzed using a scanning electron microscope (SEM). The elemental distributions of grain, intergranular carbide eutectics, and inclusion in the CoCrFeNi-CNTs composite coating are investigated using an energy dispersive spectrometry (EDS). The distribution of CNTs in the CoCrFeNi-CNTs composite coating is further observed using a transmission electron microscope (TEM). The microhardness distribution from top to fusion line in the CoCrFeNi-CNTs composite coating is tested using a digital microhardness tester under the parameters of load of 100 g, dwell time of 15 s, and test position spacing of 0.1 mm. The neutral salt spray corrosion resistance of the CoCrFeNi-CNTs composite coating is tested using a salt spray corrosion test chamber under corrosion time of 36, 168, and 269 h.
The agglomeration problem of CNTs on CoCrFeNi raw powder surface is solved successfully through the mechanical mixing method [Figs.1(c) and (d)]. The original microstructural features of CoCrFeNi raw powder and CNTs are well protected as the energy is greatly reduced without using a milling ball (Fig.1). Then, the CoCrFeNi-CNTs composite coating with nice internal forming is prepared on 304 stainless steel by laser cladding (Fig.2). The grains of the CoCrFeNi-CNTs composite coating exhibit a single face-centered cubic (FCC) structure (Fig.3). According to the morphological difference, the grains can be divided into planar grain, cellular dendrite, columnar dendrite, and equiaxed grain (Fig.4). The M7C3 type carbide eutectics are formed at the grain boundaries [Fig.5(a)]. The undecomposed CNTs are dispersed within the grain [Fig.5(b)]. The Si/C inclusion is derived from the molten substrate material [Figs.4(c) and (d), Fig.6, and Table 3]. The hardness distribution in the CoCrFeNi-CNTs composite coating is uniform (Fig.7). Owing to the second phase strengthening effect of CNTs and M7C3 carbides, the hardness level can be increased by over 70 HV compared to that of the CoCrFeNi coating (Fig.7). After 269 h neutral salt spray corrosion, pitting occurs only in the area around the shed Si/C inclusion, but no corrosion is found in the grain or other area within the grain boundary (Fig.8).
The mechanical mixing method can effectively inhibit the agglomeration tendency of the CNTs on the surface of the CoCrFeNi powder, and the microstructures of the CoCrFeNi powder and CNTs are well protected, laying the foundation for the subsequent laser cladding process. The macro- and micro-forms of the CoCrFeNi-CNTs composite coating are good and no crack is observed. The pore diameters are not over 30 μm. The CoCrFeNi-CNTs composite coating exhibits a single face-centered cubic crystal structure. The grains can be divided into planar grain, cellular dendrite, columnar dendrite, and equiaxed grain in accordance with the morphological difference. After entering the coating molten pool, the CNTs are partially cleaved to free carbon, which is distributed within the grain boundaries and grains. The solution carbon at the grain boundary forms M7C3 type carbide eutectics with Cr. The other CNTs retain the original microstructure and disperse in the grain. The microhardness of the CoCrFeNi-CNTs composite coating is increased by over 70 HV by the multiple reinforcement of the intergranular M7C3 type carbide eutectics, in-grain CNTs, and solution carbon. The presence of M7C3 type carbide eutectics and CNTs will not significantly reduce the corrosion resistance of the CoCrFeNi-CNTs composite coating; however, the inclusion of Si/C in the coating from 304 stainless steel substrate will have an adverse effect on the corrosion resistance of the CoCrFeNi-CNTs composite coating. Pitting corrosion will be formed in the region of the dropped Si/C inclusion. Therefore, strictly restricting the inclusion of Si/C into the coating will further improve the corrosion resistance of the CoCrFeNi-CNTs composite coating.
1 引言
自Yeh等[1-2]提出一种全新的合金设计思想以来,高熵合金因其出色的力学性能及抗腐蚀性能,受到了学术界和工业界人士的广泛关注[3-6]。等原子比的CoCrFeNi高熵合金为面心立方(FCC)晶体结构[7-8],具有优异的低温力学性能[9],已经成为研究CoCrFeNiMn[10]、CoCrFeNiCu[11]、CoCrFeNiTi[12]等新型高熵合金的重要基础。然而,CoCrFeNi高熵合金的室温力学性能并不突出,严重限制了其在表面强化领域的应用潜力[13]。
近年来,碳的同素异构材料(如碳纳米管、石墨、石墨烯等)已经被广泛用于强化高熵合金涂层的研究[14-16]。Medina等[17]将石墨靶材作为碳源,采用磁控共溅射技术制备出碳含量可调的CoCrFeMnNiCx高熵合金薄膜,测试发现,当碳原子数分数(x)增加到11%时,薄膜的纳米压痕硬度提高到16 GPa,大幅高于无碳薄膜的8 GPa水平,耐腐蚀性能也得到进一步改善。Xiao等[18]以石墨烯作为碳源,采用等离子体烧结技术制备出不同碳含量的CoCrFeMnNiCx高熵合金块体,测试发现,当碳原子数分数增加到10.7%时,合金的显微硬度由327.8 HV大幅提高到566.4 HV,而磨损速率从6.5×10-5 mm3/(N·m)下降到0.47×10-5 mm3/(N·m)。Singh等[19]以碳纳米管作为碳源,采用等离子体烧结技术制备出不同碳含量的FeCoCrNiCuCx高熵合金块体,测试发现,当碳原子数分数增加到9.0%时,合金的腐蚀速率比之前减小了88.6%,继续增加碳含量则腐蚀速率又会增大。显然,采用等离子体烧结技术能够制备碳掺杂高熵合金块体,但难以实现基材上涂层的快速制备。磁控溅射技术虽然可以制备碳掺杂高熵合金涂层,但涂层厚度较薄,仍难以满足机械零部件在恶劣环境下的服役要求。
近年来,激光熔覆技术已经被广泛应用于合金涂层的快速制备。得益于激光束能量密度高的特点,利用该技术能够在熔池快速凝固过程中生成细小的晶粒组织,有助于提高合金涂层的力学性能[20-22]。研究人员已经尝试在激光熔覆CoCrFeNi系高熵合金涂层中添加适量Al、Mo、Si、B、Ti、Mn等元素以改善涂层的组织及力学性能[23-26]。Chen等[27]通过在激光熔覆CoCrFeNi高熵合金涂层中周期地添加适量Al元素,成功制备出FCC和体心立方(BCC)双相结构复合涂层,涂层的显微硬度得到改善。Li等[28]通过在激光熔覆CoCrFeNi高熵合金涂层中添加适量Ti元素,在涂层基体中原位生成了BCC结构晶间析出相和弥散分布的TiO2金属间化合物,涂层的显微硬度得到改善。但目前通过在激光熔覆CoCrFeNi高熵合金涂层中添加适当碳纳米管来实现涂层组织相变并改善显微硬度水平的研究仍然不足,针对激光熔覆CoCrFeNi-CNTs复合涂层的中性盐雾腐蚀行为研究依然较少。本文采用机械混合法代替高能球磨法,尝试解决碳纳米管的团聚问题,成功制备出CoCrFeNi-CNTs复合粉末原材料,最终通过激光熔覆技术成功制备出CoCrFeNi-CNTs高熵合金复合涂层,系统研究了新型高熵合金复合涂层的宏微观组织特征、显微硬度分布及其在中性盐雾条件下的腐蚀行为,为该类涂层未来的工业应用提供了参考。
2 试验材料及方法
激光熔覆试验采用的基板材料为304不锈钢,尺寸为200 mm×200 mm×9 mm,试验前使用砂纸和丙酮清理表面。将质量分数高于99.5%的Co、Cr、Fe、Ni按等物质的量混合,利用惰性气体雾化技术制备得到CoCrFeNi高熵合金粉末,以该粉末作为涂层基体材料,粒度范围为45~105 µm,实际测量的成分如
表 1. 高熵合金粉末实际测量成分
Table 1. Measured components of high-entropy alloy powder
|
表 2. 激光熔覆高熵合金复合涂层的优化工艺参数
Table 2. Optimized process parameters of laser cladding CoCrFeNi high-entropy alloy composite coating
|
以多壁的碳纳米管(CNTs)作为碳源,其最外层碳管直径范围为4~6 nm,长度范围为0.5~2.0 µm。碳纳米管属于纤维状一维纳米材料,表现出明显的强团聚效应,而且碳纳米管容易纠缠粘结在一起,因此碳纳米管在粉末表面的团聚问题难以解决[29-30]。在不使用磨球的情况下,机械混合方法能够大幅地减弱碳纳米管与CoCrFeNi粉体发生碰撞时产生的能量、热量和形变问题,碳纳米管能够充分地与CoCrFeNi粉体表面发生摩擦而逐渐被剥离,从而碳纳米管在CoCrFeNi粉体表面的团聚问题得到解决。因此,不使用磨球是实现这一过程的关键。基于以上原因,在不放入磨球的情况下,对CoCrFeNi粉末和碳纳米管进行机械混合,优化参数为:碳纳米管的质量分数为1.0%,转速为240 r/min,混合时间为10 h,混合后将粉末置于干燥箱内70 ℃下烘干处理4 h,罐内通入氩气防止粉末高温氧化。机械混合前后的CoCrFeNi粉末和碳纳米管形貌如
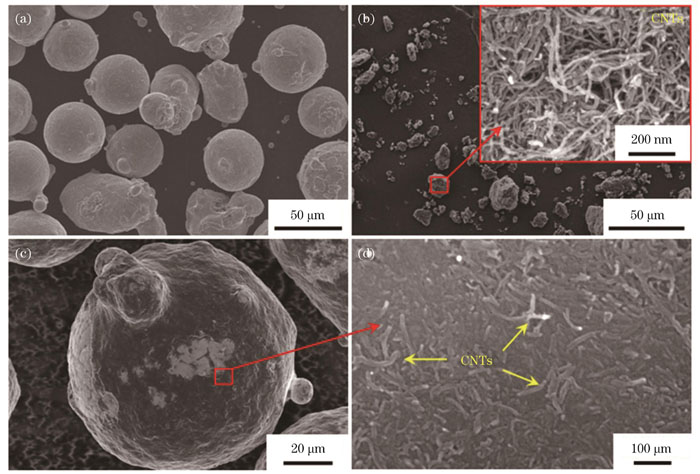
图 1. 机械混合前后CoCrFeNi粉末和碳纳米管的显微形貌。(a)CoCrFeNi粉末;(b)CNT粉末;(c)CoCrFeNi-CNTs粉末;(d)图1(c)局部放大
Fig. 1. Micromorphologies of CoCrFeNi powder and CNTs before and after mechanical mixing. (a) CoCrFeNi raw powder; (b) CNT raw powder; (c) CoCrFeNi-CNTs powder; (d) local magnification of Fig. 1 (c)
采用主要由光纤激光器、六轴工业机器人、送粉器组成的平台进行激光熔覆试验。为了减小304不锈钢基板元素对涂层化学成分的不利影响,设定熔覆沉积14层金属,采用交替扫描策略,每层扫描路径旋转90°,氩气保护,激光熔覆制备CoCrFeNi-CNTs复合涂层的过程及实际成形效果如
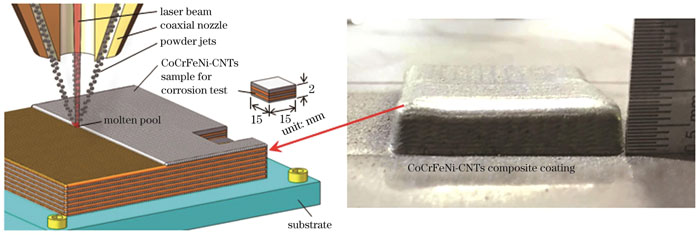
图 2. 激光熔覆制备CoCrFeNi-CNTs复合涂层过程示意及实物图
Fig. 2. Laser cladding diagram for preparing CoCrFeNi-CNTs composite coating and physical image
采用金相显微镜(OM)、扫描电镜(SEM)、能谱仪(EDS)对涂层截面的宏微观形貌、化学成分及分布进行分析。采用X射线衍射仪(XRD)对涂层内的物相组成进行分析。采用透射电镜(TEM)对涂层中碳纳米管的分布特征进行观察。采用电子显微硬度仪测量涂层截面内的硬度分布,从涂层截面的顶端向熔合线等间距进行测量,相邻测试点间隔0.1 mm,载荷为100 g,保载时间为15 s。采用盐雾腐蚀试验箱,对涂层进行连续中性盐雾测试,取样时间设定为36、168、269 h,采用扫描电镜对腐蚀前后涂层的微观形貌进行分析。中性盐雾测试的取样位置如
3 结果与分析
3.1 复合涂层的相结构
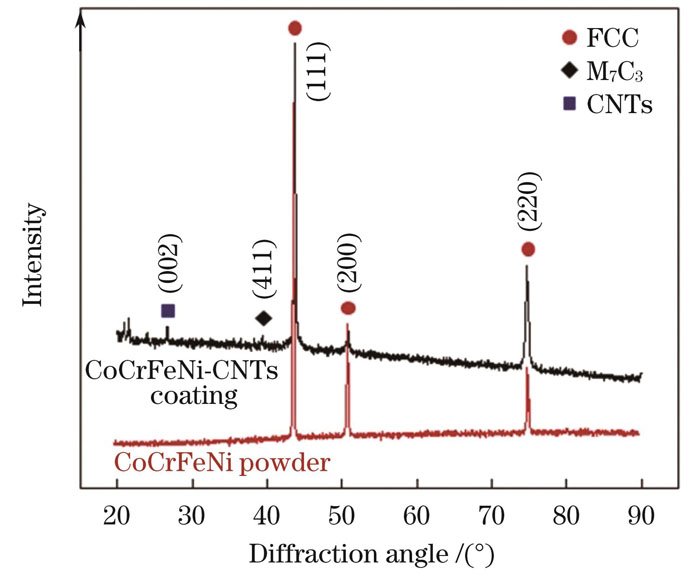
图 3. CoCrFeNi原粉末与CoCrFeNi-CNTs复合涂层的XRD谱
Fig. 3. XRD patterns of CoCrFeNi raw powder and CoCrFeNi-CNTs composite coating
3.2 复合涂层的组织形貌
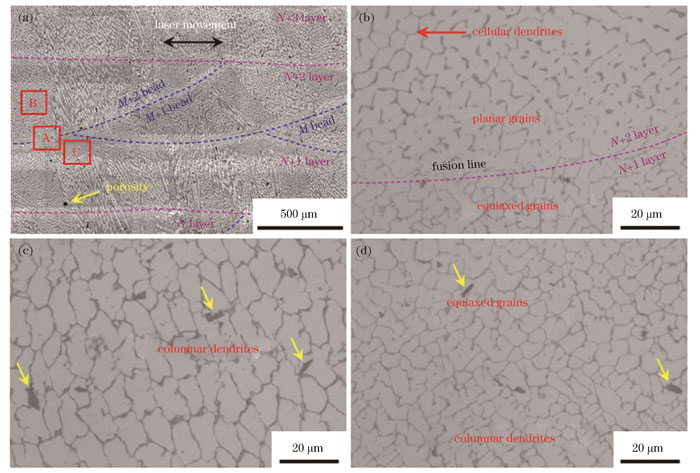
图 4. CoCrFeNi-CNTs复合涂层的截面金相形貌。(a)涂层截面的低倍金相形貌;(b)A区域的微观形貌;(c)B区域的微观形貌;(d)C区域的微观形貌
Fig. 4. Sectional metallographic morphologies of CoCrFeNi-CNTs composite coating. (a) Low magnification of metallographic morphology of coating cross section; (b) micro-morphology of region A; (c) micro-morphology of region B; (d) micro-morphology of C region
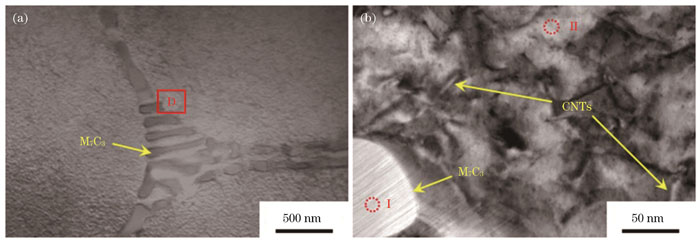
图 5. CoCrFeNi-CNTs复合涂层的透射电镜显微形貌。(a)晶界碳化物形貌;(b)D区域的放大形貌
Fig. 5. TEM microstructure of CoCrFeNi-CNTs composite coating. (a) Intergranular carbide morphology; (b) enlarged morphology of D region
表 3. CoCrFeNi-CNTs复合涂层微观区域的EDS测试结果
Table 3. EDS results measured at microscopic areas of CoCrFeNi-CNTs composite coating
|
对
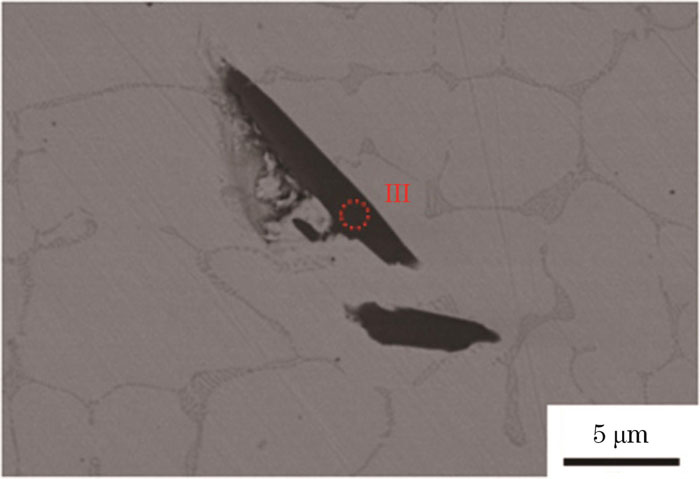
图 6. CoCrFeNi-CNTs复合涂层中未知物的扫描电镜显微形貌
Fig. 6. SEM microstructure of unknown substances in CoCrFeNi-CNTs composite coating
3.3 复合涂层的硬度
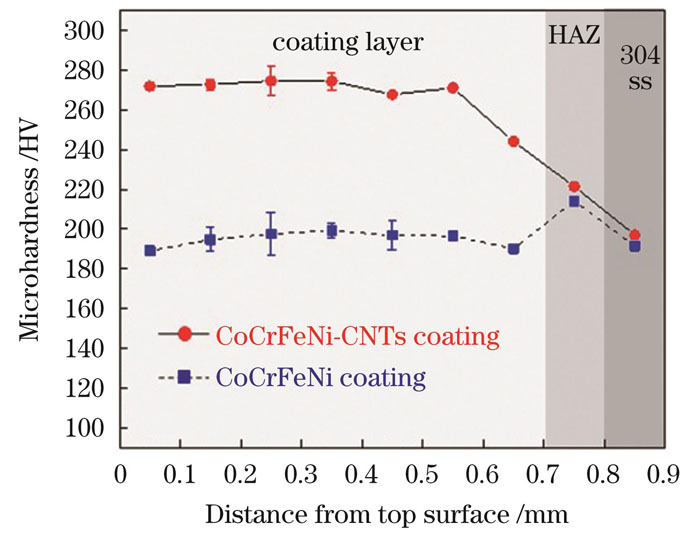
图 7. CoCrFeNi-CNTs和CoCrFeNi涂层内的显微硬度分布对比
Fig. 7. Comparison of microhardness distributions in CoCrFeNi-CNTs and CoCrFeNi coatings
3.4 复合涂层的盐雾腐蚀行为
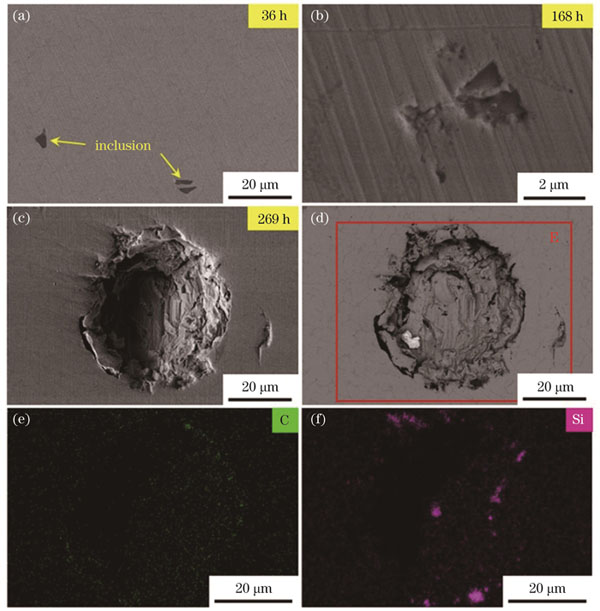
图 8. 不同盐雾腐蚀时长下CoCrFeNi-CNTs复合涂层的扫描电镜显微形貌。(a)36 h;(b)168 h;(c)269 h(二次电子模式下成像);(d)269 h(背散射模式下成像);(e)E区域的碳元素分布;(f)E区域的硅元素分布
Fig. 8. SEM microstructures of CoCrFeNi-CNTs composite coating under different salt spray corrosion time. (a) 36 h; (b) 168 h; (c) 269 h (imaging in secondary electron mode); (d) 269 h (imaging in backscatter mode); (e) distribution of C element in area E; (f) distribution of Si element in area E
4 结论
在优化参数下采用机械混合方法能够实现碳纳米管在CoCrFeNi粉体表面的均匀包覆,有效解决了碳纳米管的固有团聚问题,为碳纳米管增强激光熔覆CoCrFeNi涂层的成功制备提供了支持。
CoCrFeNi-CNTs复合涂层内无裂纹缺陷生成,气孔直径小于30 μm,晶粒组织由单一FCC结构的平面晶、胞状枝晶、柱状枝晶、等轴晶组成,晶界组织由M7C3碳化物共晶组成,利用透射电镜发现残余碳纳米管在晶粒内弥散分布。
CoCrFeNi-CNTs复合涂层内碳化物和残余碳纳米管均具有第二相强化作用,涂层的显微硬度水平能够提高70 HV以上。
M7C3碳化物共晶及碳纳米管的存在并未显著降低复合涂层内晶粒及晶界的耐腐蚀性能,但被304不锈钢基板引入复合涂层内的Si/C类夹杂物会对复合涂层的耐腐蚀性能产生不利影响,点蚀现象会在脱落的Si/C类夹杂物区域内发生,晶界处的侵蚀导致点蚀坑持续扩大。
[1] Yeh J W, Chen S K, Lin S J, et al. Nanostructured high-entropy alloys with multiple principal elements: novel alloy design concepts and outcomes[J]. Advanced Engineering Materials, 2004, 6(5): 299-303.
[2] Yeh J W, Chang S Y, Hong Y D, et al. Anomalous decrease in X-ray diffraction intensities of Cu-Ni-Al-Co-Cr-Fe-Si alloy systems with multi-principal elements[J]. Materials Chemistry and Physics, 2007, 103(1): 41-46.
[3] 邹朋津, 董刚, 王梁, 等. 激光熔覆制备CrNiAlCoMoB0.5高熵合金涂层的组织与耐腐蚀性能研究[J]. 中国激光, 2015, 42(s1): s103003.
Zou P J, Dong G, Wang L, et al. Microstructure and corrosion resistance properties of CrNiAlCoMoB0.5 high entropy alloy coating prepared by laser clading[J]. Chinese Journal of Laser, 2015, 42(s1): s103003.
[4] 张松, 吴臣亮, 伊俊振, 等. FexCoCrAlCu/Q235激光合金化层组织及性能研究[J]. 中国激光, 2014, 41(8): 0803006.
[5] Su J, Raabe D, Li Z M. Hierarchical microstructure design to tune the mechanical behavior of an interstitial TRIP-TWIP high-entropy alloy[J]. Acta Materialia, 2019, 163: 40-54.
[6] Fan Q K, Chen C, Fan C L, et al. Ultrasonic suppression of element segregation in gas tungsten arc cladding AlCoCuFeNi high-entropy alloy coatings[J]. Surface and Coatings Technology, 2021, 420: 127364.
[7] Qi Y L, Cao T H, Zong H X, et al. Enhancement of strength-ductility balance of heavy Ti and Al alloyed FeCoNiCr high-entropy alloys via boron doping[J]. Journal of Materials Science & Technology, 2021, 75: 154-163.
[8] Feng H, Cui S Y, Chen H T, et al. A molecular dynamics investigation into deformation mechanism of nanotwinned Cu/high entropy alloy FeCoCrNi nanolaminates[J]. Surface and Coatings Technology, 2020, 401: 126325.
[9] Gludovatz B, Hohenwarter A, Catoor D, et al. A fracture-resistant high-entropy alloy for cryogenic applications[J]. Science, 2014, 345(6201): 1153-1158.
[10] 翁子清, 董刚, 张群莉, 等. 退火对激光熔覆FeCrNiCoMn高熵合金涂层组织与性能的影响[J]. 中国激光, 2014, 41(3): 0303002.
[11] 王勇, 李明宇, 孙丽丽, 等. FeCrNiCo(Cu/Mn)高熵合金组织及腐蚀性能[J]. 中国有色金属学报, 2020, 30(1): 94-102.
Wang Y, Li M Y, Sun L L, et al. Microstructure and corrosion property of FeCrNiCo(Cu/Mn) high entropy alloys[J]. The Chinese Journal of Nonferrous Metals, 2020, 30(1): 94-102.
[12] 李萍, 庞胜娇, 赵杰, 等. CoCrFeNiTi0.5高熵合金在熔融Na2SO4-25%NaCl中的腐蚀行为[J]. 中国有色金属学报, 2015, 25(2): 367-374.
Li P, Pang S J, Zhao J, et al. Corrosion behavior of CoCrFeNiTi0.5 high entropy alloy in molten Na2SO4-25%NaCl[J]. The Chinese Journal of Nonferrous Metals, 2015, 25(2): 367-374.
[13] Peng Y W, Gong J M, Christiansen T L, et al. Surface modification of CoCrFeNi high entropy alloy by low-temperature gaseous carburization[J]. Materials Letters, 2021, 283: 128896.
[14] Bahrami A, Mohammadnejad A, Sajadi M. Microstructure and mechanical properties of spark plasma sintered AlCoFeMnNi high entropy alloy (HEA)-carbon nanotube (CNT) nanocomposite[J]. Journal of Alloys and Compounds, 2021, 862: 158577.
[15] Chen L B, Wei R, Tang K, et al. Heavy carbon alloyed FCC-structured high entropy alloy with excellent combination of strength and ductility[J]. Materials Science and Engineering: A, 2018, 716: 150-156.
[16] Luo T, Zhang H L, Liu R R, et al. Mechanical and damping properties of the multi-layer graphenes enhanced CrMnFeCoNi high-entropy alloy composites produced by powder metallurgy[J]. Materials Letters, 2021, 293: 129682.
[17] Medina L Z, Tavares da Costa M V, Paschalidou E M, et al. Enhancing corrosion resistance, hardness, and crack resistance in magnetron sputtered high entropy CoCrFeMnNi coatings by adding carbon[J]. Materials & Design, 2021, 205: 109711.
[18] Xiao J K, Tan H, Chen J, et al. Effect of carbon content on microstructure, hardness and wear resistance of CoCrFeMnNiCx high-entropy alloys[J]. Journal of Alloys and Compounds, 2020, 847: 156533.
[19] Singh S, Shaikh S M, Kumar M K P, et al. Microstructural homogenization and substantial improvement in corrosion resistance of mechanically alloyed FeCoCrNiCu high entropy alloys by incorporation of carbon nanotubes[J]. Materialia, 2020, 14: 100917.
[20] 李洪波, 郭猛, 王琳, 等. H13/Ni/WC混合粉末梯度熔覆层的激光熔覆制备及耐磨性研究[J]. 激光与光电子学进展, 2021, 58(3): 0314006.
[21] 张宇鹏, 王永东, 徐刚, 等. 石墨烯对激光熔覆Ti-C-Nb增强Ni基涂层组织与性能的影响[J]. 激光与光电子学进展, 2022, 59(1): 0114002.
[22] 刘昊, 高强, 满家祥, 等. 激光熔覆CoCrFeMnNiTix高熵合金涂层的微观组织及性能研究[J]. 中国激光, 2022, 49(8): 0802002.
[23] Juan Y F, Li J, Jiang Y Q, et al. Modified criterions for phase prediction in the multi-component laser-clad coatings and investigations into microstructural evolution/wear resistance of FeCrCoNiAlMox laser-clad coatings[J]. Applied Surface Science, 2019, 465: 700-714.
[24] Shu F Y, Liu S, Zhao H Y, et al. Structure and high-temperature property of amorphous composite coating synthesized by laser cladding FeCrCoNiSiB high-entropy alloy powder[J]. Journal of Alloys and Compounds, 2018, 731: 662-666.
[25] Guo Y X, Shang X J, Liu Q B. Microstructure and properties of in situ TiN reinforced laser cladding CoCr2FeNiTix high-entropy alloy composite coatings[J]. Surface and Coatings Technology, 2018, 344: 353-358.
[26] Zhang H F, Yan H L, Yu H, et al. The effect of Co and Cr substitutions for Ni on mechanical properties and plastic deformation mechanism of FeMnCoCrNi high entropy alloys[J]. Journal of Materials Science & Technology, 2020, 48: 146-155.
[27] Chen D, Guan Y J, Jin G, et al. In-situ synthesis of a FeCoCrNiCu/FeCoCrNiAl composite high entropy alloy coating by laser cladding[J]. Surface and Coatings Technology, 2023, 461: 129447.
[28] Li Y Y, Liu H, Liu X H, et al. Microstructure, thermostability and tribological behavior of composite CoCrFeNiTix high-entropy alloy coatings fabricated by laser cladding[J]. Optik, 2023, 283: 170899.
[29] 张家诚, 江吉彬, 黄旭, 等. 碳纳米管含量对激光熔覆镍基复合涂层组织与性能的影响[J]. 中国激光, 2022, 49(2): 0202301.
[30] 寿寅任, 潘卓, 曹正轩, 等. 基于碳纳米管泡沫的高效宽谱极紫外辐射[J]. 光学学报, 2022, 42(11): 1134021.
韩冰, 陈曦, 姜梦, 陈文龙, 张东东, 曹立超, 张俊爽, 滕宪斌, 陈彦宾. 激光熔覆碳纳米管增强高熵合金涂层及耐腐蚀性能[J]. 中国激光, 2023, 50(24): 2402205. Bing Han, Xi Chen, Meng Jiang, Wenlong Chen, Dongdong Zhang, Lichao Cao, Junshuang Zhang, Xianbin Teng, Yanbin Chen. Laser Cladding High‑Entropy Alloy Coating Reinforced by Carbon Nanotubes and Its Corrosion Resistance[J]. Chinese Journal of Lasers, 2023, 50(24): 2402205.