248 nm准分子激光刻蚀的无裂损石英玻璃表面微通道
下载: 937次
1 引言
微流控芯片技术具有微型化、集成化、高效率等优势[1-2],在生物医学检测、化学反应等领域得到了广泛关注。玻璃材料具有良好的透光性、亲水性、电绝缘性、化学稳定性等优势[3],尤其是高纯度的熔融石英玻璃在紫外波段具有良好的透光性,是微流控芯片的理想基底材料之一。近年来,利用激光对玻璃材料微纳结构进行加工成为了国内外学者的研究热点之一。目前,采用高能激光束加工石英玻璃微结构的方法主要有激光诱导等离子体加工、超短脉冲激光加工和纳秒脉冲紫外激光加工。激光诱导等离子体加工主要采用激光诱导固体或液体靶材产生等离子体,从而间接刻蚀石英玻璃。2007年,Kawaguchi等[4]报道了利用较高吸收率的靶溶液在石英片上进行激光诱导背部湿刻蚀,成功完成了宽度为9 μm、深度为300 μm的高深宽比微槽的刻蚀加工,但该方法的刻蚀效率非常低,刻蚀率仅为每脉冲10 nm。超短脉冲激光加工主要是将飞秒脉冲激光聚焦光敏玻璃材料内部来直写改性材料[5-7],并通过酸腐蚀制作玻璃内部微通道。该方法获得的三维微通道无需键合,而且可以得到三维立体结构的微流控芯片。然而,目前飞秒激光加工系统的加工效率和稳定性较低。近年来,关于飞秒激光[8]和皮秒激光[9]对玻璃材料的直接损伤也在不断研究中,其工业化应用还有待发展。纳秒脉冲紫外激光加工主要采用准分子气体激光器及固体激光器,如Lan等[10-11]采用355 nm三倍频固体激光器直写刻蚀石英玻璃表面微通道,但玻璃边缘裂损现象比较严重;Ihlemann等[12]采用248 nm(KrF)纳秒准分子激光直接刻蚀石英玻璃时也存在裂损的情况,单独采用157 nm(F2)[13]或193 nm(ArF)[12,14]纳秒脉冲准分子激光器可以直接实现石英玻璃无裂损的刻蚀加工,但刻蚀率较低(157 nm、193 nm激光的刻蚀率分别小于每脉冲80 nm、200 nm);而Zhang等[15]利用157 nm(F2)及248 nm(KrF)两种准分子激光和双光束复合的方法,也实现了对石英玻璃的无裂损刻蚀,但该方法所使用的加工系统复杂程度高,且调试难度大。到目前为止,玻璃微流控芯片的激光加工,由于受加工效率、系统稳定性方面的制约,未能实现工业规模化。
目前,248 nm纳秒脉冲准分子激光器成为了微加工领域主要的工业应用激光器,具有输出稳定、单脉冲能量高等优势。本文深入分析了248 nm纳秒脉冲准分子激光刻蚀石英玻璃过程的机理,研究了无裂损刻蚀石英玻璃的方法以及激光直接加工石英玻璃发生裂损的影响因素,实现了不同形状的石英玻璃表面微通道的无裂损加工。利用该技术制作微流控芯片,具有结构质量好、加工效率高等优势。
2 实验材料及方法
2.1 实验材料及处理方法
实验中使用的石英玻璃材料为1 mm厚的江苏宜兴晔辉玻璃仪器厂生产的JGS1型熔融石英玻璃片,试样尺寸为20 mm×20 mm。JGS1型熔融石英玻璃具有较高的纯度和均匀性,其中SiO2的质量分数不低于99.96%,另含有极少量的金属杂质离子及羟基,该石英玻璃在190~2500 nm波段范围内的透光性良好。实验前将石英玻璃试样放入无水乙醇中超声清洗10 min,然后取出风干。
2.2 实验装置及研究方法
采用准分子激光掩模投影直写加工系统,实验装置示意图如
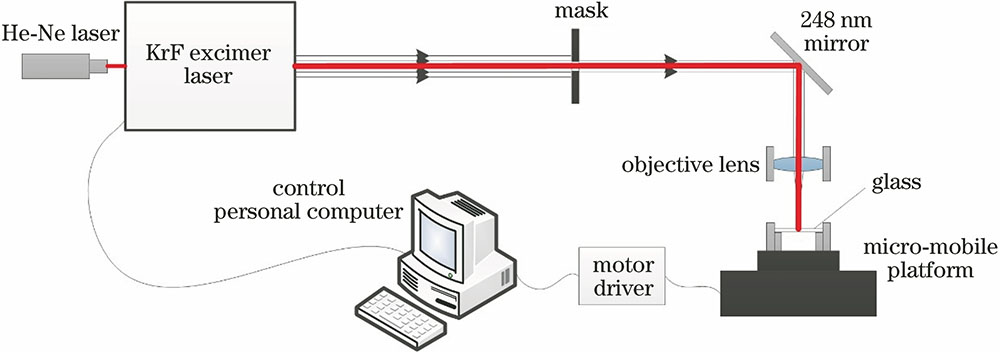
图 1. 248 nm准分子激光加工玻璃装置示意图
Fig. 1. Schematic of setup for glass processed by 248 nm excimer laser
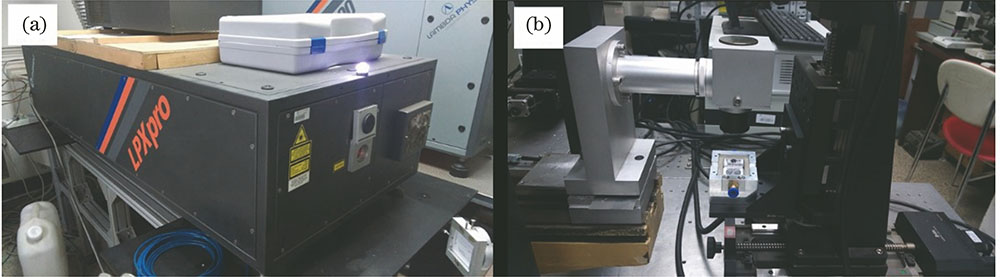
图 2. 实验主要装置。(a)准分子激光器;(b)加工平台
Fig. 2. Main experimental setups. (a) Excimer laser; (b) processing platform
激光器为美国Coherent公司生产的LPXpro型准分子激光器(工作气体:KrF,波长:248 nm,激光脉冲工作重复频率:1~50 Hz,脉宽:30 ns,最大输出单脉冲能量:1200 mJ),其实物图如
加工前调节掩模孔位置,使所透过的激光束为准分子激光器输出激光束的中心区域,该区域光束的激光能量密度较高且分布相对均匀。加工时试样悬空放置(即上下表面均为空气),且其上表面位于掩模投影的像面附近,调节激光输出脉冲能量大小及样品位置,使试样上表面处的激光能量密度达到石英玻璃的刻蚀阈值。
实验时,分别采用激光束相对样品静止的静态点刻蚀方法及激光扫描直写方法,以研究刻蚀机理及无裂损刻蚀石英玻璃的激光能量阈值。然后采用激光扫描直写的方法研究无裂损加工石英玻璃表面微通道的方法,并观察刻蚀加工过程中的实验现象。加工实验完成后,利用光学显微镜及日本日立公司S-3400N扫描电子显微镜(SEM)观察石英玻璃表面加工后的表面形貌并分析成分元素含量,采用美国Veeco公司的Wyko NT1100白光干涉仪测量石英表面微结构的尺寸参数,利用美国Newport公司的1918-R激光能量计测量刻蚀位置处的激光单脉冲能量。实验中测得刻蚀处聚焦投影正方形激光光斑的边长为95 μm,测得的刻蚀处激光单脉冲能量除以正方形光斑的面积即可获得刻蚀位置的激光平均能量密度。
3 实验结果与分析
3.1 248 nm纳秒脉冲准分子激光与石英玻璃作用过程的机理
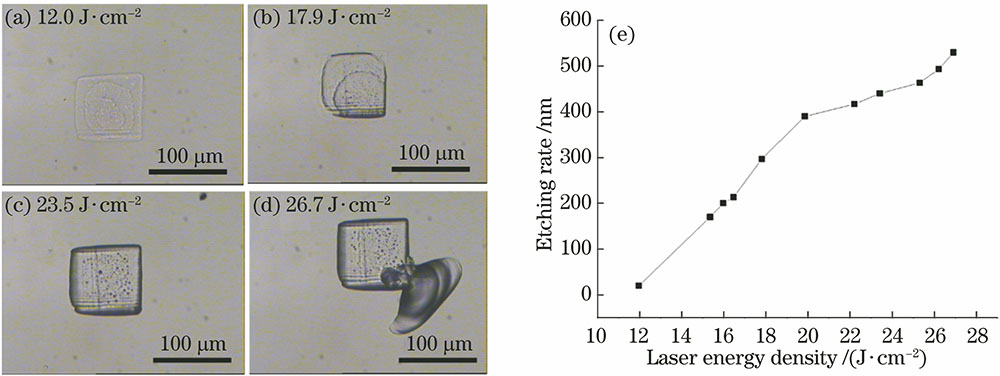
图 3. (a)~(d)不同激光能量密度下的刻蚀石英玻璃表面后的光学显微镜照片;(e)激光对石英玻璃的刻蚀率随激光能量密度的变化情况
Fig. 3. (a)-(d) Optical microscope photographs of silicon glass etched under different laser energy densities; (e) laser etching rate for silica glass versus laser energy density
不同激光能量密度作用于石英玻璃的刻蚀结果如
以上所测得的激光能量密度为其刻蚀光斑内的平均值。由白光干涉仪测量的静态刻蚀微槽底部的形貌如
式中
由(1)~(2)式可知
由(3)式可得,当
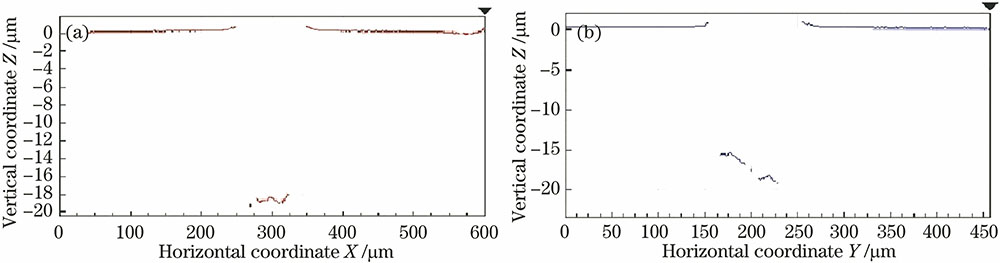
图 4. 静态刻蚀微槽的底部形貌在(a) X及(b) Y方向上的变化趋势
Fig. 4. Changing trends of bottom morphology of statically etched micro-groove in X and Y directions
激光刻蚀石英玻璃的表面形貌及分析如下。石英玻璃发生无裂损刻蚀的微观结构形貌如
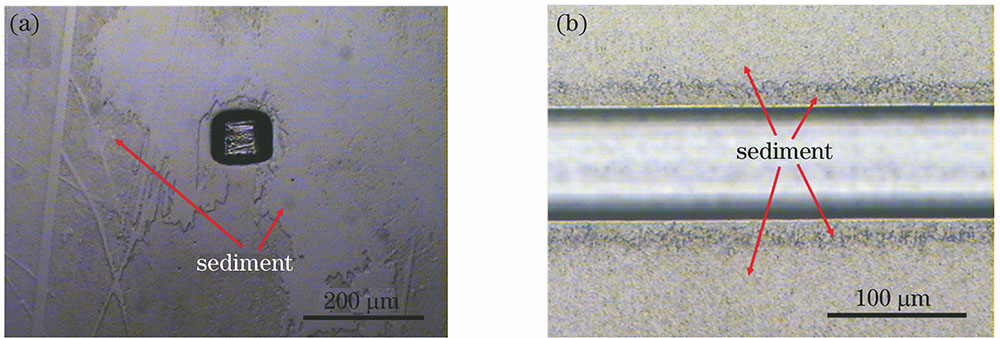
图 5. 石英玻璃刻蚀的光学显微镜照片。(a)静态刻蚀方槽的周边沉积物的形貌;(b)直写刻蚀微通道沉积物的形貌
Fig. 5. Optical microscope photographs of etched silica glass. (a) Morphology of sediment surrounding statically etched groove; (b) morphology of sediment of direct-writing etched micro-groove
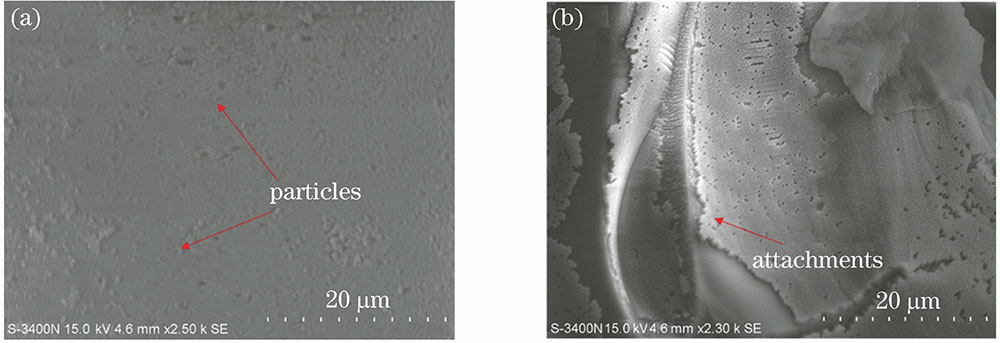
图 6. 石英玻璃刻蚀后沉积物的局部SEM照片。(a)散落的微颗粒;(b)熔融的附着物
Fig. 6. Local SEM photos for sediment of etched silica glass. (a) Scattered particles; (b) fused attachments
通过SEM对石英玻璃的基底物质及刻蚀后表面附着层物质进行能谱分析,结果见
表 1. 石英玻璃刻蚀前后的化学成分含量(原子数分数,%)
Table 1. Chemical compositions of silica glass before and after etching (atomic fraction, %)
|
基于以上实验现象及结果可知,248 nm纳秒准分子激光刻蚀石英玻璃过程中的光致电离存在多种电离机制。石英玻璃中含有微量的金属杂质离子缺陷对紫外激光具有较强的吸收作用,可以引起光致离子缺陷电离。石英玻璃中主要成分硅氧键的键能为4.7 eV,而248 nm波长的光子能量约为5.0 eV,略高于硅氧键的键能。但由于石英玻璃的微观结构是硅氧四面体以顶角相连形式组成的无规则三维网络结构,当较低能量密度激光辐照时,离子无法摆脱硅氧四面体网络结构的束缚,石英玻璃不能发生电离刻蚀。当激光能量密度较高时,激光对石英玻璃的光化学电离速率大于其束缚结合速率,可以使材料发生电离刻蚀;并且由于激光脉冲作用的时间为纳秒量级,光致电离物质对辐照的激光产生重吸收而发生强烈的等离子体团爆炸现象,同时此过程也伴随有热烧蚀而产生熔融状的生成物。因此,激光能量密度是决定石英玻璃材料发生刻蚀以及产生碎裂的关键因素之一。
3.2 248 nm准分子激光静态刻蚀石英玻璃发生裂损的相关诱因
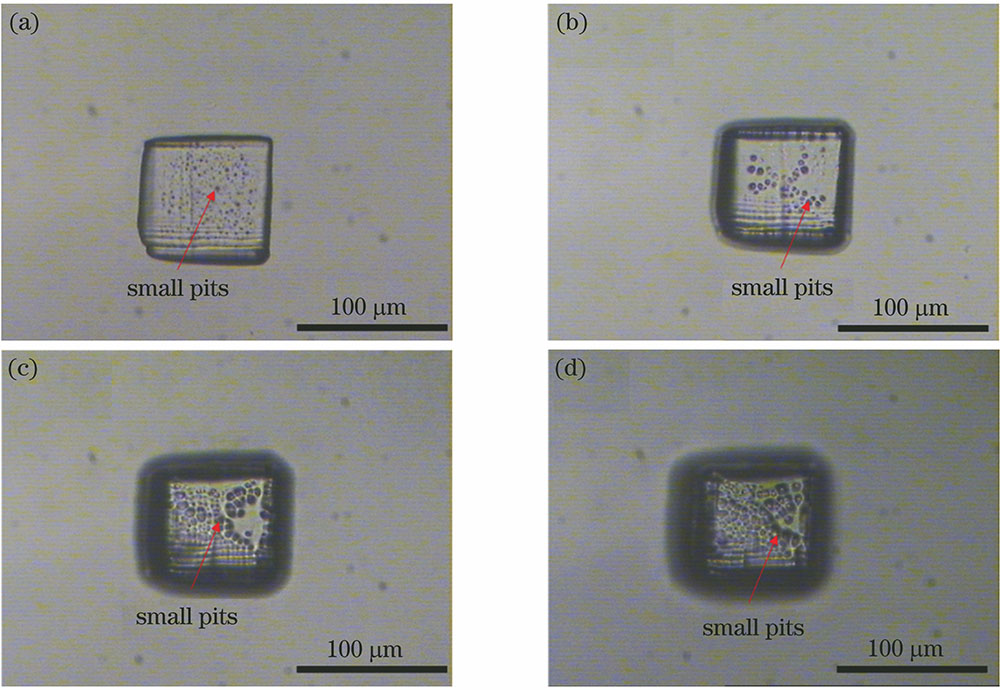
图 7. 不同激光脉冲个数作用下微槽底部的形貌。(a) 20个脉冲;(b) 40个脉冲;(c) 80个脉冲;(d) 120个脉冲
Fig. 7. Bottom morphologies of micro-grooves under different numbers of laser pulses. (a) 20 pulses; (b) 40 pulses; (c) 80 pulses; (d) 120 pulses
石英玻璃原始表面的结构缺陷(裂纹和微碎块)对激光加工玻璃产生裂损情况的影响也非常大。如
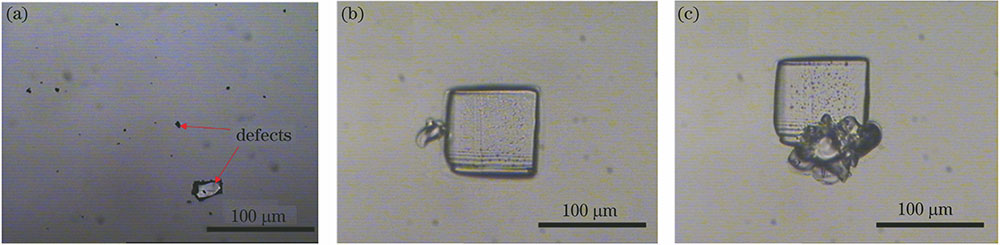
图 8. 石英玻璃表面有缺陷时的裂损情况。(a)原始表面; (b)刻蚀后的裂损情况1; (c)刻蚀后的裂损情况2
Fig. 8. Crack conditions of silica glass surface with defect. (a) Original surface; (b) crack condition 1 after etching; (c) crack condition 2 after etching
静态刻蚀所使用的准分子激光器的脉冲触发模式为激光器内部信号触发,脉冲重复频率最高只有10 Hz,改变激光重复频率对刻蚀结果基本无影响。这主要是由于该模式下脉冲间隔最短约为1 ms,远大于激光脉冲的脉宽(30 ns)、激光与材料的作用时间(10 fs~10 ns)及等离子体的膨胀和辐射时间(1 ns~100 μs)[17],因此产生的热积累较弱,重复频率的改变对石英玻璃静态刻蚀结果的影响不明显。
3.3 248 nm准分子激光无裂损直写刻蚀石英玻璃的表面微通道
激光扫描直写刻蚀石英玻璃微通道受激光脉冲重复频率和扫描速率变化的影响较大。激光扫描直写刻蚀位置处的实际激光光斑尺寸为95 μm×95 μm,激光器的脉冲触发方式为外部触发,重复频率最高为50 Hz,此时激光器的最高工作电压为21 kV,激光能量密度为23.5 J·cm-2,扫描速率为6 mm·min-1,在不同激光重复频率下扫描一次获得的石英玻璃微通道如
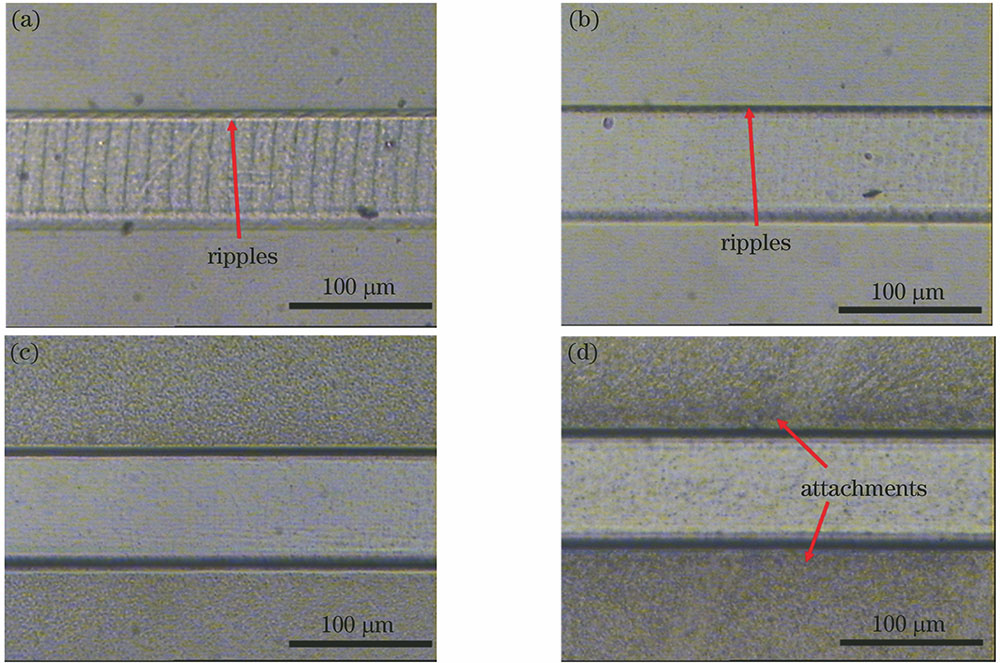
图 9. 不同激光重复频率下石英玻璃微通道的形貌。(a) 6 Hz; (b) 10 Hz; (c) 20 Hz; (d) 50 Hz
Fig. 9. Morphologies of silicon glass micro-grooves under different laser repetition frequencies. (a) 6 Hz; (b) 10 Hz; (c) 20 Hz; (d) 50 Hz
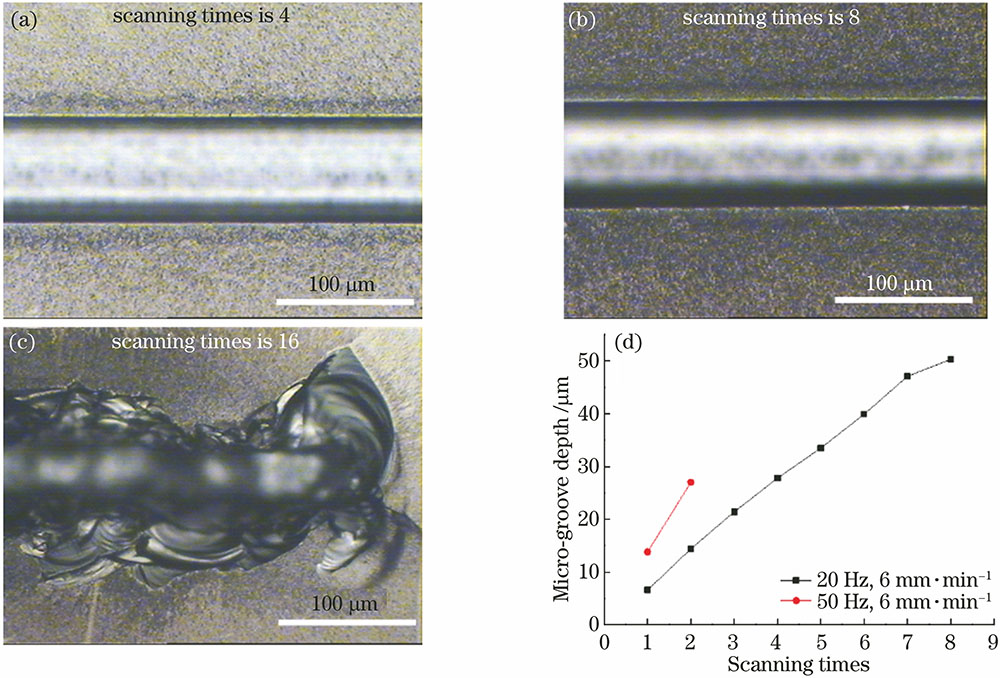
图 10. (a)~(c)当重复频率为20 Hz时,不同扫描次数下的微通道光学显微镜照片;(d)微通道深度随扫描次数的变化
Fig. 10. (a)-(c) Optical microscope photos of micro-grooves under different scanning times at repetition frequency of 20 Hz; (d) micro-groove depth versus scanning times
当激光重复频率和扫描速率一定时,通过多次反复扫描直写不同形状的表面微通道来研究微通道裂损情况随刻蚀深度的变化规律。
激光直写圆形微通道时,系统采用圆弧插补的运动方式进行多次重复扫描,结果如
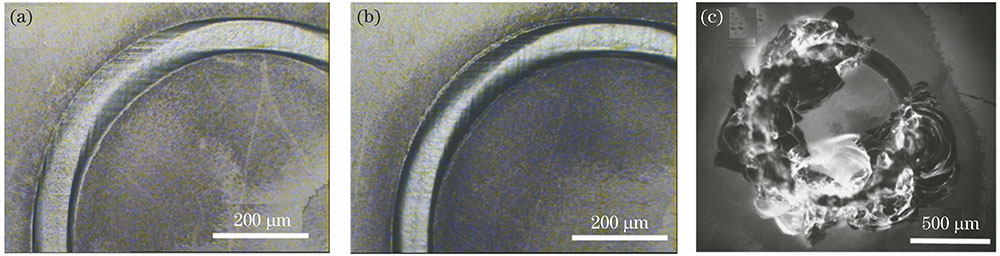
图 11. 当重复频率为50 Hz、扫描次数为(a)1和(b)2时,圆形微通道的光学显微镜照片;(c)当重复频率为30 Hz、扫描次数为3时,圆形微通道的光学显微镜照片
Fig. 11. Optical microscope photos of circular micro-grooves when scanning times is (a) 1 and (b) 2 at repetition frequency of 50 Hz; (c) optical microscope photo of circular micro-groove when scanning times is 3 at repetition frequency of 30 Hz

图 12. 当激光能量密度为23.5 J·cm-2、扫描速率为6 mm·min-1时,无裂损石英玻璃表面微通道的光学显微镜照片。(a)整体结构;(b)圆弧段(激光重复频率50 Hz);(c)直线段(激光重复频率40 Hz)
Fig. 12. Optical microscope photos of crack-free silica glass micro-grooves when laser energy density is 23.5 J·cm-2 and scanning speed is 6 mm·min-1. (a) Overall structure; (b) circular arc section (laser repetition frequency is 50 Hz); (c) straight line section (laser repetition frequency is 40 Hz)
基于以上研究,设计了优化的激光加工参数,进行了直线段及圆弧段复合连接的石英玻璃表面微通道的加工研究。
4 结论
实验研究了248 nm纳秒脉冲准分子激光无裂损加工JGS1型石英玻璃表面微通道的方法,结论如下。
1) 准分子激光刻蚀石英玻璃的机理为光致电离及光热效应的共同作用,激光能量密度决定了电离产生的等离子体冲击强度,激光重复频率决定了加工过程中的热积累程度,通过调节激光能量密度及重复频率可以实现对石英玻璃的无裂损刻蚀加工。
2) 激光能量密度是决定石英玻璃发生刻蚀及裂损的主要因素之一。无裂损刻蚀石英玻璃的激光能量密度阈值区间为16~30 J·cm-2,激光能量低于该区间时不能发生有效刻蚀,高于该区间容易引发材料的裂损;激光对石英玻璃的刻蚀率随着激光能量密度的增大而增大,最大刻蚀率可达每脉冲500 nm。
3) 诱发激光加工石英玻璃发生裂损的因素还有:石英玻璃材料原始表面的缺陷,刻蚀激光光斑能量密度的不均匀分布所导致的小麻点状缺陷,多次重复扫描时轨迹的不重合;另外,随着刻蚀深度的增加,等离子体团爆炸对玻璃微通道侧壁的冲击强度增大,而侧壁受激光冲击次数增多,其耐疲劳性能及抗压能力降低,也容易发生裂损。
4) 基于优化的激光加工参数,当石英玻璃表面微通道的宽度小于100 μm时,可以实现无裂损直线型(深度小于或等于50 μm)及圆弧型(深度小于或等于28.5 μm)微通道的加工,扫描一次获得的直线段及圆弧段复合连接的无裂损石英玻璃表面微通道的总长度超过21 mm。
研究结果为高效率激光加工玻璃微流控芯片及硬脆性材料微结构器件提供了一定的参考。
[1] 郑小林, 鄢佳文, 胡宁, 等. 微流控芯片的材料与加工方法研究进展[J]. 传感器与微系统, 2011, 30(6): 1-4, 7.
[2] 耿利娜, 全宗良, 侯妮, 等. 蛋白质分离玻璃微流控芯片的制作方法[J]. 北京理工大学学报, 2013, 33(4): 436-440.
[5] 何飞, 程亚. 飞秒激光微加工: 激光精密加工领域的新前沿[J]. 中国激光, 2007, 34(5): 595-622.
[6] 蔡海龙, 闫雪亮, 王素梅, 等. 飞秒激光微通道加工研究进展[J]. 北京理工大学学报, 2012, 32(10): 991-1003.
[8] 黄媛媛, 钱静, 邵冲云, 等. 飞秒激光在不同羟基浓度纯石英玻璃内部诱导缺陷研究[J]. 中国激光, 2017, 44(1): 0102011.
[9] 郝艳飞, 孙明营, 时双, 等. 皮秒激光烧蚀K9玻璃后表面损伤研究[J]. 中国激光, 2017, 44(1): 0102015.
[11] 王汕. 激光刻蚀抛光石英玻璃工艺研究[D]. 武汉: 华中科技大学, 2012.
WangShan. A study on laser etching and polishing quartz glasses technology[D]. Wuhan: Huazhong University of Science & Technology, 2012.
[13] 戴玉堂, 徐刚, 崔健磊. 透明材料的深紫外激光三维微刻蚀工艺[J]. 应用激光, 2009, 29(5): 411-414.
[14] IhlemannJ. UV-laser ablation of fused silica mediated by solid coating absorption[C]. SPIE, 2007, 6458: 64580E.
[16] 刘志超, 许乔, 欧阳升, 等. 熔石英紫外激光初始损伤形态分析分析[J]. 强激光与离子束, 2009, 21(7): 1207-1211.
[17] 王聪. 基于电子动态调控的超快激光微纳制造新方法的第一性原理计算及其验证[D]. 北京: 北京理工大学, 2014: 19- 26.
WangCong. First-principles calculations and their validations for ultrafast micro/nanofabrication based on electron dynamics control[D]. Beijing: Beijing Institute of Technology, 2014: 19- 26.
Article Outline
杨桂栓, 陈涛, 陈虹. 248 nm准分子激光刻蚀的无裂损石英玻璃表面微通道[J]. 中国激光, 2017, 44(9): 0902004. Yang Guishuan, Chen Tao, Chen Hong. Crack-Free Silica Glass Surface Micro-Grooves Etched by 248 nm Excimer Lasers[J]. Chinese Journal of Lasers, 2017, 44(9): 0902004.