飞秒激光加工超硬材料的研究进展
下载: 2823次
1 引言
20世纪60年代,世界上第一台红宝石激光器诞生。随着科学技术的不断发展,从长脉冲到短脉冲再到如今的超短脉冲激光陆续问世。自20世纪80年代起,激光脉宽正式步入飞秒阶段,现有实验已证实飞秒激光脉宽最短可以达到2.5 fs。近几十年来,随着飞秒激光器技术的不断发展,其应用已深入到光电子元件[1-3]、材料科学[4-9]、3D打印[10-12]、生物医学[13-14]、环境科学[15]等领域。相比于长脉冲激光,飞秒激光具有极短的脉宽,当飞秒脉冲激光作用到靶材上时,焦点区域附近不会发生显著的损伤,且在极短的时间尺度内,加工过程中的冲击波及热传导等影响都可以忽略不计[16-17]。航空、航天、**、计算机、光学、汽车等领域的飞速发展,对材料提出了轻量化、高强度等要求,各种有色金属、合金以及非金属复合材料在各行各业中都得到了日益广泛的应用,这也对超精密加工提出了更高的要求,各种加工性能优异的切削刀具的研制也成为了必然趋势。超硬材料具有硬度高以及耐腐蚀性和光电性能优异等独特的优势,因此,超硬材料刀具或超硬材料涂层刀具成为加工各类新型难加工材料的理想工具。在光电子元件领域,各类超硬材料的掺杂半导体材料也广泛应用,使得超硬材料自身的加工制造面临着高质量、高精度、高加工效率等一系列挑战。用普通刀具直接对超硬材料进行加工会使刀具产生严重磨损,而利用微秒或纳秒等长脉宽激光加工超硬材料则会由于较大的热影响区而导致加工精度不高。飞秒激光除了能实现现代意义上的“冷加工”之外,还具有高效性、精确性、加工材料的广泛性和多样性等诸多优点,从而使得其对超硬材料进行微纳加工的前景更加广阔。为此,本文总结了近年来国内外飞秒激光加工超硬材料的研究成果和现状,以及飞秒激光与超硬材料的作用机理,探索飞秒激光加工超硬材料的规律及方法,这对促进超硬材料在多元领域内的应用及推动飞秒激光加工技术的进一步发展具有参考价值。
2 飞秒激光加工超硬材料的机理与方法
2.1 超硬材料的性质
超硬材料是指维氏硬度大于40 GPa的材料,它们是不可压缩固体,具有高电子密度和高键能的共价键[18]。由于其独特的性能,超硬材料在研磨剂、切削刀具以及耐磨保护涂层等多方面有着广泛应用。在我国,超硬材料通常是指金刚石和立方氮化硼(CBN),这两种材料在很多方面具有极其相似的特性,例如均具有立方晶体结构(见
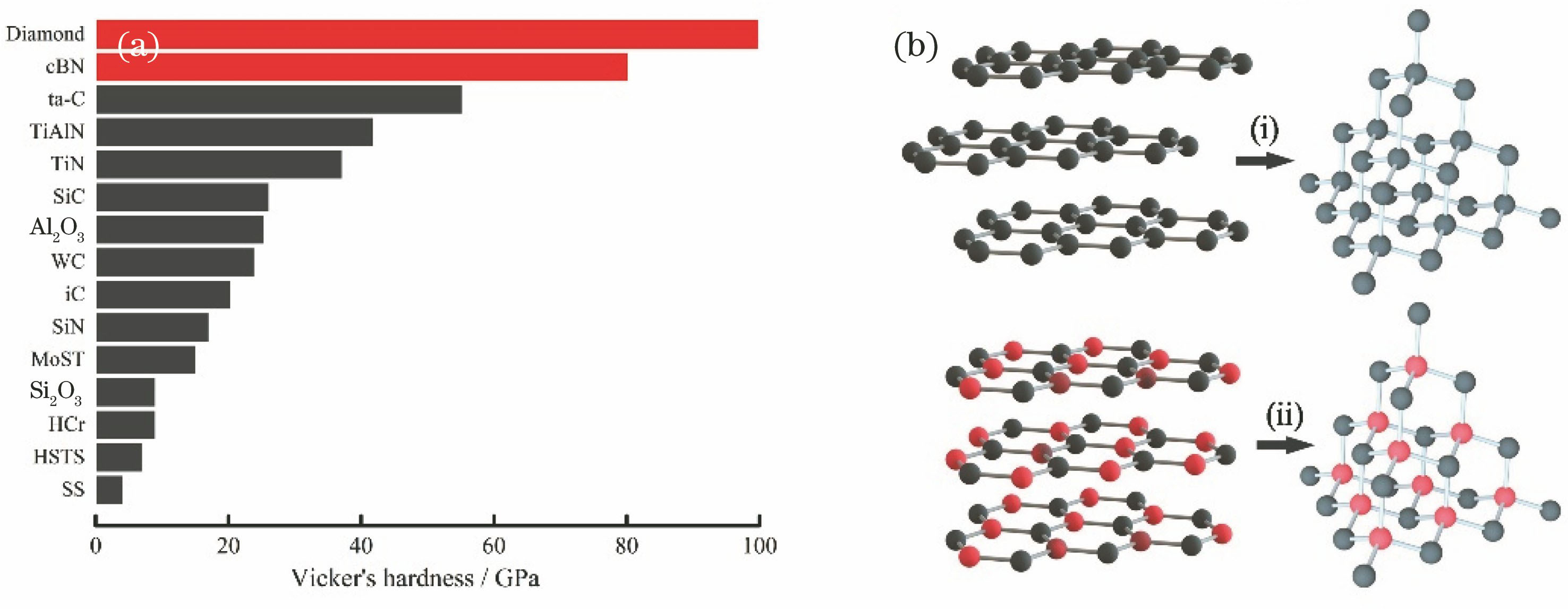
图 1. 两种典型超硬材料的硬度及其原子结构。(a)不同材料的硬度表;(b)金刚石及立方氮化硼的立方晶体结构
Fig. 1. Hardness and atomic structures of two typical ultrahard materials. (a) Hardness of different materials; (b) cubic crystal structures of diamond and CBN
表 1. 金刚石与立方氮化硼的属性及其应用
Table 1. Properties and applications of diamond and CBN
|
![激光-靶材交互作用过程中一系列物理现象的发生时域[21]](/richHtml/lop/2019/56/19/190003/img_2.jpg)
图 2. 激光-靶材交互作用过程中一系列物理现象的发生时域[21]
Fig. 2. Timescale of physical phenomena involved in laser-material interaction[21]
2.2 飞秒激光加工超硬材料机理
在激光-靶材交互作用过程中,在不同的时间尺度内会分别发生多光子吸收、隧穿电离(通常在1 fs后)、雪崩电离(约50 fs后)、电子加热(约100 fs后)、电子-晶格间的能量传递(约1 ps后)、热扩散(约10 ps后)和相变(约1 ns后)等一系列物理现象,如
激光作用下的材料烧蚀阈值是指可在光学显微镜下观测到靶材表面破坏时所需的最小激光能量密度。当作用在材料表面或内部的激光强度大于材料的烧蚀阈值时,即可实现对材料的刻蚀。对于脉宽大于10 ps的激光,由于材料表面载流子分布的不统一性,不存在精确的激光诱导材料烧蚀阈值。但对于飞秒激光加工而言,多光子电离可以释放束缚电子,使材料具有精确的烧蚀阈值。材料烧蚀阈值的大小不仅取决于吸收机制、材料性质、微观结构、表面形貌以及缺陷,还取决于激光的波长、脉宽、功率等参数[24-25]。实际的飞秒激光加工往往是多脉冲加工,材料的单脉冲激光烧蚀阈值
![长脉冲激光加工和短脉冲激光加工区别示意图[23]](/richHtml/lop/2019/56/19/190003/img_3.jpg)
图 3. 长脉冲激光加工和短脉冲激光加工区别示意图[23]
Fig. 3. Schematic of difference between long-pulse laser processing and short-pulse laser processing[23]
![飞秒脉冲激光作用下靶材表面最大温度演化及激光能量累积效应示意图[26-27]。(a)靶材表面最大温度演化;(b)激光能量累积效应](/richHtml/lop/2019/56/19/190003/img_4.jpg)
图 4. 飞秒脉冲激光作用下靶材表面最大温度演化及激光能量累积效应示意图[26-27]。(a)靶材表面最大温度演化;(b)激光能量累积效应
Fig. 4. Schematics of evolution of maximum temperature of target and pulse energy incubation effect in femtosecond laser processing[26-27]. (a) Evolution of maximum temperature of target; (b) pulse energy incubation effect
由于飞秒激光多脉冲烧蚀累积效应的存在,实际的单脉冲烧蚀阈值与多脉冲烧蚀阈值之间的关系为[28-29]:
式中:
当激光作用到材料表面时,能量一部分被反射,另一部分被吸收。在激光辐照材料的初始阶段,光学吸收的模式一般为两种:1)单个光子能量直接被激发的自由电子吸收;2)多个光子累积能量被原子或分子内部的电子跃迁或振动跃迁吸收。当激光能量足够大时,随着光学吸收过程的进行,受自由电子浓度的影响,材料内部等离子体激元被激发,逆轫致辐射随即发生。
材料的光吸收特性取决于其带隙能量
式中:
式中:
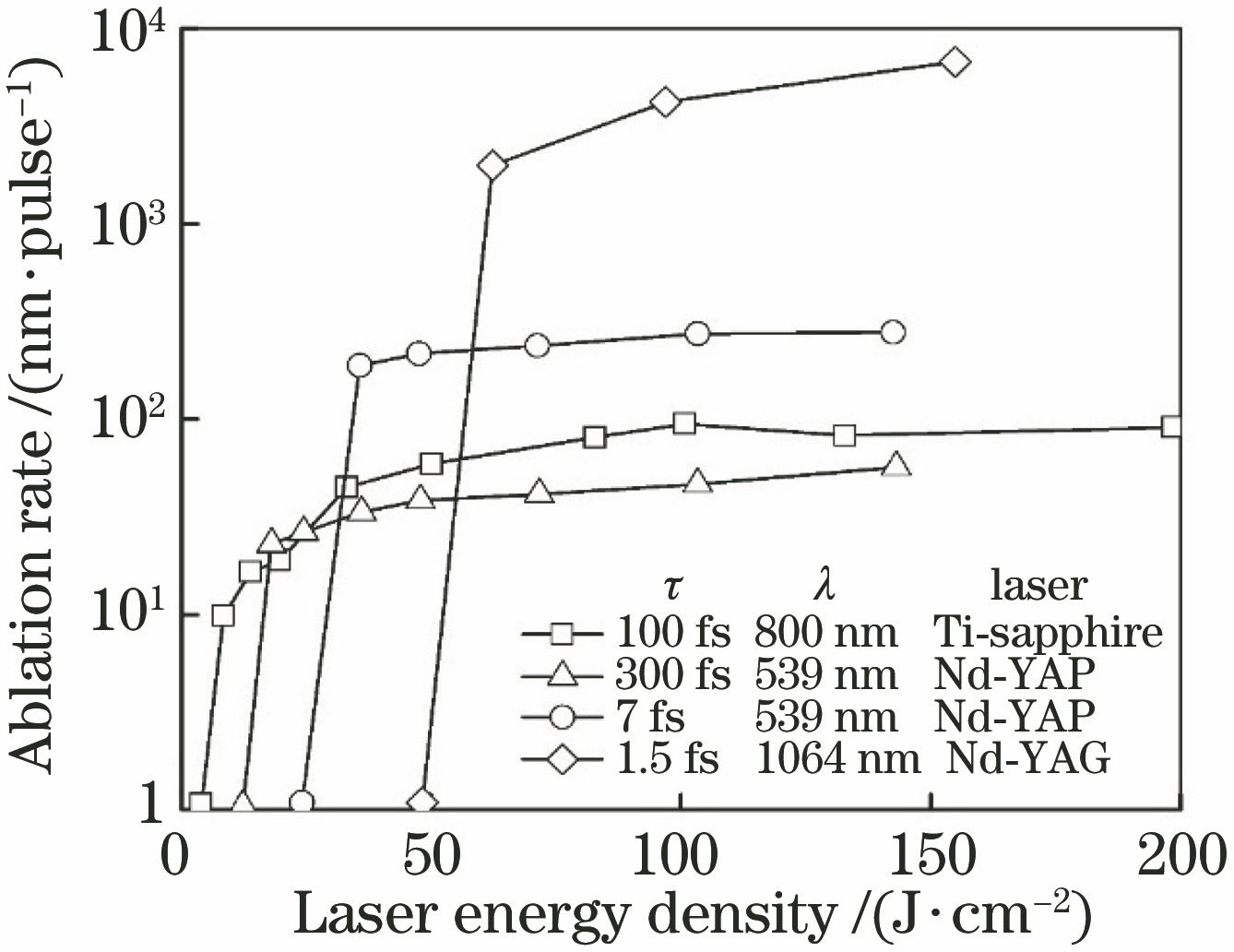
图 5. 不同脉宽下金刚石烧蚀率与激光能量密度的关系曲线
Fig. 5. Functional relationship between ablation rate of diamond and laser energy density under different pulse durations
超硬材料作为一种绝缘/半导体材料,导带中没有足够的自由载流子,且具有非常大的带隙宽度,其光学吸收并非直接由自由电子引起,而是首先形成电子-空穴对,共价键中被束缚的价电子获得足够的累积能量后跃迁到导带成为自由电子。在长脉冲激光作用下,自由电子吸收激光能量并将晶格加热至临界温度,该过程电子对能量的吸收是线性的,对晶格的加热是均衡的,但当光子能量不足以克服超硬材料极高的带隙能量时,单纯的线性吸收无法实现对材料的刻蚀;而在超短脉冲飞秒激光作用下,由于激光能量在极短的时间间隔内作用到焦点半径仅为微米量级的区域内,其激光强度可达1015 W/cm2以上,通常将此量级的强场作用中的物理现象称为非微扰现象,非微扰过程一般发生在激光强度大于1012 W/cm2之后,此时电子受到的激光电场作用力已经可以与原子核对电子的库仑吸引力相比拟,将激光场视为微小扰动的高阶微扰论不再适用[35]。对波长为1024 nm的激光而言,
式中:
![非线性吸收与雪崩电离机制示意图[36]](/richHtml/lop/2019/56/19/190003/img_6.jpg)
图 6. 非线性吸收与雪崩电离机制示意图[36]
Fig. 6. Schematics of non-linear absorption and avalanche ionization mechanism[36]
哈尔滨工业大学的郭斌团队[25]采用Keldysh参数来界定不同激光能量密度条件下的电离状态。Keldysh参数的计算公式为
式中:
![飞秒激光功率对数与单晶金刚石表面烧蚀点直径平方的拟合曲线[25]](/richHtml/lop/2019/56/19/190003/img_7.jpg)
图 7. 飞秒激光功率对数与单晶金刚石表面烧蚀点直径平方的拟合曲线[25]
Fig. 7. Fitting curve between logarithmic laser power and square of dimple diameter machined by femtosecond laser on SC diamond[25]
两种机制在激光功率为80 mW处开始过渡,对应的功率的对数为4.38。随着激光功率由10 mW增大至260 mW,烧蚀直径由18.5 μm增加至71.9 μm,在这一过程中,
此外,当激光束从光学低密度介质传输到高密度介质时,激光会在进入界面时发生180°的相位偏移,但在激光束出射面没有发生相移。同时,入射激光作用到靶材表面产生热电子,这些热电子穿透材料到达出射面并形成独立的静电场,其电场强度
式中:
由(7)式可知,对于金刚石及立方氮化硼这类折射率大于1的高透光材料,利用飞秒激光对其进行体内加工时,激光出射面(背表面)比激光入射面(前表面)获得的激光能量更高,这为超硬材料的飞秒激光加工提供了一种新思路:将激光焦点首先聚焦于靶材背表面,焦点相对于靶材自下而上实现体内微通道的刻蚀成型[40-41]。该方法不仅有利于碎屑的直接排出,还可减小裂纹等缺陷对靶材关键表面的不良影响,这是因为自下而上微孔刻蚀完成后前表面的烧蚀影响(如裂纹等)几乎不可见。因为激光作用造成的局部损伤位置可有效吸收入射脉冲能量,从而诱发等离子体刻蚀[42],所以激光的有效作用范围及热渗透程度是影响材料刻蚀质量的关键因素,飞秒激光的有效作用范围即激光烧蚀体(LAV)的作用范围(-
式中:
式中:
2.3 飞秒激光加工超硬材料的方法
超硬材料的飞秒激光加工最常见的方法是激光直写技术,通过控制激光束或靶材沿

图 9. 在不同激光脉冲能量、重复扫描次数、聚焦物镜倍率下加工得到的金刚石的侧面扫描电镜图
Fig. 9. SEM photographs of polycrystalline diamond side profiles processed at different pulse energies, scanning numbers, and focusing objective magnification
虽然激光直写技术具有装置简单、线加工效率高等特点,但飞秒激光直写技术在加工超硬材料过程中也存在诸多不足。首先,飞秒激光直写加工作为一种激光刻蚀技术,较高的激光功率会使刻蚀区域周围质量受到一定的影响,导致刻蚀区域周围的质量不可控,而较低的激光功率则会大大降低加工效率,尤其是在体加工中这一缺陷尤为突出。上述问题的解决方案通常是采用合适功率的飞秒激光辐照靶材表面继而对改性区域进行后处理刻蚀,从而避免激光能量过大影响刻蚀点周围的形貌。后处理方法又包含湿法刻蚀[51-52]和干法刻蚀[40,53]。此外,通过改进飞秒激光直写加工系统也可实现飞秒激光高精度、高效率的加工目的。例如,吉林大学构建了一种由大范围水平位移平台和高速旋转台组成的极坐标系飞秒激光直写平台,该平台有效解决了传统扫描加工在加工面积、加工精度和加工效率之间的矛盾[54]。近年来也有在液体环境中进行飞秒激光加工的初步探索,其原理是液体环境有助于提升冷却效率,减少碎屑残留以及改变激光熔覆层反冲压力,最终改善激光诱导纳米结构[55]。其次,作为一种逐点加工方法,激光焦点在靶材表面或内部从左至右自上而下逐行完成扫描刻蚀,最终实现目标结构,其加工能力会随着越来越复杂的材料成形要求而受到严重制约,例如当加工复杂轮廓表面时,利用激光直写技术需要激光束与靶材配合移动或不断地调整彼此的相对位置,从而大大增加了加工的复杂程度和加工时间,加工精度也难以保障。最后,由于飞秒激光与靶材作用过程的高度非线性,飞秒激光加工的空间分辨率对焦点处光强的空间分布非常敏感,需要对飞秒激光进行时域和空域的相干操控,以实现飞秒激光高精度、高效率的加工要求。利用激光束整形技术对激光束进行调制整形能够有效弥补直写加工的局限性,提高飞秒激光加工的分辨率。例如,通过引入衍射光学元件可将激光分束,然后在多焦点、同参数下于靶材表面形成周期性图案[56],但是该方法只能实现各焦点一致的图案加工,对非周期图案或要求各焦点不同步的加工则难以适应。
飞秒激光是一种高斯光束,可利用光寻址空间光调制(OA-SLM)技术对其进行调制以形成具有特定预期形状的光束,这是激光整形技术的另一种经典应用。空间光调制器(SLM)一般分为液晶光阀(LCLV)和数字微镜器件(DMD)两种,液晶光阀可实现对光强及其相位的双重控制,而DMD只允许二进制开/关强度调制。液晶SLM可以修正光束畸变,使激光焦点随着在金刚石内深度的变化而变化,从而实现波阵面的动态调整(动态自适应波阵面),并可减小因金刚石-空气界面折射率失配而引起的聚焦像差[57-58]。通过液晶SLM技术对高斯光束施加适当的空间相位,还可产生加速光束,使其以高度局域化强度分布波瓣形式沿弯曲的弧线传播。加速光束具有自横向加速、无衍射及自愈的优良特性,在传播过程中光场强度的分布轮廓具有较高的稳定性,可实现对靶材一次加工成形曲面,或在靶材表面一次辐照加工出弧形轨迹并保证较高的精度[59]。中国科学技术大学通过在液晶空间光调制器上加载叠加闪耀光栅全息图实现了控制焦点位置的二维扫描加工方法,并通过控制全息图的挖空区域实现了能量的可控[60];进一步地,通过在液晶空间光调制器上加载闪耀光栅和球面波因子的相位全息图,或在同一光路装置中的SLM上循环加载对应于同一张目标图的多张计算全息图,中国科学技术大学首次提出了基于液晶空间光调制器的飞秒激光焦点控制扫描加工和图形化曝光加工双模式加工系统,为飞秒激光双光子聚合加工在二维、三维复杂微纳结构快速加工中的应用提供了新方式[61]。
在仅需调制强度而对激光相位无要求的条件下,DMD是调制飞秒激光束的最优选择。一方面DMD相比液晶光阀成本更低,另一方面在飞秒脉冲下DMD的破坏阈值(约为1 mJ/m2)略高于液晶光阀的破坏阈值(100 μJ/m2~1 mJ/m2),可承受10万脉冲而保持无损工况[62]。在基于可编程图像投影的飞秒激光掩模加工中,通过调整DMD投影镜片的数量,加工精度不再依赖于平台位移,而是依赖于增加投影镜片数量(目的是增加目标图案的像素)后的保真度[63]。同时,这种基于图像投影的平行加工方式无需光束扫描或靶材移动即可一次成形复杂的图案,在10 ms内利用10个飞秒激光脉冲即可实现亚微米级的清晰结构,在编码加密等特殊领域具有广阔的应用前景[64]。
![超硬材料的常见飞秒激光加工方法。(a)激光直写技术[48];(b)加速光束[59];(c)干法刻蚀辅助加工[53];(d)强度掩模投影加工[64];(e)基于SLM技术的飞秒激光双模式加工系统[61]](/richHtml/lop/2019/56/19/190003/img_10.jpg)
图 10. 超硬材料的常见飞秒激光加工方法。(a)激光直写技术[48];(b)加速光束[59];(c)干法刻蚀辅助加工[53];(d)强度掩模投影加工[64];(e)基于SLM技术的飞秒激光双模式加工系统[61]
Fig. 10. Common femtosecond laser processing methods for ultrahard materials. (a) Laser direct writing[48]; (b) accelerated beam[59]; (c) dry etching assistant processing[53]; (d) intensity mask projection processing[64]; (e) femtosecond laser dual-mode rapid fabrication system based on SLM[61]
3 飞秒激光加工超硬材料的研究及应用
3.1 飞秒激光加工金刚石材料
金刚石材料具有高硬度、低热膨胀系数等诸多优良的特性,对紫外及可见光谱、红外光谱、微波谱是透明的,同时它还是极好的绝缘体(击穿电压高达107 V/cm),可作为高质量的空穴型半导体(掺硼)。此外,金刚石具有独特的辐射稳定性、化学惰性、生物相容性和许多其他的重要特征,上述特性使得金刚石材料具有极广泛的应用[24,65]。随着人造金刚石技术[高温高压法(HPHT)人造金刚石及化学气相沉积(CVD)金刚石]的不断发展,金刚石材料的获取变得越来越容易,且价格低廉,这为金刚石刀具、金刚石电子元件的应用发展提供了良好的支撑。然而金刚石的特性也使得对它的加工尤其是精密加工、微纳加工变得十分困难,如对金刚石材料的切割、钻孔、抛光及表面结构化等。用普通刀具直接对超硬材料进行加工会使刀具产生严重磨损,加工精度也无法得到高质量的保证,且加工效率不高。因此研究人员针对高效率、高分辨率加工及标记技术产生了浓厚兴趣,其中激光加工就是许多方法中的一种。由于微秒或纳秒激光加工所显现出的热影响区较大的问题[66-67],飞秒加工成为近年来的研究热点,利用飞秒脉冲激光加工可将加工精度扩展到亚微米甚至纳米尺度[68]。在金刚石材料的加工方面,飞秒激光可在金刚石表面诱导出尺寸低至50 nm的纳米结构[30]。
激光加工金刚石材料的一大特征是材料的气化或化学刻蚀并非直接发生,而是通过激光诱导金刚石转变成石墨相进而对石墨相气化或刻蚀,最终实现对金刚石的加工。金刚石具有高透光率、高热导率以及化学惰性等特性,而石墨相却是不透明的,且其导热性相对较差,化学性质也相对活泼,因此,这一碳相转变对于金刚石材料的加工是极其重要的。相比于长脉宽激光,飞秒激光加工金刚石可直接诱发电子雪崩使金刚石中的碳原子电离,等离子体吸收激光能量进而将晶格加热至发生石墨化的临界温度
哈尔滨工业大学通过实验确定了金刚石在低能量密度和高能量密度飞秒激光下的烧蚀阈值,其中高低能量密度下拟合到的烧蚀阈值分别为2.35 J/cm2和0.29 J/cm2,对应的激光功率分别为55.79 mW和6.92 mW[25]。哈尔滨工业大学还通过飞秒激光点刻蚀及线刻蚀实验,得出了飞秒激光在低能量密度条件下刻蚀单晶金刚石可获得较好的表面形貌且无明显裂纹这一结论,实验结果如

图 11. 不同功率下飞秒激光点刻蚀及线刻蚀区域的微观形貌。(a)~(f)点刻蚀;(g)~(i)线刻蚀
Fig. 11. Micro-morphologies of ablated area obtained by femtosecond laser spot etching and line etching at different laser powers. (a)-(f) Spo tetching; (g)-(i) line etching
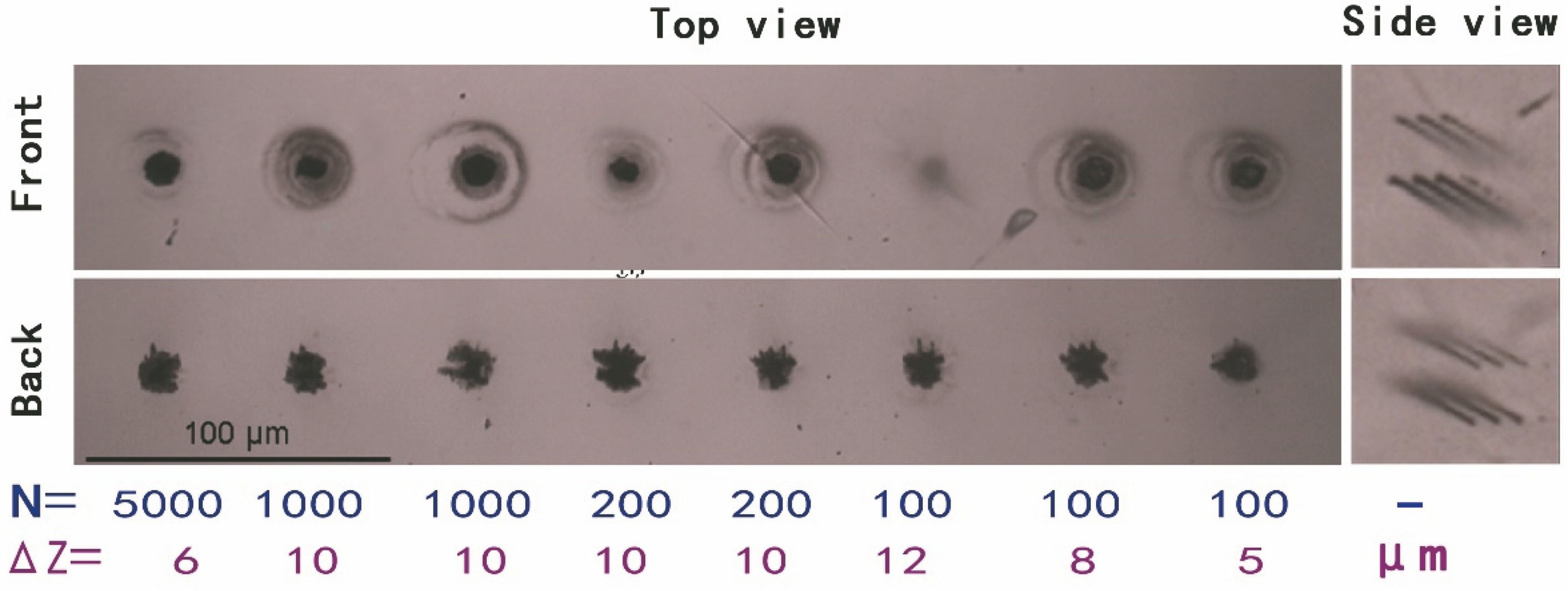
图 12. 激光能量为4 μJ的飞秒激光加工石墨通道阵列,N是脉冲数,ΔZ是步长;侧视低倍率光学显微照片显示了通过块体的石墨化通道的连续性
Fig. 12. Graphite channel arrays fabricated by femtosecond laser with energy of 4 μJ. N is number of pulses; Z is step length; side-view low-power optical micrographs illustrate continuity of graphitization channels through bulk diamond
日本庆应义塾大学的Ogawa等[46]利用飞秒激光加工出了无黏结剂的多晶金刚石(BLPCD)微铣刀,刀具的成型过程见

图 13. 飞秒激光直写加工的应用。(a) BLPCD微铣刀的加工过程,从左至右:BLPCD毛坯,FSPL球头成型,BLPCD微铣刀成品;(b) SC金刚石平面折射透镜的SEM照片
Fig. 13. Applications of femtosecond laser direct writing. (a) Processing process of BLPCD micromilling tool, from left to right: BLPCD blank, FSPL ball forming, finished BLPCD micromilling tool; (b) SEM photograph of SC diamond plane refractive lens
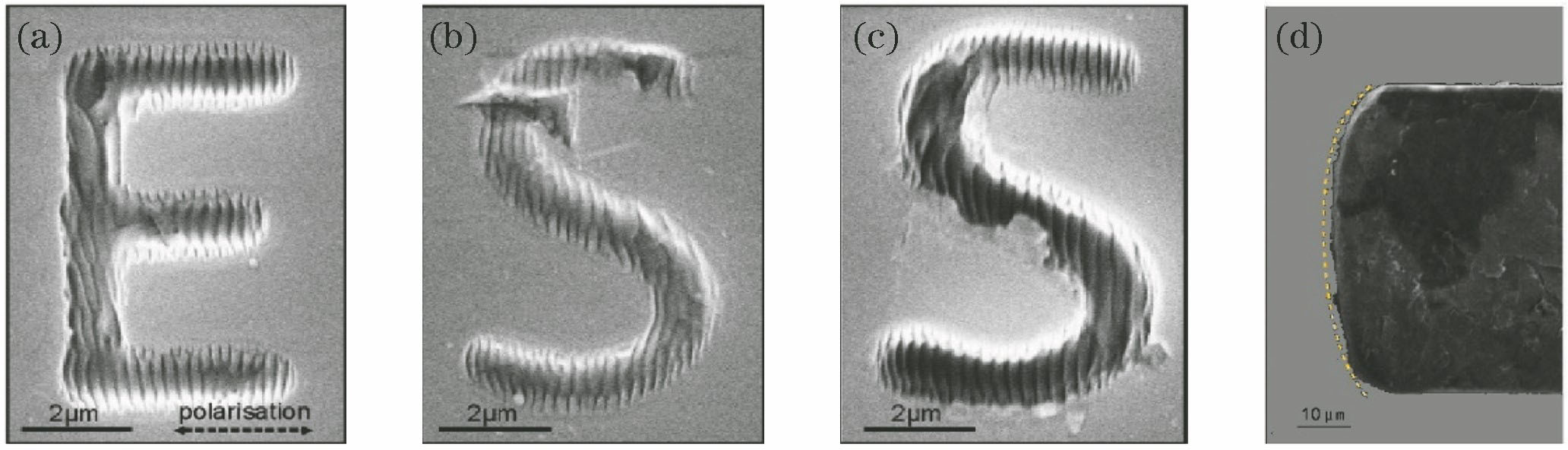
图 14. SLM技术的应用。 (a)、 (b)多晶金刚石表面10个脉冲加工字母,虚线双箭头代表激光偏振方向;(c)多晶金刚石表面50个脉冲加工的字母;(d)飞秒激光加速光束加工出的凸面SC金刚石边缘的SEM照片
Fig. 14. Applications of SLM technologies. (a)(b) Letters processed by 10 pulses on surface of polycrystalline diamond, with dotted double arrows representing direction of laser polarization; (c) letter “S” processed by 50 pulses on surface of polycrystalline diamond; (d) SEM photograph of convex SC diamond edges processed by femtosecond laser acceleration beam
金刚石除了用作磨具、微型刀具或电子元器件材料外,另外一种广泛的用途是作为保护涂层。金刚石薄膜分为单晶、多晶和非晶态材料,单晶和多晶金刚石材料常常是在高温下形成的。类金刚石碳(DLC)是在常温下形成的一种亚稳态的非晶态材料,可分为含氢类金刚石膜(a-C∶H)和不含氢类金刚石膜(a-C)。一般a-C的sp3键含量高于a-C∶H,所以具有更高的硬度。当a-C中sp3键的含量达到70%以上时,即所谓的非晶四面体碳(ta-C),因为其结构主要以sp3键合[72-73],所以拥有与金刚石相近的属性,例如高硬度、良好的摩擦学性能以及化学惰性。同时,因为DLC制备技术比金刚石制备技术更简便,成本也更低,所以DLC被广泛应用于工业领域[73-74]。然而,也正是由于其超高的硬度使得传统的加工方法难以实现对DLC的精密加工。应用飞秒激光加工DLC的研究主要集中在薄膜的表面改性上。薄膜改性的原理是通过调整激光偏振态、扫描速度、能量密度等参数在DLC表面诱导出周期性微纳结构,进而改善材料表面的摩擦特性[75-79]。
3.2 飞秒激光加工立方氮化硼
虽然金刚石刀具具有很高的硬度及良好的切削性能,但其易解理、硬度各向异性和化学稳定性差的特点使其在加工硬度较高的材料时极易造成过度磨损,尤其是加工黑色金属时,由于金刚石与铁极易发生化学反应,刀具寿命严重缩短。通常认为金刚石刀具的磨损主要是由刀-屑接触界面的扩散、氧化、石墨化及碳化物的形成引起的。相应的解决方法主要有:1)振动辅助加工或超间歇切削,以减少刀具-工件连续接触的时间;2)适当的冷却液能有效地降低刀具的磨损和切削力;3)对工件进行热化学表面处理,即通过改变材料亚表层的化学成分,在一定程度上抑制刀具与工件之间的化学反应。上述方法无一例外均会增大切削加工的复杂程度。
立方氮化硼(CBN)的硬度、热导率仅次于金刚石,但它的化学稳定性及热稳定性优于金刚石。特别地,高温高压下由洋葱结构氮化硼前驱体制备的无掺杂纳米孪晶立方氮化硼(nt-CBN)具有由致密的片状纳米颗粒组成的微观结构(平均厚度为4 nm)[80],独特的纳米孪晶微结构赋予了nt-CBN高硬度、高耐磨性以及优良的断裂韧性以及热稳定性等一系列特性。这些特性使CBN刀具成为替代金刚石切削淬火钢、铸铁、黑色粉末金属和耐热合金等材料的理想刀具。近年来,聚晶立方氮化硼(pCBN)和无掺杂纳米孪晶立方氮化硼(nt-CBN)应用于超精密加工的研究屡见报道[80-81]。但是,目前国内外对飞秒激光加工CBN的材料去除机理的研究相对较少,燕山大学及哈尔滨工业大学联合团队的最新研究[82]表明:当飞秒激光由低功率向高功率过渡加工时,对nt-CBN材料的定点刻蚀存在由弱烧蚀至强烧蚀作用的突变。在低功率条件下,飞秒激光点刻蚀nt-CBN的主要机制为弱烧蚀,具体又可分为两个阶段:1)在刻蚀初期,材料去除机制主要为快速热气化,在累积效应的作用下,表层材料首先被去除;2)随着刻蚀直径的增大,激光能量密度逐渐减小至不足以实现材料的快速热气化,此后的去除机理开始向快速熔化转变,在材料气化与熔化的双重作用下,孔的内壁逐渐形成纳米驼峰结构,如
![低功率下nt-CBN材料的飞秒激光点刻蚀去除机理[82]](/richHtml/lop/2019/56/19/190003/img_15.jpg)
图 15. 低功率下nt-CBN材料的飞秒激光点刻蚀去除机理[82]
Fig. 15. Material removal mechanism of nt-CBN by femtosecond laser spot etching at low power[82]
当飞秒激光输出功率达到一定值时,材料的去除机制会突变为强烧蚀,此时烧蚀主要为快速热气化与相爆炸的协同作用,驼峰状结构开始消失,取而代之的是爆裂状结构;进一步增大输出功率则会出现典型的亚波长LIPSS。此外,燕山大学及哈尔滨工业大学联合团队研究对比了基于光束扫描的动态烧蚀过程与定点刻蚀对材料的破坏机制,发现动态烧蚀过程中强、弱烧蚀的转变可在较低功率下发生,说明与静态刻蚀相比,扫描刻蚀更易实现对材料的连续破坏。此外,他们还采用上文提到的
在CBN材料的飞秒激光加工应用方面,主要围绕微刀具成型和刀具表面处理两个方面进行。燕山大学研究团队利用飞秒激光轮廓加工技术及后续的离子束精细研磨技术成功制备出了用于加工淬硬钢的nt-CBN微刀具(
大阪大学的Voevodin等[83-85]从2009年起就开始研发飞秒激光诱导的“变色龙”表面CBN刀具,以应对极软/极硬材料以及高速切削等切削工况[86-89],并成功研发出可抗切屑黏结,抗凹坑磨损、侧面磨损,并能适应干湿摩擦工况的表面结构化刀具。其可行性原理主要包含:1)表面微纳结构可作为固体润滑剂实现切削界面的自润滑[90-91];2)飞秒激光诱导的微纳结构可在毛细作用下促进切削液充分渗透进切削界面,改变刀具表面对切削液的浸润性[92-93];3)黏着滑动接触下的摩擦力可表示为
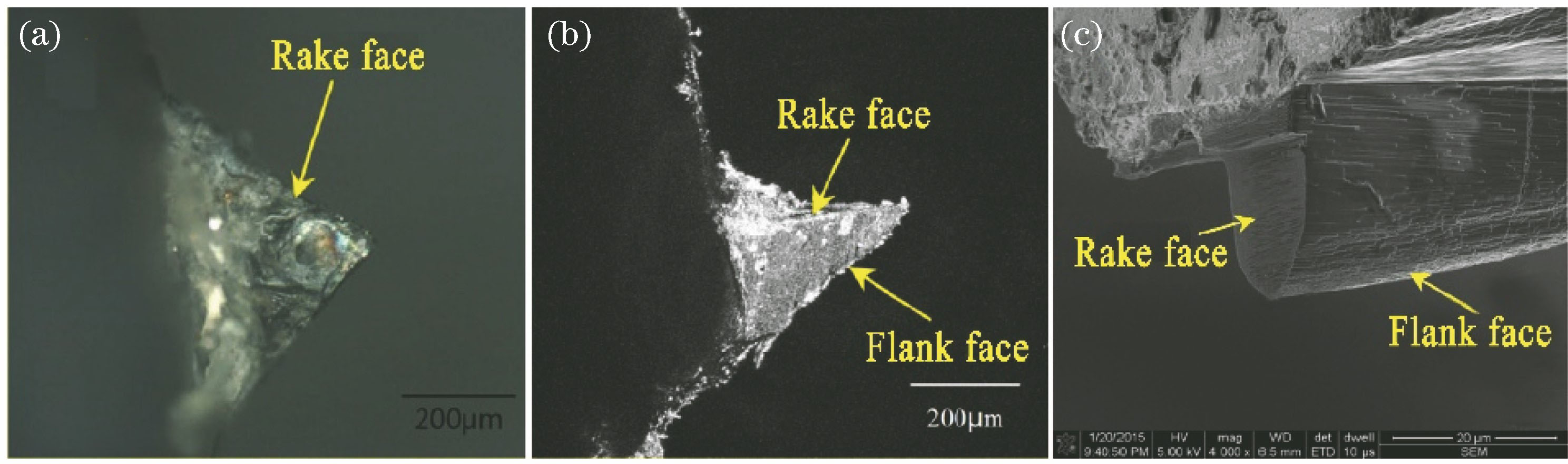
图 16. nt-CBN刀具。 (a)、(b)飞秒激光加工的nt-CBN 微刀具毛坯;(c)聚焦离子束研磨后nt-CBN微刀具成品
Fig. 16. nt-CBN tool. (a)(b) Blanks of nt-CBN micro-tool processed by femtosecond laser; (c) finished nt-CBN micro-tool after focused ion beam grinding
刀具在加工铝合金材料过程中,由于铝合金材料的低熔点、高延展性等特点,产生的切屑极易黏附在刀具切削刃上,进而诱发刀具损坏。虽然切削液辅助切削能够在一定程度上降低刀具的磨损,但是在深孔钻削、磨削以及攻丝等特殊加工环境下,切削液难以到达有效切削位置并发挥作用。为了解决上述问题,Sugihara等[86]利用飞秒激光微加工技术开发了三种表面微织构CBN刀具:微沟槽平行于主切削刃的刀具、微沟槽垂直于主切削刃的道具以及带状微纳纹理刀具。初步的切削实验证明:当且仅当在湿加工条件下,刀具表面微织构才能起到显著的抗切屑黏结作用,且带状微纳纹理在改善切削摩擦性能方面的效果最为显著;在干加工条件下,由于产生的切屑过大(150 μm×150 μm),CBN刀具表面的微织构反而会强化切屑的黏附效应,实验结果见
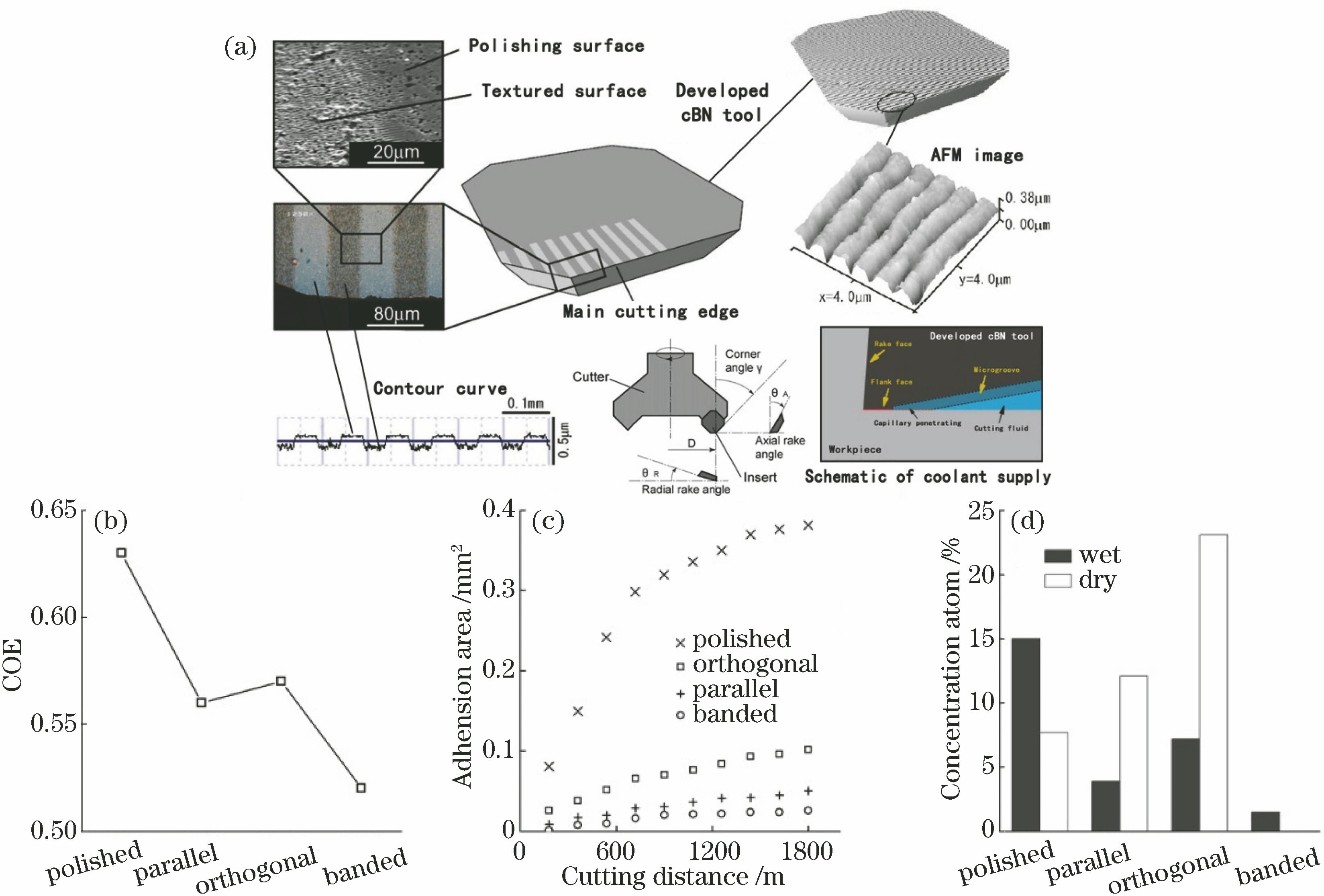
图 17. 飞秒激光诱导表面微织构CBN刀具表面微观形貌及不同刀具在不同切削条件(干加工/湿加工)下的切削实验结果分析。(a)表面微观形貌;(b)不同织构(原始抛光表面、平行微织构、交叉微织构和带状微织构)刀具的摩擦因数;(c)不同织构刀具切削长度与黏结面积的关系;(d)不同织构刀具在干/湿工况下刀具表面的黏结浓度
Fig. 17. Surface micro-morphologies of CBN tool fabricated by femtosecond laser and cutting experimental results of different tools under different cutting conditions (dry/wet processing). (a) Surface micro-morphologies; (b) comparison of friction coefficients of polished surface, parallel, orthogonal, and banded micro-textured tools; (c) relationship between cutting length and adhension area of different micro-textured tools; (d) atom concentration of targets on surface of different micro-textured tools
进一步,通过调整飞秒激光参数研究不同CBN刀具表面带状微结构的方向及凹凸比对切削性能的影响,Sugihara等[87]成功解决了干加工条件下微织构刀具黏结切屑的问题,并得出了在CBN刀具表面形成平行于主切削刃、凹凸面宽度比为50 μm∶20 μm的带状微条纹可使CBN刀具抗黏结性达到最佳效果的结论,微织构刀具表面黏结程度实验结果如
![微织构刀具表面黏结程度的实验结果[87]。(a)不同参数下CBN刀具切削实验后前刀面的三维轮廓,白色箭头指示区域为铝合金切削黏结; (b)干摩擦下切削长度增加至1800 m时切屑的变化,蓝色箭头及方框代表普通刀具的加工结果,红色箭头及方框代表最优方案的加工结果](/richHtml/lop/2019/56/19/190003/img_18.jpg)
图 18. 微织构刀具表面黏结程度的实验结果[87]。(a)不同参数下CBN刀具切削实验后前刀面的三维轮廓,白色箭头指示区域为铝合金切削黏结; (b)干摩擦下切削长度增加至1800 m时切屑的变化,蓝色箭头及方框代表普通刀具的加工结果,红色箭头及方框代表最优方案的加工结果
Fig. 18. Experimental results of surface adhesion degree of micro-textured tools[87]. (a) Three-dimensional profile of rake face of CBN tools after cutting experiment under different parameters, where white arrow indicates cutting adhesion area of aluminum alloy; (b) changes of cutting chips when cutting length increases to 1800 m under dry friction. Processing results marked by blue arrow and box attribute to traditional tool, while red arrow and box marked results are processed by optimum tool
虽然CBN刀具在切削铁基合金材料方面比金刚石刀具更具优势,但CBN刀具的制作成本是普通硬质合金刀具的10倍以上,高昂的成本依然限制着CBN刀具的工业应用。尤其是在高速切削加工时,平整的后刀面在与工件接触时会阻碍切削液渗透进加工界面,进而导致刀具快速磨损,造成严重浪费。为了解决上述问题,运用飞秒激光加工技术加工或对刀具表面进行后处理是行之有效的方法。以100~500 m/min的切削速度高速切削718铬镍铁合金的实验结果见
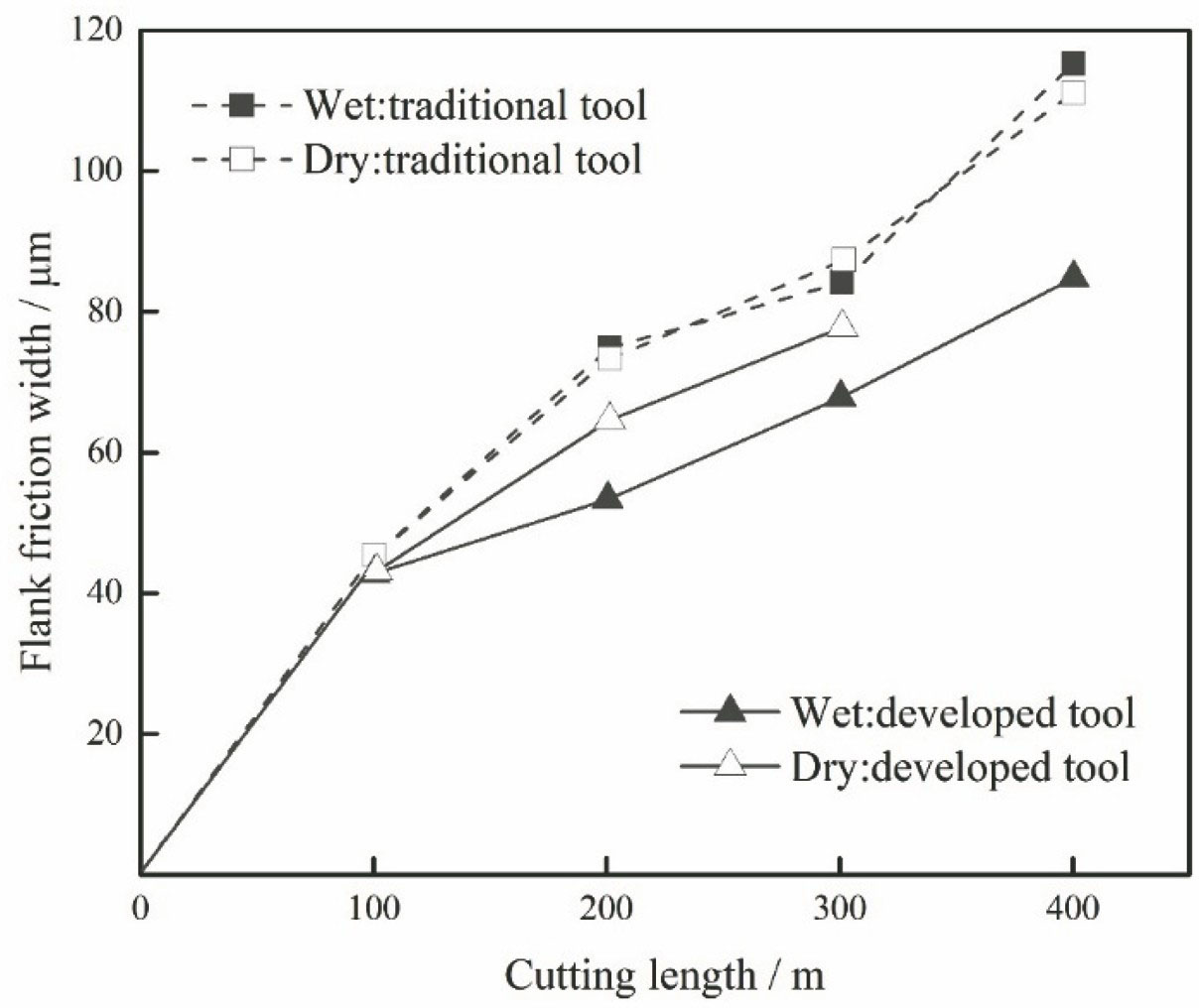
图 19. 普通CBN刀具和织构化CBN刀具在干湿两种工况下切削长度和后刀面摩擦宽度的关系图
Fig. 19. Relationship between cutting length and flank friction width of traditional CBN tools and micro-textured CBN tools under dry and wet conditions
4 结束语
飞秒激光独特的优异特性使得飞秒激光加工技术在超精密特种加工领域越来越受到青睐,其产值不断攀升,应用前景广阔。近年来,广大研究者对飞秒激光加工超硬材料的研究越来越深入,研究成果也已逐步走出实验室并实现工业化应用。另外,随着超硬材料人工合成技术的不断成熟和发展,以及各类新型复合超硬材料的陆续问世,超硬材料的生产工艺和性能都已实现了巨大突破,所带来的高性能和超长的工作寿命也很好地弥补了成本上的劣势,应用价值不可估量。飞秒激光加工技术自身所具备诸多独特优势,应用于超硬材料刀具的加工、制备及后处理时,会使难加工材料的高精度、高质量的加工成型更加快速高效,从而将超精密加工领域推向更深的层次。将飞秒激光加工技术应用于超硬光电子元器件的微纳加工,其研究成果又会反哺飞秒激光技术的发展和突破。总而言之,飞秒激光应用于超硬材料的加工应用前景非常广阔。通过总结近几年飞秒激光技术在超硬材料加工方面的研究和应用,亦可窥见该领域发展存在亟待解决的技术难点及相关的解决思路和发展趋势。
第一,虽然诸如掩模加工以及干涉图案加工等各类辅助加工方法已被成功应用于超硬材料的飞秒激光加工应用中,有效地弥补了飞秒激光传统直写加工技术在应对复杂结构加工时存在的不足,但值得注意的是,相比于普通材料的飞秒激光加工方法,可供应用于超硬材料加工的飞秒激光技术依然有限,且这些方法仍存在各种问题。例如近年来研究较多的飞秒激光SLM调制技术,由于SLM存在局部区域对入射光的调制失效缺陷(死区),当入射激光功率过低时,光栅作用会导致输出功率分布不均匀,而入射激光功率过高又会产生过曝,最终导致加工精度下降。因此不断改善光束整形技术或扩展其他材料领域的飞秒激光加工技术至超硬材料,甚至发展新型的飞秒激光加工工艺,是飞秒激光加工走向更高精度、更高效率的超精密加工应用的一个突破口。
第二,随着超硬材料突飞猛进的发展,各类新型复合超硬材料陆续问世,且在各领域应用中表现出良好的性能,人工可合成的超硬材料体积也越来越大。由于超硬材料自身独特的性质,目前飞秒激光对它的加工多为“微型”加工,探索各类新型激光介质,发展更为先进的激光锁模技术、脉冲啁啾放大技术及其他光学元件,使飞秒激光由超快走向超强,故实现对大体积超硬材料的精密加工是十分必要。此外,飞秒激光器本身价格昂贵,发展高功率、小型便携式飞秒激光系统以降低飞秒激光加工成本也是一个较有价值的研究方向。
第三,飞秒激光与超硬材料相互作用机理的研究理论尚不完整。在飞秒激光-金刚石相互作用机制的研究方面,国内外均做了较多的研究报道,但对于其内部各种非线性效应的竞争关系以及不同气液加工环境乃至靶材晶向对飞秒激光加工效果影响方面的研究还处于探索阶段,尚无明确的理论验证。虽然很多研究者提出了自己的飞秒激光加工预测模型,但往往局限在单一的实验环境下,没有建立起较为可靠的基于飞秒激光加工系统的仿真模型;对飞秒激光加工CBN的研究,目前我国处于领先地位,但仍有许多问题需要解决,如飞秒激光加工CBN过程中强弱烧蚀机制突变临界点的确定及有效控制、飞秒强激光场与CBN材料内部原子层面的作用机制、飞秒激光诱导的相变等问题需要广大科研工作者的进一步探索。
第四,除了飞秒激光加工手段的改进,对加工对象的预处理方法的研发或新型复合材料的拓展也是促进飞秒激光加工超硬材料技术发展的可行途径。常见的干法或湿法刻蚀预处理方法的运用已较为成熟,并可适用于各种不同的加工需求。通过探索适用性更强、效率更高的超硬材料预处理方法,研究超硬材料的加工特性,并将其应用于飞秒激光加工中以提高加工的精度和效率,对于进一步推进飞秒激光加工技术的应用具有深远意义。
[1] Li S L, Huang Z P, Ye Y K, et al. Femtosecond laser inscribed cladding waveguide lasers in Nd∶LiYF4 crystals[J]. Optics & Laser Technology, 2018, 102: 247-253.
[2] 陈燕青, 高炳攀, 林炎章, 等. 飞秒激光微加工制备金属线栅太赫兹偏振片[J]. 中国激光, 2018, 45(8): 0802005.
[3] Xu H L, Sun H B. Femtosecond laser 3D fabrication of whispering-gallery-mode microcavities[J]. Science China Physics, Mechanics & Astronomy, 2015, 58(11): 114202.
[4] Balbus G H, Echlin M P, Grigorian C M, et al. Femtosecond laser rejuvenation of nanocrystalline metals[J]. Acta Materialia, 2018, 156: 183-195.
[5] Zhang R, Huang C Z, Wang J, et al. Micromachining of 4H-SiC using femtosecond laser[J]. Ceramics International, 2018, 44(15): 17775-17783.
[6] Kawashima T, Sano T, Hirose A, et al. Femtosecond laser peening of friction stir welded 7075-T73 aluminum alloys[J]. Journal of Materials Processing Technology, 2018, 262: 111-122.
[7] 张学谦, 邢松龄, 刘磊, 等. 带热障涂层的高温合金飞秒激光旋切打孔[J]. 中国激光, 2017, 44(1): 0102013.
[8] 丁腾, 王雪辉, 王关德, 等. 高重频飞秒激光焊接石英玻璃[J]. 中国激光, 2018, 45(7): 0701007.
[9] Wang M L, Yang L J, Zhang S, et al. Experimental investigation on the spiral trepanning of K24 superalloy with femtosecond laser[J]. Optics & Laser Technology, 2018, 101: 284-290.
[10] OstendorfA,[\s]{1}KorteF,[\s]{1}KamlageG,[\s]{1}et[\s]{1}al.[\s]{1}3D[\s]{1}laser[\s]{1}microfabrication:[\s]{1}principles[\s]{1}and[\s]{1}applications[M].[\s]{1}Weinheim:[\s]{1}Wiley-VCH[\s]{1}Verlag[\s]{1}GmbH[\s]{1}&[\s]{1}Co.[\s]{1}KGaA,[\s]{1}2006.[\s]{1}
[11] 胡文锦, 许兵, 史杨, 等. 飞秒激光制备高敏感度流量传感器[J]. 中国激光, 2018, 45(9): 0902001.
[12] 龙婧, 熊伟, 刘莹, 等. 基于飞秒激光直写的三维高定向碳纳米管组装[J]. 中国激光, 2017, 44(1): 0102003.
[13] Sato Y, Tsukamoto M, Shinonaga T, et al. Femtosecond laser-induced periodic nanostructure creation on PET surface for controlling of cell spreading[J]. Applied Physics A, 2016, 122(3): 184-186.
[14] Baumgart J, Humbert L, Boulais É, et al. Off-resonance plasmonic enhanced femtosecond laser optoporation and transfection of cancer cells[J]. Biomaterials, 2012, 33(7): 2345-2350.
[15] Xu H L, Cheng Y, Chin S L, et al. Femtosecond laser ionization and fragmentation of molecules for environmental sensing[J]. Laser & Photonics Reviews, 2015, 9(3): 275-293.
[16] Gamaly E G, Rode A V, Luther-Davies B, et al. Ablation of solids by femtosecond lasers: ablation mechanism and ablation thresholds for metals and dielectrics[J]. Physics of Plasmas, 2002, 9(3): 949-957.
[17] Bonse J, Krüger J. Probing the heat affected zone by chemical modifications in femtosecond pulse laser ablation of titanium nitride films in air[J]. Journal of Applied Physics, 2010, 107(5): 054902.
[18] RiedelR,[\s]{1}WiehlL,[\s]{1}ZerrA,[\s]{1}et[\s]{1}al.[\s]{1}Superhard[\s]{1}materials[M][\s]{1}∥[\s]{1}Dronskowski[\s]{1}R,[\s]{1}Kikkawa[\s]{1}S,[\s]{1}Stein[\s]{1}A.[\s]{1}Handbook[\s]{1}of[\s]{1}solid[\s]{1}state[\s]{1}chemistry.[\s]{1}Weinhein:[\s]{1}Wiley-VCH[\s]{1}Verlag[\s]{1}GmbH[\s]{1}&[\s]{1}Co.[\s]{1}KGaA,[\s]{1}2017:[\s]{1}175-[\s]{1}200.[\s]{1}
[19] Phaal C. Surface studies of diamond[J]. Industrial Diamond Review, 1965: 486-489.
[20] Sawaoka A. Boron nitride: structural changes by shock compression and preparation of superhard compacts by very high pressure sintering[J]. American Ceramic Society Bulletin, 1983, 62(12): 1379-1383.
[21] Tan D Z, Sharafudeen K N, Yue Y Z, et al. Femtosecond laser induced phenomena in transparent solid materials: fundamentals and applications[J]. Progress in Materials Science, 2016, 76: 154-228.
[22] SugiokaK,[\s]{1}MeunierM,[\s]{1}PiquéA.[\s]{1}Laser[\s]{1}precision[\s]{1}microfabrication[M].[\s]{1}Berlin:[\s]{1}Springer,[\s]{1}2010.[\s]{1}
[23] Mikhail[\s]{1}R.[\s]{1}Selecting[\s]{1}industrial[\s]{1}laser[\s]{1}optics[J/OL].[\s]{1}Vision[\s]{1}Spectra,[\s]{1}2014-07[2019-02-15].[\s]{1}https:∥www.photonics.com/Articles/Selecting_Industrial_Laser_Optics/a55750.
[24] Konov V I. Laser in micro and nanoprocessing of diamond materials[J]. Laser & Photonics Reviews, 2012, 6(6): 739-766.
[25] Wu M T, Guo B, Zhao Q L, et al. The influence of the ionization regime on femtosecond laser beam machining mono-crystalline diamond[J]. Optics & Laser Technology, 2018, 106: 34-39.
[26] Liu N. Processing of back surface of Si wafers with a pulsed Nd∶YAG laser[J]. Journal of Laser Micro/ Nanoengineering, 2016, 11(2): 232-238.
[27] 李智华, 范敬钦, 李普年, 等. 能量累积效应对飞秒激光诱导表面周期结构的影响[J]. 中国激光, 2010, 37(1): 68-73.
[28] Liang J C, Liu W D, Li Y, et al. A model to predict the ablation width and calculate the ablation threshold of femtosecond laser[J]. Applied Surface Science, 2018, 456: 482-486.
[29] Nathala C S R, Ajami A, Husinsky W, et al. . Ultrashort laser pulse ablation of copper, silicon and gelatin: effect of the pulse duration on the ablation thresholds and the incubation coefficients[J]. Applied Physics A, 2016, 122: 107.
[30] Forster M, Huber C, Armbruster O, et al. 50-nanometer femtosecond pulse laser induced periodic surface structures on nitrogen-doped diamond[J]. Diamond and Related Materials, 2017, 74: 114-118.
[31] Kononenko V V, Kononenko T V, Pimenov S M, et al. Effect of the pulse duration on graphitisation of diamond during laser ablation[J]. Quantum Electronics, 2005, 35(3): 252-256.
[32] 董志伟, 张伟斌, 郑立威, 等. 利用飞秒激光和纳秒激光脉冲加工金刚石[J]. 红外与激光工程, 2015, 44(3): 893-896.
[33] Wu B Y, Deng L M, Liu P, et al. Effects of picosecond laser repetition rate on ablation of Cr12MoV cold work mold steel[J]. Applied Surface Science, 2017, 409: 403-412.
[34] Park C, Farson D F. Precise machining of disk shapes from thick metal substrates by femtosecond laser ablation[J]. The International Journal of Advanced Manufacturing Technology, 2016, 83: 2049-2056.
[35] 叶地发, 刘杰. 飞秒强激光场中的原子、分子: 非微扰现象研究[J]. 物理, 2009, 38(12): 908-913.
Ye D F, Liu J. Nonperturbative phenomena of atoms and molecules irradiated by ultra-strong femtosecond laser pulses[J]. Physics, 2009, 38(12): 908-913.
[36] KönigK,[\s]{1}OstendorfA.[\s]{1}Optically[\s]{1}induced[\s]{1}nanostructures:[\s]{1}biomedical[\s]{1}and[\s]{1}technical[\s]{1}applications[M].[\s]{1}Berlin,[\s]{1}München,[\s]{1}Boston:[\s]{1}Walter[\s]{1}de[\s]{1}Gruyter[\s]{1}GmbH,[\s]{1}2015:[\s]{1}50-[\s]{1}51.[\s]{1}
[37] Wang J, Wang C H, Liu Y S, et al. Microstructure and chemical bond evolution of diamond-like carbon films machined by femtosecond laser[J]. Applied Surface Science, 2015, 340: 49-55.
[38] Liu X, Du D, Mourou G. Laser ablation and micromachining with ultrashort laser pulses[J]. IEEE Journal of Quantum Electronics, 1997, 33(10): 1706-1716.
[39] HiranoM,[\s]{1}Kawamura[\s]{1}KI,[\s]{1}Hosono[\s]{1}H.[\s]{1}Encoding[\s]{1}of[\s]{1}holographic[\s]{1}grating[\s]{1}and[\s]{1}periodic[\s]{1}nano-structure[\s]{1}by[\s]{1}femtosecond[\s]{1}laser[\s]{1}pulse[J].[\s]{1}Applied[\s]{1}Surface[\s]{1}Science,[\s]{1}2002,[\s]{1}197/198:[\s]{1}688-[\s]{1}698.[\s]{1}
[40] Wulz T, Canfield B K, Davis L M, et al. Pulsed femtosecond-laser machining and deep reactive ion etching of diamond[J]. Diamond and Related Materials, 2017, 74: 108-113.
[41] 梁德志, 王敏, 杜晨林, 等. 飞秒激光背部湿刻石英玻璃微通道的研究[J]. 激光技术, 2017, 41(2): 174-177.
[42] Qin[\s]{1}SJ,[\s]{1}Li[\s]{1}W[\s]{1}J.[\s]{1}Process[\s]{1}characterization[\s]{1}of[\s]{1}fabricating[\s]{1}3D[\s]{1}micro[\s]{1}channel[\s]{1}systems[\s]{1}by[\s]{1}laser-micromachining[J].[\s]{1}Sensors[\s]{1}and[\s]{1}Actuators[\s]{1}A:Physical,[\s]{1}2002,[\s]{1}97/98:[\s]{1}749-[\s]{1}757.[\s]{1}
[43] Chen L, Zhang P, Chen J X, et al. Influence of processing parameters on the structure size of microchannel processed by femtosecond laser[J]. Optics & Laser Technology, 2018, 106: 47-51.
[44] Zhao Q L, Jiang T, Dong Z W, et al. Ablation threshold and material removal mechanisms of SiC processed by femtosecond laser[J]. Journal of Mechanical Engineering, 2010, 46(21): 172-177.
[45] Zhang P, Chen L, Chen J X, et al. Material removal effect of microchannel processing by femtosecond laser[J]. Optics and Lasers in Engineering, 2017, 98: 69-75.
[46] Ogawa Y, Ota M, Nakamoto K, et al. A study on machining of binder-less polycrystalline diamond by femtosecond pulsed laser for fabrication of micro milling tools[J]. CIRP Annals, 2016, 65(1): 245-248.
[47] Chen J Y, Jin T Y, Tian Y J. Development of an ultrahard nanotwinned CBN micro tool for cutting hardened steel[J]. Science China Technological Sciences, 2016, 59(6): 876-881.
[48] Yin J, Chen G Y, Xiong B, et al. Femtosecond pulsed laser fabrication of a novel SCD grinding tool with positive rake angle[J]. Applied Physics A, 2018, 124: 859.
[49] 熊彪, 陈根余, 殷赳, 等. 飞秒激光加工单晶金刚石锥形阵列的试验研究[J]. 应用激光, 2018, 38(2): 270-277.
[50] 黄建衡, 梁国文, 李冀, 等. 飞秒激光制备多晶金刚石微结构阵列[J]. 中国激光, 2017, 44(3): 0302007.
[51] Li G, Feng G Y, Wang S T, et al. Femtosecond laser assisted fabrication of networked semi-occlusive microfluidic channel on fused silica glass surface[J]. Optik, 2017, 140: 953-958.
[52] Wang F, Shan C, Yan J P, et al. Application of femtosecond laser technique in single crystal diamond film separation[J]. Diamond and Related Materials, 2016, 63: 69-74.
[53] Liu X Q, Chen Q D, Guan K M, et al. Dry-etching-assisted femtosecond laser machining[J]. Laser & Photonics Reviews, 2017, 11(3): 1600115.
[54] 姜俊, 刘晋桥, 徐颖, 等. 曲面基底衍射光学元件的激光直写技术[J]. 中国激光, 2017, 44(6): 0602002.
[55] Hoppius[\s]{1}JS,[\s]{1}MaragkakiS,[\s]{1}KanitzA,[\s]{1}et[\s]{1}al.[\s]{1}Optimization[\s]{1}of[\s]{1}femtosecond[\s]{1}laser[\s]{1}processing[\s]{1}in[\s]{1}liquids[J].[\s]{1}Applied[\s]{1}Surface[\s]{1}Science,[\s]{1}2019,[\s]{1}467/468:[\s]{1}255-[\s]{1}260.[\s]{1}
[56] Jia X, Dong L L. Fabrication of complex micro/nanopatterns on semiconductors by the multi-beam interference of femtosecond laser[J]. Physics Procedia, 2014, 56: 1059-1065.
[57] Simmonds R D, Salter P S, Jesacher A, et al. Three dimensional laser microfabrication in diamond using a dual adaptive optics system[J]. Optics Express, 2011, 19(24): 24122-24128.
[58] Murphy S A, Booth M, Li L, et al. Laser processing in 3D diamond detectors[J]. Nuclear Instruments and Methods in Physics Research Section A: Accelerators, Spectrometers, Detectors and Associated Equipment, 2017, 845: 136-138.
[59] Mathis A, Courvoisier F, Froehly L, et al. Micromachining along a curve: femtosecond laser micromachining of curved profiles in diamond and silicon using accelerating beams[J]. Applied Physics Letters, 2012, 101(7): 071110.
[60] 饶生龙, 吴培超, 张晨初, 等. 基于空间光调制器的能量可控飞秒激光加工[J]. 中国激光, 2017, 44(1): 0102008.
[61] 吴培超, 张晨初, 杨亮, 等. 基于空间光调制器的飞秒激光双模式快速加工[J]. 中国激光, 2018, 45(10): 1001005.
[62] O'Keeffe K. Robinson T, Hooker S M. Generation and control of chirped, ultrafast pulse trains[J]. Journal of Optics, 2010, 12(1): 015201.
[63] Mills B, Feinaeugle M, Sones L, et al. Sub-micron-scale femtosecond laser ablation using a digital micromirror device[J]. Journal of Micromechanics and Microengineering, 2013, 23(3): 035005.
[64] Mills B, Heath D J, Feinaeugle M, et al. Laser ablation via programmable image projection for submicron dimension machining in diamond[J]. Journal of Laser Applications, 2014, 26(4): 041501.
[65] Aharonovich I, Greentree A D, Prawer S. Diamond photonics[J]. Nature Photonics, 2011, 5(7): 397-405.
[66] Kononenko T V, Komlenok M S, Pashinin V P, et al. Femtosecond laser microstructuring in the bulk of diamond[J]. Diamond and Related Materials, 2009, 18(2/3): 196-199.
[67] Takayama N, Yan J W. Mechanisms of micro-groove formation on single-crystal diamond by a nanosecond pulsed laser[J]. Journal of Materials Processing Technology, 2017, 243: 299-311.
[68] 乔玲玲, 储蔚, 王哲, 等. 基于整形飞秒激光脉冲的三维微纳制备[J]. 光学学报, 2019, 39(1): 0126012.
[69] Polikarpov M, Snigireva I, Morse J, et al. Large-acceptance diamond planar refractive lenses manufactured by laser cutting[J]. Journal of Synchrotron Radiation, 2015, 22(1): 23-28.
[70] Kononenko T V, Ralchenko V G, Ashkinazi E E, et al. Fabrication of polycrystalline diamond refractive X-ray lens by femtosecond laser processing[J]. Applied Physics A, 2016, 122: 152.
[71] 徐世珍, 宋文亮, 祖小涛. 金刚石表面飞秒激光直写微米石墨线[J]. 实验室研究与探索, 2016, 35(4): 52-54.
Xu S Z, Song W L, Zu X T. Study of graphite line micromachining on diamond surface by femtosecond laser direct writing[J]. Research and Exploration in Laboratory, 2016, 35(4): 52-54.
[72] Robertson J. Amorphous carbon[J]. Advances in Physics, 1986, 35(4): 317-374.
[73] Robertson J. Diamond-like amorphous carbon[J]. Materials Science and Engineering: R: Reports, 2002, 37(4/5/6): 129-281.
[74] Milne W I. Electronic devices from diamond-like carbon[J]. Semiconductor Science and Technology, 2003, 18(3): S81-S85.
[75] Yasumaru N, Miyazaki K, Kiuchi J. Femtosecond-laser-induced nanostructure formed on hard thin films of TiN and DLC[J]. Applied Physics A: Materials Science & Processing, 2003, 76(6): 983-985.
[76] Yasumaru N, Miyazaki K, Kiuchi J. Control of tribological properties of diamond-like carbon films with femtosecond-laser-induced nanostructuring[J]. Applied Surface Science, 2008, 254(8): 2364-2368.
[77] Pimenov S M, Jaeggi B, Neuenschwander B, et al. Femtosecond laser surface texturing of diamond-like nanocomposite films to improve tribological properties in lubricated sliding[J]. Diamond and Related Materials, 2019, 93: 42-49.
[78] Zavedeev E V, Zilova O S, Barinov A D, et al. Femtosecond laser microstructuring of diamond-like nanocomposite films[J]. Diamond and Related Materials, 2017, 74: 45-52.
[79] Nikaido S, Natori T, Saito R, et al. Nanostructure formation on diamond-like carbon films induced with few-cycle laser pulses at low fluence from a Ti∶sapphire laser oscillator[J]. Nanomaterials, 2018, 8(7): 535.
[81] Revel P, Jouini N, Thoquenne G, et al. High precision hard turning of AISI 52100 bearing steel[J]. Precision Engineering, 2016, 43: 24-33.
[82] 靳田野, 陈俊云, 王金虎, 等. 纳米孪晶立方氮化硼的飞秒激光材料去除机理[J]. 机械工程学报, 2019, 55(9): 198-205.
Jin T Y, Chen J Y, Wang J H, et al. Material removal mechanism of nanotwinned cubic boron nitride by femtosecond laser ablation[J]. Journal of Mechanical Engineering, 2019, 55(9): 198-205.
[83] Voevodin A A, Zabinski J S. Supertough wear-resistant coatings with ‘chameleon’ surface adaptation[J]. Thin Solid Films, 2000, 370(1/2): 223-231.
[84] Voevodin A A, Fitz T A, Hu J J, et al. Nanocomposite tribological coatings with “chameleon” surface adaptation[J]. Journal of Vacuum Science & Technology A: Vacuum, Surfaces, and Films, 2002, 20(4): 1434-1444.
[85] Voevodin[\s]{1}AA,[\s]{1}Shtansky[\s]{1}DV,[\s]{1}Levashov[\s]{1}EA,[\s]{1}et[\s]{1}al.[\s]{1}Nanostructured[\s]{1}thin[\s]{1}films[\s]{1}and[\s]{1}nanodispersion[\s]{1}strengthened[\s]{1}coatings[M].[\s]{1}Dordrecht:[\s]{1}Springer,[\s]{1}2004:[\s]{1}1-[\s]{1}8.[\s]{1}
[86] Sugihara T, Enomoto T. Development of a cutting tool with a nano/micro-textured surface: improvement of anti-adhesive effect by considering the texture patterns[J]. Precision Engineering, 2009, 33(4): 425-429.
[87] Sugihara T, Enomoto T. Improving anti-adhesion in aluminum alloy cutting by micro stripe texture[J]. Precision Engineering, 2012, 36(2): 229-237.
[88] Sugihara T, Enomoto T. Crater and flank wear resistance of cutting tools having micro textured surfaces[J]. Precision Engineering, 2013, 37(4): 888-896.
[89] Sugihara T, Tanaka H, Enomoto T. Development of novel CBN cutting tool for high speed machining of inconel 718 focusing on coolant behaviors[J]. Procedia Manufacturing, 2017, 10: 436-442.
[90] Voevodin A A, Zabinski J S. Laser surface texturing for adaptive solid lubrication[J]. Wear, 2006, 261(11/12): 1285-1292.
[91] Basnyat P, Luster B, Muratore C, et al. Surface texturing for adaptive solid lubrication[J]. Surface and Coatings Technology, 2008, 203(1/2): 73-79.
[92] 杨奇彪, 肖晨光, 陈中培, 等. 激光诱导氧化铝陶瓷刀具的表面浸润性[J]. 激光与光电子学进展, 2017, 54(10): 101401.
[93] 杨奇彪, 陈中培, 杨涛, 等. 飞秒激光加工YG6不同微织构表面浸润性研究[J]. 激光与光电子学进展, 2018, 55(9): 091404.
[94] Shaw[\s]{1}MC,[\s]{1}Cookson[\s]{1}JO.[\s]{1}Metal[\s]{1}cutting[\s]{1}principles[M].[\s]{1}2nd[\s]{1}ed.[\s]{1}New[\s]{1}York:[\s]{1}Oxford[\s]{1}University[\s]{1}Press,[\s]{1}2005.[\s]{1}
Article Outline
魏超, 马玉平, 韩源, 张遥, 陈雪辉. 飞秒激光加工超硬材料的研究进展[J]. 激光与光电子学进展, 2019, 56(19): 190003. Chao Wei, Yuping Ma, Yuan Han, Yao Zhang, Xuehui Chen. Femtosecond Laser Processing of Ultrahard Materials[J]. Laser & Optoelectronics Progress, 2019, 56(19): 190003.