基于单幅图像的集成电路引脚共面性检测方法
下载: 1218次
1 引言
印刷电路板(PCB)是电子产品的核心部件,而集成电路(IC)芯片作为PCB重要的电子器件,其贴装质量的好坏将直接影响电子产品的品质。表面贴装型IC因具有集成度高 、管脚多、间距小等特点,目前已成为主流的封装形式。引脚是IC芯片内部电路与PCB上电路连接的“桥梁”。若IC芯片引脚不满足共面性要求,即最低引脚平面与最高引脚平面的垂直距离大于0.1 mm[1-3],在贴装时易出现空焊、连锡等缺陷,从而影响电子产品的功能和寿命,因此,IC芯片引脚的共面性检测是确保其贴装质量的关键。目前,对IC引脚的共面性检测方法主要分为两类,即二维检测法和三维检测法。二维检测法通过采集样品图片,分析IC引脚特征,进而实现IC缺陷的检测和分类[4-6]。三维检测法则通过恢复IC引脚样品表面的三维形貌,进而评估其与正常良品的差异,以检测IC引脚贴装缺陷[7]。与二维检测法相比,三维检测法对待测物体的颜色、纹理、边缘等特征依赖程度较低,可更全面地评价待测物体的质量[8]。
三维检测法可分为接触式和非接触式检测。接触式检测主要有三坐标测量机[9-10]和接触式轮廓仪[11-12],该类方法的测量精度高,但速度慢,且在测量时需要与待测物体进行接触,容易对待测物体表面造成损伤[13]。非接触式检测主要是光学测量方法。光学测量方法可分为两类,即主动检测法和被动检测法[13-15]。主动检测法对IC引脚投射特定的结构光,被引脚调制的结构光经解调后可得引脚的三维信息。主动检测法主要有飞行时间法[16]、激光三角法[17]、结构光法[18]等。主动检测法测量精度高,但易受环境光线的干扰,此外在检测过程中需确保引脚表面各区域均被光源照射,因此,该过程需移动物体或光源,易出现移位误差而导致误判。被动检测主要依靠环境光或结构光反射,从一个或多个摄像头获取的二维图像中提取距离信息,形成三维表面数据[19-20]。被动检测法主要有单目视觉法和双目立体视觉法。单目视觉法使用单个相机采集IC引脚图像,根据光照模型及物体表面特性等先验知识设计算法以恢复IC引脚的三维形貌。双目立体视觉法采用两个相机采集IC引脚在不同视角下的图像,基于三角测量原理,并结合图像特征匹配点的视差信息以恢复IC引脚表面的三维形貌[21]。双目立体视觉法使用前需对两台摄像机的内外参数进行标定,在恢复物体表面三维形貌时需完成不同图像的特征匹配,测量过程复杂且运算量较大[21-24]。而单目视觉法仅需对一台摄像机进行内外参数标定,匹配过程中无图像特征点,利于降低计算量。
为克服双目视觉的图像特征匹配问题和主动检测法的机械移位误判问题,本文基于单幅图像提出一种IC芯片引脚共面性检测方法,用以提高检测精度和稳定性。首先建立IC引脚光照反射模型,分析入射光光强与图像灰度之间的关系;其次在上述关系的基础上建立入射光光强与图像灰度关系模型;最后基于关系模型,提出IC引脚共面性检测方法。
2 单目视觉系统
3 基于单幅图像的三维计算模型
在光学成像系统中,图像中的每一个像素点均为图像传感器上一个微小的感光元,像素点的灰度值能反映进入相机光线的强度。为进一步分析,建立如
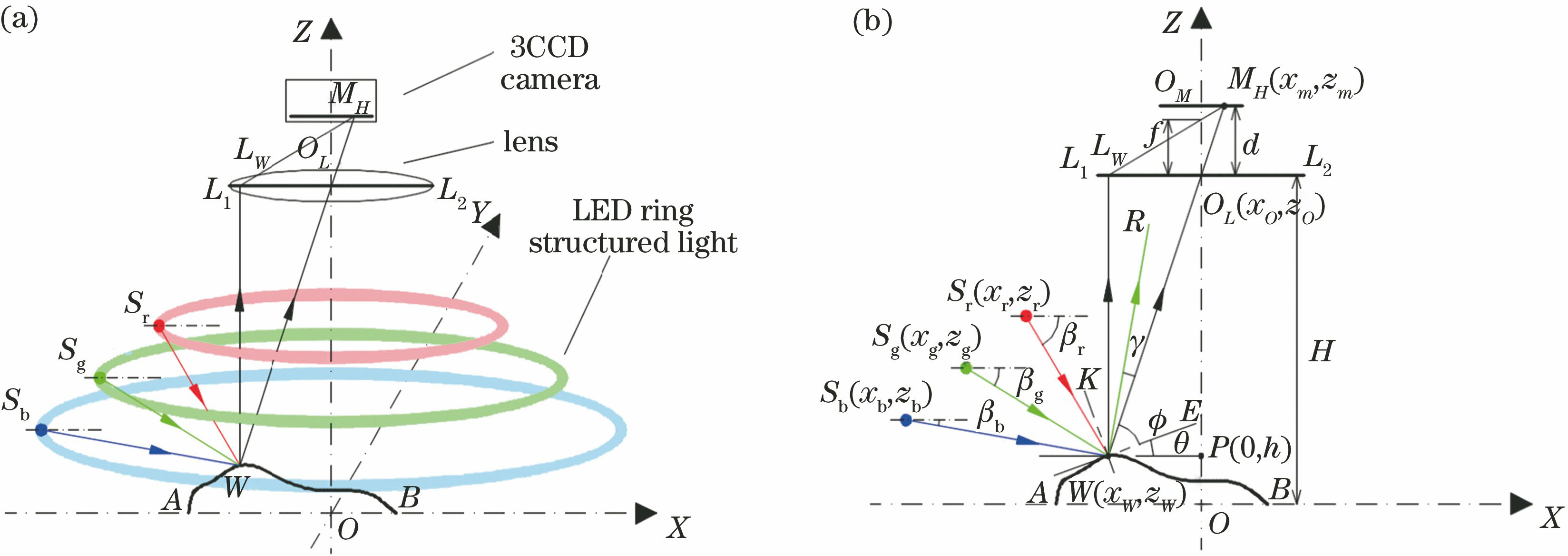
图 3. 单目视觉系统模型。(a)光照模型;(b)简化模型
Fig. 3. Model of monocular vision system. (a) Illumination model; (b) simplified model
在
在所采用的单目视觉系统中,将红、绿、蓝光线与平面XOY的夹角分别设为βr、βg、βb,实际反射光线与在横截面中过W点的切线的夹角为ϕ,则
根据θ,ϕ,β和γ之间的关系,可得红、绿、蓝光理论反射光线和实际反射光线的夹角γr、γg、γb分别为
将(2)式代入(3)式,可得
式中:0<γr<
式中:Gr、Gg、Gb为彩色图像的灰度值;Ir、Ig、Ib可通过实验标定;fr、fg、fb可通过初始实验算出;σW为检测区域,在图像中表示与点W对应的像素点在X和Y方向上的位置;zW为待测点的高度。在所采用的单目视觉系统中,(xr,zr)、(xg,zg)、(xb,zb)均已知,xW可以通过X方向上图像坐标与像素坐标的变换关系确定。因此,在(5)式中,未知量只有zW、ϕ、θ,通过求解(5)式,即可解出此三个未知量。在图像中,所有检测区域均可采用相同的方法求取相应高度信息,进而完成待测物体表面的三维重建,实现表面质量检测。
4 实验结果与分析
在工业检测中,常用的IC芯片尺寸小于10 mm×10 mm,少数IC芯片的最大尺寸小于18 mm×12 mm。为检测本文方法的有效性,将针对实测最大高度为1.58 mm的IC芯片引脚及其焊点进行三维测量实验。实验过程采用环形结构光源,且相机成像视场为24 mm×18 mm(满足绝大部分IC芯片的检测),相机分辨率为1024 pixel×768 pixel。实验所用的软件为MATLAB R2017a。实验所用计算机配置为双核 Intel(R) Core(TM) i5-4210U CPU 1.70 GHz,2.40 GHz处理器,8 GB内存,64位操作系统。
检测过程中,被测材质对光的反射特性易受入射光强的影响。实验前,使用照度计标定环形结构光源焦点处的光强,分别为Ir=2510 cd,Ig=2620 cd,Ib=766 cd。为测得材料对光的影响系数,需采用与IC引脚相似材质的标定物进行初始实验。初始实验将已知高度的焊锡垫片作为标定物,使用与环形结构光源光强相同的单色LED点光源,以不同入射角照射焊锡标定物,获得一组图像序列,分析图像序列中处于标定物同一位置标定点的灰度变化规律,通过实验数据拟合出入射角与灰度值函数方程,从而确定方程中材料对光的影响系数[27]。如
表 1. 材料对光的影响系数
Table 1. Effect coefficient of material on light
|
表 3. 基于灰度迭加法的IC焊点及引脚的三维检测结果
Table 3. 3D detection results of IC solder joints and pins based on gray superposition methodmm
|
图像进行预处理后,基于IC引脚图像的颜色特征对引脚进行区域划分,分为引脚外侧焊点区域、靠近外侧焊点的引脚根部区域、靠近芯片本体的引脚顶部区域、根部区域和顶部区域之间的引脚过渡区域,对不同区域分别进行计算。
表 2. IC焊点和引脚的三维检测结果
Table 2. 3D detection results of IC solder joints and pinsmm
|
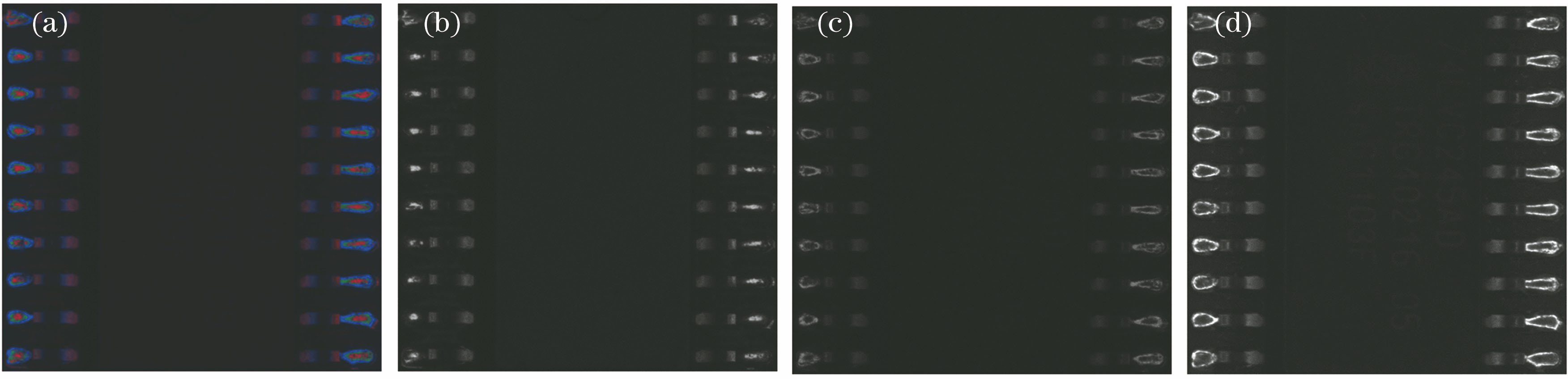
图 4. IC图。(a)原图;(b)红色通道;(c)绿色通道;(d)蓝色通道
Fig. 4. IC diagrams. (a) Original image; (b) red channel; (c) green channel; (d) blue channel

图 5. IC芯片重建图。(a) IC芯片侧视图;(b) IC芯片Y方向视图
Fig. 5. Reconstruction result of IC. (a) Sideview of IC; (b) Y direction view of IC
为进一步检验实验结果的有效性,实验过程中将测得的高度信息转换为实际高度,并与实际测量的引脚及其焊点的三维图进行对比。为节省检测时间,截取原始图像中IC芯片引脚部分进行测量。在572 pixel×589 pixel的芯片图像中,取左侧焊点X轴像素为30和左侧引脚根部X轴像素为66的截面,焊点截面如
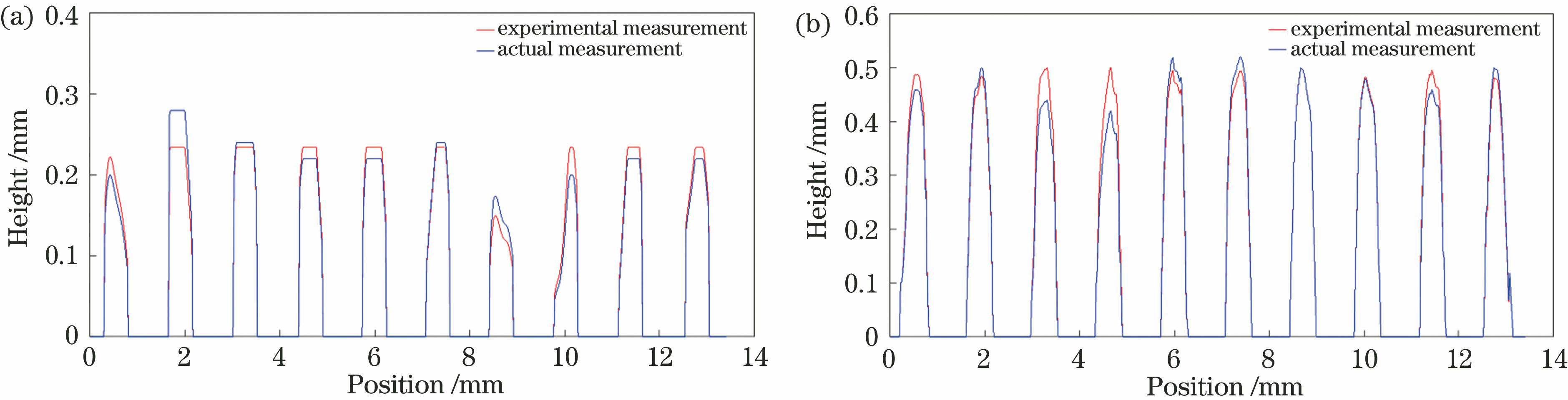
图 6. IC芯片截面图。(a) IC芯片焊点截面;(b) IC芯片引脚截面
Fig. 6. Cross-sections of IC. (a) Cross-section of IC solder joints; (b) cross-section of IC pins
如
为进一步检验本文方法的有效性,采用基于单目视觉的灰度迭加法[27]对
如
为了进一步证明本文方法的可重复性,使用如

图 8. 灰度迭加法的IC芯片重建图。(a) IC芯片侧视图;(b) IC芯片Y方向视图
Fig. 8. Reconstruction results of IC by using gray superposition method. (a) Sideview of IC; (b) Y direction view of IC
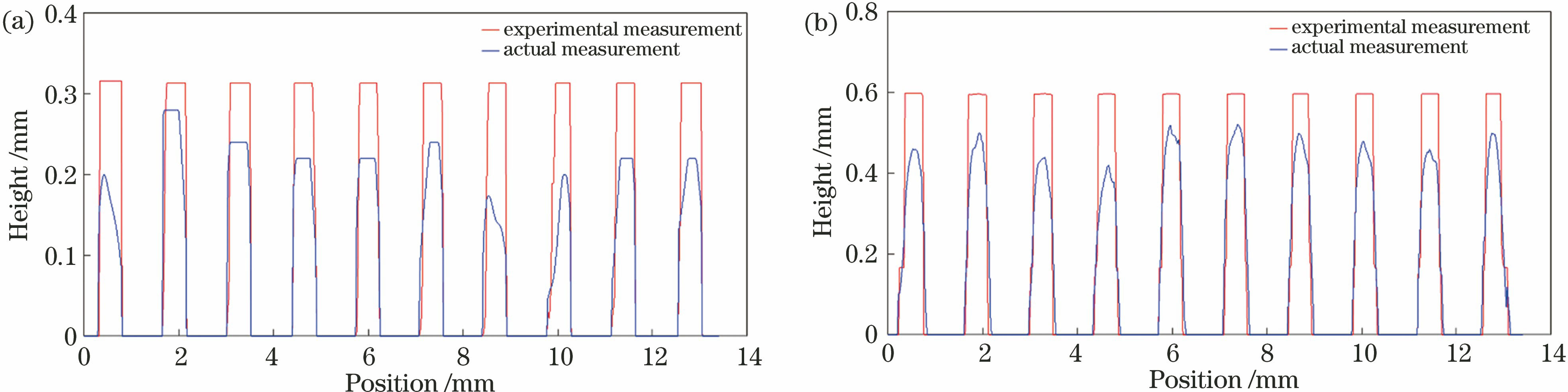
图 9. 灰度迭加法的IC芯片截面图。(a) IC芯片焊点截面;(b) IC芯片引脚截面
Fig. 9. Cross-sections of IC by using gray superposition method. (a) Cross-section of IC solder joints; (b) cross-section of IC pins
5 结论
基于单目视觉成像系统,建立入射光光强与图像灰度值的关系模型,提出基于恢复待测物表面形貌的三维检测方法。在标定红、绿、蓝三色入射光强的过程中,建立该三色光光照强度与其三通道图像灰度的对应关系模型,并给出关系模型中高度信息的求解方法,该方法能准确恢复引脚及其焊点的表面形貌,实现引脚共面性检测。采用本文方法检测,不仅可恢复待测物体的表面形貌,还可基于求解出的倾角信息对所得的高度信息进行检验,从而提高了重建精度和检测的可靠性。实验结果表明:本文方法的测量结果与实际高度的误差小于±0.08 mm,相对误差为-2.6%,检验了本文方法的有效性;IC芯片检测误差的置信区间为[-5%,5%],置信水平为95.12%,表明本检测方法具有较好的稳定性。
[1] 杨城, 邓勇. 表面贴装集成电路引脚整形研究[J]. 电子与封装, 2014, 14(9): 5-8, 32.
Yang C, Deng Y. The study of reforming pins for surface mount integrated circuit[J]. Electronics and Packaging, 2014, 14(9): 5-8, 32.
[2] 中华人民共和国国家质量监督检验检疫总局. 半导体集成电路封装术语: GB/T 14113-1993[S]. 北京: 中国标准出版社, 1993.
General administration of quality supervision, inspectionandquarantine of the people's republic of China. Terminology of packages for semiconductor integrated circuits: GB/T 14113-1993[S]. Beijing: China Standards Press, 1993.
[3] 中华人民共和国工业和信息化部. 半导体集成电路小外形封装引线框架规范: GB/T 15878-2015[S]. 北京: 中国标准出版社, 2015.
Ministry ofindustryandinformationtechnology. Semiconductor integrated circuits—specification of leadframes for small outline package: GB/T 15878-2015[S]. Beijing: China Standards Press, 2015.
[4] Wu F, Zhang X. Feature-extraction-based inspection algorithm for IC solder joints[J]. IEEE Transactions on Components, Packaging and Manufacturing Technology, 2011, 1(5): 689-694.
[5] Cai N, Lin J, Ye Q, et al. A new IC solder joint inspection method for an automatic optical inspection system based on an improved visual background extraction algorithm[J]. IEEE Transactions on Components, Packaging and Manufacturing Technology, 2016, 6(1): 161-172.
[6] Chen S H, Perng D B. Automatic optical inspection system for IC molding surface[J]. Journal of Intelligent Manufacturing, 2016, 27(5): 915-926.
[7] Wen X, Song K, Niu M, et al. A three-dimensional inspection system for high temperature steel product surface sample height using stereo vision and blue encoded patterns[J]. Optik, 2017, 130: 131-148.
[8] 宋丽梅, 周兴林, 徐可欣, 等. 基于单幅测量图像的三维缺陷检测技术[J]. 光学学报, 2005, 25(9): 1195-1200.
[9] Li Y D, Gu P H. Free-form surface inspection techniques state of the art review[J]. Computer-Aided Design, 2004, 36(13): 1395-1417.
[10] Sidki H M, Amer M. Evaluation of CMM for flatness measurements[J]. Metrology and Measurement Systems, 2008, 15(4): 585-593.
[11] 周明宝, 林大健, 郭履容, 等. 微结构表面形貌的测量[J]. 光学精密工程, 1999, 7(3): 7-13.
Zhou M B, Lin D J, Guo F R, et al. Measurement of microstructure surface topography[J]. Optics and Precision Engineering, 1999, 7(3): 7-13.
[12] YangL, GaoY, Wang XZ, et al., 2005, 295/296: 489- 494.
[15] 郭萌, 胡辽林, 李捷. 基于多幅图像的陶瓷碗表面缺陷的局部点云重建[J]. 光学学报, 2017, 37(12): 1215002.
[16] Lange R, Seitz P. Solid-state time-of-flight range camera[J]. IEEE Journal of Quantum Electronics, 2001, 37(3): 390-397.
[18] 潘伟, 赵毅, 阮雪榆. 结构光测量中获取高精度相位的新方法[J]. 光学学报, 2004, 24(5): 687-691.
[19] Bogue R. Three-dimensional measurements: a review of technologies and applications[J]. Sensor Review, 2010, 30(2): 102-106.
[20] 李进军, 赵宏. 一种基于多模式单演特征检测与匹配的三维视觉测量方法[J]. 光学学报, 2011, 31(7): 0712007.
[21] 王珊, 徐晓. 基于双目单视面的三维重建[J]. 光学学报, 2017, 37(5): 0515004.
Wang S, Xu X. 3D reconstruction based on horopter[J]. Acta Optica Sinica, 2017, 37(5): 0515004.
[22] 雷彦章, 赵慧洁, 姜宏志. 一种单双目视觉系统结合的三维测量方法[J]. 光学学报, 2008, 28(7): 1338-1342.
[23] Wei Y J, Wu C D, Wang Y, et al. Diffusion-based three-dimensional reconstruction of complex surface using monocular vision[J]. Optics Express, 2015, 23(23): 30364-30378.
[24] 曾昭鹏, 张江乐, 魏志尚, 等. 一种基于智能手机成像的三维重建方法[J]. 激光与光电子学进展, 2018, 55(11): 111502.
[25] 卢盛林, 张宪民. 无铅焊点检测光源的分析与优化设计[J]. 光学精密工程, 2008, 16(8): 1377-1383.
[26] 白雪飞, 张宗华. 基于彩色条纹投影术的三维形貌测量[J]. 仪器仪表学报, 2017, 38(8): 1912-1925.
Bai X F, Zhang Z H. 3D shape measurement based on colour fringe projection techniques[J]. Chinese Journal of Scientific Instrument, 2017, 38(8): 1912-1925.
[27] 吴福培, 郭家华, 张宪民, 等. PCB焊点表面三维质量检测方法[J]. 仪器仪表学报, 2018, 39(5): 233-240.
Wu F P, Guo J H, Zhang X M, et al. 3D quality inspection method for PCB solder joint surface[J]. Chinese Journal of Scientific Instrument, 2018, 39(5): 233-240.
Article Outline
吴福培, 朱树锴, 李昇平. 基于单幅图像的集成电路引脚共面性检测方法[J]. 光学学报, 2020, 40(1): 0111023. Fupei Wu, Shukai Zhu, Shengping Li. Coplanarity Inspection Method for Integrated Circuit Pins Based on Single Image[J]. Acta Optica Sinica, 2020, 40(1): 0111023.