荧光成像技术探测熔石英元件亚表面缺陷
下载: 1245次
1 引言
随着高功率激光装置的不断改进和发展,激光器高能量输出成为趋势。由于熔石英材料具有化学稳定性好、无体内损伤的优点,熔石英光学元件是高功率激光装置中最常用和重要的光学元件之一。熔石英光学元件加工成型过程包括切割、研磨、抛光等工序,即使在光学显微镜下看起来完美无缺的光学元件,也不可避免地存在表面下几到几十微米的亚表面层。这个亚表面层内存在微裂缝、杂质等缺陷[1-2],当足够高的激光能量持续辐射时就会产生激光诱导损伤,这是目前熔石英光学元件产生激光诱导损伤的主要原因。因此熔石英光学元件亚表面缺陷的探测与表征对评价和提升熔石英光学元件的激光损伤性能来说极为重要。
熔石英光学元件亚表面缺陷的探测方法分为有损探测和无损探测两种。有损探测主要有HF酸刻蚀、等离子体刻蚀等。有损探测虽然能够实现熔石英光学元件的亚表面缺陷探测,但是对熔石英造成无法逆转的损害,导致熔石英无法使用,因而比较浪费材料。无损探测可克服该缺点,既能达到探测熔石英亚表面缺陷的目的,又不损害熔石英,从而节约材料和成本。目前常用的无损探测技术有光热弱吸收[3]和全内反射显微技术[4]等。光热弱吸收灵敏度较高,但其探测速度非常慢,并且探测速度难以得到大幅度提升。全内反射显微技术速度可以提升,但其灵敏度太低。
本文提出一种探测熔石英光学元件亚表面缺陷的方法即荧光成像法,该方法不仅能很好地解决上述两个短板,还可以实现无损测试。利用该方法对比研究了不同加工工艺下熔石英光学元件的亚表面缺陷[5-8],并通过表面粗糙度测试和损伤性能测试开展了该方法在探测与损伤相关的熔石英亚表面缺陷有效性研究。
2 熔石英光学元件亚表面缺陷检测原理
基于熔石英光学元件亚表面缺陷吸收辐照紫外激光后会发射出波长在410~580 nm范围的荧光,设计如
利用
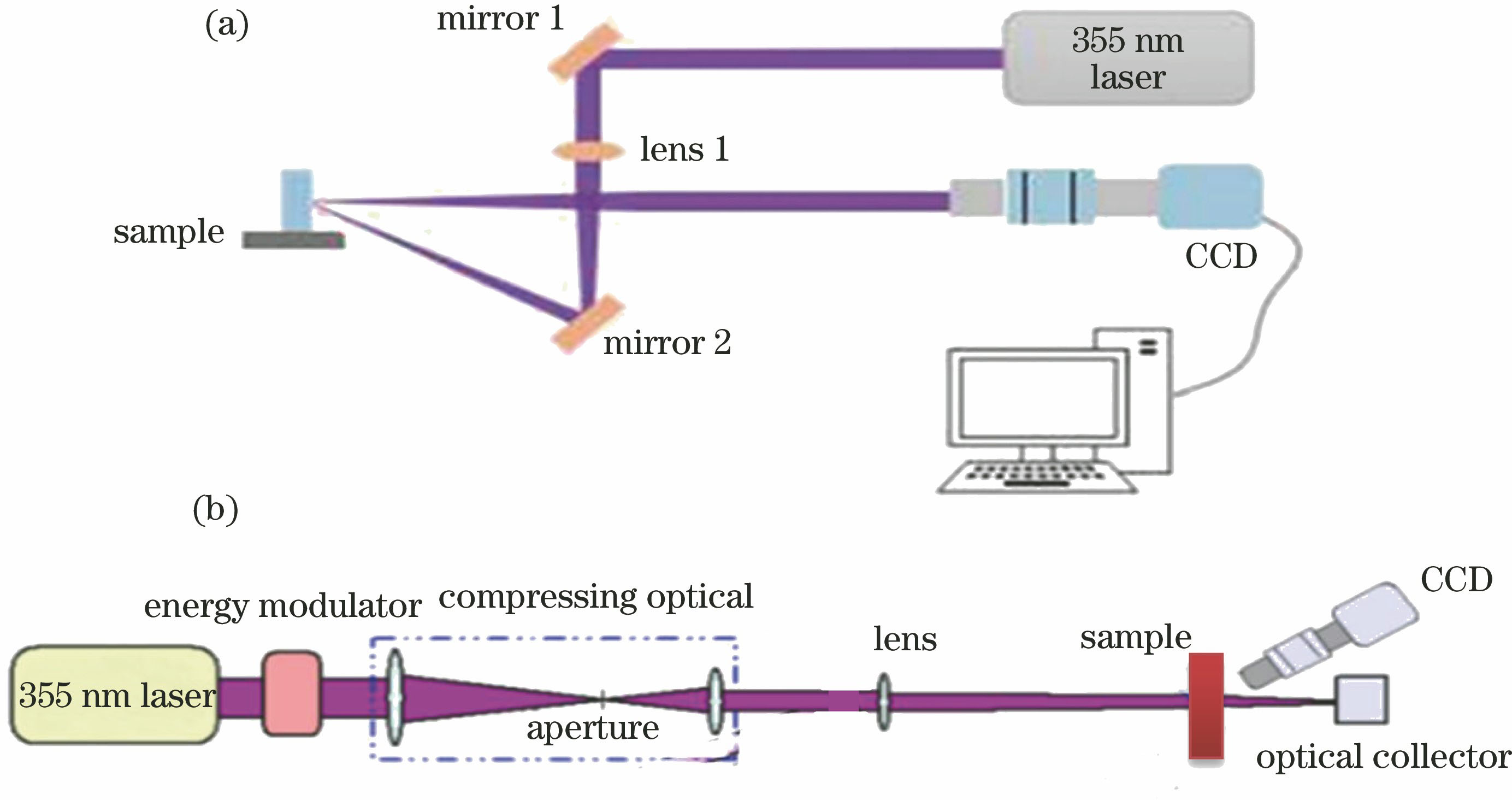
图 1. (a)荧光无损检测熔石英亚表面缺陷示意图;(b)光学元件的激光损伤测试光路示意图
Fig. 1. (a) Schematic of subsurface defect of fused silica in fluorescence non-destructive testing; (b) laser damage test optical path of optical elements
3 检测样品制备
熔石英光学元件加工的具体流程为采购材料、磨砂、抛光、修粗糙度。磨砂时,选用不同砂号的砂,从粗到细,每种砂所磨的尺寸和时间均有不同要求;再进行抛光,选用不同颗粒度的氧化铈抛光粉和不同的抛光盘,从粗到细抛光;最后修粗糙度。
表 1. 各熔石英样品的粗糙度
Table 1. Roughness of fused silica samples
|
4 测试结果及分析
4.1 荧光成像技术无损测试熔石英亚表面缺陷
采用荧光成像技术对
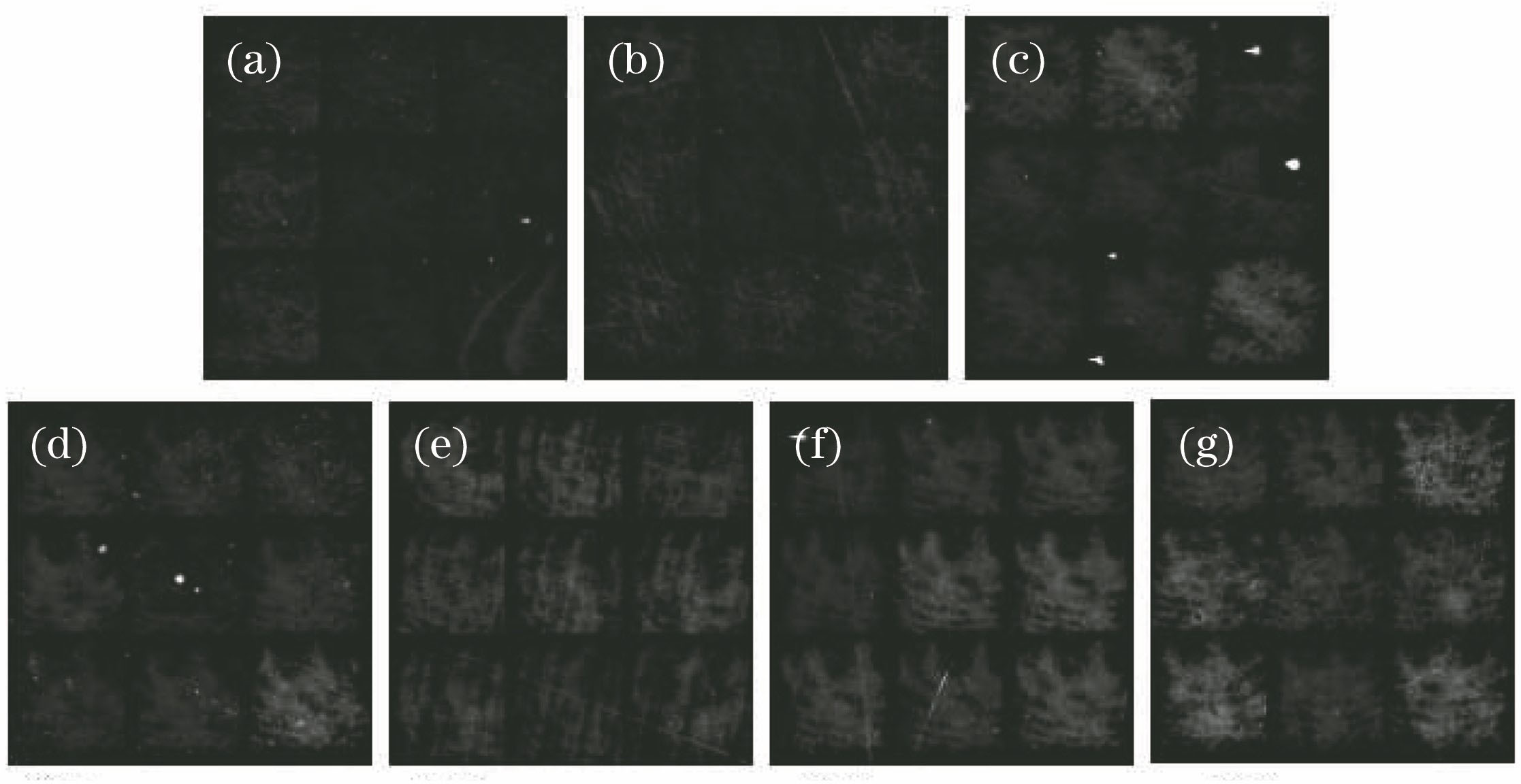
图 2. 熔石英元件亚表面缺陷的荧光图像。(a) Ort1;(b) Ort2;(c) Ort3;(d) Ort4;(e) Ort5;(f) Ort6;(g) Ort7
Fig. 2. Fluorescence images of subsurface defects of fused silica elements. (a) Ort1; (b) Ort2; (c) Ort3; (d) Ort4; (e) Ort5; (f) Ort6; (g) Ort7
表 2. 荧光无损探测统计表
Table 2. Fluorescence non-destructive detection statistics
|
行对比。结果表明,荧光测试结果中的划痕、亮点位置及其形状大小都与光学显微镜测试的结果基本一致,因此荧光无损测试的结果是可靠的。
为了便于数据分析,利用相关软件进行统计分析,获得各个样品的缺陷所占面积比,如
4.2 熔石英样品的损伤性能
对
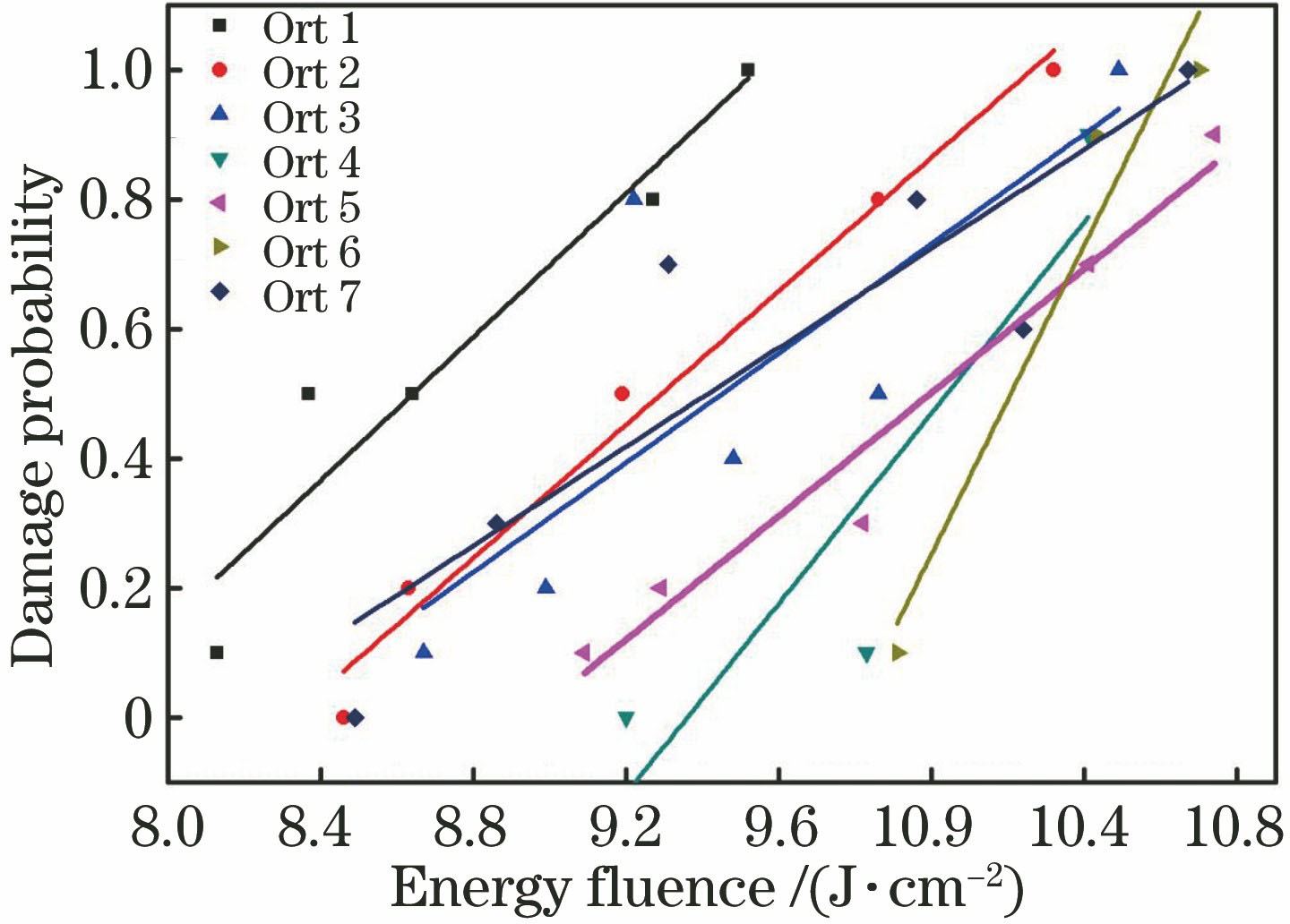
图 3. 熔石英光学元件的激光损伤概率与能量密度的关系曲线
Fig. 3. Curves of laser damage probability and energy density of fused silica optical elements
表 3. 不同熔石英样品的零概率损伤阈值
Table 3. Zero-probability damage threshold for different fused silica sample
|
5 结论
利用荧光成像技术无损探测了熔石英亚表面缺陷,并通过熔石英亚表面缺陷与激光诱导损伤性能的相关性研究可知,荧光缺陷密度与熔石英亚表面缺陷成正比,荧光缺陷密度越大熔石英光学元件损伤阈值越低。同时,从实验角度揭示表面粗糙度与熔石英元件的损伤性能和亚表面缺陷均无明显关系。研究结果表明,荧光成像技术可以有效评价光学元件损伤性能。
[3] 王英剑, 胡海洋, 李庆国, 等. 高反射硅镜弱吸收的研究[J]. 中国激光, 2001, 28(10): 937-940.
[4] 崔辉, 刘世杰, 赵元安, 等. 全内反射显微技术探测亚表面缺陷新方法研究[J]. 光学学报, 2014, 34(6): 0612004.
[5] 项震, 聂传继, 葛剑虹, 等. 光学元件亚表面缺陷结构的蚀刻消除[J]. 强激光与粒子束, 2007, 19(3): 373-376.
[7] 徐世珍, 吕海兵, 田东斌, 等. 酸蚀深度对熔石英三倍频激光损伤阈值的影响[J]. 强激光与粒子束, 2008, 20(5): 760-764.
[9] Hobbs D S. MacLeod B D, Riccobono J R. Update on the development of high performance anti-reflecting surface relief micro-structures[J]. Proceedings of SPIE, 2007, 6545: 65450Y.
[14] Sun C H, Gonzalez A, Linn N C, et al. Templated biomimetic multifunctional coatings[J]. Applied Physics Letters, 2008, 92(5): 051107.
[18] 邹广健, 张宝富, 李诚鑫, 等. 光电震荡器的混沌光子压缩采样方法[J]. 中国激光, 2017, 44(11): 1106002.
[20] 丁俊伟, 梁斌明, 蒋强, 等. 近零折射率材料相位特性及应用[J]. 激光与光电子学进展, 2017, 54(3): 031603.
李洪路, 刘红婕, 蒋晓东, 黄进, 曹林洪. 荧光成像技术探测熔石英元件亚表面缺陷[J]. 激光与光电子学进展, 2019, 56(1): 011004. Honglu Li, Hongjie Liu, Xiaodong Jiang, Jin Huang, Linhong Cao. Subsurface Defects in Fused Silica Elements Detected by Fluorescence Imaging Technology[J]. Laser & Optoelectronics Progress, 2019, 56(1): 011004.