1 北京工业大学北京市精密测控技术与仪器工程技术研究中心,北京 100124
2 河南科技大学河南省机械设计及传动系统重点实验室,河南 洛阳 471003
相对于接触式测量,机器视觉检测这种非接触式测量具有效率高、信息全、稳定性好、可识别缺陷等优点,在齿轮检测领域得到越来越广泛的应用。近十年来出现了影像仪、闪测仪、CVGM仪器、在线检测设备等多种基于机器视觉技术的齿轮检测仪器,它们既可以实现齿轮综合式测量,又可以实现齿轮分析式测量。回顾了齿轮视觉检测仪器的发展历程和特点,分析了齿轮视觉检测中边缘检测、亚像素定位、特征提取和模式识别等算法的研究和应用进展,总结了机器视觉在齿轮精度测量和齿轮缺陷检测两个方面的技术发展,并指明了齿轮视觉检测仪器与技术的发展前景。
机器视觉 齿轮测量 齿轮视觉检测仪器 齿轮精度测量 齿轮缺陷检测 激光与光电子学进展
2022, 59(14): 1415006
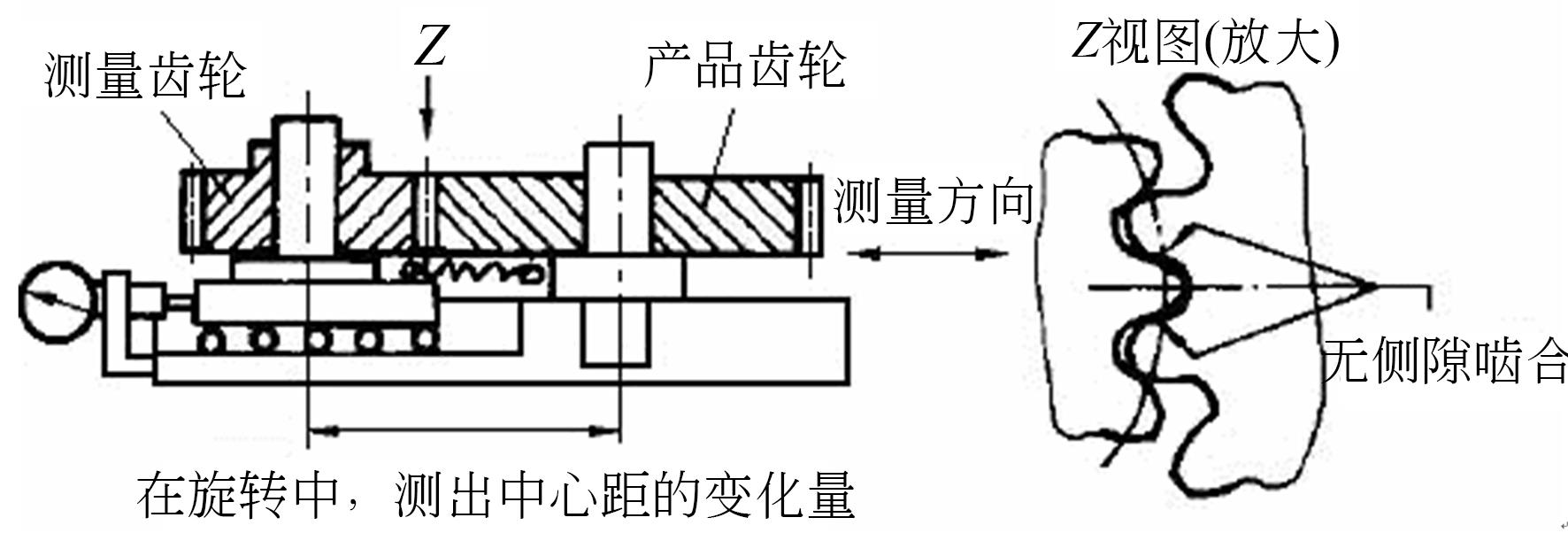
北京工业大学 材料与制造学部 北京市精密测控技术与仪器工程技术研究中心,北京100124
To address the data processing problem of double-flank gear rolling tests in a cloud platform, in this study, the evaluation of radial composite deviations, deployment of cloud data processing systems, and design of cloud data processing software are investigated. The cloud platform for a cloud data processing system of a double-flank gear rolling test adopts the architecture of “Linux+Tomcat+MySQL+Java” and employs Java Web technology. Herein, the method of deploying a web application in a cloud platform is presented, the cloud data processing system of the double-flank gear rolling test is designed, and the data interaction between the client and cloud, and that between the instrument and cloud are realized. The key aspects of the software design include the network IP address, front-end access interface of the data processing software for the double-flank gear rolling test, database, and evaluation of radial composite deviations. Furthermore, the cloud processing system interface is presented, and evaluation experiments of radial composite deviations are conducted. Radial composite deviations can be obtained through the evaluation of the measurement data from the instrument end. For the sample of the measured product gear, the radial composite deviation was 32.7 and tooth-to-tooth radial composite deviation was 9.5 μm, with a grade 8 accuracy in accordance with the standard GB/T 38192-2019. Therefore, this study is expected to serve as a reference for the development of cloud data processing technology for precision instruments.
齿轮测量 双面啮合测量 云平台 云处理 Javaweb Gear metrology double flank gear rolling test cloud platform cloud data processing Javaweb
1 北方民族大学 电气信息工程学院,宁夏 银川 750021
2 北京工业大学 机械工程与应用电子技术学院, 北京 100124
研究了齿轮误差三维评定方法, 以消除测量仪器定位误差对齿轮误差评定的影响, 提高齿轮测量仪器的测量精度。分析了传统齿轮二维评定方法的弊端, 提出将齿轮误差评定从二维评定模式转变为三维评定模式。该评定模式不再要求齿轮各项误差测量点位于特征面内, 实现了三维空间内的齿轮误差测量与评定。为提高齿轮三维误差评定算法的效率, 通过螺旋降维方法将三维数据降至二维数据, 再对二维测量数据进行各项误差的评定。以特大型齿轮激光跟踪在位测量系统作为实验对象, 对4级标准齿轮的齿廓误差进行了测量, 并与传统的齿轮二维误差评定方法以及德国ZEISS公司InvolutePro软件的评定结果进行了对比。结果表明: 传统齿轮二维误差评定方法有较大误差, 三维齿廓评定方法与德国ZEISS公司InvolutePro软件评定结果一致, 精度达到0.1 μm, 证明了提出的齿廓误差三维评定方法完全正确, 可以消除仪器定位误差对测量结果的影响, 提高了测量仪器的测量精度。
齿轮测量 定位误差 三维评定 螺旋降维法 gear measurement positioning error three-dimensional evaluation spiral dimensionality reduction method
1 中国计量科学研究院, 北京 100029
2 北京工业大学 机械工程与应用电子技术学院, 北京 100124
为了通过测量齿面拓扑轮廓来获取特征线误差, 提出了一种基于正交距离回归齿面的误差计算方法。 对该方法涉及的实际齿面与理论齿面匹配算法、拓扑轮廓误差的计算与分解及齿面特征线误差的评定算法进行了研究。首先, 通过坐标测量方法获取的齿面拓扑数据, 建立包含回归齿面参数的非线性方程。然后, 求解非线性方程得到回归齿面参数的最优近似解, 从而得到与实际齿面匹配的理论齿面, 拓扑测量点相对理论齿面的正交距离即为齿面拓扑误差。最后, 基于齿轮误差多自由度理论, 对实际齿面进行局部自由度及全局自由度回归, 进一步分解出齿面的齿廓误差和螺旋线误差。以一标准圆柱直齿轮的齿面拓扑测量点数据为例进行了误差计算, 结果显示: 计算的结果与直接进行特征线测量的结果差值小于0.5 μm, 表明提出的基于正交距离回归齿面进行齿轮误差评定的方法是有效的, 可以应用于坐标类仪器检测齿轮误差。
齿轮测量 正交距离回归 齿轮误差评定 坐标测量法 gear metrology orthogonal distance regression evaluation of gear error coordinate measurement method 光学 精密工程
2015, 23(11): 3192
1 哈尔滨工业大学 精密仪器研究所, 黑龙江 哈尔滨 151400
2 东北石油大学 电子科学学院, 黑龙江 大庆 163318
为评定齿轮测量中心测量不确定度,提出了一种基于拟蒙特卡罗法(quasi Monte-Carlo method,QMC)的齿轮测量不确定度评定方法。研究了齿轮测量中心的几何误差源,应用坐标变换法建立了齿轮测量中心精密测量模型,采用拟蒙特卡罗仿真法对齿轮测量中心测量不确定度进行了评定,并分析了评定的稳定性。评定实验表明,该方法可准确评定齿轮测量中心测量不确定度,评定结果最大偏差为2.35%,评定方法稳定。
齿轮测量中心 拟蒙特卡罗法 测量不确定度 gear measuring center quasi Monte-Carlo method(QMC) measurement uncertainty
北京工业大学 机械工程与应用电子技术学院, 北京 100124
提出了面向特大型齿轮的激光跟踪多站位定位测量方法以提高特大型齿轮激光跟踪在位测量系统的齿轮定位精度并精确确定测量仪器与被测齿轮位置与姿态的关系。根据激光跟踪仪多站位测量提供的冗余数据优化求解空间两点间共线方程, 建立了特大型齿轮激光跟踪多站位测量模型。然后, 提出了利用奇异值分解修正多站位测量模型解析矩阵条件数的方法。实验结果表明, 使用多站位测量模型求得的不同站位待测点间距离的标准差的均值为0.008 mm, 明显小于直接在不同站位下测量的标准差均值0.024 mm, 表明多站位测量模型具有良好精度控制效果。本文的研究提高了齿轮定位时所需测量点的三维测量精度, 为特大型齿轮激光跟踪多站位测量系统建立齿轮坐标模型提供了可靠的数据来源。
齿轮测量 激光跟踪多站位测量 奇异值分解 特大型齿轮 gear measurement laser tracker multi-station measurement singular value decomposition mega-gear
1 北京工业大学 机械与应用电子技术学院, 北京 100124
2 哈尔滨量具刃具集团有限责任公司, 黑龙江 哈尔滨 150040
为了实现特大型齿轮精密测量, 介绍了作者提出的特大型齿轮激光跟踪在位测量原理, 重点阐述了其中的几项关键技术。特大型齿轮激光跟踪在位测量系统整合了激光跟踪仪的大尺寸测量能力和三坐标测量机的高精度, 采用激光跟踪仪建立齿轮工件坐标系和三维测量平台坐标系, 通过激光跟踪仪坐标系将齿轮工件坐标系与三维测量平台坐标系关联起来, 并建立了相应坐标系的拟合模型及算法。同时, 建立了三维测量平台的姿态调整模型, 通过姿态调整机构完成了三维测量平台的姿态调整, 进而确保三维测量平台与齿轮轴线的位置关系满足要求。最后, 给出了该在位测量系统的实测结果。实验结果表明: 特大型齿轮激光跟踪在位测量系统原理正确可行, 满足6级以下特大型齿轮的精密测量。
特大齿轮 齿轮测量 激光跟踪仪 在位测量 姿态调整 mega gear gear measurement laser tracker in-site measurement attitude adjustment
1 北京工业大学 机械工程与应用电子技术学院, 北京 100124
2 Physikalisch-Technische Bundesanstalt Braunschweig und Berlin, 38116 Braunschweig, Germany
针对目前便携式坐标测量机测量大齿轮的采样策略和评定算法存在的不足, 设计了两种特殊的辅助标尺-渐开线标尺及螺旋线标尺。利用设计的两种标尺在大齿轮齿面上对齿廓及螺旋线的测量点进行标注, 开展了齿轮的在位重复性测量的实验研究。利用关节臂坐标测量机及激光跟踪仪测量系统在德国计量研究院研制的1 m外径齿轮样板上开展了测量实验, 采用INVOLUTE Pro对采样数据点进行评定, 给出了测量结果及测量不确定度。测量实验表明, 基于新的齿轮测量方法, 关节臂坐标测量机比激光跟踪仪测量系统测量结果更为精确, 测试结果与标定值最大相差8.16 μm。实验结果验证了提出方法的有效性, 为便携式坐标测量机在大齿轮测量领域的应用提供了依据。
大齿轮测量 便携式坐标测量机 大齿轮样板 large gear measurement portable coordinate measuring machine large gear standard
北京工业大学 机械工程与应用电子技术学院, 北京 100124
为确保齿轮测量仪器的高精度校准, 国际标准ISO/TR 10064-5:2005推荐了新型的双球渐开线样板。该样板采用高精度球体的部分圆弧代替渐开线, 通过误差补偿, 获得高精度渐开线以实现渐开线溯源。研究了该样板相关的理论问题, 为双球样板设计与应用提供了理论基础。针对数控齿轮测量仪器常釆用的电子展成法, 分析并给出了理想安装条件下和存在安装误差时双球渐开线样板的原理误差及其计算公式; 根据最优圆弧思想, 使用最小二乘法推导出双球中心距的优化公式; 最后给出了原理误差的补偿方法。基于上述基本理论, 开发了双球样板设计软件并研制了一块模数为2.268 1 mm、齿数为40、压力角为20°的双球渐开线样板。
齿轮 齿轮仪器 齿轮测量 齿轮样板 双球渐开线样板 gear gear instrument gear measurement gear artifact Double-ball Artifact(DBA) 光学 精密工程
2011, 19(12): 2963