高能激光单晶硅反射镜纳米精度控形控性制造技术
下载: 1371次特邀综述
Significance In high-power infrared laser systems, monocrystalline silicon reflectors are widely used, and the reflectors need to achieve high-precision, high-stability beam transmission under high-power laser irradiation for long durations. The high accuracy of components and laser load capacity are both highly desired. With the continuous development of high-energy laser technology, the performance of existing monocrystalline silicon components has been unable to support the further improvement of system output power and performance, which has become a technical shortcoming. A high-energy laser system requires optimum reflector performance in systems, i.e., precision and laser load capacity. The pursuit of full-frequency spatial error restraint and reduction of laser energy absorption rate depends on fabrication quality. However, at present, fabrication technology inherits from traditional optical processing, and it is difficult to achieve both precision and laser load capability. Accordingly, it is necessary to investigate manufacturing methods and processes and combine innovative manufacturing techniques with application characteristics. By discussing the present situation and key technology of monocrystalline silicon component manufacturing, we hope technical support for realizing nanoprecision shape control manufacturing of monocrystalline silicon can be provided.
Progress This article summarizes the current status of and difficulties in manufacturing high-energy laser aspheric components and reveals the typical processing defect morphology and generation mechanism that reduce the laser load capacity. Based on the realization of high-precision processing of aspherical components, the role of new methods of controllable flexible body processing based on immersion smooth polishing, ion beam sputtering cleaning, and other methods in controlling defects is discussed to realize the formation of high-energy laser aspherical components. The specific research includes the following aspects:
(1) Nanoprecision surface shape control manufacturing technology. With continuous improvement in energy transmission ratio and irradiation distance of laser systems, the quality of optical parts has also increased. Nanoprecision manufacturing requires the full-frequency band error to converge to the nanometer order of magnitude. At this time, the surface shape error and the medium- and high-frequency roughness at the macroscopic scale will be in the same order of magnitude, and the correlation between them will be obviously enhanced. In recent years, our research group has vigorously developed ultraprecision cutting (
(2) Nanoprecision intrinsic surface controllability generation method. The surface of monocrystalline silicon generally leads to some typical damage precursors such as absorbable impurities, cracks, and scratches during mechanical polishing. The types and densities of these damage precursors seriously restrict the damage resistance of optical components. As a new form of subsurface defect, the body before nanodamage can be divided into mechanical, pollution, and structure types. Our research group has conducted a series of investigations on the monocrystalline silicon intrinsic surface processing method and the craft. It removes the optical component surface defect (
(3) Nanoprecision shape control combination process. To achieve the goal of nanoprecision surface shape control, our research group has realized a combination process of high precision and low defect (
Conclusion and Prospect The main achievements of high-precision and low-defect control manufacturing technology in the Precision Engineering Laboratory of National University of Defense Technology in recent years are reviewed. The high-precision and low-defect combination processing technology developed by our research group has been applied to the processing of monocrystalline silicon, which supports the development of high-power laser systems.
1 引言
在红外高能激光系统中,单晶硅反射镜被广泛使用[1]。反射镜需要在高功率密度激光的长时间辐照下实现高精度、高稳定性的光束传输,对元件精度与激光负载能力都有着极高的要求[2-3]。为了提升高通量强光元件的成形、成性以及高效率经济制造,国内外研究人员近几年致力于研究获得单晶硅元件本征表面的加工方法与工艺,包括弹塑性域材料去除与清洗技术等[4-8]。但目前尚缺乏基底加工工艺、残余缺陷、吸收率之间关系的研究,且无完备的理论来阐述如何同时提升元件的加工精度和激光负载能力。因此,通过开展制造方法与工艺方面的研究,结合应用特点创新制造技术获得低损伤洁净表面,成为进一步提升元件激光负载能力的新思路和技术发展趋势。本课题组提出的使用磁流变、离子束等可控柔体加工技术提升了单晶硅元件的激光负载能力,突破了纳米精度表面控形制造技术、纳米精度本征表面控性生成方法、单晶硅高精度低缺陷组合工艺等一系列关键技术,提高了单晶硅元件的加工效率和加工效果,为单晶硅元件的高精度低缺陷控形控性制造提供了一条新的技术途径。
2 纳米精度表面控形制造技术
随着激光系统能量传输比和辐照距离的不断提升,对光学零件质量的要求也日益提高。纳米精度制造要求全频段误差一致收敛到纳米量级,此时宏观尺度的面形误差和中高频粗糙度将处于同一数量级,它们之间的关联性将明显增强。在多年的研究中,本研究团队大力发展了超精密切削、磁流变、离子束和保形光顺技术,目的是获得全频段亚纳米精度光学表面。
2.1 低频面形误差——超精密切削、磁流变
目前,平面单晶硅的磨削缺陷已经得到很好的抑制,甚至可以直接使用超精磨制造出光学表面。澳大利亚昆士兰大学的Zhang[9]、日本茨城大学的Zhou等[10-11]、中国大连理工大学的康仁科等[12]均通过化学机械磨削方法获得了高质量表面,但在曲面单晶硅磨削中尚未完全解决亚表面损伤的问题。近年来,单晶硅超精密切削技术逐渐成熟,该技术通过超声振动、纳米冷却液等有效抑制了刀具的磨损,提升了表面质量。金钊等[13]采用MgO软磨料砂轮进行了纳米精度的单晶硅磨削,亚表面损伤接近于零。哈尔滨工业大学的陈冰[14]在非球面磨削中将亚表面缺陷深度控制在了5 μm左右。本研究团队通过高速度、高刚度、微粒径的超精密磨削加工进一步提升了面形精度,减小了缺陷层的深度[15]。本研究团队对超精密磨削的损伤层深度进行了理论计算与实际测试。

图 1. 单晶硅超精密磨削后的缺陷深度。(a)初始表面,深度为0;(b)深度为1.5 μm;(c)深度为2.5 μm;(d)深度为3 μm
Fig. 1. Defect depth distribution after ultra-precision grinding of single crystal silicon. (a) Original surface, depth is 0; (b) depth is 1.5 μm; (c) depth is 2.5 μm; (c) depth is 3 μm
磁流变抛光技术是利用磁流变抛光液在磁场中的流变性进行抛光的一种超精密加工方法,其独特的剪切加工特性能够使单晶硅在加工过程中不产生破碎缺陷。湖南大学的尹韶辉等[16]使用斜轴磁流变抛光技术高效率地制造了小口径单晶硅非球面镜,其粗糙度均方根(RMS)小于 1 nm,面形精度(峰谷值)小于 69 nm。本研究团队基于弹性接触力学和双刃圆模型,分析了磁流变弹性域加工的条件,认为弹性域化学加工是实现磁流变超光滑无损加工的重要条件。
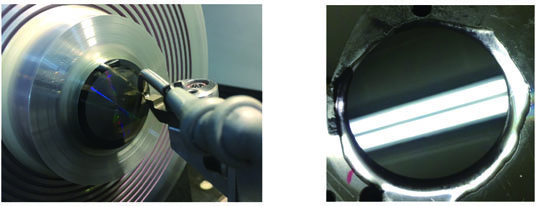
图 2. 单晶硅磁流变抛光。(a)加工中;(b)加工后
Fig. 2. Single crystal silicon magnetorheological polishing. (a) Polishing process; (b) after polishing
2.2 中高频误差——保形光顺
光学元件中高频误差的高低直接关系到整个系统的成败。光顺加工是控制光学镜面高频误差的最重要手段之一,对于光学元件全频段误差的一致收敛具有重要意义。
对于中频误差,一般在精抛光阶段插入光顺工艺加以抑制。光顺工艺利用抛光盘的刚度在中频误差的高点处产生比低点处更大的抛光压强来优先去除局部高点误差,使中频误差收敛。但单晶硅强激光反射镜中大量采用的是非球面设计,甚至包括柱面设计,光顺工艺无法直接应用。如
![柱面光顺工艺[17]。(a)柱面光顺实物图;(b)半刚性柱面光顺盘;(c)光顺前的局部中频误差;(d)光顺后的局部中频误差](/richHtml/zgjg/2021/48/4/0401007/img_3.jpg)
图 3. 柱面光顺工艺[17]。(a)柱面光顺实物图;(b)半刚性柱面光顺盘;(c)光顺前的局部中频误差;(d)光顺后的局部中频误差
Fig. 3. Cylindrical smoothing process[17]. (a) Practical equipment for cylindrical smoothing process; (b) semi-rigid cylindrical smoothing plate; (c) mid spatial frequency error before smoothing; (d) mid spatial frequency error after smoothing
3 纳米精度本征表面控性生成方法
在机械抛光处理过程中,单晶硅表面一般会出现一些典型的损伤前驱体,如吸收性杂质、裂纹、划痕等,这些损伤前驱体的种类和密度严重制约了光学元件的抗损伤性能。纳米损伤前驱体作为表面、亚表面缺陷的新形态,一般可分为机械型、污染型、结构型三类。本研究团队对单晶硅本征表面加工方法与工艺进行了一系列研究,通过浸没式抛光、离子束等技术去除了光学元件的表面缺陷,获得了纳米精度的本征表面,提升了单晶硅元件的激光负载能力。
3.1 机械型表面缺陷——浸没式抛光加工
为了解决抛光过程中的划痕问题,本研究团队将浴法抛光工艺与普通的计算机控制光学表面成形(CCOS)工艺结合在一起,在工件完全浸没于抛光液中的情况下,开展了CCOS抛光加工[18],如
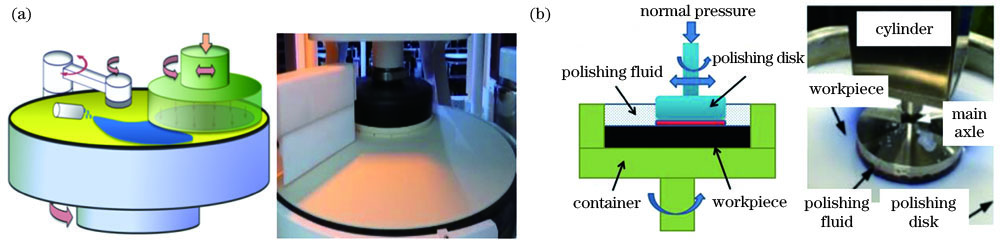
图 4. 传统抛光与浸没式抛光。(a)传统抛光装置;(b)浸没式抛光装置
Fig. 4. Traditional polishing and immersion polishing equipment. (a) Traditional polishing equipment; (b) immersion polishing equipment
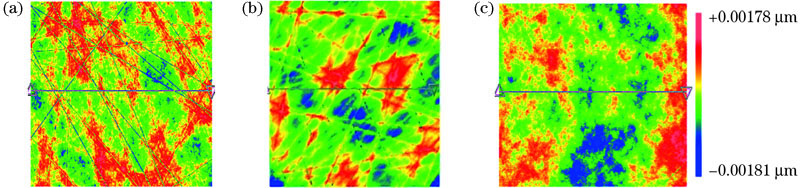
图 5. 通过大颗粒隔离实现的表面缺陷抑制。(a)空气中抛光,表面划痕;(b)空气中抛光,表面凸线;(c)浸没式抛光,表面无缺陷
Fig. 5. Surface defect suppression realized by isolating large particles. (a) Scratches on polished surfaces in air; (b) convex line on polished surfaces in air;(c) immersive polishing, without surface defects
3.2 污染型缺陷——大束流离子束清洗
除表面划痕外,单晶硅的亚表面材料在加工过程中也会产生杂质污染。为了降低污染型缺陷对元件激光负载能力的影响,美国的国家点火设施(NIF)采用兆声波酸洗工艺[19],用一定浓度的HF酸作为腐蚀液浸泡工件,以去除污染提升阈值。一方面,元件表面面形不可控,在酸蚀过程中可能会遭到严重破坏;另一方面,酸蚀反应产物的溶解度有限,沉积后会形成二次污染,反而会降低元件的激光损伤阈值。
本研究团队创新性地提出了使用离子刻蚀工艺来去除污染型缺陷,该工艺利用离子源发射的离子束流轰击光学镜面时发生的物理溅射效应来达到去除光学元件表面材料的目的[20-22],如
![离子束加工设备与物理溅射过程示意图[22]。(a)离子束加工设备;(b)物理溅射过程示意图](/richHtml/zgjg/2021/48/4/0401007/img_6.jpg)
图 6. 离子束加工设备与物理溅射过程示意图[22]。(a)离子束加工设备;(b)物理溅射过程示意图
Fig. 6. Ion beam processing equipment and physical sputtering process. (a) Ion beam processing equipment; (b) physical sputtering process
3.3 结构型缺陷——离子束抛光(倾斜入射)
在单晶硅元件的加工过程中,化学键的断裂和杂质离子的引入,会在材料体内产生大量的化学结构缺陷。这些缺陷会降低单晶硅元件的激光负载能力。
如
![离子束倾斜入射实验[23]。 (a)实验照片;(b)工件面形误差分布](/richHtml/zgjg/2021/48/4/0401007/img_7.jpg)
图 7. 离子束倾斜入射实验[23]。 (a)实验照片;(b)工件面形误差分布
Fig. 7. Tilted incident experiments of ion beam[23]. (a) Experimental photo; (b) surface error map
4 纳米精度控形控性组合工艺
为了达到纳米精度表面控形控性的目标,本团队在深入研究各种加工工艺的基础上,提出了高精度低缺陷组合工艺。该工艺区别于传统加工中各工艺的简单衔接转换,而是将全部指标的实现合理地分配到全工艺流程中,实现了单晶硅元件的高精度低缺陷控形控性制造。
4.1 组合工艺研究
本团队在深入研究纳米精度表面控形控性技术的基础上,形成了独特的单晶硅元件加工工艺,其典型的工艺流程如
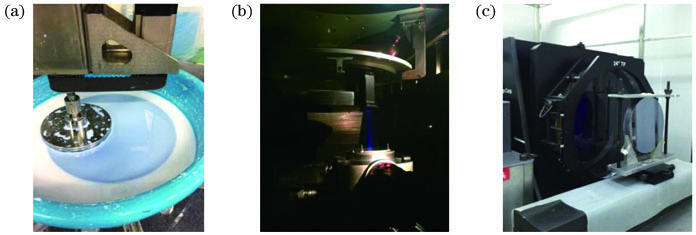
图 8. 组合工艺路线。(a)浸没式抛光;(b)离子束修形;(c)面形精度测量
Fig. 8. Combined process route. (a) Immersion polishing; (b) ion beam figuring; (c) profile accuracy measurement
4.2 组合工艺与传统工艺的对比
为了对比传统工艺与组合工艺所制造的元件的激光性能,本研究团队分别采用两种工艺制造了一件相同规格(Φ200 mm×45 mm)的平面反射镜,并进行了等功率密度测试。编号为A和B的样件分别对应传统工艺与组合工艺,如
在样件B的测试过程中,波前误差从初始的0.1 μm(峰谷值)缓慢变化至0.4 μm(峰谷值),最终仅为样件A的5%左右。同时,样件B的表面荧光点亮度与密度均小于样件A,在样件B表面观测到的膜层损伤在密度和程度上都更小。从膜层损伤形态上来看,传统工艺制造的元件表面发生了多处膜层损伤,膜层破坏严重,损伤尺寸接近毫米级,而组合工艺制造的元件表面多以疖瘤缺陷诱发的小损伤坑为主,损伤坑的直径均在20 μm左右,明显优于传统工艺。组合工艺制造的元件的表面损伤未引起能量吸收率的突变。进一步对比分析后发现,样件B的激光性能显著优于样件A,验证了全频段高精度低缺陷加工对元件性能提升的必要性,显示出了组合工艺的价值。
4.3 柱面元件高精度低缺陷加工实例
某型凸柱面镜是激光束发射出真空腔前反射经过的最后一个元件,在实际应用中,其损伤概率是光路中其他元件的数倍,需要频繁更换。当前柱面元件的激光负载能力无法满足需要,成为了整条光路的短板,因此需要使用更高质量的凸柱面反射镜来提升系统的寿命与可靠性。某型凸柱面镜元件实物如
本研究团队采用组合工艺,通过引入柱面光顺工艺、浸没式抛光工艺与离子束抛光工艺的组合,实现了控形控性加工。组合工艺加工结果如
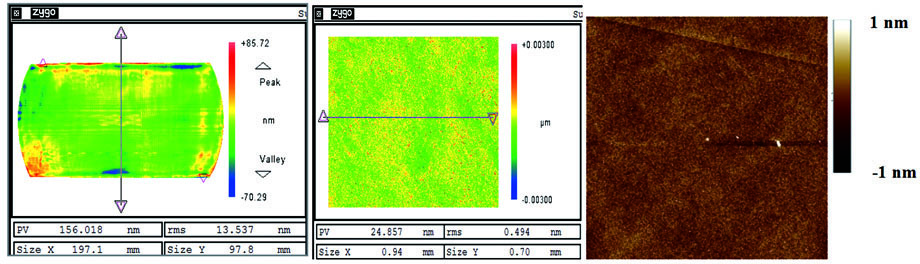
图 11. 凸柱面镜的加工结果。(a)低频面形误差RMS为13.537 nm;(b)中频面形误差RMS为0.494 nm;(c)高频面形误差RMS为0.261 nm
Fig. 11. Processing results of convex cylindrical mirror. (a) RMS of low spatial frequency surface shape error is 13.537 nm; (b) RMS of middle spatial frequency surface shape error is 0.494 nm; (c) RMS of high spatial frequency surface shape error is 0.261 nm
5 结束语
本文综述了近几年本研究团队在单晶硅元件高精度低缺陷控形控性制造技术方面取得的主要成果。本团队研发的高精度低缺陷组合加工工艺已经应用在单晶硅强光光学元件的加工过程中,为高能激光系统的发展提供了支撑。
[2] 余德明, 段微波, 李大琪, 等. 偏振和相位调控反射镜的设计与制备[J]. 光学学报, 2020, 40(15): 1531001.
[3] 邵山川, 陶小平, 王孝坤. 基于条纹反射的超精密车削反射镜的在位面形检测[J]. 激光与光电子学进展, 2018, 55(7): 071203.
[5] Tian Y, Shi F, Dai Y F, et al. Laser absorption precursor research: microstructures in the subsurface of mono-crystalline silicon substrate[J]. Applied Optics, 2017, 56(30): 8507-8512.
[6] 田野, 戴一帆, 石峰, 等. 单晶硅反射镜激光能量吸收系数与衬底表面质量的关联[J]. 国防科技大学学报, 2015, 37(6): 26-29.
[8] 张欣, 黄婷, 肖荣诗. 不同晶面单晶硅在飞秒激光作用下的行为特性[J]. 中国激光, 2017, 44(1): 0102012.
[12] 康仁科, 田业冰, 郭东明, 等. 一种硬脆晶体基片超精密磨削砂轮: CN1951635[P].2007-04-25.
Kang RK, Tian YB, Guo D M. An ultra-precision grinding wheel for hard and brittle crystal substrates:CN1951635[P]. 2007-04-25.
[13] 金钊, 李锦胜, 康仁科, 等. 应用软磨料磨削的单晶硅超精密制造技术[J]. 光电工程, 2011, 38(12): 75-80.
[14] 陈冰. 红外材料非球面透镜的超精密磨削加工关键技术研究[D]. 哈尔滨: 哈尔滨工业大学, 2015.
ChenB. Key technology on ultra-precision grinding of infrared aspheric lens[D]. Harbin:Harbin Institute of Technology, 2015.
[15] Niu YJ, Dai YF, Guan CL, et al. Study on the technology of ultra-precision grinding for aspheric mirror of monocrystalline silicon[C]//The 6th International Conference of Asian Society for Precision Engineering and Nanotechnology. Harbin: [s.n.], 2015.
[16] 尹韶辉, 陈逢军, 张导成, 等. 结合ELID磨削与磁流变光整加工的单晶硅反射镜超精密制造技术[J]. 纳米技术与精密工程, 2007, 5(3): 220-223.
[17] 田野. 单晶硅反射镜高精度低缺陷制造关键技术研究[D]. 长沙: 国防科技大学, 2018.
TianY. The key technology research of high-precision and low-defect fabrication for silicon reflectors[D]. Changsha: National University of Defense Technology, 2018.
[18] Shen Z X, Ma B, Wang Z S, et al. Fabrication of flat and supersmooth surfaces with bowl-feed polishing process[J]. Proceedings of SPIE, 2007, 6722: 67220U.
[21] Cheng W M, Chen M Y. Transformation and connection of subapertures in the multiaperture overlap-scanning technique for large optics tests[J]. Optical Engineering, 1993, 32: 1947-1950.
[22] 周林. 光学镜面离子束修形理论与工艺研究[D]. 长沙: 国防科学技术大学, 2008.
ZhouL. Study on theory and technology in ion beam figuring for optical surfaces[D]. Changsha: National University of Defense Technology, 2008.
[23] 宋辞, 田野, 石峰, 等. 单晶硅柱面反射镜离子束倾斜入射加工工艺优化[J]. 光学学报, 2020, 40(12): 1222001.
Article Outline
石峰, 田野, 乔硕, 周光奇, 宋辞, 薛帅, 铁贵鹏, 周林, 舒勇, 周港. 高能激光单晶硅反射镜纳米精度控形控性制造技术[J]. 中国激光, 2021, 48(4): 0401007. Feng Shi, Ye Tian, Shuo Qiao, Guangqi Zhou, Ci Song, Shuai Xue, Guipeng Tie, Lin Zhou, Yong Shu, Gang Zhou. Nanoprecision Control of Shape and Performance Manufacturing Technology for High-Energy Laser Silicon Components[J]. Chinese Journal of Lasers, 2021, 48(4): 0401007.