基于遗传算法的激光切割镍基合金质量优化
下载: 914次
1 引言
镍基合金GH3128是一种可以在950 ℃温度下长期工作的固熔强化型镍基高温合金,主要应用于航空发动机燃烧室的火焰筒、动力燃烧室壳体、调节片及其他高温零部件中[1-3]。镍基合金的激光切割质量预测及寻优研究对航空制造业具有现实意义。
陈宇翔等[4]采用正交法对镍基合金GH3128进行了工艺参数优化,研究结果对减小挂渣厚度具有指导意义,但未优化切缝宽度。于天驰等[5]利用交互作用正交表进行实验,准确找出了全面实验中的最优方案。但这些优化方案都局限在固定的因素水平中,故研究者们通过人工神经网络对大范围的因素水平进行优化研究并预测激光切割质量。
赵晋平等[6]采用神经网络与遗传算法结合的方法,对2Al2铝合金进行了最佳工艺参数预测并验证了其正确性。陈继民等[7]通过人工神经网络,成功指导了CO2激光的三维方位切割。郭华锋等[8]采用反向传播(BP)神经网络,对光纤激光切割切口的粗糙度进行了预测,最大相对误差为2.4%。李建敏等[9]利用MATLAB软件构建了神经网络,预测了0.9 mm厚的201钢板的光纤激光切割质量,预测误差基本在10%以内。丁华等[10]通过BP人造神经网络,预测了激光微孔的表面粗糙度,预测误差在6%左右,最大误差不超过8.08%。童桂等[11]提出了一种BP神经网络的激光切割质量控制模型,验证了通过神经网络建立切割工艺参数与切割粗糙度间的对应关系的可行性。Badkar等[12]运用响应面法与人工神经网络建立了模型,分析了激光强化纯钛的工艺参数的影响,并预测了其耐热能力与抗拉强度。Chaki等[13]运用模拟退火法与人工神经网络建立了模型,优化了激光氧气切割低碳钢的工艺参数,最佳模型预测得到热区误差为3.15%,切缝误差为2.81%,表面粗糙度误差为2.27%。
国内外文献表明,使用人工神经网络或将其与其他方法结合均可以成功建立激光切割质量与工艺参数之间的模型,将工艺参数作为输入向量,通过该模型预测切口的表面粗糙度、切缝宽度、热影响区等激光切割质量,一般认为误差低于10%时对实际加工具有指导意义。本文以泵浦灯电流、激光脉宽、切割速度及离焦量作为工艺参数变量,以综合评价分数作为激光切割质量的判断标准,将含大量实验数据的工艺参数作为人工神经网络的输入向量,以切割质量作为输出向量,建立了BP神经网络模型。选择误差最小的隐层节点的BP神经网络作为预测模型,利用遗传算法在工艺参数变量范围内进行选择、交叉及变异操作,多次迭代寻找最优值。
2 实验
2.1 实验设备与材料
实验设备为武汉楚天工业激光设备有限公司生产的型号为JHM-1GY-300B的激光切割机,激光波长为1.06 μm,激光额定平均功率为300 W,激光脉冲频率为1~200 Hz,激光脉冲宽度为0.1~20 ms,聚焦镜焦距为75 mm,光斑直径为0.3~0.6 mm。辅助气体为氧气,实验材料为镍基合金GH3128,规格为100 mm×100 mm×0.8 mm,主要成分见
表 1. GH3128的化学成分(质量分数,%)
Table 1. Chemical compositions of GH3128 (mass fraction,%)
|
激光切割原理如
2.2 实验数据
根据实践经验[4-5],选取4个因素5个水平作为神经网络的输入向量,具体因素水平见
实验指标选取综合评价分数
式中
表 2. 因素水平
Table 2. Factor levels
|
将
表 3. 样本综合评分
Table 3. Comprehensive scores of samples
|
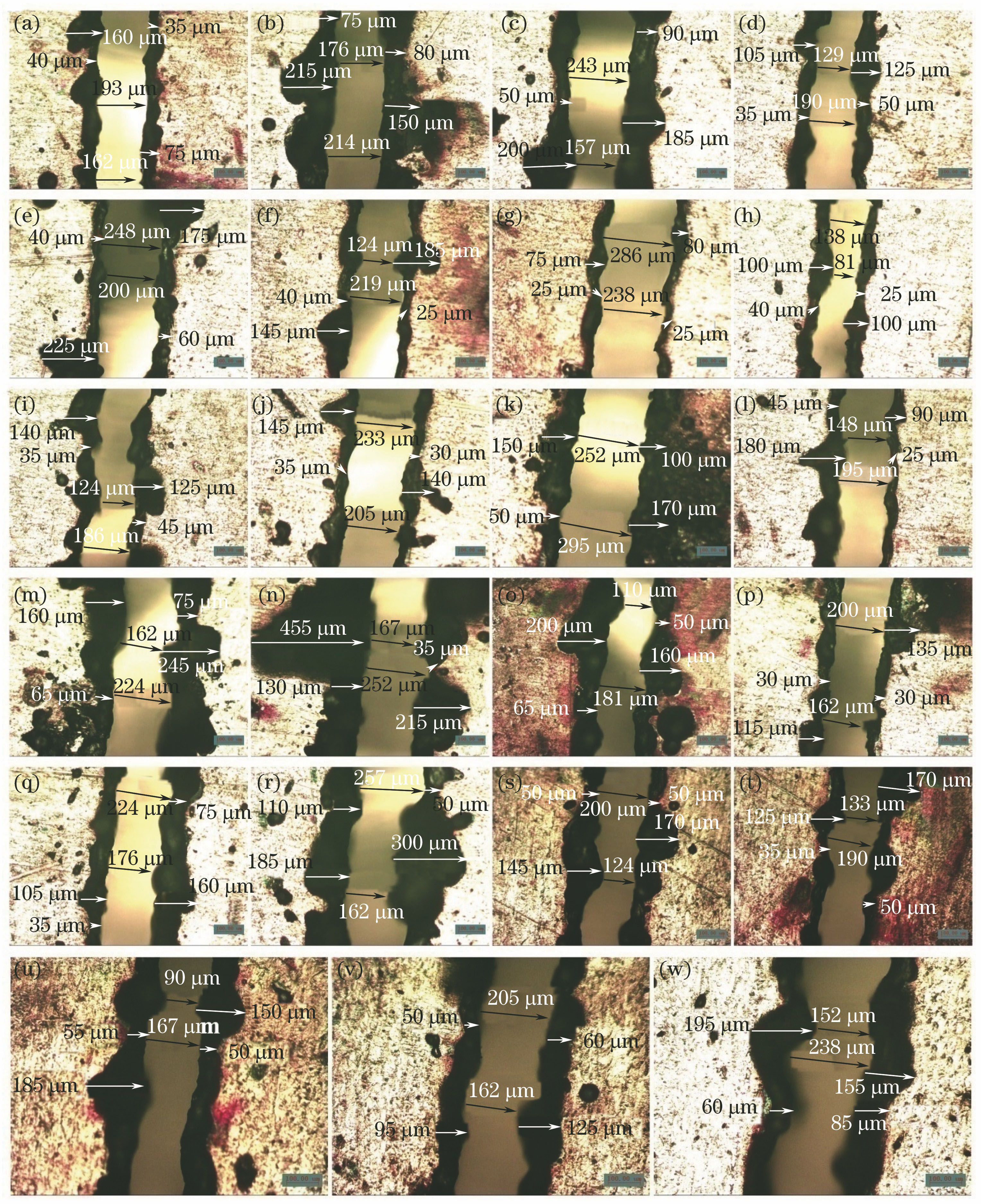
图 3. 样本金相数据的标记图。(a) 2号;(b) 3号;(c) 4号;(d) 5号;(e) 6号;(f) 7号;(g) 8号;(h) 9号;(i) 10号;(j) 11号;(k) 12号;(l) 14号;(m) 15号;(n) 16号;(o) 17号;(p) 18号;(q) 19号;(r) 20号;(s) 21号;(t) 22号;(u) 23号;(v) 24号;(w) 25号
Fig. 3. Mark graph of metallographic data of samples. (a) No. 2; (b) No. 3; (c) No. 4; (d) No. 5; (e) No. 6; (f) No. 7; (g) No. 8; (h) No. 9; (i) No. 10; (j) No. 11; (k) No. 12; (l) No. 14; (m) No. 15; (n) No. 16; (o) No. 17; (p) No. 18; (q) No. 19; (r) No. 20; (s) No. 21; (t) No. 22; (u) No. 23; (v) No. 24; (w) No. 25
3 模型建立
3.1 神经网络
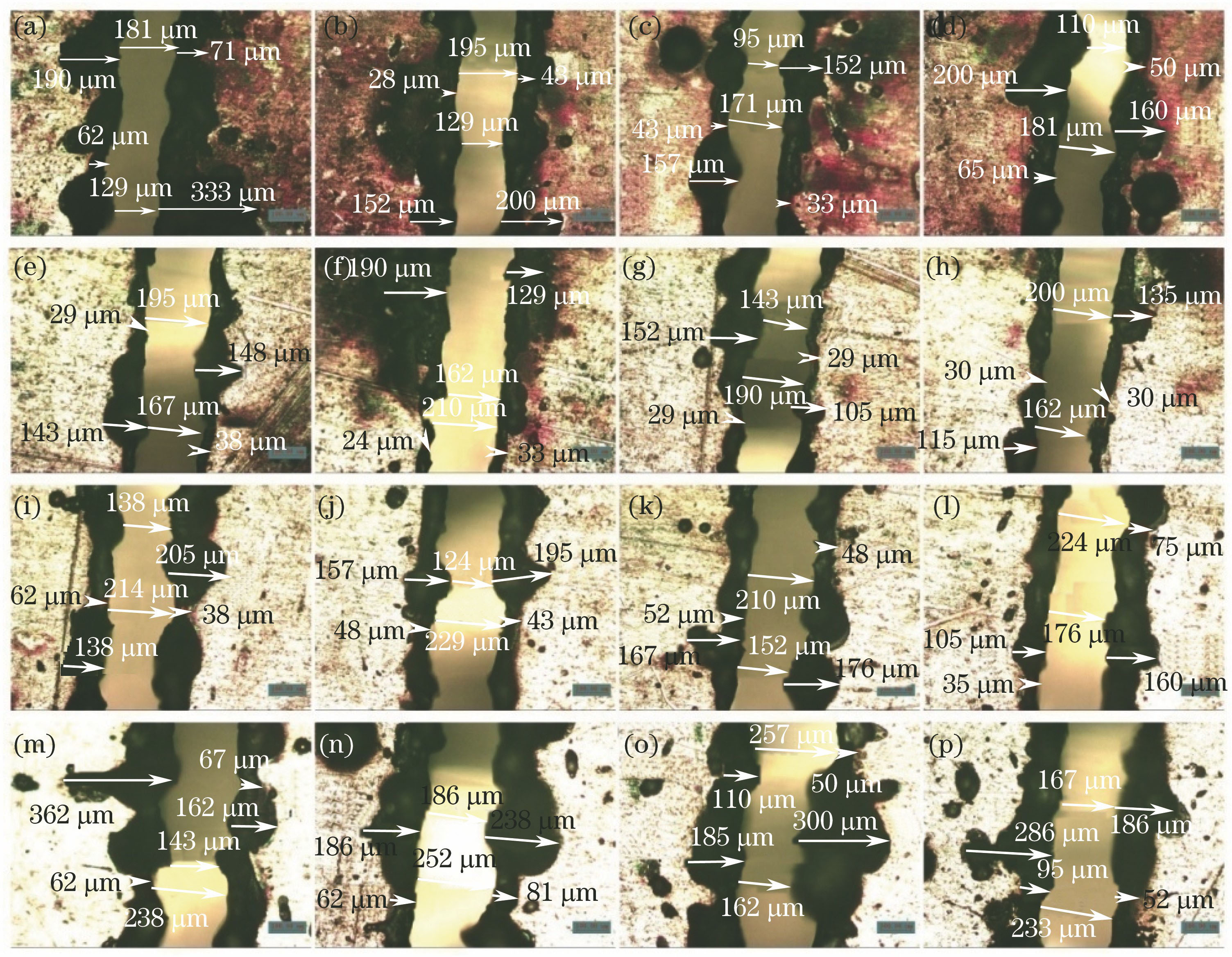
图 4. 17~20号样本的4次取样图。(a) 17号1次样本;(b) 17号2次样本;(c) 17号3次样本;(d) 17号4次样本;(e) 18号1次样本;(f) 18号2次样本;(g) 18号3次样本;(h) 18号4次样本;(i) 19号1次样本;(j) 19号2次样本;(k) 19号3次样本;(l) 19号4次样本;(m) 20号1次样本;(n) 20号2次样本;(o) 20号3次样本;(p) 20号4次样本
Fig. 4. Four-time sampling figures of samples from No. 17 to No. 20. (a) No. 17, first sampling; (b) No. 17, second sampling; (c) No. 17, third sampling; (d) No. 17, fourth sampling; (e) No. 18, first sampling; (f) No. 18, second sampling; (g) No. 18, third sampling; (h) No. 18, fourth sampling; (i) No. 19, first sampling; (j) No. 19, second c sampling; (k) No. 19, third sampling; (l) No. 19, fourth sampling; (m) No. 20, first sampling; (n) No. 20, second sampling; (o) No. 20, third sampling; (p) No. 20
表 4. 样本误差
Table 4. Sample errors
|
表 5. 隐层节点误差
Table 5. Hidden layer node errors
|
由
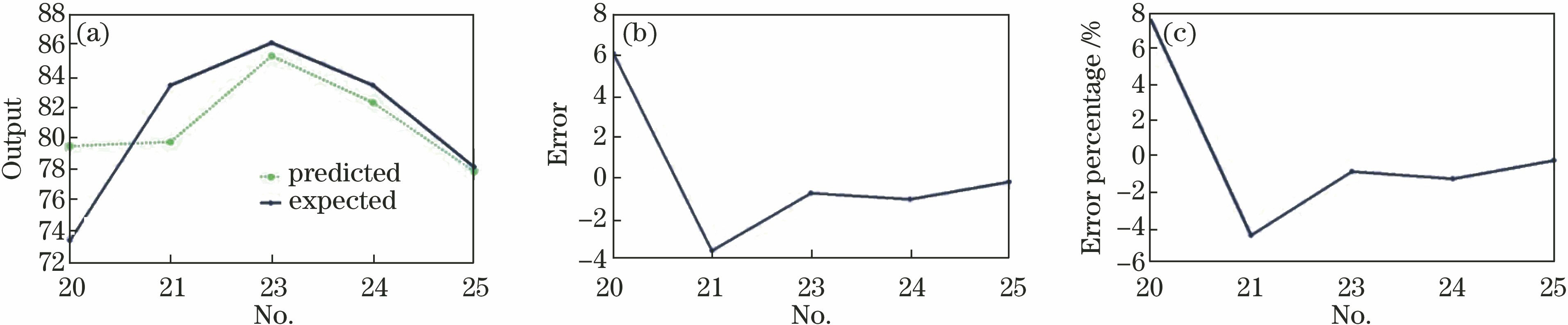
图 6. BP神经网络的预测结果。(a)预测值与期望值对比;(b)误差;(c)误差百分比
Fig. 6. Resutls predicted by BP neural network. (a) Comparison between predicted value and expected value; (b) error; (c) percentage of error
3.2 遗传算法
遗传算法优化的神经网络模型主要分为神经网络训练拟合和遗传算法极值寻优,算法流程如
由
4 验证实验
采用遗传算法优化后的最佳工艺参数进行激光切割,样本宏观图与微观图如
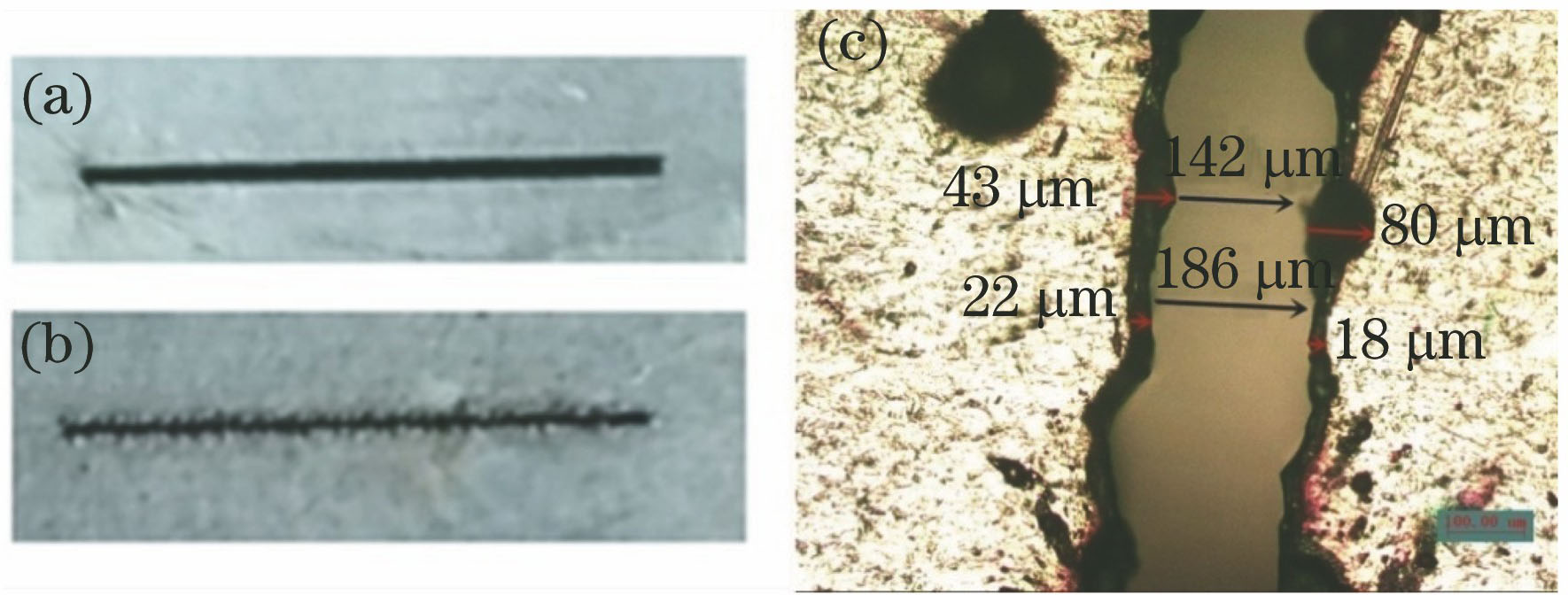
图 9. 验证实验图。(a)正面宏观图;(b)背面宏观图;(c)金相微观图
Fig. 9. Experimental diagram for test. (a) Positive macrograph; (b) back macrograph; (c) metallographic micrograph
由
5 结论
基于BP神经网络,对激光切割的镍基合金样本进行了训练函数拟合,以综合评分作为遗传算法的适应度值,对样本进行交叉、变异和迭代等操作,得到了最优适应度值及对应的工艺参数,并使用该工艺参数进行了验证实验,具体结论如下。
1) BP人工神经网络预测镍基合金的激光切割综合评分具有指导意义,其最大误差为7.66%,最小误差为-0.32%。
2) 基于遗传算法优化的神经网络对镍基合金的激光切割质量寻优具有指导意义,最优工艺参数为电流239 A,脉宽1.29 ms,切速280 mm/min,离焦量-0.83 mm。在此工艺参数下切割样本的挂渣平均宽度为81.5 μm,切缝平均宽度为164 μm。
3) 基于遗传算法优化的神经网络预测的最优值为98.41,实际值为89.53,误差为8.88,误差百分比为9.03%,误差较大但控制在10%以内,误差可以通过增大样本数进一步减小。
[1] 冯威琦, 张云丰, 陶汪, 等. 高温合金/不锈钢异种材料T型接头激光穿透焊工艺研究[J]. 中国激光, 2012, 39(10): 1003003.
[2] 罗登, 路媛媛, 郭溪溪, 等. 单晶高温合金V槽的激光修复工艺研究[J]. 中国激光, 2016, 43(5): 0503001.
[3] 明宪良, 陈静, 谭华, 等. 激光修复GH4169高温合金的持久断裂机制研究[J]. 中国激光, 2015, 42(4): 0403005.
[4] 陈宇翔, 高亮. 正交法分析激光切割高温合金钢工艺参数[J]. 激光与光电子学进展, 2016, 53(11): 111403.
[5] 于天驰, 陈宇翔, 岳鑫, 等. 交互作用优化激光切割镍基合金工艺参数[J]. 激光与光电子学进展, 2018, 55(2): 021413.
[6] 赵晋平, 彭玉海, 南永博, 等. 2Al2铝合金切割工艺参数分析与预测[J]. 陕西理工学院学报(自然科学版), 2017, 33(2): 28-33.
[7] 陈继民, 左铁钏. CO2激光三维方位切割的人工神经网络分析[J]. 中国激光, 2004, 31(2): 245-248.
[8] 郭华锋, 李菊丽, 孙涛. 基于BP神经网络的光纤激光切割切口粗糙度预测[J]. 激光技术, 2014, 38(6): 798-803.
[9] 李建敏, 李国柱, 王春明, 等. 基于MATLAB神经网络激光切割质量预测系统设计[J]. 应用激光, 2014, 34(2): 122-125.
[10] 丁华, 李炎蔚, 袁冬青. 反向传播人造神经网络预测激光微孔表面粗糙度[J]. 激光与光电子学进展, 2017, 54(1): 011407.
[11] 童桂, 徐宏, 郁汉琪. 基于模拟退火的BP神经网络激光切割质量控制模型[J]. 机械设计与制造, 2016( 6): 85- 87.
TongG, XuH, Yu HQ. Control model of laser cutting quality based on simulated annealing and BP neural network[J]. Machinery Design & Manufacture, 2012( 6): 85- 87.
[14] 曹凤国. 激光加工[M]. 北京: 化学工业出版社, 2015: 67.
Cao FG. Laser beam machining[M]. Beijing: Chemical Industry Press, 2015: 67.
[15] 韩力群, 施彦. 人工神经网络理论及应用[M]. 北京: 机械工业出版社, 2016: 51- 52.
Han LQ, ShiY. Artificial neural network theory and application[M]. Beijing: China Machine Press, 2016: 51- 52.
[16] 王小川, 史峰, 郁磊, 等. Matlab神经网络43个案例分析[M]. 北京: 北京航空航天大学出版社, 2013: 36- 38.
Wang XC, ShiF, YuL, et al.Matlab neural networks 43 cases analysis[M]. Beijing: Beihang University Press, 2013: 36- 38.
[17] 郁胜过, 张玲, 谢玮霖, 等. 基于遗传算法与Zoom FFT的光频域反射仪快速高精度频谱分析[J]. 光学学报, 2017, 37(4): 0406003.
[18] 周祥燕, 张超, 匡尚奇, 等. 基于量子衍生遗传算法的光学薄膜结构分析[J]. 中国激光, 2017, 44(12): 1203002.
[19] 高航, 薛凌云. 基于改进遗传算法的反向传播神经网络拟合LED光谱模型[J]. 激光与光电子学进展, 2017, 54(7): 072302.
张艺赢, 曹妍, 陈宇翔, 牟向伟. 基于遗传算法的激光切割镍基合金质量优化[J]. 激光与光电子学进展, 2018, 55(11): 111404. Yiying Zhang, Yan Cao, Yuxiang Chen, Xiangwei Mu. Quality Optimization of Laser-Cutted Ni-Based Alloys Based on Genetic Algorithm[J]. Laser & Optoelectronics Progress, 2018, 55(11): 111404.