抛光过程中光学元件表面划痕的形成和控制
下载: 1442次
1 引言
光学元件是光学系统中极其重要的一个组成部分,例如在美国国家点火装置中,共需要大口径光学元件7000余件以及各类小口径元件和备件30000余件[1],而这些高精度的光学元件的表面质量直接决定了整个光学系统的性能和可靠性。光学元件的表面质量最早是由McLeod等[2]于1945年提出,其中光学外观标准美军标对划痕的级数和长度都有相应要求[3]。若要控制表面质量,首要问题是抑制划痕的形成和划痕长度。目前,国内外学者对抛光过程中的划痕问题进行了研究。郭亚晶等[4]采用振镜扫描的方式实现了光学元件表面损伤的检测。韩敬华[5]研究了抛光粉的粒度分布和晶粒的大小与硬度对抛光质量的影响。梁尚娟等[6]通过对氧化铈抛光颗粒的表面改性,降低了抛光表面的粗糙度,减少团聚的抛光粉颗粒在工件表面产生的划痕。Chandra等[7]指出划痕的形成与抛光粉颗粒的团聚以及加工盘面和工件表面的硬度有关,抛光液的pH值在等电点附近或加工盘较硬时更容易产生划痕。Ring等[8]认为大粒径杂质颗粒在微观粗糙不平的盘面和工件表面之间受到足够载荷,印入工件表面并相对划动产生划痕,并研究了不同粒径的杂质颗粒在两种不同硬度工件表面形成的划痕数量与划痕深度的关系。Suratwala等[9]将划痕的形成过程简化为杂质颗粒在恒力作用下印入盘面,同时在工件表面产生划痕的过程,并且提出了划痕长度的计算公式。上述研究都没有对不同类型的划痕成因和形成条件及其具体过程进行详细研究。本文从理论上分析了不同类型划痕的形成过程,研究了划痕产生概率和长度的影响因素,就抛光液浓度和抛光盘结构对划痕形成的影响进行了实验,并研究了抛光过程中它们对抛光速率以及抛光表面粗糙度Sa的影响。
2 抛光过程中划痕的形成分析
2.1 抛光机理
目前,抛光过程的机理公认是机械、化学、物理综合作用的过程[10]。磨盘与工件相对运动时,散粒磨料将化学作用形成的较软的水解层机械去除,裸露新的表面,然后再水解、抛光去除,直到获得理想面形。这其中包含了机械去除、水解、沉积层流变作用。在抛光过程中,并不是所有的抛光粉颗粒都能参与核心抛光过程。在散粒磨料的磨削过程中,由于盘面的微观粗糙表面和宏观的开槽刮盘处理,可以参与抛光过程的颗粒数大约只有总数的30%。此外,抛光粉颗粒的粒径并不完全相同,根据其粒径分布的不同,实际受力并参与抛光过程的颗粒数只有总数的0.01%~0.1%[11]。而实际受力并参与抛光的颗粒数直接影响了单个颗粒的受力情况,从而影响划痕的产生。
2.2 划痕的形成条件
在抛光过程中划痕的形成是因为工件表面的杂质颗粒所受载荷超过了临界值,且载荷不同也会导致划痕类型不同[12]。当载荷大于弹性极限时,在接触区域会产生不可恢复的塑性亮丝,当载荷继续增大超过断裂极限时,还会形成裂纹,包括中位裂纹和侧向裂纹。
由此可知,划痕形成需要以下两个条件。
1)只有粒径大于平均粒径的杂质颗粒才有可能受到过大载荷而产生划痕。杂质颗粒的来源有很多种,大致可以分为以下两类[13]。a)抛光内部来源,主要为抛光液中氧化铈颗粒团聚和抛光过程中产生的盘面与工件的抛光残留物。b)抛光外部来源,主要为工作服上的团聚抛光颗粒、抛光盘碎屑和胶粒、抛光设备掉落的铁屑,以及工件准备送往抛光时清洗过程残留的磨砂颗粒等。
2) 盘面对杂质颗粒的支撑力足以使颗粒在工件表面产生塑性或是脆性破坏,从而在有一定速度的相对运动情况下形成划痕。Swain[14]用光学显微镜和扫描电子显微镜进行观察,发现用维氏硬度印压头刻划脆性玻璃表面时,当载荷小于0.05 N时,玻璃表面只出现塑性划痕,载荷为0.1~5 N时,玻璃表面出现中位裂纹和侧向裂纹,其中载荷为0.1~1 N时侧向裂纹不明显,当载荷大于5 N时,划痕边界有崩边,侧向裂纹出现交叉情况。
2.3 划痕的形成机理与分析
当杂质颗粒开始产生划痕时,其受力最大,盘面提供的力决定了杂质颗粒的高度。假定沥青盘面为Kelvin固体[15],此时颗粒印入盘面的应力应变关系为
式中:σ为应力;ε为应变;η为黏度;t为时间;E为工件的模量。Eε为盘面弹性应力,在划痕产生过程中相对较小,可忽略不计。在颗粒印入过程中,随着印入深度的不断增大,颗粒受力慢慢变小,印入速率也不断减小,此时有
σ随着应变引起的高度不断增大而逐渐变小,从而导致应变速率减小,直到盘面提供的支撑力不足以支持颗粒在工件表面产生划痕时划痕终止。划痕在起始和结束阶段,划痕深度逐渐变小,由脆性划痕过渡到塑性亮丝,最终杂质颗粒对工件表面的作用力不足以产生划痕时终止,完整划痕的形成过程如
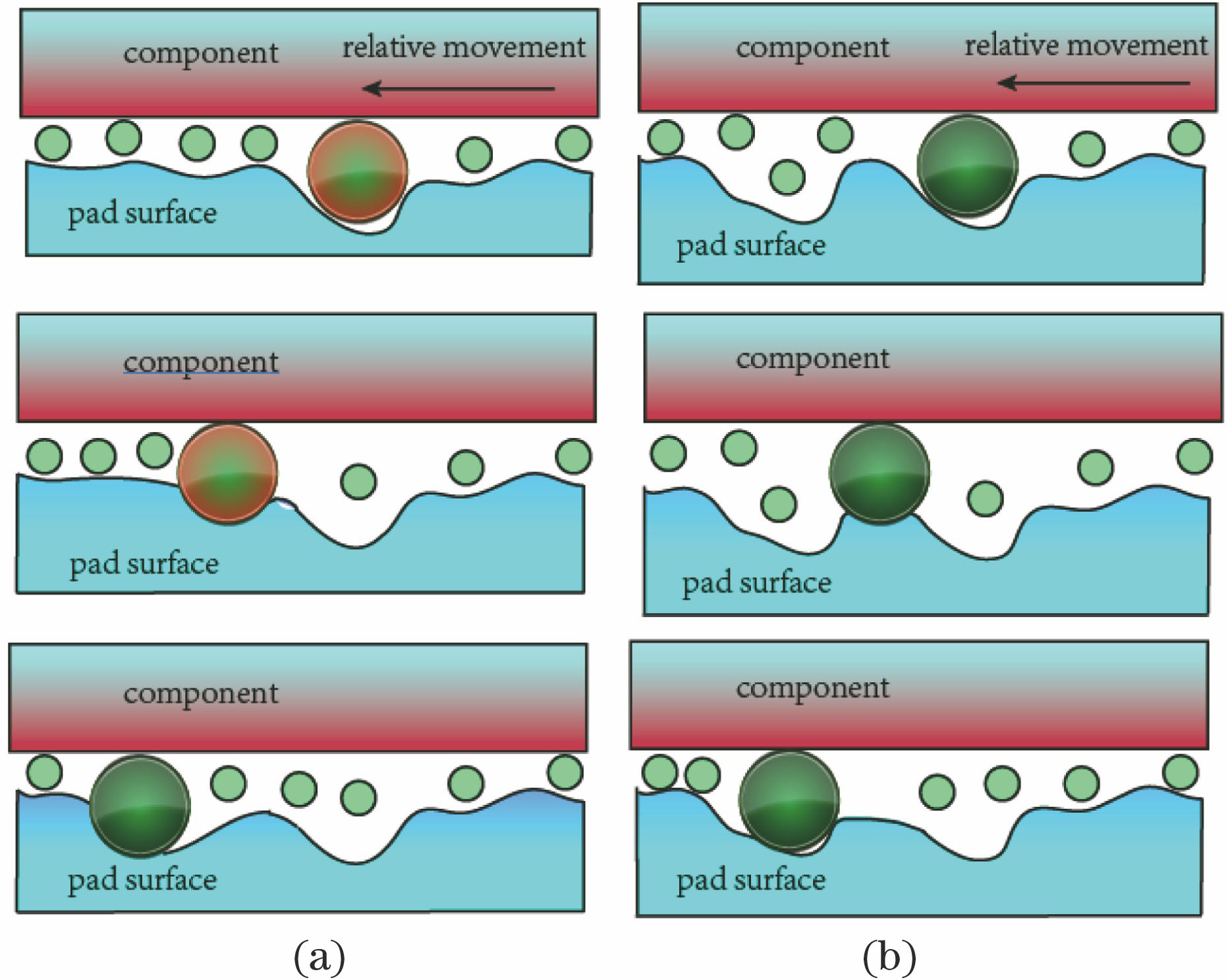
图 1. 划痕形成示意。(a)完整划痕;(b)划痕中断
Fig. 1. Schematic of scratch formation. (a) Complete scratch; (b) interrupted scratch
在划痕产生的起始阶段,不同杂质颗粒的高度有较大差异,且受力与高度变化的关系无法确定,因此整体划痕长度的预测难度较大。而在收尾阶段,大部分杂质颗粒已经嵌入抛光盘面,单颗粒受力减小,高度变化不大,受力与高度变化的关系依然无法确定,还是难以预测划痕长度,但是对于不同粒径的杂质颗粒所形成的划痕在收尾阶段的长度可以通过简化计算推算出来。
由此可以得出收尾阶段印入工件表面相同深度时杂质颗粒的粒径(R1、R2)与应力大小(F1、F2)的关系:
再根据(1)式,忽略弹性力,可推出盘面对颗粒的支撑力Fs与印入速度v之间的关系,此时大部分杂质颗粒已经嵌入抛光盘面,与盘面接触区域的面积近似为πR2,可得Fs=πR2η
由此可近似算出收尾阶段所形成的杂质颗粒划痕长度的比例关系即为印入过程的时间比值,在相同印入深度的情况下也就是印入速度(v1、v2)的反比,即:L1/L2=v2/v1=
2.4 划痕形成的控制
光学加工工艺包含研磨和抛光两个步骤,抛光作为最后一道工序,是划痕研究中需要重点关注的过程。抛光过程的三个主体分别是工件、抛光液和抛光盘。不同材料和外形工件的四大抛光特征(面形、表面质量、表面粗糙度和去除率)在相同抛光工艺下也会有差异,而本文研究的是后两个主体,即抛光液和抛光盘在加工相同的石英工件时对抛光效果的影响。
在相同的加工环境、工艺条件和相同给液速率下,使用较高浓度的抛光液意味着在抛光过程中参与抛光作用的抛光粉颗粒数目较多,参与抛光作用的磨粒的单颗粒受力减少。即使有杂质颗粒参与受力,其单颗粒受力较小,超过临界值的概率降低,从而形成划痕的概率也降低。在实际光学加工中,抛光表面产生的划痕数量并不多,为方便研究,本实验在抛光液中添加一定浓度的α-Al2O3抛光颗粒作为杂质颗粒进行破坏性实验,研究了抛光液浓度对抛光质量的影响。
Choi等[17]研究了化学机械抛光(CMP)抛光中聚氨酯抛光盘的孔隙和槽对划痕的影响,发现只有槽没有孔的抛光盘会在抛光过程中形成大量不规则划痕。抛光盘面的微孔可以容纳大粒径颗粒,避免其参与抛光作用产生划痕,即使大粒径杂质颗粒已经引起划痕,也会落入盘面微孔而导致支撑力落空,划痕终止,这就有效缩短了所产生划痕的长度。沥青抛光盘虽然在抛光过程中可以很好地贴合工件表面,抛光表面的中高频误差相对较小,抛光效果优异,但其表面也因流体性质容易变得光滑无孔,使得工件表面的粗糙度上升且容易产生划痕。因此,本文研究了沥青抛光盘改性,通过碳酸氢钠的热分解作用,沥青盘具备多微孔结构,从而在保证高频误差抑制能力的同时,有效降低抛光表面产生划痕的可能性。
综上所述,本文根据划痕的形貌特征和长度提出并验证了划痕的形成机理,并从两个方面进行抛光过程中划痕的抑制研究:一方面通过提高参与抛光的基质颗粒的数量,降低单颗粒的受力,使其难以达到形成划痕的临界受力条件,从而减少所形成划痕的数量,并同时研究工艺条件对抛光效果的影响;另一方面通过制备具有多孔结构的沥青抛光盘,在保持沥青抛光盘抛光优势的前提下,解决了其盘面容易变光滑的问题,免去了普通沥青盘在使用前需要刮盘使表面变粗糙的步骤,只需在每次使用前用毛刷将沥青盘表面微孔结构刷净即可。此外,沥青抛光盘表面微孔可以容纳大粒径颗粒,降低其参与抛光作用产生划痕的概率,即使大粒径杂质颗粒已经引起划痕,也会落入盘面微孔而导致支撑力落空,划痕终止,从而缩短了所产生划痕的长度。
3 实验与分析
3.1 实验
实验样品为熔石英玻璃,直径为100 mm,厚度为10 mm。用W14绿碳硅精磨后,再用质量浓度为4%的抛光液进行抛光,得到面形统一为凹球面的实验样品,样品的峰谷(PV)值为0.5λ左右(λ为波长)。所使用的抛光粉是中位粒径为1 μm的R3303型高纯氧化铈抛光粉。抛光设备为南京仕研光电设备有限公司的YP035型单轴研磨抛光机。抛光盘是用Gugolz 73#沥青制作的胶盘,不额外给机头加气压,机头重28 N,主轴转速为60 r/min,控制机头摆动的盘转速为30 r/min,温度为(21±1) ℃。破坏性实验用的掺杂颗粒是欣辉科技公司生产的α-Al2O3抛光颗粒,中位粒径分别为1 μm(0.6~1.6 μm)、2 μm(1.1~3.1 μm)、3 μm(1.7~6.5 μm)。抛光去除率和粗糙度实验用质量分数为4%的抛光液对空白样品进行预抛光15 min,保证样品面形和胶盘贴合后再用不同质量分数的抛光液在相同工艺参数下进行抛光,通过电子分析天平测量抛光去除质量得到抛光速率,再用ZYGO轮廓仪测量得到抛光表面粗糙度,重复进行了三组实验,取三组数据的平均值作为实验结果。破坏性实验也是先用空白样品进行预抛光15 min,保证样品面形和胶盘贴合,然后用掺杂了0.5%质量分数的Al2O3抛光颗粒的抛光液对样品进行抛光处理20 min,抛光液的质量分数分别为2%、4%和6%。另外用掺杂了0.5%质量分数的Al2O3抛光颗粒的氧化铈抛光液对样品抛光20 min,Al2O3抛光颗粒的粒径分别为1,2,3 μm。用光学显微镜观测实验产生的划痕亮丝。
为了制备多微孔结构沥青抛光盘,将200 g Gugolz 73#沥青放入恒温电炉中进行熔融,首先在110 ℃下恒温熔融,等完全熔融后,将温度提升到155 ℃恒温3 min。再将称量好的5 g碳酸氢钠添加到熔融的沥青中并搅拌均匀。最后将预热至60 ℃的抛光基板水平放置,并将熔融的沥青倒到基板上,自然冷却至室温固化,即得到多微孔沥青抛光盘。
3.2 实验结果分析
3.2.1 抛光粉质量分数对去除率与表面粗糙度的影响
不同抛光粉质量分数的抛光液对石英样品的去除率(RR)和表面粗糙度(Sa)的影响如
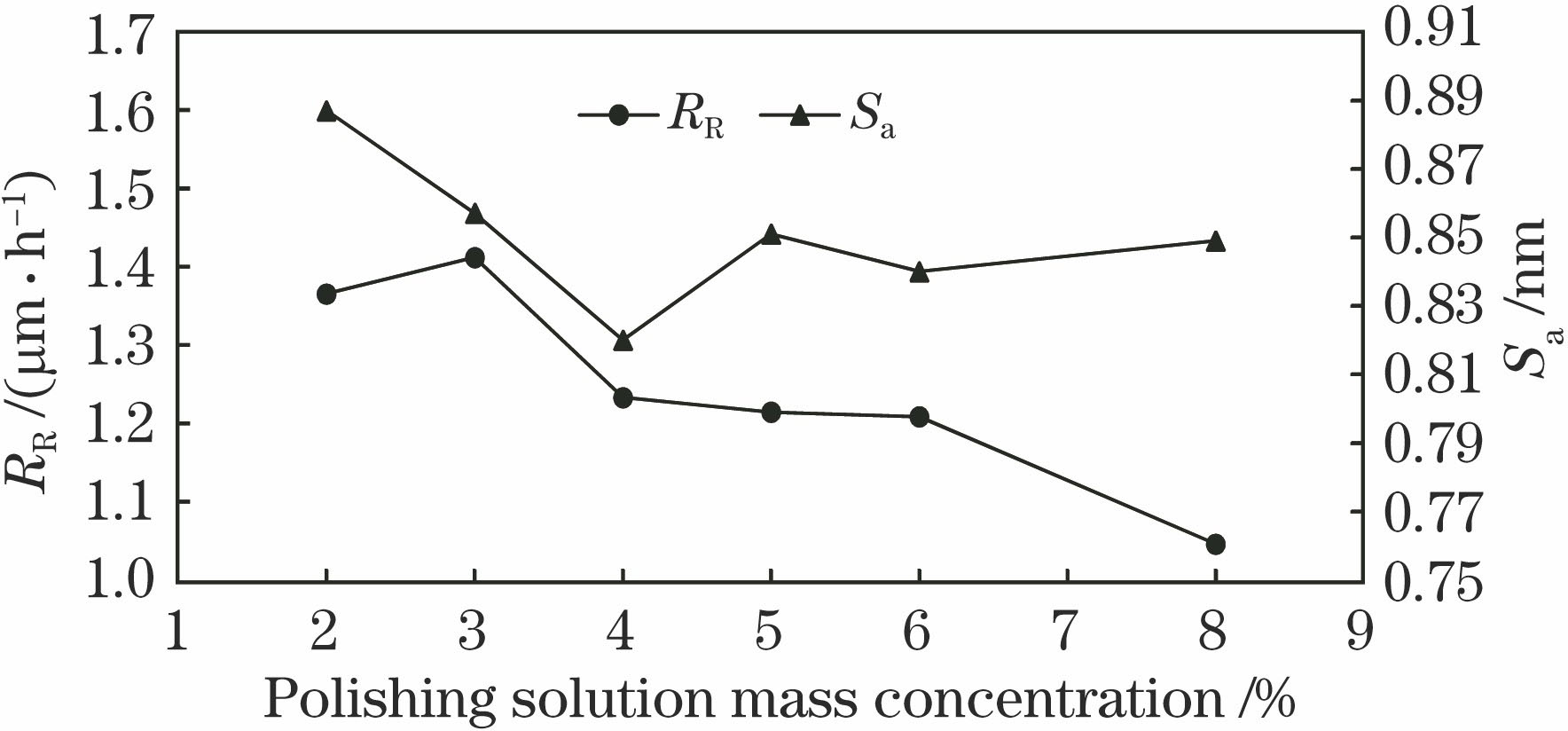
图 3. 抛光液质量浓度对抛光速率和表面粗糙度的影响
Fig. 3. Effect of polishing-powder mass fraction in polishing solution on polishing rate and surface roughness
从
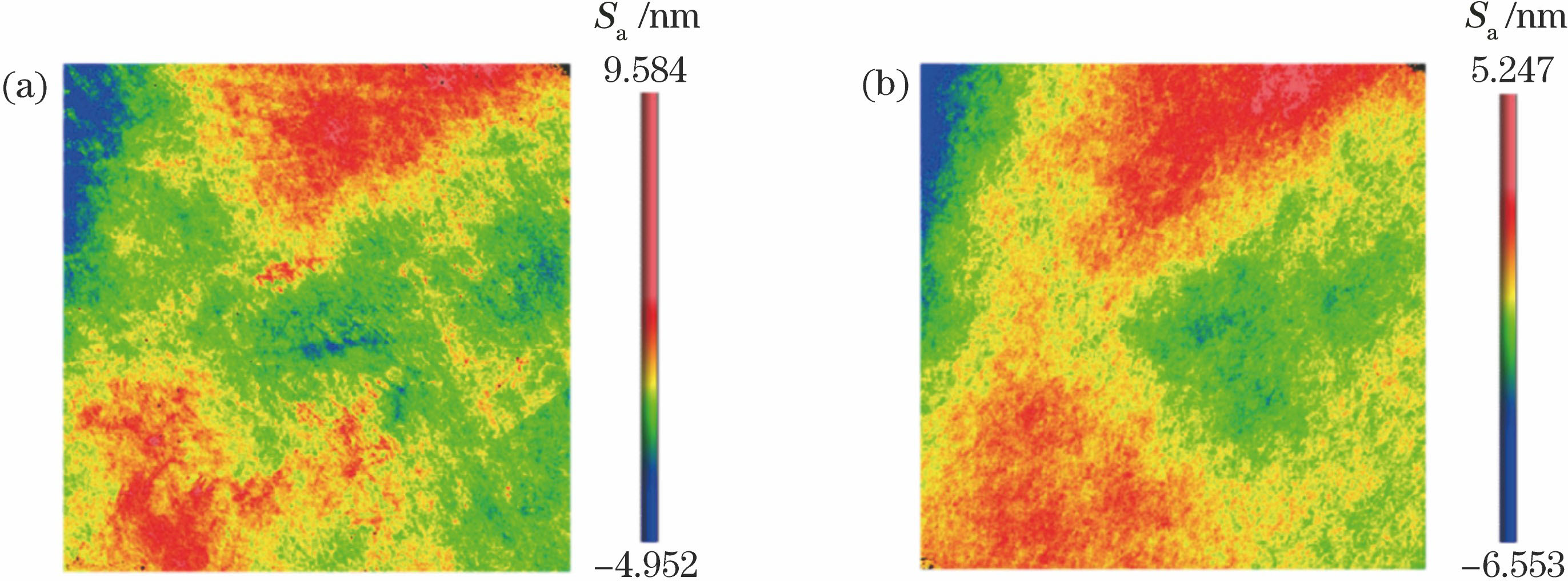
图 4. 采用不同质量浓度抛光液抛光的表面粗糙度检测结果。(a) 2%质量浓度;(b) 6%质量浓度
Fig. 4. Measured results of surface roughness polished by polishing solutions with different polishing-powder mass fractions. (a) Mass fraction of 2%; (b) mass fraction of 6%
3.2.2 划痕形貌
加工过程中出现的划痕可以分为3类,如
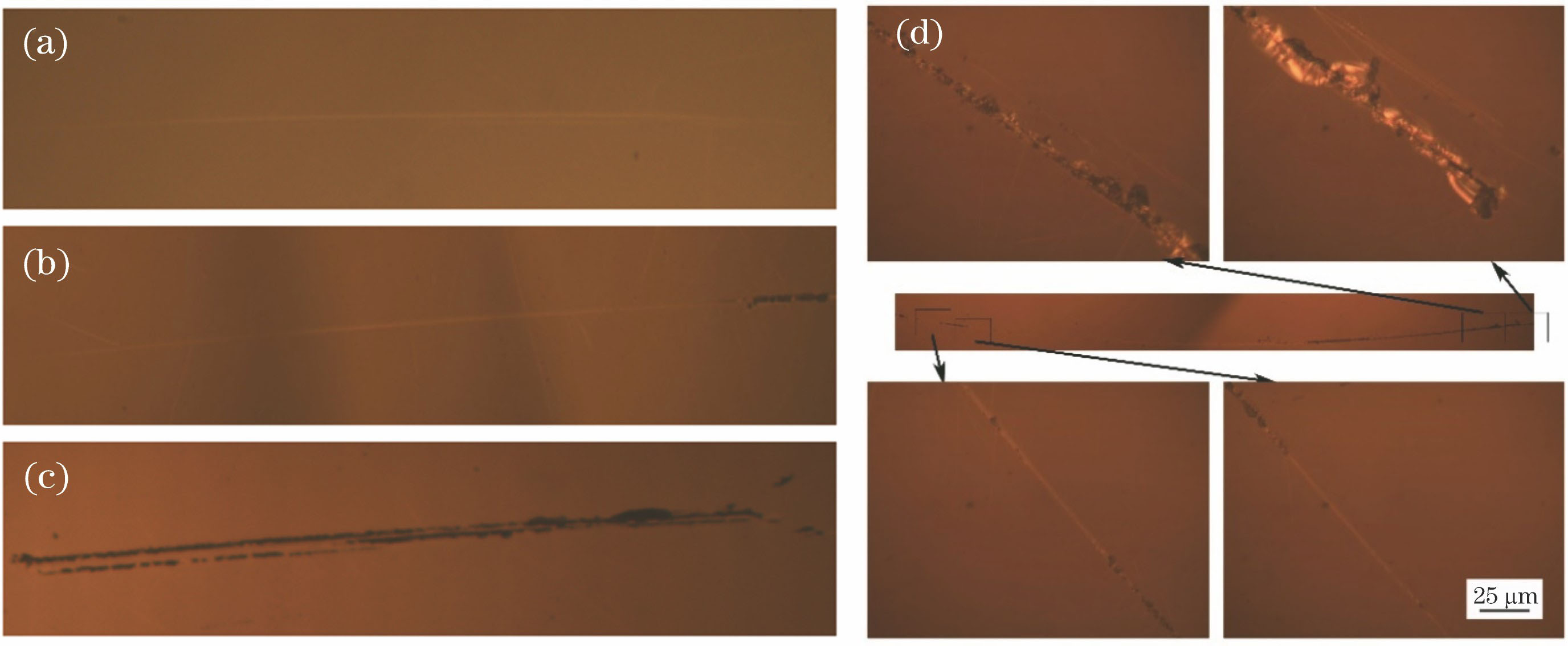
图 5. 不同类型划痕显微图。(a)塑性划痕;(b)脆性和塑性的复合划痕;(c)脆性划痕;(d)超长划痕
Fig. 5. Micrographs of different types of scratches. (a) Plastic scratches; (b) composite scratches with brittleness and plasticity; (c) brittle scratches; (d) extra-long scratches
在实际光学加工生产中,塑性划痕是最多的,它的形成条件较低,不需要较大的杂质颗粒,抛光液中也可以形成氧化铈团聚颗粒。一般情况下,宽度小于1 μm的亮丝在光学检测中是不作要求的,可以忽略。通常情况下在表面上可以决定光洁度质量级别的划痕都是
在划痕形成过程中杂质颗粒的三体滚动还会导致超长划痕的出现,严重影响了表面光洁度级别。
3.2.3 划痕长度
由划痕形成过程的分析可知:在收尾阶段,高度变化一样时,不同粒径杂质颗粒印入过程所需的时间不同,在相同工艺参数的情况下,假定颗粒相对于工件的速度相同,可得到收尾阶段划痕长度与颗粒粒径的变化关系。
积分布为50%)粒径才达到2 μm以上,因此模拟3 μm的下限比实际统计结果稍有上移,且实际统计中3 μm杂质颗粒形成的多数划痕(颗粒累积分布为67%)粒径都在2 mm以内。另外,实际统计的3 μm杂质颗粒产生的长度在4 mm以上的划痕数量比模拟结果少,这是因为在实际抛光中,杂质颗粒要形成一个完整划痕的难度较大,尤其是长划痕,其形成时间相对较长,很可能会出现盘面对杂质颗粒的支撑波动或者杂质颗粒自身碎裂等情况,使得实际形成的长划痕数量要比模拟数量少,但两者的长度范围较为一致。
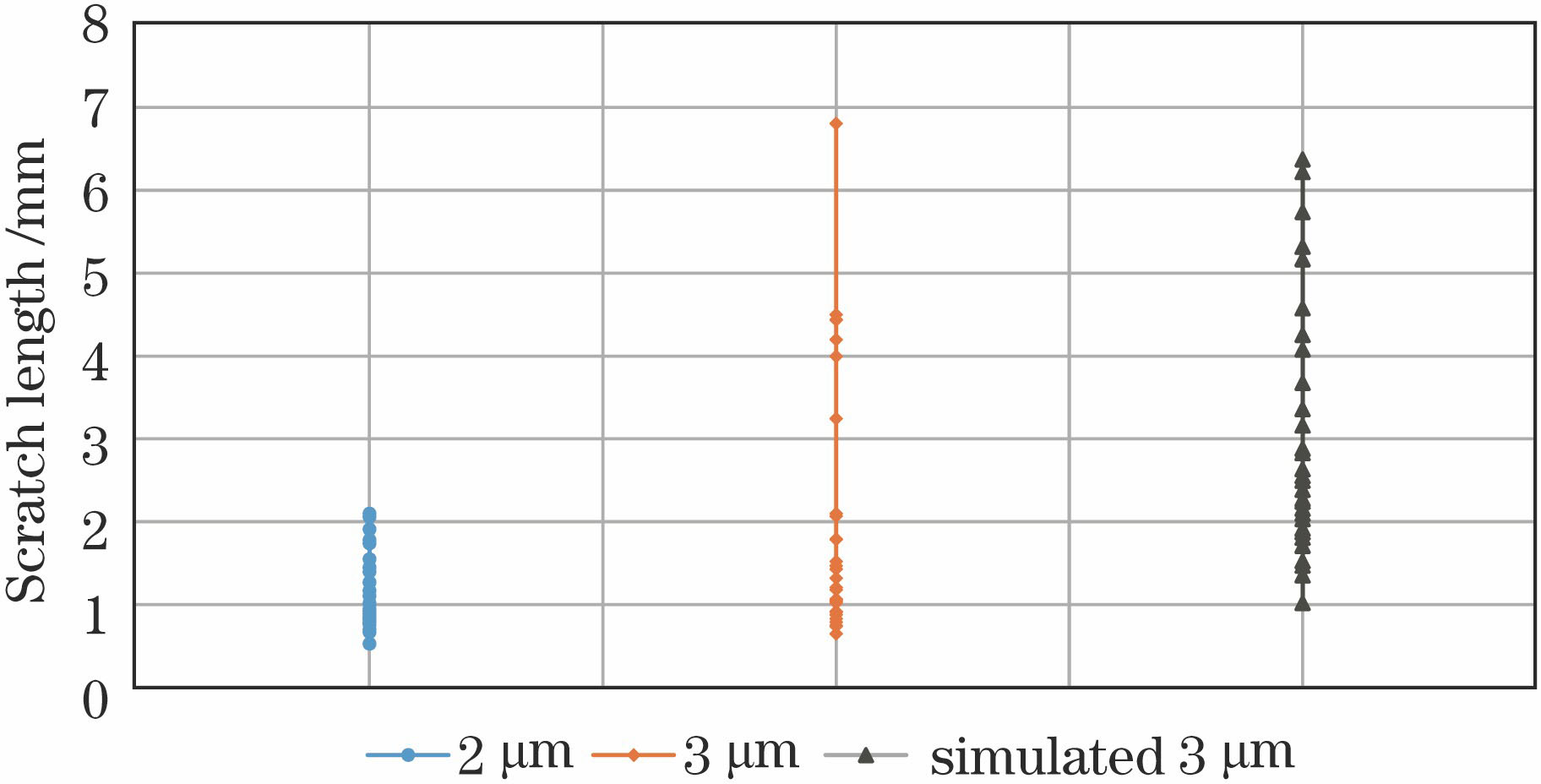
图 6. 2 μm和3 μm中位粒径的杂质颗粒形成划痕的实际统计结果与根据2 μm杂质颗粒产生的划痕长度模拟的3 μm结果
Fig. 6. Actual statistical results of scratches formed by impurity particles with 2-μm and 3-μm intermediate particle sizes and simulated 3-μm results based on scratch lengths generated by 2-μm impurity particles
3.2.4 多微孔结构抛光盘
抛光过程中,抛光盘和工件的实际接触区域大小会影响抛光效率,因此多微孔结构抛光盘的孔径不能过大,一般控制在50~500 μm,如
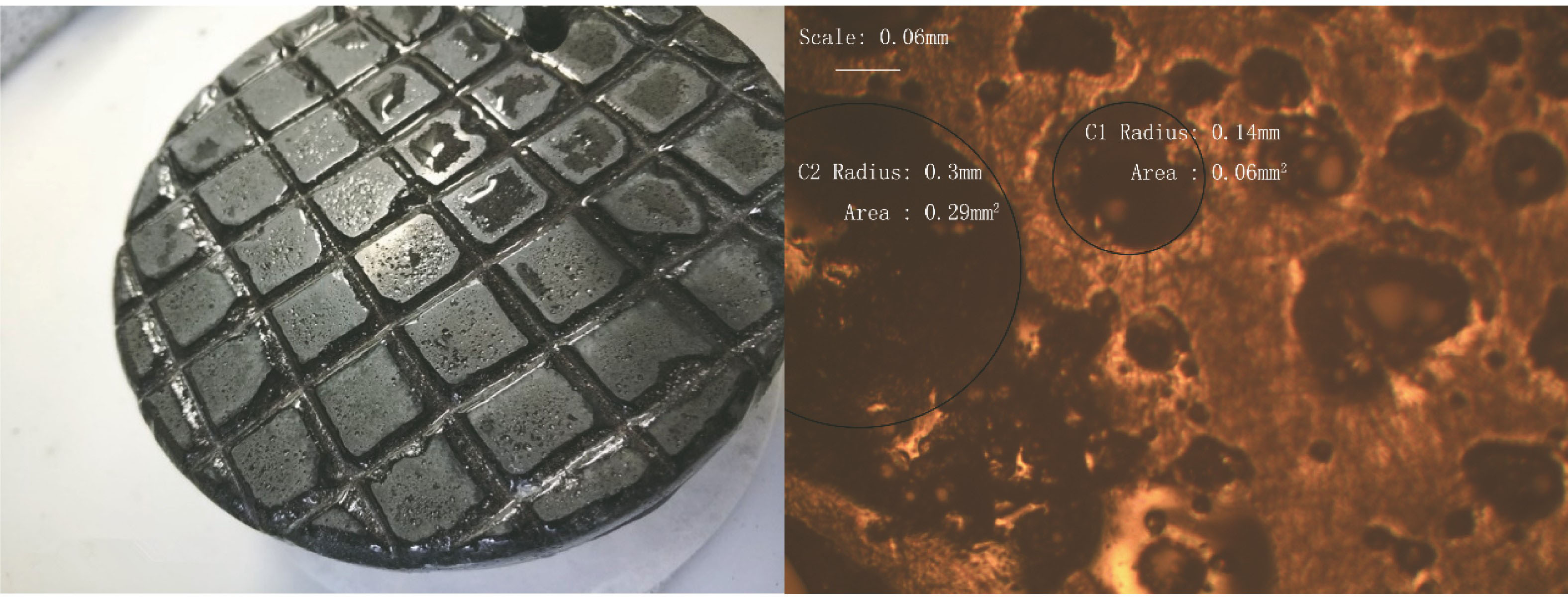
图 7. 多微孔沥青抛光盘。(a)实物图;(b)光学显微图
Fig. 7. Microporous pitch-polishing pad. (a) Physical picture; (b) optical micrograph
由于杂质颗粒产生划痕需要一定的载荷条件,因此在相同的抛光参数与工艺条件下,为保证对比性和可操作性,在抛光液中添加了同一质量分数的相同杂质颗粒,使得横向对比时各自抛光过程中杂质颗粒数量相同,从而直观看出在一定条件下抛光液中的抛光粉质量分数对所产生划痕数量的影响,结果见
根据第2节的理论分析结果,可通过提高基质抛光颗粒的数量来达到降低杂质颗粒所承受的载荷,从而降低划痕产生概率的目的。实验结果表明,随着基质抛光颗粒质量分数的增大,经过抛光20 min后,样品表面出现的划痕数量明显减少,说明在抛光过程中使用中位粒径为1 μm的R3303型抛光粉时,其在抛光液的质量分数为6%时,划痕产生的概率会相对较小。而具有多孔结构的沥青抛光盘表面能够存储大粒径的杂质颗粒,使杂质颗粒在抛光盘和工件之间参与抛光作用的可能性降低,盘面微孔结构的存在还会导致引起划痕的杂质颗粒受力落空,从而达到减少划痕数量和抑制划痕长度的目的。
表 1. 掺入相同杂质颗粒时不同质量分数抛光液在抛光过程中产生的划痕数量
Table 1. Number of scratches produced during polishing process by polishing solution with different polishing-powder mass fractions doped with same amount of impurity particles
|
此外,抛光盘表面的微孔结构使得抛光粉和工件表面接触更充分,且可以容纳更多的抛光粉颗粒,抛光效率得到了显著提升,并且饱和抛光浓度也稍有提升,如
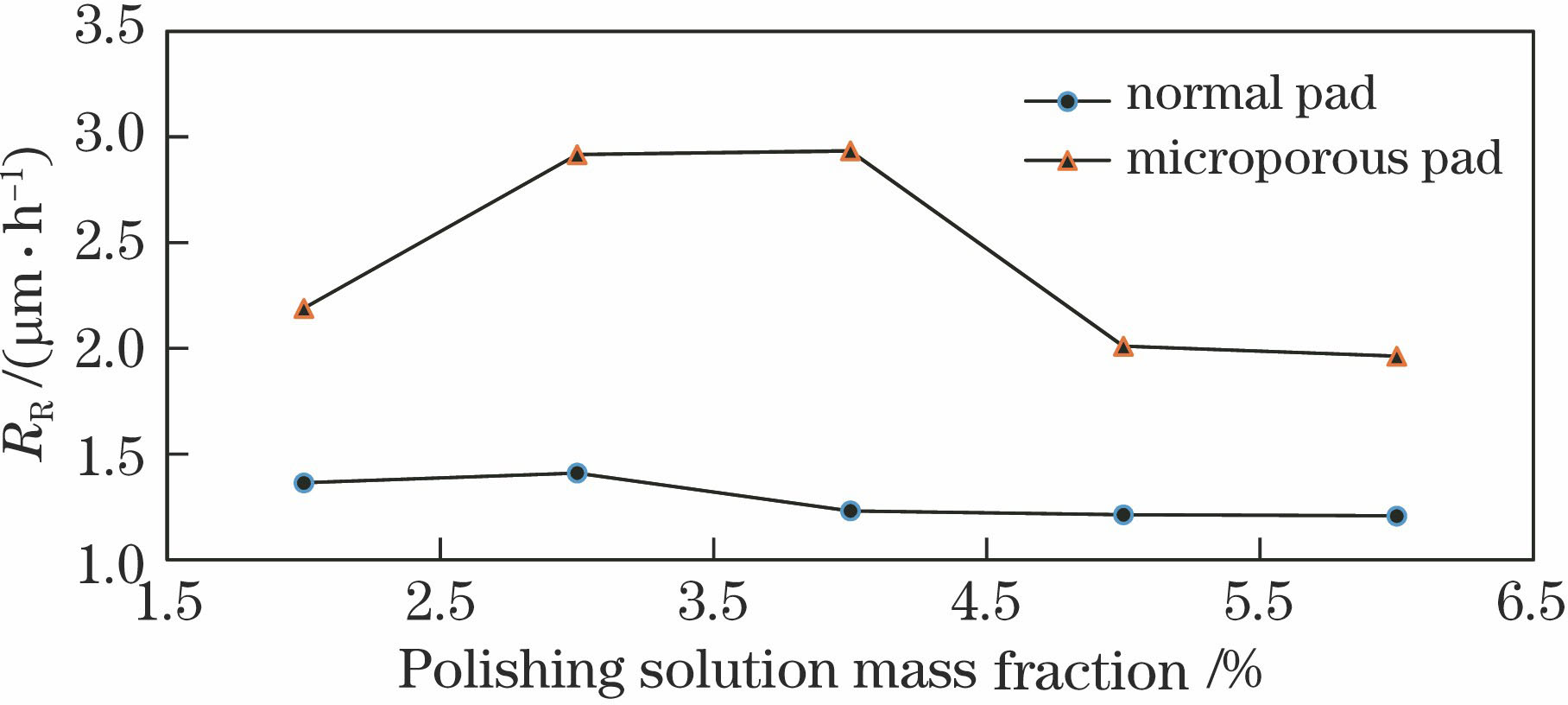
图 8. 两种抛光盘上抛光液质量浓度对抛光速率的影响
Fig. 8. Effects of polishing-powder mass fraction in polishing solution on polishing rate for normal polishing pad and microporous polishing pad
从
4 结论
在划痕产生过程中,由于很难定量分析杂质颗粒位置高度和受力随高度的变化关系,抛光过程中产生的划痕长度难以定量预测。本文通过引入不同粒径的α-Al2O3颗粒,研究了抛光过程中不同类型划痕的形成过程,发现形成的划痕长度不确定性很大:若在划痕形成过程中受到盘面给予的支撑落空,划痕中断,长度较小;若杂质颗粒出现三体滚动,划痕长度则成倍增加。本文还模拟了收尾阶段杂质颗粒形成的划痕长度与颗粒粒径的关系,发现划痕长度的比例关系为粒径比的2/3次方,与实验结果相吻合。理论分析和实验结果表明,通过提高抛光液的质量分数和在沥青盘表面添加微孔结构,可提高参与抛光作用的基质抛光粉颗粒数量,降低单颗粒的受力,其受力大小突破临界值的可能性相对降低,且由于微孔结构的存在,大粒径颗粒实际参与抛光过程的可能性相对较少,这就降低了划痕产生的概率。在综合考虑抛光去除率和抛光表面粗糙度的前提下,通过工艺改进和沥青盘改性,将抛光液的质量分数提升到6%,并利用碳酸氢钠热分解,使沥青抛光盘具有多微孔结构,能够在保证沥青抛光盘优异的抛光效果的前提下,抑制了划痕的形成和划痕长度,对实际加工有重要的指导意义。
[2] McLeod J H, Sherwood W T. A proposed method of specifying appearance defects of optical parts[J]. Journal of the Optical Society of America, 1945, 35(2): 136-138.
[3] Aikens DM. The truth about scratch and dig[C]//International Optical Design Conference and Optical Fabrication and Testing, June 13-17, 2010, Jackson Hole, Wyoming, United States. Washington, D.C.: OSA, 2010: OTuA2.
[4] 郭亚晶, 唐顺兴, 姜秀青, 等. 基于振镜扫描方式的光学元件表面损伤检测[J]. 光学学报, 2017, 37(6): 0612003.
[5] 韩敬华. 控制光学元件超光滑表面粗糙度的研究[D]. 四川: 四川大学, 2006.
Han JH. Study on controlling the super smooth surface roughness of optical components[D]. Sichuan: Sichuan University, 2006.
[6] 梁尚娟, 汤文龙, 焦翔, 等. 改性抛光剂对光学玻璃抛光质量的影响[J]. 中国激光, 2017, 44(12): 1203001.
[8] Ring T A, Feeney P, Boldridge D, et al. Brittle and ductile fracture mechanics analysis of surface damage caused during CMP[J]. Journal of the Electrochemical Society, 2007, 154(3): H239-H248.
[15] 张义同. 热粘弹性理论[M]. 天津: 天津大学出版社, 2002.
Zhang YT. Theory of thermo-viscoelasticity[M]. Tianjin: Tianjin University Press, 2002.
[17] Choi J G, Prasad Y N, Kim I K, et al. The synergetic role of pores and grooves of the pad on the scratch formation during STI CMP[J]. Journal of the Electrochemical Society, 2010, 157(8): H806-H809.
Article Outline
汤文龙, 梁尚娟, 焦翔, 樊全堂, 尹进, 朱健强. 抛光过程中光学元件表面划痕的形成和控制[J]. 中国激光, 2019, 46(12): 1202009. Wenlong Tang, Shangjuan Liang, Xiang Jiao, Quantang Fan, Jin Yin, Jianqiang Zhu. Formation and Control of Scratches on Surfaces of Optical Components During Polishing[J]. Chinese Journal of Lasers, 2019, 46(12): 1202009.