ZC1蜗杆齿廓测量测头对准误差修正
1 引 言
蜗杆是动力传动系统中的重要零件之一,准确测量蜗杆的各项误差是提高蜗杆精度和保证传动质量的重要前提。圆弧圆柱蜗杆(ZC)包括圆环面包络圆柱蜗杆(ZC1)、圆环面圆柱蜗杆(ZC2)和轴向圆弧齿圆柱蜗杆(ZC3)[1]。
蜗杆的齿廓偏差值反映了实际齿廓偏离设计齿廓的程度,主要测量仪器有齿轮测量中心和三坐标测量机。ZC蜗杆的轴向齿廓为凹形曲线,齿廓测量过程中,测头与蜗杆实际齿廓接触时易发生干涉,且测量过程受测头尺寸和测头位置等因素的影响,因此常采用齿轮测量中心。
齿轮测量中心齿轮测量中,凌明分析了测头半径对齿轮渐开线样板齿廓偏差测量的影响,当存在齿根展开角误差时,测头半径引入的测量误差会随测头半径的增大而增大,随展开长度的减小而增大[2-3]。Yin等建立了齿廓偏差测量模型,分析了X轴和Y轴坐标系建立误差对齿廓偏差的影响,得出该误差对齿廓形状偏差的影响可以忽略不计,而对齿廓总偏差和齿廓倾斜偏差的影响较大[4]。Ling等考虑探针位置误差对渐开线齿廓测量的影响,提出了渐开线测量仪测头位置调整方法,并用不同直径测头对齿形样板进行了实验验证[5]。Lin等提出了一种测头中心对准方法,用倾斜的平面镜作为标准参考[6]。
齿轮测量中心蜗杆测量中,朱志强等用插值法求解出与实际接触点较为接近的ZC蜗杆齿廓的理论接触点,减小了X轴对不准引入的原理误差[7]。祝强等为避免线性蜗杆齿廓测量发生干涉,分析了齿廓测量各阶段测球、测杆与蜗杆齿面之间的位置关系,提出了基于蜗杆和测针参数的干涉预判方法[8]。籍庆校等基于ZK蜗杆齿廓方程建立了齿廓测量误差模型,分析了测头偏离蜗杆轴截面对齿廓偏差测量结果的影响规律[9]。由此可见,测头对准误差会影响蜗杆齿廓偏差的测量结果。本文提出了齿轮测量中心ZC蜗杆测量中测头对准误差的修正方法,分析蜗杆齿廓测量原理,在ZC蜗杆轴截面齿廓方程基础上建立测头对准误差修正模型,分析测头对准误差的影响因素并开展测量实验。
2 测量原理
齿轮测量中心蜗杆齿廓测量原理如图1所示。根据被测蜗杆参数建立蜗杆齿面数学模型,以蜗杆轴线作为Z轴建立工件坐标系,测量ZC蜗杆齿廓偏差时要求测头位于蜗杆轴截面内[10]。令X=0,求得轴截面YOZ平面齿廓的理论测量点。根据理论测量点坐标控制测头进行测量,测头沿Y轴和Z轴方向由齿根运动到齿顶。测量过程中,Y轴方向的位移传感器等间距发出采样信号,对测头传感器和Z轴位移传感器进行采样,得到测头球心实际测量点的坐标数值。由实际测量点的坐标数值与理论测量点在Z轴方向的差异得到轴截面齿廓偏差,再依据GB/T 10089—2018[11]得到被测蜗杆的齿廓偏差评定结果。
3 测头对准误差修正
齿轮测量中心蜗杆齿廓测量中,对准误差是指测头运动到X轴理论零位时,偏离蜗杆轴截面YOZ平面的位移x0(见图1)。对准误差是由仪器校准时采用的校准件不同导致的,如使用渐开线样板和标准块确定的X轴零位存在差异;此外,随着仪器的老化,测头也会逐渐偏离X轴零位。在存在对准误差的情况下测头仍按原有的运动轨迹测量轴截面齿廓,得到的是偏离蜗杆轴截面的一条齿廓线,会影响蜗杆齿廓偏差的测量结果。
这里通过分析蜗杆齿面方程,建立了受测头对准误差影响的蜗杆轴向齿廓测量误差模型,将齿廓测量点投影到蜗杆轴截面,确定偏离轴截面x0处截面上齿廓线相对于轴截面齿廓线的轴向偏差,修正得到轴截面上齿廓测量点的轴向坐标。
3.1 ZC1蜗杆齿面方程
砂轮磨削ZC蜗杆时,建立图2所示的坐标系。其中,Ot-XtYtZt是与砂轮固连的动坐标系,且Zt轴与砂轮轴线重合,Ot位于砂轮轴截面中部。O-XYZ是与蜗杆固连的动坐标系,Z轴与蜗杆轴线重合。为便于说明蜗杆和砂轮之间的数学关系,建立固定坐标系Ow-XwYwZw,Zw轴和Z轴重合。
用环面盘形砂轮磨削ZC1蜗杆的螺旋面时,砂轮以较高的速度旋转,其切削刃在旋转中形成一个回转表面;蜗杆则做螺旋运动。根据砂轮与蜗杆之间的相对运动关系,得到蜗杆齿面方程[12]:
其中:a为两轴线之间的最短距离;R为砂轮产型线上任意点到Zt轴的距离;f(R)为砂轮产型线上任意点在Zt方向上的坐标值;η为蜗杆相对固定坐标系Ow-XwYwZw绕Z轴转过的角度;γ为Zt轴和Z轴的夹角,即蜗杆导程角;φ为过砂轮产型线上任意点到Zt轴的垂线与XtOtZt平面的夹角;p为螺旋参数。
3.2 蜗杆轴向齿廓测量误差模型
将受测头对准误差影响的x=x0截面齿廓线投影到x=0的轴截面上,记为
根据蜗杆齿面方程,分别建立蜗杆轴截面齿廓模型和偏离轴截面x0处截面上的齿廓模型,在此基础上建立ZC1蜗杆测头的对准误差模型。砂轮回转面相对蜗杆做螺旋运动即可生成蜗杆齿面模型。为方便后续齿廓模型的推导,令砂轮回转面方程为:
求解蜗杆轴截面齿廓时,令x=0即可。此时:
代入式(3)求得ZC1蜗杆轴截面齿廓上点的z坐标:
当测头有偏置量x0时,有:
两边同时除以,整理得:
其中:,继续化简得:
将式(9)代入式(3)中z坐标的表达式,即可得到x=x0截面上齿廓点的z0坐标:
根据式(10)与式(5),测头偏离轴截面x0处截面上的齿廓模型与蜗杆轴截面的齿廓模型相比,得到ZC1蜗杆测头对准误差引入的轴向齿廓测量误差模型:
式中:p为螺旋参数;x0为测头偏置量;x1,y1为砂轮回转面参数,见式(2)。
3.3 轴向齿廓修正值
受测头对准误差影响的蜗杆轴向齿廓测量误差Δ包含两部分,即Δ=fz+ez,如图3所示。其中fz为齿廓形状测量误差,即fz=
由此得出齿廓形状测量误差为:
式中:xa,ya是齿廓在齿顶位置时的x1,y1,见式(2)。
由式(13)可知,在蜗杆参数确定的情况下,fz是测头偏置量x0的函数。以蜗杆参数:m=4 mm,z=3,d=60.5 mm为例,测头偏置量为±60 μm,±30 μm时的齿廓形状测量误差曲线如图4所示。由图可知:测头偏置量大小相等符号相反的情况下,齿廓形状测量误差曲线在fz=0的两侧对称分布;fz随测头偏置量x0的增大而增大;在蜗杆齿根部位,fz值最大,由齿根到齿顶,fz值逐渐减小。
由于测头对准误差的存在,测量得到的齿廓偏差中包含齿廓形状测量误差,直接进行齿廓偏差评定会对测量结果产生较大影响。因此,需要对齿廓测量值进行修正,减小测头对准误差造成的影响,记受测头对准误差影响的轴向齿廓修正值为C,即有:
根据图4中的齿廓形状测量误差曲线确定每个测量点对应的修正值。将受测头对准误差影响的齿廓测量点的z值与测头对准误差轴向齿廓修正值相加,得到蜗杆轴截面上的齿廓测量点坐标,再与理论齿廓对比,得到修正后的齿廓偏差,进而减小测头对准误差对齿廓偏差评定结果的影响。
测头对准误差会对ZC1蜗杆齿廓测量产生影响。根据微小误差原理,确定测量仪器或设备精度的通行原则:仪器或设备总误差与被测参数的公差之比在1/3~1/10内。在已知蜗杆参数的条件下,由被测蜗杆的精度等级确定测头偏置量的允许值。例如,z=3,m=4 mm,d=60.5 mm的ZC1蜗杆5级精度的齿廓总偏差Fα1=12 μm,当选取测头对准误差与被测参数的公差之比为1/3时,要求测头对准误差fz≤2 μm。由图4可知,在上述条件下,测头偏置量在±60 μm之内,齿轮测量中心可测量5级精度的ZC1蜗杆。选取测头对准误差与被测参数的公差之比为1/6时,则测头偏置量在±30 μm之内,齿轮测量中心可测量5级精度的ZC1蜗杆。
4 蜗杆参数对齿廓的影响
ZC1蜗杆参数不同的条件下,测头对准误差x0对齿廓形状测量误差fz的影响不同。由式(13)和式(2)可知,除x0以外的参数均由蜗杆的基本参数(头数z、模数m和分度圆直径d)确定。其中,p=mz/2;γ=atan(mz/d);a,R由分度圆直径和模数确定;φ由头数、模数、分度圆直径确定。
在蜗杆的齿根处,齿廓形状测量误差fz最大,分析ZC1蜗杆在不同头数、模数和分度圆直径下,测头对准误差对齿廓形状测量误差的影响规律。
4.1 蜗杆头数的影响
蜗杆参数设置为:模数m=4 mm,分度圆直径d=60.5 mm。在蜗杆模数和分度圆直径不变的条件下,将头数分别设置为1,2,3,得到齿廓形状测量误差与测头对准误差之间的关系,如图5所示。测头对准误差x0=50 μm的条件下,z=1时,fz=1.0 μm;z=2时,fz=2.0 μm;z=3时,fz=3.0 μm。随着蜗杆头数的增加,齿廓形状测量误差呈均匀增大的趋势。
4.2 蜗杆模数的影响
蜗杆参数设置为:头数z=3,分度圆直径d=60.5 mm。在蜗杆头数和分度圆直径不变的条件下,将模数分别设置为4,8,10 mm,得到齿廓形状测量误差与测头对准误差之间的关系,如图6所示。测头对准误差x0=50 μm的条件下,m=4 mm时,fz=3.0 μm;m=8 mm时,fz=7.1 μm;m=10 mm时,fz=9.6 μm。随着蜗杆模数的增大,齿廓形状测量误差不断增大,并且变化越来越显著。
4.3 蜗杆分度圆直径的影响
蜗杆参数设置为:头数z=3,模数m=4 mm。在蜗杆头数和模数不变的条件下,将分度圆直径分别设置为40.0,60.5,80.0 mm,得到齿廓形状测量误差与测头对准误差之间的关系,如图7所示。测头对准误差x0=50 μm的条件下,d=40.0 mm时,fz=7.6 μm;d=60.5 mm时,fz=3.0 μm;d=80.0 mm时,fz=1.7 μm。随着蜗杆分度圆直径的增大,齿廓形状测量误差呈现减小的趋势。当分度圆直径较小时,齿廓形状测量误差的变化更加明显。
由上述分析可知,蜗杆分度圆直径对齿廓形状测量误差的影响最显著。
5 实 验
蜗杆轴截面齿廓测量实验在JE42齿轮测量中心上进行,如图8所示。该仪器示值误差为1 μm、坐标分辨力为0.1 μm。ZC1蜗杆的相关参数如下:蜗杆轴向模数为4 mm,头数为3,压力角为20°,导程角为11°13′08″。双面圆弧砂轮参数如下:砂轮半径为380 mm,砂轮曲率半径为30 mm。
齿轮测量中心复位后对测头进行标定,标定后的状态作为测头对准误差较小的初始状态,该状态不考虑测头对准误差对齿廓偏差测量结果的影响。对蜗杆下齿面第一个齿重复进行5次测量,对实测数据进行最小二乘拟合,得到平均齿廓线,依据GB/T 10089—2018进行齿廓偏差评定,评定结果如表1所示。
表 1. 初始状态齿廓偏差评定结果
Table 1. Evaluation results of tooth profile deviations
|
将测头在X轴方向的零位偏置设置为x0=60 μm,引入测头对准误差。对蜗杆下齿面第一个齿廓重复进行5次测量,得到齿廓测量值以及对准误差修正前的齿廓偏差结果,见表2。其中,第5次测量的齿廓偏差曲线如图9所示,该次测量评定得到齿廓总偏差为3.6 μm,齿廓形状偏差为2.7 μm,齿廓倾斜偏差为1.8 μm。
表 2. 测头对准误差修正前齿廓偏差评定结果
Table 2. Tooth profile deviations before error correction
|
测头对准误差会影响齿廓偏差的评定结果。将齿廓测量数据的Y轴坐标代入式(3)得到x1,y1,与测头偏置量x0起代入式(13)得到齿廓形状测量误差,根据fz确定每个点对应的测头对准误差轴向齿廓修正值C。根据修正后的齿廓偏差值,得到测头对准误差修正后的齿廓偏差评定结果,如表3所示。
表 3. 测头对准误差修正后齿廓偏差评定结果
Table 3. Tooth profile deviations after error correction
|
测头校准误差修正后,5次重复测量的齿廓偏差评定结果见表3。其中,第5次测量评定得到齿廓总偏差为2.6 μm,齿廓形状偏差为2.7 μm,齿廓倾斜偏差为-0.2 μm。第5次测量的测头对准误差修正前后的齿廓偏差曲线如图10所示,在蜗杆的齿根部位,两条曲线差异较大,由齿根到齿顶,两条曲线的差异逐渐减小。
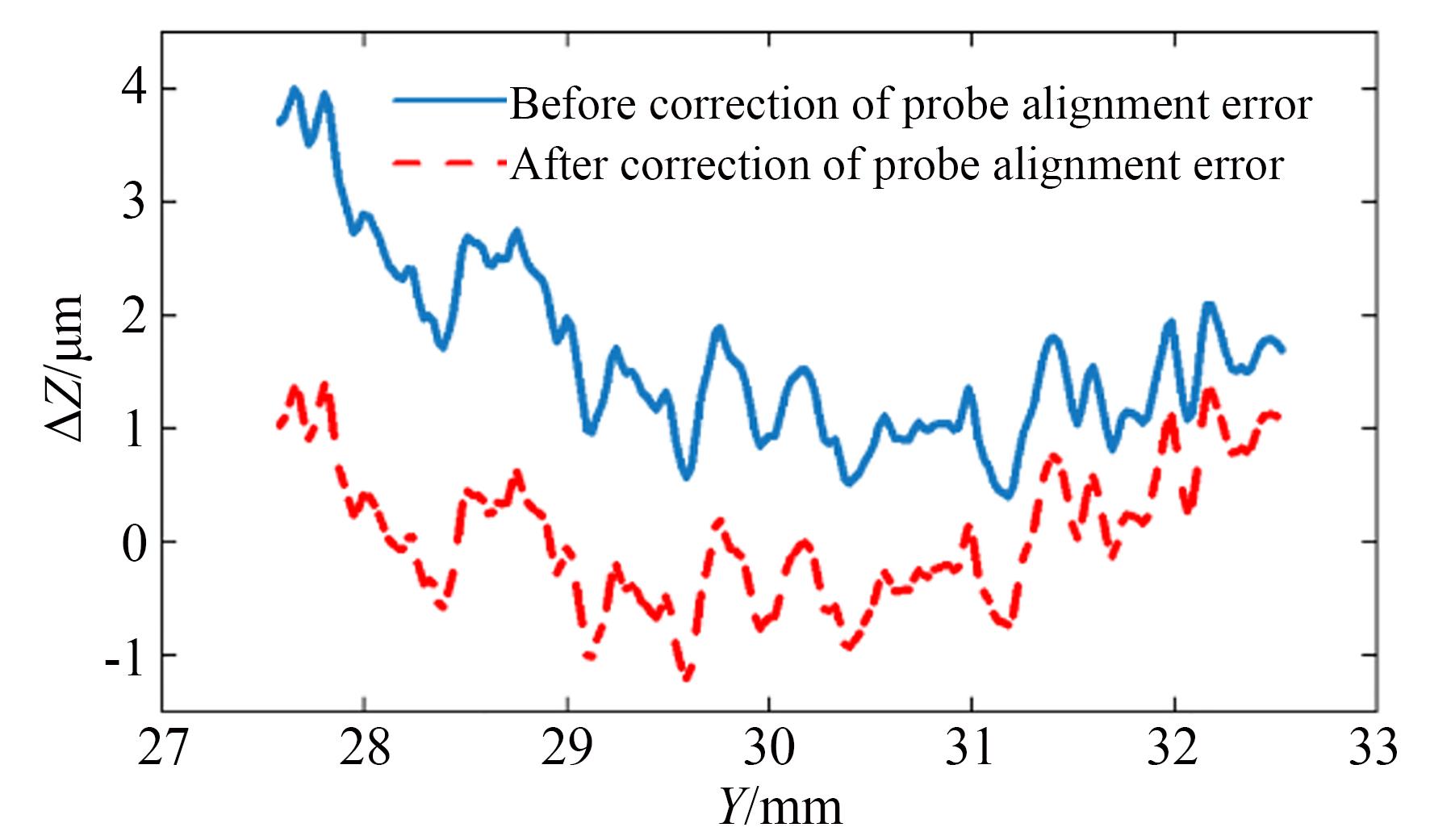
图 10. 修正前后的齿廓偏差曲线
Fig. 10. Comparison of tooth profile deviation curves before and after correction
根据表1~表3中的平均测量结果,测头对准误差修正前后的齿廓偏差评定结果对比数值列在表4中,齿廓偏差结果对比散点如图11所示。其中,δ1表示测头对准误差修正前与初始状态之间的测量结果差异;δ2表示测头对准误差修正后与初始状态之间的测量结果差异。测头对准误差修正前后,齿廓总偏差的差异值由1.2 μm降为0.2 μm,齿廓形状偏差的差异值由0.5 μm降为0.3 μm,齿廓倾斜偏差的差异值由2.5 μm降为0.4 μm。其中,测头对准误差引入的测量位置变化,对齿廓形状偏差的影响相对较小。
表 4. 齿廓偏差修正结果
Table 4. Correction result of tooth profile deviations
|
6 结 论
为了修正齿轮测量中心ZC1蜗杆齿廓偏差测量中测头对准误差的影响,本文首先分析了齿轮测量中心蜗杆轴向齿廓偏差测量原理,在ZC1蜗杆齿面方程基础上,建立了蜗杆轴向齿廓测量误差模型,修正得到轴截面上齿廓测量点的轴向坐标,再依据精度标准评定得到蜗杆轴向齿廓偏差,并分析了蜗杆的不同头数、模数和分度圆直径对蜗杆轴向齿廓测量误差的影响规律。在齿轮测量中心上开展了蜗杆轴截面齿廓测量实验,测头对准误差修正前后,齿廓总偏差的差异值由1.2 μm降为0.2 μm,齿廓形状偏差的差异值由0.5 μm降为0.3 μm,齿廓倾斜偏差的差异值由2.5 μm降为0.4 μm。测头对准误差对齿廓形状偏差的影响相对较小。本文提出的方法可有效减小齿轮测量中心测头对准误差对蜗杆轴截面齿廓偏差测量结果的影响。
[3]
[4] YIN P L, HAN F B, WANG J H, et al. Influence of coordinate system establishment error on tooth profile deviation measured by standard polar coordinate method on gear measuring center[J]. Measurement, 2022, 187: 110344.
[5] LING M, LING S Y, LI X Y, et al. Effect on the measurement for gear involute profile caused by the error of probe position[J]. Measurement Science and Technology, 2022, 33(11): 115013.
[6] DU H L, ZENG P Y, JU B F, et al. A new centering method of the measuring probe for spiral scanning-based surface profile measurement systems[J]. Measurement Science and Technology, 2017, 28(2).
Article Outline
万辉, 汤洁, 石照耀. ZC1蜗杆齿廓测量测头对准误差修正[J]. 光学 精密工程, 2024, 32(1): 53. Hui WAN, Jie TANG, Zhaoyao SHI. Correction of probe alignment error for ZC1 worm gear profile measurement[J]. Optics and Precision Engineering, 2024, 32(1): 53.