扫描速率对激光熔覆Cu80Fe20偏晶涂层组织与耐磨性能的影响
下载: 858次
1 引言
铜合金具有优良的导热、导电、延展性以及耐蚀性,常被用于制作发电机、电缆、开关装置、变压器、引线框架等[1-5]。随着科学技术的发展,人们对铜合金零部件的性能提出了更高的要求,期望铜基合金具有高的强度和耐磨性。与其他合金元素相比,铁具有成本低廉的优势,通过加入适量铁来改善铜合金硬度和耐磨性能的做法受到了研究者的广泛关注[6-9]。
Cu-Fe合金在过冷条件下能表现出一种明确的热力学趋势:液相不混溶。即,将Cu-Fe熔体过冷至液相分离温度
早期的研究结果表明[11-14],影响Cu-Fe偏晶合金在凝固过程中液相分离的主要因素包括合金成分、过冷度、冷却速率与流动状态。其中,冷却速率是最主要的因素。与其他制备方法相比,快速凝固法的冷却速率可达到106~107 K/s[8],这一方法在制备均质偏晶合金时具有巨大的潜在优势。Nagase等[15]利用甩带法成功制备了两相非晶合金Fe-Cu-Nb-B,由于多次液相分离,形成了大小各异的铜颗粒弥散分布于铁基非晶基体中的结构。Dai[16]等采用激光-感应复合熔覆技术成功制备了Fe-Cu-Cr-C复合涂层,并发现,随着扫描速率增加,激光熔池温度降低,冷却速率增加,球状颗粒粒径减小。Dai[8]等采用机械合金化和激光熔覆的方法制备了Cu95Fe5均质偏晶合金,并研究了它的结构特征、电化学性能以及磁学性能,但并未对Cu-Fe偏晶合金的耐磨性能进行表征,因此,本课题组拟通过增加Fe的含量来研究Fe-Cu合金的耐磨性能。采用激光熔覆技术在A3钢表面制备了Cu80Fe20偏晶涂层,研究了冷却速率对偏晶涂层微结构、富铁颗粒粒径以及耐磨性能的影响。
2 实验方法
实验采用尺寸为100 mm×50 mm×10 mm的A3钢作为基材。合金粉末由12Cr1Mo1V铁基合金粉末和纯铜粉末(纯度99.5%) 按1∶4 的质量比混合而成,然后进行球磨均匀化处理,球磨时间与转速分别设置为2 h与200 r/min。球磨介质为不锈钢球,且球料的质量比为15∶1。球磨结束后,将混合均匀的合金粉末置于120 ℃的电阻炉内干燥3 h,备用。
采用功率为4 kW、波长为920~1040 nm的半导体激光器(TruDiode 4006)进行单道、多道熔覆实验,采用的工艺参数如下:激光功率为1 kW,扫描速率分别为8,10,12 mm/s(在这3种速率下制备的偏晶涂层试样分别记为N1、N2、N3),光斑直径为4 mm,送粉速率为30 g/min,搭接率为50%。为了防止偏晶涂层氧化,激光熔覆实验在氩气气氛保护下进行。
采用由5 g FeCl3(质量分数为99.9%)、5 mL HCl溶液 (质量分数为37%) 与95 mL H2O配制的溶液作为腐蚀液,在常温下腐蚀偏晶涂层试样16 s。然后采用配备有X射线能谱(EDS) 分析仪的扫描电子显微镜(ZEISS Sigma 300)对偏晶涂层的显微组织进行分析,采用D/MAX-2500 X射线衍射仪表征偏晶涂层的物相,采用铜靶,管电压为40 KV,管电流为40 mA。
采用硬度仪(Vickers-1000)测试偏晶涂层和黄铜的显微硬度,加载载荷为1.96 N,保载时间为10 s。干滑动摩擦磨损实验采用环-块式摩擦磨损机(M-2000)进行,实验参数如下:载荷为120 N,时间为60 min,转速为200 r/min。试样尺寸为14 mm×8 mm×8 mm,对磨环的直径为50 mm,对磨环的材质为GCr15钢,其硬度可达60 HRC。摩擦磨损实验结束后,采用电子天平(BSA124S)称量试样的质量,进而计算试样的磨损量;采用扫描电子显微镜观察试样的磨屑和磨损表面形貌;采用白光干涉三维表面轮廓仪(Phase Shift MicroXAM-3D)测量磨痕的宽度和深度。摩擦磨损实验如
3 实验结果
3.1 偏晶涂层的几何尺寸
式中:
式中:
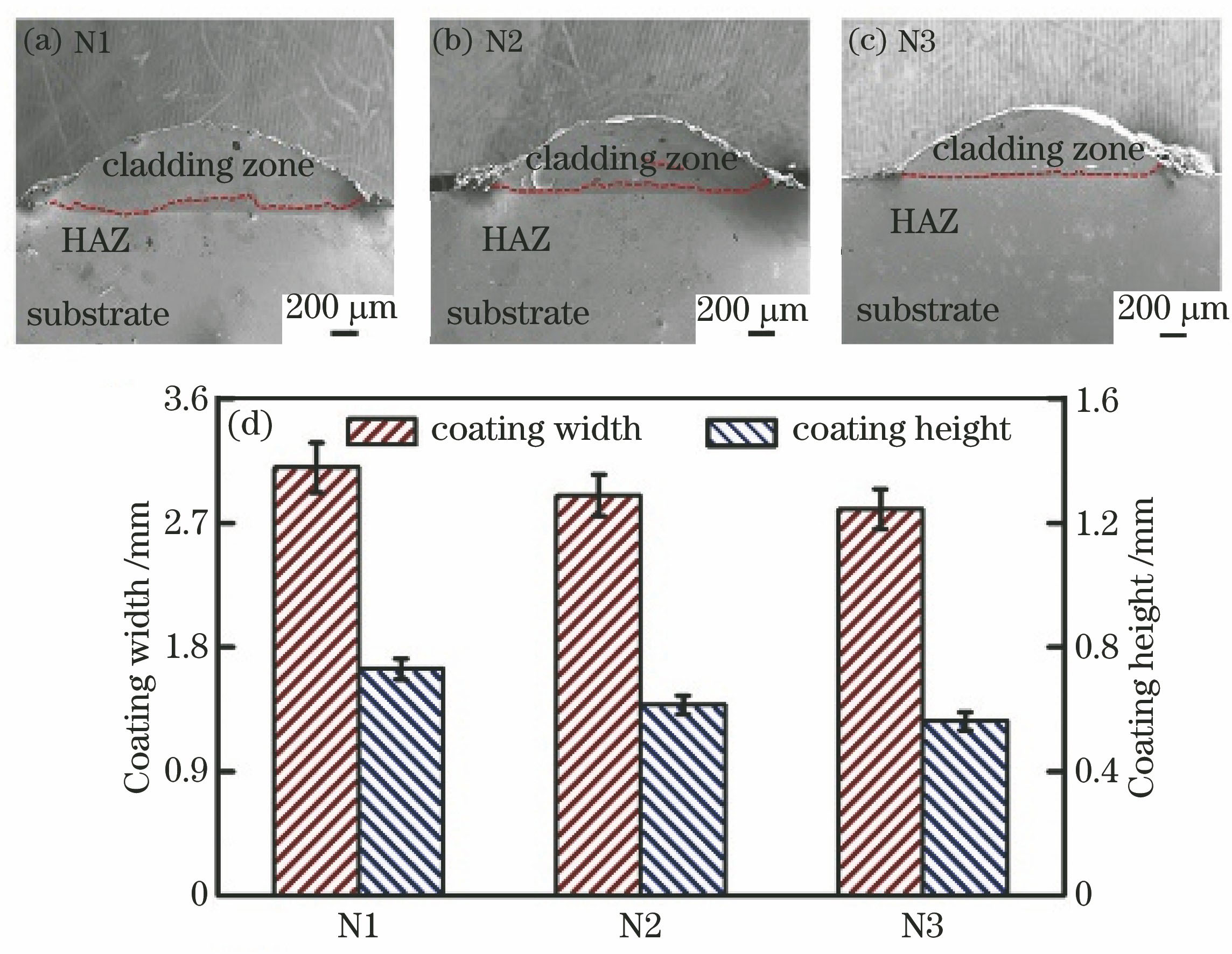
图 2. 偏晶涂层的形貌及几何尺寸。(a)~(c)形貌;(d)尺寸
Fig. 2. Morphology and geometrical characteristics of immiscible coatings. (a)-(c) Morphology; (d) geometrical characteristics
3.2 X射线衍射结果分析
3.3 显微结构
式中:
式中:
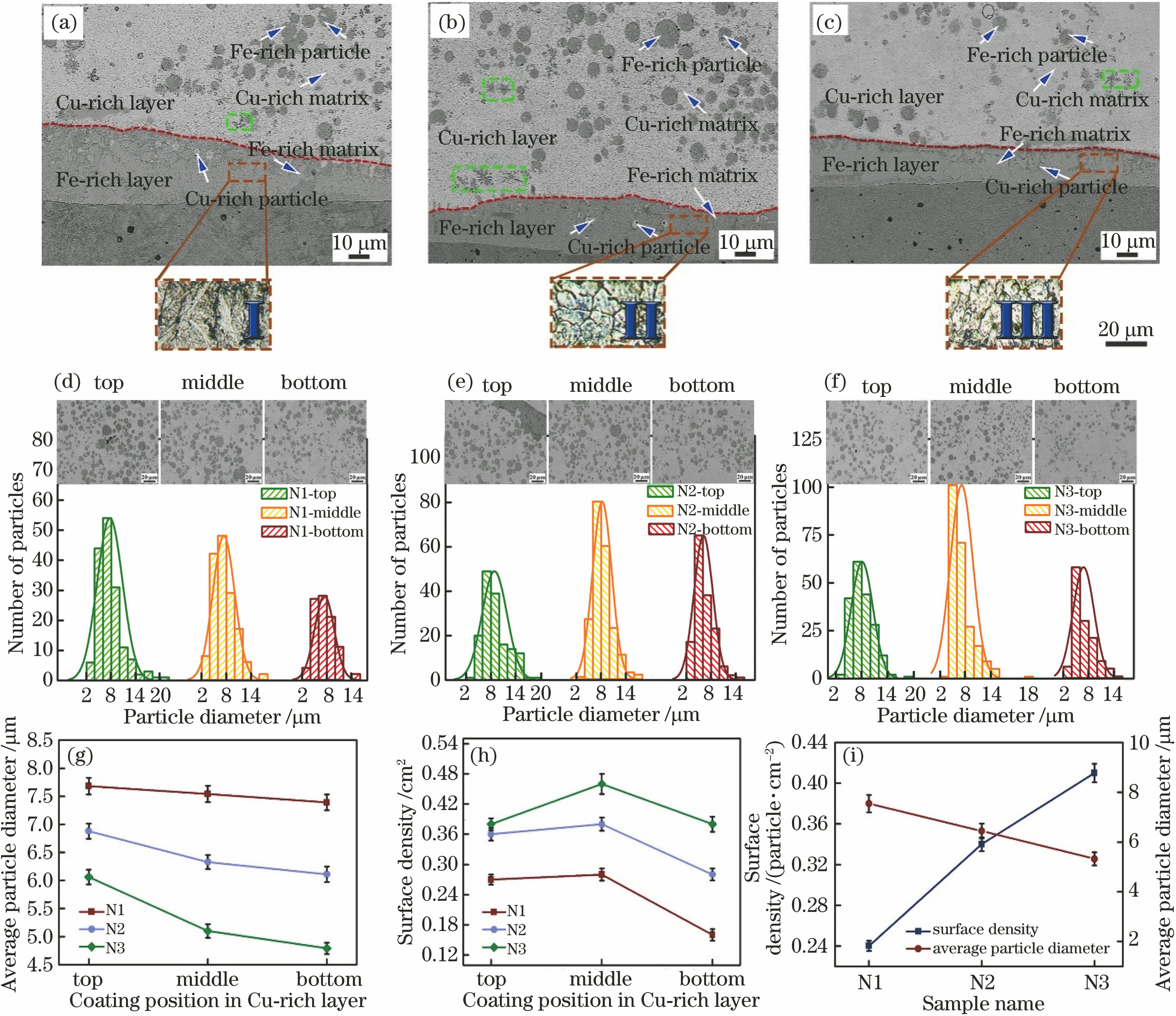
图 4. 偏晶涂层的底部形貌及定量分析结果。(a) N1的底部形貌;(b) N2的底部形貌;(c) N3的底部形貌; (d) N1中富铁颗粒的粒径分布;(e) N2中富铁颗粒的粒径分布;(f) N3中富铁颗粒的粒径分布;(g)富铁颗粒的粒径;(h)富铁颗粒的面密度;(i)富铁颗粒的平均粒径及面密度
Fig. 4. Morphology in bottom of immiscible coatings and quantitative analysis results of immiscible coatings. (a) Morphology in bottom of N1; (b) morphology in bottom of N2; (c) morphology in bottom of N3; (d) size distribution of Fe-rich particles in N1; (e) size distribution of Fe-rich particles in N2; (f) size distribution of Fe-rich particles in N3; (g) size of Fe-rich paiticles; (h) surface density of Fe-rich paiticles; (i) average particles size and surface density of Fe-rich particles
由
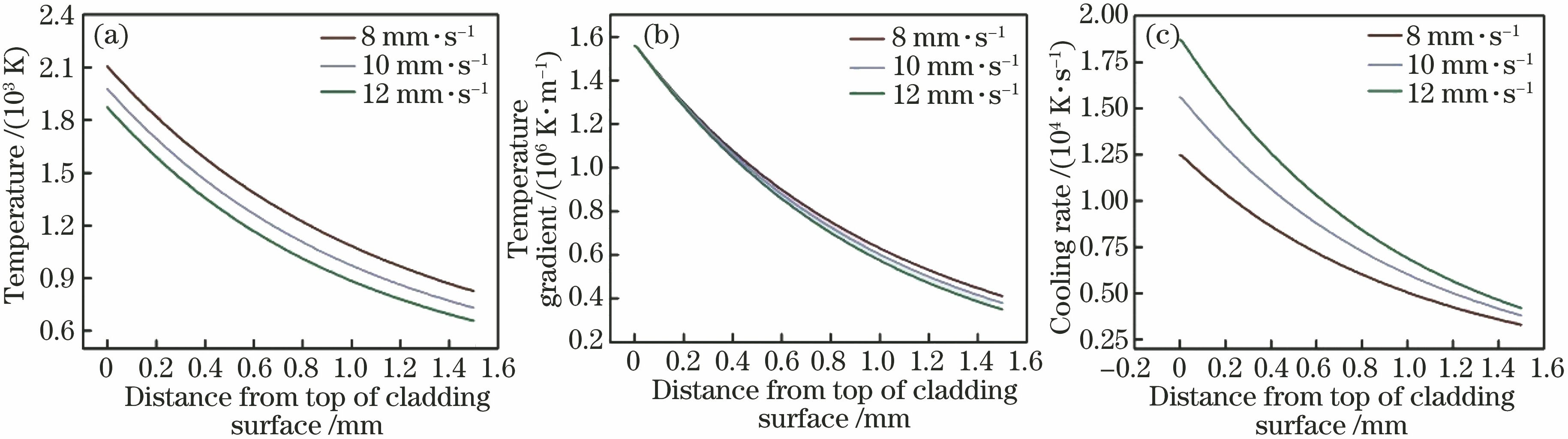
图 5. 不同扫描速率下激光熔池的性质。(a)温度;(b)温度梯度;(c)冷却速率
Fig. 5. Properties of laser molten pool at different scanning speeds. (a) Temperature profiles; (b) temperature gradient profiles; (c) cooling rate profiles
3.4 显微硬度
3.5 耐磨性能
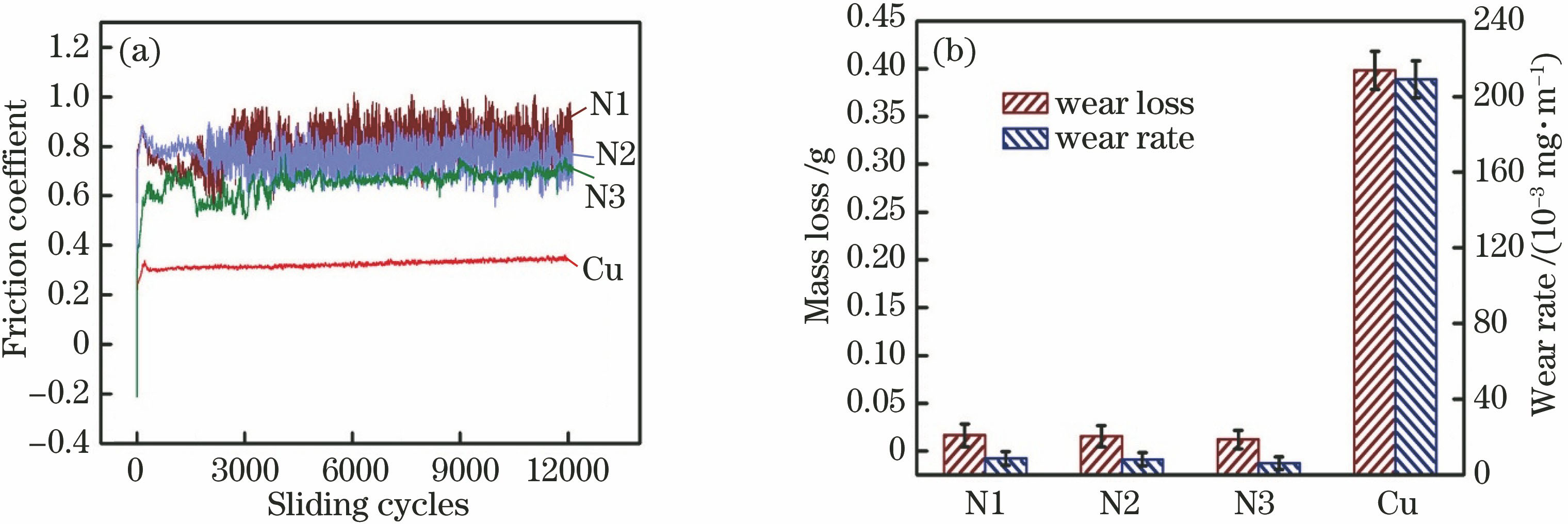
图 7. 偏晶涂层与黄铜的摩擦磨损性能。(a)摩擦因数; (b)磨损质量及磨损率
Fig. 7. Friction and wear properties of immiscible coatings and brass. (a) Friction coefficient; (b) wear loss and wear rate
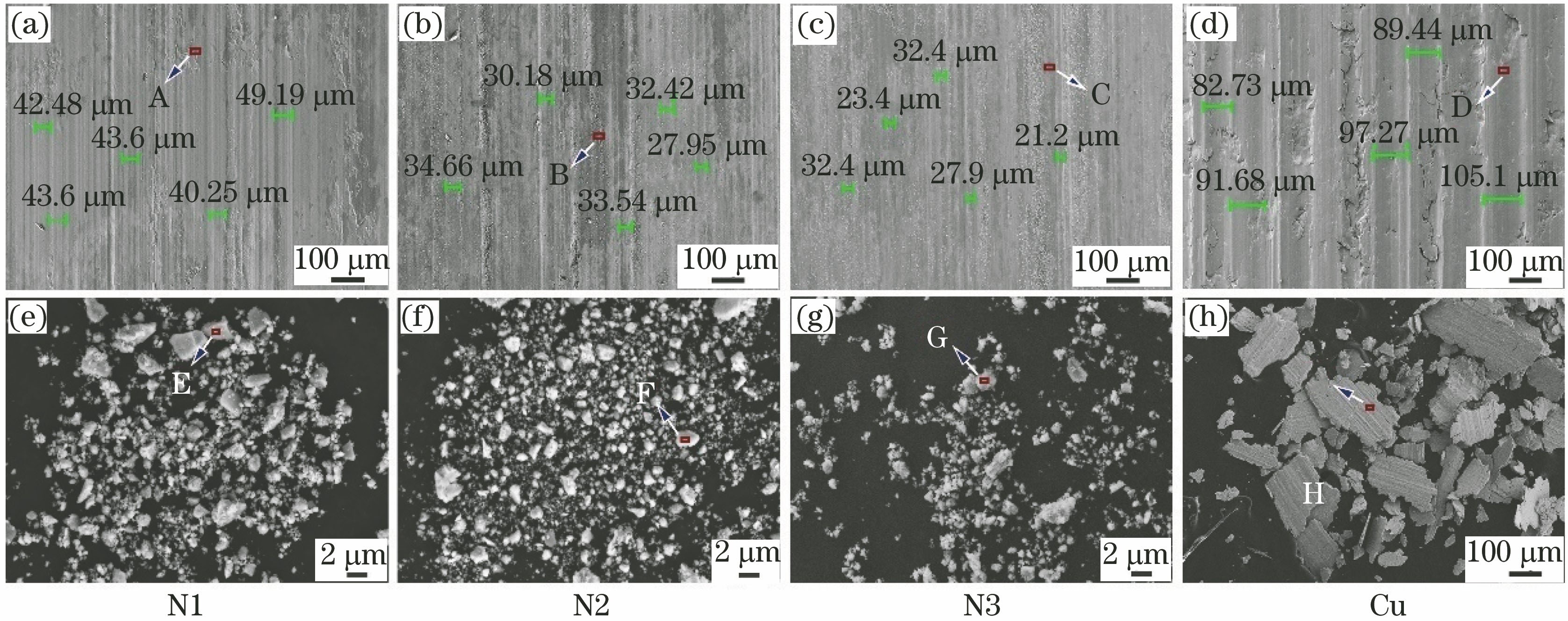
图 8. 偏晶涂层与黄铜的磨损形貌及磨屑形貌。(a)~(d)磨损形貌;(e)~(h)磨屑形貌
Fig. 8. Worn morphology and worn debris morphology of immiscible coatings and brass. (a)-(d) Worn morphology; (e)-(h) worn debris morphology
表 1. 偏晶涂层与黄铜磨损面及磨屑的EDS分析结果
Table 1. EDS results of worn surface and worn debris of immiscible coatings and brass
|
在磨损初期,偏晶涂层与对磨环相互接触,微观上表现为微凸体与微凸体的接触,两个微凸体较尖锐,在干摩擦过程中会产生相对运动[28]。对磨环的硬度可达到60 HRC,可对偏晶涂层产生挤压、磨削作用。首先,富铜基体由于黏着磨损而从偏晶涂层表面以片状的形式剥落,随后富铁颗粒暴露出来,对富铜基体产生阴影保护效应,阻止对磨环对偏晶涂层表面的进一步磨削。随着磨损的进行,富铁颗粒与富铜基体的结合力因对磨环的持续挤压作用而变弱,使其易于从富铜基体内剥落,富铁颗粒剥落的同时伴随着富铜基体的部分剥落,一部分作为磨屑,另一部分残留于摩擦副间,对磨损面产生磨粒磨损。随着磨损的进一步进行,摩擦生热导致氧化磨损的产生。因此,偏晶涂层的磨损机制主要为黏着磨损、磨粒磨损以及氧化磨损。但是,黄铜的硬度比对磨环软,在磨损过程中对磨环对黄铜表面产生强烈的磨削作用,导致磨损表面发生严重的塑形变形以及大量铜屑持续剥落。黄铜的磨损机制主要为黏着磨损和氧化磨损。此外,从
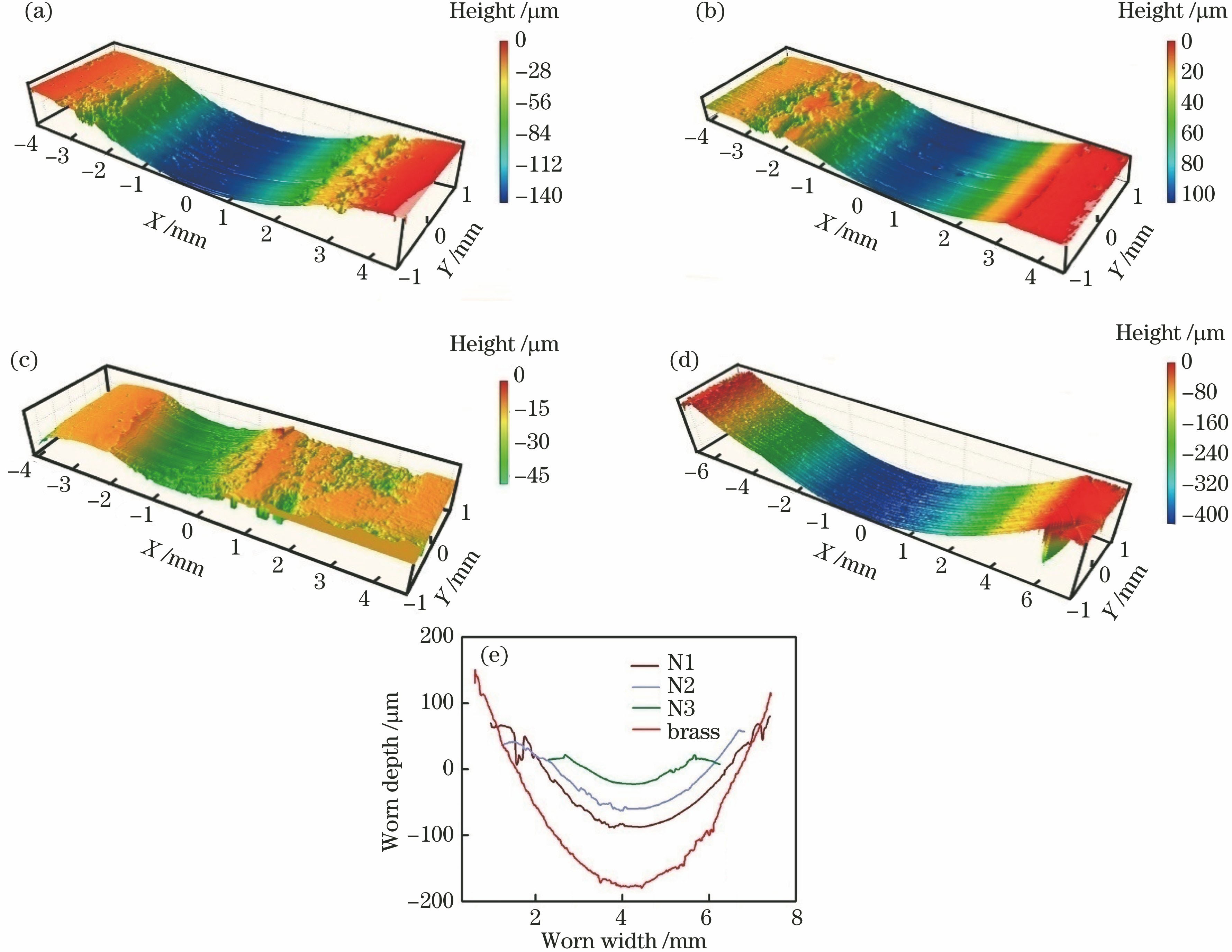
图 9. 偏晶涂层与黄铜的磨损实验结果。 (a) N1,三维轮廓; (b) N2,三维轮廓;(c) N3,三维轮廓;(d)黄铜,三维轮廓; (e)磨损曲线
Fig. 9. Wear test results of immiscible coatings and brass. (a) N1, three-dimensional profile; (b) N2, three-dimensional profile; (c) N3, three-dimensional profile; (d) brass, three-dimensional profile; (e) wear curves
4 结论
采用激光熔覆技术制备了Cu80Fe20偏晶涂层,偏晶涂层内部出现了分层现象,富铁颗粒弥散分布于在上层的富铜基体内,富铜颗粒弥散分布于下层的富铁基体内。随着激光扫描速率由8 mm/s增加到12 mm/s,富铁颗粒的平均粒径由(7.54±0.302) μm减小到(5.32±0.213) μm,面密度由0.24增加到0.41,颗粒间距的减小使得富铁颗粒对铜基体的阴影保护效应增强。此外,随着扫描速率由8 mm/s增加到12 mm/s,偏晶涂层的平均硬度由(155.62±6.78) HV增加到(181.31±8.06) HV,且均高于黄铜的硬度值(黄铜的硬度为(135±6.75) HV),其对应的磨损高度、磨损宽度分别由(140±5.60) μm与(5.50±0.28) mm降为(44.2±2.21) μm与(1.55±0.10) mm,且均小于黄铜的磨损高度和磨损宽度(黄铜的磨损高度和磨损宽度分别为(400±9.80) μm和(11±0.44) mm)。激光熔覆Cu80Fe20偏晶涂层的耐磨性能相对于黄铜得到较大提高。
[1] 方正春. 耐热和导电铜合金发展现状[J]. 材料开发与应用, 1997, 12(4): 27-31.
[3] 张生龙, 尹志民. 高强高导铜合金设计思路及其应用[J]. 材料导报, 2003, 17(11): 26-29.
[5] 袁孚胜, 钟海燕. 引线框架铜合金材料的研究现状及发展趋势[J]. 有色冶金设计与研究, 2015, 36(2): 36-38.
[9] 董江, 陈岁元, 刘大亮, 等. 铜合金表面激光原位制备钴基合金涂层的结构与机制[J]. 中国激光, 2009, 36(5): 1302-1307.
[10] Abbas S F, Kim T S. Effect of lattice strain on the electrical conductivity of rapidly solidified copper-iron metastable alloys[J]. Journal of Alloys and Compounds, 2018, 732: 129-135.
[13] CuriottoS, Pryds NH, JohnsonE, et al. Effect of cooling rate on the solidification of Cu58Co42[J]. Materials Science and EngineeringA, 2007, 449/450/451: 644- 648.
[15] Nagase T, Suzuki M, Tanaka T. Formation of amorphous phase with crystalline globules in Fe-Cu-Nb-B immiscible alloys[J]. Journal of Alloys and Compounds, 2015, 619: 267-274.
[16] Dai X Q, Zhou S F, Wang M F, et al. Microstructure evolution of phase separated Fe-Cu-Cr-C composite coatings by laser induction hybrid cladding[J]. Surface and Coatings Technology, 2017, 324: 518-525.
[17] Liu S C, Jie J C, Guo Z K, et al. Solidification microstructure evolution and its corresponding mechanism of metastable immiscible Cu80Fe20 alloy with different cooling conditions[J]. Journal of Alloys and Compounds, 2018, 742: 99-106.
[20] 谢敏, 戴晓琴, 赵淑珍, 等. 激光熔覆自组装Cu92Fe8偏晶复合涂层的相分离特征与性能[J]. 中国激光, 2018, 45(7): 0702010.
[21] Dai X Q, Zhou S F, Wang M F, et al. Effect of substrate types on the microstructure and properties of Cu65Fe35 composite coatings by laser induction hybrid cladding[J]. Journal of Alloys and Compounds, 2017, 722: 173-182.
[27] Zhou S F, Lei J B, Dai X Q, et al. A comparative study of the structure and wear resistance of NiCrBSi/50 wt.% WC composite coatings by laser cladding and laser induction hybrid cladding[J]. International Journal of Refractory Metals and Hard Materials, 2016, 60: 17-27.
[31] 曾晓雁. 激光熔覆金属陶瓷复合层中陶瓷相的行为研究[D]. 武汉: 华中理工大学, 1993.
Zeng XY. Behavior of ceramic phase in laser cladding cermet composite layer[D]. Wuhan: Huazhong University of Science and Technology, 1993.
赵淑珍, 金剑波, 谢敏, 许永波, 戴晓琴, 周圣丰. 扫描速率对激光熔覆Cu80Fe20偏晶涂层组织与耐磨性能的影响[J]. 中国激光, 2019, 46(3): 0302005. Shuzhen Zhao, Jianbo Jin, Min Xie, Yongbo Xu, Xiaoqin Dai, Shengfeng Zhou. Effects of Scanning Speed on Microstructure and Wear Resistance of Cu80Fe20 Immiscible Coatings Prepared by Laser Cladding[J]. Chinese Journal of Lasers, 2019, 46(3): 0302005.