1 厦门大学 萨本栋微米纳米科学技术研究院,福建厦门36005
2 福建省能源材料科学与技术创新实验室(IKKEM),福建厦门361005
3 厦门大学 航空航天学院,福建厦门61102
4 厦门大学 物理科学与技术学院,福建厦门361005
5 厦门大学 九江研究院,江西九江332000
在MLA曝光工艺中,曝光点的数量庞大,通过高倍率显微镜配合人工目检来判定曝光质量耗时耗力,造成工艺成本偏高。为了解决这个问题,设计了一种便于检测的圆环形图案并引入深度学习中的目标检测Yolov5模型,一定程度上能够取代人工目检,完成对曝光质量的快速判定。基于上述方法,分析了不同光刻胶厚度之下,线能量密度的最优区间与光刻胶的剖面倾角。并在同等线能量密度下通过圆度判定曝光图案失真情况。在本研究的MLA曝光工艺中,选取光刻胶厚度、激光曝光功率以及加工平台移动速度作为自变量,评价曝光合格率、光刻胶剖面倾角以及曝光圆度等加工质量参数具有重要的工程意义。
无掩膜光刻 微透镜阵列 曝光合格率 目标检测 maskless lithogrophy microlens array qualification rate object detection
1 厦门理工学院机械与汽车工程学院,福建 厦门 361024
2 福建省绿色智能清洗技术与装备重点实验室,福建 厦门 361024
3 厦门大学航空航天学院,福建 厦门 361005
线激光扫描技术多用于零件的表面检测,也可用于物体的三维重建。许多浮雕工艺品由于没有数字模型而无法复现,可利用线激光扫描将浮雕逆向生成三维模型,便于浮雕工艺品的加工。通过结合机器人与线激光,获取浮雕的点云数据,逆向建立浮雕的三维数字模型。搭建三维重建系统,根据实际模型的尺寸计算出机器人的扫描路径,机器人结合线激光扫描得到浮雕点云数据;进行点云数据的预处理,再根据基准平面,补偿带有机器人误差的点云数据;利用基于衍生的迭代最近点(GICP)算法进行点云的自动拼接,并对点云进行后处理;随后利用Delaunay三角剖分算法与曲面重建算法进行三维模型的重建。以老鹰浮雕为重建对象进行实验,实验结果表明用路径扫描拼接的点云处理更为方便,补偿数据后,精度可提高40.48%,有显著补偿效果,浮雕模型重建后与基准模型的标准差平均为0.0576 mm,可满足浮雕模型的重建需求。
线激光扫描 机器人控制 误差补偿 三维重建 浮雕 激光与光电子学进展
2023, 60(22): 2211007
气囊抛光可用于加工具有纳米级表面粗糙度和亚微米级形状精度的非球面光学元件,在光学元件加工领域应用广泛。传统气囊工具磨损检测方法成本高、耗时长、效率低,针对该问题,提出一种基于拼接数据采集平台的改进迭代最近点(ICP)拼接算法的气囊磨损检测方法。该方法通过点云拼接实现大尺寸气囊工具的磨损检测,并结合气囊磨损检测算法计算磨损量。采用体素下采样和半径滤波对拼接数据进行点云预处理,利用搭建的拼接检测数据采集平台获取良好的初始配准变换矩阵,最后利用双向K-D树近邻搜索结合ICP算法实现点云精配准。实验结果表明,所提拼接算法在保证配准精度的同时可大幅提高配准效率,并且不影响后续气囊磨损检测的精度,为大尺寸气囊工具磨损检测提供了保证。
气囊抛光 气囊磨损检测 数据采集 点云配准 激光与光电子学进展
2023, 60(16): 1612001
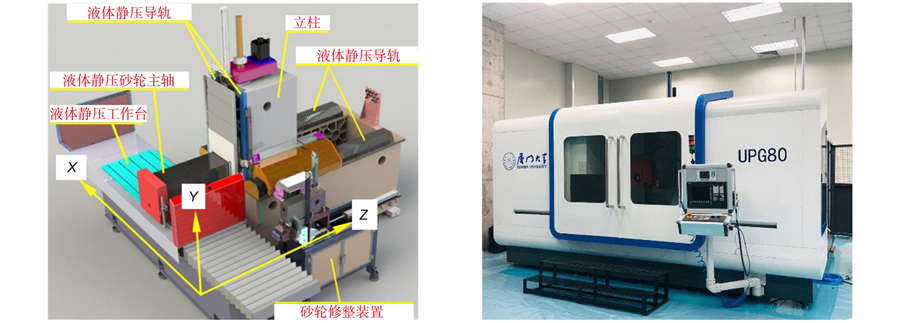
1 厦门大学航空航天学院,福建 厦门 361005
2 厦门大学深圳研究院,广东 深圳 518057
Overview: Driven by the rapid development of national optical projects such as laser nuclear fusion and aerospace telescopes, as well as high-end civilian fields such as advanced instruments and optical lenses, the requirements for full-frequency domain processing errors and surfaces of optical components are becoming more and more stringent. At this stage, the optical components generally need to go through rough grinding, fine grinding, polishing and coating, and other processes, and their surface quality mainly depends on the defect removal ability and error control level of the polishing process. Whether the fine grinding process can obtain better surface shape accuracy and low surface/subsurface damage suppression determines the processing efficiency, and the ultra-precision processing manufacturing equipment is the premise of the realization of ultra-precision machining of the optical components. So far, all countries in the world have invested in the research and development of optical ultra-precision grinding and polishing technology, and have developed more relatively mature high-precision grinding and polishing equipment, which can better meet the processing needs of most of the current optical components. For the core equipment and key technologies required for ultra-precision manufacturing, China has long relied on imports. In order to break through the bottleneck restricting the development of ultra-precision technology in China at this stage, under the traction and drive of the national large-scale engineering project, China has made remarkable progress in optical ultra-precision manufacturing equipment and technology. However, for the optical ultra-precision technology and equipment, there is still a certain gap between China and the international advanced level, and it is necessary to continue to strengthen the research. In addition to the high-end grinding and polishing equipment necessary for the ultra-precision machining of optical components, it is also necessary to strengthen the technical level of a series of key supporting units, such as ultra-precision grinding and polishing processing technology, high-end key functional components, intelligent monitoring technology of processing environment, efficient ultra-precision machining tools, processing and inspection path planning and compensation processing strategies, computer-aided manufacturing and testing software, etc. The research, development, and application of these technologies are related to the development of high-end manufacturing in the civilian fields and national defense fields, and are also the focus of the country. This paper mainly focuses on the ultra-precision machining of large-diameter optical aspherical components. Starting from the grinding and polishing process route, this paper introduces the long-term research progress of the Precision Engineering Laboratory of Xiamen University in the field of large-diameter optical aspherical component processing, and introduces in detail the technical and system achievements such as ultra-precision grinding and polishing equipment, robot-assisted grinding and polishing, equipment intelligent monitoring system, processing technology and control software.
超精密加工 磨抛装备 加工工艺 CAM软件 ultra-precision machining grinding and polishing equipment processing technology CAM software
强激光与粒子束
2022, 34(11): 119001
强激光与粒子束
2021, 33(5): 051002
针对磨削阶段大口径光学非球面元件拼接测量精度不高的问题,提出一种基于两段拼接的优化算法.首先根据多体系统运动学理论、斜率差值及逆推法建立两段面形轮廓的拼接数学模型;其次针对拼接算法中工件运动量和运动误差对拼接精度的影响,仿真分析了350 mm非球面工件的两段拼接.仿真结果表明,随着平移误差增大,拼接误差明显增大,而当控制旋转角度在8°以内、平移量在10 mm以内、旋转误差在60′以下及平移误差在3 μm以下时,拼接误差的标准偏差值在0.2 μm波动;最后利用Taylor Hobson轮廓仪和高精度辅助测量夹具对120 mm口径的非球面光学元件进行测量实验并研究工件运动量对拼接测量精度的影响.实验结果表明,当控制平移量在10 mm以内和旋转角度在8°以下时,拼接误差的标准偏差值在0.2~0.6 μm之间,能满足磨削阶段光学元件亚μm级精度的面形检测要求.
轮廓测量 两段面形拼接 工件运动量 工件运动误差 profile measuring stitching of two segments workpiece motion motion error 强激光与粒子束
2015, 27(6): 064101
1 厦门大学 物理与机电工程学院, 福建 厦门 361005
2 中国工程物理研究院 激光聚变研究中心, 四川 绵阳 621900
为保证气囊抛光过程中抛光运动的高稳定性和均匀材料去除率,对气囊抛光非球面过程中气囊工具刚度的可控性进行了研究。通过分析气囊抛光大口径光学元件时工具的受力情况,计算了气囊工具的刚度,并分析了气囊抛光工具刚度对抛光时材料去除的影响及气囊工具刚度的影响因素。设计了气囊工具刚度控制算法并进行模拟试验,仿真结果表明,在刚度标准值根据加工要求设定以后,即可通过调节工件对气囊工具的反作用力,使得气囊抛光大口径光学元件过程中气囊工具刚度可控。
大口径光学元件 气囊抛光 工具刚度 可控性 large aspheric lenses bonnet polishing stiffness controllability
1 厦门大学 物理与机电工程学院, 福建 厦门 361005
2 中国工程物理研究院 激光聚变研究所, 四川 绵阳 621900
研究了砂轮圆弧半径误差对大口径矩形轴对称非球面加工的影响。采用直线光栅式平行磨削的加工方式,建立了砂轮圆弧半径的误差分离的数学模型,分析影响面形精度的因素,根据加工及测量方式将砂轮圆弧半径误差分离出来,利用分离的砂轮圆弧半径误差更新砂轮圆弧半径,同时采用分离后的误差数据进行补偿加工。实验结果表明:对比不分离的补偿加工结果,粗磨和精磨条件下的分离误差补偿加工后的面形误差分别减小了14%和35%,该误差模型能够有效地分离出砂轮圆弧半径误差,分离误差效果明显,提高了加工的精度。
矩形轴对称非球面 砂轮圆弧半径 误差分离 补偿加工 rectangular axisymmetric aspheric surface wheel-arc radius error separation compensation grinding
1 厦门大学 物理与机电工程学院, 福建 厦门 361005
2 浙江工业大学 教育科学与技术学院, 杭州 310014
结合砂轮表面仿真及磨削过程的运动学仿真获得工件表面轮廓、形貌和粗糙度预计,可以作为磨削过程中的理论依据,是精密磨削加工技术中主要的研究内容之一。平行磨削技术是加工非轴对称非球面光学元件的重要手段,而相关的仿真过程报道还很少。提出一种基于平行磨削的精密磨削加工非球面表面生成的仿真方法,该方法主要包含使用高斯方法生成具有不同统计学特征的随机砂轮表面形貌,建立单磨粒运动轨迹方程和圆弧砂轮细分后与工件表面点接触的运动关系,据此给出平行磨削加工表面生成的数值算法,并对不同加工参数下的工件表面形貌进行仿真。仿真结果和测量结果的一致性验证了所给算法的正确性和有效性。
非轴对称非球面 平行磨削 圆弧砂轮 表面形貌 随机表面 nonaxisymmetric aspheric lens parallel grinding arc grinding wheel surface topography random surface