一种基于偏振热像的金属疲劳损伤评估方法
下载: 1145次
1 引言
疲劳失效是机械结构及零部件失效的主要形式,宏观上没有明显的塑性变形且难以检测和预防,因而构件的疲劳破坏往往会造成巨大的经济损失甚至危及生命。传统的疲劳损伤检测方法通过对材料、设备与构件的相关部位进行检测,可以有效地发现已发展成形的宏观缺陷或大部分微观缺陷,但需要花费大量时间和财力,且对于机械结构中的早期损伤难以做到有效的诊断和评价[1]。
研究表明,金属疲劳损伤是一个复杂的能量耗散过程[2]。在此过程中,金属材料接收输入的机械能,引起不可恢复的非弹性形变并改变材料内部的缺陷数量与分布,使内摩擦和位错运动引起的原子振荡加剧而向周围环境中耗散能量,表现为疲劳生热现象,在宏观上表现为材料表面温度的变化。因此,近年来基于温度场演化特征的材料静力学/疲劳和失效机理的研究得到快速发展。如:樊俊铃[3]通过宏微观力学和连续热力学理论,推导了疲劳能量耗散计算方法,结合局部热扩散方程,建立了物理意义明确的疲劳极限快速评估方法。朱达荣等[4]研究了低周疲劳过程热力学熵产率与累积熵产变化特征,在此基础上,建立了基于热力学熵的金属低周疲劳寿命预测模型。Wang等[5]以循环塑性区能量耗散率作为疲劳裂纹扩展的指标,通过对疲劳裂纹尖端区耗散过程的描述,提出了一种局部分析疲劳裂纹扩展速率的方法。de Finis等[6]考虑疲劳试验中涉及的所有热源,开发了一种新的热成像数据分析程序,提出了一种估计疲劳极限的新技术。这些研究采用实时、无损、非接触式的红外热像技术来监测材料疲劳的物理过程和热耗散,建立了多种疲劳损伤准则和寿命预测模型,从疲劳损伤和能量转化的角度快速地评定材料的疲劳性能,为降低疲劳试验成本提供了新的思路[7-8]。红外热像仪测温的瓶颈在于其精确性[9],高精度测温目前还存在较多困难,尤其是需要记录非常微小的温度变化时。原因如下:
1) 疲劳热像法主要关注材料或构件表面的能量耗散。红外图像在生成和传输过程中,会不可避免地受到热像仪成像特点及环境干扰等因素引起的随机噪声、起伏背景干扰与热扩散效应的影响,导致图像模糊、边缘扩散、可视程度降低[10];
2) 材料加工的局限性以及环境腐蚀、锈蚀等均可能给红外热像带来很大的噪声,增加了通过红外热像进行金属工件缺陷检测的难度[11];
3) 温度场信号并不是材料的固有特性,易受材料本身的热扩散性质和热边界条件的影响。目前用于疲劳损伤观测的红外热像仪在监测实际表面温度时,需先设定好物体的实际表面发射率并假定保持不变,而实际的目标表面发射率与表面显微结构有关且在疲劳损伤过程中不断变化,故通过疲劳温升信息直接研究材料的疲劳性能往往存在争议[3];
4) 采集的温度数据是试件上某个区域内的平均温度,直接用于估算材料的疲劳极限时,没有考虑疲劳损伤过程中表面微观形貌改变,表面微观形貌改变会造成表面发射率变化,进而可能会引入虚假的温度不均匀性,导致一些可疑的结果[12-15]。
从物理上来讲,能量耗散属于自发辐射,自发辐射的本质是电磁波,电场和磁场相互正交,并且垂直于自发辐射的传播方向,具有偏振特性[16]。研究表明,观测目标的自发辐射偏振信息与探测器观测角有关,从多个不同方向进行偏振成像,不仅可以获得自发辐射的强度信息(通过辐射定标可转换为温度信息),而且通过解析可以得到目标材料性质、表面粗糙度、温度、辐射率等,从而可将目标识别从表面结构上升到空间结构[17-18]。理论研究与实验已经证实,相对传统红外光强成像,红外偏振成像可以显著提高目标之间的对比度、减小复杂环境影响、凸显物体轮廓和物体细节、提升红外图像质量[19]。相对金属材料而言,由于表面具有光滑性,偏振度较大,偏振测量仪器无需准确辐射量校准就可以达到相当高的精度[20-25]。
基于上述分析,本文在热像检测的基础上融入偏振探测技术,综合利用金属试件在疲劳损伤过程中的红外偏振特征,提出一种新的基于表面红外偏振热像特征的金属疲劳损伤评估方法。以Q235低碳钢平板试件疲劳损伤为研究对象,通过搭建金属红外偏振热像疲劳损伤检测实验系统,分析金属疲劳过程中表面形貌及温度特性的变化,给出金属疲劳过程中表面热红外偏振特征的提取方法,利用主成分分析(PCA)选择图像均值及方差表征金属疲劳损伤过程中红外偏振热像的特征量,建立了基于BP(back propagation)神经网络非线性系统的预测模型,并对金属构件的疲劳损伤程度进行评估。
2 理论基础
金属疲劳损伤过程将机械能转变为热能、储能、弹塑性应变能和滞弹性内耗等其他形式的能量,其中绝大部分能量是以热能进行释放的,宏观表现为材料或构件表面温度场的变化。
根据广义胡克定律,对于均匀的弹性体,热应力和应变之间的关系满足[26]
式中:Δεii=ε11+ε22+ε33为主应变的变化;Δσii=σ11+σ22+σ33为主应力的变化;α为线膨胀系数;ΔT为温度变化;E为弹性模量,υ为泊松比。
对绝热、可逆的弹性体而言,其热力学方程有
式中:T为绝对温度;CV为等容比热容;ρ为密度;K为体积模量。由等容比热容和等压比热容Cp之间的关系可以得出
(3)式表明,在机械载荷的作用下,能量耗散使金属材料表面温度变化,温度变化与应力/应变有关。因此,通过红外热像法监测金属材料表面温度可以实现材料或构件疲劳性能参数的监测。
研究表明,疲劳损伤过程中,金属材料的阻尼系数随着疲劳载荷反转的次数变化而变化,反映了在循环应力作用下以温度形式向外耗散的耗散能,且满足[27]
式中:WP是单位体积的耗散能;W为单位体积储存的最大能量。
根据振动学理论,在自由振动过程中,金属材料阻尼与连续两点的振动峰值A1、A2的衰减比对数成正比[28-29],即
金属材料在循环加载过程中,由于位错滑移而在金属表面产生随机分布的表面起伏。本研究将连续两个表面起伏高度看成是自由振动的两个连续峰值,(4)式和(5)式表明,表面粗糙度的演化反映了疲劳损伤过程中塑性应变能的变化,反映了疲劳损伤程度。
假设在疲劳损伤过程中,光学背景温度为Tb,场景温度为Ts,所发出的热辐射为非偏振光,金属材料的表面温度为To,疲劳损伤偏振热成像如
式中:εs、rs与εp、rp分别是热辐射发射率、反射率的垂直分量和平行分量;P(T)是温度为T时Planck黑体辐射。考虑到金属物体透射率非常小且吸收的能量全部自发辐射,根据Kirchhoff定律,发射率与反射率满足
将(7)式代入(6)式可得
传统热像仪监测疲劳损伤试件时,通常预设εs=εp=ε,接收的辐射量为
当采用偏振相机进行采集时,根据偏振度的定义,有
注意到,金属材料疲劳损伤的本质是在交变载荷的作用下,分切应力最大的滑移面上滑移阻力最小的位错首先开始滑移,随着循环次数的逐渐增加,塑性变形增大,在部分晶粒的局部区域出现滑移线,经过多次应力循环后,在表面形成驻留滑移带。滑移带表面产生“挤出脊”和“压入沟”,使材料表面粗糙化[30]。粗糙化的结果,增大了发射面积,改变了金属材料的发射率[31]。因此,通过偏振成像不仅能够获得与传统热像仪测量温度对应的辐射量,还可以得到目标材质、辐射率等更多信息,能够增强红外图像质量、减小复杂环境的影响。
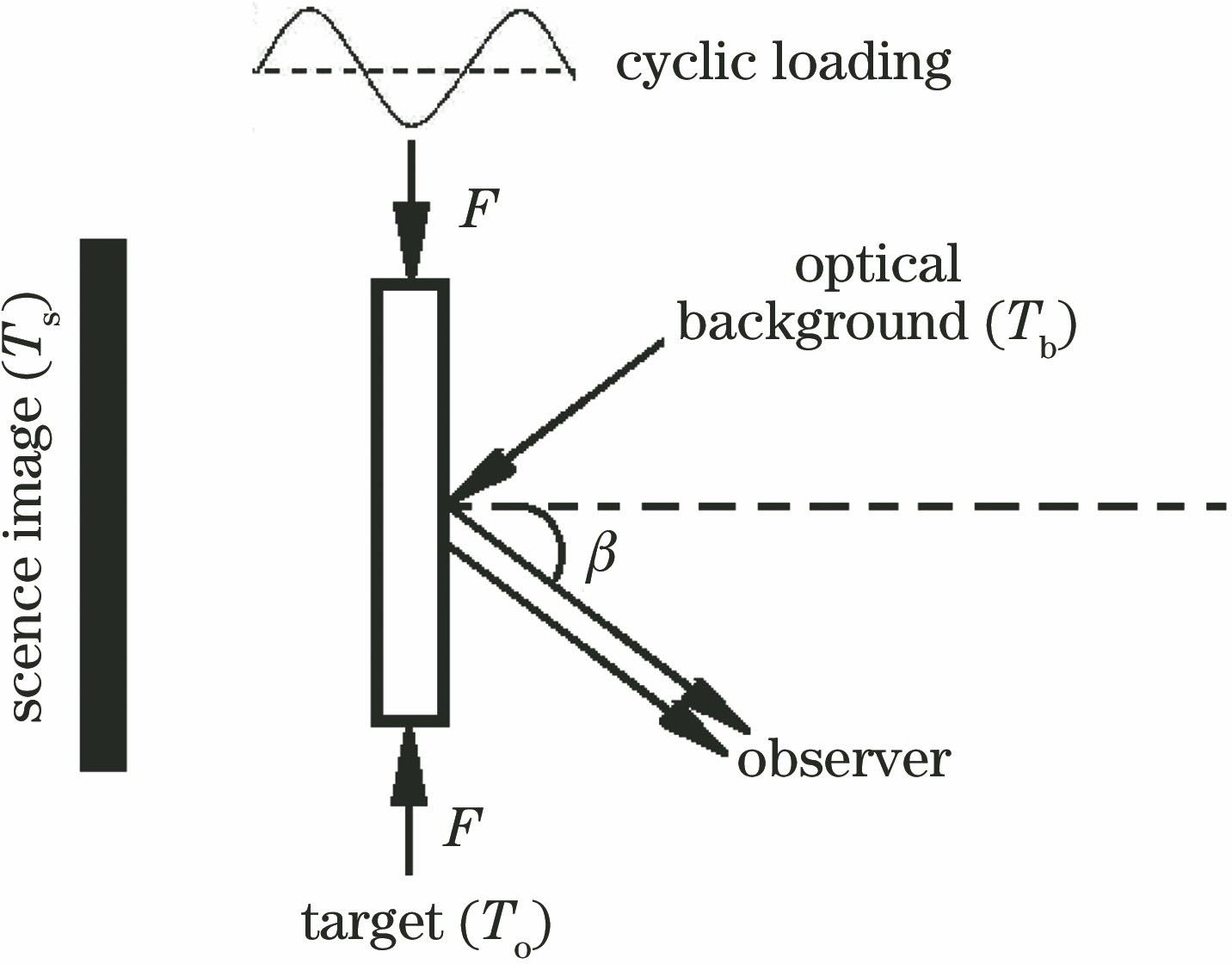
图 1. 疲劳损伤偏振热成像示意图
Fig. 1. Schematic diagram of polarized thermal imaging for fatigue damage
3 疲劳损伤实验与偏振热像获取
3.1 红外偏振成像的原理
假设目标自发辐射Stokes矢量为Sin=[S0,S1,S2,S3],其中,S0表示自发辐射的强度,S1为水平方向的线偏振分量,S2为45°方向的线偏振分量,S3与圆偏振有关,在实际测量中很小,可以忽略。则该自发辐射透过偏振方位角为α的偏振成像系统获得的图像I(α)为
当α等于0°、60°、120°时,计算的Stokes参量为
相应地,自发辐射的偏振度P和偏振角θ为
3.2 实验设备与实验材料
选取电液伺服疲劳试验机(长春机械院SDS-200)作为实验系统,采用红外偏振相机(PolarCamera-IR-640)进行偏振热像观测,采用3D 轮廓测量仪(基恩士VR-3000)对表面微观形貌进行观测。SDS-200疲劳试验机最大负荷为±200 kN,最大位移为±75 mm,可用于较大载荷疲劳监测以及静态测试。PolarCamera-IR-640型热红外偏振相机能够实时获取场景沿原始偏振方向(0°、60°、120°)的红外图像,并提供单帧采集和连续采集功能,可对三个偏振方向的图像进行实时配准校正,对偏振Stokes进行实时计算并显示。
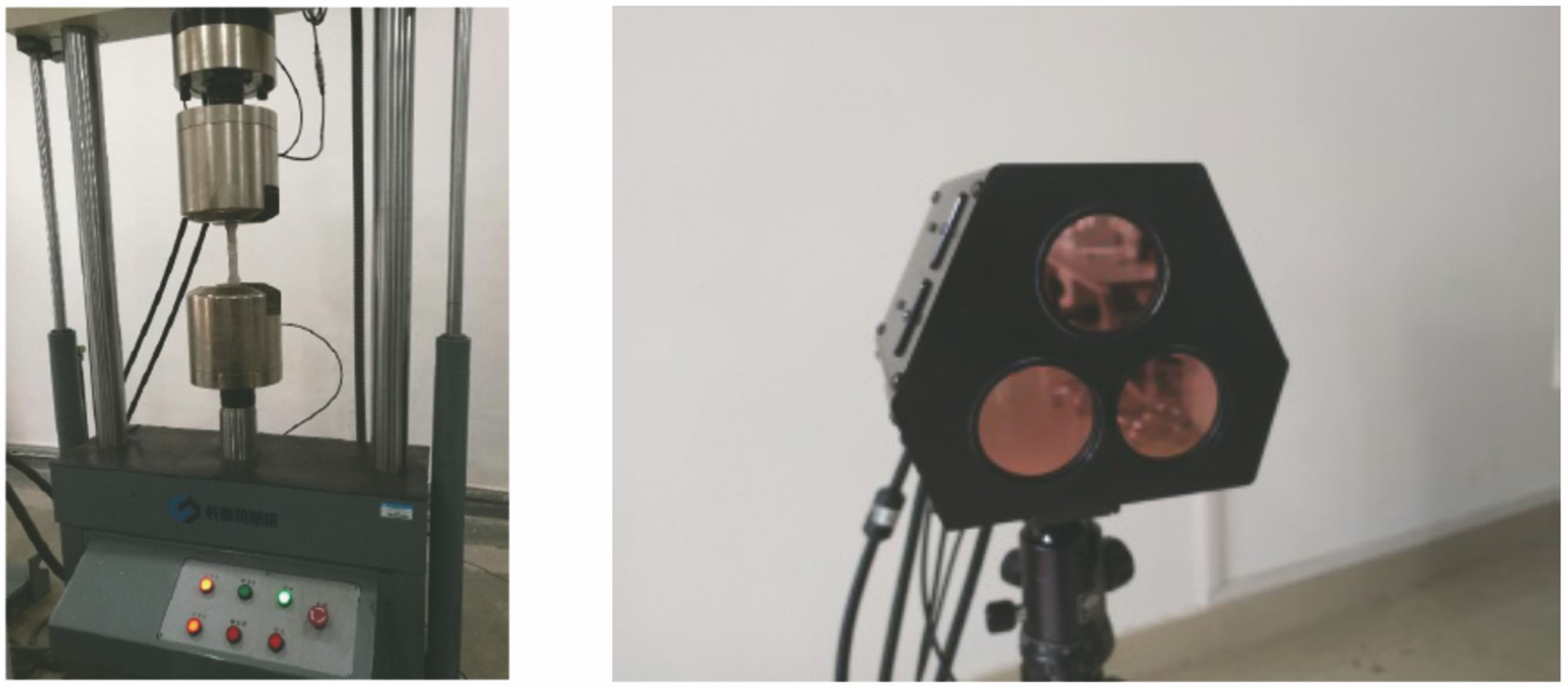
图 2. 疲劳试验机(左)与红外偏振相机(右)
Fig. 2. Fatigue testing machine (left) and infrared polarization camera (right)
试样材料为Q235碳素结构钢(GB/T 3075-2008),屈服值在235 MPa左右,含碳量适中,力学性能好,强度、塑性和焊接性能可以得到较好的配合,用途非常广泛。试验采用的Q235试样在疲劳试验机上测得其屈服载荷为35 kN。该试样由同一批次材料经激光切割加工所得,试样的几何尺寸见
对材料试样所含成分进行分析(innov x-5000 荧光光谱仪),得到材料所含元素的质量分数如
表 1. Q235化学成分参数
Table 1. Chemical composition of Q235
|
3.3 实验过程
试验前,将试样两侧表面用砂纸轴向打磨抛光并进行发黑处理以提高表面发射率。实验分成两组进行,一组用于测量疲劳过程表面微观形貌的变化,一组用于测量疲劳过程中的偏振热像。
测量疲劳过程表面微观形貌时,将试样固定在电液伺服疲劳试验机上,试件下端固定,上端承受拉伸载荷。施加频率为10 Hz、幅值为23.1 kN、均值为18.9 kN的正弦恒应变幅拉-拉疲劳载荷,利用试验机自带的计数器记录疲劳周次。达到一定周次时将其卸下并利用三维(3D) 轮廓测量仪测量其表面形貌,记录不同疲劳周次下的试样表面高度信息,进而提取表面三维形貌。相同实验共做4次。
测量疲劳过程偏振热像时,将试样固定在电液伺服疲劳试验机上,试件下端固定,上端承受拉伸载荷。施加频率为10 Hz、幅值为23.1 kN、均值为18.9 kN的正弦恒应变幅拉-拉疲劳载荷,利用试验机自带的计数器记录疲劳周次。在试样前相应角度(观测角θ=0°、30°、60°)处架设红外偏振成像系统,镜头距试样表面1 m。达到一定周次时进行一次红外偏振成像,直至试件断裂。相同实验共做10次。
为减小环境因素可能造成的干扰,实验过程在暗室内进行,且保持室内温度不变。偏振成像时,将成像目标与成像系统作为整体利用黑板对外界进行隔离。
4 实验结果与讨论
4.1 表面微观形貌演化
为直观地反映疲劳损伤过程中试样表面形貌变化,依据3D 轮廓测量仪获取的试样表面高度信息,绘制了一根试件在不同疲劳循环周次直至断裂时的表面三维形貌,如
由
4.2 热像偏振特征提取
通过偏振成像,获得不同疲劳周次时0°、60°、120°三个偏振方位角的疲劳损伤自发辐射光强图像I(0°)、I(60°)、I(120°),然后通过(8)、(9)式解析出Stokes参量S0、S1、S2图像及偏振度DOP偏振角AOP图像,如
为进一步显示自发辐射的特征,基于Tsalis熵方法分割
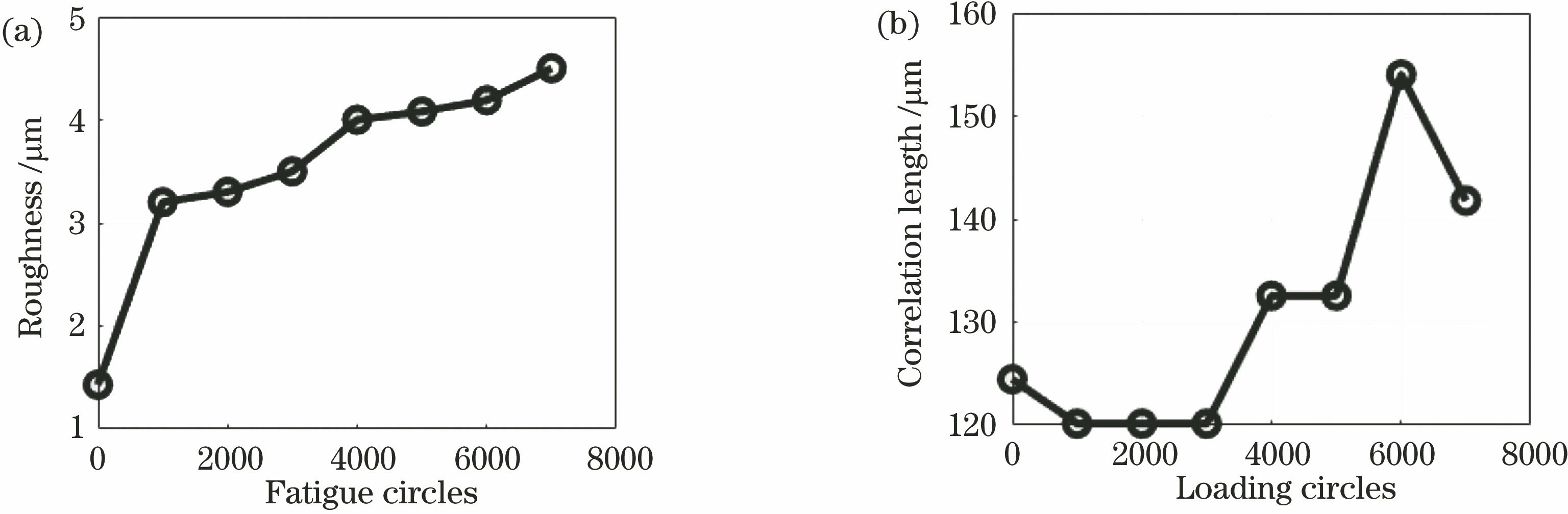
图 5. 疲劳过程(断裂前)表面粗糙度、相关长度变化。(a)表面粗糙度;(b)相关长度
Fig. 5. Evolution of roughness and correlation length during fatigue (before fracture). (a) Roughness; (b) correlation length

图 6. 自发辐射偏振方位角图像及偏振解析图像。(a) I(0°)图像;(b) I(60°)图像;(c) I(120°)图像;(d) S0图像
Fig. 6. Polarized azimuth images and S0 image of spontaneous emission after registration. (a) I(0°); (b) I(60°); (c) I(120°); (d) S0
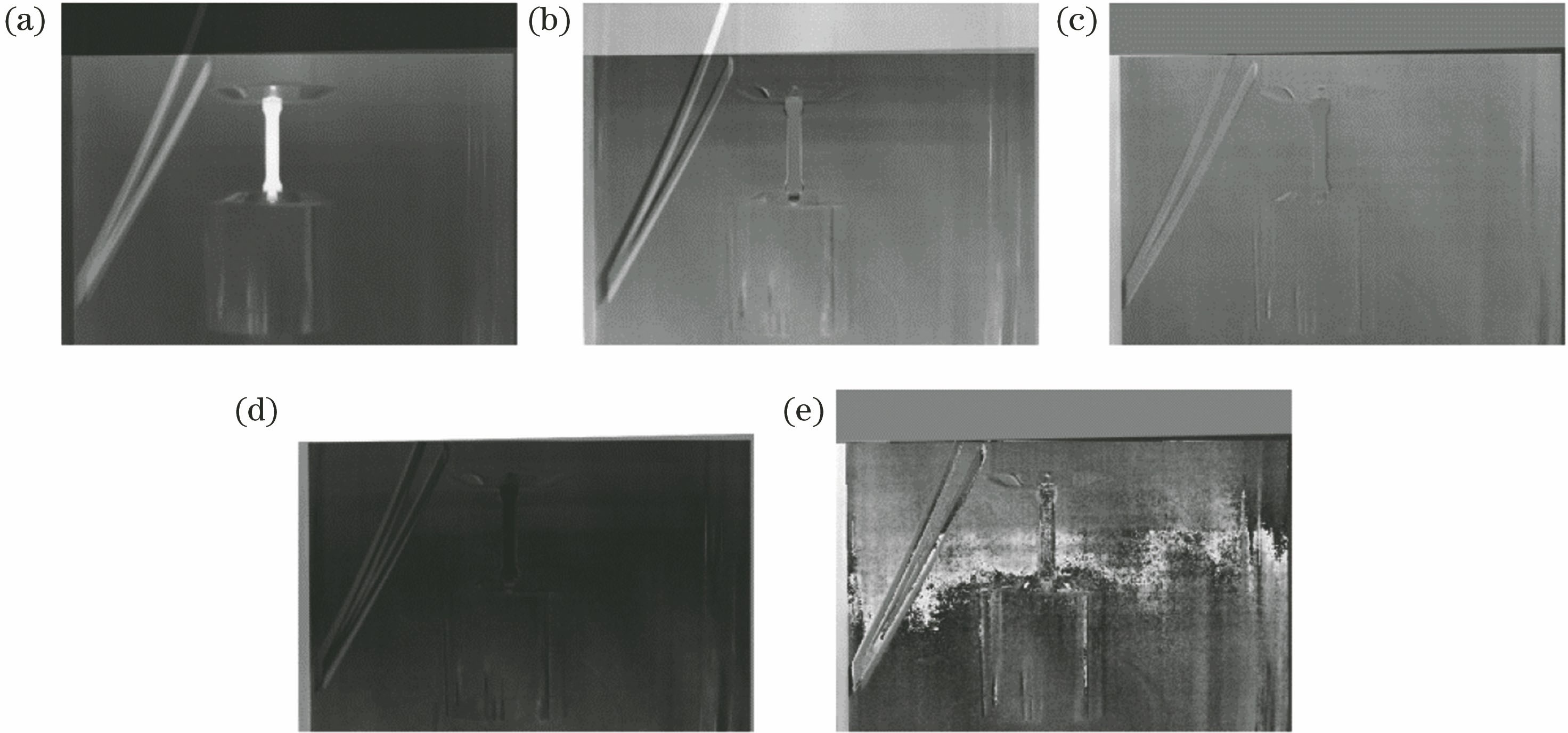
图 7. 解析后Stokes参量和偏振图像。(a) S0图像;(b) S1图像;(c) S2图像;(d) DOP图像;(e) AOP图像
Fig. 7. Stokes parameters and polarization images after analysis. (a) S0 ; (b) S1 ; (c) S2 ; (d) DOP; (e) AOP
从
4.3 主成分分析
自发辐射偏振热像的特征量较多,每个特征均从不同角度反映了疲劳损伤的程度。考虑到各特征表现的程度各不相同,为减少计算量、降低信息冗余,本文首先对热红外偏振特征量进行主成分分析,提取与试件疲劳损伤程度更为密切的特征。
设有n个样本以及p个评价指标X,其规范化矩阵为Z,相关系数矩阵为R,其中:X的矩阵元素为xij(i=1,2,…,n;j=1,2,…,p); Z的元素zij=(xij-
特征值λi即为该主成分的方差,反映了主成分在描述被评价对象时所起的作用大小。定义主成分yi的方差对总方差的贡献率为
定义前m个主成分的累积方差贡献率为
为达到降维目的,取累积方差贡献率ρ达到70%~90%的前m个主成分取代原来的p个指标。
实验过程中采集样本数量n=10,提取特征数量p=16,对这16个特征量进行主成分分析,各特征量方差贡献率wi及累计方差贡献率见
4.4 非线性预测模型
本文以主成分分析提取的特征作为输入构建基于BP神经网络的非线性模型,进行疲劳损伤程度的预测。
表 2. 特征量方差贡献率及累计方差贡献率
Table 2. Contribution rates of feature quantity variance and cumulative variance
|
BP是一种单向传播的多层前向网络,包括输入层、隐含层和输出层,通过误差反向传播算法进行实现,其具体实现过程是:先依次计算隐含层输出Hj=g(
式中:l、m、n为隐含层、输出层、输入层节点数;g是隐含层到输出层神经元之间的传递函数;(ωij、αj)、(ωjk、bk)分别是隐含层、输出层的权值和阈值;μ为学习率;ek为预测结果误差。为了避免陷入死点而难以得到最优值及可能因训练次数而降低收敛速率等问题,将隐含层、输出层激活函数选定为双曲正切函数f(μ)=
在本文中,选取方差贡献率前8个特征量
4.5 疲劳损伤预测
以Matlab2014a为平台搭建BP网络,取l=8、m=1、n=8,隐含层神经元传递函数为tansig,输出层神经元的传递函数为trainlm。取10组金属试件疲劳损伤实验数据为样本,从样本中随机选取70%的数据作为训练数据,15%作为验证数据,15%作为测试数据。对网络进行训练得到训练、验证、测试结果如
由
为进一步说明模型预测的精度,另取3组同一批次试样进行试验,将记录好的数据输入到已训练好的预测模型。结果显示,该3组数据在不同疲劳周次时预测的平均误差为16.3%、14.4%、19.2%。其中一根试件的预测结果如
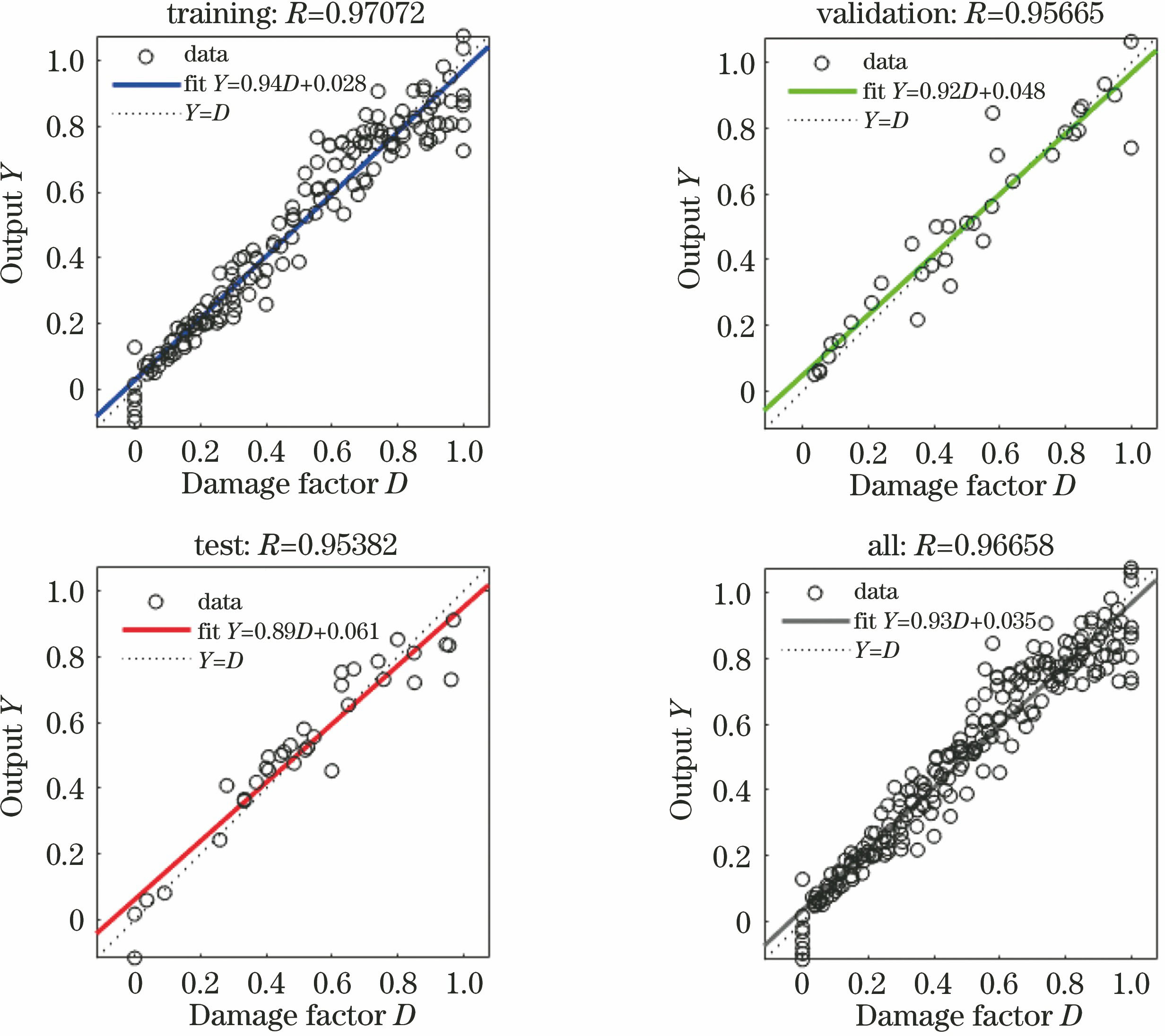
图 10. 模型训练、验证、测试及整体数据集运行结果
Fig. 10. Results of model training,validation,test and all datasets
表 3. 某根测试试件疲劳损伤预测结果
Table 3. Prediction results of fatigue damage for a tested piece
|
从
5 结论
金属表面自发辐射具有偏振特性,利用偏振成像可以获得能够反映目标材料性质、表面纹理与粗糙度、温度场、辐射率等信息的偏振图像,从而将目标识别从表面上升到多维空间结构,提高了目标识别的精度。
本文首先给出金属疲劳损伤评估偏振热成像的理论基础,从原理上说明了通过偏振成像改进热像法评估金属疲劳损伤的可能性。然后搭建了一个金属红外偏振热像疲劳损伤检测实验系统,并利用该系统观测了疲劳损伤过程表面粗糙度的变化和自发辐射的偏振图像。观测结果表明,疲劳损伤过程的表面微观形貌处于不断变化之中;自发辐射Stokes参量图像从不同角度给出了不同的信息,通过主成分分析选取目标区域图像均值和方差等8个参量作为特征量,构建基于BP神经网络非线性模型进行疲劳损伤状态预测。预测结果表明,模型训练、验证、测试结果与实际实验测量值具有较好的相关性,证明了本文方法的有效性。
[1] 周正干, 刘斯明. 铝合金初期塑性变形与疲劳损伤的非线性超声无损评价方法[J]. 机械工程学报, 2011, 47(8): 41-46, 53.
Zhou Z G, Liu S M. Nondestructive evaluation of early stage plasticity and fatigue damage of aluminum alloy using nonlinear ultrasonic method[J]. Journal of Mechanical Engineering, 2011, 47(8): 41-46, 53.
[2] Kaleta J, Blotny R, Harig H. Energy stored in a specimen under fatigue limit loading conditions[J]. Journal of Testing and Evaluation, 1990, 19(4): 326-333.
[3] 樊俊铃. 基于能量耗散的Q235钢高周疲劳性能评估[J]. 机械工程学报, 2018, 54(6): 1-8.
Fan J L. High cycle fatigue behavior evaluation of Q235 steel based on energy dissipation[J]. Chinese Journal of Mechanical, 2018, 54(6): 1-8.
[4] 朱达荣, 徐德军, 刘涛, 等. 金属低周疲劳过程热力学熵特征分析及寿命预测模型[J]. 中国机械工程, 2019, 30(16): 1904-1910.
Zhu D R, Xu D J, Liu T, et al. Thermodynamic entropy characteristics analysis and life prediction model of metal low cycle fatigue processes[J]. China Mechanical Engineering, 2019, 30(16): 1904-1910.
[5] Wang X G, Ran H R, Jiang C, et al. An energy dissipation-based fatigue crack growth model[J]. International Journal of Fatigue, 2018, 114: 167-176.
[6] de Finis R, Palumbo D, Ancona F, et al. Fatigue limit evaluation of various martensitic stainless steels with new robust thermographic data analysis[J]. International Journal of Fatigue, 2015, 74: 88-96.
[7] 张元良, 张洪潮, 赵嘉旭, 等. 高端机械装备再制造无损检测综述[J]. 机械工程学报, 2013, 49(7): 80-90.
Zhang Y L, Zhang H C, Zhao J X, et al. Review of non-destructive testing for remanufacturing of high-end equipment[J]. Journal of Mechanical Engineering, 2013, 49(7): 80-90.
[8] 刘涛, 吕盛坪, 汪方斌, 等. 低周疲劳过程金属表面热像特征提取及其熵分析[J]. 兵器材料科学与工程, 2018, 41(1): 23-29.
Liu T, Lü S P, Wang F B, et al. Feature extraction and entropy analysis of metal surface thermography in low cycle fatigue process[J]. Ordnance Material Science and Engineering, 2018, 41(1): 23-29.
[9] 刘永翔, 张健, 杜永成. 弥散介质遮蔽表面的红外成像测温方法[J]. 激光与光电子学进展, 2016, 53(9): 091201.
[10] 谢静, 杨晓燕, 徐长航, 等. 基于形态学方法的工件表面缺陷红外热像检测技术[J]. 中国石油大学学报(自然科学版), 2012, 36(3): 146-150.
Xie J, Yang X Y, Xu C H, et al. Infrared thermal images detecting surface defect of steel specimen based on morphological algorithm[J]. Journal of China University of Petroleum (Edition of Natural Science), 2012, 36(3): 146-150.
[11] 谢静, 徐长航, 陈国明. 基于MRF模型的金属工件红外热像表面缺陷检测[J]. 石油矿场机械, 2012, 41(11): 20-23.
Xie J, Xu C H, Chen G M. An infrared thermo image processing framework based on MRF model to detect surface defect on a metal element[J]. Oil Field Equipment, 2012, 41(11): 20-23.
[12] Fan J L, Guo X L, Wu C W. A new application of the infrared thermography for fatigue evaluation and damage assessment[J]. International Journal of Fatigue, 2012, 44: 1-7.
[13] Hwang S, An Y K, Kim J M, et al. Monitoring and instantaneous evaluation of fatigue crack using integrated passive and active laser thermography[J]. Optics and Lasers in Engineering, 2019, 119: 9-17.
[14] Yang R Z, He Y Z, Gao B, et al. Inductive pulsed phase thermography for reducing or enlarging the effect of surface emissivity variation[J]. Applied Physics Letters, 2014, 105(18): 184103.
[16] 牛继勇, 李范鸣, 马利祥. 热红外自发辐射偏振特性分析以及验证实验[J]. 光电工程, 2014, 41(2): 88-93.
[17] 张哲, 刘欣悦, 王建立, 等. 分时型长波红外高帧频偏振成像实验研究[J]. 液晶与显示, 2019, 34(5): 508-514.
[18] 赵永强, 马位民, 李磊磊. 红外偏振成像进展[J]. 飞控与探测, 2019( 3): 77- 84.
Zhao YQ, Ma WM, Li LL. Progress of infrared polarimetric imaging detection[J]. Flight Control & Detection, 2019( 3): 77- 84.
[19] 马帅, 白廷柱, 曹峰梅, 等. 基于双向反射分布函数模型的红外偏振仿真[J]. 光学学报, 2009, 29(12): 3357-3361.
[20] 王琪, 梁静秋, 梁中翥, 等. 分孔径红外偏振成像仪光学系统设计[J]. 中国光学, 2018, 11(1): 92-99.
[21] 陈伟力, 武敬力, 徐文斌, 等. 基于黑体红外偏振特性的定量分析探索[J]. 红外与毫米波学报, 2017, 36(6): 767-775.
[22] 陈伟力, 王淑华, 金伟其, 等. 基于偏振微面元理论的红外偏振特性研究[J]. 红外与毫米波学报, 2014, 33(5): 507-514.
[23] 汪震. 金属表面热红外偏振特性的模型研究[J]. 光学学报, 2009, 29(3): 707-711.
[24] 汪震, 洪津, 叶松, 等. 金属表面粗糙度对热红外偏振特性影响研究[J]. 光子学报, 2007, 36(8): 1500-1503.
[25] 汪震, 乔延利, 洪津, 等. 金属板热红外偏振的方向特性研究[J]. 光电工程, 2007, 34(6): 49-52.
[26] 樊俊铃, 郭杏林, 吴承伟. 疲劳特性的红外热像定量分析方法研究进展[J]. 力学与实践, 2012, 34(6): 7-17.
Fan J L, Guo X L, Wu C W. Fatigue characterisation based on quantitative infrared thermography[J]. Mechanics and Engineering, 2012, 34(6): 7-17.
[27] Mortezavi V, Haghshenas A, Khonsari M M, et al. Fatigue analysis of metals using damping parameter[J]. International Journal of Fatigue, 2016, 91: 124-135.
[28] Nowick AS, Berry BS. An elastic relaxation in crystalline solids[M]. New York: Academic Press, 1972.
[29] Haghshenas A, Khonsari M M. Damage accumulation and crack initiation detection based on the evolution of surface roughness parameters[J]. International Journal of Fatigue, 2018, 107: 130-144.
[30] Man J, Obrtlík K, Polák J. Extrusions and intrusions in fatigued metals. Part 1. State of the art and history[J]. Philosophical Magazine, 2009, 89(16): 1295-1336.
[31] 张大舜, 于洋, 陈亮. 粗糙表面的发射率特性研究[J]. 沈阳理工大学学报, 2006, 25(3): 74-76.
Zhang D S, Yu Y, Chen L. Study of the emissivity feature on the rough surface[J]. Transactions of Shenyang Ligong University, 2006, 25(3): 74-76.
Article Outline
汪方斌, 孙凡, 朱达荣, 刘涛, 王雪, 王峰. 一种基于偏振热像的金属疲劳损伤评估方法[J]. 光学学报, 2020, 40(14): 1412002. Fangbin Wang, Fan Sun, Darong Zhu, Tao Liu, Xue Wang, Feng Wang. Metal Fatigue Damage Assessment Based on Polarized Thermography[J]. Acta Optica Sinica, 2020, 40(14): 1412002.