离子束抛光等量去除的实现及抛光实验
下载: 1376次
1 引言
现代光学加工技术的一个突破性进展,是基于计算机控制的“小磨头”抛光原理的应用,近年来发展的磁流变抛光、液体射流抛光、气囊进动抛光、大气等离子体抛光和离子束抛光等技术,均为基于这一原理的抛光技术[1-2]。
离子束加工过程中利用离子束流密度分布呈单峰类高斯分布的离子束对待加工件进行刻蚀,采用非接触的加工方式,很好地避免了传统加工过程中的工件磨损、边缘效应、工件负载应力等一系列问题[3]。为了获得好的加工效果,对栅格路径进行刻蚀[4-6],采用的栅格路径加工方式是将待加工件初始面形划分为多个像素数相同的元胞,根据各个元胞内的面形数据进行高度均值求解,解出值即为该元胞区域内各点的平均去除量。另一方面,进行离子束刻蚀时,不同的叠加间距产生的刻蚀效果不同,所以对刻蚀的叠加间距进行分析,实现对光学元件的等量去除。通过分析等量去除的效果,确定等量去除最佳的叠加间距及去除速率,并对各个元胞内的平均去除量求解驻留时间,得到加工数据进行抛光修形。采用栅格路径加工方式降低了系统的运动精度和定位精度要求,对待加工样片的面形参数能够实现较快速度的收敛,提高了加工效率,降低了加工成本。
美国Kodar公司成功地应用了离子束抛光(IBF)技术对凯克望远镜1.8 m主镜微晶玻璃离轴段的残余表面误差进行了校正,主镜经过两次迭代加工,第一次迭代加工后表面误差方均根(RMS)值从0.726 μm降低到0.252 μm,第二次迭代加工后降低到0.090 μm[7-8]。德国IOM研究所使用离子束对150 mm×80 mm的微晶玻璃进行了抛光,抛光后的方均根值小于λ/100,获得了极高的加工精度[9]。国防科技大学分别采用位置加工模式和速度加工模式对光学元件进行了修形,经过两次迭代加工使其面形精度误差方均根值由初始的0.136λ提高到0.01λ(λ= 632.8 nm),平均每次迭代的面形收敛率达到3.7[10]。长春光学精密机械与物理研究所对口径Φ800 mm碳化硅表面硅改性层平面镜进行了抛光,初始面形误差方均根值为57.886 nm,经过两次抛光后RMS值为11.837 nm,收敛率达到4.89[11-13]。
本文通过精确拟合离子束去除函数,基于栅格路径刻蚀方式[11-13],对离子束不同叠加间距的去除量进行理论和实验分析,实现等量去除并给出最佳叠加间距。结合抛光实验进行分析,经过一次迭代抛光后,对比抛光前后的面形误差信息,达到较高的面形收敛率。
2 离子束等量去除的实现
离子束等量去除的实现依赖于稳定的去除函数。离子源激发的高能离子束束形呈高斯分布,因此离子束去除函数可用二维高斯函数来拟合[14-16]。对离子束束形的分布状态进行建模,建立的二维高斯数学模型为
式中:A为离子束的峰值去除率;σx为高斯函数在x方向的正态分布标准差;σy为高斯函数在y方向的正态分布标准差;μ为高斯函数位置参数。
离子束产生的高斯去除函数是对称的,因此σx与σy基本相等。进行去除函数拟合时,将去除函数分布的标准差定义为
为了准确获取离子束的束形分布状态,实验使用西安工业大学设计研发的LZSKS-1300离子束刻蚀机,离子源为射频离子源,测量设备为Zygo VERI FIRE型波面干涉仪[17]。经过大量的工艺实验确定一组离子源稳定的工艺参数:射频功率为200 W;屏栅电压为900 V;屏栅电流为13 mA;氩气流量为50 mL/min(标准状态);工作距离为65 mm;入射角度为0°;稳定工作压强为4.5×10-2 Pa。利用上述参数,对口径Φ50 mm、厚度为3 mm的熔石英平面玻璃进行10 min刻蚀。分析熔石英刻蚀前后的面形信息,拟合得到去除函数分布,如
根据离子束刻蚀过程中去除量线性变化的特点,得出离子束的峰值去除率为133 nm/min。去除函数分布可表示为
式中:30.2为高斯去除函数正态分布标准差σ(单位为pix,pix是Zygo干涉仪检测的单位),对应实际的空间尺寸为3.66 mm。高斯型去除函数的二维表达式转为空间尺寸后的表达式为
离子束高斯型去除函数是对称的,因此可使用高斯型去除函数的母线方程f(x)来表示去除函数,即
采用
2.1 一维等量去除的实现
当离子束的叠加间距分别为σ,1.5σ,2σ,2.5σ,3σ时,根据(5)式拟合得到离子束去除函数,不同位置上对应的高斯函数为
式中:n为高斯叠加的数量;k为σ的倍率系数。叠加后的曲线函数R(x),即去除深度,可表示为
叠加间距分别为σ,1.5σ,2σ的高斯函数叠加分布仿真,如
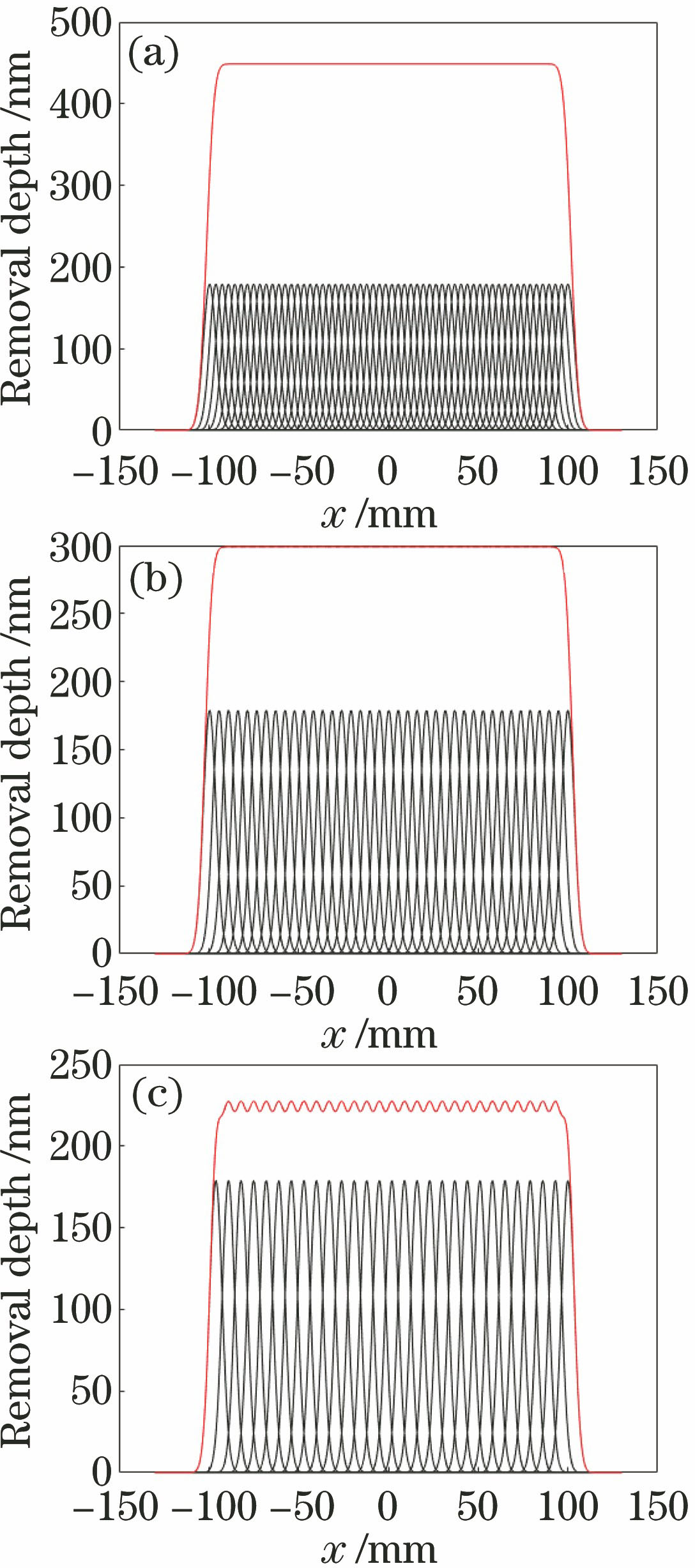
图 3. 不同叠加间距仿真图。(a)叠加间距为σ;(b)叠加间距为1.5σ;(c)叠加间距为2σ
Fig. 3. Simulation of different stacking spacings. (a) Stacking spacing is σ; (b) stacking spacing is 1.5σ; (c) stacking spacing is 2σ
对平稳区域的波动量进行定量分析,为了能够准确地描述波动量,使用的计算公式为
式中:P为叠加后平稳区域的波峰值;V为叠加后平稳区域的波谷值;γ为波动量。
γ值的大小表示波动程度的大小,波动值越大叠加效果越差。波动值分析曲线如
当叠加间距小于σ时,虽然同样能够达到平滑的叠加效果,但是达到叠加平稳状态的去除量时所需的子离子束个数比较多,进行加工时,运动系统随着加工点的增多,会严重影响加工效率。另一方面,叠加间距变小以后,等量去除的去除总量也明显提升,进行加工时要求离子源快速移动,因此要求运动系统有较高的平稳性,然而加工过程中,移动点数越多,加工件尺寸变大时,加工效率会大大降低。选择叠加间距为σ~1.6σ时,能够实现高质量的等量去除,保证加工效率。
对口径Φ50 mm的熔石英光学元件进行刻蚀,验证不同叠加间距下的刻蚀量及波动值。
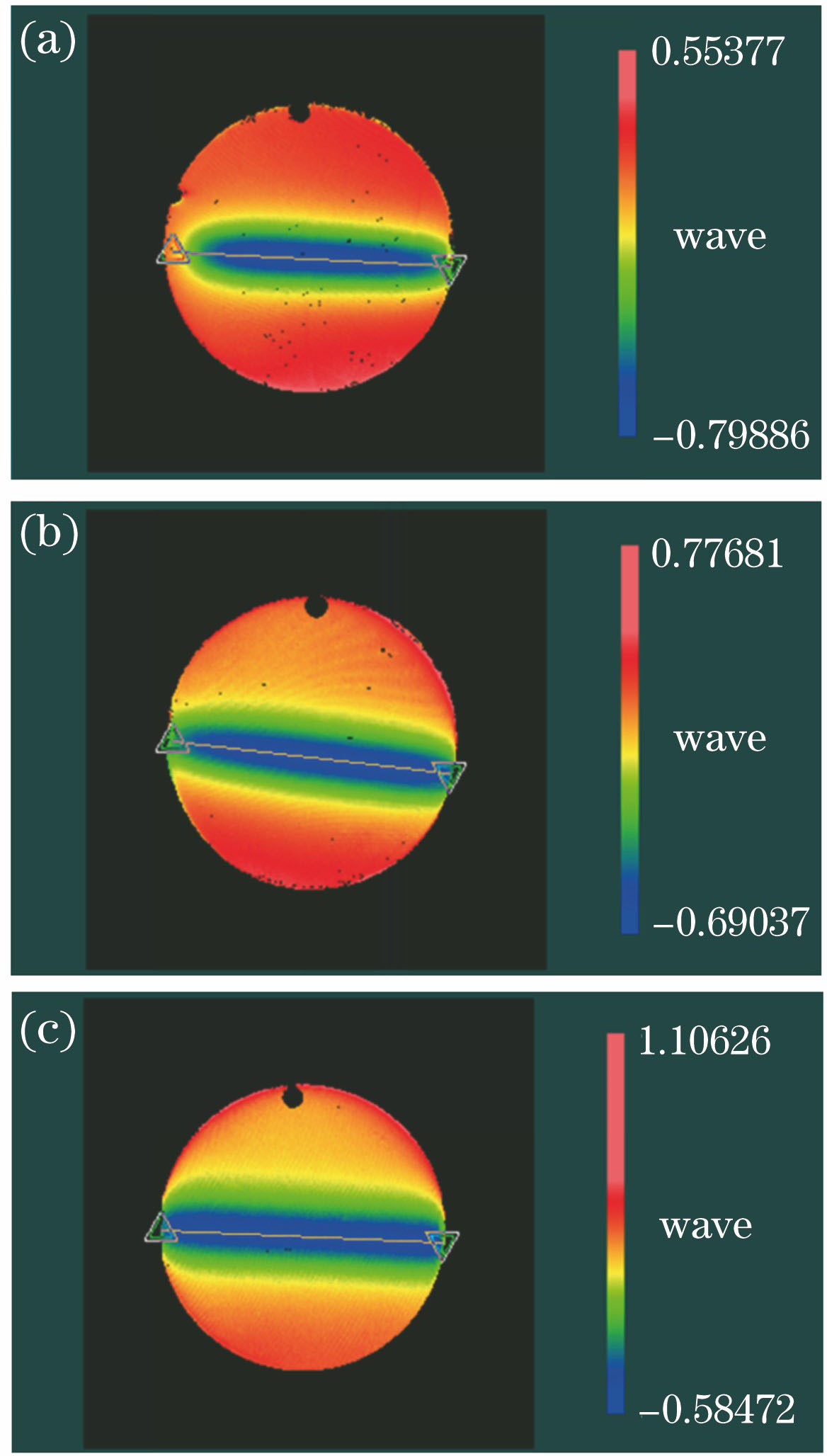
图 5. 不同叠加间距的离子束一维等量刻蚀结果。(a)叠加间距为σ;(b)叠加间距为1.2σ;(c)叠加间距为1.5σ
Fig. 5. One-dimensional equivalent-etching results of ion beams with different stacking spacings. (a) Stacking spacing is σ; (b) stacking spacing is 1.2σ; (c) stacking spacing is 1.5σ
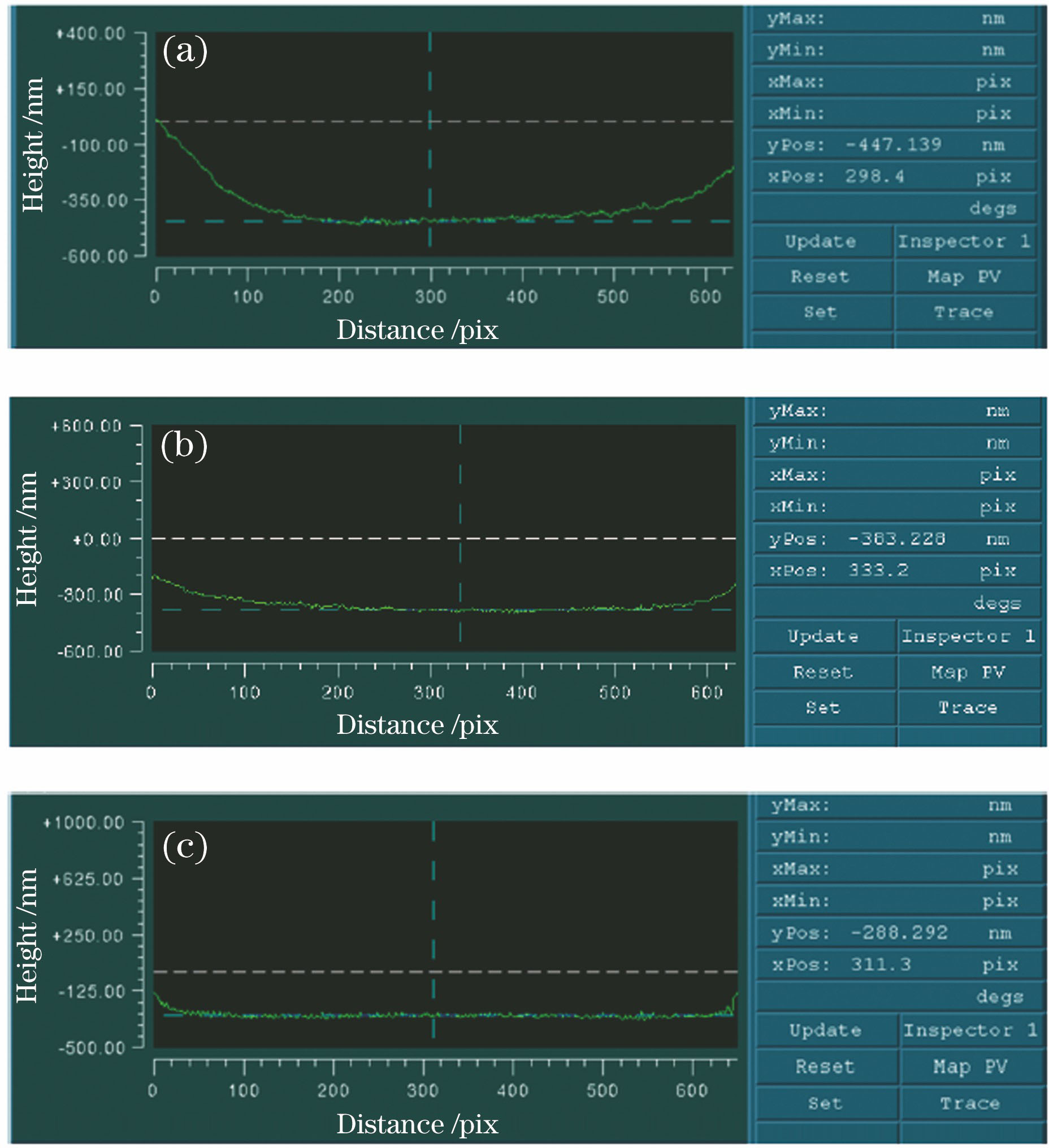
图 6. 不同叠加间距的离子束一维等量去除轮廓图。(a)叠加间距为σ;(b)叠加间距为1.2σ;(c)叠加间距为1.5σ
Fig. 6. One-dimensional equivalent removal contour of ion beams with different stacking spacings. (a) Stacking spacing is σ; (b) stacking spacing is 1.2σ; (c) stacking spacing is 1.5σ
根据
2.2 二维等量去除的实现
对一维高斯分布的叠加仿真及实验分析,说明了等量去除的可行性,并得出最佳叠加间距为σ。离子束修形过程是二维去除,对整个面形进行去除的过程中要分析两个方向上的叠加,因此不难得出另一个方向上的叠加间距仍为σ。离子束二维去除函数如(3)式所示,根据一维仿真分析对应的叠加间距进行二维去除分析。叠加后的去除函数为
式中:H(x,y)为离子束二维等量去除的理论去除量;n为x方向高斯叠加的数量;m为y方向高斯叠加的数量。
二维等量去除仿真叠加后的去除量呈方形平底锅状,如
对二维等量去除进行实验验证。在65 mm工作距离处对口径Φ50 mm、厚度为3 mm的熔石英样片进行刻蚀,实验中对样片进行13行、13列的刻蚀,单点驻留时间为30 s。
对刻蚀后的样片进行标记对准检测,并对样片的前后面形作差,作差后的面形即为刻蚀的绝对深度,在刻蚀范围内对面形误差峰谷(PV)值进行数据分析,PV值即为刻蚀深度。作差后的面形如
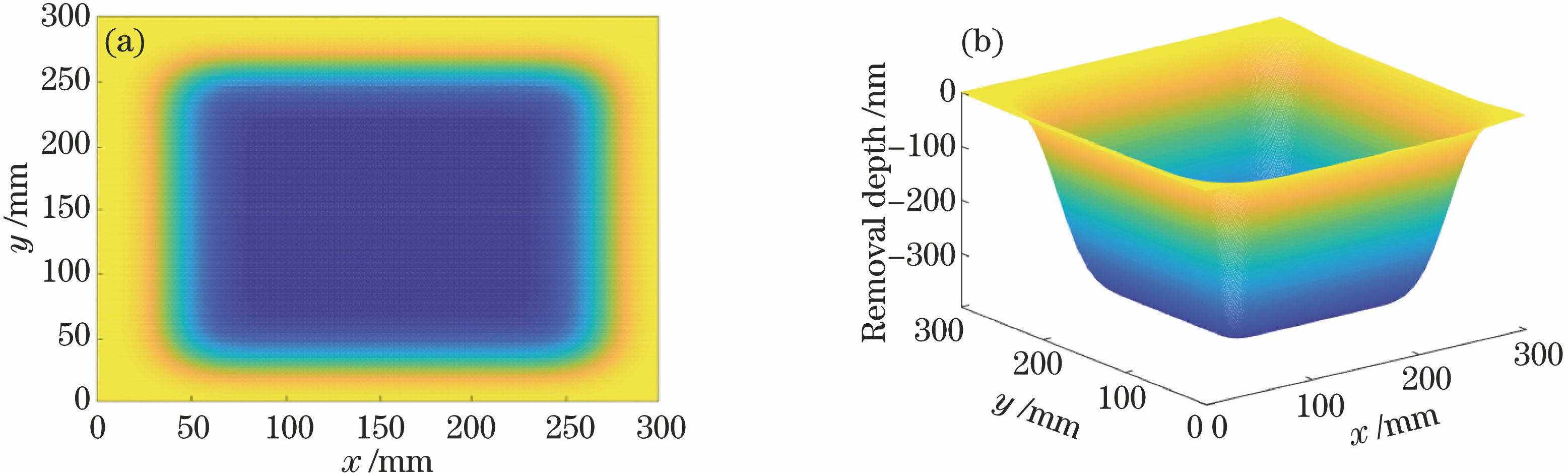
图 7. 二维等量去除仿真图。(a)俯视图;(b)侧视图
Fig. 7. Simulation of two-dimensional equivalent removal. (a) Top view; (b) side view
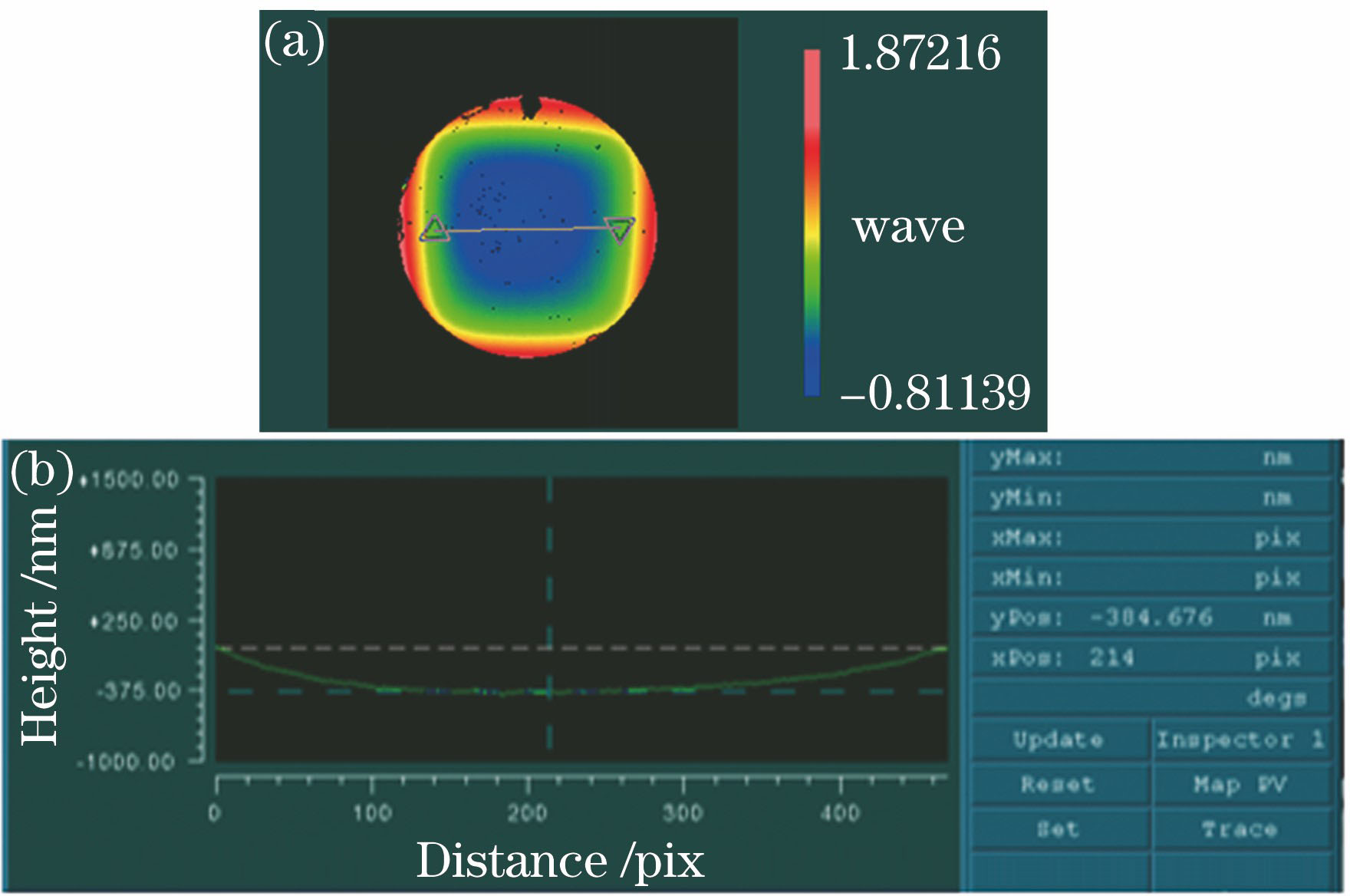
图 8. 二维等量去除结果。(a)刻蚀结果;(b)刻蚀轮廓
Fig. 8. Two-dimensional equivalent removal results. (a) Etching result; (b) etching profile
3 修形实验
修形实验的基本工艺参数如下:射频功率为200 W;屏栅电压为900 V;屏栅电流为13 mA;氩气流量为50 mL/min(标准状态);工作距离为65 mm;入射角度为0°;稳定工作压强为4.5×10-2 Pa。通过栅格路径对Φ100 mm的熔石英玻璃进行面形修正,如
将熔石英初始面形按照1.41σ的直径划分为多个元胞,根据二维等量去除速率求解各个元胞的驻留时间,如
经过4 h的抛光,离子束修形后全口径的面形如
加工的面形收敛率达到7.82。实验结果证明了采用叠加间距σ求解修形驻留时间的合理性。由于面形受夹具夹持的影响,在边缘局部也留下明显的残差。85%口径内的面形残差如
4 结论
针对离子束刻蚀熔石英材料获取熔石英材料的去除特性,精确拟合去除函数;从理论上分析了不同叠加间距下离子束的一维等量去除,并通过实验验证了不同叠加间距下的去除效果,得出最佳叠加间距,以最佳叠加间距进行二维等量去除的理论及实验分析,并进行抛光实验,根据理论分析及实验结果得出以下结论。对于一维等量去除,通过仿真分析可知,叠加间距越大,去除量总量越小,波动量越大,通过实验验证了不同叠加间距下等量去除的去除量与仿真结果一致,说明等量去除的可行性,并给出最佳的叠加间距为σ;对于波动量来说,因为实验中存在一定的对准误差,不能充分验证理论分析的波动量,实验需要进一步完善。基于一维等量去除得出的最佳叠加间距σ进行二维等量去除理论分析,并通过实验验证二维等量去除的去除率,实验结果与理论分析一致;基于二维等量去除的去除率求解待加工件的驻留时间,经过4 h抛光后,分析加工件修形前后的面形信息可得面形收敛率达到7.82。
[1] 周林, 戴一帆, 解旭辉, 等. 计算机控制抛光中基于等面积增长螺旋线的加工路径[J]. 国防科技大学学报, 2009, 31(4): 1-4.
Zhou L, Dai Y F, Xie X H, et al. A novel path used in computer-controlled polishing process based on uniform-area-increment spiral[J]. Journal of National University of Defense Technology, 2009, 31(4): 1-4.
[2] 李圣怡, 戴一帆, 解旭辉, 等. 大中型光学非球面镜制造与测量新技术[M]. 北京: 国防工业出版社, 2011: 92- 93.
Li SY, Dai YF, Xie XH, et al.New technology for manufacturing and measurement of large and middle-scale aspheric surfaces[M]. Beijing: National Defend Industry Press, 2011: 92- 93.
[3] 焦长君, 李圣怡, 王登峰, 等. 离子束加工光学镜面的材料去除特性[J]. 光学精密工程, 2007, 15(10): 1520-1526.
[4] 周林. 光学镜面离子束修形理论与工艺研究[D]. 长沙: 国防科学技术大学, 2008: 34- 35.
ZhouL. Study on theory and technology in ion beam figuring for optical surfaces[D]. Changsha: National University of Defense Technology, 2008: 34- 35.
[5] 焦长君. 光学镜面离子束加工材料去除机理与基本工艺研究[D]. 长沙: 国防科学技术大学, 2008: 20- 23.
Jiao CJ. Study on the material removal mechanisms and fundamental processes for ion beam figuring optical mirrors[D]. Changsha: National University of Defense Technology, 2008: 20- 23.
[6] 廖文林. 高精度球体类零件离子束确定性修形技术研究[D]. 长沙: 国防科学技术大学, 2010: 26- 28.
Liao WL. Deterministic ion beam figuring technology for high-precision spherical components[D]. Changsha: National University of Defense Technology, 2010: 26- 28.
[7] Allen L N. Progress in ion figuring large optics[J]. Proceedings of SPIE, 1994, 2428: 237-247.
[8] Michel F, Schindler A, Thomas H. Ion beam figuring of SiC mirrors provides ultimate WFE performances for any type of telescope[J]. Proceedings of SPIE, 1999, 3739: 142-154.
[9] SchindlerA, HaenselT, ZeunerM, et al. Ion beam figuring and ion beam polishing production tools-processing technology included-for customized solutions[C]∥Optical Fabrication and Testing, June 18, 2000, Québec City, Canada. Washington, D.C.: OSA, 2000: OWA6.
[10] 戴一帆, 周林, 解旭辉, 等. 应用离子束进行光学镜面确定性修形的实现[J]. 光学学报, 2008, 28(6): 1131-1135.
[11] 唐瓦, 邓伟杰, 郑立功, 等. 离子束抛光去除函数计算与抛光实验[J]. 光学精密工程, 2015, 23(1): 31-39.
[12] 武建芬. 离子束加工技术研究[D]. 长春: 中国科学院大学, 2010: 40- 42.
Wu JF. Research on the ion beam figuring technology[D]. Changchun: University of Chinese Academy of Sciences, 2010: 40- 42.
[13] 唐瓦. 离子束抛光大口径非球面去除模型与工艺研究[D]. 长春: 中国科学院大学, 2016: 31- 39.
TangW. Research on removal model and technology for ion beam figuring large aspherical mirror[D]. Changchun: University of Chinese Academy of Sciences, 2016: 31- 39.
[14] 段沽坪. 离子束抛光去除特性研究[D]. 北京: 中国科学院大学, 2013: 32- 33.
Duan GP. Study on removal characteristics of ion beam polishing[D]. Beijing: University of Chinese Academy of Sciences, 2013: 32- 33.
[15] 王中昱, 张连新, 孙鹏飞, 等. 射流抛光中生成高斯型去除函数的数学建模方法[J]. 光学学报, 2018, 38(10): 1022002.
[16] 李建, 张连新, 孙鹏飞, 等. 射流抛光高斯型去除函数的快速生成方法[J]. 光学学报, 2018, 38(7): 0722002.
[17] 席建普, 李彬, 任东旭, 等. 大口径非球面元件磨削轮廓测量技术研究进展[J]. 激光与光电子学进展, 2018, 55(3): 030008.
Article Outline
王玉宁, 蒋世磊, 孙国斌, 刘卫国, 党小刚. 离子束抛光等量去除的实现及抛光实验[J]. 激光与光电子学进展, 2020, 57(3): 032501. Yuning Wang, Shilei Jiang, Guobin Sun, Weiguo Liu, Xiaogang Dang. Ion Beam Polishing Equivalent Removal and Polishing Experiments[J]. Laser & Optoelectronics Progress, 2020, 57(3): 032501.