激光热源下射流强化肋与槽道散热特性对比
1 引言
随着半导体加工技术的进步,电子器件不断向高集成度方向发展。半导体激光器由于输出能量大、峰值功率高(局部可达1000 W/cm2)、器件尺寸小等优点,广泛应用于医疗和**领域,包括激光治疗仪、激光雷达、激光通信等[1-4]。然而,其电光转换效率最高仅达50%,其余输入的能量均转换为热量[5],且产生的热量分布极不均匀,呈现高斯分布的趋势,长期处于这种条件下,热电器件表面的热应力分布不均[6],当超过材料的抗拉强度或屈服强度时,材料就会被破坏,且随着泵浦功率的增大,热效应的影响更为突出,严重损害其寿命[7]。Patil等[8]基于有限元分析改变高斯热源的分布,查看金属粉末层中的温度场分布,并研究了加工表面温度分布随热源功率、高斯扫描半径等相关参数的变化。Peng等[9]分别利用2D建模与3D建模方法数值分析了二极管端面泵浦激光器的热效应,讨论并比较了两种二极管特性,包括温度分布和热透镜效应。龚宇等[10]研究了气体热效应对封闭空间自然对流光束质量的影响,并对其进行了改善。因此,如何根据温度场均匀性改善散热方式是延长高热流密度热电器件寿命的重要技术,也是突破半导体激光器光电转换效率与输出稳定性的关键。
对于均匀热流受热表面,目前已有的高效换热方式分别是微槽道换热和射流冲击换热。在受热表面或散热器表面加工微细槽道,通过增大比表面积达到强化散热的目的。赵瑞等[11]用带有斜翅片结构的热沉来封装半导体激光器,在低功耗下可满足多激光器连续工作条件下的基本散热需求。Hasan等[12]通过数值模拟的方法研究了常见微槽道的几何结构对换热特性的影响,并指出在相同通道体积时,圆形微槽道流动压降最小且换热效果最佳。王浩然等[13]利用有限元方法进行数值模拟,对微通道结构进行了优化,得到了应用于片状激光放大器热阻最小的热沉结构。由于流动阻力与通道的直径的4次方成反比,因此,微通道冷却系统的流动损失往往比较大,功耗高,且热面温度均匀性较差。
为此,研究者提出了射流冲击强化表面的散热方案。Lytle等[14]研究了当喷嘴和热面之间的距离小于喷嘴直径时的散热能力。当喷嘴-板间距小于1/4喷嘴直径时,湍流强度和速度显著增加,努塞特数出现两个峰值。李超等[15]研究了射流角、入口直径、射流间距等参数对换热特性的影响,发现被冲击表面上的对流边界层变薄时,换热系数变大。Singh等[16]通过实验和数值计算比较了3种强化表面(立方体、圆柱形、圆筒)在不同喷嘴间距下的传热能力,发现圆筒结构在翅片效率和传热效果方面表现良好。理论上,与光滑表面相比,压力损失没有显著增加,但散热能力明显提升。在均匀热流表面强化传热中,研究者往往关注喷嘴与热面距离、射流雷诺数和喷嘴几何形状等因素的影响。在实际应用中,各类表面强化方法均可增强热传递[17]。
针对激光热源特有的分布特点,为降低受热面最高温度,提升热面温度均匀性,本文提出一种射流冲击强化表面的综合散热方法。采用数值模拟方法,研究高斯分布热源条件下热面最高温度、温度均匀性、流动损失和热应力应变等特性,并与传统微槽道结果进行比较。
2 物理模型
根据本研究内容建立几何模型,
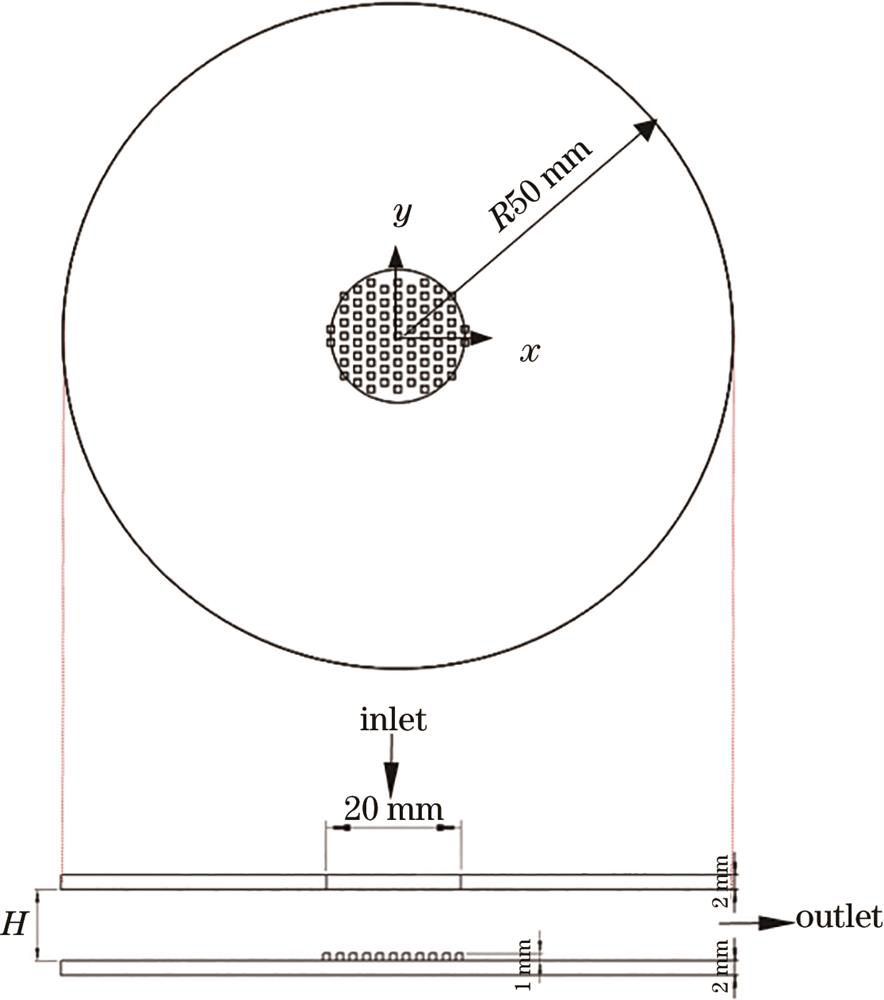
图 2. 射流冲击强化表面系统示意
Fig. 2. Schematic diagram of jet impingement strengthening surface system
研究中,固体材料为铬锆铜(CuCrZr),流体工质为去离子水。模型圆板底面受到高密度热流扫描。扫描半径为50 mm,热流呈高斯分布,以此模拟激光热源,平均热流密度为0.637 MW/m2,中心最大热流密度为1.7 MW/m2,该热源的加载程序利用UDF编写后自定义导入Fluent。
3 数值计算方法及验证
3.1 控制方程
为了简化分析,假设流动满足稳态不可压缩,整个过程满足质量、动量和能量守恒定律。建立如下流动控制方程:
式中:
3.2 网格独立性验证
为节省计算成本,同时保证计算精度,采用Fluent meshing划分网格,测试冲击射流系统网格独立性。在中心射流区设置加密区,同时在流体与固体交界面设置边界层加密。以H=0.5D、入口流速为1 m/s系统为例进行网格独立性验证,调整局部网格大小,划分为165万、201万、263万、302万等4套计算网格,具体网格尺寸如
表 1. 网格尺寸
Table 1. The size of grid
|
不同网格热源面x方向温度分布如
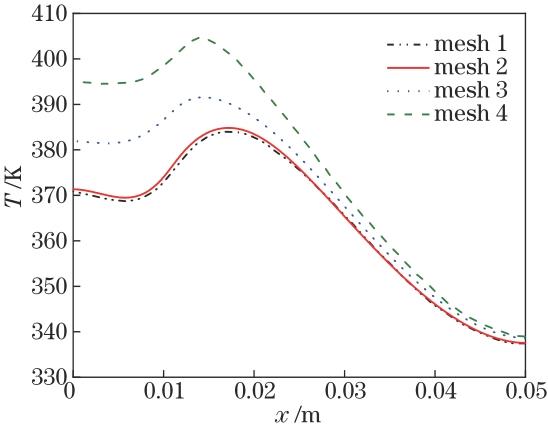
图 3. 不同网格热源面x方向温度分布
Fig. 3. Temperature distribution in x direction of heating surface with different grids
3.3 模型正确性验证
Zu等[18]对圆形射流垂直撞击平板实验进行数值模拟,并与现有的基准实验数据进行了比较,发现在7种湍流模型中,剪切应力输运(SST k-
Zuckerman等[19]经过多套网格计算发现V2F和SST模型可以更好地预测射流的扩展、滞止区的湍流效应、壁面的湍流特性以及冲击射流中的流体性质,推荐其为求解速度和精度之间的最佳选择。
为了保证模拟结果的准确性,选取SST k-ω模型对相似类型的圆孔撞击圆板进行了数值模拟,并将沿圆板平均努塞特数分布与实验结果[20]进行比较,具体如
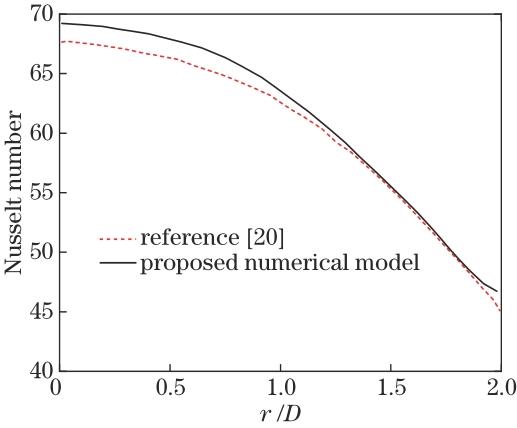
图 4. 努塞特数径向分布的数值与实验比较
Fig. 4. Comparison of Nusselt number radial distribution between simulation and experiment
4 数值结果分析
4.1 微槽道和射流冲击散热特性比较
首先对比高斯热源下微槽道与H=0.5D时的冲击射流热面温度特性。研究中,入口流速均为1 m/s,冷却工质初始温度为293.15 K,其物性参数均拟合为随温度变化的分段函数。底面加载的热流密度
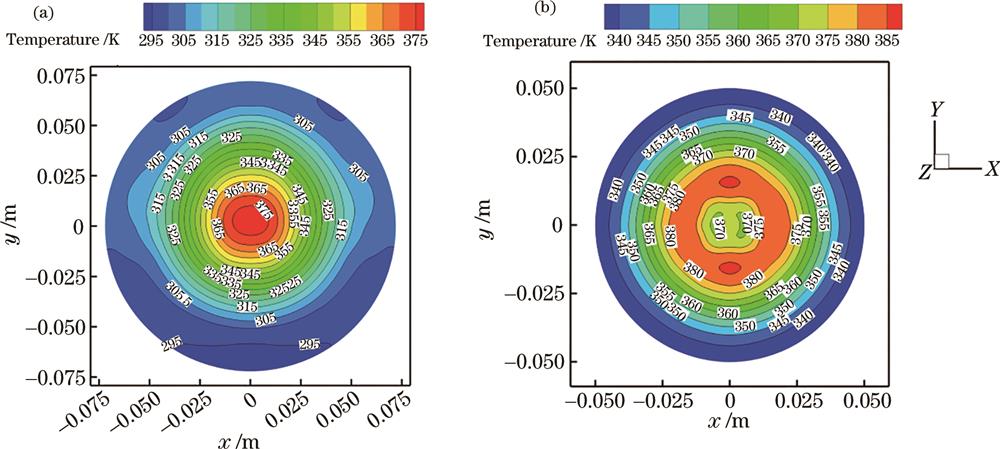
图 5. 热面温度云图。(a)微槽道;(b)强化表面冲击射流(H/D=0.5)
Fig. 5. Cloud chart of hot surface temperature. (a) Microchannel; (b) jet impingenent with the strengthened surface (H/D=0.5)
从
4.2 不同冷却系统综合评价
保持射流直径不变,逐渐减小两圆板间距,分别设置为0.25D、0.15D、0.1D。流场速度分布如
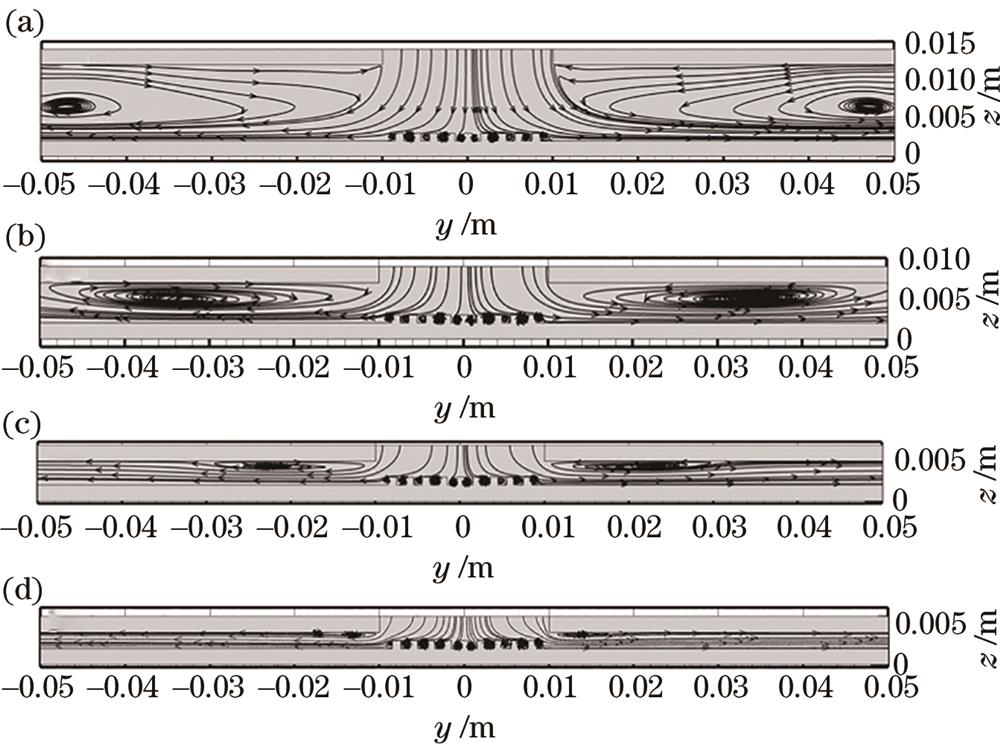
图 6. 射流冲击距离H/D对流场的影响(x=0截面)。(a)H/D=0.5;(b)H/D=0.25;(c)H/D=0.15;(d)H/D=0.1
Fig. 6. Impact of jet impingement distance H/D on flow field (cross section x=0). (a) H/D=0.5; (b) H/D=0.25; (c) H/D=0.15; (d) H/D=0.1
与微槽道相比,冲击射流具有较低的压降,同时温度均匀性提高。随着H的减小,冲击射流的压降增大。以流量系数
对比微槽道和不同冲击距离下的射流系统,得到的压降特性和温度均匀性数据如
表 2. 不同冷却系统水力特性和热力学特性比较
Table 2. Comparison of hydraulic and thermodynamic characteristics of different cooling systems
|
从
H/D为0.1的冲击射流系统热力特性最差,故提取其热源加载面温度分布,具体如
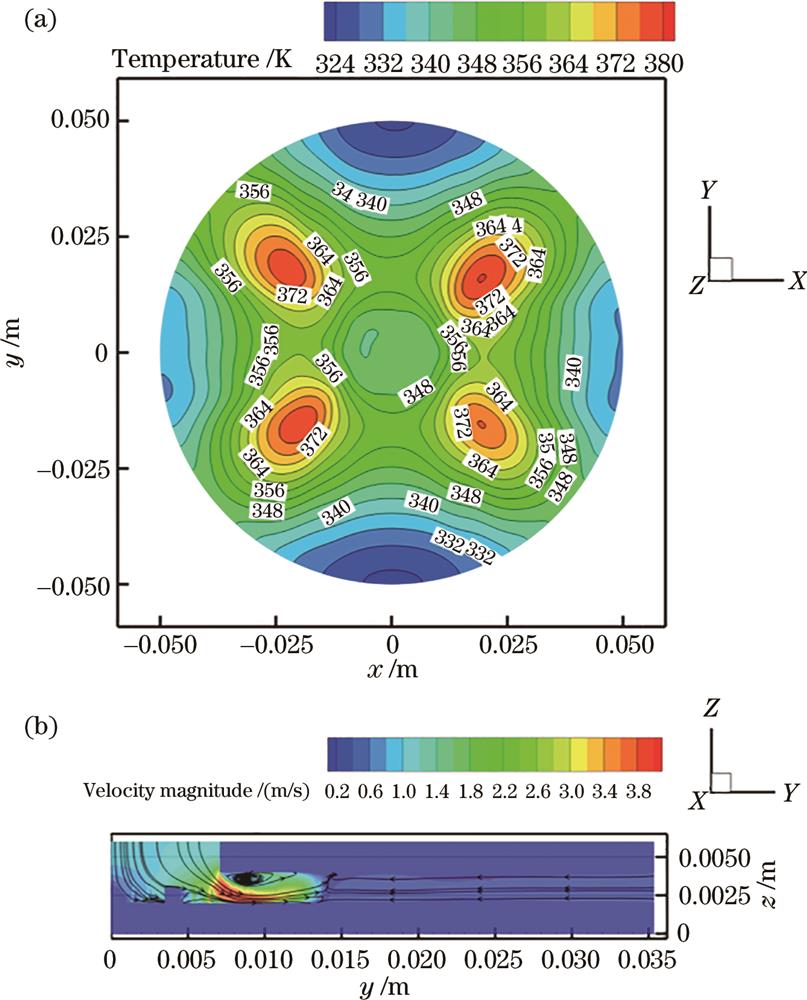
图 7. H/D为0.1的射流撞击强化表面温度云图与流场图。(a)受热面温度云图;(b)y=x截面流场图
Fig. 7. Temperature and flow field diagram of impinging jet with strengthened surface (H/D=0.1); (a) Temperature cloud mapof heating surface; (b) flow field diagram of y=x section
4.3 热应力对比
热应力是指受热面由于温差使材料发生不同程度的形变,变形程度不匹配时材料内部产生的应力。当热应力超过介质材料承受极限时,材料会被破坏,引起热电器件失效,严重损害其寿命。将计算所得的温度场导入热应力应变分析软件中,精细化处理局部网格,施加约束,求解热应力、应变等参数。通道材料为CrZrCu,密度为8880 kg/m3,线性膨胀系数为16.7×106 K-1,杨氏模量为125 GPa,屈服强度220 MPa。
由于H=0.25D的冲击射流系统综合性能最好,因此重点比较该系统与微槽道冷却系统热应力特性。取高斯热源扫描面,提取y=0至y=50 mm线上的应力分布与温度分布,如
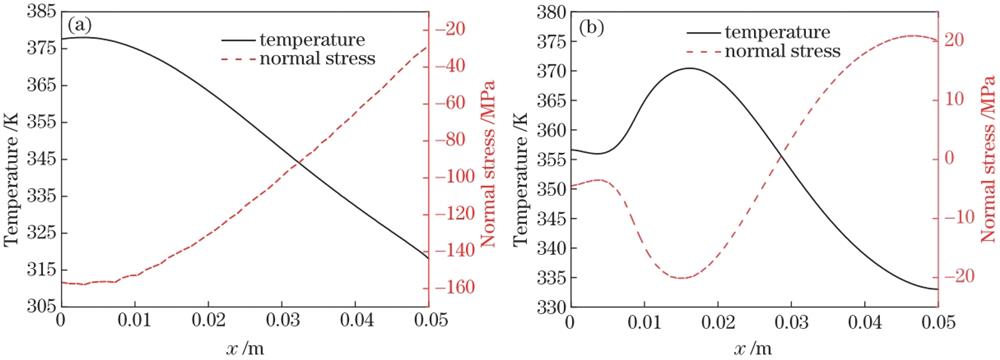
图 8. 受热面温度与热应力分布。(a)微槽道;(b)强化表面冲击射流(H/D=0.25)
Fig. 8. Temperature and thermal stress distribution of heating surface. (a) Microchannel; (b) impinging jet with strengthened surface (H/D=0.25)
同时提取了热源加载面z方向形变绘制三维曲面图,如
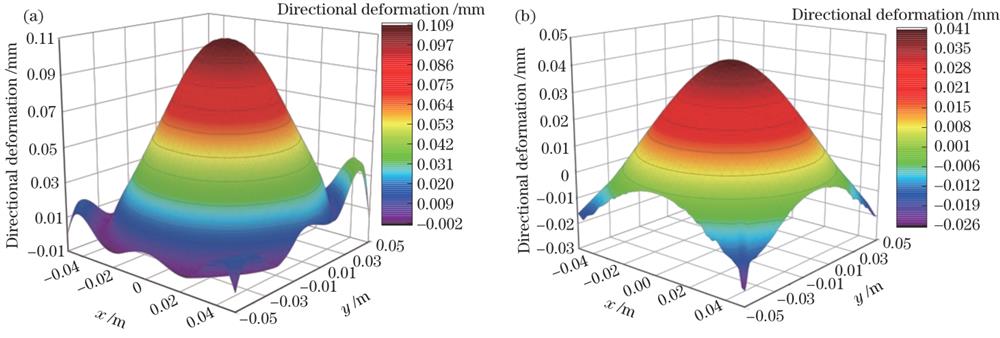
图 9. 受热面形变。(a)微槽道;(b)强化表面冲击射流(H/D=0.25)
Fig. 9. Strain of of heating surface. (a) Microchannel; (b) impinging jet with strengthened surface (H/D=0.25)
因此在同种材料的屈服极限下,射流系统(H/D=0.25)所能承受的激光热流密度明显高于微槽道冷却系统,适用性更强。这表明所提散热方案具有更好的温度和形变控制性能。
5 结论
提出射流冲击强化表面的热控方案,通过数值模拟方法对比分析了高斯分布热源条件下与微槽道散热系统的水力特性和热力特性。仿真结果表明,射流冲击距离H/D=0.5时,热面温度均匀性是微槽道系统的1.56倍,温差降低了40%,但最高温度仍然大于传统微槽道冷却系统。继续降低H使冲击区边界层减薄,横向流速提高,最大温度降低并实现了温度均匀性,以此改善换热效果。提出综合评价指标PEC来衡量冷却系统的适用性,经过对比发现H=0.25D时PEC最大,因此该系统适用于激光半导体的散热。最后,经过热应力与应变分析,发现同种材料的屈服极限下,射流系统(H/D=0.25)所能承受的激光热流密度明显高于微槽道冷却系统,适用性更强。
[1] 陈天琦. 大功率半导体激光器阵列的热应力/应变特性研究[D]. 西安:中国科学院西安光机研究所, 2018: 16-20.
ChenT Q. Research on thermal stress/strain characteristics of high-power semiconductor laser arrays[D]. Xi’an: Xi’an Institute of Optics and Fine Mechanics, Chinese Academy of Sciences, 2018: 16-20.
[2] Bonnefois A M, Gilbert M, Thro P Y, et al. Thermal lensing and spherical aberration in high-power transversally pumped laser rods[J]. Optics Communications, 2006, 259(1): 223-235.
[3] 杨静航. 半导体微腔激光器阵列散热分析及其工艺制备[D]. 长春: 长春理工大学, 2020:21-26. 10.3934/era.2020062
YangJ H. Heat dissipation analysis and technology preparation of semiconductor micro-cavity laser array[D]. Changchun: Changchun University of Science and Technology, 2020: 21-26.
[4] Hügel H. New solid-state lasers and their application potentials[J]. Optics and Lasers in Engineering, 2000, 34(4/5/6): 213-229.
[5] 陶蒙蒙, 叶锡生, 叶景峰, 等. 同带泵浦千瓦级掺铥光纤激光器输出特性理论模拟[J]. 中国激光, 2022, 49(1): 0101019.
[6] 曹健东, 程小劲, 范米, 等. 端面泵浦薄片激光器热效应补偿方法的研究[J]. 光电子·激光, 2019, 30(2): 111-116.
Cao J D, Cheng X J, Fan M, et al. Study on thermal effect compensation method of end-pumped thin-plate laser[J]. Journal of Optoelectronics·Laser, 2019, 30(2): 111-116.
[7] 高光波, 郑四木. 热电制冷在激光器冷却系统中的应用[J]. 航空精密制造技术, 2012, 48(2): 46-49.
Gao G B, Zheng S M. Application of semiconductor refrigeration to laser cooling system[J]. Aviation Precision Manufacturing Technology, 2012, 48(2): 46-49.
[8] Patil R B, Yadava V. Finite element analysis of temperature distribution in single metallic powder layer during metal laser sintering[J]. International Journal of Machine Tools and Manufacture, 2007, 47(7/8): 1069-1080.
[9] Peng X Y, Xu L, Asundi A K. Thermal lensing effects for diode-end-pumped Nd: YVO4 and Nd: YAG lasers[J]. Optical Engineering, 2004, 43(10): 2454-2461.
[10] 龚宇, 吴娟, 杨钧兰, 等. 封闭空间内热耦合效应对激光合束传输的影响[J]. 中国激光, 2023, 50(13): 1305002.
[11] 赵瑞, 石琳琳, 王越, 等. 多单管激光器微通道内部翅片结构设计及优化[J]. 激光与光电子学进展, 2023, 60(21): 2114005.
[12] Hasan M I, Rageb A A, Yaghoubi M, et al. Influence of channel geometry on the performance of a counter flow microchannel heat exchanger[J]. International Journal of Thermal Sciences, 2009, 48(8): 1607-1618.
[13] 王浩然, 王建磊, 李培丽, 等. 基于微通道热沉的片状激光放大器散热模拟及优化[J]. 中国激光, 2023, 50(7): 0701002.
[14] Lytle D, Webb B W. Air jet impingement heat transfer at low nozzle-plate spacings[J]. International Journal of Heat and Mass Transfer, 1994, 37(12): 1687-1697.
[15] 李超, 贺占蜀, 李大磊. 纯水射流流场分布及冲击换热数值模拟研究[J]. 机械设计与制造, 2020(8): 103-107.
Li C, He Z S, Li D L. Numerical simulation of water jet flow field distribution and impingement heat transfer[J]. Machinery Design & Manufacture, 2020(8): 103-107.
[16] Singh P, Zhang M Y, Ahmed S, et al. Effect of micro-roughness shapes on jet impingement heat transfer and fin-effectiveness[J]. International Journal of Heat and Mass Transfer, 2019, 132: 80-95.
[17] Sriromreun P, Sriromreun P. A numerical and experimental investigation of dimple effects on heat transfer enhancement with impinging jets[J]. Energies, 2019, 12(5): 813.
[18] Zu Y Q, Yan Y Y, Maltson J. Numerical study on stagnation point heat transfer by jet impingement in a confined narrow gap[J]. Journal of Heat Transfer, 2009, 131(9): 347-359.
[19] Zuckerman N, Lior N. Impingement heat transfer: correlations and numerical modeling[J]. Journal of Heat Transfer, 2005, 127(5): 544-552.
[20] Choo K S, Kim S J. Comparison of thermal characteristics of confined and unconfined impinging jets[J]. International Journal of Heat and Mass Transfer, 2010, 53(15/16): 3366-3371.
Article Outline
张文静, 刘明侯. 激光热源下射流强化肋与槽道散热特性对比[J]. 激光与光电子学进展, 2024, 61(5): 0514001. Wenjing Zhang, Minghou Liu. Heat Dissipation and Thermal Stress-Strain Characteristics of an Impinging Jet Strengthened Rib Surface under a Laser Heat Source[J]. Laser & Optoelectronics Progress, 2024, 61(5): 0514001.